本文从结构设计、材料筛选、表面处理、有机防护体系、防锈剂的应用、维护/维修等方面,提出了我国海洋环境服役飞机全面腐蚀控制总体思路,详细介绍了海洋环境服役飞机腐蚀防护新技术。
文| 孙志华 中国航空工业集团公司北京航空材料研究院 航空材料先进腐蚀与防护航空科技重点实验室
海洋服役环境飞机腐蚀问题严重
海洋环境服役飞机由于受到海浪冲刷、盐雾腐蚀、霉菌腐蚀、高温辐射、高温水蒸气等的环境作用,极易发生金属件腐蚀、非金属件老化、油液易污染变质等。对于经常处于湿热海洋腐蚀环境中的飞机,腐蚀问题已成为决定其寿命、保证技战术水平的关键因素。据资料统计美国1994 年至2004 年的十年间:每年约1 亿平均维修工时用于解决腐蚀及腐蚀检查工作。平均7.6 维修小时/ 飞行小时,占整个检查维修时间的36%;引发安全事故224 件, 涉及飞机227 架,经济损失达10 亿美元/ 年。而我国亚丁湾护航任务是我国海军迄今为止深入海洋最远、时间最久的任务,多种直升机在此任务中暴露出了严重的腐蚀问题,飞机不得不提前进入大修,因腐蚀所带来的经济损失达上千万。
海洋环境服役飞机全面腐蚀控制总体思路
我国海洋环境服役飞机全面腐蚀控制应借鉴英、美等国空军、海军的腐蚀控制方法,将飞机腐蚀控制研究发展为防护系统工程学,在论证、设计、选材、制造和维护的全寿命周期内贯彻和体现积极的腐蚀预防与控制理念,建立贯穿飞机全寿命周期的先进全机腐蚀控制与防护体系,满足飞行安全、高性能和长寿命设计要求。
注重综合防护设计
细化易腐蚀件连接件( 紧固件、轴承等)、特殊结构(折叠、轴套、起落架等)的设计;密封设计应突出密封材料的阻断隔离和三防性能,注重贴合面、铆钉等位置的防护;加强排水、装配设计等;加强成品件腐蚀控制设计等。

选用综合性能优良的耐蚀材料
全面综合强度、断裂韧性、耐腐蚀性、轻量化、经济性等材料性能,在满足战术技术性能的前提下,尽可能选用耐蚀材料; 从设计、选材等即把腐蚀控制技术纳入飞机结构耐久性设计;建立分级的腐蚀性能评估方法供设计选材使用。
采用新型先进表面处理技术
金属零件应采用镀层、覆盖层或沉积层,以提高材料制件的耐蚀性、耐磨性、导电性、减摩性、隔热性、装饰性等;目前飞机表面处理技术向提高材料综合防护性能及环保需求方向发展, 主要的新技术有高强度钢、钛合金高速火焰喷涂、爆炸喷涂代镀铬技术;离子镀铝、铝涂料替代镀镉用于钢、钛合金零件及紧固件防护;钛合金溶胶- 凝胶表面处理提高与漆层及胶粘剂的结合力;替代铬酸阳极化的新型环保阳极氧化技术等。
采用新型防护涂层体系
全机外表面涂料耐湿热抗盐雾表面涂料兼具有防潮拒水、高柔韧性、“三防”涂层是最佳解决方案;研发重防腐涂料以及舱内采用水基涂料等;全机结构孔和缝隙采用具有较强的渗透性的渗透型缓蚀剂,可以进入极小的缝隙和孔内,将结构表面的水分和盐份置换出来,并覆盖一层具有防腐蚀作用的膜层,增强抗腐蚀能力。
采用先进的阻蚀密封技术
采用无铬硫化体系、环境友好的低密度缓蚀改性聚硫密封剂, 提高粘接能力和防腐蚀性能;同时加强精细密封施工工艺的应用, 如采用螺钉用密封帽、专用的施工修正工具以及采用双组份单包装等。
先进的舰上腐蚀控制维护/维修技术
采用清洗、缓蚀、舰上快速腐蚀修复技术等有效控制腐蚀的发生和发展,主要的腐蚀控制维护技术包括清洗剂和缓蚀剂,而腐蚀快速舰上的维修技术有电刷镀、电刷阳极化技术原位修理, 如低氢脆刷镀镉可用于飞机起落架镀镉零部件修理,铝合金、结构钢去腐蚀产物及氧化磷化膏以及冷喷涂技术等。
材料、防护体系、易腐蚀结构服役环境耐久性评价
在服役环境谱研究基础上,建立环境模拟加速试验谱,开展户外暴晒、舰上暴晒及实验室模拟加速试验,从而获得材料、防护体系、关键(易腐蚀)结构件环境耐久性数据,为整机防护体系改进提供依据;采用飞机腐蚀损伤及腐蚀环境的原位监测技术, 将以往的“发现腐蚀- 进行修复”的模式转变为“预测腐蚀- 进行管理”的模式,根据预测结果决定飞机维护和管理策略。
海洋环境服役飞机腐蚀防护新技术
高速火焰喷涂技术(HVOF)替代电镀硬铬
高速火焰喷涂技术是通过燃料燃烧气体获得高速气流、使喷涂粉末颗粒速度到达超音速而获得涂层的工艺,其特点是焰流速度高(1500m/s 以上)、粉末粒子速度快(610~1060m/s)、涂层致密度高、焰流温度适中(2700℃)、可避免WC 等材料的高温分解或氧化等。此制备的涂层具有耐磨性、耐蚀性好、气密性好、无氢脆、长寿命、环保的优点。主要用于起落架活塞杆、柱塞、舱门插销、阻力板、钛合金襟翼滑轨等耐磨涂层的制备以及修理(见图2)。
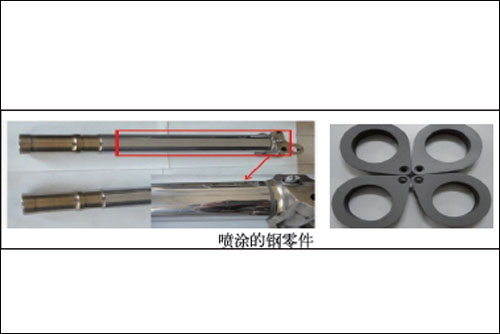
图2 高速火焰喷涂的零件
爆炸喷涂技术(D-gun/super Dgun)
爆炸喷涂技术是利用气体爆炸产生的能量,将喷涂粉末加热到一定温度和速度,喷射到基体表面形涂层,其特点是爆炸温度高达3400℃、冲击波速度达到4000m/s、喷涂颗粒飞行速度为600~1200m/s,理论上能够实现任何材料的喷涂(非金属上喷涂耐磨、导电等涂层),主要应用于衬套、螺栓、螺钉、耐磨环、复合材料上导电、耐磨涂层以及封严盘等高耐磨部件上。爆炸喷涂技术原理及设备见图3.
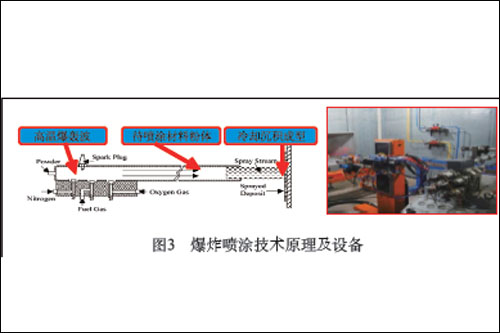
低氢脆无氰镀镉-钛(Cd-Ti)技术
低氢脆无氰镀镉-钛技术有效解决了高强度钢高耐蚀、低氢脆的防护难题,其特点是耐腐蚀性好,中性盐雾试验500h不出现红锈;低氢脆性,不会导致高强度钢氢脆;无氰化物等。与波音BAC5804氰化物镀镉-钛对比的优点主要有镀液中无氰化物、镀液稳定、工艺简单、镀层钛含量较高。主要应用于300M、30CrMnSiNi2A钢、A-100等高强度钢螺栓及起落架的防护。
离子镀铝技术(IVD)
离子镀铝技术是在真空条件下,采用高动能离子和非带电离子的轰击沉积铝靶材,在钢和钛合金表面形成铝涂层的方法。离子镀铝技术解决了油箱内紧固件防护问题,其优点是无氢脆、耐蚀性好(中性盐雾336h)、使用温度达496℃、与铝合金无电偶腐蚀、环保等。主要应用于钛合金、结构钢紧固件、结构件的防护,无金属致脆危险,同时解决中温防护和电偶腐蚀问题。
铝涂料技术
铝涂料一种由铝、树脂、固化剂、缓蚀剂等制成的有机涂料,可采用喷涂或浸涂的方法获得涂层。涂层厚度一般为5~12μm,其特点是优良的结合力、耐热、耐脱漆剂以及耐腐蚀性能,可用于钛合金紧固件防护,解决电偶腐蚀和应力腐蚀问题。与离子镀铝相比,其成本低,对零件形状无限制等,但膜层厚度的控制精度不如离子镀铝。
高耐蚀硬铬镀层封孔技术
电镀硬铬镀层由于具有微裂纹,因此传统硬铬镀层存在抗腐蚀性能差、气密性不佳等等缺点,采用518高耐蚀硬铬镀层封孔剂对硬铬层进行封闭处理,由于具有较强的渗透能力,能深入到镀层微裂纹中,可为大幅度提高涂层耐腐蚀性能,解决零件气密性问题。主要应用于活塞杆、轴承滚珠等,解决海洋环境下镀铬零件腐蚀问题以及气密性。其工艺流程简单,见图4。
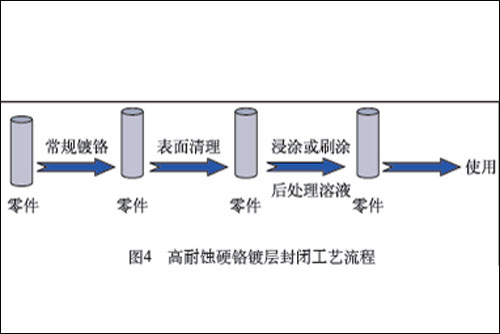
新型环保阳极氧化技术
新型环保阳极氧化技术是采用苹果酸等无铬阳极氧化液,替代常规铬酸阳极氧化工艺,达到波音公司的硼硫酸阳极氧化和空客公司的酒石酸阳极氧化膜层的性能(见表1),具有自主知识产权。其膜层厚度为3~5μm、耐中性盐雾336h、对基体疲劳性能影响很小、设备简单、无铬环保等特点,可以作为底层,提高漆膜结合力。

铝/镁合金微弧氧化技术
微弧氧化技术是指零件在微弧氧化溶液中,置于阳极,利用电化学方法使铝、镁、钛等材料的表面微孔中产生火花或微弧放电,通过高压放电与电化学氧化的共同作用,在合金表面原位产生陶瓷层,可以大幅度提高铝/镁合金的性能。主要特点是耐蚀性高,中性盐雾>1000h;硬度高,HV800~HV2000;耐磨性高,比硬质阳极化提高一倍;原位生长,与基体结合牢固;对基体性能影响相对较小;工艺环保,对环境无污染;耐热性好;绝缘性好,绝缘电阻可达100MΩ。
溶胶-凝胶表面处理技术(Sol-gel)
溶胶-凝胶表面处理技术是以金属有机化合物和无机盐为前驱体,经过水解和缩合反应聚集成1nm左右的溶胶粒子,再以溶胶为原料在基材进行涂敷,之后溶胶粒子进一步聚集生长形成凝胶,在一定温度烧结形成涂层。主要特点是是绿色环保、无毒、无铬、无重金属、不需要水清洗,工艺简便,可采用浸涂、刷涂、喷涂、淋涂;常温、低温固化;膜层透明、均匀致密,0.3~1μm,结合强度大幅度提高。
复合喷丸
喷丸强化是采用高速运动的弹丸流喷射材料表面并使其表层发生塑性变形,产生残余压应力场和变形的显微组织,抑制表面裂纹扩展,显著改善材料的疲劳性能和抗应力腐蚀性能。复合喷丸进行两次喷丸,一次采用钢丸,植入大的残余应力场;二次采用陶瓷丸或玻璃丸,改善表面完整性。主要应用于起落架、衬套以及所有喷丸零件。
孔挤压强化
孔挤压强化是利用装在挤压枪上的挤压棒,在一定的压力和挤压速度下挤压孔壁,使孔壁产生塑性变形。挤压后,金属材料的晶粒更加细小而密实,且产生加工硬化,显著提高孔的疲劳寿命,并获得较高的尺寸精度和表面光洁度。主要应用于Ф6~Ф50mm孔。孔挤压技术和衬套挤压技术已经在某直升机上成功应用,强化效果极佳使得钛合金双耳片孔模拟件疲劳极限提高40%,桨毂中央件疲劳寿命由3000小时提高到4500小时;铝合金阻尼器套筒疲劳寿命由160小时提高到4500小时。
冷喷涂技术(cold dynamic spray)
冷喷涂技术是采用15~20atm的压缩气体实现超音速低温喷涂,喷涂使用的粒子直径要求小于50μm,可喷涂铜、铝、锌等多种涂层。主要特点是喷涂时温度低;涂层氧化物含量低;可喷铜、钛、铝、纳米材料等;涂层热应力低;工艺、设备简单,不需真空;涂层结合力、致密性优于火焰喷涂。可以用于镁合金、铝合金零件的修复,见图5。
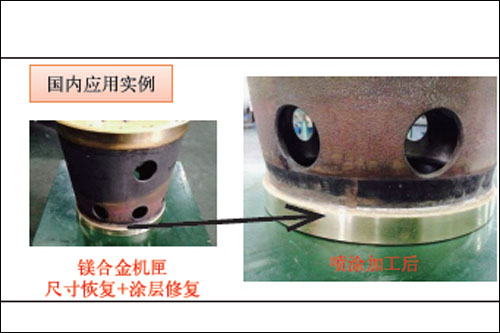
图5 镁合金机匣冷喷涂修复
无机盐铝涂料
TWL系列无机盐铝涂料以磷酸盐作为粘结剂,铝粉为填料,涂料经喷涂、高温固化(200℃)后形成涂层。该涂料主要用于燃气轮机压气机叶片以及钢或铁基材料,防止腐蚀和高温氧化。在650℃以下具有牺牲性保护基体材料的作用,耐中性盐雾可达2500h以上;根据基体的不同,可以在1200℃下提供耐高温防护。
清洗剂技术
对飞机表面采用专用的清洗剂进行清洗,一方面可以及时去除表面盐粒子,减缓由于盐粒子而引起的涂层及金属的腐蚀;另一方面可以及时清洗表面沉积的灰尘,避免灰尘吸附水分和污染物,从而引起腐蚀的发生。美国海军针对舰载飞机规定了具体的清洗频率,如当飞机在海洋上空在低于一定高度飞行后,应每天对飞机进行清洗等,大大减缓了飞机的腐蚀。目前用于飞机的清洗剂种类、特点、用途及相关产品见表2。
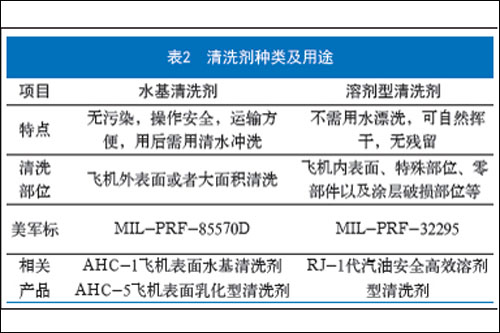
脱水缓蚀剂技术
脱水缓蚀剂有较强的渗透性,可以进入极小的缝隙和孔内,将结构表面的水分和盐份置换出来,并覆盖一层具有防腐蚀作用的膜层。美海军航空工程部门海军飞机装配后,将缓蚀剂喷洒在易于凝露的区域,尤其是结构连接处,大幅度提高整体抗腐蚀能力,消除防护薄弱环节。采用ACF-50缓蚀剂,飞机腐蚀率大大降低,如ES-3A型反潜机、S-3B型反潜机;在海鹰直升机上使用部位有机尾内表面、低凹区域及舱底等(见图6)。脱水防锈剂的种类、用途及相关产品见表3。


去腐蚀产物膏
原位快速的结构钢/铝合金的腐蚀膏维护/维修技术,既可以快速、有效地去除钢、铝基体生成的腐蚀产物,同时在清理部位形成一层耐腐蚀涂层以及与漆膜良好的底层,保证局部腐蚀部位维护、修理的需要。目前用于铝合金零件的主要是ALT-1铝合金去腐蚀产物膏和LYG-2铝合金局部化学氧化膏配套使用,直接涂于零件表面,可有效清除腐蚀产物,并生成一层与涂层结合力好,具有一定防护能力的氧化膜;无须清洗即可进行涂漆处理,方法简单,易于操作。而用于钢零件的去腐蚀氧化磷化膏主要有两种,其中BT-1软膏适用于处理铬含量不低于18%的高耐蚀性不锈钢,BT-2G软膏适用于处理铬含量为10%~18%不锈钢及30CrMnSiA。
结语
腐蚀问题已成为决定海洋环境服役飞机寿命、保证技战术水平的关键因素,其腐蚀防护与控制是一个系统工程,贯穿设计、研制、生产、使用全过程。需要从结构设计、材料筛选、表面处理、有机防护体系、防锈剂的应用、维护/维修、人员培训等方面,加强腐蚀控制,包括加强细节的密封防水设计、应用先进高性能防护技术、加强维护/维修中技术与产品的研发和应用等几个方面,最终建立起海洋服役飞机表面防护研究体系,保证海洋服役飞机的研制、生产和使用的顺利进行,全面提高海洋服役飞机的使用寿命。
孙志华,女,1969年10月出生,博士/研究员,现担任中航北京航空材料研究院表面工程研究所、表面防护研究与工程技术中心主任,一直从事航空材料先进防护技术研究;航空材料、涂层及结构件环境适应性评价及模拟加速方法研究;腐蚀性能评价与表征技术研究等。先后获得集团科技进步奖8项,发表论文50余篇、专著1份,申请专利8项。
免责声明:本网站所转载的文字、图片与视频资料版权归原创作者所有,如果涉及侵权,请第一时间联系本网删除。
-
标签: 腐蚀控制技术
相关文章
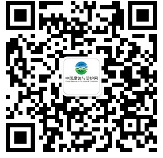
官方微信
《腐蚀与防护网电子期刊》征订启事
- 投稿联系:编辑部
- 电话:010-62316606-806
- 邮箱:fsfhzy666@163.com
- 腐蚀与防护网官方QQ群:140808414
点击排行
PPT新闻
“海洋金属”——钛合金在舰船的
点击数:8135
腐蚀与“海上丝绸之路”
点击数:6475