创新是发展的不竭动力,成果转化是发展的基石。近年来,航空工业特飞所腐蚀防护中心紧紧围绕创新与转化两个主题,着眼前沿技术,打造研发创新团队,整合优势资源与智力,将职工创新的涓涓细流汇聚成腐蚀防护中心发展的新动能,为院所的持续发展贡献力量。
以预研为基础 紧跟技术前沿
表面处理技术在结构防腐蚀中占有相当的地位。随着国家海洋战略的提出实施,提升装备海洋环境下抗腐蚀能力成为当前的研究热点。铝合金、钛合金、铝锂合金是航空领域大量使用的结构材料,阳极氧化是这类轻金属材料最常用的表面处理方法。实际使用过程中发现,普通的阳极氧化处理在我国南海海域高温、高湿、高热的环境特性下难以满足装备的抗腐蚀需求,一些装备和地面设备的腐蚀问题越来越突出,给使用和维护提出了更高的要求。
腐蚀防护中心表面工程组紧跟现代表面技术的发展,以预研课题为基础,吸收、引进、消化国内外先进的表面技术,开展先进技术在航空领域的适应性研究工作,为技术的工程化应用打下了坚实的基础。其中铝合金、钛合金的微弧氧化技术在航空领域的工程化应用研究就走出了一条以吸收、消化、再创新的发展之路。某课题提出了将典型结构耐蚀性处理方法的中性盐雾试验指标提高到 800h 以上,普通的阳极氧化只能达到 336h 的水平。接到课题后,通过调研和考察,发现微弧氧化陶瓷技术是一种在铝、镁、钛等轻金属合金表面原位生长陶瓷层的表面改性技术。其原理是置于电解质中的铝、镁、钛工件表面发生火花放电,放电过程中产生的微区高温高压条件使工件表层的原子与电解质中处于电离状态的活化氧离子反应,生产具有陶瓷结构特征的陶瓷氧化层。该陶瓷层硬度高、耐磨性好、与基体结合力强、耐腐蚀、耐高温氧化、绝缘性好,特别适用于高速运动且需要高耐磨、耐腐蚀、抗高温冲击的轻金属合金零部件。该技术于 90 年代后期引入国内开始研究,没有经典的理论,经过近 20 年的发展已逐步应用于铝合金、钛合金、镁合金要求耐磨、耐腐蚀的零件的表面处理。同时微弧氧化处理的槽液没有有害物质,过程中基本没有废液排放,属于环境友好型的表面处理技术,完全符合国家表面处理技术发展的要求。
吸收消化 创新发展
经过反复论证确定将微弧氧化作为实现该指标的表面处理技术进行重点研究,并成立了微弧氧化研究团队,开展技术攻关,系统性研究微弧氧化技术在航空领域的工程应用。
研究之初主要以基础研究为主,在实验室反复开展试片级的氧化试验,掌握微弧氧化的基本原理和工艺,研究氧化电参数、槽液参数、氧化时间对微弧氧化膜层的影响,同时开展不同厚度的膜层特性的研究,为工程应用打下坚实的基础。
航空工业要求高的可靠性和技术成熟度,安全第一是行业最突出的特点,因此也被行业外戏称为“保守”。微弧氧化作为一项新技术要实现在航空工业的应用需要进行大量的研究,积累试验数据并开展在飞机上的适应性研究工作。随着研究的深入,发现微弧氧化处理对材料的疲劳性能有影响,承力构件对疲劳要求很高,必须积累疲劳数据,为后续的工程应用提供数据支撑。目前项目团队正在持续进行铝合金、钛合金、镁合金经微弧氧化处理后材料的疲劳特性研究。
通过试片级的研究,项目组对微弧氧化有了系统全面的认识,随着研究的深入,摆在面前的就是工程化适应性研究,这也是研究的关键。毋庸置疑,实验室和工程化是有着较大差别的,工程化必须解决三个问题,一是工艺,解决零件(工件)的氧化和质量的稳定性;二是性能,评估考核工件的防护效果;三是标准化,形成规范,指导生产。
工程化研究可谓是风险与挑战共存,特别是在开展钛合金大型工件的微弧氧化研究时项目团队走出了一条引进—创新—再发展的道路。受氧化电源的限制,现有的微弧氧化技术不论国际还是国内,微弧氧化设备一次氧化处理工件的表面积一般不超过 3m 2 。目前只能保证在小型零部件的表面进行微弧氧化处理后膜层的均一性,对于大型部件只能采取多次氧化处理即分段式微弧氧化,其结果是一方面在工件的表面出现印痕,影响工件的力学性能;另一方面分段式氧化会在局部产生烧蚀,造成微弧氧化膜层的剥落。通过调研,项目组引进了具有先进水平的扫描式微弧氧化氧化技术,该技术在铝合金表面应用的比较成熟,解决了铝合金大型工件(氧化面积超过 4m 2 )的氧化问题,已经在海军舰船上实现了工程应用,经过验证完全满足舰船铝合金大型部件的防腐蚀需求。
在吸收消化该技术后,进行了平板件的试验,氧化后检查发现确发现,钛合金表面存在大量的烧蚀点和膜层局部脱落现象,大家产生了疑问,是技术问题还是工艺操作问题?项目组反复进行了数次试验,表面烧蚀现象依然严重。完全照搬是行不通的,需要进行针对性研究改进!
首先从理论着手,通过系列分析及专家咨询,最终确认造成钛合金氧化膜表面烧蚀和局部膜层脱落现象的原因主要有四个方面,一是电场强度及分布显著影响微弧氧化成膜过程。
现行使用的大型铝合金部件扫描阴极为开放式,阴极所产生的电场为扇形,正对阳极物件的地方强,其他地方弱,所形成的氧化膜厚度与电场强度有关。电场强度强的地方氧化膜就厚,弱的地方就薄。随着阴极移动,原成膜区的电场会越来越弱,弱电场不能使原有氧化膜均匀击穿放电,鉴于电场的边缘效应,放电常发生在物件的边缘或有缺陷的部位(如砂眼、气孔或放电微孔),造成局部过流而烧蚀或表层疏松层剥落。
二是微弧氧化形成的氧化膜具有烧结陶瓷的基本属性。铝合金微弧氧化膜基本为陶瓷相的 α-Al2O3,钛合金微弧氧化膜多为金红石型 TiO2 陶瓷,氧化铝陶瓷的熔点高于氧化钛陶瓷的熔点。三是铝合金成膜的电压(500V-680V)远高于钛合金(350V-520V)。因此高压形成的铝合金氧化膜的致密性要比钛合金高的多,抵御烧蚀的能力也会高于钛合金;四是二次氧化时,电压由低到高升压过程中也可造成物件边缘的氧化膜局部剥落或烧蚀;氧化过程中,施加能量过高时亦可造成氧化膜烧蚀或表面疏松层脱落。找到原因后,项目组对扫描式阴极的构型进行了研究和重新设计,通过开展封闭式阴极和半封闭式阴极的氧化分析,通过大量的理论分析计算和试验,创新性提出了“前部适度敞开,后部彻底封闭”的阴极构型,并对扫描速度进行了微调。付出总有回报,在更改设计和参数微调后,成功解决了钛合金大型工件的微弧氧化难题,并申报了钛合金大尺寸扫描式微弧氧化技术专利,为后续的工程应用奠定了坚实的基础。
结语
中心的发展离不开各专业组、项目组、各研发团队坚强有力的技术支撑。围绕中心的发展定位,不断提高团队的技术水平和业务能力,大胆创新,勇于担当,不畏困难,在其岗尽其责,齐心协力为中心的发展添砖加瓦!
● 作者简介
王小龙,男,1980 年生,毕业于武汉科技大学材料学专业,硕士研究生学历,主要从事结构材料表面处理、结构腐蚀防护设计、飞机清洗剂研发等工作,发表核心论文十余篇,先后主持或参与完成了多个型号研制、预研课题及横向技术协作项目。
免责声明:本网站所转载的文字、图片与视频资料版权归原创作者所有,如果涉及侵权,请第一时间联系本网删除。
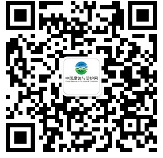
官方微信
《腐蚀与防护网电子期刊》征订启事
- 投稿联系:编辑部
- 电话:010-62316606-806
- 邮箱:fsfhzy666@163.com
- 腐蚀与防护网官方QQ群:140808414