刘洲,于美,刘建华*,李松梅
(北京航空航天大学 材料科学与工程学院 北京 100191)
liujh@buaa.edu.cn
作者简介:
刘建华博士、教授、博士生导师,北航材料科学与工程学院材料物理与化学学科责任教授。
1978年-1982年湖南大学金属腐蚀与防护专业本科毕业。1982年-1984年湖南大学化学化工系硕士课程毕业留校工作。1987年-1991年日本神户大学自然科学研究生院材料专业博士课程毕业。1992年6月晋升为教授,并荣获享受国家政府特殊津贴专家称号。1993年-1995年加拿大国家科学研究院作为高级访问学者从事合作研究。1995年8月- 北京航空航天大学材料科学与工程系教授。1997年晋升为材料专业博士生导师。1996年-1997年北京航空航天大学材料科学与工程系研究生指导主任。1997年-2000年北京航空航天大学材料科学与工程系103教研室副主任、主任。2000年-2008年北京航空航天大学材料科学与工程学院副院长。1997年至今被任命为北京航空航天大学校学术委员会委员。2002年起担任北京腐蚀与防护学会副理事长,2010年起担任中国腐蚀与防护学会理事。
近十余年来,承担国家自然科学基金、省部级科学基金项目和重大项目十多项,研究工作涉及材料科学、材料腐蚀科学与表面防护先进技术、纳米材料与功能涂层材料技术、应用电化学技术等。特别是在航空腐蚀科学与防护工程技术、航天环境装备防护工程技术、腐蚀失效预测、表面防护先进技术和纳米材料技术等方面取得了重要进展,获批国家发明专利16项,在国内外主要刊物和国际会议上发表论文260余篇,其中大多数被SCI、EI等收录;已获省部级科技进步二等奖、三等奖各4次
摘 要:本文研究了45号钢上电镀锌镍和化学镀镍磷双层膜的制备及耐腐蚀等性能。用金相显微镜观察了镀层的形貌,采用中性盐雾实验和全浸实验研究了锌镍和镍磷双层膜的腐蚀情况。结果表明,锌镍为底层镍磷为面层的双层膜呈三维网状结构,锌镍底层沿着晶界出现微裂纹,提高了膜层之间的结合力,且影响到该双层膜的耐蚀性能。当镍磷做面层时,镍磷层发生点蚀后,锌镍底层开始代替基体腐蚀。当锌镍做面层时,锌镍层为牺牲阳极,其腐蚀产物能附着在镍磷底层上,延缓镍磷层的点蚀发生。
关键字:双层膜;锌镍镀层;微裂纹;镍磷镀层;耐蚀性
1 引言
由薄层金属交替叠加而构成的多层镀层具有比单一镀层更好的机械性能,如硬度、强度、杨氏模量等,会有不同程度的提高[1]。刘道新等人证明了Ag/Ni多层膜能改善钛合金的磨损与疲劳性能[2],田修波等人研究提出菌的TiN/Cu2Zn纳米多层膜[3]。还有人提出,使用电化学方法制备能够更加方便地获得多层膜,还能克服基体形状尺寸等问题[4]。
镍基合金化学镀层厚度均匀,不受沉积表面形状和尺寸的影响,并且具有耐蚀耐磨双重性质以及其他特殊性能[5-7],各种化学镀层已在许多领域得到了广泛应用[8-10]。且化学镀镍还在铝合金、镁合金等基材上运用,拥有良好的防护性能[11,12]。
锌镍合金镀层在保护钢铁件方面优点突出,耐蚀性比锌镀层高7~10倍,且氢脆敏感性很小[13]。近年来,国内已将电镀Zn- Ni合金应用于电缆桥架、煤矿井下液压支柱、汽车钢板、五金工具及军工产品等,大大提高了产品的耐蚀性能,并节省了原材料[14]。
本文以提高耐蚀性为出发点,重点探讨了电镀锌镍和化学镀镍磷互为底层、面层的情况下双层膜的形貌、腐蚀情况,研究锌镍层和镍磷层在多层膜中的不同作用,从而为进一步研究多层膜腐蚀情况以及应用做准备。
2 实验
采用45号钢作基底材料,试样的尺寸是30mm × 20mm × 1.2mm。施镀前,试样先打磨至500目金相砂纸,然后用丙酮超声清洗5min,在70℃的碱液中除油,在5%稀盐酸中活化45 s,其中每步操作之间均用去离子水冲洗,之后立即放入镀液中施镀。
电镀锌镍合金和化学镀镍磷的镀液成分及工艺参数如表1所示。
表1 电镀锌镍和化学镀镍的配方及工艺参数
镀液 | 镀液成分 | 操作条件 |
电镀Zn-Ni合金镀液 | ZnO 20g/L,NaOH 120g/L,NiSO4·6H2O 5g/L,三乙醇胺 40ml/L,四乙烯五胺 20ml/L, 添加剂适量 | 温度 25℃; 电流密度 2A/dm2 |
化学镀Ni-P镀液 | NiSO4·6H2O 30g/L,NaH2PO2·H2O 20g/L,柠檬酸铵 50g/L | pH 9.0; 温度 90℃ |
双层膜A:前处理——电镀锌镍5min——去离子水洗——化学镀镍10min——水洗——吹干,即锌镍为底层镍磷为面层。
双层膜B:前处理——化学镀镍10min——去离子水洗——电镀锌镍5min——水洗——吹干,即镍磷为底层锌镍为面层。
采用BX51M型金相显微镜观察镀层的表面和截面形貌。通过全浸和盐雾试验考察镀层的耐蚀性能。
全浸实验——配置5%的NaCl溶液,将试样浸泡其中,置于室温下,观察出现锈斑的时间,以及锈斑随时间的变化情况。
盐雾试验——按照GB6458-86金属覆盖层中性盐雾实验标准进行。盐雾配液质量浓度为5%,温度控制在35±2℃,恒温。条件控压阀,使干净湿化的气源压力控制在70~170kPa范围内。将试样置于盐雾箱内,观察出现锈斑的时间,以及锈斑随时间的变化情况。
3 结果与讨论
2.1 双层膜形貌
在钢基体上电镀锌镍后,马上进行化学镀镍,即双层膜A,其截面形貌如图1(a)所示。图中,由下至上依次为钢基体、锌镍层(暗色)、镍磷层(亮色),两种镀层的厚度均约为3μm。可以看出,锌镍层不完整,破损成小段,而镍磷层则如钉状扎入锌镍层,直接与基体连接。综合双层膜的表面等形貌,可以发现双层膜A形成了三维网状结构,具体结构如图1(b)所示。
图1 双层膜A金相图及示意图
在钢基体上化学镀镍后,马上进行电镀锌镍,即双层膜B,其截面形貌如图2(a)所示。图中,由下至上依次为钢基体、镍磷层(暗色)、锌镍层(亮色),两种镀层的厚度均约为3μm。电沉积时一般不会对基体产生影响,故电镀锌镍后,镍磷层将保持完整,镀层均匀。其镀层示意图如图2(b)所示。#p#副标题#e#
图2 双层膜B示意图
在制备双层膜A过程中,碱性环境下,镍磷镀液会对锌镍层产生侵蚀,使锌镍层出现微裂纹,如图3所示。我们可以看到,整个镀层呈均匀的开裂,裂纹分布有一定的规律性。且被粗大裂纹划分后的小块区域中还有细微的小裂纹。
图3 锌镍层在化学镀液中受侵蚀后产生的微裂纹
为了研究裂纹的形成原因,以及三维结构的形成,分别将锌镍镀层置于镀液A(无还原剂且无硫酸镍)和镀液B(仅无还原剂)中,均在10min后取出,其表面金相图如图4所示。
图4 锌镍镀层置于两种镀液后的表面金相图
从图4可以看到,两者均出现微裂纹,且置于镀液A中的镀层微裂纹密度较大。由图4a可知,由于镀液中既没有还原剂,又没有镍离子的存在,所以裂纹应该是锌镍层自身开裂的结果。而镀液B中由于镍离子的存在,少量镍离子被锌还原,沉积在部分裂纹处,导致裂纹密度的降低,如图4b所示。
将锌镍镀层进行显晶后的金相图如图5所示。
图5 金相显微镜下锌镍镀层晶界
由图5中显示的晶界可知,锌镍镀层裂纹的产生是沿着晶界进行的。由于合金的晶界处电极电位更负,因此,在腐蚀介质中,锌镍镀层的境界会发生腐蚀,且逐渐溶解掉。由于锌镍镀层本身具有较大的内应力,配合上基体本身的残余加工应力,在热环境下发生开裂,产生微裂纹。微裂纹产生后,镍磷继续沉积,且进入到微裂纹中,从而形成三维的网状结构。
2.3 双层膜耐蚀性能
2.3.1 双层膜A的腐蚀情况
双层膜A在盐雾实验中的腐蚀变化如图6所示,图中(a)(b)(c)分别为放入盐雾箱3d,10d,14d后的腐蚀情况。可以看到,在3d时就已开始出现锈斑,但此时锈斑仍然很小。到10d时,锈斑迅速长大,占到总面积的30%。
图6双层膜A的盐雾实验照片
图7为盐雾实验两周后双层膜A的腐蚀照片及腐蚀模型。图7(a)中可以发现,双层膜表面发生破裂,露出下层的微裂纹。
锌镍合金和镍磷合金的电极电位分别约为-0.80V和-0.25V。在双层膜腐蚀过程中,镍磷层作为阴极性膜层保护基体。由于镍磷镀层在腐蚀过程中不是均匀消耗,其镍的消耗比磷快[15],并产生孔蚀[16]。孔蚀发生后,溶液从微孔中渗入后镍磷层与锌镍层符合电偶腐蚀条件,锌镍层电极电位较负,开始发生腐蚀溶解。腐蚀产物也沿着微孔堆积,最后堆积到镍磷层表面,其示意图如图7(b)所示。在去除腐蚀产物后,如图7(a)所示,露出微裂纹,说明点蚀坑倾向于出现在微裂纹附近。
图7双层膜A的腐蚀照片及模型
2.3.2 双层膜B的腐蚀情况
双层膜B在盐雾实验中的腐蚀变化如图8所示,图中(a)(b)(c)分别为放入盐雾箱3d,10d,14d后的腐蚀情况。可以看到,其锈斑生长很慢,到10d时才在局部区域出现微小的锈斑,小于总面积的5%。到14d时才出现明显的锈斑,达到总面积的5%。
图8双层膜B的盐雾实验照片
图9双层膜B腐蚀后金相图及模型
图9为全浸实验两周后双层膜B的金相图及腐蚀模型。图9(a)中最下面为钢基体,再往上颜色较深的为镍磷层,镍磷层保持得很完整,没有出现点蚀或者破损。紧贴着镍磷层往上,颜色较浅的是残留的锌镍层,此时的锌镍层已经极薄,其截面示意图如图9(b)所示。#p#副标题#e#
当锌镍作面层时,其相对于镍磷层为阳极,会被不断消耗,呈全面腐蚀状况,整个锌镍层均匀减薄。锌镍镀层的腐蚀产物ZnCl2·4Zn(OH)2均匀覆盖在镍磷镀层表面,且不易导电[12],可以较好的延缓镍磷层的点蚀发生。因此,当锌镍作为面层防护时,能有效地作为代牺牲镀层,在消耗完锌镍层后,腐蚀才能进一步深入,起到了很好的防护作用。
2.3.3 两种双层膜的耐蚀性比较
全浸实验和盐雾实验中,两种镀层的红锈锈斑大小随时间的变化曲线如图10。
(1)全浸实验 (2)盐雾实验
图10 两种双层膜的全浸实验和盐雾实验结果
由图10可知,全浸实验中,双层膜B在两周内几乎没有红锈产生,而双层膜A在1d后就开始出现红锈,并且每天都有增加,不过占的比例很小,两周后才到5%。
盐雾实验中,双层膜B的红锈生长极为缓慢,两周后仅达到5%。而双层膜A则相对较快,3d后红锈面积就已达到5%(图8)。
从两个实验中都可以看到,双层膜B较双层膜A具有更佳的耐蚀性。双层膜A的镍磷层破坏后出现点蚀坑,露出锌镍层后呈大阴极小阳极状态,锌镍消耗较快;双层膜B由于锌镍作面层,消耗速度较A的慢,呈均匀腐蚀状态。且腐蚀产物堆积在镍磷层表面,延缓了镍磷层的腐蚀破坏。因此,双层膜B比双层膜A有更佳的耐蚀性。
4 结论
(1)在制备双层膜A(镍磷作面层、锌镍作底层)时,锌镍底层会产生微裂纹,镍磷面层与锌镍底层以三维网状结构结合。且锌镍层微裂纹是沿着晶界产生的。
(2)与双层膜B(锌镍作面层、镍磷作底层的双层镀层)相比,双层膜A具有良好的耐磨性,镍磷层如钉状深扎入锌镍层,并直接接触到钢基体,加强了镀层之间的结合力。
(3)双层膜A在腐蚀过程中,镍磷层能较好地起到阻挡作用,面层破损后锌镍底层能代替基材腐蚀。双层膜B,面层能很好地完成牺牲阳极作用,且面层的腐蚀产物能延缓底层的点蚀发生。
(4)在多层膜的应用中,镍磷层与锌镍层的三维网状结合方式能较好的保证多层膜的膜层间结合力,锌镍层优秀的代牺牲能力以及镍磷层良好的阻挡能力,使这两种镀层组成的多层膜具有良好的性能。
References(参考文献)
[1] SUN Zhi-hua, LIU Ming-hui. Status Quo of Research on the Electrochemical Formation of Laminar Multilayer[J]. Corrosion and Protection, 2002, 23(3): 114-116(Ch).
孙志华, 刘明辉. 应用电沉积方法制备纳米多层膜的研究现状[J]. 腐蚀与防护, 2002, 23(3): 114-116.
[2] LIU Dao-xin,WANG Zhen-ya. The Effect of Ag/Ni Multilayer Film on Fretting Wear and Fretting Fatigue Resistance of Titanium Alloy[J]. TRIBOLOGY, 2010,30(5): 498-504(Ch).
刘道新, 王振亚. Ag/Ni多层膜对钛合金微动磨损和微动疲劳抗力的影响[J]. 摩擦学学报, 2010,30(5): 498-504.
[3] Wei Chunbei, Gong Chunzhi. Corrosion and Antibiotic Properties of Magnetron Sputtered TiN/Cu-Zn Nanomultilayers[J]. CHINESE JOURNAL OF VACUUM SCIENCE AND TECHNOLOGY, 2010, 30(1): 96-100(Ch).
韦春贝, 巩春志. 磁控溅射TiN/Cu2Zn纳米多层膜腐蚀和抗菌性能研究[J]. 真空科学与技术学报, 2010, 30(1): 96-100.
[4] Yao Su-wei, GUI Feng. STUDY ON ELECTRODEPOSITING NANOSTRUCTURE MULTILAYERS[J]. Journal of Tianjin University, 2001, 34(2): 261-264(Ch).
姚素薇, 桂枫等. 电沉积纳米金属多层膜研究[J]. 天津大学学报, 2001, Vol.34, No.2.
[5] Michael J, Dvorchak. Water-Reducible Unsaturated Polyesters as Binders and Clear Coatings for UV-Curable Furniture Coatings[J]. Journal of Coatings Technology, 1992, 64(5): 43-49.
[6] Chang-sik HA. Properties of UV-Curable Polyurethane Acrylates Using Nonyellowing Polyisocyanate for Floor Coating[J]. Journal of Applied Polymer Science, 1996, 62(7): 1011-1021.
[7] Chen-yang Y W. New UV-Curable Cyclotriphosphazenes as Fire-Retardant Coating Materials for wood[J]. Journal of Applied Polymer Science, 1998, 69: 115-122.
[8] Soon-jcon Jung. Synthesis and Properties of UV-Curable Waterborne Unsaturated Polyester for Wood coating[J]. Journal of Applied Polymer Science, 1998, 69: 695-708.
[9] 奚惠兰,胡和丰.紫外光固化木器涂料性能研究——齐聚物对涂膜性能的影响[J]. 涂料工业, 1997(1): l0-11.
[10] Zhang X.L., Liu J.H., Li S.M. Fabrication and magnetic properties of Co-Ni-P rod-shaped hollow structures based on Bacillus template[J]. Materials Letters, 2009, 63(22): 1907-1909.
[11] HU Yong-jun, CHENG Xiao-ling. Effect of catalytic activity of aluminum alloy on the chemical composition and corrosion resistance of electroless Ni–Cu–P alloy deposit[J]. Electroplating and Finishing, 2010, Vol.29, No.8: 18-23(Ch).
胡永俊, 成晓玲等. 铝合金表面催化活性对化学镀镍–铜–磷合金镀层化学组成及耐腐蚀性能的影响[J]. 电镀与涂饰, 2010, Vol.29, No.8: 18-23.
[12] CHANG Li-min, SUN Xiao. Research progress of electroless nickel plating on magnesium alloy[J]. Electroplating and Finishing, Vol.29, No.9: 25-29(Ch).
常立民, 孙小. 镁合金化学镀镍研究进展[J]. 电镀与涂饰, 2010, Vol.29, No.9: 25-29.
[13] XU Ai-zhong, WEN Bin. Research Development of Anticorrosive Mechanism of Zn-Ni Alloy Coatings[J]. Electroplating and Pollution Control,2000, 20(3): 1-5(Ch).
许爱忠, 文彬. 锌镍合金耐蚀机理研究进展[J]. 电镀与环保, 2000, 20(3): 1-5.
[14] TIAN Wei, XIE Fa-qin. Research Development of Zn-Ni Alloy Electroplating[J]. Material Protection, 2004, 37(4): 26-29(Ch).
田伟, 吴向清, 谢发勤. Zn-Ni合金电镀的研究进展[J]. 材料保护, 2004, 37(4): 26-29.
[15] H.B. Lee, D.S. Wuu. Wear and immersion corrosion of Ni-P electrodeposit in NaCl solution[J]. Journal of Tribology International, 2010, 43: 235-244.
[16] 严文, 卢长安, 白真权等. Ni-P镀层防腐性能的电化学研究[A]; 2006西部油田腐蚀与防护论坛[C], 2006年.
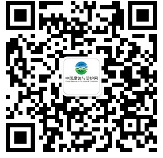
官方微信
《中国腐蚀与防护网电子期刊》征订启事
- 投稿联系:编辑部
- 电话:010-62313558-806
- 邮箱:fsfhzy666@163.com
- 中国腐蚀与防护网官方QQ群:140808414