F-35 是由主承包商洛•马公司与主合作伙伴诺格公司及BAE系统公司合作开发的。首架F-35 已在2006 年首飞。复合材料一直是其制造工作的重点。
F-35 的制造难点
F-35 的制造难点是要符合预算,即对飞机的每一个零部件必须精心计算以保证成本的优化,特别是碳纤维复合材料构件的制造,因为这种材料的结构占飞机重量的35%,飞机大部分外表面均由此种材料制成。
而F-35 的机身、机翼、尾翼分别由不同国家的供应商制造,最后在洛•马公司总装,因此F-35 制造的最大难点是飞机复合材料蒙皮厚度的控制。F-35 各阶段的生产因供应商、零部件复杂程度以及其要求各不相同。如ATK公司生产许多机翼蒙皮桁条时用的是自动纤维铺放工艺,而洛•马在制造前机身段蒙皮时用的是手工铺层。
控制F-35 复合材料蒙皮厚度的方法有2 种:一是根据精细的计算对复合材料的铺层数进行加减;另一种方法是对零件进行切削加工。洛•马公司及其合作伙伴采用了切削加工和模塑后增加铺层2种方法来确保蒙皮厚度达标。在洛•马公司,前机身蒙皮是在Invar35钢模具上用手工铺层并在热压罐中进行固化的。固化成层合板的铺层随后用切削加工法去除余量从而控制蒙皮的厚度。在ATK公司,机翼蒙皮是用纤维铺放法进行铺层并固化的,然后用洛•马公司的制造技术及生产工程人员开发的一种方法精确测量蒙皮的厚度。必要时,增加铺层,然后对整个结构进行第二次固化,该法称作固化层合板补偿法(CLC)。这样做的目的是控制厚度,是为成本达标采用的一种策略。
大型切削中心
在洛•马公司沃斯堡工厂的中心,就有一个体现这种策略的关键部门,这就是F-35 的切削及钻孔中心。它是由德国DST公司建造的,负责F-35 前机身蒙皮、机翼蒙皮以及其他复合材料工件的切削及钻削。
在DST 切削中心进行的大部分工作,采用的刀具是由AMAMCO工具公司提供的涂覆金刚石的碳化物刀具。AMAMCO 公司为中心设计了DST仿形铣刀具。
卡尔蔡斯IMI公司的测量系统是世界上最大的高精度测量系统,主要用于蒙皮尺寸、边缘以及孔的精度检验。复合材料构件经切削加工后,用该测量系统进行检测。从2008 年6月开工以来,F-35 的机翼蒙皮采用了MMZ-B Plus龙门式坐标测量机的5m×16m×2.5m 测量包线,也用于风洞模型1:1 的组件以及其他飞机机体零件的测量。
洛•马公司也用自己开发的无损检测激光超声检验系统来检验复合材料结构的孔洞及其他内部缺陷。将该系统400MHz的激光器对准复合材料结构时,从该激光器发出的信号返回到一传感器来显示蒙皮中的孔洞、裂纹、分层等缺陷。激光超声系统的运转速度为0.56m2/min,比传统的喷水超声系统快10倍,因此是F-35 制造工艺不可缺少的一部分。
钻孔
在F-35上评估了3种类型的钻孔,即手工钻孔、电动钻孔以及自动化(数控)钻孔。洛•马公司采用的大部分是自动化钻孔。在大多数情况下,F-35 的钻孔法为垛式钻孔,即将复合材料蒙皮放在支承结构上,穿过蒙皮和支承结构进行钻孔。用单一的钻头进行钻孔、铰孔以及进一步埋头铆接而成。F-35 钻孔中引人注目的是前机身,机身每一边用自动化龙门式钻头钻出750个孔。
机翼蒙皮是与支承结构堆迭起来,用辛辛那提公司的龙门式系统进行钻孔的。随后F-35 的团队用Virtek Vision 国际公司生产的激光投影系统将紧固件号码投影到蒙皮表面上, 而无需查找复杂的图纸即可进行紧固件的安放。当不能自动化钻孔时,可用样板进行人工钻孔。采用投影系统可以大大减少工时和工作量。
刀具更换门槛值的跟踪
洛•马公司用的大部分钻头采用的马达为气动和液压式。刀具的尖锐角决定钻削速度的大小。随着刀具变钝,切削时间加长。进给系统可测定钻孔时间的长短。当达到门槛值时,指示灯立即指示工人更换刀具。洛•马公司正在寻求合适的直径公差以及特殊的工艺过程控制,从而消灭不合格孔的出现。F-35 钻孔质量Cpk(过程能力指数)的目标是达到1.3,而目前为1.0,正在改进中。
所有的修边、切削系统以及钻孔工艺正在进行效率、成本、质量等因素的评估以便确定整个F-35 复合材料生产的最佳工艺。洛•马公司已在沃斯堡建立一个钻削/ 切削卓越中心继续对刀具及工艺进行开发。随着F-35 寿命的加长,洛•马公司及其供应商还有几十年对复合材料的优化和管理时间。
免责声明:本网站所转载的文字、图片与视频资料版权归原创作者所有,如果涉及侵权,请第一时间联系本网删除。
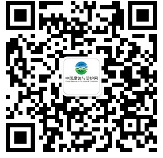
官方微信
《腐蚀与防护网电子期刊》征订启事
- 投稿联系:编辑部
- 电话:010-62316606-806
- 邮箱:fsfhzy666@163.com
- 腐蚀与防护网官方QQ群:140808414