镇海炼化公司在加工高硫(含硫)原油的同时 ,劣质高酸值原油的加工量也呈逐年快速递增的态势。高酸值原油具有密度大、酸值高、粘度大和残炭高等特点 ,给炼油生产带来了产品质量、系统平衡以及设备腐蚀等一系列不利因素 ,但因其市场资源丰富、价格相对较低 ,利用得好的话 ,也可成为企业创造效益的有效途径。
1 高酸值原油加工情况
1. 1 原油中石油酸及其分布规律原油酸值的大小反映了原油中环烷酸、脂肪酸以及酚类等酸性氧化物(总称石油酸) 的多少。在原油的酸性物质中 ,以环烷酸最为重要 ,含量也高 ,它约占原油酸性物质的 90 %。当原油酸值大 于0. 5mgKOH/ g即能引起设备腐蚀 ,故通常将酸值大于 0. 5mgKOH/ g的原油称之为高酸值原油。
环烷酸是一种带有五员或六员环的十分复杂的羧酸混合物 ,相对分子质量变化范围很大 ,但以300~400 居多。低分子量的环烷酸在水中有一定溶解度 ,而高分子量环烷酸几乎不溶于水。环烷酸在原油中的分布规律十分特殊 ,中间馏分 (250~350 ℃)环烷酸含量最高 ,而在低沸馏分和高沸馏分中环烷酸含量都比较低。也就是说环烷酸含量一般从煤油馏分开始逐渐增加 ,至柴油馏分其含量几乎达到最高峰 ,然后有所下降[1 ]。
1. 2 近年来高酸值原油加工情况镇海炼化公司共有三套常减压装置(常减压) ,其中 I套常减压按伊朗和沙轻原油对半加工设计 ,处理量 5. 0Mt/ a ; III套常减压按只加工沙轻原油设计 ,处理量 10. 0Mt/ a ,均为含硫低酸值原油 ,设计酸值小于 0. 5mgKOH/ g ;仅有 II 套常减压按卡宾达和渤海原油对半加工设计 ,处理量 3. 0Mt/ a ,设计酸值0. 58mgKOH/ g。但由于受加工量等因素制约 ,目前 II套常减压停工 ,高酸值原油主要安排在 I套常减压加工 ,如果高酸值原油集中到厂 ,也临时安排在 III套常减压加工。
近年来 ,常减压装置加工过的高酸值原油品种已达十余种 ,其中酸值最高的罗凯利亚原油 ,酸值达到3. 40mgKOH/ g。高酸值原油的酸值、加工量及所占比例均逐年快速递增 ,见表 1。2 加工高酸值原油存在的问题2. 1 高酸值原油对系统平衡的影响(1)柴油精制问题加工高酸值原油时 ,常减压柴油馏程正好处在环烷酸集中分布的范围内 ,产品中环烷酸含量大 ,因而酸度高 ,见表 2。因此 ,欲生产合格柴油必须进行精制。
目前镇海炼化公司柴油精制手段主要是碱洗电精制和加氢精制。如果集中加工高酸值原油 ,或者 Ⅰ, Ⅱ, Ⅲ套常减压连续加工高酸值原油的话 ,会导致柴油产品酸度不合格。主要原因是:
① Ⅲ加氢的能力有限 ,只能基本满足 Ⅲ常三线和催化裂化柴油的加氢要求 ,若 Ⅲ常二线酸度高时则无法加氢。
② 柴油的碱洗能力低 ,二线电离器碱洗能力为 33t/ h ,三线、催化柴油电离器碱洗能力为 65t/ h ,不能满足 Ⅰ常三线和减一线的精制要求。
③ 酸度高的柴油安排碱洗电精制时 ,会导致碱液严重乳化 ,影响精制效果。同时大量柴油被碱渣带走 ,造成全厂加工损失增加 ,大量废碱渣的处理也带来了环保问题。
表 3 所列为 2001 年 8 月 15 日 Ⅰ, Ⅲ常减压同时加工高酸值原油时 ,柴油各组分及柴油罐的酸度数据。
由表 3 可见 , Ⅰ, Ⅲ常减压同时加工高酸值原油时 ,受加氢能力的影响 , Ⅰ常三线和 Ⅲ常二线酸度较大 ,但也只能直接调合柴油 ,导致柴油罐酸度出现了高达 108. 4mgKOH/ L 的现象。
(2) 蜡油平衡问题镇海炼化公司常减压蜡油的去向有两个 ,一是作催化裂化原料 ,二是作加氢裂化原料。高酸值劣质蜡油的特点是密度大、氮含量高(见表 4) ,环烷基及部分中间基高酸值原油的蜡油氮含量较石蜡基类蜡油氮含量高 3~8 倍 ,最高的罗凯利亚蜡油氮含量高达 0. 34 % ,其中碱性氮会被催化剂的酸性中心吸附成为焦炭的一部分 ,而使焦炭量增加 ,加速催化剂的中毒 (失活) ,影响催化裂化的转化率。同时氮的存在还会影响产品的质量。作加氢裂化原料同样存在氮含量高的问题 ,含氮化合物尤其是碱性氮化合物会强烈地吸附在催化剂表面 ,使酸性中心因中和而失活。因此加氢裂化装置要求控制原料中的 氮 含 量 不 大 于 0. 18 %。同时加氢裂化原料对铁离子浓度也有要求 ,在常减压装置现有加工条件下 ,高酸值原油的蜡油铁离子浓度容易超标 ,铁盐沉积在催化剂上 ,将造成床层压力降增大。#p#分页标题#e#
(3) 劣质渣油平衡问题镇海炼化公司渣油最主要的消化途径是作焦化、化肥、沥青以及减粘裂化的原料。高酸值劣质渣油的一个显著特点是残炭高 ,其中最高的葵土油高达 20. 97 %(见表 5) ,当作为焦化原料时 ,将使焦化液体收率明显降低 ,焦炭收率大幅度上升 ,焦化产品质量变差。所产的 蜡 油 ,其 氮 含 量 都 在0. 47 %以上 ,比石蜡基类渣油的氮含量还要高 ,作催化裂化原料不合适 ,经加氢精制后作催化裂化原料成本又太高。高酸值劣质渣油部分可作道路沥青、建筑沥青原料 ,而公司加工高硫原油数量大 ,沥青原料充足。高酸值劣质渣油作化肥原料时 ,由于粘度和残炭超标 ,对生产影响较大。用减粘裂化装置减粘后作燃料油同样存在着粘度高的问题。如果在加工过程中注碱 ,钠离子又会对催化裂化和加氢裂化原料造成二次污染 ,同时作焦化原料生产的石油焦因钠含量高 ,对 CFB 锅炉也会带来不利的影响。
2. 2 加工高酸值原油对装置设备的影响加工高酸值原油对装置设备的影响主要是环烷酸腐蚀。当原油酸值大于 0. 5mgKOH/ g 时即能引起设备腐蚀。环烷酸在 220 ℃以下腐蚀很轻 ,在沸程为 270~280 ℃时腐蚀最严重 ,主要机理是环烷酸与铁反应生成油溶性的环烷酸铁 ,此后温度再升高腐蚀反而减小。但当温度达到 350 ℃时在硫化氢的作用下腐蚀又重新加剧 ,这时环烷酸不但与铁反应生成环烷酸铁 ,而且与硫化氢腐蚀产物硫化铁反应生成环烷酸铁 ,破坏硫化物形成的金属保护膜 ,因此高酸值原油比高硫原油的腐蚀范围更广。
环烷酸腐蚀反应如下[2 ]:
2RCOOH + Fe →Fe (RCOO)2 + H2
2RCOOH + FeS →Fe (RCOO)2 + H2S
目前由于 II 套常减压停工 ,高酸值原油主要安排在 I套常减压加工 ,形成了高酸、高硫(含硫)原油交替加工的格局 ,这种交替加工将阻碍保护膜的形成 ,加剧装置设备的腐蚀。从 I ,II套常减压加工高酸值原油的设备腐蚀部位看 ,从低温段至高温段均有 ,特别是减压塔的下部 ,如减二、三线及洗涤油段腐蚀最为严重。
从 I 套常减压前期加工葵土原油和罗凯利亚原油减三线铁离子分析数据看(见表 6) ,加工高酸值原油的设备腐蚀在加剧。
2. 3 加工高酸值原油对生产操作的影响⑴高酸值劣质原油几乎都是重质原油 ,轻组分少 ,重组分多 ,热量后移 ,导致生产时因低温部位热量少 ,造成电脱盐温度低。同时由于高酸劣质原油在脱盐过程中乳化严重 ,电脱盐罐油水界位控制困难 ,容易出现电压回零 ,切水发黄的现象 ,从而降低了电脱盐装置的脱盐效果。
⑵蜡油量大 ,装置冷却设备超负荷 ,蜡油冷后温度超标。
⑶渣油量大、粘度高 ,造成外放困难。如果要求渣油进低温罐时 ,由于渣油粘度大 ,传热效果差 ,不仅冷却难度大 ,而且加大了泵出难度。
⑷高酸值劣质原油“头轻脚重”,产品分布不均 ,常压拔出量少 ,减压蜡油、渣油量大 ,加大了加热炉负荷 ,产品质量控制困难 ,难以提高装置处理能力。
3 对策
3. 1 加强系统配套改造加强系统配套改造 ,以适应大量加工高酸值原油需要。目前 ,大量加工高酸值原油后续装置处理能力不配套 ,柴油碱洗能力低、加氢能力有限 ,在 Ⅰ套、Ⅲ套常减压同时加工高酸值原油时 ,柴油的高酸度问题已无法完全解决 ,若三套常减压装置同时加工高酸油 ,则柴油酸度高的问题更是无法解决。
同时蜡油氮含量高、渣油残炭高也导致平衡困难。
因此 ,扩大柴油加氢处理能力 ,新建蜡油、柴油加氢装置等配套设施十分必要。镇海炼化公司正在建造的 3. 0Mt/ a 柴油加氢装置和 1. 8Mt/ a 蜡油加氢装置投产后将解决加氢能力不足的矛盾 ,提高酸值原油加工能力。
3. 2 全面提高装置设备材质等级在没有理想的工艺防腐蚀手段的情况下 ,提高设备材质的耐蚀等级是减轻环烷酸腐蚀最有效的方法。提高材质耐蚀等级的实质就是采用加入一定量的合金元素如 Cr ,Ni , Ti 的合金钢 ,以便形成有一定效果的氧化物保护膜 ,该氧化物保护膜对金属离子扩散有着强烈的阻滞作用 ,从而保护金属不受进一步腐蚀。目前 ,常减压装置加工油种多 ,油性杂 ,特别是 Ⅰ套常减压高硫高酸、低硫高酸、高硫低酸原油交替加工 ,设备腐蚀严重。就加工高酸值原油而言 ,目前 Ⅰ套常减压一些主要部位的材质还不符合规范要求 ,如常压炉、减压炉的出口管线转油线材质为 1Cr18Ni9Ti ,常二中苏尔寿分配器材质为 1Cr13 ;一些高温部位仍有部分碳钢材质 ,如高温设备的压力表引出管线 (共 20 个) 和温度计套管(共 15 个) ,与高温管线相连的重污油线和吹扫蒸汽线 ,以及常二中 ,常二、三、四线 ,常底 ,减四线等机泵的泵缸。此外常二中和减压塔的苏尔寿填料虽然材质为 316L ,但厚度只有 0. 2mm ,长期加工高酸值原油很难保证填料不被腐蚀。Ⅲ套常减压材质在耐环烷酸腐蚀方面较 Ⅰ套常减压更差。因此要大量加工高酸值原油 ,有必要逐步提高常减压装置设备材质的耐蚀等级。#p#分页标题#e#
3. 3 采取混炼加工技术在未对 Ⅰ, Ⅲ套常减压材质耐蚀等级进行提升前 ,为保证装置的长周期运行 ,加工高酸值劣质原油时应以带炼和掺炼为主 ,并控制好混合原油的酸值低于 0. 5mgKOH/ g。计划调度部门要避免高酸值原油集中到厂 ,尽可能不要安排 Ⅰ, Ⅲ套常减压同时加工高酸值原油。在 Ⅰ套常减压加工高酸值原油时 , Ⅲ套常减压尽可能加工低酸值的含硫原油 ,这样 Ⅰ常的二线、三线和减一线可碱洗后生产柴油 ,而 Ⅲ常二线不经加氢直接产柴油也不会对柴油罐造成严重影响 ,而当 Ⅲ常二线酸度高时若要直接生产柴油 ,必须间断生产柴油 ,间断改产加氢原料 ,以便于调合。高酸值原油的蜡油可以采用控制干点的办法来控制其氮含量 ,同时可以与低氮含量的蜡油调合后给加氢裂化和催化裂化作原料。高酸值原油的劣质渣油也可以通过与低粘度渣油调合的方法供化肥作原料或作燃料油。
3. 4 重视脱盐和注碱操作原油脱盐不仅是原油蒸馏装置塔顶系统工艺防腐蚀的关键环节 ,而且是对重油催化裂化和加氢等后续加工有重要作用的原油预处理工艺。提高脱盐脱水效果 ,一方面可以减轻装置腐蚀和结垢 ,另一方面通过电脱盐装置脱水脱盐后 ,有效地减少原油中的金属离子、氯离子 ,去除杂质成分 ,优化常减压蒸馏装置产品质量。开发筛选普遍适用于高酸值劣质原油的高效破乳剂 ,优化高酸值劣质原油脱盐条件(如脱盐温度、注水量、混合强度等) ,采用合理的电场梯度等是提高电脱盐效果的有力手段。
注碱可以中和原油中所含的酸性物质 ,从而降低原油酸值。同时注碱是一种比较容易实现的防腐蚀措施 ,也是目前大部分蒸馏装置解决高酸值原油腐蚀的主要手段。在渣油不作催化裂化原料时 ,可以考虑注碱 ,但必须控制好注入量和注入时机 ,严防注碱过量和随意注碱 ,以免给后续装置生产带来不必要的困难。
3. 5 采用新型有机胺和高温缓蚀剂鉴于传统的注碱方式 ,钠离子对二次加工装置影响较大 ,可以考虑用有机胺代替苛性钠作为高酸原油的中和剂 ,如单乙醇胺 ,二乙醇胺等 ,不过成本相对较高。
针对环烷酸腐蚀特点 ,试用新型高温缓蚀剂可以达到不注碱的情况下减缓蒸馏装置高温部位环烷酸腐蚀的目的。国内目前使用较好的是 GX -195 高温缓蚀剂 ,该剂以高分子量、高沸点有机聚合物为原料 ,在金属材质表面形成吸附性保护膜 ,同时部分高温缓蚀剂直接与环烷酸作用 ,生成环烷酸脂 ,大分子量环烷酸脂可在金属表面建立吸附平衡 ,将环烷酸等有机酸与金属表面隔离 ,达到保护材质的目的 ,国内已有多家炼油企业采用 ,效果较好 ,缺点是成本稍高。考虑到镇海炼化公司原油品种较杂 ,往往高硫、高酸原油交替加工 ,不利于保护膜的形成 ,高温缓蚀剂可以考虑在长期加工高酸值原油的某一套常减压装置中使用。
3. 6 研究流速流态的控制在炼油工艺过程中 ,流速流态的控制十分重要。不同的流速流态对设备的腐蚀截然不同 ,流体流动方向的突然改变 ,流体高速冲刷 ,一些部位如转油线腐蚀特别严重。高温高速条件下 ,酸值很低的油品就可能有很高的腐蚀速率 ,即使是高合金钢材料(如 316 ,317 ,含 6 %Mo 的合金) 也会被腐蚀。
因此研究控制好流体流速、流态有利于防止环烷酸腐蚀。
4 结束语高酸值原油的加工直接关系到产品质量、设备腐蚀、操作费用及环境保护等一系列问题 ,在原油采购过程中 ,应综合考虑其经济效益 ,不能单纯追求原油的价格低廉。此外 ,考虑到三套常减压装置之间加工能力的优势互补 , Ⅱ套常减压装置在改造时应按照高酸值原油设计选材 ,设计酸值应大于1. 0 mgKOH/ g为好。
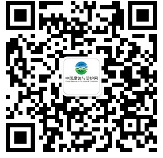
官方微信
《中国腐蚀与防护网电子期刊》征订启事
- 投稿联系:编辑部
- 电话:010-62313558-806
- 邮箱:fsfhzy666@163.com
- 中国腐蚀与防护网官方QQ群:140808414