引言
海洋的恶劣环境常导致船舶、海洋平台金属零部件腐蚀,造成极大的安全隐患。有机涂层是金属腐蚀防护的重要方法之一,其具有施工方便、成本低和维护简单等特点。
氟碳树脂漆是一种重要的有机涂料,其分子链中含有大量的高能C-F键,分子链间交联密度大,具有优异的耐候性、耐酸碱性和耐盐雾性能,常用作金属材料防护涂层。但是纯氟碳涂层的耐磨性能较差、结合强度较低,限制了氟碳涂料的应用,因此需要对涂料进行改性来提高涂层性能。
常用的改性方法有化学改性、物理共混改性和填料改性,其中填料改性中应用的颜填料可以起到修饰和增强涂层性能的作用。随着纳米材料制备技术的成熟,纳米填料在涂层中也得到了广泛的研究和应用。实验发现,由于纳米粒子物理尺寸小,比表面积大,对涂层的硬度、耐磨性、防紫外和防腐蚀等性能具有极佳的增强效果。
石墨烯是一种二维纳米结构新材料,在热学、电学、光学和力学等方面表现突出。研究表明石墨烯可有效地改善聚氨酯、环氧树脂、丙烯酸树脂等材料的性能。这是因为涂料中的石墨烯以层片状存在,并有效地封堵涂层孔隙,对H2O、O2和Cl-等腐蚀介质均显示出优异的阻隔性能,同时能够提高涂层的耐磨性和结合强度。石墨烯的分散对涂层性能具有重要的影响,常用的分散方式有原位聚合、化学改性、超声分散等。本文通过超声分散的方式,利用超声空化效应所产生的机械剪切力将石墨烯分散在氟碳树脂中制备复合涂层。通过红外光谱以及场发射扫描电镜对石墨烯和复合涂层的微观形貌进行表征,对涂层的结合强度和接触角进行测试,并采用电化学阻抗谱和盐雾试验研究石墨烯对涂层防护性能的影响。
1 实验部分
1.1 实验材料及预处理
实验所用氟碳树脂购自常州市佳美涂料有限公司;石墨烯(厚度0.8~1.2 nm,直径0.5~2 μm,单层率约80%)由南京先丰纳米材料科技有限公司提供;N,N-二甲基甲酰胺(DMF)购自国药集团化学试剂有限公司;涂层基体材料为Q235 低碳钢(C:0.15%~0.20%;Mn:0.30%~0.65%;Si≤0.30%;S≤0.15%;P≤0.04%)。将试样切割成不同尺寸形状,用SiC砂纸从100#打磨至400#,分别用丙酮、乙醇和蒸馏水超声清洗,吹干后置于干燥皿中备用。
1.2 涂层的制备
用细胞破碎仪VCX800(SONICS & MATERI-ALS,INC.)通过超声作用将石墨烯(G)在氟碳(FT)树脂中分散,得到混合均匀的有机涂料(石墨烯的含量分别为0.01wt%、0.05wt%和0.15wt%,分别记为FT-G1、FT-G5 以及FT-G15),加入固化剂和稀释剂搅拌均匀后,静置熟化5 min。采用旋涂的方式在Q235试样表面制备氟碳/石墨烯复合涂层(FTG),于60 ℃下固化24 h,得到厚度25±3 μm涂层备用,每组采用三个平行样进行实验。
1.3 微观分析和性能测试
1.3.1 微观分析
采用傅里叶红外光谱仪(Thermo Sceientific Ni-colet iS10 spectrometer,Thermo Fisher Scientific Inc.)对样品进行官能团检测分析,扫描范围为600 ~4000 cm-1,粉末试样采用KBr压片法制备,实验前需将粉末在60 ℃烘箱中干燥24 h,研磨后通过压片机制备背景样品并测试,将少量粉末试样与KBr混合研磨,压制实验样品并测试,测试系统将自动扣除背景红外图谱;将G分散在DMF中后真空干燥,采用ZEISS ULTRA 55场发射扫描电子显微镜(FESEM)对G和涂层表面微观形貌进行表征分析。
1.3.2 物理性能测试
根据标准ASTM D4541-2009《用便携式附着力测试仪测定涂层拉脱强度》,采用手持式拉拔式附着力测试仪(ProsiTest AT)将涂层从基体表面分离,以检测涂层与金属基体间的结合强度,试样尺寸为Φ25 mm×3 mm。采用静态接触角测量仪DSA100(德国克鲁士公司)测量涂层的水接触角,根据接触角的大小分析涂层的疏水性。
1.3.3 耐蚀性能测试
根据国家标准GB/T 1771—2007 进行盐雾试验,将试样切割为30 mm×30 mm×3 mm大小,涂层以外部分用环氧腻子密封,喷雾溶液为5wt%NaCl溶液,试验箱温度为35 ℃。试样分为划痕和完整涂层两种,其中划痕试样用来检测漆膜破损后的耐蚀性,完整试样则观察涂层的起泡和生锈等现象。
电化学实验试样为10 mm×10 mm×3 mm,实验前用704硅橡胶密封工作面以外的金属表面。将试样浸泡在3.5wt%的NaCl溶液中,测试试样浸泡不同时间后的开路电位(OCP)和电化学阻抗谱(EIS)。实验采用PARSTAT 2273(普林斯顿)电化学工作站进行测试,试样为工作电极,饱和甘汞电极为参比电极,铂铌丝为辅助电极,扫描频率范围为100 kHz~10 mHz,信号幅值为20 mV,采用ZsimpWin软件对实验数据进行拟合。
2 结果与讨论
2.1 微观形貌特征
通过FE-SEM观察石墨烯的微观形貌特征,结果如图1所示。由图1可以看出,石墨烯呈薄纱卷曲形状,这是由于石墨烯表面能较高,极易因表面电荷不平衡而失稳,破坏石墨烯本身的平面结构,因此呈现出褶皱形貌特征;FT涂层表面有微型大量孔洞及褶皱,而添加适量石墨烯后,涂层表面平整光滑,无明显缺陷,当石墨烯含量达到0.15wt%时,涂层表面出现较多缝隙、裂纹等缺陷,且有团聚块出现。
石墨烯、氟碳涂层、氟碳/石墨烯复合涂层的红外光谱图如图2 所示。石墨烯在3461 cm-1,1641cm-1,1384 cm-1 处有明显的特征峰,其中3461 cm-1处较宽吸收峰为水分子和未完全还原的羟基与羧基中的-OH伸缩振动峰,1641 cm-1处为C=C双键的伸缩振动峰,1384 cm-1有C-OH的伸缩振动峰,说明所使用的石墨烯含有-OH、-COOH等官能团,与文献中石墨烯的FT-IR光谱图一致。涂层红外光谱中,1222 cm-1 和1160 cm-1 处为C-F 键吸收峰,添加石墨烯后,3461 cm-1处的-OH吸收峰几乎完全消失,这是树脂固化的结果,且由于石墨烯表面的基团含量较少,对氟碳树脂的化学结构影响小,且石墨烯与氟碳主要以物理混合的方式共存,因此涂层红外光谱无明显变化。
2.2 结合强度和接触角
复合涂层的结合强度和接触角测试结果如图3所示,随着石墨烯的添加,结合强度和接触角均表现为先增大后减小的趋势。
结合强度在G 含量为0.05wt%时达到最大(12.47 MPa),相比氟碳涂层提高了44.33%,接触角变化较小,由76.76°提高到82.52°,复合涂层的疏水性有所提高。这是由于G具有疏水性,且层状分布的G可以填充涂层缺陷,增大涂层致密度,提高涂层的疏水性;且G具有极大的比表面积,能增大树脂与基体接触面积,从而提高与基体的结合力。但G含量过高时,易在自身层间作用力下团聚,导致涂层内部缺陷增多,破坏了涂层的结构和性能,降低了涂层的接触角和结合强度。对于涂层而言,亲水性使水溶液容易润湿接触面,增加了腐蚀介质渗透进涂层的机会,接触角的增大表明涂层表面疏水性的提高,有利于延缓水溶液的渗透;当水等腐蚀溶液通过扩散渗入到基体表面后,腐蚀产物的堆积扩散使涂层发生起皱鼓泡,扩大金属腐蚀区域,而较高的结合强度使溶液扩散困难,提高了涂层的抗渗性,降低了腐蚀扩展范围,使未渗透部分仍能受到涂层的保护,因此提高涂层的接触角和结合强度有利于增强涂层长期防腐作用。
2.3 腐蚀防护性能
2.3.1 盐雾试验
破损涂层中性盐雾试验165 h后的结果如图4所示。FT、FT-G1和FT-G15复合涂层破损处腐蚀情况明显比FT-G5涂层严重,腐蚀产物在缝隙处大量堆积甚至导致涂层剥离,且破损区域以外的部分有明显吸水鼓泡现象。FT-G1涂层的鼓泡面积大于其他涂层,而FT-G5仅发生轻微腐蚀。这是因为FT-G5涂层与基底金属的结合强度较高,抗溶液扩散渗透能力强,提高了破损涂层在盐雾环境中的耐蚀性能。
完整涂层盐雾试验720 h 后的结果如图5 所示,圈中部分为涂层发生明显点蚀部分。实验中发现FT、FT-G1、FT-G15在120 h时均开始有少量微孔点蚀产生,且随盐雾试验时间延长不断增大增多。而FT-G5涂层的点蚀区域明显少于其他涂层,表明其耐蚀性最好。FT-G15涂层的点蚀区数量最多,说明石墨烯含量过高对涂层的耐蚀性有不利影响。这是因为在有机涂层中添加适量石墨烯后,一方面,尺寸极小的石墨烯可以填充涂层孔隙,增加涂层致密性;另一方面,石墨烯片状结构则可以起到物理屏蔽作用,阻碍腐蚀介质在涂层中的渗透,石墨烯的强疏水性对水分子在涂层中的渗透也起到进一步阻碍作用,从而提高涂层的防护性能;而石墨烯含量过多时,由于层片间的相互作用而容易发生团聚,在涂层中形成孔洞、缝隙等缺陷,盐溶液可以通过涂层缺陷渗透到基体,造成金属的腐蚀,从而不利于金属的腐蚀防护。
2.3.2 涂层开路电位分析
图6为复合涂层开路电位(OCP)随实验时间变化曲线,可以看出,各涂层体系的OCP均不断降低,发生腐蚀的趋势不断增大。在涂层中添加G 后,FT-G1涂层OCP在实验初期高于FT涂层,但实验到288 h后两者的OCP相接近,在实验720 h后降低到-350 mV左右,FT-G5涂层OCP在浸泡初期高于0 mV,随后不断下降,在实验720 h后保持在-300mV以上,而当G含量达到0.15wt%时,OCP在初期与FT涂层相近,在288 h后急剧的下降,最终下降到-473 mV,腐蚀趋势增加,OCP较正的FT-G5涂层的腐蚀倾向低于其他涂层。
2.3.3 涂层阻抗谱分析
图7 为FT 涂层和FT-G 复合涂层在3.5wt%的NaCl中浸泡不同时间的EIS图,可以看到,FT涂层和FT-G1涂层在实验6~168 h阶段,Nyquist图呈现半径不断缩小的双容抗弧特征,具有两个时间常数,这是由于溶液快速渗透到涂层/金属界面,涂层电阻不断减小,金属发生腐蚀;随着浸泡时间的延长,涂层/金属界面的腐蚀产物逐渐堆积,扩散过程受到阻滞,在Nyquist图中表现为低频区出现War-burg扩散尾。由于FT-G1复合涂层的石墨烯含量较低,对涂层的腐蚀防护性能影响较小,因此与纯氟碳涂层表现相近。随着石墨烯含量的进一步增加,复合涂层的耐蚀性明显提高,FT-G5涂层在6~288 h阶段的Nyquist图表现为单容抗弧特征,说明溶液向涂层的渗透受到较大的阻碍,涂层具有良好的防护作用,随后出现的双容抗弧表明溶液逐渐渗透到涂层。金属表面形成的腐蚀微电池使基体发生腐蚀,但涂层仍保持完整,具有一定防护作用。
当石墨烯含量达到0.15wt%时,整个实验过程中,Nyquist图均为高频容抗弧和低频Warburg 阻抗的组合,这一方面是由于含量较高的石墨烯发生了团聚,另一方面则因为石墨烯的比表面积很大,当其含量较高时,其吸油量很大,树脂不能很好覆盖和浸润石墨烯,使涂层中的孔隙等缺陷增多,溶液向涂层内部的渗透通道增加,导致溶液的扩散速率增大,金属腐蚀较快,在浸泡168 h时即出现锈点。因此,在氟碳树脂中添加适量石墨烯时,柔韧性良好的石墨烯与树脂分子链相互作用,层状叠加的石墨烯延长了腐蚀介质的传输通道,使涂层力学性能和屏蔽性能得到增强,但是过量的石墨烯增加了涂层缺陷,反而不利于金属的腐蚀防护。
采用图8所示的等效电路作为物理模型对EIS图进行拟合分析,可以得到溶液电阻Rs、涂层电容Qc、涂层电阻Rc以及涂层下金属腐蚀反应的电荷转移电阻Rct、双电层电容Qdl等信息,另外当出现扩散尾时引入Warburg阻抗Zw来拟合。拟合发现,对于FT涂层和FT-G1复合涂层,在6~168 h阶段、288~720 h分别用图8(b)和图8(c)中的等效电路进行较好的拟合,而FT-G5涂层EIS图在6~288 h和360~720 h阶段分别用图8(a)和图8(b)进行拟合,FT-G15用图8(c)所示电路拟合较好。由于涂层电阻(Rc)和电荷转移电阻(Rct )可用来表示涂层对金属基体的防护性能,因此通过分析Rc和Rct来研究涂层的防腐蚀性能。
图9 为拟合所得的Rc 和Rct,可以看到,FT-G5涂层的Rc和Rct远高于其他涂层,表明石墨烯含量为0.05wt%的复合涂层具有最佳的腐蚀防护性能。值得注意的是,FT-G5 涂层的Rc 和Rct 在初期快速下降,随后分别保持在107 Ω·cm2和108 Ω·cm2以上,这可能是由于涂层阻抗较高时,腐蚀介质在涂层中的渗透对涂层电阻的影响较明显,导致涂层电阻和电荷转移电阻的急剧下降;其他涂层的Rc和Rct变化相对较小,但在360 h后Rc均低于106 Ω·cm2,Rct比FT-G5涂层低2个数量级。可以明显地看到,纯氟碳涂层的Rc和Rct在长时间浸泡后均低于复合涂层,表明添加石墨烯有利于提高涂层的防腐性能,其中含0.05wt%石墨烯的复合涂层腐蚀防护作用最好。
3 结论
(1)在氟碳涂料中添加石墨烯,涂层的结合强度最大提高了44.33%,接触角测试表明复合涂层疏水性有一定的提高。
(2)盐雾试验和电化学实验研究结果显示,添加石墨烯后,涂层的防护性能提高,当石墨烯含量为0.05wt%时,复合涂层体系的开路电位正移,腐蚀倾向降低,涂层电阻和电荷转移电阻比氟碳涂层高2~3个数量级,在实验720 h后仍保持较高值,复合涂层具有优异的防腐蚀性能,石墨烯过量时将导致涂层防腐蚀性能下降。
更多关于材料方面、材料腐蚀控制、材料科普等方面的国内外最新动态,我们网站会不断更新。希望大家一直关注中国腐蚀与防护网http://www.ecorr.org
责任编辑:王元
《中国腐蚀与防护网电子期刊》征订启事
投稿联系:编辑部
电话:010-62313558-806
邮箱:fsfhzy666@163.com
中国腐蚀与防护网官方 QQ群:140808414
免责声明:本网站所转载的文字、图片与视频资料版权归原创作者所有,如果涉及侵权,请第一时间联系本网删除。
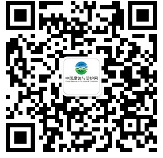
官方微信
《中国腐蚀与防护网电子期刊》征订启事
- 投稿联系:编辑部
- 电话:010-62313558-806
- 邮箱:fsfhzy666@163.com
- 中国腐蚀与防护网官方QQ群:140808414