0 引言
【研究意义】较之大量在海洋开发中应用的钢铁,锌因具有较负的电位而被广泛应用于海洋钢结构的防腐。如用于阴极保护的锌阳极、热浸锌、热喷涂锌、电镀锌、防腐涂料的富锌涂料、冷镀锌等。世界锌产量的 50% 以上被用于钢铁的防腐 。热浸锌和富锌涂料是最早用于海洋的防腐方法,该方法在长期使用中显露出的缺点在新近发展的冷镀锌方法中得到克服。其中,热浸锌、冷镀锌和富锌涂料 3种锌防腐方式在海水中表现不同,彼此间有着明显差异。因此,研究这 3 种锌防腐层在海水中的腐蚀性能和防污性能具有十分现实的意义。【前人研究进展】锌在防腐领域的应用最早是 1815 年作为牺牲阳极被提出。通常认为 1828 年戴维提出的船底铁皮连结锌块可以使铁得到保护,是海洋阴极保护的萌芽。锌阳极在第一次世界大战中得以应用,第二次世界大战已成为成熟的保护技术 。金属镀层技术始于 16 世纪,古罗马人把铁件浸入熔化的锡中制造出镀锡制品,后人称为“马口铁”。法国化学家Melouin 熔化金属锌,发明了热浸锌工艺。 1836 年法国人 Somel 把热浸锌技术用于工业生产 。经过多年的改进,热浸锌技术早已自动化、标准化、商业化 。20 世纪 30 年代澳大利亚人在水玻璃中加入锌粉,经热烘干发明富锌涂料。美国人在 50 年代发明的固化型技术无机富锌涂料在二战中被广泛应用 。随着近代科技的发展,富锌涂料中的锌粉提纯到 4 个 9 的高纯度(99.995% ),而颗粒直径仅为3~5 μ m ,使其在富锌涂料中的堆积更加密实,锌粉在富锌涂料中的干膜含量达到 96% 以上,这些性能使富锌涂料被应用于现今新型环保且维修极为方便的防腐技术,即冷镀锌技术。通过不同方法,把锌附着在海洋钢结构上,使钢铁得以保护,前人已有研究 。【本研究切入点】探讨热浸锌、冷镀锌和富锌涂料 3 种锌防腐层在天然海水中的腐蚀与防污性能优势差别。【拟解决的关键问题】将 3 种不同锌防腐钢板在青岛中港进行对比试验,研究其对海洋生物污损的控制及其防腐效果。
1 材料与方法
1.1 材料取 普 碳 钢 ( M60 ) 3 块 加 工 成 600 mm ×60mm×5mm (一端打孔 φ 18mm ),其中 1 块涂富锌涂料(JR - FX ), 1 块进行热浸锌处理, 1 块进行冷镀锌处理。
1.2 热浸锌试板制备制备过程参照文献进行:( 1 )抛丸———去除钢铁试板上的锈污,依钢铁试板上的锈层厚度不同,清除时间不同。除净锈污后,钢铁试板表层呈银灰色。(2 )酸洗———以 18% ( V / V )的稀盐酸,加入六次甲基四胺缓冲剂,配置成酸洗液。把试板吊入酸洗液中,约 8~10min 。(3 )水洗———试板经过酸洗后,盐酸等会残留在上面,必须用水清洗干净。(4 )浸锌———用葫芦岛 60 号出口锌(纯度 99。99% )熔化成锌液(500℃ 左右),把试板浸入锌液中,使其均匀附上 锌 层。(5 )漂 洗———浸 锌 后 的 试 板 用 2%( W / V)的NH 4 Cl 溶液进行漂洗。
1.3 冷镀锌试板制备
1.3.1 镀层液制备JP1618 型冷镀锌的镀层液制备:先把 JP - SZ - 20型树脂液加入活动桶,启动高速分散机,在 300r /min 慢速搅拌下,缓慢加入锌粉。锌粉加入完毕后,调整转速至 ≥1 000r / min ,保持搅拌 ≤30min ,搅拌均匀,待涂层液可以在刮板上平整形成涂层时,停止搅拌,过滤保存,得到 JP1618 型冷镀锌的镀层液成品。
1.3.2 试板制备( 1 )对钢铁试板进行机械除锈(喷砂、抛丸等),使其表面清洁度达到ISO 8501 - 1 : 2007 中规定的Sa2。5 级,相当于 GB / T 8923.1 — 2001 中规定的Sa2.5 级。( 2 )将配套的专用稀释剂加入 JP1618 型冷镀锌的镀层液中,搅匀、过滤并稀释,稀释剂与 JP -1618 型冷镀锌镀层液的稀释比为 0.15∶1 。( 3 )使用有气喷涂的方法正面喷涂一层冷镀锌,喷涂时注意喷枪上下左右游走,使喷涂均匀,膜厚为 120 μ m左右。(4 )喷涂完放置 7d ,使涂膜实干。反面喷涂重复上述操作。
1.4 富锌涂料试板制备喷涂前的表面处理和冷镀锌相同,然后将富锌涂料(JP - FX )的双组份按比例混合( A∶B=9∶1 ),将配套的专用稀释剂加入富锌涂料中,搅匀、过滤。
涂装方法同于冷镀锌方法。
1.5 海港试验把 3 块试板通过螺栓紧固到塑料固定装置上制成试验用的试架。 2014 年 4 月 10 日把试架投放到青岛中港海中,使各试板的 3 / 4 浸入海水中,1 / 4 暴露在大气中。分别在浸海 10d 、17d 、 24d 、 58d 、 89d 、 1.5 年后取出,检查全部试板的表观状态并照相记录。 1.5 年后对以上 3 块试板上附着的生物进行分类取样,照相称量,分析主要污损生物群落结构组成,计算主要污损生物间的质量百分比。
2 结果与分析
如图 1 所示,将经过热浸锌、冷镀锌和富锌涂料处理的 3 种试板放入海水中 10~24d ,手触摸 3 种试板表面有粘滑感觉,为微生物粘膜,其中,热浸锌试板未发现可视生物,冷镀锌试板表面有淡绿色粘膜,富锌涂料试板表面有绿色粘膜;3种试板的涂层均完整,无锈迹。浸海58d后,热浸锌试板和冷镀锌试板表面布满浒苔和石莼等海藻,富锌涂料试板表面布满浒苔和石莼,石莼长10~20cm ,阳面多于阴面。浸海89d后,热浸锌试板水线处布满浒苔,水线以下10cm 开始出现密集的小藤壶,并有少量苔藓虫和海鞘;冷镀锌试板水线处布满浒苔,其余被藤壶、海鞘和苔藓虫布满;富锌涂料试板水线以下10cm 被浒苔、石莼布满,其余被藤壶、海鞘、苔藓虫布满。浸海1.5年后,3种试板表面附着以大量的苔藓虫类和藻类为主的污损生物群落。
根据表1可知,浸海1.5年后,热浸锌试板上主要附着有藤壶、浒苔和石莼3种污损生物,其中藤壶为优势种;冷镀锌试板上主要附着有海鞘、牡蛎、石莼、浒苔, 4种主要污损生物在质量比例上相差不大;富锌涂料试板上主要附着有贻贝、马尾藻、石莼、水螅,其中贻贝、水螅、石莼为主要污损生物。对比3种镀锌试板,贻贝在富锌涂料试板上附着最多,水螅仅在富锌涂料试板上附着并且成为优势物种,热浸锌试板和冷镀锌试板上的生物种类以及质量都少于富锌涂料试板。
3 讨论
富锌涂料、热浸锌二者是传统的防腐方法,富锌涂料在海洋重防腐工程中仅作为配套底漆使用,如今常用于海水介质的配套防腐体系是环氧富锌底漆+环氧中间漆+环氧防腐面漆。而热浸锌是金属粒子通过热扩散渗透作用在铁镀件和Zn涂层中间形成Zn - Fe 二元体系的锌合金防腐层,在当今海洋重防腐工程中单独使用。在此基础上,近代研究技术将锌粒子纳米化、高纯度化,称之为锌加技术,形成冷镀锌防腐体系。这 3 种防腐方法根据不同防腐设计目的,可用于不同海洋工程结构防腐中 。
海洋锌保护层的钢结构腐蚀,在锌保护层未破损、钢铁未接触海水之前,是锌的海水腐蚀。热浸锌试板和冷镀锌试板在浸海 1。5 年后,其锌保护层完整、未出现钢铁腐蚀。试板在 1.5 年的浸海过程中是锌受到腐蚀,由于不同海区、不同材料与工艺及试验时间长短等多种不同因素影响,锌在海水中的腐蚀率相差较大 。研究发现,在海水中锌腐蚀初期的产物为 ZnO ,72h 后为 ZnCl 2 和 Zn ( OH ) 2,以后 慢 慢 形 成 稳 定 产 物 ZnCl2 · 4Zn ( OH ) 2 和Zn 5 ( CO 3 ) 2 ( OH ) 6 · H 2 O 。当海水中含硫化物时,海水pH值 >7。2 ,则锌腐蚀产物为 ZnS ,其饱和度较小 。当镀锌层被破坏后,钢铁与海水接触,锌成为牺牲阳极,起到阴极保护作用,此时,锌的腐蚀产物为 ZnO 。
热浸锌和冷镀锌技术在海水/金属界面均有一定浓度的锌粒子存在,而富锌涂料中的锌粒子浓度较小,有机树脂成分在其表面占一定的比例,只有在树脂水解后才能将锌粒子释放,因此富锌涂料海水/金属界面的游离态锌离子浓度远小于热浸锌、冷镀锌海水/金属界面,防污效果明显较低。冷镀锌是经过特殊表面处理的超细锌粉和 JPS2 - 20 石墨烯纳米改性包覆锌的技术 ,确保了涂层干膜中含锌质量百分比达到 96% ,使其对钢铁具有良好的保护性能,然而此种包覆技术降低了锌的防污性能,所以防污性弱于热浸锌。
由于热浸锌是把镀板浸入锌池进行浸锌,所以对产品的尺寸限制比较大,如镀锌厚度不匀或者某些地方无法镀锌,则修补起来比较困难;而冷镀锌是采用喷涂方式形成防腐层,所以相比热浸锌技术,对产品的尺寸限制较小,施工方式较灵活,修补维护方便。以上两种技术的结合,已成为海洋工程重防腐技术的重要方法 。
4 结论
经历1.5年的海港试验,热浸锌试板镀锌层和冷镀锌试板镀锌层完整无裂纹、无锈点,而富锌涂料试板涂层开裂起皮、锈蚀失效,生物污损程度高于热浸锌和冷镀锌镀锌层。同时,经历1。5年的海港试验,热浸锌试板上的生物种类以及质量最少,表明热浸锌对污损生物的 排 斥能 力大 于 冷 镀 锌 和 富 锌涂料。
作者:马士德 1 ,5 ,姚振玲 2 ,廖阳飞 3,赵君 4,韩文 2 ,李博亮 2,周萌 6,张杰 1
(1。中国科学院海洋研究所,山东青岛 266071 ; 2。青岛东启机械设备有限公司,山东青岛266071 ; 3。湖南金磐新材料科技有限公司,湖南长沙 410000 ; 4。海洋化工研究院有限公司,山东青岛 266071 ; 5。中国老教授协会海洋防腐防污专业委员会,山东青岛 266071 ; 6。青岛龙达电器有限公司,山东青岛 266000 )
更多关于材料方面、材料腐蚀控制、材料科普等方面的国内外最新动态,我们网站会不断更新。希望大家一直关注中国腐蚀与防护网http://www.ecorr.org
责任编辑:王元
投稿联系:编辑部
电话:010-62313558-806
中国腐蚀与防护网官方 QQ群:140808414
免责声明:本网站所转载的文字、图片与视频资料版权归原创作者所有,如果涉及侵权,请第一时间联系本网删除。
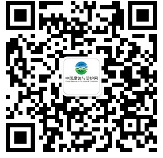
官方微信
《中国腐蚀与防护网电子期刊》征订启事
- 投稿联系:编辑部
- 电话:010-62316606-806
- 邮箱:fsfhzy666@163.com
- 中国腐蚀与防护网官方QQ群:140808414