王勇1,2郑玉贵1,* 姚治铭1 柯伟1 孙文海3 王建强3
1中国科学院金属研究所 金属腐蚀与防护国家重点实验室,沈阳,中国,110016
2东北石油大学 材料科学与工程系,大庆,中国,163318
3中国科学院金属研究所 沈阳材料科学国家(联合)实验室,沈阳,中国,110016
*通讯作者E-mail: ygzheng@imr.ac.cn
摘 要:采用HVOF喷涂方法在304不锈钢基体上制备了一种FeCrMoMnWBCSi非晶态合金涂层。用扫描电镜(SEM)和X射线衍射仪(XRD)等对涂层的微观形貌及成分进行了分析表征。采用电化学腐蚀测试和旋转圆盘冲蚀的方法对涂层和304不锈钢在模拟海水介质中的腐蚀及冲蚀性能进行了研究。结果表明:在1% NaCl溶液中,304不锈钢具有较低的点蚀抗力,涂层表现出较宽的钝化区间和较高的钝化电流密度,表明其具有优异的抗点蚀能力和稍低的均匀腐蚀抗力。非晶结构及钝化膜中高含量的Cr、Mo、W氧化物等增加了其抗点蚀能力,而孔隙降低了均匀腐蚀抗力。在模拟含沙海水介质中,冲蚀速率随沙粒粒径、沙含量及流速的增大而增加。304不锈钢和涂层的冲蚀过程均以机械损伤为主,硬度对冲蚀过程起决定性作用。304不锈钢表现出以大量塑性变形为特征的典型的韧性损伤机制,涂层冲蚀过程的机械损伤则优先发生于涂层缺陷部位(孔隙、氧化物夹杂等),其它区域只发生微小的刮擦。高的硬度和均匀的非晶组织结构使涂层在海水介质中呈现出优异的抗冲蚀性。在含氯介质中稳定的钝化膜以及优异的抗冲蚀性能,使得铁基非晶涂层有望应用于含沙海水介质中一些泵、阀等高速过流部件的冲蚀防护。
关键词:耐磨;耐蚀;非晶涂层;钝化;冲刷腐蚀;HVOF
资助信息:本研究得到“973”项目(2007CB613906)和国家自然科学基金项目(50971121/E010301)的资助。
1 前言
冲刷腐蚀是由电化学腐蚀和机械冲刷过程所引起的材料加速破坏,由于腐蚀性物质存在时腐蚀和冲刷的联合作用所致。炼油厂、电厂、化工车间的一些阀、热交换器及各种旋转设备(叶轮、涡轮、泵等)极易发生冲蚀失效。图1为一个冲蚀失效的某核电站海水冷却泵叶轮(图中箭头所指为冲蚀较严重部位),叶轮材料为0Cr18Ni9(304不锈钢)。
图1. 发生冲刷腐蚀失效的海水冷却泵叶轮
用于抗冲蚀的材料应该同时具有优异的耐蚀性和耐磨性。早期的选材多集中于一些耐蚀性较优的材料,如不锈钢、铜合金等。但较高的成本和较低的抗冲刷性限制了这些材料作为抗冲蚀材料的应用。鉴于冲蚀多发生于零件的表面或局部部位,在低成本的材料表面喷涂不同类型的陶瓷或金属涂层是一种不错的选择。除了可利用这些高硬度的涂层提高其耐冲刷性外,涂层还具有易修复性。超音速火焰喷涂(HVOF)是20世纪80年代兴起的一种热喷涂技术,由于在喷涂时提高了熔滴射流速度并降低了颗粒的过热程度,所制备的涂层具有高硬度、孔隙率低、抗磨损性好等优点,多用来制备耐蚀、耐磨及耐蚀/耐磨合金涂层。HVOF制备的WC-Co-C涂层具有较高的抗冲刷性,但耐蚀性有待提高。HVOF制备的625合金涂层、镍铝青铜涂层、Ni-Cr-Mo-Si-B合金涂层等具有较高的耐蚀性,但耐磨性受限[1-5]。
非晶态合金由于不存在晶体材料的晶界、缺陷、偏析和析出物等缺陷,表现出许多晶态金属所不具备的良好力学性能、优异的耐腐蚀和耐磨性,受到广泛关注。铁基非晶合金具有较强的非晶形成能力,在保持优异高强度、高硬度和耐蚀性的同时,又具有较高的性价比,但较差的塑韧性使其作为一种涂层材料更具应用前景[6-7]。HVOF制备的铁基非晶涂层孔隙率较低,对提高耐蚀性有利。由于在热喷涂过程中,涂层增加到一定厚度,晶化和氧化难以避免,但晶化有利于提高其硬度,对提高耐磨性有利[8-11]。但这种具有优异的耐蚀性和耐磨性的铁基非晶涂层在含沙海水介质中的抗冲蚀性能如何还不得而知。
本文采用HVOF法制备了的一种铁基非晶涂层,测试了涂层的常规性能,采用电化学腐蚀测试和旋转圆盘冲蚀的方法研究了涂层与基体304不锈钢在模拟海水介质中的腐蚀和冲蚀性能。为海水泵叶轮抗冲蚀材料的选择提供一定参考。
2 实验方法
利用电磁感应熔炼制备Fe54.2Cr18.3Mo13.7Mn2.0W6.0 B3.3C1.1Si1.4 (wt.%)母合金,各组成元素纯度为 99.99 %。利用气体雾化法制备非晶粉末,粉末粒度为 <45 μm。HVOF设备采用美国 Metco 公司的 DJ2700 系统。基体材料选用304不锈钢。喷涂距离为 250 mm,送粉速率为20 g/min,氧/燃气比为4.6。喷涂涂层厚度为200μm。同时,采用熔体旋辊急冷法制备了同成分的非晶薄条带。条带宽 2-3 mm,厚 ~50 μm。
X射线衍射(XRD)分析在Rigaku D/max2400衍射仪上进行。利用Quanta600扫面电子显微镜(SEM)观察涂层的组织结构和试样冲蚀后的表面形貌。涂层中的孔隙率通过配有分析软件的Leica MPS30光学显微镜进行图像分析。利用维氏显微硬度计MVK-H3对涂层截面和基体进行显微硬度值测试。
腐蚀性测试材料包括:304不锈钢、涂层和条带。腐蚀性能测试在电化学测试系统 (EG&G PAR 2273) 上进行。三电极系统采用铂电极,工作电极(样品)和参比电极(甘汞电极)。腐蚀液主要选用1% NaCl 溶液,当开路电压稳定1小时后,进行动电位极化曲线测量,扫描速率为 0.33 mV/s。 X射线光电子能谱(XPS)表面分析技术在ESCALAB 250表面分析仪上进行。采用Al靶作为X射线源。涂层和304不锈钢在1% NaCl 溶液中腐蚀浸泡10 h后进行XPS测试。
冲蚀性测试材料包括:304不锈钢和涂层。利用自制旋转圆盘仪进行冲蚀行为评价。该装置可实现在恒温条件下沙粒较好悬浮状态,试样用尼龙夹具固定在转盘的盘面上, 试样的表面与盘面保持在同一平面, 试样暴露面积为7.07cm2。圆盘在高速旋转中引起近盘面处液体中的石英沙对材料产生低攻角冲刷腐蚀。实验介质的选择主要参考某核电站实际海水环境([Cl-]: 0.519-0.921%, 平均含沙量:3-6 kg m-3 ,最大含沙量:12 kg m-3)。实验时主要考查沙粒粒径、沙含量及流速对冲蚀性能的影响。冲蚀实验时间均为10小时。实验后计算失重和冲蚀速率,用SEM观察试样损伤表面形貌。
3 结果与讨论
3.1 涂层微观结构
图2插图是气体雾化法制备的非晶合金粉末。所选用的粉末粒度为15~45 μm。大部分粉末为球形或近球形颗粒,只有个别较大颗粒上面附着一些小颗粒,即卫星组织(Satellites)。#p#副标题#e#
图2. 非晶粉末、条带和涂层的XRD以及粉末的SEM
图3. 涂层的横截面背散射SEM图
粉末、相同成分条带以及涂层的XRD结果见图2。可以看出,条带在2θ = 40~50° 的范围内显示出漫散的衍射峰,表明其为完全非晶态结构。而粉末和涂层的XRD图谱中出现了一些尖锐的晶体峰,说明其中存在一定的晶体相。涂层的尖锐晶体峰更为明显,晶体相主要是由Fe2C、Cr7C3、Cr2B、M23C6和极少量的氧化物组成。图3为涂层的横截面背散射SEM图,涂层呈现出典型的层状特征,层间含有较多半熔状态的颗粒和孔隙。
3.2 动电位极化行为
图4 为非晶条带、涂层和304不锈钢在1 % NaCl中动电位极化曲线。涂层和条带均表现出快速钝化和宽的钝化区间,过钝化电位高达1.2 V,反映出条带和涂层都具有优异的抗局部腐蚀能力。而304不锈钢则表现出较窄的钝化区间和较低的过钝化电位(0.4 V),说明其具有较低的抗点蚀能力。但从钝化电流来看,304不锈钢具有最低的钝化电流(10-6 A∙cm-2),反映出较优异的抗均匀腐蚀能力。涂层与同成分的条带相比,较高的钝化电流主要是由于涂层中孔隙的存在,孔隙降低了涂层的抗均匀腐蚀能力。
图4. 条带、涂层和304不锈钢在1 % NaCl中动电位极化曲线
3.3 XPS
为了深入分析非晶涂层具有稳定钝化区间的原因,对涂层和304不锈钢在1 % NaCl中浸泡10 h后的表面膜进行了XPS分析,典型的XPS全谱扫描见图5。从图5可知,涂层的表面膜中包含了一些特征谱线,如Fe 2p、Cr 2p、Mo 3d、Mn 2p、W 4f、Cl 2p、O 1s及C 1s等,表面钝化膜主要由Fe、Cr、Mo、Mn、W等元素组成。在304不锈钢表面膜中则只有出现Fe 2p、Cr 2p、Ni 2p、Mn 2p等明显的特征谱线,表面钝化膜主要由Fe、Cr、Ni、Mn等元素组成。
图5. 涂层和304不锈钢表面浸泡10h后的XPS全谱图
因此,涂层表面钝化膜层中Mo和W元素的存在(主要是Mo)是提高其钝化能力的主要原因。表面层中富Mo氧化物的形成对提高其钝化能力和局部腐蚀具有双重作用,一是形成的MoO2产物可以起到阻挡腐蚀介质的作用,进而降低了膜的溶解速率。二是富Mo氧化物可以改变钝化膜的成分,Mo6+可以增加钝化膜的厚度(如MoO3)以及稳定内层Cr氧化物(如MoO42-),抑制了钝化膜的破裂和局部腐蚀的发生。另外,W元素的存在也可以抑制钝化膜的溶解,提高其钝化能力。
3.4 冲蚀行为
涂层和304不锈钢的冲蚀速率随沙粒粒径变化结果如图6所示。很明显,大粒径的沙粒可以引起更高的冲蚀速率,涂层和304不锈钢在75-150目条件下的冲蚀速率分别是200-300目条件下的8倍和42倍。涂层表现出较高的抗冲蚀能力。
图7为涂层和304不锈钢的冲蚀速率随含沙量变化曲线。随含沙量的增加,涂层和304不锈钢的冲蚀速率均增加至一最大值(最大含沙量:9 kg∙m-3),然后趋于平稳。主要是由于过量的沙粒间的“屏蔽效应”,沙粒间互相碰撞降低了在试样表面的有效的撞击作用。在达到最大含沙量之前,304不锈钢的冲蚀速率急剧增加,而涂层的冲蚀速率随含沙量变化并不明显。#p#副标题#e#
图6. 冲蚀速率随沙粒粒径变化图
(实验条件:1% NaCl,含沙12kg m-3,流速18 m s-1 )
图7. 冲蚀速率随含沙量变化图
(实验条件:1% NaCl,75-150目沙,流速18m s-1 )
图8为涂层和304不锈钢的冲蚀速率随流速变化曲线。从图中可知,涂层的冲蚀速率不敏感于流速变化,而304不锈钢的冲蚀速率则近乎成线性趋势增加。冲蚀过程的失重速率与流速具有以下关系:w∝vn,n为速率指数,通常在0.8-12之间,主要取决于材料、腐蚀介质、沙含量、粒径以及流速等因素。n多随流速和冲刷作用的增加而增加,在高流速时作用更为明显。304不锈钢在高流速时冲蚀速率的增加主要来源于机械损伤,涂层的高硬度和均匀的非晶组织结构使涂层在海水介质中呈现出优异的抗冲蚀性。
一般对于浆料体系中的冲蚀过程,材料硬度的增加减小了冲刷的作用从而降低了冲蚀速率。从图6可知,涂层的平均硬度比304不锈钢高2倍多,这也是涂层呈现出较低的冲蚀速率的主要原因。从图2涂层的XRD结果可以得出,涂层中Fe2C、Cr7C3、Cr2B及M23C6等晶体相的出现导致了涂层硬度的提高。
图8. 冲蚀速率随流速变化图
(实验条件:1% NaCl,含75-150目沙12 kg m-3)
3.5 冲蚀形貌及冲蚀机理
图9为冲蚀10 h后涂层和304不锈钢表面及侧面的SEM形貌。从冲蚀后试样的表面形貌看(图9a, 9b),所有的试样表面均发生与流动方向一致的颗粒划伤,可以断定两者的冲蚀过程均是以冲刷为主进行。在304不锈钢表面均匀分布着程度较小的颗粒划伤,由于其较低的硬度出现了明显的韧性冲刷损伤特征,在局部部位还有少量点蚀坑出现(图9a箭头所示)。相对来说,涂层表面则出现一些较严重的冲蚀坑(源自涂层孔隙处,图9b箭头所示),坑外部位则无明显的颗粒划伤。图9c,9c'分别为304不锈钢沿平行和垂直于流动方向冲蚀后的侧面形貌,平行于流动方向的侧面呈现出与流动方向一致表面减薄层(图9c中直线所示),而垂直于流动方向的侧面则只有和流动方向一致微小的槽状冲蚀痕迹出现(图9c'箭头所示),说明304不锈钢的冲蚀过程是以层状减薄的方式在材料表面逐步进行。涂层沿平行和垂直于流动方向冲蚀后的侧面形貌如图9d和9d'所示,涂层的两个侧面都没有减薄层出现,表现出与流动方向无关的特征,恶化只发生在涂层中局部的孔隙处,而涂层外其他区域只有微小的刮擦痕迹,可见涂层中孔隙的恶化可能是引起涂层冲蚀破坏的主要原因。
图9. 冲蚀10 h后涂层和304不锈钢SEM形貌
冲蚀表面:(a)304不锈钢, (b)涂层
平行于冲蚀方向侧面:(c)304不锈钢, (d) 涂层
垂直于冲蚀方向侧面:(c') 304不锈钢, (d') 涂层
结合冲蚀形貌分析,304不锈钢和涂层的冲蚀机理见图10所示。图10a~10d为304不锈钢冲蚀过程,10e~10h为涂层的冲蚀过程。虽然二者在含氯溶液中均可在表面形成钝化膜,但破裂的钝化膜只有在化学稳定的介质中才能迅速修复,才可能对冲蚀过程起到抑制作用。另外,高的含沙量、高的冲击角及高的流速都会破坏表面的钝化膜,消弱其对冲蚀的抑制作用。在此实验条件下,介质中的氯离子会破坏钝化膜的稳定性,尤其对于点蚀能力较低的304不锈钢,在其表面极易发生点蚀(图10b)。沙粒冲刷优先发生于钝化膜破裂处阻碍其及时修复(图10c),再加上较低的硬度,最终导致冲蚀以层状减薄的方式逐步进行,在冲蚀后的不锈钢表面形成韧性为主的冲刷痕迹和少量点蚀坑(图10d)。对于涂层来说,喷涂过程中孔隙不可避免(图10e),但涂层在含氯介质中具有较稳定的钝化膜(图10f),所以冲刷只能始于涂层表面的孔隙部位。由于冲刷会在涂层孔隙破坏处形成一极强的湍流区,从而加速孔隙部位的冲刷破坏。况且,一旦孔隙恶化,腐蚀介质便易沿孔隙进入涂层层状间隙并引起局部缝隙腐蚀,导致相邻涂层间结合强度降低,发生涂层剥离(图10g)。最终在孔隙处形成了比较明显的冲蚀坑形貌,其它部位只有较小的刮擦特征(图10h)。
图10.涂层和304不锈钢冲蚀机理
(a)~(d) 304不锈钢,(e)~(h)涂层
4 应用
从目前的实验结果看,与点蚀阻力较低的304不锈钢相比,涂层稳定的钝化膜特性使其可以应用于海水环境。况且,涂层具有比304不锈钢更优异的抗冲蚀性能,可以作为在一些高速含沙海水中易发生失效的旋转设备(泵、阀等)的冲蚀防护涂层。但是,涂层中孔隙的存在是引起涂层均匀腐蚀速率增大的主要原因,而冲蚀的破坏又源自于涂层中的孔隙。因此,实际应用时应根据具体的工况条件来平衡非晶形成能力、硬度和孔隙率等多种因素。进一步的优化喷涂工艺,降低涂层孔隙及后序的封孔处理是提高铁基非晶涂层抗腐蚀及抗冲蚀性能的重要途径。#p#副标题#e#
5 结论
1. 采用超音速火焰喷涂(HVOF)技术制备了一种FeCrMoMnWBCSi非晶金属涂层,涂层除具有非晶态结构特征外,含Fe2C、Cr7C3、Cr2B、M23C6和极少量的氧化物组成的晶体相。
2.在1% NaCl溶液中,304不锈钢表现出较低的点蚀抗力,铁基非晶涂层具有优异的抗点蚀能力和较低的均匀腐蚀抗力。非晶结构及钝化膜中高含量的Cr、Mo、W氧化物等增加了其抗点蚀能力,而涂层制备过程中孔隙的形成则降低了其均匀腐蚀抗力。
3.在模拟含沙海水介质中,冲蚀速率随沙粒粒径、沙含量及流速的增大而增加。304不锈钢和铁基非晶涂层的冲蚀过程均以机械损伤为主。304不锈钢表现出以大量塑性变形为特征的典型的韧性损伤机制,涂层冲蚀过程的机械损伤则优先发生于涂层孔隙等缺陷部位。高的硬度和均匀的非晶组织结构使涂层在海水介质中呈现出优异的抗冲蚀性。
4. HVOF喷涂技术可以扩大铁基非晶合金涂层的应用范围,铁基非晶涂层在含氯介质中具有稳定的钝化膜和优异的抗冲蚀能力,有望应用于含沙海水介质中一些泵、阀等高速过流部件的冲刷腐蚀防护。
致 谢
本研究得到“973”项目(2007CB613906)和国家自然科学基金项目(50971121/E010301)的资助,在此一并表示感谢。
References(参考文献)
[1] A.Neville, T.Hodgkiess, J.T.Dallas, A study of the erosion-corrosion behavior of engineering steels for marine pumping applications[J], Wear,1995,186:497-507.
[2] K.Sasaki, G.T.Burstein, Erosion-corrosion of stainless steel under impingement by a fluid jet[J], Corrosion Science,2007, 49:92-102.
[3] S.Z.Luo,Y.G.Zheng,J.Li,W.Ke, Slurry erosion resistance of fusion-bonded epoxy powder coating[J],Wear,2001,249:733- 738.
[4] Yugui Zheng, Zhiming Yao, Xiangyun Wei, Wei Ke, The synergistic effect between erosion and corrosion in acidic slurry medium[J], Wear,1995,186-187:555-561.
[5] R.J.K.Wood, Erosion-corrosion interactions and their effect on marine and offshore materials[J], Wear,2006,261:1012-1023.
[6] D.J.Branagan, M.C.Marshall, B.E.Meacham, L.F.Aprigliano, R.Bayles, E.J.Lemieux, T.Newbauer, F.J.Martin, J.C.Farmer, J.J.Haslam, S.D.Day, Wear and corrosion resistant amorphous/ nanostructure steel coatings for replacement of electrolytic hard chromium[C], International Thermal Spray Conference,2006, 5:1-6.
[7] J.Farmer, F.Wong, J.Haslam,J.Estill, D.Branagan,N.Yang, C.Blue, Development, processing and testing of high-performance corrosion-resistant HVOF coatings[C], American Nuclear Society Conference,2003, 8:1-6.
[8] X.Q.Liu, Y.G.Zheng, X.C.Chang, W.L.Hou, J.Q.Wang, Z.Tang, A.Burgess, Microstructure and properties of Fe-based amorphous metallic coating produced by high velocity axial plasma spraying[J], Journal of Alloy and Compound,2009,484: 300-307.
[9] Y.Wang, Y.G.Zheng, W.Ke, W.H.Sun, J.Q.Wang, Corrosion of high-velocity oxy-fuel (HVOF) sprayed iron-based amorphous metallic coatings for marine pump in sodium chloride solutions [J], Materials and Corrosion, 2011, 62, in press.
[10] Y.Wang, Y.G.Zheng, W.Ke, W.H.Sun, W.L.Hou, X.C.Chang, J.Q.Wang, Slurry erosion-corrosion behaviour of high-velocity oxy-fuel (HVOF) sprayed Fe-based amorphous metallic coatings for marine pump in sand-containing NaCl solutions[J], Corrosion Science,2011, 53(10): 3177-3185.
[11] Y. Wang, S.L. Jiang, Y.G. Zheng,W. Ke, W.H. Sun, J.Q. Wang, Effect of porosity sealing treatments on the corrosion resistance of high–velocity oxy–fuel (HVOF) –sprayed Fe–based amorphous metallic coatings, Surface & Coating Technology, 2011, in press.
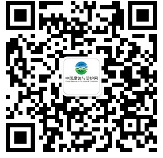
官方微信
《中国腐蚀与防护网电子期刊》征订启事
- 投稿联系:编辑部
- 电话:010-62313558-806
- 邮箱:fsfhzy666@163.com
- 中国腐蚀与防护网官方QQ群:140808414