1.3.2.1石油天然气工业
公路、铁路、水路、航空和管道五大输送方式各有长短,油气管道运输的优点主要表现为:输送成本比铁路、公路低,且不像水运严重受到地理位置的限制;建造价格比铁路低,且施工周期短;输送量越大,成本越低;占地面积小;节省人力,管理费用低;节省能源;安全性高;损耗少,几乎无污染;价格稳定,供给不受气候、交通的影响而有保证。
由于管线腐蚀而引起的损失是巨大的,因此,了解腐蚀发生的原因并采取有效的防护措施有着十分重大的意义。金属在不同的环境条件下可以发生不同的局部腐蚀,如孔蚀、缝隙腐蚀、应力腐蚀、晶间腐蚀、磨损腐蚀等。管线腐蚀就是管线在各种环境因素作用下发生化学反应,使管线性能下降、状态改变,直至损坏变质的一种自然现象。腐蚀的发生与温度、压力、电偶、焊缝、土壤环境、微生物、大气及现有的防护措施等因素密切有关。
输油管道基本上采用碳素钢无缝钢管、直缝电阻焊钢管和螺旋焊缝钢管。输油管道的敷设一般采用地上架空或埋地两种方式。但无论采用那种方式,当金属管道和周围介质接触时,会发生化学作用或电化学作用引起表面锈蚀。金属管道遭到腐蚀后,在外形、色泽以及机械性能方面都将发生变化,影响所输油品的质量,缩短输油管道的使用寿命,严重可能造成泄漏污染环境。
在使用1~2年就发生腐蚀穿孔造成油气泄漏的现象也时有发生。EGIG(欧洲输气管道事故数据组织 — European Gas pipe line Incident Data Group)在对该组织的8个成员单位的管线事故调查数据进行分析的一份报告中显示,由于腐蚀而引起的事故在事故总量中居第三位,仅次于第三方因素和施工、材质缺陷。前苏联的统计资料表明,管线腐蚀事故占停气事故的30 %,天然气管线腐蚀事故累积超过2000次,其中有一次竟死亡800多人。另据美国国家标准局调查表明,1975年美国油气工业因腐蚀造成的年度损失费用为90亿美元。
国内的数据显示,1988年全国发生油气田管道事故248起,其中由腐蚀引起的就有202起。在诸多油气设施中,以油气管线腐蚀事故最为触目惊心。目前全世界范围内管线正以每年40, 000 km的速度增长。如此大量的管线埋设在地下,其外部长期受到土壤介质、杂散电流的腐蚀以及各种微生物的侵蚀,内部受到含有H2S、CO2、Cl- 等油、气、水的腐蚀,致使管道发生穿孔泄漏和开裂性事故,引发严重的后果。尤其在高压下工作的管线一旦发生破裂,很容易引发火灾、爆炸等灾难性事故。我国对腐蚀损失所做的统计表明,腐蚀所造成的损失约占国民经济的3%,其中石油天然气工业是受腐蚀危害最严重的部门之一。我国的油气田大多数分布在盐碱沼泽地带,属于中、强,甚至特强腐蚀土壤,对各类管道、埋地设施的腐蚀很严重。随着我国油气田开发进入中后期,作为油田主要设施的管道,其腐蚀问题将越来越突出,甚至成为困扰油田生产的一个重要因素。因此,了解腐蚀发生的原因,采取有效的防护措施,有着十分重大的意义。
(1)电化学腐蚀
电化学腐蚀是指金属表面与离子导电的介质发生电化学作用而产生的破坏。地下土镶的物理化学性质的不均匀性和金属材质的电化学不均衡性就为埋地管道的电化学腐蚀创造了条件。电化学腐蚀是埋地管道中最常见的腐蚀形式。
(2)细菌腐蚀
土壤中的一些细菌比如硫酸盐还原菌在贫氧的情况下能加快腐蚀的进程,其作用机理是参加电极反应将可溶性硫酸盐转化为硫化氢,这些细菌利用反应放出的能最来繁殖。而且硫化氢会与金属反应引起阴极去极化作用,这就是所谓的细茵腐蚀。细菌腐蚀受许多因素的影响,如土壤的含水量,酸碱性,周围温度以及盐类物质。相关文献指出在pH值为6.2~7.8的贫氧沼泽地带细菌的活动最频繁。
(3)化学腐蚀
化学腐蚀是指金属管道表面的材料直接与环境中的非电解质发生化学作用而引起的破坏。其主要破坏机理是非电解质中的氧化剂与金属表面的原子相互作用而形成腐蚀产物。化学腐蚀与电化学腐蚀的不同之处在于腐蚀的全过程没有电流的产生只是电子在金属与氧化剂之间的传递。一般在常温和干燥的环境下并不会发生化学腐蚀,但是在高温下就容易被氧化生成一层氧化膜。在管道输送油品的过程中,由于油品中含有丰富的有机硫化物,很容易与金属管道发生化学腐蚀。
与发达国家相比,国内油气管道的腐蚀情况显然要严重得多。主要存在以下问题:
(1)老管道进入腐蚀事故多发期。日前在运营的大多数老管道建于20世纪70年代前后,受当时技术水平的限制,管道的防腐蚀设计特别是防腐涂层的选型缺乏科学性,几乎无一例外地选用了石油沥青防腐涂层,经过20多年的运行,大多数石油沥青涂层已经老化,特别是运行温度较高的管道。而目前管道防腐大修技术相对落后,致使涂层维修滞后,管道保护不足,进入腐蚀事故高发期。
(2)腐蚀防护专业人员相对欠缺。特别是管道运营与维护操作层面的技术人员、防腐蚀施工及管理人员大多没有经过腐蚀防护专业方面的技术培训,对管道腐蚀控制中出现的问题不能及时察觉并处理。即便是防腐蚀设计人员也主要集中在阴极保护设计方面,涂层选型与设计既没有相应的指导性文件,也缺少科学的评价与决策过程。
(3)没有系统的腐蚀控制管理规程。虽然相关技术规范与标准较多,但大多针对防腐蚀设计、施工与材料的实验室测试,且相对零散,而有关腐蚀控制系统管理方面的标准和规程较少。
目前国外许多国家正在推行管道风险与完整性管理方法,并开发出了相应的管理程序,将管道的腐蚀控制纳人完整性管理体系,实行积极的监测与维护。
(4)各部门缺乏沟通机制与信息交流平台。科研、设计、施工、运营管理等各个部门的沟通与协调一致,对管道腐蚀的有效控制起着重要的作用,但目前没有相应的机制促进沟通,也缺乏信息交流的平台,难免导致科研脱离实际、设计失之偏颇、施工质量受损、运营管理低效。
(5)防腐蚀工程质量控制需要进一步加强。工程质量的全面控制包括原材料/设备质量、施工质量、监造/监理质量、验收质量控制。尽管目前已实行了市场准人、招投标、监造/监理等制度,但对监造/监理、验收质量的控制缺乏有效的监督和检查。
建议及对策:
(1)开展中国石油管道腐蚀现状调查、分析与对策研究工作
对油气管道的腐蚀现状进行全面调查,分析腐蚀原因,制定相应的对策。
(2)全面推行腐蚀风险监测与完整性管理体系
大多数管道运营者通过遵守其管理规程和国家法规来控制风险,但是管理规程通常是惯例性要求,并不能适应不同需求和风险的各种管道。这种不适应体现在两方面:①可能会漏掉某些新的风险;②应用环境不够灵活,阻止了可识别并消除关键风险的新技术的应用。
管道管理部门从管道设计和运营中的规章管理向风险管理过渡,将风险管理作为维护和改善管道安全水平的最经济有效的方法,风险管理承认要消除所有风险是不可能的,认为控制风险的最佳方法是分析并有效利用现有资源,而不是简单地遵守规章和规范。
开发油、气管道完整性管理程序,全面推行腐蚀风险监测与完整性管理体系,将腐蚀控制纳入完整性管理体系,主要包括以下工作:
1)管道系统数据管理,包括收集、分析、整合;2)腐蚀风险评价;3)完整性评价(内检测、试压和直接评价);4)对评价的响应与腐蚀减缓措施;5)评价的时间间隔;6)与腐蚀有关的完整管理程序的效能测试;7)有关管道外腐蚀、内腐蚀及应力腐蚀风险的完整性管理方案。
(3)建立管道基线检测与评价、周期性检测与评价制度
对新建管道进行基线检测与完整性评价,建立管道系统最初的完整性资料;由于腐蚀是一种时效性危险因素,因此必须对运营管道进行周期性检测与再评估,监测腐蚀风险的控制情况。
(4)开展管道直接评价
除了第三方活动破坏外,油气管道更多的风险来自腐蚀。直接评价是一种利用结构化过程的完整性评价方法,在不能对管道进行内检测和试压评价时,通过该方法综合管道的物理特征、运行历史结合管道检查、检测和评价的结果,评价管道完整性,主要适合于外腐蚀、内腐蚀。直接评价主要涉及4个步骤:1)预评估;2)间接检测;3)直接检查;4)后评估。
目前国外已有相应的外腐蚀直接评价标准NACE RP 0502(2002年颁布)和内腐蚀评价的标准NACE RP 0104(2004年颁布)。
(5)管道防腐蚀从业人员技术培训
对有关从业人员进行技术培训,实行腐蚀专家、腐蚀工程师、腐蚀技术员资质认证、持证上岗制度。提高从业人员专业素质,确保管道腐蚀控制工作的效能。
(6)整合现有技术标准体系,加快国际先进技术标准采标进程
对现有技术标准、规范进行修订、整合,搜集引进国外先进技术标准特别是完整系评价与管理方面的标准并转化采用,补充、完善油气管道腐蚀控制的标准体系。
(7)建立腐蚀与防护数据库与信息管理系统,加强腐蚀数据管理
与腐蚀相关的数据的数量与质量直接影响到腐蚀风险评价的置信度及腐蚀风险控制系统的效能。因此建立腐蚀与防护数据库与信息管理系统,收集并有效利用相关数据,是管道完整性管理必不可少的环节。
(8)加强技术交流与合作、强化工程质量监督
鼓励技术人员参加国际技术交流与合作,每年或每两年召集管道防腐科研、设计、施工、运行管理等部门的技术人员进行一次行业内技术研讨会,提供沟通与信息交流平台,同时加强设计方案审查、施工质量监控、运行维护管理。
油气采集储运行业的腐蚀问题可通过采取一些必要的措施加以控制,这些控制和减缓腐蚀事故及损失的措施和经验绝大部分都有过成功应用的实例,主要有:
(1)遵循标准选材设计施工;(2)脱除腐蚀介质,减缓油气介质的腐蚀性;(3)采取适当、有效的防护措施,如加注缓蚀剂、防护涂层、阴极保护及几种方法联合使用;(4)建立腐蚀监测系统,把握腐蚀动态;(5)对管道而言,进行定期清管排污;(6)增加防腐投入;(7)立足国情,开发研制适合我国国情的防腐系列产品;(8)加强防腐工作领导,建立防腐专业机构和制度,提高管理水平。
针对国内站场管网的腐蚀现状,提出以下几点建议:
(1)鉴于国内站场管道防腐蚀层材料的性能与先进国家防腐蚀材料的性能相比仍存在一定差距,建议进一步引进、开发性能优异、适合于站场施工的新型管道防腐蚀材料和修复技术。
(2)在对站场埋地管网实施区域性阴极保护的基础上,建议加强对专业技术人员的培训,提高管理质量。
(3)加快对国外先进管道监检测技术和设备的引进和消化,定期开展站场管网的监检测和综合评价,保证管道的安全运行。
(4)对现有技术标准、规范进行修订和整合,制定油气站场管网腐蚀的控制标准,促进站场管道的完整性管理。
(节选自《我国石油天然气工业腐蚀成本调查报告》)
1.3.2.2煤炭工业
我国是世界上最大的煤炭生产国和消费国,煤炭是我国的主要能源,在一次能源结构中煤炭占比高达70 %以上,预计在今后相当长的一段时间内都不会改变。然而,实际开采与洗选过程中因设备腐蚀而造成的经济损失非常惊人,煤炭设备的腐蚀将不仅引发大量资源浪费和停工停产等问题,而且还对煤炭的安全生产埋下了重大隐患。我国煤炭主要是地下开采,煤炭系统的设备多处于井下阴暗、潮湿、含腐蚀性气体的空气或酸性矿井水的环境中,腐蚀现象严峻。传统的涂料防护、热浸镀锌防护、热喷锌与涂料复合防护层、玻璃钢组合管道等均在煤矿管道获得了一定应用,并取得了一定的使用效果,但仍难以满足矿井的设计使用寿命。
煤炭作为我国的主要能源,并且在今后相当长的一段时间内都不会改变。2014年我国煤炭产量达到38.7亿吨,接近世界煤炭产量的1/2,煤炭开采和洗选业主营业务收入达到330, 045.87亿元,利润总额为1, 268.5亿元。根据煤炭工业发展规划,2015年全国煤矿采煤的机械化程度达到75%以上,其大中型煤矿将达到95 %以上,30万吨及以上中小型煤矿则达到70 %以上。因此开采与洗选过程中因设备腐蚀而造成的经济损失非常惊人,煤炭设备的腐蚀将不仅引发大量资源浪费和停工停产等问题,而且还对煤炭的安全生产埋下了重大隐患。从中国煤炭年产量趋势来看,煤炭产量最然增速日趋缓慢,但仍然在不断增加,并且产量可观。近年来国内生产的“三机一架”的产量表明,煤炭的生产是靠消耗大量的钢材换来的。
煤炭生产中地下作业占大部分,井下见不到阳光,又有水,火,瓦斯,地热,地压的顶板冒落等灾害的威胁。鉴于井下的特殊环境,金属腐蚀问题非常严重。立井井筒装备,提升容器,各种管路普遍受到腐蚀影响,井下开采的煤矿一般都需要提升、运输、通风、排水等系统,以保证安全生产和持续稳产,这些系统也受到不同程度的腐蚀。煤炭生产中的地面洗选设备设施则长期处于潮湿高温环境下,腐蚀状况相当严重。
随着煤炭工业的发展,人们从实践中逐步认识到矿山腐蚀的严重性和防腐工作的重要性。从70年代末期开始,煤炭系统开始重视矿山设备的防腐工作,逐步采取了一系列措施,加强科研攻关和新技术的推广应用,制定、颁发了《煤矿立井井筒装备防腐蚀技术规范》,取得了显著成绩。几十年来,煤炭系统先后有“酸洗、钝化表面处理工艺”、“干湿两用防锈漆”和“ZM系列增摩型钢丝绳防锈脂”等3项防腐成果获国家发明奖;有多项课题获煤炭部科技进步奖。但由于中国地域广阔,煤炭资源分布广泛,煤矿数量众多,其中乡镇小企业数量多等特点,煤炭生产加工过程中的腐蚀问题依然严峻,防止腐蚀的措施的研究、推广及应用依然是重中之重。
我国煤炭生产主要是地下开采,地下煤矿数量约占98 %。煤矿井下相对湿度高,井下水酸、碱、盐等含量大,以及有害气体在水中的溶解为电化学腐蚀过程提供了导电性良好的介质。由于工作需要,井下通风量大,供氧充分,为阴极反应的进行提供了有利条件。煤炭开采过程中频繁的磨擦磨损也大大加速了金属构件的腐蚀进程。我国部分矿井腐蚀调查和实验室模拟试验结果表明,钢铁在井下的单侧年平均腐蚀深度为0.2~1.2 mm,为海洋环境中钢铁腐蚀程度的2~3倍。
从腐蚀环境特征分析,煤炭行业腐蚀主要分为空气腐蚀和矿井水的腐蚀。由于井下空气中含有的一氧化碳、二氧化碳、甲烷、二氧化硫和硫化氢等气体具有较高的湿度和温度,材料遭到的腐蚀比城市大气还要严重。研究表明,当空气中的相对湿度高于60%时,由于毛细管凝结和吸附等作用,水蒸气会在金属表面形成水膜。二氧化硫等气体的溶入不但增加了液膜的导电性能,而且由于溶液呈酸性更加速了腐蚀。由于二氧化硫和氧的共同作用使铁转变成易溶的FeSO4,后者进一步氧化并水解为硫酸,再与铁反应,从而加速了腐蚀反应的进行。
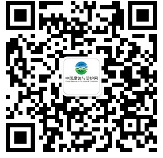
官方微信
《中国腐蚀与防护网电子期刊》征订启事
- 投稿联系:编辑部
- 电话:010-62313558-806
- 邮箱:fsfhzy666@163.com
- 中国腐蚀与防护网官方QQ群:140808414