海洋工程构筑物大致分为:海岸工程(钢结构、钢筋混凝土)、近海工程(海洋平台、钻井、采油、储运)、深海工程(海洋平台、钻井、采油、储运)、海水淡化、舰船(船体、压载舱、水线以上),简称为船舶与海洋工程结构。船舶与海洋工程结构的主要失效形式包括:均匀腐蚀、点蚀、应力腐蚀、腐蚀疲劳、腐蚀/磨损、海生物(宏生物)污损、微生物腐蚀、H2S与CO2腐蚀等等。控制船舶和海洋工程结构失效的主要措施包括:涂料(涂层)、耐腐蚀材料、表面处理与改性、电化学保护(牺牲阳极、外加电流阴极保护)、缓蚀剂、结构健康监测与检测、安全评价与可靠性分析及寿命评估。
从腐蚀控制的主要类型看(表1),涂料(涂层)是最主要的控制方法、耐腐蚀材料次之,表面处理与改性是常用的腐蚀控制方法,电化学保护(牺牲阳极与外加电流)是海洋结构腐蚀控制的常用手段,缓蚀剂在介质相对固定的内部结构上经常使用,结构健康监测与检测技术是判定腐蚀防护效果、掌握腐蚀动态以及提供进一步腐蚀控制措施决策和安全评价的重要依据,腐蚀安全评价与寿命评估是保障海洋工程结构安全可靠和最初设计时的重要环节。建立全寿命周期防护理念,结合海洋工程设施的特点及预期耐用年数,在建设初期就重视防腐蚀方法,通过维修保养实现耐用期内整体成本最小化并保障安全性,是重大海洋工程结构值得重视的问题。
表1 腐蚀防护方法及中国的防腐蚀费用比例
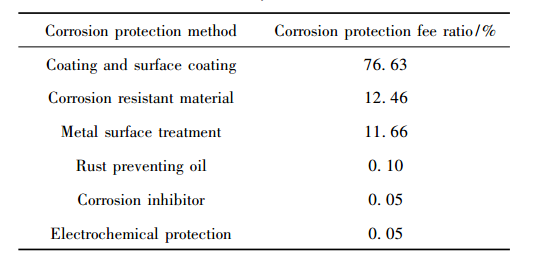
3.1防腐涂料(涂层)
涂料是船舶和海洋结构腐蚀控制的首要手段。海洋涂料分为海洋防腐涂料和海洋防污涂料两大类。按防腐对象材质和腐蚀机理的不同,海洋防腐涂料又可分为海洋钢结构防腐涂料和非钢结构防腐涂料。海洋钢结构防腐涂料主要包括船舶涂料、集装箱涂料、海上桥梁涂料和码头钢铁设施、输油管线、海上平台等大型设施的防腐涂料;非钢结构海洋防腐涂料则主要包括海洋混凝土构造物防腐涂料和其他防腐涂料。
海洋防腐蚀涂料包括车间底漆、防锈涂料、船底防污涂料、压载舱涂料、油舱涂料、海上采油平台涂料、滨海桥梁保护涂料以及相关工业设备保护涂料。海洋防腐涂料的用量大,每万吨船舶需要使用4~5万升涂料。涂料及其施工的成本在造船中占10%~15%,如果不能有效防护,整个船舶的寿命至少缩短一半,代价巨大。
海洋防腐领域应用的重防腐涂料主要有:环氧类防腐涂料、聚氨酯类防腐涂料、橡胶类防腐涂料、氟树脂防腐涂料、有机硅树脂涂料、聚脲弹性体防腐涂料以及富锌涂料等,其中环氧类防腐涂料所占的市场份额最大,具体见表2。实际上,从涂料使用的分类看,涂料可以分为:底漆、中间漆和面漆。其中,底漆主要包括富锌底漆(有机:环氧富锌;无机:硅酸乙酯)、热喷涂铝锌;中间漆主要有环氧云铁、环氧玻璃鳞片;面漆包括聚氨酯、丙烯酸树脂、乙烯树脂等。
表2 我国重防腐涂料的种类与比例
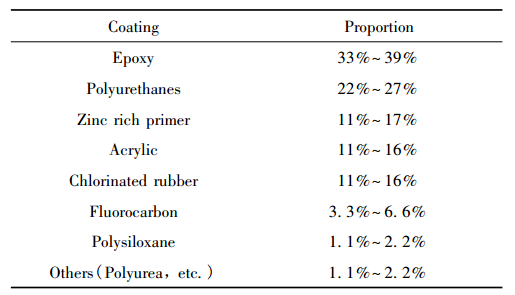
我国重防腐涂料增长率较快,2012年我国涂料总产量1270万t,居世界第一位,但企业数量多,单产低。
我国涂料生产企业有上万家,但产量在5000t以上的涂料企业不足10%。美国涂料年生产总量约700万t,厂家只有400多个。日本是世界第3大涂料生产国,总产量200万t,生产企业只有167家。我国涂料公司的产值低:从企业销售额来看,我国最大的涂料公司的年销售额不足AkzoNobel(阿克苏诺贝尔)公司的1/50。此外,我国许多涂料公司的产品质量还有待进一步提高。我国虽有先进的纳米复合涂料技术,但其产量还需要进一步扩大。
到现在为止,全世界主要重防腐涂料已全部进入中国。在技术要求较高的集装箱和船舶涂料领域,外资和合资企业的产品占据了我国80%以上的市场份额(表3);20世纪90年代末,国际著名的船舶涂料公司基本上都已进入中国,并在中高端市场占据相当大的份额,例如海上石油钻井平台和海上设施所用的重防腐涂料被Jotun(佐敦)、Hempel(赫普)、AkzoNobel、PPG和日本关西等公司所垄断,其中Jotun公司就占有海洋工程领域60%的市场份额;到目前为止,我国95%的船舶涂料市场均为国外公司所垄断。值得欣慰的是,由于中国有先进的纳米技术,最近国外两大海洋涂料公司(Jotun、Hempel)开始批量采购我国的纳米氧化物浓缩浆,并按照指定的工艺制备先进的船舶用纳米复合涂料,已开始应用到船舶中在我国重防腐涂料市场里,曾经我国最大的国营重防腐涂料厂———上海涂料公司麾下的开林造漆厂,采取合资的方法经营,2009年,该厂在这一领域销售额增加10%,其中包括钢结构涂料60%,船舶涂料40%。
表3 2009 年国外涂料企业等在我国重防腐蚀涂料各领域中的市场份额

值得指出的是:船舶涂料不仅技术要求高(例如:压载舱涂料在苛刻环境下工作,且属于关键部位,要符合国际海事组织(IMO)的PSPC标准、有船级社的证书,目前都采用国外产品),更要求满足5年维修寿命,生产企业的资质和认证齐全;同时,船舶涂料的种类多,配套性要好;还需要建立全球售后服务网络(24h到位),方便维护。我国一般的涂料企业都难以达到这些要求,导致我国涂料企业难以进入船舶涂料的市场竞争中,这是我国海洋涂料几乎全面被国外占领的主要原因。
未来海洋重防腐涂料的发展方向是:环保、节能、省资源、高性能和功能化。例如:①低表面处理防锈涂料不但可以减轻表面处理的压力,避免预处理对环境造成的污染,并可节约大量维修费用;②无铅无铬化是无公害高性能防锈颜料和填料的发展方向;③水性无机富锌涂料作为零VOC的环保型水性防腐涂料被广泛应用;④无溶剂涂料是研究的热点,主要有无溶剂环氧涂料、无溶剂聚脲和聚氨酯涂料;⑤纳米粒子的引入可以改善涂料流变性,提高涂层附着力、涂膜硬度、光洁度和抗老化性能,是重要的发展方向之一;⑥超耐候性面漆———氟碳树脂及含氟聚氨酣等改性材料是面漆基料的极佳选择,除用于船壳漆外,还可用于接触强腐蚀介质的内舱涂料等。换句话说,高固体化、无溶剂化(包括粉末涂料化)或弱溶剂化、水性化、无重金属化、高性能化、多功能化、低表面处理化、省资源化以及智能化等是涂料发展的国际趋势。
3.2防污涂料
海水全浸环境中,船舶和钢桩、平台、管线等移动和固定工程设施都不可避免遭受海洋污损生物附着影响,造成生物污损。船体附着的藤壶等污损生物,能使船舶航行阻力增加15%,燃油费上升40%~50%。
防污涂料是海洋涂料中的一个特殊品种,其主要目的是阻止海洋生物对海洋构筑物的附着、污损,保持船底或海洋结构的光滑、清洁。防污涂料无论是基于低表面能、还是自抛光概念,都要在涂料中添加“毒素”———防污剂。传统的防污毒料种类很多,其中无机类包括氧化亚铜(也有其他的铜化合物,如硫氰酸亚铜等)、氧化汞(虽有效但污染环境,早已禁用)、氯化锌(辅助防污剂)等,有机类包括有机锡化合物(三丁基锡TBT或三苯基锡化合物TPT,已被禁用)、有机氧化合物(DDT,它对藤壶有特效,但DDT太稳定,不易降解,污染环境,已在全世界被禁用)。
我国对海生物污损的防护研发起步晚,1966年成立了全国性攻关会战组(跨行业、跨地区,科研、生产、使用3结合),历经15年,缩小了有机锡(TBT)类防污涂料与国外技术水平的差距,但基础材料与关键技术仍远远落后于国外。我国拥有30余万艘近海船舶,过去一直普遍使用含TBT、DDT防污涂料,严重污染了海洋环境。随着世界海洋工业的迅速发展和环境保护法对船舶工业的影响,高污染的涂料将会逐步禁止使用,我国履行国际公约,2008年全面禁止生产和使用含三丁基锡TBT防污涂料,2009年全部停止溶剂法氯化橡胶生产线,2010年全面禁止使用含DDT船底防污涂料,并逐步限制含铬防锈涂料,同时把含氧化亚铜防污涂料列入“高污染、高环境风险”名单,规定氧化亚铜作防污济是过渡性措施。到2025年,北美的小型船舶将禁止使用防污涂料。所以,发展防污涂料的环境友好的替代防污技术显得十分紧迫。
我国对于生物污损的发生机制及基于仿生原理进行防污控制的材料方面开展了一系列研究。先后探讨了硫酸盐还原菌(SRB)为主要构成的生物膜的形成机制,并筛选出了可以对该膜进行溶解破坏的蛋白酶,溶解消除率可达85%以上;研究了表面能、表面结构特征、弹性模量等对生物附着的影响规律,利用化学分子自组装的方法实现了对仿生表面微结构的制备,建立了对防污表面微结构特征进行表征的方法,可以同时满足对石莼孢子和硅藻在不同结构特征表面的附着情况进行预测的要求。
从发展趋势来看,探清影响生物附着发生时与材料表面作用的内在本质因素并发展环境友好防污材料是重点。从本质上看,生物的附着是其分泌的黏附蛋白和材料表面之间的化学结合的过程,所以探清这种吸附界面间的化学作用机理是未来发展的关键。污损生物存在种类多样和附着机制复杂的特点,但是与材料表面接触并通过黏附蛋白与表面结合作用达到足够的附着力是其中的必要条件,因此对环境友好材料的发展应从抑制生物与材料表面的接触,降低黏附蛋白活性结构的吸附作用,使之无法形成足够的附着力等方面来进行考虑。
我国学者利用天然辣素的固有环境友好特性、异噻唑啉酮防污剂的防污活性以及含辣素功能结构树脂(高分子)和丙烯酸锌/铜树脂体系,研发出了环境友好型自抛光防污涂料,在黄渤海、东海、南海3个海区使用,达到12~24个月防污期效,该涂料从技术上打破了国外垄断。近年来,我国学者通过把纳米材料添加到涂料中也表现出良好的耐污性。
目前,防污涂料的寿命已经从3年提高到5年,甚至最近进一步提高到7.5年。从防污涂料的应用状况看,无论树脂体系、防污剂体系、复配技术及市场,国外公司均处于主导地位。我国南海平台容易生长海生物,目前没有特效的长效防污防腐配套体系,有待国内自主开发。
3.3耐腐蚀材料
海洋中使用的耐腐蚀材料包括:耐海水腐蚀钢、耐腐蚀钢筋、双相不锈钢、钛合金、铜合金、复合材料、高分子材料、高性能混凝土等。金属和钢筋混凝土的使用量最大。
耐腐蚀金属材料是通过调整金属材料中的化学元素成分、微观结构、腐蚀产物膜的性质,实现降低电化学腐蚀的反应速度,从而可以显著改善金属材料的耐腐蚀性。
美国从1936年开始研制耐海水腐蚀钢,到1951年研制成功了“Mariner”钢。法国研制出Cr-Al系的耐海水腐蚀钢APS系列。日本的几大钢厂也已研制出不同的系列,如新日铁Mariloy系列钢、JFE海洋系列钢、三菱制钢NEP-TEN50与60、神户制钢所TAICORM50A.B.C。德国研发出HSB55C钢(Ni-Cu-Mo系)。我国从1965年起开始研制耐海水腐蚀钢,主要有Cu系、P-V系、P-Nb-Re系和Cr-Al系等类型,如08PV、08PVRe、10CrPV等,但与国外比较,我国的耐海水腐蚀钢还有待进一步研发。近年来日本已经在船舶上使用免涂装的耐腐蚀钢,已有20多条船采用了耐腐蚀钢,日本在极力推荐使之成为国际标准用钢。此外,运动部件还需要考虑耐腐蚀性与耐磨损性能的相互协调,同时具有耐腐蚀磨损的能力。
3.4浪花飞溅区
包覆技术为了有效控制浪花飞溅区的严重腐蚀,基于把腐蚀介质与材料隔离的原理,日本提出采用局部包覆耐腐蚀蒙乃尔合金、中间填充缓蚀油膏的方法,随后又进一步改进包覆材料,现已经产业规模化应用。我国侯保荣院士通过引进、消化吸收、再创新,把浪花飞溅区包覆技术成功用于我国青岛区域的海洋大桥、近海平台以及海上风电基础部位浪花飞溅区的示范工程中,采用氧化聚合型包覆防腐技术用于螺栓与法兰等异型结构、桥梁的拉索与防水套、风电大气区的焊接部位等的示范工程中,实现了不依靠日本独立使用该项技术进行水下施工。浪花飞溅区保护罩-复层矿脂包覆防腐材料技术采用优良的缓蚀剂成分和能隔绝氧气的密封技术,系统由4层紧密相连的保护层组成,即矿脂防蚀膏、矿脂防蚀带、缓冲层和防蚀保护罩,分成若干个系列,对规则和非规则设施均可以实施保护,目前已制定出企业标准。该技术的有效腐蚀防护效果达30年以上。防蚀保护罩主要是采用玻璃钢或者增强玻璃钢防护材料。如果采用更耐蚀的金属材料(例如钛合金),将使该技术具有更好的防腐性能和耐冲击性能,也将具有更便捷的施工流程。
在众多防腐材料中,钛合金无疑是最佳的选择之一。钛合金强度高、质量轻、耐海水腐蚀性好。我国在钛合金的研究、生产和加工制造方面也都有丰富的经验,特别是近年来,钛合金的价格趋于下降。日本已将钛合金应用于羽田机场跑道钢桩的浪花飞溅区保护。通过进一步对钛合金保护罩在材质、模具和耐腐蚀性等方面的深入研究,完全有可能应用于复层矿脂包覆防腐技术。此外,也初步研发了一种防污胶带材料,这种防污胶带可以直接贴到船舶等设施表面,替代防污涂料。
3.5表面处理与改性表面
改性或称为表面处理,是采用化学物理的方法改变材料或工件表面的化学成分或组织结构以提高部件的耐腐蚀性。化学热处理(渗氮、渗碳、渗金属等)、激光重熔复合、离子注入、喷丸、纳米化、轧制复合金属等是比较常用的表面处理方法。前3种是改变表层的材料成分,中间两种是改变表面材料的组织结构,后者则是在材料表面复合一层更加耐腐蚀的材料。
虽然对于大面积的海上构筑物可以采用重防腐涂料等防护技术,但对于许多形状复杂的关键部件,如管件、阀门、带腔体、钢结构螺栓、接头等复杂结构的零部件,在其内部刷涂层比较困难,传统的防腐涂料无法进行有效保护并很难达到使用要求。因此一方面通过提高材料等级来防腐,例如:使用黄铜、哈氏合金、蒙乃尔合金、钛等金属材料来制作复杂的零部件。另一方面,亟需发展先进的低成本表面处理等防腐技术。例如:随着超深、高温、高压、高硫、高氯和高二氧化碳油气田尤其是海上油气田的相继投产,传统单一的材料及其防腐技术已不能满足油气田深度开发的需要,双金属复合管的应用正在迅速扩大[43],即采用更耐腐蚀的材料作为管道的内层金属实现抗腐蚀。
钛合金密度小、比强度高、可加工性好及耐海水腐蚀性强,是一种优异的船舶材料。常常可用作复合材料的顶层(当然也可以单独使用)以耐腐蚀。然而钛合金较低的耐磨性能、耐高温氧化性能及其对异种金属的电偶腐蚀等制约了其在船舶中的实际应用。通过微弧氧化在钛合金表面原位生长氧化物陶瓷层,可显著改善钛合金的以上性能。
对于复杂结构部件,常采用化学镀镍进行表面处理。近年来银/钯贵金属纳米膜化学镀是一种新的方法,它与基体形成化学电偶,银/钯将诱使基体金属阳极钝化或在钝化膜被破坏时在钯提供的阳极电流作用下将有更好的自修复能力,从而起到较好的防护作用。
海洋工程中使用的关键运动部件,如柴油机汽缸套、燃机轮机叶片、传动系统减速箱、齿轮、蜗轮、蜗杆、各类传动轴、钻铤、钻头、井下打孔工具、稳定器、推进器、滚轴等,常服役于高温、高压、高湿、高磨损、高冲蚀等恶劣环境条件下,其腐蚀、磨损速率比陆地严重数倍以上。这些关键部件发生故障,除了要负担新件的高额成本外,还要承担由此造成的重大停工、停产损失甚至包括人员伤亡损失。关键部件的安全运行与高可靠性往往标志着一个国家海洋工程装备技术的先进程度。这些部件通常都需要进行表面处理或改性。
以先进热喷涂技术、先进薄膜技术、先进激光表面处理技术、冷喷涂为代表的现代表面处理技术,是提高海洋工程装备关键部件性能的重要技术手段。
超音速火焰喷涂(HVOF)是20世纪80年代出现的一种热喷涂方法,它克服了以前的热喷涂涂层孔隙多、结合强度不高的弱点。HVOF制备耐磨涂层替代电镀硬铬层是其最典型的应用之一,已应用在球阀、舰船的各类传动轴、起落架、泵类等部件中。近年来,低温超音速火焰喷涂(LT-HVOF)以其焰流温度低、热量消耗少、沉积效率高而成为HVOF的发展趋势。应用LT-HOVF可获得致密度更高、结合强度更好的金属陶瓷涂层、金属涂层。如:在钢表面制备致密的钛涂层,提高钢的耐海水腐蚀性能;在舰船螺旋桨表面制备NiTi涂层,提高螺旋桨的抗空蚀性能。
等离子喷涂是以高温等离子体为热源,将涂层材料融化制备涂层的热喷涂方法。由于等离子喷涂具有火焰温度高的特点,非常适合制备陶瓷涂层,如Al2O3、Cr2O3涂层,从而提高基体材料的耐磨、绝缘、耐蚀等性能。但是,等离子喷涂制备的涂层存在孔隙率高、结合强度低的不足。近年来发展的超音速等离子喷涂技术克服了这些不足,成为制备高性能陶瓷涂层的极具潜力的新方法。
气相沉积薄膜技术主要包括物理气相沉积和化学气相沉积。利用气相沉积薄膜技术可在材料表面制备各种功能薄膜。如起耐磨、耐冲刷作用的TiN、TiC薄膜,兼具耐磨与润滑功能的金刚石膜,耐海水腐蚀的铝膜等。
激光表面处理是用激光的高辐射亮度、高方向性、高单色性特点作用于金属材料特别是钢铁材料表面,可显著提高材料的硬度、强度、耐磨性、耐蚀性等一系列性能,从而延长产品的使用寿命并降低成本,如利用激光熔敷技术对扶正器进行表面强化来提高其表面耐磨、耐蚀性能。激光技术的另一个重要应用则是对废旧关键部件进行再制造,即以明显低于制造新品的成本,获得质量和性能不低于新品的再制造产品,如对船用大型曲轴和扶正器的再制造等。
冷喷涂是俄罗斯发明的一种技术,由于喷涂温度低,在海洋工程结构的腐蚀防护中具有潜在的应用价值。
总之,现代表面工程技术是提高海洋工程装备关键部件表面的耐磨、耐腐蚀、抗冲刷等性能,满足海洋工程材料在苛刻工况下的使役要求,延长关键部件使用寿命与可靠性、稳定性的有效方法,也是提升我国海洋工程装备整体水平的重要途径。
3.6电化学保护
金属-电解质溶解腐蚀体系受到阴极极化时,电位负移,金属阳极氧化反应过电位减小,反应速度减小,因而金属腐蚀速度减小,称为阴极保护效应。电化学(阴极)保护法分两种:外加电流阴极保护和牺牲阳极阴极保护。
牺牲阳极阴极保护是将电位更负的金属与被保护金属连接,并处于同一电解质中,使该金属上的电子转移到被保护金属上去,使整个被保护金属处于一个较负的相同的电位下。该方式简便易行,不需要外加电源,很少产生腐蚀干扰,广泛应用于保护小型(电流一般小于1A)金属结构。对于牺牲阳极的使用有很多失败的教训,失败的主要原因是阳极表面生成一层不导电的硬壳,限制了阳极的电流输出。
外加电流阴极保护是通过外加直流电源以及辅助阳极,迫使电流从介质中流向被保护金属,使被保护金属结构电位低于周围环境。该方式主要用于保护大型金属结构。
近些年来,深海环境下材料及构件阴极保护的研究受到了格外的重视。阴极保护可以采用牺牲阳极方式,也可以采用外加电流方式。从可靠性和管理维护等方面来看,以牺牲阳极型的阴极保护居多。
腐蚀、生物侵蚀和污染使海洋建筑物付出极大代价。世界近海工程的发展推动了这方面的研究工作。新的阴极防护系统和先进的保护涂料得到了发展,后者包括特殊的抗污染的化合物和防腐掺合剂。腐蚀作用随环境不同而呈现出巨大差异。
世界各国对舰船的腐蚀问题给予了高度重视,如美国海军舰船通用规范等都提出了采用阴极保护与涂层联合防腐蚀的措施,并对方案设计、设备选型、系统安装、调试验收、日常维护进行了详细的规定。
目前,国外舰船阴极保护技术的发展主要体现在两个方向:一是阴极保护设计技术的提高,如采用计算机辅助优化设计;二是外加电流阴极保护系统各部件材料的不断改进和性能的不断提高,如辅助阳极以及混合金属氧化物阳极等。
我国也早在20世纪60年代就开始了外加电流阴极保护实船试验,并在20世纪70年代初就在第一艘驱逐舰上成功安装了外加电流系统。我国1982年制定了“船体外加电流阴极保护系统”的国家标准,目前研制出的外加电流阴极保护装置也已在舰船上大量安装使用。
外加电流阴极保护的关键首先在于电流分布场的计算,国外发展了大型标准软件,目前我国的相关软件都需要进口;其次是施加电流的设备,这方面我国虽然能生产一部分小电流设备,但大电流设备几乎完全依赖进口,即使我国能生产同等较低电流的设备,由于国外设备的可靠性高,即使价格高出30%,国外船商仍然不采用我国生产的设备。
20世纪60年代开始,我国开发了一系列的常规牺牲阳极材料,目前无论船舶还是海洋工程结构的常规阴极保护都大多采用了国产阳极,几乎完全实现了国产化,并且已大量出口。近年来我国也开发了深海牺牲阳极(深海环境)、低电位牺牲阳极(高强钢等氢脆敏感材料)和高活化牺牲阳极(干湿交替环境)材料,但这类关键部位的牺牲阳极材料还是主要国外进口。
3.7缓蚀剂
具有表面活性的化学物质在金属表面上首先进行物理吸附,然后转化为化学吸附,占据金属表面的活性点,从而达到抑制腐蚀的作用。缓蚀剂的类别有:无机类缓蚀剂、有机类缓蚀剂、复配缓蚀剂、其他缓蚀剂等。缓蚀剂在封闭场合经常使用,包括油井、输油气的船舶等。因此,缓蚀剂也与阻垢剂、杀菌灭藻剂、清洗剂等联用,又发展出缓蚀阻垢剂等。
3.8结构健康监测与检测
无论是钢结构还是混凝土中的钢筋,监测与检测是掌握腐蚀状态的关键手段,其可以进行结构的提前预警,同时也是寿命评价的基础,从而保证装备及人员的安全。监测的参数主要包括:腐蚀电位、阴极保护效果、结构的腐蚀速度、海生物污损情况、涂层状况、结构厚度变化、材料中的氢含量、环境参数等单参数以及多参数,参数监测和智能化的实时原位监测可实现工程结构全寿期内的腐蚀状态分析和寿命评估。我国的海洋腐蚀监测/检测设备及基础设施的监控比较薄弱。
目前,海洋腐蚀监测手段也仅仅在200m以上的海域应用比较成熟,在200m以下水深的腐蚀判断标准不明确、腐蚀环境数据匮乏,造成了腐蚀监测的不确定性。
海洋平台和海洋油气储罐内腐蚀监测、腐蚀挂片和腐蚀探针全部采用国外产品。
3.9安全评价、可靠性分析、寿命评估
保障船舶和海洋工程结构的安全性和可靠性是一项长期任务。由于较严重的腐蚀,服役过程中结构是否安全可靠需要进行评价;设计寿命到达后,考虑到结构的可用性和工程的实际需求,开展寿命评价和延寿更是当前的重要课题。积累各种服役条件下的材料环境性能数据、发展监测与检测技术、提出寿命模型,以期开展工程结构的安全评价、可靠性分析、寿命评估。
我国从“六五”至“九五”期间[53],积累了大量在大气、土壤、海水和淡水环境中的材料腐蚀数据,建立数据库20个,共计6大类材料(黑色金属、有色金属、混凝土、高分子材料、保护层、电缆和光缆),353种材料,试样93237片。2006年补投黑色金属、有色金属、高分子材料、涂镀层材料、建材5大类材料,积累了材料腐蚀数据近万个,环境因素数据约8万个,建立了腐蚀库43个。2007年针对西沙典型大气环境,进行了黑色金属、有色金属、高分子、涂镀层和建筑材料共计7435件样片的投试工作,并开展了数据积累和数据库建设工作。
寿命评价方法包括经验法、类比法、快速试验法、数学模型法等。虽然针对海洋平台结构和海底管道,从研究的角度我国也已提出自己的疲劳评价方法,但在实际应用中,我国一直是直接引起国外软件,对其中的模型、试验依据完全不了解。实际上国外也缺乏成熟的理论方法。特别是随着钢的强度级别的提高,高强钢应力腐蚀、腐蚀疲劳和氢脆问题更为突出;高强钢在深海中的氢脆问题可能会严重,且阴极保护升高氢脆敏感性。我国导管架平台寿命期已到,如果需要平台继续服役,阳极消耗殆尽,采用何种方法延寿是紧迫课题,国外已有相关技术。
3.10不同材料的防护差异
海洋工程中使用的材料体系众多,包括钢铁材料、钢筋混凝土结构、有色金属材料(铝合金、钛合金、铜合金、镁合金等)、复合材料等。从使用量上看,钢铁、钢筋混凝土用量最大。就腐蚀防护技术而言,前述的多种防护技术在不同材料上都可应用,然而,不同材料防护技术相互之间存在差异。复合材料的轻量化特点,在海洋工程中的使用有望进一步加大,其防护技术还有待深入探讨。
目前,我国没有海洋钢筋混凝土平台,海工用钢筋混凝土主要用于海岸工程、海外大桥。海工钢筋混凝土的长效防护是国际上非常重要的课题。如何保障我国众多的跨海大桥长期寿命至关重要。高性能、长寿命的海工钢筋混凝土对我国南海及岛礁工程的建设具有重要价值。钢筋混凝土破坏的主要原因是海洋中的氯离子渗透、接触到钢筋,导致钢筋发生腐蚀。为了有效控制氯离子的渗透,除了提高混凝土本身抵抗氯离子渗透的性能外,在混凝土表面施加防护涂料是常用办法,国外已经广泛使用,我国近年来已开始重视。
更多关于材料方面、材料腐蚀控制、材料科普等方面的国内外最新动态,我们网站会不断更新。希望大家一直关注中国腐蚀与防护网http://www.ecorr.org
责任编辑:汪玉玲
投稿联系:编辑部
电话:010-62313558-806
中国腐蚀与防护网官方 QQ群:140808414
免责声明:本网站所转载的文字、图片与视频资料版权归原创作者所有,如果涉及侵权,请第一时间联系本网删除。
相关文章
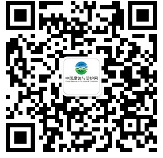
官方微信
《中国腐蚀与防护网电子期刊》征订启事
- 投稿联系:编辑部
- 电话:010-62316606-806
- 邮箱:fsfhzy666@163.com
- 中国腐蚀与防护网官方QQ群:140808414
点击排行
PPT新闻
“海洋金属”——钛合金在舰船的
点击数:8125
腐蚀与“海上丝绸之路”
点击数:6461