春江潮水连海平,海上明月共潮生。“海洋素来是文人墨客创造文化的温床,同时也是国家自然资源的巨大宝藏。走向海洋,是我国经济继续深化发展和加强国防建设的重要步骤,党的十九大报告明确指出要加快推进海洋强国战略建设。随着我国海洋经济的快速发展,船舶逐渐向大型化、智能化、绿色环保方向发展,海洋工程装备也由近海、浅海走向远海、深海,对船舶与海洋工程材料的性能提出了更高的要求。如何强化和提高船舶在复杂海洋环境下的抗腐蚀性能成为我国走向深远海的当务之急。为此,我们特邀请到许立坤研究员就我国目前海洋船舶腐蚀防护技术发展现状及未来发展方向做相关方面的精彩解读。
许立坤,研究员,材料科学与工程专业博士生导师。现为中国船舶重工集团公司高级技术专家,第七二五研究所海洋腐蚀与防护国家级重点实验室常务副主任,山东省泰山学者,海洋防腐研究领域的权威专家。
记者:众所周知,海洋苛刻的腐蚀环境是影响海洋工程结构及船舶服役性能和使用寿命的关键因素,作为海洋船舶防腐方面的专家,请您为我们简要介绍一下海洋船舶腐蚀的类型及腐蚀原因,并大致介绍一下目前主要有哪些腐蚀防护技术可以减少海洋腐蚀带来的危害?
许立坤研究员: 由于海洋环境的严酷性,腐蚀是海洋船舶必须面对的一个关键问题,腐蚀不仅增大维护维修工作量,减少船舶的在航率,缩短船舶的使用寿命,而且会严重影响船舶的可靠性和安全性,因而船舶的腐蚀问题受到各相关方的广泛关注。影响船舶腐蚀的因素非常多,也非常复杂,包括各种环境因素以及材料和结构因素。例如,海水的温度、盐度、化学组成、流速、含沙量、溶解氧浓度、pH 值、污染物及其浓度、微生物和宏观污损生物,以及由于波、浪、流、冰等导致的环境载荷等等都会对船舶的腐蚀产生影响,这些物理、化学、生物、力学的因素常常交织在一起,发生耦合作用,导致腐蚀的机制更为复杂。船舶不同的部位所处工况环境也有很大差异,例如船体水下部位以及附体(舵、推进器、减摇鳍等)处于海水全浸状态,船体水线区处于间浸状态,上层建筑处于海洋大气环境,海水管路系统处于流动海水环境,压载舱处于海水干湿交替环境,污水舱处于油污水环境,货油舱处于原油、沉积水、蒸汽或凝露环境等。同时,船舶除了船体结构以外,还有很多的系统和设备,其结构复杂,可达性差,工况多变,并且涉及众多的材料,如碳钢、低合金钢、不锈钢、铝合金、铜合金、钛合金、橡胶、复合材料等,这些特点显著增大了船舶腐蚀问题的复杂性和解决的难度。各种常见的腐蚀类型几乎都能在船上找到,如均匀(全面)腐蚀、点蚀、缝隙腐蚀、应力腐蚀、晶间腐蚀、脱成分腐蚀、冲刷腐蚀、空泡腐蚀、腐蚀疲劳、微生物腐蚀、电偶腐蚀、氧浓差腐蚀、沉积腐蚀、杂散电流腐蚀等等。每种腐蚀都是材料受所处环境作用的结果。有些腐蚀具有明显加速作用,如杂散电流腐蚀、微生物腐蚀等,能在很短的时间内就造成船舶结构或管路严重的腐蚀破坏。
要防止船舶的腐蚀,应避免”头痛医头、脚痛医脚“,需要采取系统性的腐蚀控制方法或腐蚀管理体系,以便系统性地解决腐蚀问题。其在时间维度上应为全寿命周期的腐蚀控制,涉及设计、建造、使用、维护、延寿和退役等全过程;在空间维度上应将船舶作为整体进行全系统的腐蚀控制,需要考虑不同部位、不同零部件、不同设备和系统之间的相互影响;在技术维度上应将多种适用的防腐蚀技术集成应用,发挥各防腐措施之间的协同作用;在管理维度上应是全要素的腐蚀控制,涉及人员、设备、材料、方法、环境、标准规范以及监测与评价等诸多方面,通过不断完善防护措施,实现船舶防腐水平的持续改进。
在具体的防腐技术方面,首先要做好防腐设计和选材工作。船舶的许多腐蚀问题都来自于设计不合理或材料选择不当。例如,舱底吸干头位置不合理,导致长期积水,使得舱底板发生严重腐蚀。又例如,海水管路采用紫铜材料,但设计海水流速超过了其允许的工作流速,从而导致严重的冲刷腐蚀,在弯头、三通、管接头等紊流区域尤其易发生腐蚀穿孔。采用双相不锈钢以期改善海水管路的耐蚀性,结果反而在管路的法兰连接处出现了严重的缝隙腐蚀,导致泄漏。诸如此类的事例还有很多。在设计阶段就对腐蚀问题做充分的考虑,并采取有效的措施,可以达到事半功倍的效果。这对相关设计人员提出了更高的要求,他们需要具有足够的防腐知识和经验,同时应建立相应的防腐设计规范,加强选材和防护方案的评审,开展相关试验验证,以保证设计和选材的合理性。此外,在一些严苛的腐蚀环境和工况下,设计选用高性能的耐蚀合金材料或长寿命防护涂层体系,尽管会增加初期建造成本,但却可以有效降低全寿命周期的费用,具有很高的效费比。
涂层和阴极保护是船舶广泛采用的防腐蚀技术。有机涂层可以将金属基体和腐蚀介质隔离,通过采用合适的树脂和颜填料来提高涂层阻挡腐蚀介质的能力,有的涂层还具有对基体金属的钝化或缓蚀作用,有的涂层含有锌粉、铝粉,对钢基体还具有一定的阴极保护作用。由于船舶不同部位的工况环境不同,因而需要采用不同的防腐涂层体系。除了涂料本身的性能外,表面处理和涂装过程对涂层的保护效果和使用寿命有非常大的影响。尤其对于复杂结构和空间狭窄的内部舱室,只有严格按照规范和工艺要求执行才能够保证涂层达到预期的性能。金属涂层(或镀层)以及陶瓷涂层等在船舶的某些部位或部件上也得到成功的应用,除了具有防腐保护作用外,有的还具有耐磨、绝缘、防滑等其它功能。阴极保护技术主要应用于浸泡在海水中的船体(含附体)、处于海水间浸状态的压载水舱以及海水管路系统和设备等。阴极保护常常和有机涂层联合采用,可以起到协同作用,阴极保护可以有效防止涂层缺陷和破损处金属的腐蚀,而涂层可以显著降低阴极保护电流密度,使保护电位分布更均匀,获得更经济有效的保护效果。
记者:您长期从事海洋腐蚀及材料环境适应性研究工作,尤其在船舶腐蚀防护方面有着扎实的理论基础和丰富的经验。请您详细谈一下您和您的团队研究上所做的工作和取得的进展和成就。并谈谈这些科研工作成果或技术的应用状况及产生的效益?
许立坤研究员: 我是 1989 年从哈尔滨工业大学金属材料专业研究生毕业后进入七二五研究所青岛分部工作的,入所以来,在陈光章研究员、董克贤研究员、王朝臣研究员等老一辈专家的带领和指导下,一直从事海洋腐蚀与防护领域的相关研究和工程应用工作,主要涉及电化学保护技术、材料深海腐蚀试验方法及环境适应性、先进表面防护涂层技术等研究方向。
在电化学保护领域,我们团队研制了具有自主知识产权的高性能钛基金属氧化物辅助阳极材料,通过采用多组元混合金属氧化物涂层体系,采用聚合物溶胶 - 凝胶方法在钛合金基体上制备了具有良好导电性和稳定性的电催化涂层阳极,显著提高阳极的电化学性能,其在海水中的稳定消耗率仅为 1-2?mg/A·a,使用寿命可达到 20 年。其性能达到甚至优于铂复合阳极,而价格更低。发明了长寿命热浸涂银 / 氯化银参比电极,解决了传统粉压法电极易粉化提早失效的问题,该参比电极在海水中具有极高的电位稳定性和良好的抗极化性能,使用寿命可达到 20 年,和船舶的使用寿命相匹配。研制了大排流量辅助阳极组件和高稳定性参比电极组件以及基于开关电源的智能恒电位仪,建立了新一代船体外加电流阴极保护系统,实现了船体外加电流阴极保护技术的升级换代。在此基础上,我们先后制定外加电流阴极保护相关国家标准、国家军用标准共 5 项,并参与制定了船舶阴极保护的 ISO 国际标准。针对船舶复杂海水管路系统的突出腐蚀问题,开展了管路系统材料的冲刷腐蚀性能和腐蚀电化学行为研究,掌握了船舶海水管路系统的腐蚀规律,确定了不同管系材料的允许最大设计流速,研制了适用铜合金以及铜 - 钛复合结构保护的长寿命铁合金牺牲阳极材料与组件,通过优化选材、阴极保护、电绝缘、管件耐冲蚀镀层等技术的集成应用,有效消除了海水管路系统中的腐蚀”热点“,解决了船舶海水管路系统腐蚀泄漏的难题。针对船舶海水压载舱等干湿交替部位存在的严重腐蚀问题,开展了集成防腐蚀技术研究,研制了适于间浸环境的腐蚀保护状态监检测装置和技术。通过数值模拟,实现了涂层和阴极保护的协同优化,有效消除了复杂结构的电流屏蔽效应,避免了保护电位过负导致高强钢氢脆的风险。通过腐蚀保护状况的原位监测和状态评估,实现了保护方案的持续改进和优化提升。
在深海腐蚀与防护研究方向上,我们是国内最早开展深海腐蚀试验研究的单位,先后研制了多型深海原位腐蚀试验装置和室内深海模拟试验装置,成功开展了从表层海水到超大水深的不同深度材料环境适应性试验研究,积累了大量的实海环境数据和材料深海环境腐蚀数据,建立了首个深海腐蚀数据库。掌握了不同材料的深海腐蚀与老化规律,探讨了海洋工程装备材料的深海腐蚀损伤机制。研制了适于深海环境的高性能牺牲阳极材料、深海防腐涂层以及深海原位电化学测量装置,成功开展牺牲阳极实际深海环境电化学性能测试研究,为深海装备的腐蚀防护提供了重要的技术支撑,研制的深海牺牲阳极和防护涂层已应用于中海油水下生产系统的腐蚀保护。在大量实践和经验积累的基础上,我们提案并主持编制《深海腐蚀试验方法导则》ISO 国际标准,该标准的制定提升了我国在该技术领域的话语权和影响力,对降低深海试验风险,保障深海装备的安全服役具有重要的意义。
在先进涂层技术方向,我们主要开展了紧固件复合涂层技术、金属 / 陶瓷防腐防污涂层技术以及自修复防腐涂层技术的研究。基于锌铝鳞片和改性环氧的复合涂层,在满足紧固件旋合性和力学性能要求的同时,显著提高其耐蚀性能,其耐盐雾试验明显高于镀锌、渗锌、达克罗等常用紧固件涂层,在海洋大气及干湿交替环境中的防腐寿命显著延长。针对船舶海底门格栅存在的腐蚀与污损问题,采用热喷涂和冷喷涂工艺方法,研制了金属 / 陶瓷防腐防污涂层,显著提高格栅耐冲刷腐蚀性能,并能防止海生物污损附着。近年来,我们在自修复防腐涂层方向也开展了一些探索研究,制备了基于水触发的微胶囊自修复涂层以及基于担载缓蚀剂的纳米粒子的自修复防护涂层,开展了自修复机制研究,相关研究成果已在 CorrosionScience,?Journal?of?Materials?ChemistryA?等刊物上发表,受到同行的关注,并获得科技部国际科技合作交流项目资助。
作为工业部门的研究机构,我们的研究工作和海洋装备实际需求紧密结合,研制的先进电化学保护材料、新型外加电流阴极保护系统、腐蚀保护监检测技术、紧固件复合涂层技术、金属 /陶瓷防腐防污涂层技术以及海水管路集成防腐蚀技术等成果已在海军舰船、远洋船舶、核电站海水冷却系统等工程中得到广泛应用,取得了很好的效果,产生了显著的经济效益和社会效益。科研成果先后荣获中国腐蚀与防护学会科技进步一等奖、中国船舶重工集团公司技术发明一等奖、国家工业与信息化部科技进步一等奖等奖励。
记者:据悉,您受邀参加 2019第六届海洋材料与腐蚀防护大会,并将在大会上做主会场报告,请问您有何重要的研究成果要与我们分享,请您简要谈谈这项研究的最新进展和应用。
许立坤研究员: 在第六届海洋材料与腐蚀防护大会上,我将就船舶阴极保护的若干关键问题与大家交流。大家都知道,阴极保护是防止金属海水腐蚀的有效方法,在船舶上已得到广泛的应用。然而,伴随着高性能船舶的发展,对船舶阴极保护技术也提出了新的要求。例如,随着全球气候变暖和海冰融化,北极航线开通将成为可能,但低温海水会导致船体外加电流阴极保护用混合金属氧化物(MMO)阳极的性能显著降低。此外,常规 MMO 阳极在高电流密度下使用寿命会显著缩短,需要进一步的改进提升。对于经常处于海水干湿交替环境的压载水舱,其工况环境会显著影响牺牲阳极的电化学性能,常规牺牲阳极在这种工况条件下性能会明显劣化,以至不能对压载舱结构提供有效的保护。另外,高强钢材料在新型高性能船舶上得到越来越多的应用,而高强钢存在氢脆敏感性,如何避免高强钢结构产生过保护也是必须解决的问题。上述这些问题对船舶阴极保护提出了挑战。
该报告将分析工况环境条件变化对船舶阴极保护的影响,并就如何解决这些问题与大家一起探讨。
记者:作为海洋腐蚀防护领域的专家和知名学者,请结合您的科研工作,谈一下目前我国在海洋腐蚀防护领域的发展现状和存在的差距,展望一下我国海洋船舶腐蚀防护技术未来应如何更好发展?
许立坤研究员: 伴随我国海洋经济的发展以及建设海洋强国战略的实施,海洋腐蚀与防护领域也迎来了快速发展的机遇。目前国内已掀起海洋腐蚀与防护研究的热潮,很多单位和团队都在开展这方面的研究,也取得了很多创新的成果。从相关国际刊物上发表的论文来看,我国学者的相关论文数量和质量都有显著的提升,在石墨烯应用、仿生涂层、智能自修复涂层、绿色防污涂层、深海腐蚀、光生阴极保护等前沿方向上我国科技工作者都很活跃。然而,在原创性和基础性研究的深度上还有待加强。目前在应用技术研究层面和国外的差距尤为明显,例如,船舶上使用的高端防腐防污涂料还主要是国外著名涂料公司的产品,占据了绝大部分市场。一些新产品新技术还缺少工程化研究,离实际工程应用还有一定的距离。需要加强产、学、研、用的结合,研发更先进的防腐蚀材料和技术,以满足不断增长的海洋装备和设施发展的需要。在船舶腐蚀防护领域,应关注工况环境条件变化以及新材料应用所带来的腐蚀防护新需求,发展新型高性能电化学保护技术,发展先进的防腐防污涂层材料,突出长期效(寿命)、绿色环保、易涂装施工等特性。同时,要加强腐蚀管理,做好船舶的系统性腐蚀控制,不断提高船舶的腐蚀防护水平。
后记:
不积跬步,无以至千里;不积小流,无以成江海。正是在许立坤研究员为代表的广大科研工作者们兢兢业业、科研报国的切实工作推动下,我国的海洋腐蚀防护事业才会不断迈入新台阶。为有牺牲多壮志,敢叫日月换新天。祝愿许主任团队在海洋防腐领域做出更大的成绩,为中华民族伟大复兴平添助力。
● 人物简介
许立坤,1965 年 10 月出生,工学博士,研究员,博士生导师。现为中国船舶重工集团公司第七二五研究所海洋腐蚀与防护国家级重点实验室常务副主任,国防科技创新团队带头人,中国船舶重工集团公司高级技术专家,山东省泰山学者特聘专家。长期从事海洋腐蚀与防护技术研究,主持完成重大、重点科研课题 20 余项。获部级科技进步一等奖 2 项、二等奖 2 项,中国腐蚀与防护学会科技进步一等奖 2 项,中国船舶重工集团公司技术发明一等奖 1 项。主编 ISO 国际标准 3 项,荣获国际标准化组织卓越奖(ISO Excellence Award)。在国内外学术刊物发表研究论文 150 余篇,其中 SCI、EI 收录论文约 70 篇。出版专著 1 部,并为 3 部专著撰写相关章节。获授权国家发明专利 35 项。多项研究成果在海洋装备等实际工程中得到广泛应用。主要学术兼职有:中国船舶重工集团公司科技委委员;中国腐蚀与防护学会常务理事,中国表面工程协会科学技术委员会委员;国际标准化组织金属与合金腐蚀技术委员会专家委员,全国钢标准化技术委员会金属和合金腐蚀分技术委员会委员,全国海洋船标准化技术委员会船用材料应用工艺分技术委员会委员;中国科学院海洋腐蚀与生物污损重点实验室学术委员会委员;海洋腐蚀与防护国家级重点实验室学术委员会委员;《中国腐蚀与防护学报》编委 ,《腐蚀科学与防护技术》编委,《材料开发与应用》编委等。
免责声明:本网站所转载的文字、图片与视频资料版权归原创作者所有,如果涉及侵权,请第一时间联系本网删除。
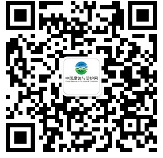
官方微信
《中国腐蚀与防护网电子期刊》征订启事
- 投稿联系:编辑部
- 电话:010-62316606-806
- 邮箱:fsfhzy666@163.com
- 中国腐蚀与防护网官方QQ群:140808414