镁锂合金( magnesium-lithium alloy) 是在镁基体中添加锂元素,其比重介于1. 4 ~ 1. 6 之间,密度较一般镁合金更低,在需要轻量化结构材料的交通、电子、医疗产品等领域展现出广阔的应用前景。但由于镁锂合金的腐蚀电位较低、耐蚀性极差,使用前必须进行适当的表面改性处理。
与普通阳极氧化、化学转化及电镀等技术形成的陶瓷层性能相比,微弧氧化陶瓷层是在弧光放电条件下,由阀金属表面原位生长而来,有着更高的耐磨性和耐蚀性。为了进一步提高微弧氧化陶瓷层的性能,有学者将高硬度碳化硅颗粒、纳米氧化铝等中性物质通过超声作用,均匀分散在电解液中,制备出包覆相应添加剂的微弧氧化陶瓷层。由于高硬度颗粒包覆于陶瓷层之中,极大地提高了微弧氧化陶瓷层的耐磨性。实验基于提高微弧氧化陶瓷层减摩性的目的,通过在电解液中加入石墨烯添加剂,以期制备出含碳的微弧氧化陶瓷层,进而改善其陶瓷层性能。
实验结果表明,在超声和搅拌的作用下,石墨烯添加剂均匀的分散到电解液之中,使得试样表面起弧电压降低30 V 左右、表面放电通道孔径明显减小、并且在17 μm 厚的微弧氧化陶瓷层中检测到碳元素的梯度分布。随后大量的研究工作表明,通过在电解液中加入石墨烯添加剂,制备出含碳的微弧氧化陶瓷层由于放电通道孔径的减小,对其耐蚀性的提高有着明显改善的作用。
本文主要研究了在石墨烯添加剂加入电解液前后,制备的微弧氧化陶瓷层在3. 5% NaCl 溶液中耐蚀性能的变化,以及含碳陶瓷层在两种腐蚀条件下( “浸泡在不同浓度NaCl 溶液中3 h”和“在3. 5%NaCl 溶液浸泡不同时间”) 耐蚀性能,并分析了含碳陶瓷层对提高其耐腐蚀性能的机理。
1 试验材料及方法
1. 1 材料与试剂
试验材料为镁锂合金,试样尺寸为20 mm ×30 mm × 3 mm,其成分为( 质量分数,%) : 5% Li、3. 5%Al、1% Zn、1. 2% Ce、1. 5% Mn、余量为Mg。石墨烯添加剂( 石墨烯分散液) 由北京碳世纪科技有限公司提供,其干粉颗粒度为325 目。微弧氧化前试样需要经过砂纸打磨,去除机械加工时表面形成的氧化皮,并在抛光机上进行抛光,随后在超声清洗机中超声10 min,最后使用热风迅速吹干。将试样与镁丝的一端相连,连接处用高分子液体密封胶覆盖,镁丝的另一端固定在微弧氧化设备( 如图1 所示) 正极支架上,试样作为阳极,不锈钢电解槽作为阴极。
实验所用的电解液为硅酸盐体系,其各组分含量分别为: 硅酸钠( 10 g /L) ,氢氧化钾( 5 g /L) 、十二烷基苯磺酸钠( 3 g /L) 、石墨烯添加剂( 5 mL /L) 。采用WHD-60D 型单极性微弧氧化脉冲电源。输出参数为: 电流2 A、占空比50%、频率500 Hz、处理时间30 min。电解液温度保持25 ℃、电解液pH 值为12。石墨烯添加剂的含量分别为0 mL /L 和5 mL /L。
1. 2 试验检测
采用SSX-550 型扫描电子显微镜观察了陶瓷层截面形貌; 采用X 射线能谱仪对微区元素进行点扫描; 采用EPMA-1600 型电子探针对陶瓷层截面进行线扫描分析; 采用D8 FOCUS—X 射线衍射仪对陶瓷层物相组织进行检测分析; 采用电化学工作站对陶瓷层的耐蚀性进行了检测并讨论。电化学实验采用三电极体系,试样为工作电极,饱和甘汞电极作为参比电极,铂电极作为辅助电极。试样表面裸露出面积为1 cm2,分别检测在两种腐蚀条件下,陶瓷层的耐蚀性能。采用CS360 型电化学工作站检测试样的动电位极化曲线,扫描电位( 相对开路电位) - 0. 1 ~ 0. 1 V,扫描速率为0. 5 mV/s。
2 结果与讨论
2. 1 表面形貌及物相分析
图2 为镁锂合金经微弧氧化处理后陶瓷层表面SEM 形貌照片。由图2( a) 可以看出未加入石墨烯添加剂制备的试样表面形貌如同火山喷发并堆积而成,陶瓷层表面微孔尺寸在1. 5 ~ 2. 5 μm 之间,孔径尺寸变化大,分布不均匀且在放电微孔处有裂纹产生。而由图2( b) 可以看出加入石墨烯添加剂( 5 mL /L)后制备的试样表面微孔大小趋于均匀,尺寸在0. 5 μm 左右,孔径尺寸变小且没发现有裂纹产生。在恒流工作模式下,由于石墨烯添加剂的加入,使得起弧电压降低30 V 左右,这样单脉冲击穿陶瓷层的能量降低,表现为试样表面放电通道分布均匀,孔径尺寸减小。
XRD 衍射图谱如图3 所示。由图可知,镁锂合金基体主要有Li、Li3Mg7、Li3Mg17、LiAlSi4O10物相组成。未加入石墨烯添加剂制备的试样表面Li3Mg7和Li3Mg17物相相对峰值较基体有所降低,且多出MgO、Mg2 SiO4以及SiO2 3 种物相。微弧放电过程中产生的热能,可使微区的固态镁瞬间发生熔融,Mg 原子通过放电通道向基体/陶瓷层界面处迁移,与吸附在界面处的O 原子结合形成MgO。而在高温和碱性环境条件下,使得生成的SiO2和MgO 熔融并发生反应,最后在溶液的冷淬作用下,熔融氧化物转变为MgO和Mg2 SiO4的混合物。与其相比,加入石墨烯添加剂后制备的试样MgO 物相的相对峰值较高,并且又出现了新的Mg2 SiO4衍射峰,表明陶瓷层中MgO 和Mg2 SiO4物相含量在逐渐增多。说明石墨烯添加剂的加入在降低起弧电压的同时,也促进了陶瓷层中MgO 和Mg2 SiO4物相含量的升高。
2. 2 截面形貌及线扫描分析
图4( a) 和4( b) 分别为电解液中石墨烯添加剂含量为0 和5 mL /L 时,所制备的试样经金相腐蚀后的截面SEM 照片。可以看出,镁锂合金基体的显微组织由浅色长条状的富镁α 相固溶体和深色β 相固溶体组成。陶瓷层主要有疏松层( 1) 和致密层( 2)组成。两者的疏松层厚度均约为8 μm,但图4( b) 试样疏松层中因微弧放电而产生的微孔尺寸明显小于图4( a) 试样,这是由于石墨烯添加剂的加入,使得终止电压降低,减小了单脉冲放电的能量,故而产生的微孔尺寸较小,这也与陶瓷层表面微孔尺寸的变化趋势相同。而图4( a) 试样疏松层内部存在尺寸较大的微裂纹和颗粒,这是因为在疏松层形成过程中,由于表面微弧放电产生瞬间高温烧结作用以及电解液的急速“冷淬”作用,使得陶瓷层外层产生较大过冷度,内应力来不及释放,便造成疏松层内部生成大量微裂纹。此外,图4( b) 试样的致密层厚度约为10 μm,明显厚于图4( a) 试样的厚度5 μm,并且,其致密层中并无发现明显的微裂纹产生,这首先是由于电解液的“冷淬”作用对致密层的影响相对较小,其次是石墨烯添加剂的加入,降低了单脉冲微弧放电的能量,促进并保持了致密层的生长。
图4( c) 为试样陶瓷层截面线扫描( AB 线) 元素含量分析,其中0 ~ 8 μm 段,C 元素来自镶嵌粉( 成分主要为有机物) ,故其含量较高。在8 ~ 25 μm 段( 陶瓷层) ,Si 和O 元素均有先上升后降低的趋势,其主要来自参与氧化反应的电解液; Mg 元素含量逐渐升高,最终趋于基体Mg 元素的含量值; C 元素含量逐渐降低并趋近于零。微弧氧化反应一旦开始,将在放电通道内部产生瞬间高温高压,将基体熔融并喷射出的熔融物,在电解液“冷淬”作用下迅速凝固,并将部分石墨烯包覆在陶瓷层中,使得放电通道附近局部区域的陶瓷层厚度增加。此外,石墨烯在超声分散的作用下弥散分布于电解质溶液中,由于其表面能较大,能够吸附电解液中电子,而使本身带上负电。在强电场作用下,其能够随电解液沿放电通道进入陶瓷层内部并参与到陶瓷层生成的反应之中。
2. 3 耐蚀性研究
图5 为不同试样在质量分数3. 5% 的氯化钠溶液中浸泡3 h 测得的极化曲线,其计算结果如表1 所示。未加入石墨烯添加剂制备的试样自腐蚀电位相比原始试样提高0. 13 V,其腐蚀电流密度减小6 倍左右。加入石墨烯添加剂制备的试样自腐蚀电位相比原始试样提高0. 26 V,其腐蚀电流密度减小10 倍左右。其结果表明,通过在电解液中加入石墨烯添添加剂,在降低起弧电压的同时,能够降低单脉冲击穿陶瓷层的能量,减小放电通道尺寸,使得腐蚀液离子渗入陶瓷层的阻力变大,进而明显提高的陶瓷层耐蚀性。其次,放电结束之前,在熔融物从孔道喷出之后,弥散分布于电解液中的石墨烯随电解液进入放电通道,并迅速凝固,对腐蚀液离子的渗入也起到一定的阻碍作用。
图6 为加入石墨烯添加剂后制备的试样在不同质量分数( 3. 5%、5%、7. 5%、10%) 的氯化钠溶液中浸泡3 h 时间下测得的动电位极化曲线,其计算结果如表2 所示。由图可知,随着氯化钠溶液浓度的升高,试样自腐蚀电位由- 1. 61 V 降低到- 1. 63 V。
其腐蚀电流密度逐渐升高,当NaCl 溶液浓度10%时,腐蚀电流密度达到最大值8. 70 × 10 - 03 mA/cm2,其值增大了将近40 倍,明显加快了试样的腐蚀损坏。表明随着Cl - 离子浓度的升高,Cl - 在陶瓷层中的渗透扩散速度加快,降低了陶瓷层的自腐蚀电位,加速了腐蚀介质对基体的腐蚀破坏。分数3. 5% 的氯化钠溶液中,不同浸泡时间下测得的动电位极化曲线。其计算结果如表3 所示。由图可知,随着浸泡时间的延长,试样的自腐蚀电位逐渐降低,由- 1. 56 V 降低到- 1. 63 V,自腐蚀电位降低了约0. 07 V。其腐蚀电流密度逐渐升高,由浸泡3 h 时的2. 28 × 10 - 04 mA/cm2,升高到浸泡96 h 时的2. 92 × 10 - 03 mA/cm2,提高了10 倍左右,明显会加快腐蚀介质对基体腐蚀。年腐蚀速度也增大了近15 倍左右。
图8 为加入石墨烯添加剂后制备的试样在质量分数3. 5%的氯化钠溶液中,浸泡不同时间后的表面形貌图。表4 为能谱仪测得图8( a) 、8( b) 、8( c) 中A、B、C 三处点元素含量。由图8( a) 可以看出,在腐蚀初期,试样表面看不到任何腐蚀附着物,但有几条腐蚀裂纹产生。由8( a) 内嵌放大图可以看出,腐蚀裂纹是由在放电微孔处开始萌生,并逐渐向四周扩展延伸。其中A 处元素含量以Mg、Si、O 为主,没检测到Cl 元素,说明腐蚀初期,主要产生腐蚀裂纹,并没有产生腐蚀产物。随着腐蚀时间延长至12 h,裂纹的数量和尺寸逐渐增大,使得疏松层开始发生脱落。由8( b) 内嵌放大图看出,疏松层表面附着大量腐蚀产物。测得B 处含有大量Cl 元素,说明其为腐蚀产物。
疏松层和腐蚀产物的脱落,导致腐蚀液中的Cl - 离子渗入致密层的速度加快,使得腐蚀裂纹深度增加,逐渐延伸到致密层中。当腐蚀时间达到96 h 时,试样表面块状腐蚀产物已经发生脱落。测得C 处Cl 元素含量为2. 00%,表明Cl - 已经渗入到基体表面,开始腐蚀基体。如图8( c) 所示,疏松层已完全脱落,内部致密层也受到严重腐蚀。通过在电解液中加入石墨烯添加剂,在一定程度上改变了电解液的电导率、粘度等参数,这就降低了试样表面起弧电压,减少了单脉冲放电能量,并且微弧放电微区分布趋于均匀,使得生成的膜层致密层微孔尺寸较小,且无明显微裂纹产生,对腐蚀液离子的渗入阻碍较大。此外,由于微弧放电瞬间高温作用,微孔周围电解液迅速蒸发,在对流传质和扩散迁移的作用下,石墨烯添加剂一部分参与到膜层的生成反应之中,虽未改变膜层表面结晶相的类型,但改变了膜层表面个元素的相对含量; 另一部分伴随电解液进入放电通道,随着温度的迅速降低,石墨烯添加剂便已颗粒物的形式存在于放电通道之中,对腐蚀介质离子的渗入起到明显的阻碍作用,进而改善了微弧氧化膜层的耐蚀性能。
3 结论
1) 通过在微弧氧化电解液中加入石墨烯添加剂,降低了起弧电压,并制备出含碳微弧氧化陶瓷层。其陶瓷层表面放电微孔尺寸仅为0. 5 μm 左右,相比不加入石墨烯添加剂制备的试样的孔径尺寸明显降低;
2) 陶瓷层表面主要由Li3Mg7、Li3Mg17、Mg2 SiO4以及MgO 等物相组成,由于石墨烯添加剂的加入,促进了Mg2 SiO4以及MgO 等物相的形成,提高了其在陶瓷层中的含量;
3) 极化曲线计算结果表明,含碳陶瓷层明显提高了其自腐蚀电位,降低了电流密度和腐蚀速度。而且,陶瓷层在高浓度的Cl - 离子溶液中腐蚀较快,随着浸泡时间延长,Cl - 离子不断深入到陶瓷层内部,造成了基体的腐蚀。
更多关于材料方面、材料腐蚀控制、材料科普等方面的国内外最新动态,我们网站会不断更新。希望大家一直关注中国腐蚀与防护网http://www.ecorr.org
责任编辑:王元
《中国腐蚀与防护网电子期刊》征订启事
投稿联系:编辑部
电话:010-62313558-806
邮箱:fsfhzy666@163.com
中国腐蚀与防护网官方 QQ群:140808414
免责声明:本网站所转载的文字、图片与视频资料版权归原创作者所有,如果涉及侵权,请第一时间联系本网删除。
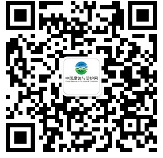
官方微信
《中国腐蚀与防护网电子期刊》征订启事
- 投稿联系:编辑部
- 电话:010-62313558-806
- 邮箱:fsfhzy666@163.com
- 中国腐蚀与防护网官方QQ群:140808414