高温结构材料是航空发动机、航天火箭发动机上各种热端部件的关键材料,可以说航空航天工业的发展离不开高温结构材料的发展, 先进航空航天器更依赖于高性能高温结构材料的研究开发。现代航空航天器迫切要求提高发动机的推重比, 这就要求尽可能提高发动机的工作温度。同时这也对高温结构材料提出了一个更高要求: 既具有更高的综合性能(强度、韧性、蠕变性能和环境特性等),又具有较低的密度。
传统的镍基、钴基高温合金的使用温度都在1100℃以内(包括采用冷却技术), 已接近熔点的90%。由于受熔点的限制,继续提高其使用温度已变得越来越困难[1]。因此,寻求新体系高温结构材料显得尤为重要。自20 世纪70 年代末以来, 熔点为1400~1600℃的金属铝化物(主要是Ni-Al,Ti-Al 和Fe-Al 系) 为主流的高温结构用金属间化合物得到了广泛而深入的研究。目前,已有部分Ni-Al 和Ti-Al系化合物合金及其复合材料步入实用化研究阶段。但是,随着对金属铝化物研究的逐步深入,发现金属铝基材料的使用温度与目前广泛应用的Ni 基高温合金相比性能提高有限, 因此研究使用温度超过传统镍基、钴基高温合金和金属铝基化物的新型超高温结构材料成为了目前高温结构材料领域的迫切需求[2]。目前主要研制的超高温结构材料有: 难熔金属硅化物、金属间化合物、陶瓷及陶瓷基复合材料、C/C 复合材料等,本文对他们的研究进展进行了综述。
1 难熔金属硅化物
金属材料的高强度大致上与其熔点成正比,单从高强度来考虑,钨、钼、钽、铌、铼和钒等高熔点金属可以作为理想的超高温结构材料[3]。难熔金属是最早进行研究并得到应用的超高温结构材料。由于难熔金属的抗氧化性能差、脆性大, 在难熔金属领域,提高难熔金属的高温抗氧化抗腐蚀性能,增加难熔金属的韧性是一个持久的研究热点。难熔金属硅化物具有高熔点(高于2000℃),在1600℃下还具有良好的热稳定性和抗氧化性能, 因而受到特别的关注,也成为超高温结构材料研究的新热点之一。受密度和可加工性能的影响, 目前国内外研究较多的是钼硅化物和铌硅化物。
1.1 钼硅化物
钼硅化合物有三种:MoSi2、Mo5Si3 (T1) 和Mo3Si。其中MoSi2具有熔点高(2050℃)、密度低(6.31g/cm2)、热膨胀系数低、热导率高、耐腐蚀性能好等优点。但是MoSi2作为高温结构材料仍然有三个问题有待解决[4]:①MoSi2的室温韧性低;②MoSi2因韧脆转变特性和玻璃相SiO2的存在而表现出较低的高温强度; ③MoSi2在400~600℃范围内抗氧化性能极差。为了解决上述问题,目前主要通过合金化、复合化以及改进制备工艺等方法以达到低温韧化和高温强化的目的,但目前仍未达到满意的效果。Mo5Si3(熔点2180℃)从室温到熔点没有相变,因具有很强的共价键蠕变强度高, 其高温抗蠕变性能远优于MoSi2,但其高温抗氧化性能很差,易形成多孔的氧化膜和Mo 的挥发性氧化物, 以及在中温下有pesting 现象,不能单独用作高温结构材料[5-7]。Meyer等人[8-10]研究发现添加少量B 可极大提高Mo5Si3的抗氧化性,并且消除了中温pesting 现象。目前研究方向也由MoSi2转到Mo-Si-B 三元体系上,潘昆明、刘张涛等人[11-12]通过放电等离子烧结(SPS)和原位合成法制备T2(Mo5SiB2)相合金,SPS 制备出纯度高致密且粒度细小的T2 相合金, 而原位合成法在机械合金化后没有形成Mo3Si+Mo5SiB2, 而仅形成合金元素在Mo 中过饱和固溶体和弥散分布在其中的亚微米级颗粒。潘昆明[11、13]等对T2(Mo5SiB2)相合金进行了室温下力学性能和不同温度下的压缩断裂行为进行了研究,在室温下沿(001)面发生解理断裂,随温度升高,T2 相断裂方式由室温下的解理断裂向穿晶解理-沿晶混合模式转变,T2 相脆-韧转变发生在1000~1200℃。目前, 多相Mo-Si-B 合金的微观组织和成分点对氧化性能(特别是中、高温阶段)、合金化和掺杂对材料结构和性能的影响等尚缺乏系统的理论研究[14],因而多相Mo-Si-B 合金工艺的研究以及相应的系统理论研究是今后努力的方向。
1.2 铌硅化物
Nb5Si3熔点高(2484℃),密度低(7.16 g/cm2),高温热稳定性好,良好的抗氧化抗蠕变性能。但Nb5Si3在室温较差的韧性及冷热加工能力, 限制了作为高温结构材料的应用。近年来,韧相增韧已成为进一步改善陶瓷及金属间化合物性能的有效方法[15]。铌基固溶体韧性相(Nbss)和硅化物强化相(Nb5Si3)构成的Nbss/Nb5Si3原位复合材料具有平衡的力学性能,被广泛研究[15-16]。目前主要通过多元合金化和抗氧化涂层提高NbSS/Nb5Si3复合材料的高温抗氧化性能。添加的合金元素( 主要有:Ti、Mo、W、V、Hf、Cr、C、Y 和B 等[16-17]),依靠固溶强化、增加新的强化相、改善合金显微组织结构可以使NbSS/Nb5Si3复合材料获得均衡的低温韧性、高温强度和高温抗蠕变性能, 但其高温强度和抗蠕变性能还有待进一步的提高, 高温抗氧化性能不足仍是其作为高温结构材料应用的主要障碍[18],合金化提高其高温抗氧化性能的作用是有限的[19]。在材料表面制备抗氧化保护涂层是兼顾力学性能和高温抗氧化性能的有效途径,例如, 对于大型薄壁构件, 采用热稳定性最好的MoSi2涂层,能够保证工作温度达到1500℃[20]。抗氧化涂层虽可以极大地改善抗氧化性能, 但涂层与基体之间存在热膨胀系数失配、结合力弱的问题,另外还可能发生涂层与基体互扩散、涂层与环境的不良化学反应,从而导致铌基体力学性能下降。
2 金属间化合物
有序金属间化合物的特点是晶体结构中组成元素原子作长程有序排列, 原子间结合力强, 除金属键外还形成一部分共价键或离子键, 兼备了陶瓷材料和金属材料的双重特性,综合性能指标优于钴基、镍基等传统的高温合金,韧性又高于普通的陶瓷材料[21]。大多数金属间化合物在室温下都呈低塑性,倾向于脆性解理和沿晶开裂。环境脆性[22-24]是许多金属间化合物脆性的主要原因,环境脆性与温度、应变速率以及环境等密切相关, 金属间化合物中的活性元素(Al、V、Ti、Si 等)与空气中的水汽发生表面催化反应形成原子氢, 氢再通过扩散进入合金内部引起氢脆所致。自从Izumi 等人[25]首次发现在Ni3Al 合金中添加少量的B 可显著提高其延展性以来,人们对合金元素抑制环境脆性的机理展开了大量的研究[27-28]。防止解理开裂最基本的方法之一是提高材料的纯洁度, 试验研究表明, 室温时很脆的TiAl 合金使用高纯度原材料后, 在不添加其它合金元素的情况下, 伸长率可达到2.7%[26]。
为解决金属间化合物脆性问题,利用合金化改变金属间化合物的晶体结构类型,提高对称性,为材料变形提供附加的滑移带,从而改善其韧性。邓文[28]等研究了B 微合金化对Ni3Al 晶界结合力的影响,结果表明说明B 原子能够强烈地偏聚到Ni3Al 合金的晶界等空位型缺陷上, 使该处的价电子密度与基体相同,从而增加了这些区域的键合力,相应增强了晶界的结合力。断口特征由沿晶断裂变为穿晶断裂。同时还可以在金属间化合物基体内引入增强相形成的金属间化合物基复合材料这样可以结合各组成相的优异性能,如加入SiC 晶须等脆性第二相可以在低温下增加裂纹偏折的吸收能,利用高温陶瓷增强相可抑制位错移动和晶界滑移来改善抗蠕变性能[29]。
3 结构陶瓷及其复合材料
结构陶瓷具有比金属更高的强度和耐腐蚀性能,同时还具有密度小、热膨胀系数低、耐磨性高、高温强度高、热稳定性和化学稳定性好等优点。近年来, 单体结构陶瓷研究的重点材料包括氮化硅(Si3N4)、碳化硅(SiC)和氧化锆(ZrO2)等,它们具有较高强度、较高热震抗力和较高的可靠性,但是其本质上的脆性和较强的缺陷敏感性极大限制了它的应用与推广[30]。为了克服高温结构陶缺陷敏感性高、韧性低、可靠性差的缺点,出现了陶瓷基复合材料。
连续纤维增韧陶瓷基复合材料(如C/SiC,SiC/SiC 等)克服了金属材料密度高和耐温低,结构陶瓷脆性大和可靠性差,碳/ 碳复合材料(C/C)抗氧化差和强度低, 以及氧化物陶瓷基复合材料抗蠕变性差等缺点[31-32]。由于Cf/SiC 抗氧化性能较碳化硅纤维增韧碳化硅陶瓷基复合材料(SiCf/SiC)差,到目前为止,国内外普遍认为,航空发动机热端部件最终获得应用的应该是SiCf/SiC[32]。然而作为复合材料,连续纤维增韧陶瓷基复合材料依然存在着基体、纤维、界面相间的热膨胀系数(CTE)不匹配,相界面之间结合力弱的问题。目前, 高温结构陶瓷的增韧已从单一的纤维(或晶须)补强的陶瓷基复合材料发展到两相颗粒弥散多相复合陶瓷材料、自补强多相复合陶瓷以及表面梯度多相复合陶瓷等完整系列的多相复合陶瓷,再结合氧化锆相变增韧机制的引入,使陶瓷材料的强化增韧达到极好的效果[33-34]。此外还可通过材料结构的改变来达到增韧的目的,如自增韧结构、仿生叠层结构及梯度功能材料等[35]。通过强韧化,陶瓷材料的力学性能特别是断裂韧性已有很大提升,但仍属脆性材料的范畴,同时在成本、可靠性和寿命预测方面仍需要做出努力。
4 C/C 复合材料
碳纤维增强碳基(C/C)复合材料具有杰出的高温力学性能(如高热稳定性、低热膨胀系数、耐腐蚀、耐摩擦磨等),同时又具有很高的比强度和良好的高温持久强度,这使得C/C 复合材料成为了极具吸引力的高温结构材料[36]。然而C/C 复合材料的优异性能只有在惰性气氛下才能保持, 因为它在空气中370℃就开始氧化[37],并且氧化速率随温度的升高迅速增大。由于C/C 复合材料在制造过程中基体内部不可避免地会存在着许多缺陷, 这些缺陷又易成为活性中心,与被吸附的氧在杂质微粒(Na、S、K、Mg等)的催化作用下发生反应,生成的CO 或CO2而引起C/C 复合材料的失重[38]。因此,开发可靠的氧化保护系统是C/C 复合材料作为高温结构材料应用的关键。
目 前,C/C 复合材料抗氧化防护的途径主要有以材料本身抑制氧化反应为前提的内部基体改性技术和以防止含氧气体接触扩散为前提的外部抗氧化涂层技术两类[39]。由于基体改性技术并未获得突破性的研究进展, 只能解决1000℃以下的氧化防护问题,更高温度下的氧化防护则必须依赖抗氧化涂层,故抗氧化涂层技术得到了人们的广泛重视。然而抗氧化涂层与C/C 复合材料基体之间的热膨胀系数存在失配,易导致涂层开裂和涂层与基体的分离, 进而导致碳纤维增强体直接氧化而使循环寿命缩短。因此解决涂层与基体间热膨胀系数不匹配和提高界面结合强度是增强C/C 复合材料抗氧化性能的关键。
5 防护涂层
5.1 多层复合涂层
由于单一涂层往往无法满足C/C 复合材料抗氧化的要求,在实际应用中多采用多层复合涂层。多层复合涂层能够限制各单层缺点, 发挥它们各自的优点和独特性能,并且各层之间能够相互协调,相互补充[40]。最简单的复合涂层是双层复合涂层[41]。由于SiC 与C/C 复合材料具有良好物理化学相容性,因而双层复合涂层大多采用它作为过渡层以缓解热应力,封填层一般选用耐火氧化物、高温玻璃或高温合金作为封填层。该种涂层利用封填层对SiC 内涂层的裂纹和孔隙进行愈合, 从而提高复合涂层的抗氧化能力。史小红等[42]采用包埋法在在碳/ 碳复合材料表面制备了TaSi2/SiC 双层复合涂层,结果表明两层之间没有明显的界面,并且能在1773K 的空气介质中能有效保护碳/碳复合材料233 h。双层复合涂层的基础上,在过渡层与封填层之间加入阻挡层,可显著提高抗氧化涂层的抗氧化效果和寿命。在三层复合涂层的封填层外再加一层热障涂层, 可阻止内层在高速气流中的冲刷损失、在高温下的蒸发损失以及在苛刻气氛里的腐蚀损失。这种四层结构复合涂层的设计构思被认为是唯一适合1800℃以上抗氧化防护的涂层技术[43]。
5.2 功能梯度涂层
由于功能梯度材料(FGM)的杨氏模量和热膨胀系数是连续变化的, 故功能梯度材料能有效缓解热膨胀失配, 增强涂层与基体以及涂层与涂层之间的结合力[44-45]。近些年来,研究者对C/C 复合材料的功能梯度材料涂层做了大量研究, 并主要集中于功能梯度材料涂层的制备方法上。利用渗硅技术制得的(SiC/Si3N4)/C 功能梯度涂层,使C/C 复合材料的抗氧化温度提高到了1550℃[46-47]。由于Si3N4拥有与SiC 相同的耐火性, 而且其热膨胀系数小于SiC,因此更好解决了涂层与材料之间热膨胀系数不相匹配的矛盾,提高了涂层的抗氧化能力。
6 展望
难熔金属硅化物、金属间化合物、陶瓷基复合材料和C/C 复合材料均被认为是传统高温合金的替代材料, 同时也成为了超高温结构材料领域的研究热点。近几十年来,高温合金替代材料获得了飞速的发展, 然这些材料由于某些难以完美解决的缺陷或成本上的因素,使得它们的应用仍十分有限。再加上新体系高温结构材料的研发周期长、资金投入量大、风险高, 这使得人们对研制新型替代材料产生了更为谨慎的态度。
传统的高温合金在力学强度、高温抗氧化耐腐蚀、加工性能、焊接性能以及性价比等方面都具有不可替代的优势。因此,传统高温合金的改进仍将是现阶段高温结构材料发展的重点,而高温合金替代材料还有很多工作要做(包括理论、机理的研究和制备工艺),重点是突破这些材料的应用瓶颈。与此同时,由于防护涂层不仅具有防氧化抗腐蚀的功能,而且还可在高的环境温度下保持低的基体温度,因此防护涂层的开发和应用在将来会得到进一步的加强。
更多关于材料方面、材料腐蚀控制、材料科普等等方面的国内外最新动态,我们网站会不断更新。希望大家一直关注中国腐蚀与防护网http://www.ecorr.org 责任编辑:王元 《中国腐蚀与防护网电子期刊》征订启事
投稿联系:编辑部
电话:010-62313558-806
邮箱:ecorr_org@163.com
中国腐蚀与防护网官方 QQ群:140808414
免责声明:本网站所转载的文字、图片与视频资料版权归原创作者所有,如果涉及侵权,请第一时间联系本网删除。
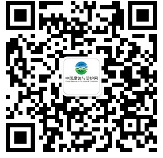
官方微信
《腐蚀与防护网电子期刊》征订启事
- 投稿联系:编辑部
- 电话:010-62316606-806
- 邮箱:fsfhzy666@163.com
- 腐蚀与防护网官方QQ群:140808414