仇银燕1,2,朱华1,林安1 ,汪的华1,*
1、武汉大学资源与环境科学学院,武汉 430072
2、中南林业科技大学林学院,长沙 410004
* 联系人Email:wangdh@whu.edu.cn
仇银燕,中南林业科技大学林学院讲师,硕士。1977年11月生于湖南省邵阳市。2002年毕业于武汉大学环境科学专业。现主要从事环境科学的教学与研究工作,参与环境保护部公益项目研究1项。
仇银燕
摘要:硅酸盐、稀土金属盐和壳聚糖都是对环境友好的化合物,本文采用电化学方法研究了稀土铈盐与硅酸盐、稀土铈盐与壳聚糖、稀土铈盐与硅酸盐及壳聚糖组成的复合体系对锌的钝化作用及其防护性能。结果表明,硅酸盐和稀土铈盐、稀土铈盐和壳聚糖的复合体系均能在锌表面形成耐蚀性较好的钝化膜,表现出缓蚀协同效应。
关键词:镀锌层;钝化;协同缓蚀;壳聚糖;稀土
1 引言
镀锌是钢铁构(零)件最重要的防护性镀层之一,镀后的钝化处理是进一步提高其耐蚀性的重要途径。由于传统的铬酸盐钝化环境污染严重,其应用受到严格的限制,环境友好的无铬钝化技术的研发非常紧迫[1-3]。硅酸盐是沉淀型缓蚀剂,在溶液中,带负电荷的SiO32-或SiO2胶团与溶解下来的金属离子结合形成保护膜覆盖在金属表面[4]。稀土金属盐通过在材料表面形成含稀土的氧化物和氢氧化物转化膜,阻滞氧的扩散和电子传递。[5-6壳聚糖则可能形成CS-Zn(Ⅱ)络合物[7]。三者的成膜机理各不相同。目前,仅靠单一组分形成的钝化膜或化学转化膜的耐蚀性能均远逊于铬酸盐钝化体系,发挥它们各自的长处组成复合钝化体系是探索高性能无铬钝化体系的方向。在本实验中,试图将硅酸盐、稀土铈盐和壳聚糖组成新的复合钝化体系,探讨它们对金属锌的协同缓蚀作用,以开发环境友好的钝化技术。
资助信息:本项目受到中国教育部新世纪优秀人才支持计划(NCET-08-0416)和中央高校自主科研项目资助。
2 实验
2.1 材料与试剂
0.1mol/L Ce(NO3)3,0.1mol/L Na2SiO3,3%NaCl溶液,粉状壳聚糖(CS),D.D≥90%,用盐酸(0.1mol/L)溶解CS配成溶液,30% H2O2。试液用二次蒸馏水配制。
2.2锌电极的钝化
本工作实验了三种典型的复合钝化体系和工艺,作为比较,同时也进行了三种单组分体系的钝化实验,具体操作如下所述。
Ce1:将锌电极放入pH=4、约30℃的0.1mol/L的Ce(NO3)3 中4-5min,加入适量H2O2促进成膜;将成膜的锌电极再放入0.1mol/L Na2SiO3 中5min,温度60-70℃。取出后,用蒸馏水冲洗,在60℃烘箱老化15min,常温下冷却。
Ce2:钝化液:0.1mol/L Ce(NO3)3 35ml;0.05mol/L CS 1-5ml;H2O2少量;pH3-5,温度约30℃。将锌电极浸入5min。取出后,用蒸馏水冲洗,在60℃烘箱老化15min,常温下冷却。
Ce3:将锌电极放入含0.067mol/L Ce(NO3)3和0.02mol/L CS的溶液中 4-5min,加入H2O2促进成膜,溶液pH 3-4,温度约30℃;将成膜的锌电极再放入0.1mol/L Na2SiO3中5min,温度60-70℃。取出后,用蒸馏水冲洗,在60℃烘箱老化30min,常温下冷却。
单一的铈盐钝化:钝化液:0.1 mol/L Ce(NO3)3溶液;H2O2少量;pH值3-4。温度约30℃,将锌电极放入,时间3-5min。钝化后,用蒸馏水冲洗,在60℃烘箱老化15min,常温下冷却。
铬酸盐钝化:钝化液:Cr2O3 3-5 g/L;浓硫酸 0.6-0.9 ml/L;浓硝酸 0.4-0.7 ml/L。温度为室温,将锌电极放入,时间30-60S。钝化后,用蒸馏水冲洗,在60℃烘箱老化10-15min,常温下冷却。
硅酸盐钝化:钝化液:Na2SiO3·9H2O 90g/L,硫酸适量,30%H2O2 100ml/L,pH2-4,室温,时间1min。
2.3 电化学测量
电化学测量在30±2℃下进行,电解液为中性的3%NaCl溶液。工作电极为纯锌,饱和甘汞(SCE)为参比电极,铂片为辅助电极,交流阻抗测定的频率范围100k Hz-10m Hz,电位幅值5mV。测量仪器为CHI660电化学工作站。
3 结果与讨论
在中性NaCl 溶液中,锌的腐蚀过程包括锌的阳极溶解和氧的阴极还原。
Zn → Zn2+ + 2e
O2 + 2H2O +4e → 4OH-
溶解的Zn2+和OH-生成Zn(OH)2沉淀在锌的表面,并转化为锌的氧化物ZnO,形成钝化膜,
Zn2++OH-→ Zn(OH)2→ZnO+H2O
有Cl-存在时,氢氧化锌与Cl-反应生成可溶解的化合物Zn-Cl-OH,破坏钝化膜导致腐蚀。
3.1 硅酸盐与铈盐复合钝化
锌电极按Ce1配方和工艺进行钝化后,测量得到的交流阻抗谱示于图1,为了比较,对未经钝化和经铈盐、铬酸盐单组分钝化后测得的结果一并列于图1中。
图1 铬酸盐、铈盐、铈硅复合盐钝化的锌电极在3%NaCl溶液中的交流阻抗谱#p#副标题#e#
锌在含Na2SiO3溶液中,表面形成含锌的氢氧化物和硅酸盐膜[8],对锌的阳极和阴极过程都有抑制作用。锌在含铈盐溶液中,阴极区氢和氧的还原导致局部pH升高,当pH达一定值时,铈的氢氧化物或氧化物便沉积在锌的表面,形成铈的转化膜[8]。
2Ce3+ + 6OH-→ 2Ce(OH)3 → Ce2O3 + 3 H2O
H2O2的加入,加速了成膜反应,部分Ce3+被氧化成Ce4+,使膜呈黄色,
2Ce3+ +H2O2 → 2Ce4+ + OH-
表面形成的少量 Zn[OH]与铈的水合物或氢氧化物反应而生成H+,使转化膜中含有H+。在Na2SiO3溶液中,SiO32-与这些H+中和并沉积在铈的氧化物膜的缺陷处起封闭作用,膜更稳定。
成膜后的锌电极在中性NaCl溶液测得的阻抗谱是双容抗弧,一个与钝化膜的的电阻、电容有关,出现在高频端,另一个与反应电阻及双电层电容有关,出现在低频端。而铬酸盐钝化膜表现为单容抗弧特征。拟合的电路参数见表1。由表中数据可见,稀土和硅酸盐复合钝化层电极反应阻抗是单纯稀土盐钝化的1.6倍,耐蚀性有很大的提高,但离铬酸盐钝化还有较大的距离,需要进一步优化配方和工艺条件。
表1 自然腐蚀电位下阻抗谱的等效电路参数
钝化体系 | Cf (μF) | n1 | Rf (kΩ) | Rt (kΩ) | Cd (μF) | n2 |
Ce1 | 43.2 | 0.740 | 2.65 | 6.01 | 432.0 | 0.952 |
Ce(NO3)3钝化 | 15.9 | 0.659 | 2.48 | 3.70 | 203.4 | 0.980 |
Blank | 37.4 | 0.740 | 0.98 | 0.91 | 6.21×103 | 0.756 |
K2CrO4钝化 | 18.8 | 248.0 | 0.607 |
3.2 稀土与壳聚糖复合钝化
将0.1mol/L Ce(NO3)3和0.05mol/L 壳聚糖以不同体积比混合,分别对锌电极进行处理,测得成膜后的锌在自然腐蚀电位下的阻抗谱如图2。可见,随着混合液中壳聚糖的量不同,所形成的膜的耐蚀性也有差别。成膜后的锌电极的阻抗谱也呈双容抗弧特征,拟合后的电路参数列于表2。
当Ce(NO3)3和壳聚糖以2:1的体积比混合,即浓度分别为0.07和0.017mol/L时,具有最好的耐蚀效果,反应电阻是单纯铈盐中钝化的2.9倍。稀土铈为镧系元素,含有未充满的4f电子,壳聚糖的氨基和羟基都含有孤对电子,容易与稀土离子络合。在金属——溶液界面,除生成铈的氧化物和氢氧化物膜外,壳聚糖分子也能吸附在表面,并与Zn2+、Ce3+形成络合物,进一步提高了膜的致密性,从而增加了膜的耐蚀性。
图2 不同配比的铈盐与壳聚糖溶液中钝化的锌电极在3%NaCl溶液中的交流阻抗谱
表2 铈盐与壳聚糖复合液中钝化处理后EIS图谱的等效电路参数
Ce/CS (体积比) |
Cf (μF) | n1 | Rf (kΩ) | Rt (kΩ) | Cd (μF) | n2 |
1:1 | 50.5 | 0.560 | 1.43 | 4.12 | 456.5 | 0.829 |
5:1 | 15.6 | 0.827 | 1.16 | 2.01 | 879.0 | 0.951 |
2:1 | 15.7 | 0.717 | 1.84 | 10.6 | 219.0 | 0.700 |
3.3 硅酸盐、铈盐、壳聚糖三元复合钝化体系研究
根据对SEM结果的观察,三元复合钝化后,锌表面的转化膜从外观上与硅酸盐和铈盐复合钝化差不多,在稀土膜的表面均匀覆盖着一层硅酸盐沉淀;单纯的铈盐转化膜由厚度不均的基膜和附着其上的不同形状和大小的微粒组成。从测得的交流阻抗谱看,反应电阻与硅酸盐和铈盐复合液钝化相当,而小于铈盐和壳聚糖复合液,钝化效果没有明显提高,需要进一步优化。
图3 铈盐、硅酸盐和壳聚糖复合液钝化锌电极在3%NaCl溶液中的交流阻抗谱
4 结论
锌在硅酸盐和铈盐复合液中形成的钝化膜表现出了较好的耐蚀性,二者的复合优于单组分钝化;铈盐和壳聚糖复合液的钝化,能提高膜的致密性,具有很好的耐蚀效果;对于铈盐、硅酸盐和壳聚糖三元体系,与硅酸盐和铈盐复合液钝化效果差不多,有待进一步深入研究。
参考文献
[1] 陈锦虹,卢锦堂,许乔瑜等,镀锌层上有机物无铬钝化涂层的耐蚀性,材料保护,2002,35(8):29-31.
Chen J H, Lu J T, Xu Q Y, Corrosion resistance of organic chromate-free passivation coating for galvanized steel [J]. Materials Protection. 2002, 35(8):29-31 (in Chinese)
[2] 刘艳荣,周婉秋,赵强等,镀锌板表面无铬钝化的研究进展,电镀与精饰,2010,32(4):22-26.
Liu Y R, Zhou W Q, Zhao Q, Advances on surface non-chromium passivation of galvanized steel plate [J], Plating & Finishing, 2010,32(4):22-26. (in Chinese)
[3] 章江洪,张英杰,闫磊等,镀锌产品无铬钝化技术研究进展, 材料保护, 2009, 42(3):49-57.
Zhang J H, Zhang Y J, Yan L, Progress in Research on Chromium-Free Passivation of Galvanized Wares [J], Materials Protection, 2009, 42(3):49-57 (in Chinese)
[4] 董鹏,张英杰,锌镀层硅酸盐钝化膜的耐腐蚀性能,材料保护, 2010, 43(10):5-8.
Dong P, Zhang Y J, Corrosion resistance of silicate passivation film on electro-deposited zinc coating [J], Materials Protection, 2010, 43(10):5-8 (in Chinese)
[5] Bethenourt M, Botana F J, et al. Lanthanide compounds as environmentally friendly corrosion inhibitors of aluminium allors: a review. Corr. Sci., 1998, 40(11): 1803-1819.
[6] Arenas M A etal. Growth mechanisms of cerium layers on galvanized steel [J]. Electrochemical Acta, 2003, 48(24):3693-3698.
[7] Manov S, Lamazouere A M, Aries L, Electrochemical study of the corrosion behavior of zinc treated with a new organic chelating inhibitor. Corr. Sci., 2000, 42: 1235-1248.
[8] Aramaki K., The inhibition effects of chromate-free, anion inhibitors on corrosion of zinc in aerated 0.5M NaCl. Corr. Sci., 2001, 43(3): 591-604.
[9] Aramaki K., Treatment of zinc surface with cerium(III) nitrate to prevent zinc corrosion in aerated 0.5M NaCl. Corr. Sci., 2001, 43(11): 2201-2215.
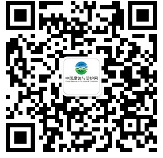
官方微信
《中国腐蚀与防护网电子期刊》征订启事
- 投稿联系:编辑部
- 电话:010-62313558-806
- 邮箱:fsfhzy666@163.com
- 中国腐蚀与防护网官方QQ群:140808414