海洋环境是一种苛刻的自然腐蚀环境,舰船由于结构复杂,其船体、装置、管路、电子设备等均会受到腐蚀危害。长期以来,我国在舰艇防腐设计和新技术应用方面做了大量工作,目前各类舰船的综合耐蚀性能已得到了显著提高,但与美俄等海军强国相比,还有很多防腐蚀技术工作需要发展完善。
文| 张 波 钢铁研究总院青岛海洋腐蚀研究所 青岛钢研纳克检测防护技术有限公司
由于腐蚀是海军舰艇结构和设备最主要的损坏形式,因此多年来各国一直在不懈地进行防腐蚀研究。目前,美、德、英、法、俄等国海军已制定有专门的标准,并将腐蚀控制工作纳入到舰艇的论证、设计、建造、使用和修理全过程中。自上世纪50 年代以来,美、苏/ 俄海军开展了大量的舰艇防腐基础性研究和长期的材料试验研究,目前其舰艇防腐控制水平居世界前列。美国建立了大规模、配套齐全、技术先进的多个材料腐蚀试验场所,对其海军装备材料进行长年的腐蚀研究,但由于腐蚀问题的复杂性和普遍性,大型舰艇尤其是航母的腐蚀仍然是美国海军面临的首要技术问题。
与国外的先进技术和雄厚研究基础相比,我国在舰艇防腐设计和应用方面也作了大量工作,特别是近10 年来,在选材、设计、工艺和建造方面取得了长足的进步, 一大批新材料、新技术、新工艺和新装备在新造舰艇上得到了应用,舰艇的可靠性和安全性有了明显改善。但是应该清楚地看到,我国在舰艇防腐方面的研究和应用技术与发达国家相比尚有很大差距,基础性研究较薄弱,尤其是对材料腐蚀特性的研究和腐蚀数据的积累难以满足新造舰艇防腐设计的要求。
国内外舰船腐蚀防护现状
海洋环境的高盐度、高温和高湿环境使舰船和武器装备遭到严重的腐蚀,同一种结构材料在海洋环境中的腐蚀往往要比内陆高出数十倍。我国海军舰艇防腐维修费用很高,舰艇因腐蚀而丧失战斗性能的事故也曾有发生。例如:某潜艇上层壳体因严重腐蚀失去强度,引起钢板破裂;停靠在舟山码头的某艇因杂散电流腐蚀而发生船壳严重受损;南海地区某型艇在一次维修中更换的钢板达1/3,既增加了维修工作量,降低了在航率,又造成巨大的经济损失;在陆上和淡水中能很好运作的两栖装甲战车却无法适应海上环境条件…… 这一切都源于严酷的海洋腐蚀环境。
近三十年来我国在舰用涂料、阴极保护技术、防海生物技术等方面开展了大量的研究工作,制定了相关的防护标准和规范,使我国舰船的腐蚀防护技术取得了长足的进步。目前,全寿命、全系统的防腐蚀观念在我国舰船设计、建造和使用部门中得到越来越广泛的重视和初步贯彻,推动了各项技术的发展,其中舰船的阴极保护、电解防污技术及产品已达到较高水平。
美国国会在相关审计调查报告中指出,美军装备及基础设施的年直接损失约200 亿美元,构成武器系统全寿命周期费用的最大部分。2004 年,美国国防部发布了长达118 页的《腐蚀预防和减缓战略计划》,制订了武器装备及基础设施腐蚀防护的长期战略。目前,此战略已实施10 年, 对于降低美军舰船装备的腐蚀发挥了重要的作用。
舰船腐蚀防护技术发展动态
舰船腐蚀防护技术是综合性的“边缘” 学科,解决舰船腐蚀防护问题要从耐蚀材料的选用、涂层保护、电化学保护和防海生物污损等多方面综合入手。
耐蚀材料的选用
(1) 船体用结构钢
船体结构钢是现代舰船建造最主要、最重要、最关键的结构材料,其性能优劣直接关系舰船战术性能的提高,须具有足够的强度和韧性、良好的工艺性及耐海水腐蚀性能。
美国的船体结构钢从50 年代就开始建立HY 系列高强度结构钢的体系平台。发展了综合性能好的屈服点达到550MPa 级HY-80 钢,该钢用于美国海军第二代的弹道导弹核潜艇--“伊桑·艾伦”级核潜艇的全部耐压壳体,该级艇的最大下潜深度可以达到300m.在HY-80 钢基础上,改变合金含量及回火温度以提高强度,研制了屈服点690MPa 级HY-100 钢。20 世纪60 年代中期, 美国研制了屈服点不低于896MPa 级HY- 130 钢,一直到80 年代,HY 系列钢仍然是美国舰船的主要结构用钢。美国用HY-130 钢建造的“海狼”号最新式攻击型核潜艇, 下潜深度可达560m.
进入20 世纪80 年代后,随着超低碳、超纯净钢冶炼、微合金化及控轧控冷等冶金技术的发展,美国研制开发了不需预热或者只需较低温度预热就能焊接的HSLA 系列钢,其强韧性达到同级别HY 系列钢的水平,而焊接性更好,且合金元素含量低, 大大降低了舰船成本,使船体结构钢的开发进入了一个新时代。
俄罗斯60 年代形成了比较完整的AK 系列钢,目前已逐渐被AB 系列钢所取代。日本舰艇用钢研制开发水平是很高的,列入防卫厅规格的就有Ns30、Ns46、Ns63、Ns80、Ns90、Ns110 等各级舰艇用钢。
我国从60 年代初开始,通过研仿试制成功了主要舰船用钢,如921、922、923 钢以及与其配套使用的铸钢、锻钢等。从70 年代开始,自行研制了我国第一代舰船用钢901、902、903 低合金船体钢及配套材料。
进入80 年代,我国海军装备有了很大发展,开始研制综合性能更好的第二代舰船用钢及其配套材料。日前在结构钢及配套材料方面正在逐步形成以强度级别为系列,品种规格较完整的耐蚀可焊钢系列, 主要代表有907A 系列钢、945 系列钢、921A 系列钢等。我国舰船用钢40 年来的研制与发展基本上满足了不同时期舰船建造的需要,但是与国外先进海军国家舰船用钢相比还有一定差距。
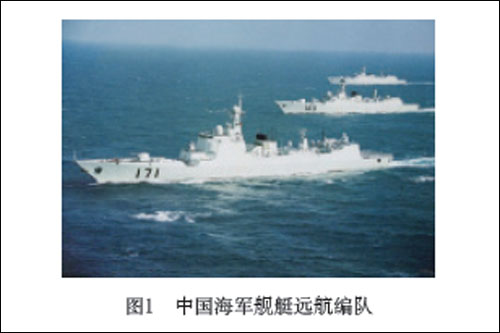
(2) 船体用铝合金
舰船的轻量化及合金材料再生利用的要求,使铝合金在实际应用中得到进一步的发展。铝合金由于具有密度小、比强度大以及无磁性、高导电性和导热性等特点, 已被用于建造中小型舰艇,主要目的是减轻舰艇的重量、提高航速和各种性能。
20 世纪60 年代以来,美国海军研制应用了耐海水腐蚀性能良好的Al-Mg-Si 系合金,及中强可焊的Al-Zn-Mg 系合金。目前,在船壳体结构上用的铝合金主要是5083、5086、5456 这三种合金,它们的耐腐蚀性能、机械性能和焊接性能都很好。俄罗斯在船体上使用较多的是Al-Cu-Mg 系合金,作为快艇壳体材料。
我国于60 年代以后形成舰船及装甲板用的铝合金系列,如LF 系、LD30、LD31、919 铝合金、147、4201 和180 铝合金等。
(3) 船体用钛合金
由于现代潜艇要求下潜深度愈来愈大, 钛合金具有高比强度、耐海水腐蚀、无磁性等特点,在潜艇上的应用相当广泛。是制造潜艇和深潜器耐压壳体极有前途的材料,各国都很重视船用钛合金的研究开发。
国外早在20 世纪50 年代就开展了钛合金的应用研究,70 年代以后,钛合金广泛应用于潜艇和深潜器的耐压壳体。俄罗斯在建造钛合金核潜艇研究和制造技术上, 处于国际领先地位,也是用钛合金建造耐压壳体的唯一国家。到目前为止俄罗斯研制的核潜艇已有四代,从第一代661 型(P 级) 试验性核潜艇开始就采用钛合金作耐压壳体。俄罗斯“阿尔法”级核潜艇耐压壳体是用钛合金制造的,据称下潜深度可达900m,水下航速42kn.
我国船用钛合金的研究始于20 世纪60 年代。几十年来,研究开发的船用钛合金基本能满足水面船舶、潜艇和深潜器的不同强度级别和不同部位的要求。
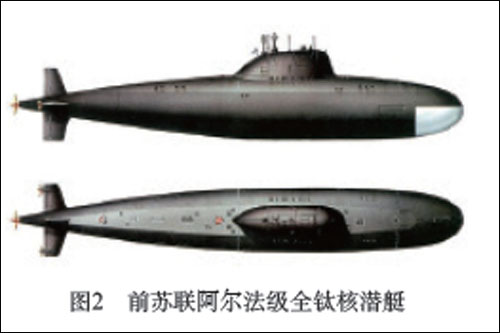
(4) 管系材料
舰上的消防管路,动力系统管路和冷却水系统管路经常因腐蚀、振动,而漏水、漏油、漏汽,称为“三漏”.为治理舰艇的“三漏”,只有在流速低于1.5m/s 时才选用紫铜管,一般情况下均推荐采用B10、B30 白铜管。在流速更高或需耐更强烈的冲刷腐蚀的情况,应选用钛管或双相不锈钢管。只有在流速不高、对防蚀性能也要求不高的情况下才采用普通铜管、钢管或镀锌管。
涂层保护
涂层保护分金属性涂( 镀) 层和非金属油漆涂层,后者在舰艇上被大量采用。与先进国家相比,我国现有舰船涂料的研制水平除个别特殊品种外基本相当,一般情况下,船体一次施涂后可达3~5 年内不需进坞重新涂装。
目前,对海洋大气部位、潮差飞溅区和水下部位的油漆保护已具有了多种配套体系和比较长的防蚀能力,但防污漆仍需加强研制。防污漆中有机锡已被国际上普遍禁用,氧化亚铜(或硫氰酸铜)渗出型涂料为国内舰船现用的防污漆,其防污期效仅为3~5 年。近年,低表面能防污漆在舰船上的应用取得了一定的进展。
电化学保护
电化学阴极保护技术在舰船腐蚀防护中始终占据着重要地位。
(1) 阴极保护所用材料及部件
①牺牲阳极材料
舰用牺牲阳极材料主要有锌基、铝基和铁基三种,其中铝基阳极由于电容量大, 可以通过合金改性获得高活性和高电化学效率,现已逐步取代锌基阳极全面用于船体的阴极保护设计。铁基阳极则多用于铜质管路的内壁保护。
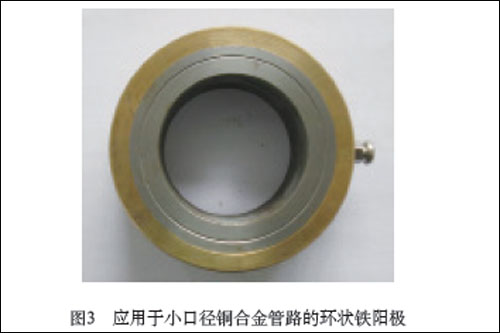
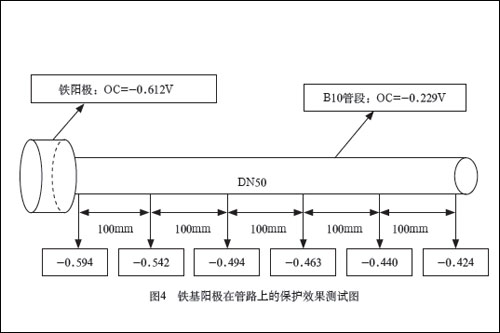
②外加电流阴极保护系统
外加电流阴极保护系统由控制电源、辅助阳极,参比电极及接地装置等组成。系统的寿命可与舰船服役寿命相当。
作为关键部件的辅助阳极主要有镀铂钛阳极和钛基贵金属氧化物阳极,由于钛基贵金属氧化物阳极价格低廉,制作方便, 已在各类应用中大量取代铂钛阳极,这些阳极的使用寿命能达到≥ 25 年。新型线型金属氧化物阳极的应用发展特别值得关注, 若能在舰船上取得应用突破,将极大扩展阴极保护的应用范围和保护效能。
(2) 阴极保护技术与其它防腐技术的联用
①阴极保护与涂覆层的联用:阴极保护与油漆涂层联用已有相当长的历史,彼此之间既可以相互提高保护功效,又必须不断提高其匹配兼容能力。近年研究较活跃的导电涂层,就是将阴极保护技术和涂层保护技术相结合,也是金属防蚀与防生物污损技术的综合。
②阴极保护与电解防污技术联用:阴极保护和电解防污同为电化学方法,可以将这两种技术在一个系统内完成。如在冷却管系中同时装上铜、铝阳极,当通上小直流电后,在铜阳极上析出铜离子抑制海生物附着,同时管路也作为阴极得到保护, 铝阳极溶解后形成Al(OH)3 粘胶,粘附在结构上也能起到防蚀的效果。
舰船腐蚀防护工作的启示
(1) 搞好我国舰船防腐的必要性
应该说美军的防腐管理和技术已处于国际领先水平,但为了进一步提高舰船装备的战备性、安全性,相应的防腐投入依然不断增加,并制定了长期的腐蚀防护技术发展战略。随着我国新舰船不断投入使用,腐蚀防护问题也会更加突出,为了保证装备完好性,减少腐蚀损失,搞好舰船装备防腐是必须完成的战略性任务。
(2) 系统性的开展材料腐蚀据积累及数据库建立等基础工作
随着我国新型舰船的研制和各类新材料的不断应用,系统性的开展材料环境腐蚀数据积累工作并建立功能强大的数据库, 既能够服务于新型舰船的设计、建造、使用和维护等各个流程,又能为后续舰的设计选材及防护提供必要的数据基础,从而效支持舰艇的全寿命维护工作。这方面的工作内容包括:常用材料(黑色金属、有色金属、涂镀层、高分子材料)在服役环境下的腐蚀试验及数据积累;管系材料在不同使用环境(包括温度、盐度、流速、含沙量等环境参数)下的腐蚀数据积累; 新型高强不锈钢在应用环境下的腐蚀性能以及与其他材料的匹配性能数据积累等。
(3) 加大对舰船腐蚀防护技术工程化验证的投入
针对目前缺乏对舰船装备腐蚀防护技术综合应用的工程化验证的情况,应进行系统全面的需求分析和调查规划,并增加相应投入。有必要在舰船装备研制生产过程中就提出明确的腐蚀防护技术的环境适应性要求,对材料、工艺、零部件乃至设备整机进行充分的工程化环境适应性验证试验。
(4) 建立信息交流与共享平台
防腐蚀信息共享和交流对于搞好舰船防腐具有十分重要的意义。我们可以借鉴美军的做法,建立我国舰船装备防腐蚀网络平台。在这个平台上,可以宣传有关装备防腐法规、开展技术推广和交流。除此之外,可以定期或不定期的召开舰船装备防腐交流会,出版相应的刊物等。
结语
解决舰船的腐蚀问题是一项长期、艰巨的任务,腐蚀的发生是必然的,抑制腐蚀的发生、发展则依赖与材料本身的耐蚀性、涂层体系、表面处理方法、电化学保护等多种技术手段的发展和应用。但最根本的是在掌握所用材料腐蚀性能的基础上, 合理的进行配套设计,将防腐蚀的思想贯彻到整个设计建造过程中,循序渐进的解决各类腐蚀问题,这样才能最大程度的避免腐蚀危害,为实现舰船全寿命全周期的腐蚀防护设计思想提供技术保障。
免责声明:本网站所转载的文字、图片与视频资料版权归原创作者所有,如果涉及侵权,请第一时间联系本网删除。
-
标签: 舰船腐蚀防护
相关文章
无相关信息
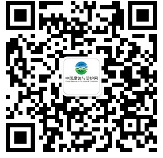
官方微信
《腐蚀与防护网电子期刊》征订启事
- 投稿联系:编辑部
- 电话:010-62316606-806
- 邮箱:fsfhzy666@163.com
- 腐蚀与防护网官方QQ群:140808414
点击排行
PPT新闻
“海洋金属”——钛合金在舰船的
点击数:8135
腐蚀与“海上丝绸之路”
点击数:6475