含焊接缺陷的横梁底板疲劳裂纹扩展速率
2014-08-11 16:20:09
作者:本站整理来源:=$docheckrep[1]?ReplaceBefrom($ecms_gr[befrom]):$ecms_gr[befrom]?>
张瑞金*,谢里阳*,张啸尘*
*(东北大学机械工程与自动化学院,沈阳 110819)
*(东北大学机械工程与自动化学院,沈阳 110819)
摘要:由于焊接工艺的原因,某车型横梁底板与补板焊接深度小于补板厚度,在理论分析中,可以将底板与补板之间存在未焊透区域近似处理为等效板面裂纹。车体服役过程中,在垂直于裂纹面的交变应力作用下,初始裂纹可能会发生疲劳扩展,裂纹扩展进入边梁翼板,可引发边梁裂纹,影响车体结构安全。本文通过有限元数值模拟和疲劳裂纹扩展试验,研究了含焊接缺陷的横梁补板裂纹在Ⅰ型加载条件下的疲劳裂纹扩展规律,采用ANSYS 的APDL 程序化语言编程建立模型,并对其进行数值模拟分析,得到了在不同裂纹长度下应力强度因子,拟合出裂纹尖端的应力强度因子公式,得到横梁底板-补板焊缝在不同水平的循环应力作用下的疲劳裂纹扩展寿命。
关键词:焊接,疲劳裂纹,应力强度因子,扩展速率,有限元模拟
Fatigue Crack Growth Rate of Crossbeam Soleplate with Welding Defects
Zhang Ruijin,Xie Liyang,Zhang Xiaochen
( Mechanical Engineering School, Northeastern University,Shenyang 110819,China )
Abstract:Due to the reason of welding technology, the welding depth between the soleplate and the cover plate on Crossbeam is less than the thickness of cover plate. In theoretical analysis, this welding defect can be conservatively considered as an equivalent surface crack. In the serving life of aHigh-Speed Electric Multiple Units (EMU) Train, initial cracks may propagate under alternating fatigue stress. When the fatigue cracks extend into the edge plate, it will be very dangerous to the whole structure. Using the FEM simulation and fatigue crack propagation test, this paper studied the fatigue crack propagation process on the crossbeam with welding defects. On the basis of ANSYS APDL programming language, the stress intensity factors were calculated with different crack length, then the formula of the crack tip stress intensity factor could be fitted. Furthermore, fatigue crack propagation life could be got under different levels of cyclic stress.
Key words:Welding, Fatigue Crack, Stress Intensity Factor, Growth Rate,FEM Simulation
联系方式
张瑞金:rjzhang@mail.neu.edu.cn
关键词:焊接,疲劳裂纹,应力强度因子,扩展速率,有限元模拟
Fatigue Crack Growth Rate of Crossbeam Soleplate with Welding Defects
Zhang Ruijin,Xie Liyang,Zhang Xiaochen
( Mechanical Engineering School, Northeastern University,Shenyang 110819,China )
Abstract:Due to the reason of welding technology, the welding depth between the soleplate and the cover plate on Crossbeam is less than the thickness of cover plate. In theoretical analysis, this welding defect can be conservatively considered as an equivalent surface crack. In the serving life of aHigh-Speed Electric Multiple Units (EMU) Train, initial cracks may propagate under alternating fatigue stress. When the fatigue cracks extend into the edge plate, it will be very dangerous to the whole structure. Using the FEM simulation and fatigue crack propagation test, this paper studied the fatigue crack propagation process on the crossbeam with welding defects. On the basis of ANSYS APDL programming language, the stress intensity factors were calculated with different crack length, then the formula of the crack tip stress intensity factor could be fitted. Furthermore, fatigue crack propagation life could be got under different levels of cyclic stress.
Key words:Welding, Fatigue Crack, Stress Intensity Factor, Growth Rate,FEM Simulation
联系方式
张瑞金:rjzhang@mail.neu.edu.cn
责任编辑:赵泽南
《中国腐蚀与防护网电子月刊》征订启事
投稿联系:刘娟 电话:010-82387968-807
QQ: 2850329508 邮箱:liujuan@ecorr.org
中国腐蚀与防护网官方 QQ群:140808414
相关文章
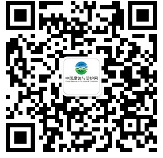
官方微信
《中国腐蚀与防护网电子期刊》征订启事
- 投稿联系:编辑部
- 电话:010-62313558-806
- 邮箱:fsfhzy666@163.com
- 中国腐蚀与防护网官方QQ群:140808414
点击排行
PPT新闻
铝合金LDH自修复自抗菌膜层构建
点击数:466
碳钢及合金钢应用与区别
点击数:393