0 引言
核能作为世界上公认的清洁能源,有高效、安全和经济的特点,是缓解当前水资源和煤电短缺的重要资源。锆合金因热中子吸收截面小, 力学性能及耐腐蚀性能优良而作为核电站反应堆元件的包壳材料及其它堆内材料。为了降低核反应堆循环成本、延长设计使用寿期、提高热循环效率及降低压水堆冷却剂温度,对锆合金的耐腐蚀及抗高温氧化性能提出了更高的要求。锆合金表面改性可赋予锆合金在工作介质中耐高温、防腐蚀、耐磨损、抗疲劳、防辐射、导电、导磁等各种特性,对提高锆合金可靠性,延长核反应堆使用寿命具有很大的经济意义和推广价值。
锆合金表面涂层是提高抗高温氧化腐蚀性能的有效措施。热障涂层、MCrAlY包覆涂层、铝化物涂层、改进的铝化物涂层等是改善锆合金抗高温氧化腐蚀性能主要的几种涂层,这些涂层往往比锆合金基体有着更优越的性能,其中包括塑性、韧性、硬度、耐腐蚀性、抗腐蚀性等。
1 热障涂层
热障涂层是一层陶瓷涂层,它沉积在耐高温金属或超合金的表面,热障涂层对于基底材料起到隔热作用,降低基底温度,因而制成的器件能在高温下运行。
锆合金在核反应堆内高温、高压水环境下易与水蒸气发生反应Zr+2H2O=ZrO2+2H2↑,产生的氢气在高温环境中容易引发“氢爆”,造成核安全事故,而陶瓷涂层高强度、高硬度、耐磨损、耐高温、抗氧化、抗腐蚀和化学性能稳定等特性可解决上述状况。例如碳化硅陶瓷涂层,具有耐高温、耐腐蚀和优良的核反应堆内性能,在锆合金表面沉积SiC涂层可有效隔绝水与锆包壳管在堆内环境下吸氢和腐蚀。王美玲等在锆合金表面制备碳化硅涂层,涂层与基体紧密结合,界面没有空洞和裂纹,涂层颗粒细小均匀,电化学腐蚀实验表明碳化硅涂层明显改善了锆合金的耐腐蚀性能。锆包壳管综合性能的提高取决于涂层的抗高温氧化、腐蚀、高温结构稳定和涂层表面致密、孔隙率低及涂层基体良好的结合性能、热膨胀系数相匹配等性能。文献 在锆合金表面制备Ti 3 SiC2和Ti 2AlC涂层, 并在1100~1300 ℃范围内进行抗氧化实验。在高温氧化过程中,涂层中Si、Al元素与基体进行互扩散形成Zr-Si、Zr-Al等金属间化合物,涂层与基体的结合强度显着提高,涂层具有优良的抗高温氧化效果。文献[7]为提高锆包壳管在核反应堆环境下的抗高温氧化及腐蚀性能,在锆合金表面制备硅和铬涂层。涂层中硅元素在高温下形成的玻璃形态SiO2填补了涂层中孔隙,增加了锆合金基材与涂层之间的结合强度,降低了氧及腐蚀液进入涂层速率,大大提高了锆合金耐蚀性能。
2 MCrAlY包覆涂层
MCrAlY包覆涂层成分可按要求控制,且兼顾腐蚀性与力学性能,另外,涂层对基体合金力学性能影响较小,涂层较厚等特点。MCrAlY涂层,其中M为Fe、Ni、Co以及它们的组合等元素。
MCrAlX包覆涂层中大量的铬元素在氧化过程中形成MCr2O4尖晶石结构氧化物等强阻挡层,使涂层具有优良的抗高温氧化、耐热腐蚀等性能。A12O3和Cr2O3通常被认为是防护效果较好的两种膜层。当温度升高达到1000 ℃时,Cr2O3氧化成挥化性的CrO3,失去保护性能,因此高温下,涂层要求能生成连续完整的A12O3膜。核反应堆高温、高压蒸汽环境中,包壳管主要破坏形式为高温氧化及热腐蚀,因此要求包壳管涂层中含Cr量较高。涂层中的Al元素主要以A12O3形式存在。但Al含量过高会导致涂层脆性增大,延性-脆性转变温度高等缺陷,过低则不能形成连续致密的氧化膜,涂层抗氧化性能得不到明显提高。合金中加入活性元素是为了提高氧化膜的黏附性,改善其氧化性能和腐蚀性能。活性元素Y、Ce、La等在合金中的溶解度很低,加入过多时会在晶界处偏聚,降低其抗高温氧化和热腐蚀性能。利用磁控溅射在锆合金表面沉积原子比不同的4种FeCrAl涂层(Fe/Cr/Al= 53/29/18 at%,62/4/34 at%,71/7/22 at%,86/10/4 at%),涂层厚度为0.3~1 μm,在700℃进行高温蒸汽实验,并与未涂层锆合金试样进行对比。
氧化增重数据显示前三种涂层对锆合金的抗高温氧化及腐蚀性能有显着的提升,而Fe/Cr/Al原子比为86/10/4 at%的涂层试样,因Cr、Al含量相对较低,氧化严重。FeCrAl涂层试样在高压釜(模拟沸水反应堆环境)实验20 d膜层依然完好,在1100 ℃的高温蒸汽中,由于FeCrAl涂层中Fe元素与基材锆合金形成了Fe-Zr共晶相导致了涂层的完整性被破坏。
3 铝化物涂层
铝化物涂层工艺简单、性能稳定、成本低,可满足一般的性能要求等特点,具有优异的抗高温氧化和硫化性能。在锆合金表面渗铝,随着铝含量的不同,铝元素与锆基体形成多种共晶化合物(如图1),其中一些共晶化合物(如Zr-Al相)能大幅度提高锆合金的抗高温氧化腐蚀性能,自20世纪中期以来铝化物涂层在抗高温氧化方面被大量研究应用。
铝化物涂层虽具有上述优点,但涂层和基体之间的元素互扩散导致涂层退化现象严重,成分不能按要求控制,抗热腐蚀性能不足,对基材力学性能影响大。A12O3膜在高温环境服役时很容易从合金表面剥离,涂层中的铝消耗很快,导致抗氧化能力的丧失。高温氧化过程中Al涂层中的Al因向基体扩散而逐渐贫化,涂层的热稳定性随之降低。
为改善铝化物涂层耐腐蚀性能,在铝化物涂层中加入Cr、Si、Ti、Pt等元素可解决上述铝化物涂层的不足。渗铝层在高温氧化过程中铝元素与氧结合形成连续致密的α-Al2O3保护膜,可将合金抗氧化温度提高约200℃。利用反应非平衡磁控溅射制备铝含量不同的(CrxAll-x)N复合涂层。结果表明,CrN中AlN的最高含量为77.2%。CrAIN薄膜中AIN的含量为75%时涂层的相结构将由B1(即NaCI结构)转变为B4(六方)结构。随着铝含量的逐渐增加,薄膜结构逐步转变为立方结构,择优取向为(111)方向。涂层硬度随之增加,从18 GPa到30 GPa,当铝含量超过某一临界值时,硬度值缓慢下降。铝元素的注入,使得(CrxAl1-x)N薄膜的耐磨性能得到了极大提高,其耐磨性是CrN涂层的近6倍。(CrxAl1-x)N涂层其抗氧化温度达到了900 ℃,具有极好的高温抗氧化性能。
文献简述了铬铝涂层中铬含量对涂层的抗高温氧化性能的影响,Al-Cr涂层加入Cr使涂层内富含铬形成扩散层,减少铝的二次扩散,固溶在β-MAX相的Cr可以防止β在快冷时发生的马氏体转变,Cr元素的存在会降低Al氧化形成A12O3的临界含量,从而能显着提高涂层的高温抗氧化耐腐蚀性能。当Al-Cr涂层中Cr的含量过低时,Cr固溶于涂层中,既不能有效地抑制基体界面Cr的偏析,又增加了涂层的微观缺陷,导致抗氧化性能不理想。Al-Cr涂层中适量的Cr可以抑制基体中的Cr在基体表面偏析,阻止基体向不稳定相的转变,涂层的抗氧化性能随之显着地提高。采用磁控溅射在锆合金表面制备AlCr涂层,结构平坦、组织致密, 颗粒细小,氧化膜均匀,高温下Al元素形成的Al2O3氧化膜致密坚固, 不具有挥发性,Cr2O3氧化膜与Al2O3氧化膜的紧密结合提高了锆合金在反应堆中的高温抗氧化性能。改进的铝化物涂层,既保留了铝化物涂层优异的抗高温氧化性能,同时Cr加入形成的连续致密的Cr2O3具有显着耐高温腐蚀作用,阻碍了锆合金的腐蚀氧化。在Zr-4合金表面利用多弧离子镀制备2~4μm的TiAlN和AlCrN涂层,涂层表面均匀,无明显缺陷,涂层与锆合金结合紧密,Ti、Al、Cr高温氧化过程中分别与氧结合形成的氧化物对锆合金高温耐腐蚀及氧化起到了阻碍作用。文献采用冷喷涂技术在Zr-4 合金表面制备Ti2AlC涂层,在700 ℃氧化60 min,并与基体对比发现,Ti2AlC涂层表面形成了Al2O3等连续致密的氧化膜,阻碍了涂层内部及基材氧化,涂层锆基合金氧化速率显着降低。
4 展望及建议
多种单质元素的加入可显着改善合金使用性能,为添加多种物理性能相差较大元素来提高综合性能涂层的制备提供了思路;在锆合金表面制备含有某些单质元素的涂层,涂层进行原位反应是提高锆合金基材抗高温氧化腐蚀性能应重点研究的方案。单质元素比合金元素在原位反应中更易与锆合金基材形成稳定新相,对涂层抗高温氧化及热腐蚀具有重要的研究意义。多种元素涂层在高温条件下某些元素选择性氧化,生成一层致密氧化膜阻挡氧、氢、硫等破坏性,元素进入到涂层和基体可有效隔绝锆合金在水环境下的腐蚀和吸氢,延长反应堆包壳材料的使用寿命,同时减少严重事故的发生,对延长燃料寿命、增加堆芯的安全性具有重要意义。
更多关于材料方面、材料腐蚀控制、材料科普等方面的国内外最新动态,我们网站会不断更新。希望大家一直关注中国腐蚀与防护网http://www.ecorr.org
责任编辑:王元
《中国腐蚀与防护网电子期刊》征订启事
投稿联系:编辑部
电话:010-62313558-806
邮箱:fsfhzy666@163.com
中国腐蚀与防护网官方 QQ群:140808414
免责声明:本网站所转载的文字、图片与视频资料版权归原创作者所有,如果涉及侵权,请第一时间联系本网删除。
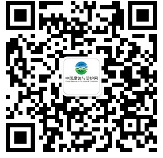
官方微信
《中国腐蚀与防护网电子期刊》征订启事
- 投稿联系:编辑部
- 电话:010-62313558-806
- 邮箱:fsfhzy666@163.com
- 中国腐蚀与防护网官方QQ群:140808414