文/ 马娜,王理·反应堆燃料及材料国家级重点实验室
秦金光·江苏核电有限公司
作者简介
马娜,助理研究员,硕士,2011年毕业于中国核动力研究设计院反应堆燃料及材料专业,目前从事反应堆材料结构与性能研究,及核电站技术服务领域工作。
本文以某核电站大修时发现壁厚减薄超标而更换下来的管道件为研究对象,通过成分分析、微观形貌分析和氧化膜分析等手段,结合管道的运行工况环境分析,最终明确了这些管道的壁厚减薄模式分别为冲刷腐蚀、流动加速腐蚀和汽蚀,并提出针对性改进措施建议。
核电站二回路的主蒸气管道、主给水管线、凝结水管线、疏水管线、部分抽气管线等用材主要是碳钢。近年来,许多核电站出现了二回路碳钢管道壁厚减薄现象,并由此引发了不少安全事故。1986年发生在美国Surry核电站中的冷凝水管道弯头破裂事故,以及2004年发生在日本Mihama核电站中的给水管道破裂事故,均造成了人员伤亡。研究表明,这些管道发生破裂都是管道出现严重的壁厚减薄导致的。
某核电站在大修的超声检查中发现,二回路中部分小规格(管径小于50mm)的弯管、弯头和孔板出现了破口或壁厚减薄现象。针对此情况,在被更换下的壁厚减薄管道中选取了一些典型管段进行分析,并根据分析结果给出应对措施建议。由于管道样品较多,本文仅给出具有代表性的两个弯管和一个孔板管道样晶的分析过程。
样品选取
本文选取了三个样晶进行分析:I号为疏水系统中的弯管,2号为给水系统中的弯管,3号为疏水系统中的孔板。比较I号、2号弯管,研究流速对于壁厚减薄的影响;比较1号弯管、3号孔板,研究管内流体状态对壁厚减薄的影响。三个管道样品材料均为20G优质碳钢,其样品尺寸信息和服役工况如表1所示。
1号弯管位于该核电站2号机组主蒸汽系统的高压疏水管线系统中,高压疏水器前,控制阀后。主蒸汽系统压力远高于疏水系统的压力,故高压管线疏水系统中流速较高。从该核电站系统流程图册中可以发现,在1号机组的相同位置设置有节流孔板,相应弯管并未发生壁厚减薄现象。而1号弯管所在的2号机组相应位置并未设置节流孔板,弯管发生明显壁厚减薄。
2号弯管位于给水系统的低压加热器和高压加热器之间,除氧器之后,属于给水泵出口逆止阀的旁路管道,弯管下游为一个旁路阀。一般情况下,旁路阀是闭合的,当给水泵单向阀出现故障或进行检修时才打开旁路阀,给水通过旁路阀进入高压加热器。特殊情况下,流体可以经该旁路进入除氧器,对除氧器进行清洗。由上述分析可知:2号弯管内为经过除氧的给水,水质较好,且水温较高;弯管内长期有给水存在,可以传质,但是由于旁路阀不常打开,故传质速度较慢。
3号节流孔板位于I号机组的高压管线疏水线上,控制阀后,疏水器前,与1号弯管位置类似。孔板前后焊缝间长度为75mm,孔径为10mm,孔长22mm,两侧为120度梯形过渡,核电站二回路蒸汽管道中的凝结水经疏水管线汇入高压疏水器内,由于主蒸汽系统压力远高于疏水系统的压力,故管中流速较高。
将上述管道样品沿轴向和周向锯开并实测发现:1号弯管严重减薄(约1.5mm),内壁黑色发亮,有尖锐的冲刷痕迹;2号弯管壁厚轻微减薄(约0.3mm),内壁呈暗红色;3号节流孔板在距离焊缝10mm处出现腐蚀穿孔,穿孔附近壁厚减薄明显且表面粗糙,呈漩涡状冲刷痕迹。三个样品的局部形貌如图1所示。
为了研究上述管道壁厚减薄的原因,进行了相关分析工作。
试验结果
化学成分分析
采用电感耦合等离子体一原子发射光谱(ICP一AES)仪和碳、硫专用分析仪对上述管道样品进行了化学成分分析,并与GB5310一2008(高压锅炉用无缝钢管)进行比较,结果如表2所示。可以看出:管道中的Mn、Si、P等元素含量均符合标准的要求,但1号弯管中C元素含量偏低,s元素含量是国标中限值的两倍多。2号弯管中s元素含量也是国标中限值的两倍多。
金相分析
取上述管道样品进行镶样、研磨、抛光,用2%硝酸-酒精刻蚀,置于金相显微镜下观察其金相组织,结果如图2所示:样品的金相组织正常,由铁素体晶粒和呈网状分布的珠光体构成,夹杂物较少,表层无脱碳现象。
微观形貌分析
利用扫描电子显微镜(SEM)观察发生壁厚减薄部位基体的形貌特征。管道表面附着一层黑色或暗红色的氧化膜,采用克拉克溶液100g浓HCL+2gSb203+5gSnCL)进行了管道样品的脱氧化膜处理,以便观察基体。SEM下基体的微观形貌如图3所示。
1号弯管肘部内壁在低倍下可见波纹状形貌,高倍下可见表面较明显的韧窝,局部有材料损失,说明管道内壁在外力作用下发生塑性形变,并且有材料剥落现象。2号弯管在低倍下观察到表面呈鱼鳞状分布的凹坑,尺寸约为200~300μm.高倍放大情况下,可见铁素体晶粒及晶粒中不同取向的晶面,无明显的机械形变特征。3号节流孔板表面可见大量细微的韧窝,尺寸为几微米到十几微米不等,明显小于碳钢晶粒,说明材料表面的各细微局部均分别受到了外力作用。
表面膜分析
对管道样品原始内壁的氧化膜进行了Ⅹ射线衍射分析,结果如图4所示。1号弯管内壁尽管呈黑色,但是氧化膜衍射峰中Fe304特征峰很低,说明表面氧化膜非常薄,证明其生成时间很短。2号弯管内壁检测到了中等强度的Fe304特征峰,说明该弯管表面氧化膜相对较厚,存在时间较长。3号节流孔板内壁检测出了较弱的Fe304特征峰,说明表面有氧化膜,但较薄。
分析讨论
1号弯管
C元素作为一种强化元素,可以提高碳钢的强度和硬度,从而提高耐磨损、耐冲刷腐蚀的能力。1号弯管中C元素含量偏低,使得其硬度降低,耐磨性下降,耐冲刷腐蚀的能力下降。1号弯管处于高压疏水管线,内部流速较高,与流体接触的表面在高速流体的作用下,表面材料不断被冲蚀掉,导致管道减薄。由于表面材料不断损失,故氧化膜不易留存,因而也起不到保护基体的作用。
另外,钢中的S是有害元素,会与Mn元素形成MnS塑性非金属夹杂物,影响钢的抗氢致裂纹(HIC)和抗硫致应力开裂(SSC)性能。但无论是金相分析还是微观形貌分析,都未观察到其对壁厚减薄的直接影响。
通过上述分析认为,1号弯管内的高速流体导致管道受到冲刷作用,发生壁厚减薄,属于冲刷腐蚀。若在其上游设置节流孔板,将增加管道中的流动阻力,降低流体的压力,起到保护管道的作用,避免管道发生因冲刷腐蚀导致的减薄。
2号弯管
2号弯管表面氧化膜是三类样品中最厚的,且基体无可见的形变特征和机械作用导致的材料损失,说明氧化膜隔离了流体对基体的直接作用。从工况条件分析,2号弯管位于给水系统的旁路,内部流速缓慢,不足以对管道材料产生冲刷作用。但流动的介质加速了氧化膜的溶解和氧通过氧化膜向基体的扩散,导致氧化膜在溶解的同时也不断生长,最终使管壁减薄,符合流动加速腐蚀的过程。另外,2号弯管微观形貌呈鱼鳞状,也属于典型的流动加速腐蚀形貌。
尽管2号弯管中的S元素含量也偏高,但分析中同样未观察到其对壁厚减薄的直接影响。
通过上述分析认为,2号弯管发生壁厚减薄的特征表现为氧化膜的加速溶解和生长,属于流动加速腐蚀。根据目前对流动加速腐蚀的认识,更换碳钢材料,使用Cr含量高于1%的低合金钢是较有效的途径。对于正在使用的碳钢管道,应加强管道壁厚的监测。
1、2号弯管虽然同属于弯管,但内部流速差异很大,因此发生壁厚减薄的机理完全不同,处理方式也截然不同,在工程实际中应注意区别。
3号孔板
与1号弯管相比,3号节流孔板下游的弯管并未发生明显的壁厚减薄现象,说明节流孔板的存在确实可以降低流速、降低流体压力,从而避免管道发生因高速流体导致的冲蚀减薄。但是3号孔板自身出现了减薄穿孔,在损伤表面观察到的大量细微韧窝,说明材料表面的各细微局部均分别受到了外力的作用。
分析其工况认为,外力的来源与流体经过孔板时产生的气泡有关:流体经过孔板时压力下降,低于流体的饱和蒸汽压力,于是产生气泡,即闪蒸;当下游流体的压力回升,气泡发生溃灭,对材料局部造成巨大冲击,即汽蚀。从材料已发生的微区塑性变形来看,其原因主要为汽蚀。
综上,尽管3号孔板有效抑制了下游弯管的冲刷腐蚀,但该节流孔板的结构形式导致流体通过时对孔板材料产生了汽蚀作用,导致孔板壁厚减薄并穿孔。因此应优化节流孔板的设计或者使用多级节流孔板。
结束语
经过上述分析,得出以下结论。
(1)1号弯管内的高速流体导致了冲刷腐蚀,造成管壁减薄。解决措施为:①在管道适当位置安装一定的分流系统来分担流量,或增大管径,降低管道中的流速。②提高管道中Cr元素含量,使用更加耐冲刷腐蚀的低合金钢或不锈钢。③减少弯管的使用或增大弯管的曲率半径,缓解由于流体方向改变而造成的扰流程度。
(2)2号弯管内发生的是以氧化膜加速溶解和生长为特征的流动加速腐蚀。解决措施为:①提高钢管中的Cr元素含量或更换耐流动加速腐蚀的材料(如不锈钢)。②控制氧浓度在合理的范围内(主要通过控制加入联氨的量),控制腐蚀发生的环境。③加强对流动加速腐蚀敏感区域的壁厚测量力度。
(3)流体经过节流孔板时产生气泡溃灭导致对材料的汽蚀是3号孔板壁厚减薄、穿孔的原因。解决措施为:①根据具体的使用工况(如系统的流量、流速等)重新设计孔板,如孔径、孔板厚度等。②设计多级孔板,通过多次降压,避免汽蚀的发生。
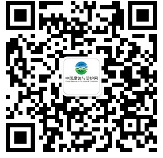
官方微信
《中国腐蚀与防护网电子期刊》征订启事
- 投稿联系:编辑部
- 电话:010-62313558-806
- 邮箱:fsfhzy666@163.com
- 中国腐蚀与防护网官方QQ群:140808414