袁训华,张启富
钢铁研究总院 先进金属材料涂镀国家工程实验室 北京 中国 100081
Email:xhyuan092@sina.com
作者简介:
袁训华(1979.9-),工程师,博士,山东寿光人。2007年毕业于昆明理工大学材料加工工程专业获工学硕士学位,2011年毕业于钢铁研究总院材料学专业,获工学博士学位。现供职于中国钢研科技集团有限公司先进金属材料涂镀国家工程实验室。
主要从事金属材料腐蚀与防护、涂镀层技术开发及镀层性能研究等工作。发表论文二十余篇,申请专利2项,硕士毕业论文获云南省优秀硕士论文奖,博士毕业论文获钢铁研究总院优秀博士论文奖。
袁训华
摘 要:为定量分析热镀锌合金化镀层中各相的含量,采用XRD、电解剥离并结合扫描电镜的观察结果分别对工艺不同的热镀锌合金化镀层进行相结构分析,结果表明,XRD可以定性地判断镀层中含有的合金相的种类及工艺不同的镀层中各相的相对含量,但不能定量的给出镀层中合金相的含量;而电解剥离在足够低的电位扫描速度下可以使镀层中的各相逐相溶解,利用测得的极化曲线和各相的初始溶解电位能够实现对镀层中各合金相的定量分析。
关键词:电解剥离;热镀锌合金化钢板;电化学;相结构
1 引言
热镀锌合金化-镀层具有良好的耐蚀性、涂装性及焊接性而被广泛的应用于汽车和家电行业[1-3]。合金化镀层是由大量的锌-铁金属间化合物构成的,主要包括ζ相(FeZn13-中心对称的单斜晶体)、δ相(FeZn7-超点阵密排六方)、Г1相(FeZn4或FeZn21-面心立方)、Г相(Fe3Zn10-体心立方)[4-6]等,合金化镀层的相结构会由于退火工艺的不同而发生变化。通过对合金化镀层的合金化工艺、组织结构及性能的研究发现镀层的组织结构及镀层中各相的含量对镀层的性能具有重要影响。
目前,合金化镀层组织结构分析的手段主要有金相、扫描电镜、X射线衍射等[7],只能对镀层结构进行成分测定、形貌观察和各合金相的定性分析,而镀层中各相的定量分析至今尚无切实可行的方法,如用X射线衍射进行定量分析时,可以用各相特征峰判定各相的存在,用峰的积分强度表示各相的相对含量,但由于镀层各相衍射谱线难以区分,峰与峰之间相互影响、叠加,且强度的大小也可能受到镀层织构的影响,误差较大,所以难以测定同一试样中各相的百分含量[8]。
热镀锌合金化镀层的电解剥离是在特定的实验条件下实现镀层的逐相剥离,并测定各相的极化曲线,从而实现镀层中各相定量分析的一种电化学方法。采用适当的电位扫描速度可以使合金化镀层中平衡电极电位较低的一相选择性溶解,平衡电极电位较高的各相处于相对稳定状态,镀层中的各相发生选择性溶解,从而能够清晰地显示各相的溶解过程,定量地研究镀层的相结构。因此,本文通过选取合适的电解质溶液,采用足够低的扫描速度,对合金化时间不同的热镀锌合金化镀层进行电解剥离试验。通过测定镀层的极化曲线,计算各相溶解过程中消耗的电量,进而对镀层的组织结构进行定量分析。
2 试验
2.1 热镀锌镀层的合金化处理
实验材料为某钢厂热镀锌机组生产的含铌热镀锌超低碳烘烤硬化钢(BH220),钢板厚度为0.8mm,锌锅中的铝含量为0.13~0.14wt.%,钢板两侧镀层的平均重量分别为85g/m2和82g/m2.实验室进行合金化处理,合金化温度为500℃,合金化时间分别为10s、30s、60s、180s,冷却速度为16℃/s。
2.2 镀层相结构分析
用ICAP-9000电感耦合等离子体发射光谱仪(ICP-AES)测定工艺不同的合金化镀层的化学成分。用Philips Analytical X' Pert PRO MPD X射线衍射仪(XRD)分析热镀锌合金化镀层的相结构,靶材为Cu-Kα,加速电压为40KV,电流为30mA,λ=0.154nm,衍射角度2θ范围为35~85°,扫描速度为2°/min,铁含量不同的镀层的X射线衍射能谱如图1。用Galvanostat Moldel 273A(EG&G)电化学测试系统测定不同工艺的热镀锌合金化镀层的极化曲线。采用三电极体系,参比电极为饱和甘汞电极(SCE),辅助电极为铂电极,介质为200g/l NaCl+100g/l ZnSO4溶液,测试电位范围为-1.2~-0.6V(相对于饱和甘汞电极SCE),电位扫描速度为0.01 mV/S。
3 结果与讨论
3.1 工艺不同的热镀锌合金化镀层的ICP-AES分析#p#分页标题#e#
不同合金化工艺下得到的热镀锌镀层的ICP-AES)分析结果如表1,从表中可以看出随着合金化时间的延长镀层中的铁含量高逐渐增加,锌含量逐渐降低。
表1 合金化工艺不同的热镀锌合金化镀层的化学成分(wt. %)
time / s composition |
10 | 30 | 60 | 180 |
Al | 0.17 | 0.16 | 0.15 | 0.16 |
Fe | 5.87 | 11.73 | 15.02 | 19.67 |
Zn | 93.96 | 88.11 | 84.83 | 80.17 |
3.2 工艺不同的热镀锌合金化镀层的相结构
由铁含量不同的合金化镀层表面X射线衍射结果如图1,由图1可知,合金化镀层中的锌-铁合金层主要由ζ相、δ相及Γ组成,紧靠钢基体的是Γ相,然后是δ相,最外层是ζ相。从XRD图谱中不仅可以定性地判断镀层中含有的相结构的种类,还能从其特征峰的强度比较镀层中各相的相对含量,由图1可以看出,随着镀层中平均铁含量的增加,热镀锌合金化镀层中的ζ相只在镀层铁含量为5.87wt%时其特征峰才明显(图1a),当镀层中的平均铁含量增加到11.73wt%时,特征峰(235)ζ、(131)ζ和(279)ζ相对强度逐渐减小并消失,因此,ζ相随镀层中其它相的生长而逐渐被消耗掉。随着铁含量的增加,镀层中δ相特征峰(330)δ在图1b谱中的相对强度最高,之后随着铁含量的增加其相对强度逐渐降低,当镀层中的铁含量小于15.02wt%时,随着镀层中铁含量的增加δ相含量逐渐增加,这是由于随着合金化时间的延长镀层中ζ相逐渐转变为δ相的结果。当δ相含量增加到一定程度时到达最高值,其后随着镀层中铁含量的进一步升高,δ相含量逐渐降低。而Г相的特征峰(660)Г、(10 10 0)Г和(14 4 2)Г随着铁含量的增加逐渐升高(图1c、d),镀层中Г相含量逐渐增加(图1d)。从图1d(14 4 2)Г相的衍射特征峰可以明显看出,当镀层平均铁含量较低时,其对应位置特征峰不明显,随着平均铁含量的增加,其特征峰相对强度逐渐升高,当镀层中的平均铁含量为19.67wt%时达到最大值。说明当铁含量大于15wt%时(330)δ强度逐渐降低而(660)Г、(10 10 0)Г和(14 4 2)Г峰值强度逐渐升高,这主要是由于随着合金化时间的延长镀层中的δ相逐步转变为Г相的结果。由以上分析结果可知,镀层的相结构随着合金化工艺不同而变化,当合金化时间为10s时镀层主要由ζ相和δ相组成;当合金化时间为30s、60s和180s时镀层主要由δ相和Г相组成;此外XRD很难区分合金化镀层中的其他相结构。
图1 铁含量不同的热镀锌合金化镀层的XRD衍射图谱
3.3 热镀锌合金化镀层的电解剥离试验
3.3.1 热镀锌合金化镀层的J-E曲线
四种热镀锌合金化镀层的电解剥离曲线如图2所示。在相同的测试参数条件下,用同一种试样对镀层进行多次极化曲线测试,将各相逐相溶解除去,依次待某相溶解完毕时终止测试,并进行剩余镀层各相的X射线衍射分析,以确定被溶去相的相结构[7-8],通过试验得到了各相的表观初始溶解电位,如表2。
表2 合金化镀层各相的初始溶解电位(vs. SCE.)
合金相名称 | 初始溶解电位[7] | 初始溶解电位[8] | 初始溶解电位 |
η | -1.080 | -1.064 | -1.100~-1.050 |
ζ | -1.030 | — | -1.050~-1.075 |
δ | -0.970 | -0.989 | -0.950~-0.975 |
Г1 | -0.900 | -0.901 | -0.825~-0.900 |
Г | -0.810 | — | -0.775~-0.850 |
图2中试样a极化曲线的第1个溶解相的电位范围为-1.09V~-1.03V,对应的初始溶解电位为-1.07V,与表2中文献值相吻合,可初步确定为η相;第2个溶解相的电位范围为-1.01V~-0.986V,对应相初始溶解电位为-1.01V,故确定为ζ相;第3个溶解相的电位范围为-0.986V~-0.978V,为ζ+δ相;第4个溶解相的电位范围为-0.978V~-0.852V,其溶解电位范围包含了表2中所示的δ和Г1相的溶解电位,因此该峰为δ+Г1的混合相;第5个溶解相的电位范围为-0.852V~-0.803V,根据表2可知其为Г1+Г的混合相;第6个溶解相的电位范围为-0.803V~-0.693V,根据表2可知其为Г相。合金化镀层的断面结构如图3a,从图中可以看出合金化镀层断面靠近表面的地方为垂直于Zn/Fe界面的栅柱状晶粒组织,主要由纯锌η相和ζ相组成,而靠近基体的地方则是取向杂乱并相互连结的晶粒,主要由ζ相和δ相组成。#p#分页标题#e#
由表2可以看出δ相和Г1相的初始溶解电位相互叠加,所以很难区分δ相和Г1相。这是由于合金化镀层中的Г1相常镶嵌于δ相中,电化学试验中,当δ相尚未完全溶解时,Г1相就开始溶解,两相的极化曲线难于分开,所以可将Г1相和δ相作为一个整体处理。同样,电化学方法也无法区分开Г相和Г1相。以此类推可以确定试样b镀层主要是由ζ相、δ+Г1相、Г1+Г相及Г相组成,镀层断面结构如图3b;从图中可以看出合金化镀层断面靠近表面的位置为垂直于Zn/Fe界面的栅柱状组织,主要由纯锌δ相组成,而靠近基体的地方则是致密的δ相和Г相。试样c镀层主要是由δ+Г1相、Г1+Г相及Г相组成,镀层断面结构如图3c所示,从图中可以看出随着合金化时间的延长,镀层的断面主要由致密的δ相和Г相组成,靠近钢基体的地方则是铁含量较高的Г相;试样d镀层主要是由δ+Г1相、Г1+Г相及Г相组成,镀层的断面结构如图3d所示,从图中可以看出随着合金化时间的延长及镀层中的铁含量的增加镀层中Г相的厚度逐渐增加,约占整个镀层的80%左右,只在靠近镀层表面的部位存在一层薄薄的δ相。
试样1~4的初始溶解峰逐渐向后推移,即随着镀层中Fe含量的增加,溶解电位逐渐升高,需要更高的电位才能使其溶解,说明随着铁含量的增加,镀层中ζ相逐渐减少并消失,δ+Г1相先增大后减少,Г1+Г相和Г相的总和逐渐增加,当铁含量增加至20wt.%左右时,其值达接近50%,说明Г相的含量随着铁含量的增加而逐渐增加。
图2 合金化工艺不同的镀层电解剥离曲线合金化时间:(a)10s,(b)30s,(c)60s,(d)180s
图3 工艺不同的热镀锌合金化镀层断面的SEM形貌 合金化时间:(a)10s,(b)30s,(c)60s,(d)180s
3.3.2 合金化镀层各相的定量分析
根据表2中各相的初始溶解电位可知,在恒定且足够小的电位扫描速度下,镀层中各相根据其初始溶解电位的大小,依次从小到大,逐相溶解,可得到各相溶解过程的电流-电位曲线,由于电位扫描速度一定,也可以得到溶解过程的电流-时间曲线,因此可计算出溶解各相时消耗的电量,进而计算出各相的百分含量。
根据法拉第定律[10],有关系式如下:
式中,W-合金相总量(g),M-合金相化学当量(mg/C),Q-电量(C),I-电流密度(mA/cm2),E-电位(V),R-电位扫描速度(mV/s),AFe 、BZn-铁元素和锌元素电化学当量(mg/C),a、b-合金相分子式加权。根据有关公式计算,各合金相的电化学当量如表3。
表3 镀层合金相的化学当量
合金相名称 | 化学式 | 电化学当量/mg·c-1 |
η | Zn | 0.324 |
ζ | FeZn15 | 0.339 |
δ | FeZn7 | 0.336 |
Г1 | Fe11Zn40 | 0.332 |
Г | Fe4Zn9 | 0.328 |
合金化镀层溶解时的极化曲线如图2,由图2可以直接得到每一相的初始溶解电位和镀层在溶解过程中的电流变化情况,结合表2可以直观地得到镀层的主要相组成,并通过计算峰面积求得溶解过程的电荷迁移量,再结合表3和式4可进行定量计算得到镀层中各主要合金相在含量,从而可以计算出各相占镀层总量的百分比,计算结果如表4。
表4 热镀锌合金镀层中各相的定量计算结果(wt.%)
合金相名称 | 试样1 | 试样2 | 试样3 | 试样4 |
η | 8.52 | 3.25 | ||
ζ | 20.60 | 22.53 | 16.14 | 5.52 |
δ+Г1 | 60.24 | 58.84 | 61.92 | 36.81 |
Г1+Г | 8.61 | 12.39 | 16.71 | 46.51 |
Г | 2.03 | 2.99 | 5.23 | 11.16 |
从表4可以看出,试样1为不完全合金化镀层,镀层表面仍有纯锌η相存在,含量约占整个镀层的8.52wt%,δ相和Г1相的含量约为60.24wt%;试样2为正常合金化的镀层,镀层主要由ζ相、δ相、Г1相及Г相组成,其中δ相和Г1相的含量最多,约为58.84wt%;试样3为轻微过合金化的镀层,镀层主要由δ相、Г1相及Г相组成,其中δ相和Г1相的含量最多,约为61.92wt%;试样4为严重过合金化的镀层,镀层主要由δ相、Г1相及Г相组成,其中Г1相和Г相的含量最多,约为46.51wt%.#p#分页标题#e#
4 结论
(1)XRD可以定性的判断热镀锌合金化镀层中含有的合金相的种类及工艺不同的镀层中合金相的相对含量,但不能定量的给出镀层中合金相的含量。
(2)用电解剥离的方法在足够低的电位扫描速度下可以使热镀锌合金化镀层中的各相逐相溶解,利用测得的极化曲线和各相的初始溶解电位可以实现对镀层中各合金相的定量分析。
References(参考文献)
[1] S Iwamoto, S Ochiai H Okuda. Analysis of group-buckling and -debonding behaviors of galvannealed coating layer on steel substrates under applied tensile strain[J]. ISIJ Int., 2009, 49(1):139-145.
[2] S Ochiai, S Iwamoto, T Nakamura. Crack spacing distribution in coating layer of galvannealed steel under applied tensile strain[J]. ISIJ Int., 2007, 47(3): 458-465.
[3] Y Nunomura T Takasugi Plastic deformation and fracture behavior of galvannealed coating[J]. ISIJ Int., 2003, 43(3):454-460.
[4] Zhang Q F, Liu B J, Huang J Z. Modern continuous hot dip galvanizing of steel sheets[M]. Beijing: Metallurgical Industry Press, 2007.
张启富, 刘邦津, 黄建中。 现代钢带连续热镀锌[M]. 北京:冶金工业出版社, 2007.
[5] T. Takasugi and J. Machida. Plastic deformation and fracture behavior of galvannealed coating under compressive stress circumstance[C]. Galvantech'07. 7th international conference on zinc and zinc alloy coated steel sheet, Osaka, Japan 2007: 230.
[6] Kyung-Keun Lee, In-Hwan Lee, Cheul-Ro Lee, et al. In-situ observation in a scanning electron microscope on the exfoliation behavior of galvannealed Zn-Fe coating layers[J]. Surf. Coat. Tech., 2007, 201: 6261-6266.
[7] Nogueira T M C, Seixas U R, Rios P R. Application of voltammetric stripping to a galvannealed coating on an interstitial free steel sheet[J]. ISIJ int., 1998, 38(7): 775-777.
[8] H.Baudin, A.Beysserias, F.Dalard, etal. Electrochemical stripping of galvannealed steel[C]. Galvaatech`92: 2nd Int.Conf. on Zinc and Zinc Alloy Coated Steel Sheet, Amsterdam, Netherlands, 8-10 Sept. 1992: 455-460.
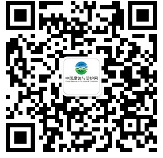
官方微信
《中国腐蚀与防护网电子期刊》征订启事
- 投稿联系:编辑部
- 电话:010-62313558-806
- 邮箱:fsfhzy666@163.com
- 中国腐蚀与防护网官方QQ群:140808414