中国梦的核心是工业现代化,先进制造业是工业现代化的支柱,高端机械装备制造是强国的标志,直接关系国民经济繁荣、国家安全建设和科技创新战略。第四次工业革命号角的吹响让中国制造业迎来了难得的发展机遇,也面临着前所未有的严峻挑战。不可否认,我国机械制造业取得了令人瞩目的成就,但与世界先进水平相比,仍存在较大差距,“大而不强”是目前不争的事实。如何提升我国机械制造业的核心竞争力,迈向全球价值链的高端?如何加快我国由制造大国向制造强国转变的步伐?面对机械制造业的转型升级,材料和制造技术将何处何从?
11月2日,在中国工程院化工、冶金与材料工程第十一届学术会议期间,带着这一系列的疑问,记者有幸采访到了抗疲劳制造缔造者、金属材料科学家、中国航发北京航空材料研究院研究员、中国工程院院士赵振业。赵院士忧国忧民、语风犀利率真令记者肃然起敬。整个采访过程严肃而祥和,记者被这位79岁科学家浓烈的爱国热忱和坚毅的科研精神所深深地感染!
赵振业院士
潜心科研酿硕果 赤忱丹心报祖国
赵振业出生在中华文明的发祥地之一河南省原阳县,求学于西北工业大学金属学及热处理专业,学成后北上京城,在西山脚下的中国航空发动机集团北京航空材料研究院(以下简称“航材院”)几十年如一日从事航空超高强度钢应用基础理论、合金设计和工程应用研究,并成为国内外知名的金属材料科学家。
1961年,23岁的赵振业毕业后被分配到航材院。他回忆说,很庆幸一接触工作便投入了我国第一个12%Cr钢的研究。跟着老一辈研究人员学步,而且一学就是十多年。作为一个主要参研者,看到亲自创造的综合性能优于国外同类合金的新钢种,并先后在三个航空发动机上压气机转子叶片、轮盘应用并取得成成功,他感到自豪!回味在那场“文化大革命”中日夜兼程走完的从合金设计、实验研究、工业试制到发动机工程应用技术研究、构件制造、演示与生产全过程,从中学到的知识,积累的经验,培养的勤学习惯和研究创新启蒙,他认为不仅很值得,而且是终生受益!
1975年起,他受命主持研究航空中温超高强度钢,步入新的研究领域,开始独立研究。当时除了美国把热作模具钢H11用作飞机构件外,世界上还没有一个真正的航空中温超高强度钢。他从研究二次硬化和强韧化基本理论出发,在相变、热处理、力学性能、工艺性能等系统探索基础上,研究成功38Cr2Mo2VA中温超高强度钢。由于巧妙地利用了Mo元素的强二次硬化效应,少量Cr元素与Mo配伍能压低Mo的硬化峰值,减少其对基体韧性的伤害程度,调整钢的韧性;少量Cr还可以提高Mo硬化峰前的硬度,调整钢的回火曲线,拓宽回火温度范围等特性,不仅达到了超高强度、综合力学性能良好、耐温高达500℃,而且,合金元素总添加量不足5%,从而将中温超高强度钢由中合金体系降为低合金体系。新钢种的研究成功,解决了飞机后机身超温超重的选材问题,还历练了他自主创新的能力和智慧,并获得国家发明三等奖。
起落架是飞机的第一关键构件,疲劳性能要求很高。长期以来,起落架寿命短,故障多,一直是困扰我国飞机设计发展和安全可靠使用的难题。1983年秋,他开始主持超高强度钢300M长寿命起落架应用研究课题。首先结合我国熔炼设备和技术现状提出“提纯原材料,降低硫含量”、“镦-拔开坯”技术路线建议,与抚顺钢厂创新提纯技术,于1985年一举达到美国标准要求和实物水平,开拓了一条自己的冶金技术路线,中国航空超高强度钢开始走上了VIM+VAR双真空熔炼的高纯道路。300M钢是世界最好的起落架钢,强度高,韧性良好,固有(应力集中系数Kt=1)疲劳强度高,用作起落架可做到体积小、重量轻、寿命长、使用可靠。但是,其突出缺点是疲劳强度对应力集中敏感和氢脆敏感。如不解决,非但不能满足起落架要求、充分发挥其超高强度优越性,还会潜在灾难性隐患。为此,提出了发展材料应用科学与技术思路,从抗疲劳原理出发,设计了长寿命起落架的总体技术方案。研究并提出一种“无应力集中”抗疲劳概念,创新了抗疲劳应用技术体系,即表面完整性机械加工技术体系、表层组织再改造性技术体系、表面完整复合防护技术体系、构件细节设计技术体系和(分课题负责人为主创新的)10多项先进工艺。这些技术克服了300M钢的两项弱点,回复了因应力集中丧失的疲劳强度,抑制和防止了氢脆。用国产300M钢制造起落架的疲劳寿命一举达到5000小时未失效,增加载荷30%再继续试验至6000小时仍未失效。这一结果远远超过了课题规定3000小时指标,也超过了国外同类起落架5000小时最高规定寿命指标。如今,起落架已广泛应用于多种飞机,使用至今无任何故障。长寿命起落架研究成功开拓了一条材料应用研究道路,又增添了超越国外先进水平的经历和能力。该研究获得国家科技进步一等奖。
我国是一个海洋大国,飞机需要在极端海洋气候环境中服役,他摒弃了国外的超高强度钢发展道路和认识,坚持研究发展超高强度不锈钢,解决腐蚀问题,提高全寿命期经济可承受性发展方向。经过几年强韧化机理探索,初步获得三个新机理:超细马氏体板条、超细沉淀相M2C、Fe2Mo和逆转变奥氏体。优选了一个合金成分体系:Fe-13Cr-12Co-Mo-Me。在实验室采用VIM+VAR双真空高纯熔炼和控制相变热处理后,抗拉强度接近1900MPa,断裂韧性(KIC)达到110MPam1/2 ,率先把不锈钢提升到了超高强度高韧性。与此同时,还设计了一种表层硬化型不锈齿轮轴承钢Fe-14Cr-12Co-Mo-Nb-Me,力学性能达到σb ~1850MPa,KIC~110MPam 1/2,探索研究的表层超硬-韧化方法可使钢的表面硬度达到HRC70以上,500℃下的硬度保持在HRC63,率先把齿轮轴承钢也提升到了超高强度、高韧性,获得国家发明专利。
经历50多年研究,他的科研成果构筑了我国航空超高强度钢体系架构:低合金钢、中合金钢、高合金钢和不锈钢,发表了数十篇学术论文和“合金钢设计”专著,培养博士生,被誉为“超高强度钢之父”。集多项航空超高强度钢研究创新、工程应用成功、达到和超过国外先进水平,他提出了材料科学与工程“两个全过程”概念,即“材料研制全过程”和“材料应用研究全过程”。将材料科学与工程从“四要素”时代领入了“两个全过程”新时代,新时代的特征是材料兼具极限性能和极限服役性能。当记者问到中国先进材料的发展方向时他坚定地强调了一个字:“纯”!
如今79岁高龄他仍坚守在科研一线,满怀信心地在和年轻同伴们研究创新先进材料,为我们伟大祖国的材料事业继续奉献着光和热!用赵院士自己的话说:“我只是众多科研工作者中的一员,我在做我应该做的事情。我们伟大的祖国走向富强、繁荣,赶超发达国家是我毕生的愿望!”
坚持自主创新路 成就制造强国梦
习近平总书记说过:“实现中华民族伟大复兴的中国梦,就是要实现国家富强、民族振兴、人民幸福”。
中国梦的核心是工业现代化,先进机械制造业是工业化的支柱,高端机械装备制造是强国的主要标志,机械制造直接关系国民经济繁荣、国家安全建设和科技创新战略发展。赵院士创新了抗疲劳制造——新一代先进制造技术。
赵院士说,经历60年发展、特别是改革开放30多年发展中国已经成为一个机械制造大国和世界第二大经济体,正在向机械制造强国迈进,这是一个历史性转变。当前遇到的最大困惑和难题是机械制造升级转型,问题未得解决不仅迟滞转变进程,导致了国民经济下滑,而且这一趋势还会继续。国民经济生产力构成中制造占60%以上,社会财富的60%由机械制造创造,而中国仅占20 %左右,空间和潜力很大,解决了机械制造升级转型问题经济不但不再下行,反而会走上发展快车道。所以,举国上下在探索一条机械制造强国之道。道路是什么,该如何走,赵院士提出了自己的见解:抗疲劳制造是必由之路。
他解释说,高端机械装备制造是高科技传承,产业链和价值链的高端,改变中国引进仿制、竞争弱势的根本出路。高端机械装备制造是一个复杂的体系,如构件、部件到整机的机械结构体系以保证功能,功能、性能与全寿期的成本统一的经济可承受性体系以保证生存等。同时保障这些体系的是长寿命、高可靠,其体现者是关键构件。所谓关键构件包括转动构件、传动构件、主承力构件,它们都在动态下服役,主要失效模式是疲劳。大量机械装备提前失效、失事造成灾难性后果,并非结构存在什么问题,而是由于关键构件疲劳失效。据报,飞机空中解体、火车出轨、塔吊突然倒塌、儿童游乐车突然倒塌居然都是因为对接螺栓疲劳失效。一个不起眼的关键构件失效不仅严重威胁机械装备服役安全、酿成灾难性后果,而且导致机械装备的功能、经济可承受性乃至信誉都荡然无存。可见,没有关键构件高端机械装备制造无疑于无米之炊!中国制造的关键构件存在寿命短、可靠性差、结构重等三大问题,当然无法升级转型到高端机械装备制造。关键构件是设计、材料、制造三位一体技术集成。所以,关键构件必须建立三个技术体系:设计技术体系、材料技术体系、制造技术体系。其中,设计技术体系主司结构,材料技术体系主司强度,制造技术体系主司寿命。设计、材料、制造三个技术各自独立、互不孕育,而融合一体、不可分割,同等重要、不可偏废方能制造出关键构件。但是,长期以来制造不仅没有作为核心技术发展,反而被边缘化了。关键构件和高端机械装备是制造出来的,没有先进制造技术无异于纸上谈兵。中国没有先进制造技术,当然无法制造出关键构件高端机械装备。制造技术、关键构件、高端机械装备制造一脉相承。他讲了一个小故事,早在1950年美国发展民航客机用涡轮喷气发动机拟定寿命30000小时,但被搁浅了,原因是主轴承达不到寿命要求。于是,从选材开始、冶金、制造、试验一路研究,到1960年主轴承寿命达到了30000小时,发动机投入生产、服役。1983年中国研制的一种发动机拟定寿命200小时,也是因为主轴承达不到寿命要求被搁浅。不过,解决办法是有什么用什么。接着研究新型发动机时还是主轴承达不到寿命要求,还是有什么用什么,应付凑合。如今,主轴承制约了发动机和高端机械装备制造。所以,在科学技术发展中没有捷径,该做的事一定要做。今天偷个懒,明天要花更大功夫补偿,甚至贻误大事。
赵院士说,纵观世界机械制造技术已发展三代:“成形”制造、表面完整性制造、抗疲劳制造。所谓“成形”制造就是中国普遍采用的按照设计图纸规定要求制造构件的技术,基本特征是制造与寿命无关。“成形”制造带来两大问题:一是导致高强度材料不敷应用,即诱发疲劳强度应力集中敏感,当应力集中系数Kt=3时疲劳强度降低约50%,Kt=5时降低约80%,高强度铝合金、钛合金、高温合金、超高强度钢、齿轮轴承钢等均如此;二是关键构件提前疲劳失效,即“成形”制造留下的切削刀痕不连续造成了很高的应力集中,该处成为疲劳源,导致构件提前疲劳失效,高强度铝合金、钛合金、高温合金、超高强度钢、齿轮轴承钢构件也均如此,并成为“两大问题”的原因,亟待淘汰。
50年前全世界都和中国现状一样,而美国于1948年到1970年花了20多年时间研究成功表面完整性制造。所谓表面完整性制造是控制表面完整性、以疲劳为判据和提高疲劳强度的制造技术,理论基础是疲劳,关键心技术是切削和表面强化,高强度材料和构件疲劳强度应力集中敏感得到改善。对“成形”制造的最大进步在于表面完整性制造与寿命相关,并取得三大效果:关键构件长寿命、高可靠、结构减重,美国战机F15、F16寿命达到5000飞行小时世界最高水平,西方发达国家普遍采用进而垄断了高端机械装备制造至今已半个世纪,走出了一条机械制造强国道路。这就是西方发达国家制造的关键构件和装备寿命更长,可靠性更高的原因。但是,表面完整性制造认识局限、效果有限,应予跨越。
赵院士和他的团队花了30年时间研究创新一种抗疲劳制造。提出了新概念:抗疲劳制造是控制表面完整性和表面变质层、以疲劳为判据和达到极限疲劳强度的制造技术;提出了新理论:“无应力集中”抗疲劳概念;建立了关键技术体系:抗疲劳制造关键技术体系、极限寿命设计技术体系、极限性能材料体系等,形成了第三代机械制造技术。用以制造的超高强度钢、齿轮轴承钢、耐温高强度钛合金、高温合金疲劳寿命均提高100倍以上;制造的飞机起落架疲劳寿命达到和超过美国F15、F16战机 5000飞行小时世界最高规定寿命,多种飞机使用,从1991年服役至今无一故障;制造的主轴承滚珠接触疲劳寿命达到400万小时,对比试验超过世界领先水平的同一轴承滚珠一个数量级。抗疲劳制造颠覆了材料,推动先进材料跨入“两个全过程”新时代,走上极限性能和高纯净度发展道路;颠覆了设计技术,亟待创新理论和方法,走上极限寿命、极限可靠性、极限减重设计。抗疲劳制造建立了机械制造新理念:从“成形”制造的精密、高效、表面完整性制造的精密、长寿命、高效到抗疲劳制造的精密、极限寿命、高效;关键构件的寿命从“成形”制造的(设定数量级为1)表面完整性制造的10提高到抗疲劳制造的100;抗疲劳制造改变了疲劳失效模式并与制造无关,因而制造的关键构件达到了极限寿命、极限可靠性、极限减重。风水轮流转,遂后大家将看到的是中国制造的关键构件和装备比西方发达国家制造的寿命更长,可靠性更高!
赵院士呼吁,加速抗疲劳制造研究发展,建立抗疲劳制造、极限寿命设计、极限性能材料新三位一体技术体系是机械制造升级转型的当务之急,是提升国民经济发展的根本道路,是实现机械制造强国的根本道路。转变60年养成的习惯和观念,从仿制惯性中挣脱出来,换上创新理念和思维,举国上下聚焦抗疲劳制造,落实措施,一定会在不长时间成就中国成为一个达到和超过西方发达国家的关键构件制造强国和高端机械装备制造强国。表面完整制造曾经为西方发达国家带去了机械制造强国,抗疲劳制造是中国的一个强国机遇,关键是应抓住机遇!
遵守科学规律 实践中华民族伟大复兴梦
采访到科研成果如何获得时赵院士很有感慨地说,他很庆幸自己走上了科学研究道路,但一辈子有太多辛苦;他忠实于科学研究,一辈子奉献给了创新;他乐于科学研究,有诸多成功享受。他说,一个人毕生要做两件事情“一是认识世界求得生存,一是改造世界求得生存好”。一个科研工作者要做三件事:认识科学规律知道能做什么,遵守科学规律并开拓创新,发现科学规律知道该做什么并做到更好。所以,在50多年的科研生涯中他从不吝惜劳苦与智慧,主动把研究目标定在领先国际水平上,不仅连续创新成功多项达到和领先国际水平的成果,而且发现多项科学规律,提出了新概念、新理论、新技术。
1、科学技术“全过程研究”概念
集多项研究成功经历提出了一种科学技术“全过程研究”概念。他推崇科学认识论。科学认识论指出,人类在认识客观世界时需要经历认识、实践,再认识、再实践……认识单元的反复循环才能获得相对真理,只有真理才可用以改造世界。他实践科学认识论,认为科学技术研究是人类认识客观世界的组成部分。把科学技术研究作为一个“全过程研究”,即认识单元,并分解为四个要素:应用基础理论、科学技术、工程化生产和服役失效反馈,四个要素反复循环才能获得相对真知,真知才可用以成就产品和人才。其中,“应用基础理论”直接导向技术创新,“科学技术”是研究创新的主体,“工程化生产”是有价值的形式,“服役失效反馈”是科学技术的可用性;后一个要素是前一要素的归宿与判据,不能导致科学技术创新的应用基础理论是不适用的理论,不能工程化生产并形成有价值的形式的科学技术是无用的,不能适应服役的产品应予抛弃,服役失效反馈是“全过程研究”或一个认识单元的终结。实践是检验真理的唯一标准,“服役失效反馈”理论与“应用基础理论”一致证明“科学技术”是真知,认识结束,不相一致时“全过程研究”反复进行直到一致。
赵院士强调,研究科学技术的目的全在于应用,实践“全过程研究”可以获得可用可靠的科学技术。“全过程研究”是科学技术研究的普遍规律和准则,务必遵守这一科学规律,实施这一准则。因为已有太多的教训:很多科学技术研究者不知道“全过程研究”,更少有人实施“全过程研究”,以致立了很多研究项目获得成功的很少,可用可靠的的成果更少;很多研究者辛劳多年却未做出成果,虚度了年华;不少研究者用非真知教授学生,流传了大量的错误概念,混乱了学术环境,贻误了一代又一代学子。
2、材料科学与工程“两个全过程”概念
纵观千百年人类文明发展史清晰可见材料的身影,经历了石材、木材、铁材、复合材料,材料是人类进步的推动力。如今,先进材料已经发展成为科学前沿,理论、实验达到高水平,具有极限性能特征,极大地推动多种学科发展,殊不知先进材料经历了艰难的发展历程。半个世纪前材料还处于科学和工程分立而相互制约的状态,直到上个世纪70年代美国才找到了一个科学规律:材料科学与工程,结束了混沌状态,推动了材料大发展,并成为高等专业教育的一级学科。到了90年代中又找到了一个新规律:材料科学与工程“四要素”,并推动材料获得极限性能。所谓“四要素”指的是成分、组成与结构,合成与加工,性质和服役行为,西方发达国家普遍采用“四要素”研究材料,材料科学与工程进入“四要素”时代,几年前还发展了“基因设计”。没有规矩不能成方圆。中国也将材料科学与工程列为高等专业教育的一级学科,却未能遵循“四要素”研究材料,甚至知之甚少,导致了与西方发达国家材料的差别和落后状态。
研究材料的目的全在于应用,用得好才是好材料。赵院士研究发现具有极限性能的材料并不一定好用,甚至不可应用。例如,久负盛名的低合金超高强度钢300M具有极限力学性能:抗拉强度σb~1960MPa、屈服强度σ0.2~1625MPa、伸长率δ5~10 %,断面收缩率ψ~40 % 、断裂韧性KIC~80 MPam 1/2、疲劳强度σF ~1035MPa,广泛用做各种飞机起落架。但是,当构件表面压一个硬度压痕造成应力集中后疲劳强度骤降至245MPa,在海水介质中仅为105MPa,因而成为一个不可应用材料。不仅300M钢,高强度铝合金、钛合金、齿轮轴承钢、高温合金同样如此,即疲劳强度应力集中敏感,如不解决,服役中潜在灾难性后果。为此,他提出了材料应用研究概念,研究应用技术,并赋予了材料极限服役性能。例如,300M钢在任何高应力集中下疲劳强度均达到1000MPa以上,真正成为一个可用可靠材料。不仅300M钢,高强度铝合金、钛合金、齿轮轴承钢、高温合金同样如此,即抑制了疲劳强度应力集中敏感。于是,他提出了材料科学与工程“两个全过程”概念:一个是“材料研制全过程”,一个是“材料应用研究全过程”。“材料研制全过程”赋予材料极限性能,“材料应用研究全过程” 赋予材料极限应用性能,“两个全过程” 赋予材料极限服役性能。材料科学与工程进入了“两个全过程”新时代。
3、“无应力集中”抗疲劳概念
赵院士发现了高强度材料疲劳强度应力集中敏感现象和关键构件服役中提前疲劳失效现象,其原因均为高应力集中。在“成形”制造中高应力集中体现为切削加工刀痕不连续处,应力集中很高,并导致高强度材料不敷应用,关键构件“三大问题”;在表面完整性制造中体现为表面强化留下的凹凸处,应力集中较低,材料疲劳强度应力集中敏感程度降低,关键构件恢复到长寿命、高可靠、结构减重。但是,材料疲劳强度应力集中敏感现象和关键构件服役中提前疲劳失效现象的始作俑者仍然是制造,材料和构件的潜力仍未得到充分发挥,威胁服役安全。为彻底解决材料疲劳强度应力集中敏感和关键构件服役中提前疲劳失效问题,赵院士研究了一种抗疲劳制造技术,消除了制造带来的应力集中,疲劳强度应力集中敏感现象得以消除,即不同应力集中下材料疲劳强度均为无应力集中时的材料疲劳强度,从而材料潜能得到充分利用;关键构件服役中提前疲劳失效现象也得以消除,疲劳失效与制造无关,并达到极限寿命、极限可靠性、极限减重。从而提出了“无应力集中”抗疲劳概念:带有应力集中的构件具有无应力集中时的疲劳强度。其核心是从应力集中视角认识疲劳问题,从应力集中入手解决寿命问题。遵照这一理论研究创新了一系列的抗疲劳制造技术,用以制造的不同应力集中高强度铝合金、钛合金、高温合金、超高强度钢、齿轮轴承钢构件疲劳强度全都达到无应力集中时的疲劳强度,应力集中系数越高疲劳寿命提高越多,如应力集中系数Kt=4构件疲劳寿命提高了100倍、甚至1000倍以上。在“无应力集中”抗疲劳概念指导下机械制造技术走上了抗疲劳制造之路,机械制造进入了抗疲劳制造新时代。抗疲劳制造为中国升级转型高端机械装备制造提供了保证,为关键构件制造强国和机械制造强国开启了大门。
赵院士最后强调,科学规律是创新之源,遵守科学规律是创新之本,发现科学规律是创新之魂。尊重科学是中华民族的传统美德,传承并发扬这一美德是中华民族伟大复兴的希望和保证。
后记:“中国梦、强国梦”是中国当代每个仁人志士的理想和奋斗目标。坚定不移地推进中国工业化进程是立国之本和经济发展的必然选择,迈向“制造强国”的关键是发展先进制造技术、材料技术和设计技术,升级转型关键构件和高端机械装备制造。大家行动起来,传承和发扬老一辈科学家无私奉献和坚韧不拔的科研精神,为祖国的美好明天而努力拼搏吧!
人物简介
赵振业,中国工程院院士,金属材料科学家,抗疲劳制造的缔造者。1937年生,1961年毕业于西北工业大学。北京航空材料研究院研究员、博士生导师,中国航空学会材料分会名誉主任委员,北京航空航天学会副理事长。曾任北京航空材料研究院副总工程师,全国热处理学会理事长。
50多年来一直从事航空超高强度钢应用基础理论、合金设计和应用技术专业研究。主持超高强度钢300M应用研究,研究成功中国第一个VIM+VAR高纯净超高强度钢300M,提出“应用研究”概念,建立应用技术体系,用其制造的起落架疲劳寿命达到6000飞行小时未失效,达到并超过国外5000飞行小时最高规定寿命;主持研制成功国内外第一个航空中温超高强度钢38Cr2Mo2VA ,研制成功中国第一个12%Cr钢GX-8,率先将不锈钢、不锈钢齿轮轴承钢提升到超高强度高韧性水平。研究成果构筑了中国航空超高强度钢体系架构并达到世界先进水平,广泛应用于10多种先进型号飞机和发动机关键构件至今数十年无故障。提出“材料研制”和“材料应用研究”“两个全过程”概念,引领材料科学与工程进入了一个新时代。30多年来赵振业研究抗疲劳制造,提出新概念、新理论和关键技术体系,建立了机械制造新理念,用以制造的各种高强度合金高应力集中构件疲劳寿命提高100倍以上,超过国外先进水平。颠覆了材料,推动先进材料走上极限性能、高纯净道路;颠覆了设计,推动理论和方法创新,发展极限寿命设计。将机械制造领入了以极限寿命、极限可靠性、极限减重为特征的抗疲劳制造新时代,为中国升级转型高端机械装备制造提供了核心技术,为制造强国开启了大门。曾荣获国家科技进步一等奖、国家发明三等奖等国家级科技成果奖5项,合金发明专利2项,发表学术论文60余篇,专著《合金钢设计》。
声明: 本网原创,转载时请务必标明文章来源和作者信息。未经允许, 严禁用于商业用途。
免责声明:本网站所转载的文字、图片与视频资料版权归原创作者所有,如果涉及侵权,请第一时间联系本网删除。
-
标签: 赵振业, 抗疲劳制造, 中国航发北京航空材料研究院, 中国工程院
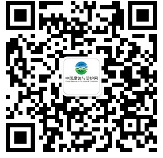
官方微信
《中国腐蚀与防护网电子期刊》征订启事
- 投稿联系:编辑部
- 电话:010-62316606-806
- 邮箱:fsfhzy666@163.com
- 中国腐蚀与防护网官方QQ群:140808414