摘要
轻水反应堆(LWR)是国际上多数核电站采用的堆型。锆具有良好的加工性能,优良的机械性能,较高的熔点、优异的耐蚀性能及核性能,被用作燃料包壳和堆芯结构材料,是发展核电及核动力舰船不可替代的关键结构材料和功能材料。随着核电技术的发展,对堆芯包壳材料性能提出了更高的要求,本文综述了核用锆合金包壳材料的国内外研究和使用现状以及新型SiC包壳材料的研发现状。总体来说,锆合金在未来几十年内仍是核反应堆包壳材料的主要用材,开展新合金的研发,不断提升锆合金的性能是世界各国研究者共同的目标;适时加大投入力度,强化条件建设,就能加快具有国内自主知识产权锆合金的产业化步伐,可最终实现核电及核动力堆用锆合金材料的自主化;SiC材料具有更高的熔点?更好的耐腐蚀性能,是一种极具应用潜力的材料,有可能成为第4代核反应堆的包壳材料,但还需投入大量研究。
1 前言
锆及锆合金具有独特的核性能,良好的加工性能,在300~400℃的高温高压水和蒸汽中有良好的耐蚀性能,被主要用作轻水反应堆的燃料包壳和堆芯结构材料(燃料包壳、压力管、支架和孔道管),广泛用于民用反应堆和军用动力堆,是发展核电及核动力舰船不可替代的关键结构材料和功能材料,因此被誉为“原子时代第1金属”。近年来,各国在提高反应堆的安全性、可靠性以及在降低核电成本的同时,积极提高反应堆的运行功率,这必然会对用作包壳和堆芯结构材料的耐蚀性能和力学性能提出更高的要求。因此,国内外科研人员都在持续研发性能更加优异的锆合金。SiC包壳材料以及开展包壳材料涂层保护技术的研究,目的均在提升核反应堆的安全性、可靠性和经济性。
2 Zr合金包壳材料研究进展
2.1 Zr合金的成分研究现状
军事上的需求是推动锆(铪)工业起步的主要动力。金属Zr就是美国发展核潜艇的产物,后来,随着人类对高效、清洁能源的需求,锆被大量地应用到核电反应堆。
锆主要以合金的形式被用于制作轻水核反应堆的燃料组件的包壳管、压力管、格架、端塞、仪表盒等,其中包壳管的用量最大,占整个锆材用量的80%左右。燃料组件是核反应堆的核心,其安全性和可靠性取决于Zr合金包壳,因此锆合金材料是核反应堆堆芯的关键结构材料,被称为核反应堆的“第1道安全屏障”,燃料组件是核电站运行的消耗品,每一个换料周期(12个月或18个月),1/3的燃料组件需要更换。为了加深燃耗、降低燃料循环、提高反应堆功率、延长换料周期,核发达国家将锆合金包壳等结构材料放到战略性的高度加以重视,开发出了可用于大型先进压水堆、性能优异的锆合金材料及组件,垄断了世界核电用Zr合金材料市场。
目前国际上开发的锆合金主要有Zr-Sn系、Zr-Nb系和Zr-Sn-Nb系3大类。在20世纪50年代,美国发展了Zr-2合金,由于Zr-2合金耐高温水及蒸汽腐蚀的性能较好,因此自1967年以来,一直被用作沸水堆燃料元件包壳材料及其它堆芯结构材料。
Zr-2合金在高温下腐蚀时容易吸氢,造成合金的脆化,称为“氢脆”,如美国萨凡纳河反应堆中的Zr-2合金包壳管就因“氢脆”的原因而造成了早期破损事故,随后又有多起因“氢脆”而导致的反应堆燃料元件破损事故的报道。为克服此缺点,研究人员去掉了Zr-2合金中的Ni并提高了Fe含量,从而开发出了Zr-4合金。在360℃高温高压水中,Zr-4合金的吸氢量明显减少,仅为Zr-2合金的1/2至1/3?Zr-4合金被广泛用作压水堆和加压重水堆的元件包壳和沸水堆的元件盒以及其它堆芯结构材料等。在Zr-4合金基础上,通过降低Sn含量进一步发展了低SnZr-4合金。与常规Zr-4合金相比,低SnZr-4合金具有更好的耐腐蚀性能。
前苏联开发成功的Zr-1Nb合金(Zr-Nb系合金)主要用作压水堆元件的包壳材料。Zr-1Nb合金的强度和塑性与Zr-2合金基本相同,但吸氢要比Zr-2合金小。
Zr-2合金、Zr-4合金、Zr-1Nb合金称为第1代锆合金,低SnZr-4合金称为第2代锆合金。
核电反应堆的发展方向是提高卸料燃耗,延长换料周期,以降低核电成本。这就要求增加燃料的燃耗,提高冷却剂的温度并调整冷却剂的pH值,即燃料包壳的工况变得更为苛刻。目前的常规Zr-4合金和改进Zr-4合金已不能满足燃耗达55GWd/tU反应堆的运行要求。为此各国都在研究性能更好的新型锆合金,纷纷开展了综合Zr-Sn及Zr-Nb系合金优点的新型锆合金(Zr-Sn-Nb系合金)的研制。20世纪90年代,法国成功开发出M5合金,当燃耗达到60GWd/tU时,M5合金的氧化膜厚度只有Zr-4合金的1/3,吸氢量只有Zr-4合金的1/5,而且辐照生长和蠕变性能都优于Zr-4合金。M5合金的堆内腐蚀对反应堆温度和中子通量的敏感性比Zr-4合金的要小的多。
美国开发了Zirlo合金作为燃料元件的包壳材料,在BR3堆中经平均燃耗为71GWd/tU的考验后,其均匀腐蚀比Zr-4合金小50%,辐照生长和蠕变性能也优于Zr-4合金。
此外,俄罗斯研制出E635合金、日本研制出NDA合金、韩国研制出HANA合金、德国研制出PCA合金、这些合金都具有比Zr-4合金更好的堆内性能,尤其是德国开发的Zr-Nb-Sn-Fe-V合金经反应堆辐照考验,在燃耗高达98GWd/tU时,腐蚀还未发生加速现象。
Zirlo、M5、HANA等Zr-Sn-Nb系锆合金称为第3代锆合金,它们已取代第1、2代锆合金在第3代压水堆核电站中进行了系统广泛的商业应用,表1给出了国际上已经使用和试用成功的典型锆合金成分。
近10年来,随着核电技术的进一步发展,各国在新锆合金成分研制方面继续前行,美国、法国、韩国等国家在已经商用的成功的锆合金基础上,开展了成分优化或新合金成分的研究,新研制的锆合金大多已经或正在进行堆内辐照考验,并已部分取得堆内辐照考验数据。国内为了打破国外厂商对锆合金成分的垄断,以中核集团、国家核电和广核集团等为代表的核电龙头企业也开始注重开发具有自主知识产权的锆合金,目前堆外研究都已取得不错研制结果,但缺乏堆内辐照数据,总体上落后于国外。各国的新锆合金成分研发见表2~表5。
2.2 锆材工业化生产现状
目前,各个核发达国家均建成了从原子能级海绵锆到核级锆合金结构材料(管、板棒材)完整的产业链,美国的华昌、西屋,法国的法玛通等公司代表了锆合金产业化的世界先进水平。
我国锆合金的研究和工业化生产始于20世纪60年代,期间解决了锆、铪分离技术,制取出了原子能级海绵锆,具备了原子能级海绵锆的工业化生产技术,成为当时少数几个具备工业化生产海绵锆,铪的国家之一,并研制出了Zr-2、Zr-4合金结构材料以及Hf控制棒,其中,Zr-2合金、Hf控制棒成功装备了我国的第1代核动力工程,Zr-4合金用于秦山核电站,这是国内首批应用于核反应堆的锆、铪产品?Zr-2合金及Hf材获得了国家科技进步特等奖(子项),秦山核电站用锆材获得了国家科技进步二等奖。
“八五”以后,西北有色金属研究院在国家项目的支持下,研制了低SnZr-4合金(改进Zr-4合金),以该材料制备的成套技术为依托,组建了具有20世纪90年代世界先进装备水平的西北锆管有限责任公司,主要生产动力堆用Zr-4合金包壳管,实现了真正意义上与国际接轨的锆合金结构材料的批量化生产,基本满足了我国重点工程对锆材的需求。但因装备的不配套,其生产线并不完整,缺少专用熔炼炉及大型的管坯挤压设备,因此Zr-4管的生产是从管坯开始的,而管坯则依赖国外进口,因其产量低,对管坯的需求量也较少,因此,进口渠道暂时还未受到限制。
西北有色金属研究院与中国核动力研究设计院一起开展了高性能新型锆合金的研制,并取得了突破性进展?研制了两种新型锆合金——N36(NZ8)、N18(NZ2)合金,并获得了相关的专利。
在“十五”期间,西北有色院针对N18新型锆合金板材进行工艺优化和扩大规模试验,开展应用性能研究。基本上弄清了N18新锆合金的相转变温度,为合金板材的加工工艺提供了依据。研究了合金的应力腐蚀开裂行为;对中试N18新锆合金板材开展了加工后的显微组织、渗氢、氢化物取向、织构等研究;开展了工业规模N18新锆合金的工程应用研究。结果表明:与Zr-4合金相比,N18合金的抗疖状腐蚀性能显著提高,均匀腐蚀、应力腐蚀、吸氢性能、焊接性能、力学性能也有所提高,物理性能等其它性能与Zr-4合金相当。目前,N18新锆合金已有堆内初步辐照数据。“十一五”期间,针对N18合金重点研究了板材工程化所涉及的加工工艺问题,掌握了工业规模铸锭的熔炼、锻造等工艺、获得了优化的板材热。冷轧加工工艺,具备了工业化生产的技术基础。
2009~2011年,西北有色院依托国家863课题研发成功了一种Zr-Nb系锆合金——C7合金,其名义成分为Zr-1Nb-0.01Cu-0.0025S,已获得发明专利(ZL200810232541.1)。目前已经成功制备了φ280mm/500kg级铸锭,生产出了φ9.5mm×0.57mm包壳管材?φ10mm端塞用棒材、δ0.8mm和δ0.3mm的格架用条带材,摸索了管材的加工工艺,但未进行工艺优化及定型研究。
2010~2013年,在中核集团的支持下,中国核动力研究设计院联合西北有色院在前期研究的基础上,开展了N36合金工程化规模的核电包壳用管、棒材研制、通过研究,掌握了N36锆合金的t级铸锭的熔炼、锻造、挤压工艺,打通了采用国产两辊轧机两道次轧制,配合进口KPW25轧机生产φ9.5mm×0.57mm管材的生产工艺,所生产的管材的外观、尺寸、超声、涡流等测试均满足核电包壳用材的苛刻技术条件,2012~2013年,N36锆合金包壳管被制作成燃料组件,在中核集团的某核电站进行实际工况下的辐照考验,有可能成为中国自主知识产权的高性能燃料组件的标志性产品。
在锆材的工业化生产方面,上海高泰稀贵金属股份有限公司成立于1998年5月,专门从事锆管和不锈钢管的生产。目前已经和法国法玛通公司合资成立中核阿海珐(上海)锆合金管材有限公司(CAST)(双方各占50%股份),合资公司专门生产法玛通公司的M5合金管。该公司不具备熔炼、锻造、管坯加工能力,完全依赖法玛通公司从法国进口锆管坯进行生产。
国核锆业股份公司(国核锆业)成立于2007年12月,是国家核电技术公司与宝钛集团有限公司的合资公司,现在已经建成了完整的锆合金材加工生产线,承接美国西屋公司ZIRLO合金的技术转让任务,并将为我国引进的AP1000核电站,提供换料用锆合金材。
西部新锆核材料科技有限公司(西部新锆)成立于2013年4月,公司是以发改委、工信部、财政部三部委批准的“自主化先进压水堆燃料组件用锆合金结构材料产业化”项目为推动,由西北有色金属研究院发起,并由西安工业资产经营有限公司、中信金属有限公司等股东共同出资设立的。2013年9月,中核集团的独资子公司中国核燃料有限公司入股西部新锆公司,成为公司的第一大股东,公司注册资本变更为2.3亿元。公司主要从事自主化核能用锆材的研发与中试,肩负着自主知识产权核级锆材核心技术的转化、中试及小批量生产,对确保国家未来新型核电事业发展的战略需求具有关键支撑作用。
2.3 Zr合金研发及生产的国内外差距
具有自主化的核级海绵锆生产技术尚未产业化
目前仅有朝阳东锆开发的锆、铪分离技术达到了100t级的规模并经过了验证。但其装备水平和规模难以通过国家的核安全认证,因此无法在工程中使用。
已建成投产的大型海绵锆生产企业国核维科锆铪有限公司,利用的技术为美国西屋公司转让技术,不具有自主知识产权,产品的使用还受到美国公司的严格控制。
所以国内海绵锆(铪)的产能还不足以支撑国内自主发展核电、核动力堆及出口电站用料的需求。
新一代锆合金尚未实现商业化生产和应用
国内新一代锆合金堆外研究水平基本和国际同步,但是国外新合金如M5、Zirlo等已现了工业化生产,并在核电站得到了应用,国外新研发的锆合金也很快进行了堆内辐照考验而国内研发的新合金(N18、N36、C7等)仍处于工程化研发阶段。
国内自主化堆芯用锆合金结构材料仅具备了小型核电站用Zr-4合金配套的生产能力,1991年正式并网发电的秦山核电站使用了西北有色院等研发的Zr-4合金材料?我国引进核电站全部使用的是国外锆合金材料,包括法国M5合金?美国西屋公司Zirlo合金和俄罗斯的E110锆合金,造成目前我国大型核电站使用的锆材全部依赖进口的不安全局面。
尚无自主化核心技术的核级锆材生产企业
国内目前已建成的核级锆材生产企业,均无自主知识产权的锆合金专利产品生产核心技术,其锆材生产技术及合金均依靠国外引进。如中核阿海珐(上海)锆合金管材有限公司生产M5合金材,其生产技术、生产管理均依靠法方提供。国核宝钛锆业股份公司引进的是美国Zirlo合金材生产技术,目前自身并无自主知识产权的合金。由于多种原因,国内还未能依托自主知识产权的锆合金及制备技术建立的专业核级锆材生产线。
这种局面制约了我国核电自主发展,更无从谈及走出国门,参与国际竞争。不树立我国核电自主品牌,就不可能使我国从核电大国走向核电强国。
虽然国内在核级锆材方面和国外存在着差距,但目前国内企业已掌握了工程化条件下的核级海绵锆生产技术及一整套锆合金结构材料的加工技术。因此适时加大投入力度,强化条件建设,就能加快具有自主知识产权锆合金的产业化步伐,最终实现核电及核动力用锆合金材料的自主化,并参与国际市场竞争。
3 SiC包壳材料研究进展
锆合金作为核燃料包壳材料已经40多年了,在未来几十年内锆合金仍将是压水堆堆芯用主要包壳材料,但随着核电技术的进步,换料周期的增长,安全性要求的提升,尤其是2011年3月日本福岛核电站事故中的氢气爆炸给核电站造成了最严重的损害,并造成大量的放射性产物释放事故,而爆炸的元凶———氢气是灼热蒸汽与过热核燃料棒的锆合金包壳接触产生的。因此,研发具有一定程度包容事故能力的包壳材料,成为国际上核燃料领域发展的新方向。而SiC是一种极具应用潜力的材料,有可能成为第4代核反应堆的包壳材料。
SiC/SiC复合材料与锆合金相比有以下优势:①由于其熔点高(高纯SiC熔点2730℃,Zr熔点1852℃),工作温度极限很高(2000℃),所以在冷却剂丧失(LOCA)事故发生时也不会发生危险。②由于SiC与水蒸气反应活性很低,发生失水事故时,温度升高也不会产生大量氢气发生危险,并且避免反应放热。③SiC水侧腐蚀速率很低,可以大大延长换料周期。④相比锆合金,SiC具有更低的中子吸收截面,可以节省约25%的燃料。⑤高的机械强度降低了磨损导致失效的几率。⑥得益于SiC可以在LOCA工况下工作,可以提高约30%的功率。⑦核燃料燃烧更充分,提高功率,减少废料的放射性,降低废料处理难度。
但与锆合金包壳相比,SiC材料的劣势有:①价格昂贵;②工艺不成熟,不能达到包壳管要求(尺寸,公差等);③作为包壳管材料,工程应用数据缺乏;④获得许可证尚需漫长时间;⑤换用SiC做包壳,很多相关规格标准,甚至反应堆热工设计都需重新变动,比如UO2丰度、换料周期等。
目前SiC复合材料包壳管一般有以下两种类型:
3.1 纯SiC型
纯SiC型的结构分内、外两层,如图1所示:内层为整体致密SiC层,防止气态裂变产物外泄(见图1a),图1a中还标注了内层结构的细节、外层为SiC/SiC复合材料层(纤维+渗入SiC)SiC纤维是提供机械强度,在发生事故时保持固态裂变产物不外泄,维持基本几何形状。其渗入SiC是增加致密度,并提供腐蚀保护,防止磨损。
3.2 SiC金属复合型
这种包壳管将SiC材料与传统的金属材料复合制成包壳管,包壳管的形式为:金属层+整体致密SiC层+纤维层结构,图2和图3分别为碳化硅金属复合型燃料棒样品及结构示意图,从图3看出,这种燃料棒分为内层、中间层和外层3层复合结构。内层为金属衬里,一般为传统的锆合金材料,主要起保证气密性,防止气态裂变气体外泄,与传统锆合金燃料棒类似,包壳管两端也采用焊接密封端口;中间层为整体致密SiC材料,主要增加包壳的强度,提升力学性能;外层为SiC纤维,与中间层的致密SiC间添加纯碳润滑层,通过滑动传递应力,可获得一定的延展性,并且具有良好的耐腐蚀性能。
SiC包壳与水反应缓慢,与传统锆合金包壳相比,可把产生氢气的风险降低几千倍,避免福岛核电站的类似事故,在正常工况条件下也具有老化慢?耐蚀性能好,使用寿期长的特点。但作为一种新型核电用材料,尚需投入大量基础研究及工程应用研究,才能进一步走向实用。
4 结语
关于我国轻水反应堆用包壳材料的研发工作谨提出以下几点看法:
1 锆合金在未来几十年内仍是核反应堆包壳材料的主要用材,开展新合金的研发,不断提升锆合金的性能是世界各国研究者共同的目标。
2 国内在核级锆材研制方面和国外存在着差距,但目前国内企业已掌握了工程化条件下的核级海绵锆生产技术及一整套锆合金结构材料的加工技术。因此适时加大投入力度,强化条件建设,就能加快具有自主知识产权锆合金的产业化步伐,可最终实现核电及核动力用锆合金材料的自主化,并参与国际市场竞争。
3 SiC材料具有更高的熔点、更好的耐腐蚀性能,是一种极具应用潜力的材料,有可能成为第4代核反应堆的包壳材料,但还需投入大量研究。
(本文版权属于《中国材料进展》)
免责声明:本网站所转载的文字、图片与视频资料版权归原创作者所有,如果涉及侵权,请第一时间联系本网删除。
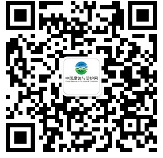
官方微信
《腐蚀与防护网电子期刊》征订启事
- 投稿联系:编辑部
- 电话:010-62316606-806
- 邮箱:fsfhzy666@163.com
- 腐蚀与防护网官方QQ群:140808414