摘要:综述了金属腐蚀及其防护,从防腐材料、结构设计及防腐工艺应用等方面阐明了现代防腐技术在汽车领域的应用,并简要介绍了未来涂装防腐的发展趋势。
涂装对于汽车制造来讲有两个重要作用,一是对汽车防腐蚀,二是增加汽车美观。大量调查资料表明,每年因锈蚀造成的损失相当惊人。据统计,每年全世界因腐蚀报废而损耗的金属约一亿吨,占年总产量20%-40%,也有人估计,世界上每年冶金产品的1/3,将由于腐蚀而报废,其中2/3可再生,其余的因不可再生而散落在地球表面,这是直接的经济损失。因腐蚀而引起的设备损坏,质量下降,环境污染以及爆炸,火灾等间接损失更是无法估量。同样汽车腐蚀造成的经济损失也是巨大的,据20世纪80年代的统计,全世界每辆汽车因腐蚀造成的损失平均每年为150-250美元。因此研究如何避免腐蚀,延缓腐蚀速度成为经济建设中迫切需要解决的重大问题之一。
一、 腐蚀
(一)、金属腐蚀的机理
腐蚀又称为锈蚀,是钢铁材料中的铁元素与空气中的水分发生了氧化反应,而生成的一种覆在其表面的锈膜。金属腐蚀变化过程一般是从其表面开始的,表现为外表先失去光泽,使光滑表面变得粗糙不平,且覆盖一层金属氧化物;然后逐步向内层腐蚀。金属腐蚀的机理主要是原金属转化成金属氧化物,造成结构件或元件生锈、损坏甚至不能修复而报废。按照金属腐蚀过程的不同机理,可将其分为化学腐蚀和电化学腐蚀;化学腐蚀有三个因素形成,即:裸露的金属、湿气(电解质)、氧;电化学腐蚀是指金属表面与电解质溶液发生电化学反应而产生的破坏,反应过程有电流产生,即由于局部电池的形成而引起的腐蚀。汽车钢铁件的腐蚀大部分是电化学腐蚀。
(二)金属腐蚀的常见类型:
1、一般腐蚀
将金属零部件不做保护放置在室外,几个星期后会发现该金属件生锈了。若使用的是铝合金则在表面生成三氧化二铝,若使用的是铁,则在整个表面上覆盖了红色锈斑。因此汽车车身内侧和外侧涂密封就是为了防止此类腐蚀,但是若车身撞伤后没有及时修补防腐,那么裸露部分则会很快就会生锈。
2、缝隙腐蚀
金属在腐蚀性介质中,其表面或因铆接、焊接、螺纹连接,与非金属连接,或因表面落有灰尘、垢层、沙粒、附着沉积物等固体物质时,由于接触面间的缝隙内存在电解质溶液而产生的腐蚀现象。缝隙腐蚀在各类电解液中都会发生。钝化金属如铝合金、不锈钢、钛等对缝隙腐蚀的较为敏感。
3、坑蚀
引擎盖和底梁上往往可以看到许多很小的凹陷或缺口,这是因为在行驶过程中泥沙、石块撞伤涂膜所致,这些地方沾上湿气或雨水后很容易生锈,即坑蚀;若不作保护,坑蚀则会加剧并呈纵向和横向发展。坑蚀部分的处理主要采用磷酸盐溶液来除锈,处理后再进行涂料的涂装密封保护。
4、晶间腐蚀
晶间腐蚀主要出现在焊接过程。焊接时若环境温度达到800摄氏度就会引起此类腐蚀。晶粒结构在此温度下发生了组织性改变,但温度更高或工件已冷却出现腐蚀的几率反而降低。通常距离焊点3-4mm的地方易出现腐蚀。点焊时,腐蚀表现为距离焊点1-2mm的同心圆,如:不锈钢排气装置出现故障就是由这种腐蚀引起的。通常晶间腐蚀出现在奥氏体、铁素体不锈钢和铝合金构件上。
5、风化
当塑料保险杠触碰到车身时常常会擦伤车身表面涂膜,引起涂料剥落从而发生腐蚀。风化包括磨损的化学反应。螺栓或接线柱松动则会出现这种腐蚀。
6、置换
主要表现是有色金属表面颜色发生变化,如,黄铜元件或老式散热罩长期经太阳光照射后颜色变淡;铝合金凸轮箱几乎呈白色,这类腐蚀是在特定的环境下发生了置换反应,从而改变了合金的表层组织成分并引起了颜色变化。
7、应力腐蚀断裂(SCC)及氢脆
SCC是引起车身损坏的一个主要原因,金属板受力会产生应力,从而可能会引起车身损坏。如车门开关不当引起震动,也会产生应力。氢脆是一种由氢所引起的材料塑性下降或开裂的现象,可以视为是SCC的特例之一。#p#分页标题#e#
8、电偶腐蚀
凡是具有不同电极电位的金属相互接触,并在一定的介质中发生的电化学腐蚀即是电偶腐蚀。如热交换器中的不锈钢管和碳钢板连接处,碳钢在水中作为阳板而被加速腐蚀。
常见汽车主要腐蚀形式有:汽车车身斑状腐蚀,车身车门等零部件的穿透腐蚀,不同金属连接处的电偶腐蚀,各类连接区的缝隙腐蚀,不锈钢、铝合金工件的点腐蚀,承受载荷件的应力腐蚀破裂和腐蚀疲劳,以及各零部件均匀减薄的全面腐蚀。
(三)影响汽车腐蚀的主要因素
引起汽车腐蚀的主要因素有使用环境气候因素、自身结构因素以及人为因素。
1、汽车使用环境比较恶劣且多变,是造成汽车零部件腐蚀损坏的主要原因。
(1)湿气的影响:在车身下部积淀的泥沙、水分和污垢会加速腐蚀;
(2)相对湿度的影响:在相对湿度高的区域(如沿海地区),腐蚀将加速进行,特别是温度在凝固点以上的区域,大气污染超过规定的区域以及道路撒盐化冰的区域更是如此。
(3)温度的影响:对于通风不良处的零件来说,温度增加会使其腐蚀程度加速。
(4)空气污染的影响:工业污染(酸雨)、海岸区域含盐分的空气或使用浓度高的道路化冰盐水都会使腐蚀加速。此外,化冰盐水还会使油漆表面加速裂开。
含有湿气的污垢或碎屑物积淀在车身板部分、凹槽或其他部位;汽车内部产生的腐蚀环境如发动机产生的高温和含硫、氯离子等的燃烧废气,蓄电池产生的酸雾、漏液;工作中振动、冲击产生的应力,摩擦、碰撞引起的局部破损等也是引起汽车零部件腐蚀损坏的主要原因。
2、汽车自身结构因素:主要是受材料因素和设计因素引起的。
3、人为因素:使用者在使用过程中使用不当或不注意也会造成车身腐蚀并使其加剧。
(四)汽车腐蚀的危害
1、对汽车自身的危害:
(1)、破坏汽车美丽的外观;
(2)、造成汽车零部件尺寸减薄,降低其机械强度;
(3)、造成汽车零部件腐蚀穿透使其丧失原有的功能;
(4)、造成零部件出现裂纹或脆性断裂;
(5)、使汽车容器件渗漏,造成滴油漏水。
总之,腐蚀将导致汽车整体性能降低,并降低其使用品质和寿命。
2、对社会的危害:
(1)、造成巨大的经济损失;
(2)、造成社会资源(材料和能源)的巨大浪费;
(3)、造成严重的环境污染;
(4)、可能会带来严重的交通事故。#p#分页标题#e#
二、常用防腐材料
性能优异的防腐材料是确保汽车防腐质量的根本所在。汽车常用防腐材料主要有前处理材料、防腐涂料、抗石击胶、密封胶、各种防护蜡等。
(一)、涂漆前处理材料:
汽车在涂漆前必须进行磷化或其它表面处理,以消除影响涂膜防腐质量的有害因素,进而增强底漆与基材间的附着能力,使整个复合涂层真正起到防腐、防锈和金属保护作用。汽车在涂装前的表面处理主要包括表调、除油、脱脂、活化、除锈、磷化、钝化几个部分,因此前处理材料一般包括脱脂材料(有机溶剂、酸性脱脂剂、强碱液脱脂剂、弱碱性脱脂剂)、除锈材料(润湿剂、缓蚀剂、酸液)、钝化材料(含铬钝化剂、无铬钝化剂)、表面调整剂、磷化剂(高温锰系磷化液、高温高锌磷化液、中低温低锌磷化液)、防锈剂、以及其它打磨、除锈材料等。
(二)、常用防腐涂料
防腐涂层的寿命,与基材表面的处理质量、涂装配套体系、涂层厚度等有很大的关系。然而选择性能适宜的防腐蚀涂料,是获得优异防腐涂层的前提条件。
1、环氧树脂类涂料:
以环氧树脂作为主要成膜物质的环氧型防腐涂料至今仍是使用最方便、用量最大(40%以上)、范围最广(在许多领域均可)、作用最重要(主要品种)的防腐涂料品种。由于环氧树脂及其固化物分子结构中含有许多醚键(-O-)和不易水解的羟基(-OH)等极性基团,易于与极性的金属基材表面润湿,可以使其与金属表面之间产生很强的附着力;另一方面更重要的是与其固化过程有关,环氧基是三元环,它的固化过程是逐步开环的加成反应。因此环氧防腐涂料具有较强附着力和耐腐蚀性能。
2、富锌涂料:
该涂料中金属锌含量较高,因此它对金属表面的保护机理类似于喷锌涂层、镀锌层对金属的保护机理,它对金属基体表面具有双重保护作用,即:电化学保护作用和屏蔽作用。富锌涂料主要适用于底盘、需进行点焊连接的车身骨架和仓门蒙皮的表面防锈,但此类涂料对人体有一定的毒性,施工时必须要配戴好防毒面具,以防中毒。
3、含氯树脂类涂料:
采用含有大量氯原子的聚合物作为主要成膜物质的防腐涂料,称为含氯防腐涂料。常见的主要有两大类,一类是乙烯类树脂防腐涂料:如过氯乙烯涂料、聚氯乙烯涂料;另一类是橡胶类聚合物的防腐涂料:如氯磺化聚乙烯橡胶涂料、氯化橡胶涂料、氯丁橡胶涂料、氯化氯丁橡胶涂料等。此类涂料能防霉、能阻燃自熄、耐水,耐酸、耐碱、耐盐雾性能较好。但漆膜不耐高温(一般不超过60℃),对涂漆件焊接时漆膜灼伤严重,并且在高温下能产生氯气,氯气和空气中的水气反应生成盐酸,可进一步腐蚀周围裸露的钢铁材料;这种漆抗渗透性、润湿性能较差,一般对底材表面的处理质量要求较高,不适宜用于带锈涂装、焊缝补漆等。
4、酚醛树脂类涂料:
酚醛树脂类涂料是以酚醛树脂和改性酚醛树脂为主要成膜物质,加入桐油和其他干性油混合炼制后,再加入颜料、有机溶剂、催干剂和其他辅助材料混合炼制而成的一种涂料。此类涂料涂层坚硬、易干燥、光亮。有良好的防腐性能和电绝缘性能。
5、聚酯树脂类涂料:
聚酯树脂类涂料的主要成膜物质有饱和聚酯树脂和不饱和聚酯树脂两类。其中以不饱和树脂制成的涂料品种较多,此类涂料形成的涂层能自干也可烘干。涂料含溶剂少,涂层较厚,光亮丰满,涂层坚硬耐磨,保色保光性能好,以及能耐弱碱弱酸的侵蚀等。
6、氟碳类涂料:
氟碳涂料由于组织成分中含有C-F键,键能为485kJ/mol,原子间结合力强,所以其更耐日光曝晒,更耐酸、碱、盐等有害介质的腐蚀。
7、玻璃磷片涂料:
玻璃是无机材料,其组织成分决定了它具有良好的抗老化性能及耐化学腐蚀性能。玻璃磷片极薄,它在涂层中可与金属基体平等叠压排列,形成致密的防渗层;据测可达数百层,有效阻止了腐蚀介质扩散渗透到被保护基体表面,并且延长了介质渗透的途径和时间,从而提高了涂层的抗渗透性能及耐蚀性能。同比其它材料,玻璃鳞片涂层抗介质渗透性可提高到几十倍。
8、聚氨酯涂料
聚氨酯涂料是种类较多,主要可分为两大类:一类是单组分湿固化聚氨酯涂料异氰酸基的预聚物,涂布以后,涂膜与空气中的湿气反应产生交联固化。常用的有以蓖麻油醇解物或以聚醚为基础的预聚物。此类涂料的主要优点是使用方便,可以避免现场配制的麻烦。主要缺点是色漆制造比较复杂,成品的储存期限也比较短。另一类是双组分聚氨酯涂料包括多羟基组分和多异氰酸酯两组分,在使用前将两组分混合,由多羟基组分中的羟基与多异氰酸酯组分中的异氰酸根反应而交联成膜。所采用的多羟基化合物的种类很多,如聚酯、聚醚、环氧树脂和丙烯酸树脂等。涂层的耐熟、耐水和耐油性良好。#p#分页标题#e#
9、高固体分涂料
该涂料性能优越,采用聚氨酯预聚物制备的高性能、高固体分涂料和改性环氧其固含量达97%,涂料一次涂敷厚度在150μm以上,同等条件下涂层中针孔数量比普通防腐涂料少2/3以上。国内有研究报道,另外它与普通防腐涂料相比有以下优异性质,可挥发成分含量极小,高压下抗渗透性强;固化时间短,涂层光滑致密,抗冲击强度好;具有良好的抗流挂性质,施工工艺性能较好。
(三)、抗石击胶与密封胶:
由于车身底架经常处于雨水冲刷和砂石撞击的恶劣环境中,因此车身底架部位的钢板结构件对涂装的防腐性能要求较高。对于轮罩蒙皮外表面、挡泥板前后面、仓板外表面以及车身下裙内蒙皮部位需重点加强防腐处理,国内汽车生产厂家一般对以上部位喷涂丙烯酸改性沥青抗石击涂料或橡胶改性弹性防腐胶,此类材料采用高压无气喷涂,具有防水、耐腐蚀、耐冲击、防震、附着能力强的优点。一些中高档车为避免出现防腐盲区经常大量采用胶粘、密封工艺,对各处的缝隙、空腔结构进行涂胶密封,隔绝腔内基体表面与腐蚀介质的接触,防止缝隙或夹层内出现流锈水和进水现象。
(四)、各种防护蜡:
蜡是一种优良的防锈材料,防锈蜡具有极强的涂挂性、适宜的涂膜厚度、粘附性和防锈性,并且蜡液性能稳定,常温喷涂,工艺简单,喷涂成本较低。防护蜡按用途可以分为内腔防护蜡、底盘蜡、车体表面防护蜡、发动机防护蜡等。内腔防护蜡主要用于对点焊形成的缝隙、型钢内腔、夹层结构、装配孔边缘等部位进行防锈处理;底盘防护蜡由于喷涂时雾化效果优于抗石击涂料,一般用于车身底架外露型钢和底盘部件的防锈;发动机防护蜡具有优良的耐湿耐热性能,蜡膜不易剥离,不粘灰尘,涂于发动机表面用于隔绝发动机金属表面与空气接触。漆面防护蜡具有优良耐候性,可防漆膜变色、擦伤,适用于汽车在海运运输过程中的车体表面防护、防锈。
三、在汽车结构设计与制造过程中防腐
(一)、从汽车结构设计上防腐
汽车在制造过程中应尽量避免在喷漆前出现封闭的空腔区域以防止出现无法喷漆的防腐盲区;在外形设计上注意防护、避免积存水汽和尘土。对执行磷化处理的工件要开设工艺流液孔,防止积液;不同金属连接时应尽量选取电位接近的金属,或采取绝缘措施避免电化学腐蚀;为防止焊缝部位由于灼伤漆皮清理不到位而出现补漆质量差的现象,应尽量减少采用带漆件焊接;蓄电池仓内由于酸雾严重,强调涂层的耐酸性,同时应保证仓内敞口通风;并且涂层应注重耐酸性或仓内加装非金属衬里(防护罩壳);车辆设计时应考虑选用性能优良的耐腐蚀材料,如镀锌板、玻璃钢、铝合金板、彩卷板、复合材料和工程塑料等;为防止钢板搭接缝部位出现流锈水现象,对所有外露搭接缝处需涂覆密封胶;工件或整车涂漆前采取适宜的防锈工艺,尽量防止钢铁材料带锈涂装。注意外露件的保护,电器件与接头布置在内侧,或加防护罩壳。整车外露易腐蚀和易进水的部位设防尘罩。零部件设计时考虑其均匀腐蚀,选择一种或几种组合防腐方式。汽车常用的防护方式有涂层、电镀、转化膜和涂防锈油脂等。不同的工艺,具有不同的耐腐蚀性能。通过完善表面处理要求,提高零件设计的合理性,以及有效规范表面处理工艺,促进了产品外观质量和耐蚀性的提高。
(二)、在汽车制造过程中的防腐
1、汽车制造中的金属机件防腐措施
(1)、金属表面处理和表面除油
金属分为有色金属和黑色金属两大类。由于材料种类不同故其表面处理方法也有所不同;金属表面处理可分为:除锈、除油、脱脂、磷化、纯化等几种。汽车零部件在制造加工、保管和使用中,常常接触到各种油脂而形成油污或因保管不当而锈蚀。在车身涂装前,须经过除油、除锈等表面处理。常用的方法有化学转换膜法、非晶Ni-P合金镀层技术、溶剂除油法、碱液清洗法、表面除锈法以及气象沉积法等。
(2)、使用防腐装饰涂料
现实生活中有70%以上的汽车暴露在易于腐蚀的环境中,长期受到风吹雨淋,酸、碱、盐和微生物的腐蚀,使设备的机械性能下降、使用价值降低,甚至造成提前报废。防腐涂料涂膜有很强的附着力,起着隔离水分、烟雾、防撞石击以及外来腐蚀物质侵蚀的作用,使被涂物体表面受到保护。因此防腐涂料是作为金属防腐最普遍的应用方法之一。#p#分页标题#e#
2、汽车车身表面防护处理措施
(1)、采用镀锌钢板。
为了防止钢板件锈蚀,所有的外部冲压件都要采用镀锌钢板,镀锌层厚度10μm。镀锌钢板置于自然环境下,每年镀锌层自然减薄2μm,基本可以维持车身寿命5年。
(2)、磷酸处理。
磷酸处理亦称喷漆前的预处理。在对车身钢板进行脱脂清洗之后,应给车身涂上一层磷酸锌,涂了这层磷酸锌(3μm左右)既能起到第一次保护的作用,也有利于下一道涂层的黏附。
(3)、阴极电泳处理。
阴极电泳处理亦称为上底漆,电泳涂层较厚(30~50μm),该涂料为水溶性涂料,实施过程中应采用电解方式对所有暴露在外的钢板表面和车身底部进行处理。电泳底漆的主要步骤为:入槽浸泡(至少2min);用UF溶液冲洗4道,其中浸泡清洗一次(目的是使夹缝、封闭梁内部清洗干净);用去离子水冲洗2道;烘干(可使车身焊装时采用的点焊密封胶固化)。
(4)、密封--涂抗石击涂料。
涂抗石击涂料的主要目的是防止水、灰尘、气味进入车厢内,车厢底部的涂料能保证车厢底部不锈蚀和不致被沙砾、碎石块撞坏,这种涂料弹性好,可以吸收和缓冲碎石的撞击能量,涂料以喷涂方式覆盖于轮罩内部、底板外表面,车身侧面下裙部。在所有外部可见的钢板搭接处用喷涂或挤涂的方式涂密封胶,必要时用刷子对缝隙进行密封,此外对发动机罩盖和骨架问采用这种胶,按工艺要求进行逐点填充式挤涂。
(5)、底漆。
底漆亦称漆胎,是直接涂在经过表面处理的被涂物体表面上的第一道漆。主要作用是是防止金属表面的氧化腐蚀、填平金属基材表面的细微缺陷和锈斑、增强金属表面与腻子、腻子与中间涂层或面漆之间的附着力,延长使用寿命,是整个涂层的基础。
(6)、中间涂料。
中间涂料又名二道浆,它是处于底漆或腻子之上,面漆之下,用来提高其总涂层厚度,协助底漆和腻子填平细微凹陷之类欠缺,以提高面漆的鲜映性以及光泽性等方面的一类涂层。一般涂层较厚,大约为40um,在迎风面还要厚一些,中涂油漆物理性能与底漆、面漆不同,它的弹性较强,底漆与面漆则比较脆硬。中涂层油漆的功能主要是吸收灰、砂等对面漆的冲击力;加强底漆与面漆之间的附着力;使面漆丰满,起填补的效果。中涂后需进行烘干,烘烤温度为(140±5)℃。中涂后的烘烤也同时使抗石击涂料和密封胶得以固化。
(7)、面漆。
汽车面漆是汽车车身涂装最后的一层涂料;其物理化学性能稳定,除了使汽车外观更美观漂亮以外,同时也能承受自然环境对汽车的侵蚀,如潮湿、氧化、雨水、含盐物质、含酸物质、阳光辐射、砂石撞击等。常用的主要有醇酸面漆、氨基醇酸面漆、硝基面漆、丙烯酸面漆、聚酯面漆和过氯乙烯面漆等。
(8)、存放防护涂层。
对于露天存放3个月以上的车身其外表面应喷涂一层水溶性防护蜡。该防护蜡加有紫外线防护剂,使用前用皂类洗涤剂和清水冲洗掉防护蜡从而使油漆重现光彩。
四、在汽车服役中防腐
(一)、应用防锈剂对车身进行处理。购到新车后要尽快防锈,在易附着水分及泥土较多的地方,密封或半密封的部位,如面板底部、车门内侧、护板衬垫内、底板下面、挡泥板的接合部、灯类装设处等容易生锈的地方,喷涂一层含蜡的自行封闭的防锈剂。专业的防锈工作,包括在正确的位置钻孔,通过所钻的孔喷漆防锈。不同车型上的钻孔位置是不尽相同的,应根据具体车型的详细说明进行。喷漆后要用橡胶或塑料塞子,将所钻的孔塞住。
(二)、平时及时作好除锈工作;在换季维护时,做有计划的防锈处理。
(三)、对一些特殊的腐蚀性极强的痕迹(如沥青、焦油、鸟粪、昆虫的尸体等),要及时予以清除。注意清除时应选用专用清洁剂。
(四)、经常用水管对车身进行冲洗,冲洗车身底板下面、翼子板下面和易于生锈的其他部位,同时要清洗掉车门槛上的污垢;定期打蜡,以保护喷漆层并保持涂膜光亮。注意:不要使用较高水压的水喷洗,以防淋到车身各处,特别是车窗、发动机罩盖及行李箱盖接合之处,否则容易引起锈蚀。
(五)、车辆使用前、中、后,要及时地清除车体上的灰尘,尽量减少车身静电对灰尘的吸附。并保持车门底部和后挡板的排水孔畅通,以避免积水并引起腐蚀。
(六)、雨后要及时冲洗,除去泥污;雨后车身上的雨渍会逐渐缩小,是雨水或酸性物质的浓度逐渐增大,如果不尽快用清水冲洗雨渍将会损害面漆。清洗时,应尽量不用或少用地下水,清洗后用干静的不含水分的布擦拭;擦拭时,应顺着水流的方向自上而下轻轻的擦拭,不应画圈和横向擦拭。
(七)、喷漆的部件如果缺漆,应及时补漆、防锈或打蜡;没有喷漆的部件,应经常检查,发现缺防护油膜,应及时维护;车辆在二级维护时,应分解除锈、以免锈死。
(八)、汽车封存防腐,应选择良好的停放环境,注意通风、除尘、恒温等。经常检查车辆是否有较小的损伤,如有损伤应及时进行修理。金属部件表面尽可能做保护处理,如采用电镀、喷镀等金属覆盖层,法兰和磷化(即金属件表面形成一层氧化膜),非金属覆盖层(如油漆、橡胶沥青等),暂时覆盖层(如涂抹润滑油脂等)。#p#分页标题#e#
(九)、经常检查车辆是否有小的损伤,若有损伤应及时进行修复。
(十)、经常检查车身下部,若有沙砾,污物等,应用水将其冲洗干净。
(十一)、夏日,要防止车辆暴晒,若有条件最好将车辆停放到阳光不能直接照射到的地方,以减轻对漆面的损伤,达到预防腐蚀的效果。
(十二)、在冬季行车,往往遇着先是雨夹雪,后又是气温骤降,车身漆膜会浮上一层薄冰和积雪。这时可用蒸汽洗车或热水洗车机进行冲洗,然后擦干即可;此外,浮雪可用高压水冲洗。
五、当前汽车主要防腐技术的应用
(一)、阴极电泳(CED)底漆
汽车用底漆要求具有以下特性;对经过表面处理的车身具有良好的附着力和抗石击强度;具有极好的耐腐蚀性、耐水性以及良好的抗化学药剂性;与中间涂层和面漆涂层配套性好;应具有长期储存不变稠、不沉底结块的性能,并可随时稀释是用;适应大批量流水线生产,且具有良好的施工性能,能适应先进的涂装工艺。恰恰阴极电泳底漆符合以上标准,且在目前的各种油漆施工工艺中,阴极电泳底漆防腐能力最强,这一点是经过瑞典防腐研究所证明过的。阴极电泳底漆漆膜均匀、平整光滑、展平性好并具有良好的耐蚀性;在磷化处理后电泳,耐盐雾能力极强。此外,美国PPG公司开发的双层电泳可省略中涂工序,提高利用率可达90%,进一步提高车身耐腐蚀性,并有效节约了成本。目前,阴极电泳涂料主要采用环氧树脂,氨基树脂,聚氨酯树脂等,与汽车所用面漆(丙烯酸或聚氨酯磁漆)具有良好的配套性。
阴极电泳涂装工艺经过近30年的不断发展完善,现已成为汽车涂装中最成熟的涂底漆(或底面合一涂层)的先进技术之一。
(二)、水性涂料的静电涂装工艺
静电喷涂是以接地的被涂物为阳极,涂料雾化器或电栅作为阳极,接上高压电,在两极间形成高压静电场,在阴极间产生电晕放电,使喷出的漆滴带电,并进一步雾化,带电漆滴受电场作用沿着电力线方向被高效地吸附在被涂物上。而水性静电涂装主要是采用水性涂料进行中涂和面漆。从20世纪90年代以来,为保护环境,无论我国还是欧美所有新建涂装线都开始采用了电泳底漆或粉末涂料,中涂采用水性涂料或高固体分涂料,面漆采用水性底色加高固体分清漆。随着静电涂装技术和计算机控制技术的进步,高转速杯式静电喷涂(简称ESTA)已被广泛采用,此方法可有效降低VOC排放量,如果车身涂装全部采用水性涂料VOC排放量可以降低到27克每平方米。
(三)、达克罗技术
达克罗技术产生于20世纪50年代末,我国在1994年从日本引进该项技术。达克罗即锌铬涂层,是一种以锌粉、铬酸、铝粉和去离子水为主要成分的新型的防腐涂料,是当前国际金属表面处理的高新技术。经达克罗处理的金属制品性能优异,超强的耐蚀性,一般达克罗涂层厚6-8um就可保证在盐雾试验中1200h以上不出红锈,其防锈效果是传统电镀锌、热镀锌或涂料涂覆法的7~10倍;无氢脆性,达克罗处理工艺决定了经处理过的金属表面没有氢脆现象,适用于高强度受力件;高耐热性,其耐热温度可达300℃以上,而传统的电镀锌法,在温度达到100℃时铬酸盐涂膜就开始起皮报废了。达克罗涂层与金属基体有良好的结合力,而且与其他附加涂层有强烈的粘着性,处理后的零件易于喷涂着色,与有机涂层的结合力甚至超过了磷化膜;良好的渗透性,由于静电屏蔽效应,工件的深孔、狭缝,管件的内壁等部位难以电镀上锌,因此工件的上述部位无法采用电镀的方法进行保护,达克罗则可以进入工件的这些部位形成达克罗涂层。在汽车排气管、发动机缸盖、螺栓、垫圈、螺帽等紧固件以及小型外露件结构上已经开始大量使用并获得了较高的评价。所以,达克罗十分适合汽车零部件的防腐。
(四)、纳米技术:
由于纳米材料具有特殊的抗老化、抗紫外线,高强度和韧性,良好的静电屏蔽效应,色泽变换效应以及抗菌消臭功能;在制造某些性能优异的新型汽车防护材料时,可将纳米粉体按一定比例加入涂料中,从而改善涂料性能,增强防腐、抗紫外线等性能。比如在涂料中添加纳米三氧化二铝、纳米二氧化硅等可提高涂层的表面强度和耐磨性;将10%纳米级二氧化钛粒子完全分散于涂料中,可使面漆耐蚀性大大提高;将改性纳米碳酸钙以质量15%加入聚氨酯清漆中,可提高清漆光泽性、柔韧性、流平性及涂层硬度。最近,美国TIC公司研发了一种全氟纳米薄膜材料,它模仿自然界荷叶的疏水、防尘、自清洁原理,具有极低的表面能和极强的疏水功能,经过纳米技术处理过的金属表面几乎对水无亲和能力,因而阻止了水的侵蚀而达到防腐蚀的效果。
六、涂装防腐工艺的发展趋势
涂装防腐工艺总的发展趋势是在现有涂装防腐技术的基础上,遵从无公害、无污染、节省能源、经济高效即所谓的“4E”原则。
七、结束语
引起汽车腐蚀的主要因素有使用环境因素和其自身结构因素。整车防腐质量的提升必须从产品结构的设计、防腐材料的选用、正确的施工工艺、严格的施工管理入手,并且要善于运用先进的防腐工艺和材料,从根本上提高汽车产品的防腐质量。
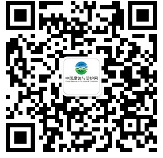
官方微信
《中国腐蚀与防护网电子期刊》征订启事
- 投稿联系:编辑部
- 电话:010-62313558-806
- 邮箱:fsfhzy666@163.com
- 中国腐蚀与防护网官方QQ群:140808414