镁合金是最轻的金属结构材料之一。镁合金具有高的比强度和比刚度,良好的减震性和电磁屏蔽性,易回收、无污染等特点而成为一种理想的现代工业材料,被广泛应用于航空、航天、汽车、电子等工业领域。然而,耐蚀性差成为制约镁合金发挥性能优势的主要因素。因此,镁合金在工业应用前必须进行适当的表面处理以增强其耐蚀性。阳极氧化是镁合金最常见的一种表面处理方法。目前,研究镁合金阳极氧化工艺和镁合金基体的腐蚀较多,而对于阳极氧化处理后镁合金的腐蚀行为研究较少。为此,本实验将利用电化学阻抗谱方法研究AZ91D 镁合金阳极氧化膜层在NaCl 溶液浸泡过程中的腐蚀行为,为镁合金阳极氧化工艺的改进提供帮助。
1 材料与方法
实验所用材料为铸镁合金AZ91D。材料表面依次用180#,360#,800#,1500#碳化硅水磨砂纸进行打磨,自来水清洗,去离子水清洗,丙酮擦洗晾干,置于干燥器待用。
氧化膜制备工艺流程:化学除油(除油剂为2%;温度为15℃~40℃;时间为2 min)→自来水漂洗→去离子水漂洗→酸处理(密度为1.42 g/ml 的HNO3 20g/L~50 g/L;温度为室温;时间为30 s~60 s)→自来水漂洗→去离子水漂洗→脉冲阳极氧化→自来水漂洗→去离子水漂洗→热风吹干→封闭处理。脉冲阳极氧化溶液配方由氢氧化钠、硅酸盐、硼酸盐及添加剂组成,溶液组分中不含氟、磷、铬及其它重金属离子,属于环保型。脉冲阳极氧化参数为:占空比为30%;脉冲频率为650 Hz;峰值电流密度为45 mA/cm2;溶液温度为15±2℃;氧化时间为10 min。封闭处理采用环保型的Si 化合物作为封闭介质的工艺。
电化学阻抗谱的测量是在开路电位下进行。测量仪器为上海辰华有限公司生产的CHI604A 电化学分析仪。试样为工作电极,大面积铂片为辅助电极,饱和甘汞电极为参比电极,工作电极面积为10 mm×10mm。腐蚀介质为 3.5%NaCl 水溶液,pH 值为6.8~7.2。用恒温水浴控制实验温度为35±1℃。用金属网包覆三电极体系,起屏蔽作用。测量频率范围为0.01 Hz~105 Hz。测量前试样先在测试溶液中预浸约20 min。阻抗谱的解析采用ZSimpWin 软件。以上实验所用到的化学试剂均为分析纯试剂,溶液均采用去离子水配制。
2 结果与讨论
图1 为AZ91D 镁合金阳极氧化膜在35℃,pH=7的3.5%NaCl 溶液中浸泡不同时间的电化学阻抗谱图。
由图1 可以看出:阳极氧化膜的电化学阻抗谱图随浸泡时间的增加而发生改变,这是由于氧化膜层的结构会发生相应改变;阳极氧化膜在刚浸泡及其后的一段时间里(0 h~10 h),电化学阻抗谱呈现出2 个容抗弧,1 个在高频区,另1 个在低频区,这与文献[7]中所提到的经过沸水封闭处理后的L3 铝阳极氧化膜在0.01mol/L NaCl 溶液中的阻抗谱相似;当氧化膜浸泡时间达到21 h 时,此时的电化学阻抗谱除原有的容抗弧外,在高频部分又显示出另一小容抗弧的迹象,如图2 所示。这与文献[8]中提到的20# 碳钢在0.17 mol/LK2Cr2O7 溶液中添加NaCl 使溶液中Cl-的浓度为0.2mol/L 时,29 h 后电极表面有多个蚀孔时的电化学阻抗谱极为相似,说明此时氧化膜已经穿孔,诱导期结束,进入了孔蚀发展期。
根据文献,高频区主要显示氧化膜多孔层的性能,而低频区则主要显示阻挡层的性能。因此,2 个容抗弧分别对应于氧化膜上的多孔层和阻挡层的阻抗行为。在借鉴相关文献的基础上,结合所研究的实际腐蚀体系特点,本实验分别采用图3a (模型为R(RQ)(RQ) )和图3b (模型为 R(Q(R(RQ))) )所示的等效电路来拟合阳极氧化膜层在孔蚀诱导期和在孔蚀发展期的电化学阻抗谱图。
采用ZSimpWin 软件对测量得到的阳极氧化膜浸泡期间的电化学阻抗谱进行参数解析,考察这些参数随时间的变化,试图找出这些参数与腐蚀状态的相关性。
图4 为利用图3a (模型为R(RQ)(RQ) )所示的等效电路来拟合图1 中阳极氧化膜在浸泡时间为0 h~10 h时所得各参数随浸泡时间变化的关系。解析可得包括弥散效应指数在内的7 个参数,分别是溶液电阻Rsol,多孔层电阻Rp,多孔层表面/介质界面的常相位角元件Qp 的电容Yp 和弥散效应指数np,阻挡层电阻Rb,阻挡层表面/介质界面的常相位角元件Qb 的电容Yb 和弥散效应指数nb。
由图4a 可以看出,溶液电阻Rsol 很小,在浸泡初期Rsol 值略有升高,然后趋于稳定。从图4b 和图4c可知:多孔层电阻Rp 随浸泡时间的延长而减小;而多孔层的电容Yp 则随浸泡时间的延长而增大。这可能是因为在浸泡初期,电解质溶液进入多孔层,因此,初期的Rp 值有较大幅度的下降,随着多孔层溶液含量趋于“饱和”时,Rp 值变化也就趋于缓慢。而电容Yp则由于溶液进入多孔层后,随多孔层的粗糙度增加而增大。由图4d 可见,弥散效应指数np 值与浸泡时间的变化基本无关,这与文献的实验结果相吻合。图4e 说明,阻挡层电阻Rb 随浸泡时间的延长而减小,这可能是由于镁合金阳极氧化膜的阻挡层存在若干微观缺陷(如微裂纹)和薄弱部位,浸泡溶液仍能渗透到阻挡层,从而引起Rb 值随浸泡时间的延长而减小。在拟合结果中(图4f 和图4g),阻挡层的电容Yb 和弥散效应指数nb 与浸泡时间的关系均没有明显的规律性。
按照孔蚀过程的电化学机理,在孔蚀发展期,电极表面存在2 个不同的反应区:1 个是发生在蚀孔内基底金属面上的反应;另1 个是发生在孔外氧化膜表面上的反应。前者电极电位要负于后者电极电位,故在两者短路耦合时,蚀孔内的金属表面上主要进行阳极溶解反应。与氧化膜表面的阴极区相比,蚀孔内的阳极区的面积要小得多,故蚀孔内的阳极电流密度很大,从而使蚀孔内溶液中的欧姆电位降不可忽略。此时可用模型为 R(Q(R(RQ)))来拟合电化学阻抗谱。
图5 为利用图3b(模型为 R(Q(R(RQ))) )所示的等效电路来拟合图1 中阳极氧化膜在浸泡时间为21 h~48 h 时所得各参数随浸泡时间变化的关系。解析可得包括2 个弥散效应指数在内的7 个参数,分别是溶液电阻Rsol,氧化膜表面/介质界面的常相位角元件Q1的电容Y1 和弥散效应指数n1,蚀孔内溶液电阻R1,蚀孔内阳极金属/介质界面的常相位角元件Q2 的电容Y2和弥散效应指数n2,蚀孔内的反应电阻R2。从图5a可看出,溶液电阻Rsol 随浸泡时间的延长逐渐减小。这可能是由于随浸泡时间的延长腐蚀加剧,从而使溶液中的离子数量增多引起的。从图5b 可知,电容Y1随浸泡时间的延长而增大。这是因为Y1 随固体腐蚀产物在氧化膜表面的沉积和氧化膜表面的粗糙度的增加而增大。从图5c 可见,弥散效应指数n1 随浸泡时间的延长而减小,即氧化膜上的弥散效应增大。Mansfeld认为弥散效应同电极表面的粗糙度和电流分布的不均匀程度有关。随着浸泡时间的延长即腐蚀的进行,一方面氧化膜的蚀孔数增多与扩大,使氧化膜表面的粗糙度增加,另一方面在氧化膜表面上沉积有固体的腐蚀产物,影响了电流的分布,因此,氧化膜上弥散效应指数随之减小。蚀孔内溶液电阻R1 应与蚀孔中的溶液浓度、蚀孔个数及尺寸有关,而蚀孔内阳极金属/介质界面的常相位角元件Q2 的电容Y2 及弥散效应指数n2与蚀孔中的电极过程及各种影响因素和蚀孔个数有关。在拟合结果中(图5),它们与浸泡时间的关系均没有明显的规律性,但氧化膜表面/介质界面的常相位角元件Q1 的电容Y1 和弥散效应指数n1 及蚀孔内的反应电阻R2 随浸泡时间的变化存在一定的规律。从图5g 可知,蚀孔内的反应电阻R2 随浸泡时间的延长而减小。这是因为一旦氧化膜穿孔,腐蚀介质NaCl 与镁合金基体接触,镁合金的腐蚀加快,蚀孔内的反应电阻R2 就减小。随着腐蚀的继续进行,蚀孔底部金属镁(阳极)便发生溶解,即:
阴极为析氢反应(蚀孔外表面),即:
蚀孔内的镁离子不断增加,在孔蚀电池产生的电场作用下,蚀孔外的阴离子(Cl-)不断向孔内迁移、富集,孔内Cl-离子浓度升高。同时由于孔内镁离子浓度的升高并发生水解,即:
文献证实表面沉积NaCl 的镁合金在纯空气环境中腐蚀时腐蚀产物中含有Mg2(OH)3Cl.3H2O),结果使孔内溶液H+ 浓度升高,pH 值降低,溶液酸化,相当于使蚀孔内镁合金处于HCl 介质中,处于活化溶解状态,使蚀孔内的反应电阻R2 不断降低,腐蚀不断向前发展。水解产生的H+ 和孔内的Cl-又促使蚀孔侧壁镁合金的继续溶解,发生自催化反应,即:
蚀孔口形成的Mg(OH)2 腐蚀产物沉积层,阻碍了扩散和对流,使蚀孔内溶液得不到稀释,从而造成了上述闭塞电池效应。
3 结论
1) 在孔蚀诱导期,随浸泡时间的延长,溶液电阻Rsol 和多孔层的电容Yp 有所增大,多孔层电阻Rp 和阻挡层电阻Rb 逐渐减小,弥散效应指数 np 值基本不变,而阻挡层的电容Yb 和弥散效应指数nb 的变化无明显的规律性。
2) 在孔蚀发展期,随浸泡时间的延长,溶液电阻Rsol,弥散效应指数n1 和蚀孔内的反应电阻R2 逐渐减小,电容Y1 逐渐增大,而蚀孔内溶液电阻R1,蚀孔内阳极金属/介质界面的常相位角元件Q2 的电容Y2 及弥散效应指数n2 的变化无明显的规律性。
更多关于材料方面、材料腐蚀控制、材料科普等方面的国内外最新动态,我们网站会不断更新。希望大家一直关注中国腐蚀与防护网http://www.ecorr.org
责任编辑:王元
《中国腐蚀与防护网电子期刊》征订启事
投稿联系:编辑部
电话:010-62313558-806
邮箱:fsfhzy666@163.com
中国腐蚀与防护网官方 QQ群:140808414
免责声明:本网站所转载的文字、图片与视频资料版权归原创作者所有,如果涉及侵权,请第一时间联系本网删除。
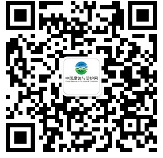
官方微信
《中国腐蚀与防护网电子期刊》征订启事
- 投稿联系:编辑部
- 电话:010-62313558-806
- 邮箱:fsfhzy666@163.com
- 中国腐蚀与防护网官方QQ群:140808414