随着海洋强国战略的推进,开发海洋工程装备已上升为国家战略层面。海洋工程包括资源开发、装备制造和军事工程等,其中海洋平台、船舶舰艇、海底管路等重要的装备设施均由金属材料制造而成[1]。在海洋环境下,耐腐蚀性是保证金属材料服役稳定性和寿命的关键因素。早期,多数海洋工程设施由钢材制造,存在耐蚀性差、密度大等缺点,无形中增加了海洋工程装备的重量,不符合国家轻量化的发展需求。相比而言,铝合金具有质轻、比强度高、加工性能优良等特点,因而早已广泛应用于航空航天、交通运输和建筑工程等行业[2-3]。由于铝合金表面形成的钝化膜对于保护基体、抵抗海洋环境下的腐蚀有着重要作用,因此铝合金成为使用率仅次于钢的第二大金属材料,在海洋工程领域应用前景广阔,将铝合金作为一种新型材料应用于海洋工程成为当前的研究热点[4-5]。
1 铝合金的应用
铝合金是一类有色金属,具有密度低、强度高等优点,且兼具优良的导电性、导热性和耐腐蚀性能。从19 世纪末开始,铝合金逐渐在船舶制造、海洋工程领域有所应用,到20 世纪五六十年代,新技术使得铝合金在耐腐蚀和强度性能上取得了突破,自此被广泛应用[6-8]。由于海洋工程装备的不同结构件服役的环境、受力也不同,因此根据实际应用开发出1~8种不同系列的铝合金,其中2 系、5 系、6 系和7 系铝合金是海洋工程装备制造时常用的4 个系列。
2 系铝合金是一类硬质合金,主要分为Al–Cu 系和Al–Cu–Mg 系[9]。2024–T4 属于Al–Cu–Mg 系,无磁性,硬度约为HB120~145,是海洋石油钻杆的主要材料,用来开采海洋石油和天然气资源[10-11]。2024铝合金具有质轻、强度高等特点,与传统钢相比,能够减轻钻机负荷、节约能耗,提高钻杆在H2S 等恶劣环境中的耐腐蚀能力,降低海洋平台总质量[12-13]。Al–Cu 系铝合金(如2A10、2A12 和2A14 等)曾为船舶、舰艇外壳的制造材料,后因腐蚀性能的限制,被高系铝合金替代[14]。目前,2A10 是铝合金船体、民用船舶上层建筑专用的铆接构件[15-16]。
5 系铝合金主要为Al–Mg 系列,根据Mg 合金含量的不同,又将其分为不同牌号,海洋工程常用的5系铝合金牌号见表1[17]。5 系铝合金因耐腐蚀性优异,因而在海洋工程领域的应用较多[18]。在船舶制造中,表1 海洋工程用5 系铝合金的化学组成(质量分数)[17]壳体结构采用5083、5086 铝合金,5052 和5454 铝合金用来制作船舶甲板和上层舾装壁板[14, 19-21]。在海洋运输过程中,液化天然气(LNG)储罐对材料性能的要求较苛刻,需在低温下保证材料的强度、力学性能和腐蚀性能不受影响,5083 铝合金具有同时满足以上条件的性能,是可燃冰、天然气等海上低温储存装置的主要制造材料[22]。海洋运输容器(如油箱、水泵、导管、散热器、烟囱等船舶零配件)采用5A 系列铝合金。在海洋和海岸设施建造中,海洋平台停机坪的材料开始由传统用钢向铝合金转变,耐蚀铝合金的使用节约了腐蚀维护、涂装防护涂层的成本,减轻了平台的自质量,铝合金的抗震动、抗冲击等性能也缓解了飞机起落对海洋平台的冲击。5754 铝合金常用来建造船舶停靠码头的浮坞,对于防止浮坞在浪花飞溅区的腐蚀、延长使用寿命具有重要意义[23]。5 系铝合金在海洋军事上也有所应用,如护卫舰、快艇及炮艇的壳体材料。
6 系铝合金指Al–Mg–Si 系列合金,其具有可塑性和加工性能良好等优点,经过冲孔、挤压等工艺锻造成为型材、板材,可应用于船舶甲板、壳体结构,船舶上层建筑的门、窗、盖等配件及生活区域的床柜、家具等也多采用6 系铝合金[24-25]。6 系铝合金常见的牌号为6063、6061、6005A 和6063,最初用于建筑工程,后由于其具有优异的力学性能和焊接性能,开始用于船舶制造(如用于制造船舶舷窗)。6063 是辽宁号航空母舰建造中使用频率最高的一类铝合金[26-27]。6061 可用来制作船上的桅杆、舷梯等,但可焊性较差,因此常作为铆接构件使用[19]。
7 系铝合金是一类高强韧合金,最初作为航天材料被开发,后来逐渐应用于轨道交通、船舶制造等领域。在海洋工程方面,深潜器、鱼类外壳及其发射器常使用7 系铝合金[28]。7075 铝合金拥有高强比和抗疲劳性能,是工业上常用的结构材料[29-30]。由于Al–Zn–Mg–Cu(7 系)铝合金的显微组织较复杂,存在金属间化合物和强化相,发生晶间腐蚀、点蚀的危险性较大,因此在海洋上的应用范围受到极大限制,仅用于制造少部分承重和受力构件[31]。7A33 被称为海洋铝合金,弥补了7 系铝合金腐蚀性能较差的短板,是继5 系后耐腐蚀性能较佳的铝合金,硬度与2系硬质铝合金相当,已经被用来制造水上飞机、直升机和两栖飞机[17]。
2 铝合金在海洋环境中的腐蚀
根据材料在海洋环境中发生腐蚀的位置,将海洋环境分为海洋大气、浪花飞溅、海洋潮差、海水全浸和海底海泥等5 个区域[32]。根据海洋工程用钢在不同服役区域腐蚀程度的差异,绘制腐蚀速率图(见图1)[33]。从图1 可以看到,在海洋大气区,由于金属表面薄液膜中的氯离子浓度较高,因此易使材料出现腐蚀失效现象;在浪花飞溅区,工作的机械装备受到干湿交替、冷热变化的影响,腐蚀程度最严重;在海水全浸区,虽然溶解氧含量较低,但海洋工程装备仍会受到海水中各种类型离子(如SO42?、Cl?)的侵蚀,其表面仍会出现腐蚀损伤。除此之外,由深海区域的微生物,以及交变压力引起的腐蚀疲劳和应力腐蚀等都是海洋工程装备服役时的潜在威胁,因此下面综述一下铝合金在海洋大气、浪花飞溅、海水全浸等3 个区域的腐蚀行为。
图1 海洋区域的划分和钢的腐蚀速率[33]
2.1 海洋大气区
在海洋大气环境下,金属表面会形成一层盐浓度极高的薄液膜,致使金属腐蚀速率约为内陆大气环境下的2 倍。在大气环境下,金属腐蚀常用的测试手段有2 种:室外暴露和室内加速实验。室外暴露实验耗时长,放样和取样过程困难,但测试环境与材料实际应用环境相符,实验结果准确可靠。室内加速实验可控性强、操作简单,在实验箱中即可进行,但模拟环境与实际环境有所差异,只能考虑主要的影响因素,实验结果有待验证。学者们[9, 34-37]针对海洋大气环境中各类铝合金的腐蚀行为研究得较多,对于腐蚀发生的机理也进行了探讨。
Sun 等[9]在中国青岛、广州、琼海和万宁等地的4 个沿海实验点进行了20 年的暴露实验,同时在实验室开展了腐蚀加速实验,研究了2024–T4 铝合金的剥落腐蚀行为。结果表明,在万宁测试的样品最先出现剥落腐蚀,广州的样品最晚发生剥落腐蚀,剥落腐蚀的发生与铝合金表面海盐颗粒数量、湿度和温度密切相关。测试结果表明,2024–T4 表面主要形成了γ–Al(OH)3 和α–Al2O3·3H2O 等2 种铝化合物。张欢等[34]通过SO2 盐雾实验模拟海洋酸性大气环境下2024–T351 的腐蚀情况,发现铝合金表面出现了大量的圆形状腐蚀坑,腐蚀产物呈网状,在电化学测试中电荷转移电阻(Rct)先减后增,这是Cl?与腐蚀产物间的相互作用所致。Li 等[35]为了加深对铝和镁合金连接件在海洋大气环境下腐蚀行为的理解,将连接件放置于夏威夷海洋实验点户外暴露6 个月后对样品表面进行SEM 观察(见图2),发现连接件发生了缝隙腐蚀,铝合金在连接区域内的腐蚀情况较严重,产生了微米级的腐蚀坑(见图2c2),腐蚀产物为水铝矿(γ–Al(OH)3)。Cui 等[36]将7A01 铝合金放置于西沙群岛高湿热大气环境下进行户外暴露实验,测试时间为4 年,期间取不同暴露时长的样品进行失重、电化学阻抗(EIS)等腐蚀检测。结果表明,在室外暴露1 个月后Nyquist 图中先出现了感抗弧,后来感抗弧消失,这预示着点蚀开始发生。利用等效电路图对EIS 曲线进行拟合,根据拟合结果计算样品的极化电阻(Rp)发现,暴露时间为1 年和2 年的铝合金的Rp 值最高。由于Rp 值与耐腐蚀性能呈正相关,故暴露一段时间后的样品较全新样品的耐腐蚀性能好,说明铝合金表面形成的腐蚀产物层进一步抑制了腐蚀。当实验进行到中后期时,铝合金表面出现剥落腐蚀,这与腐蚀产物在晶界处堆积后引发的楔形效应有关。Zhao 等[37]为了确定大气污染物对铝合金海洋大气腐蚀行为的影响,在青岛对7A85 铝合金进行了长期室外暴露实验。结果发现,铝合金的力学性能显著下降,屈服强度和伸长率分别降低了24.5%和79.2%。7A85中的金属间化合物Al2CuMg 和Al7Cu2Fe 不仅破坏了表面钝化膜,还作为阴极与基体形成了微电偶腐蚀对,导致点蚀的出现[38]。另外,环境中的硫化物污染物在腐蚀区域溶解,与腐蚀介质共同深入晶界区,从而加速了腐蚀。
以上研究表明,在海洋大气区这种高盐、高湿、高辐照环境下,铝合金表面形成了具有高Cl?浓度的薄液膜,其会不断侵蚀和破坏氧化膜的完整性,薄液膜的厚度不同造成的腐蚀损伤也有所差异。铝合金表面除了会形成氧化物膜和薄液膜外,工业海洋大气环境中的SO2、NO、PM2.5 等污染物也会沉积在铝合金表面,形成污染物层。这些成分多样、厚度不一的电解质溶液会导致铝合金在海洋大气区的腐蚀行为非常复杂,这也成为当前腐蚀科研人员重点研究的方向。
2.2 浪花飞溅区
浪花飞溅区处于海–气交界面,指位于海域平均潮位以上、海浪飞溅波及的最高点以下的区域[39]。浪花飞溅区处于干湿交替条件下,兼具薄液膜和海水全浸等2 种腐蚀形态,2 种腐蚀形态循环交替存在,致使海洋工程装备在浪花飞溅区的腐蚀最为严重 [40]。浪花飞溅区的氧含量充足,海水液膜在阳光照射下被蒸发,致使液膜厚度变薄、盐浓度增大[41]。相较于大气腐蚀,浪花飞溅区腐蚀一直处于干湿交替变化中[42],海浪冲击着金属表面形成的保护性钝化膜,对材料施加着来自不同方向的冲击力[43]。由此可见,浪花飞溅区遭受着全部类型的腐蚀破坏,包括全面腐蚀、局部腐蚀和应力腐蚀[44-45]。
图2 化学清理后铝片的表面图片(a)以及图a 中位置1—3 的扫描电镜图(b1—d2)[35]
学者们对浪花飞溅区合金钢腐蚀行为的研究较多[40-41, 43-44, 46-48],对于铝合金的研究文献较少[49-50]。Liang 等[50]在浪花飞溅区、海洋潮差区和海水全浸区对6060 铝合金进行了2 年的暴露实验,得到的浪花飞溅区腐蚀形貌如图3 所示。从整体来看,铝合金表面出现了局部腐蚀,放大图箭头指示发现颗粒间隙的存在,这种现象被以往文献认为是发生了晶间腐蚀[51-52]。3 个区域铝合金的腐蚀行为存在差异,铝合金在海水全浸区的局部腐蚀最严重,其次是浪花飞溅区和海洋潮差区。Hou 等[49]和李春玲等[53]分别利用热喷涂和电弧喷涂方法在钢表面制备了铝合金涂层,2 个团队都设计了室内加速测试装置来模拟铝合金涂层在浪花飞溅区的腐蚀,前者发现,铝合金涂层在浪花飞溅区和海洋潮差区均表现出良好的耐腐蚀性能,并且在浪花飞溅区没有出现像裸钢那样严重的腐蚀速率峰值;后者的实验结果表明,铝合金涂层比基体钢失重小,耐腐蚀效果良好,当涂层发生点蚀导致完整性被破坏后,仍可以作为牺牲阳极对基体钢起到保护作用。
通过文献调研发现,在浪花飞溅区,铝合金与钢不同,没有出现腐蚀加速行为。随着铝合金在海洋工程领域应用量和范围的增加,加之浪花飞溅区是腐蚀发生的重灾位置,研究海洋工程常用的5 系、6 系铝合金在浪花飞溅区的腐蚀行为显得极为迫切。目前无针对浪花飞溅区铝合金腐蚀的系统研究。
2.3 海水全浸区
图3 6060 铝合金在浪花飞溅区的腐蚀形貌[50]
在海水全浸区,随着海水深度的增加,pH 值、溶解氧含量、压力、温度等因素也发生着变化,因此材料在表层海水中与深海的腐蚀行为有所不同[54]。在表层海水中,腐蚀的主要原因为Cl?破坏了钝化膜,导致点蚀发生。Kim 等[55]为了确定不同铝合金在海水环境下的最优性能,进行了多组电化学测试,发现高强7075 铝合金的电流密度最大,5456 铝合金的电流密度最小,在海水中的耐腐蚀性最好。Zhang 等[56]在渤海湾海水中对5A06 合金进行了力学和腐蚀实验,经海水浸泡后铝合金表面出现了点蚀和剥落腐蚀,但腐蚀破坏没有影响到铝合金的力学性能。当浸泡到第12 天时,5A06 铝合金的疲劳寿命下降得最明显,减少了54.83%。随着浸泡时间的延长,腐蚀寿命逐渐增加并趋于稳定,这是由于裂纹尖端的钝化减少了加载过程的裂纹扩展。Lokas 等[57]为了对比温度变化对铝合金腐蚀行为的影响,将AA5083 铝合金置于在Sibenik 地区收集的海水和咸水电解质中进行腐蚀实验。结果表明,在18、25、30 ℃等3 种温度下,腐蚀都起始于阴极沉淀物周边的铝基体,两者形成的微电偶促进了腐蚀的发生;在温度为25 ℃和30 ℃海水中,铝合金表面出现了更多的点蚀坑。Ahmad 等[58]在阿拉伯半岛海水中对6092 铝合金进行了局部腐蚀测试,6092 铝合金表面形成的Al(OH)3 和Al2O3·3H2O对基体起到了保护作用,抑制了腐蚀的发生,金属间粒子Al2Cu 是点蚀发生的首选位置。肖宝靓等[59]将船用5083 铝合金置于静态海水中进行浸泡腐蚀实验,结果表明,海水中Cl?首先会依附在铝合金表面活性位点上,与钝化膜发生反应,使其溶解破坏,致使基体外露;Cl?与铝基体反应生成了可溶性AlCl3,产生了腐蚀坑;在测试时间2 个月后,腐蚀产物的堆积起到了屏障作用,使隔离铝基体免受腐蚀侵害。
在深海极端环境中溶解氧含量较低、盐度较高,静水压力随着海水深度的增加不断升高。除热液区外,深海平均温度为3 ℃。与表层海水相比,pH 值、氧含量、静水压力等因素的变化会对铝合金的腐蚀产生额外影响[60-61]。彭文山等[62]研究了1060 铝合金在不同海水深度下浸泡不同时间的腐蚀行为,结果发现,腐蚀类型以点蚀和缝隙腐蚀为主。随着海水深度的增加,铝合金逐渐出现白色絮状腐蚀产物,覆盖范围也逐渐扩大,说明静水压力加速了铝合金的腐蚀。孙飞龙等[63]将5052 和6061 铝合金置于南海水深为800 m 和1 200 m 处进行腐蚀实验,发现与浅海腐蚀类似,两者均发生了点蚀和铆接处的缝隙腐蚀,只是深海腐蚀程度更严重。在深海中,溶解氧含量的降低不仅促进了Cl?的渗透,也增加了点蚀形核,还抑制了氧扩散,形成了氧浓差电池和闭塞电池,两者共同作用增加了深海环境中点蚀发生的敏感性。另外,由于6061 铝合金中的MgSi 相与Al–Fe–Si 基体间形成的微电偶电位差较大,所以6061 铝合金比5052 铝合金的点腐蚀更严重。Canepa 等[64]利用超级中微子探测器测试了5—8 系铝合金在意大利西部3 350 m 处海域的腐蚀行为,发现4 类铝合金中6 系合金最耐腐蚀,8 系的腐蚀性最差。8 系铝合金主要以点蚀为主,7 系铝合金则受到点蚀、缝隙腐蚀和脱落腐蚀的共同影响,这与7 系铝合金中富铜相有关。
3 铝合金其他类型的腐蚀
从铝合金在海洋大气区、浪花飞溅区和海水全浸区的腐蚀行为可知,铝合金在海洋环境中的腐蚀以点蚀、晶间腐蚀和剥落腐蚀为主。由于海洋工程装备的服役环境较复杂,因此铝合金在外界条件干扰下还会发生其他类型的腐蚀,如应力与腐蚀环境耦合而引发的应力腐蚀、冲刷腐蚀、腐蚀疲劳等;铝合金与其他不同材料接触时因电位差不同导致的电偶腐蚀;由海水中活性生物引起的微生物腐蚀等[65]。根据腐蚀发生的频率和危害性,下面对海洋工程用铝合金的应力腐蚀和微生物腐蚀进行详细介绍。
3.1 应力腐蚀
应力腐蚀开裂(SCC)指在腐蚀环境中,金属或合金材料由于内部裂纹扩展,造成完整材料突然发生脆断的现象。裂纹扩展是一个长期的过程,由于脆断是毫无预兆的,因此易出现巨大的灾难和财产损失[66]。前文提到,7 系铝合金具有高强韧特性,是海洋工程承力构件的常用材料,也是遭受应力腐蚀危害最深的一类铝合金。Wang 等[67]研究了2024 铝合金和7075铝合金在含Cl?的溶液和薄液膜中的SCC 行为,以此模拟铝合金在海水和海洋大气环境下的腐蚀。结果表明,2024 铝合金在薄液膜中的腐蚀破坏和SCC 敏感性比溶液中更严重,而7075 铝合金虽在薄液膜环境下的腐蚀情况较严重,但SCC 敏感性却比在溶液中轻。铝合金表面发生阳极溶解会产生缺陷,促进溶液中氢的放电、渗入和脆化,在应力、阳极溶解和氢脆的协同作用下7075 铝合金在溶液中的SCC 敏感性最大。吴建山等[68]对Al-Zn-Mg 合金在不同加载方向下的SCC 行为进行了研究,加载方向设置为横向和纵向。结果表明,横向试样在312 h 时发生断裂,纵向拉伸试样在360 h 时仍未发生断裂,并且在横向试样处测得的腐蚀电流密度是纵向试样的5 倍,可见7 系铝合金在纵向拉伸时的抗应力腐蚀能力较强。
3.2 微生物腐蚀
海水中的微生物腐蚀是困扰铝合金结构安全稳定的另一大难题,海洋中常见的微生物种类有硫酸盐还原菌(SRB)、铁氧化菌(FOB)、产酸菌(APB)等[69-70]。SRB 作为一类厌氧微生物,常寄生于海洋油气工程管道内部和海底海泥区,对海洋工程金属构件的腐蚀危害较大[71-72]。针对SRB 在海洋工程用钢腐蚀行为的研究较多,其作用机理为H2S 或其他酸性代谢产物改变了基体表面的局部环境,SRB 代谢过程中会消耗阴极氢,导致腐蚀加速[73]。目前,微生物对铝合金腐蚀行为的影响逐渐受到学者们的关注。Andrade 等[74]和Guan 等[75]都对海洋常用的5052 铝合金的SRB 腐蚀行为进行了研究,有趣的是两者的实验结果大不相同,前者认为SRB 分泌的胞外聚合物(EPS)在铝合金表面形成了具有保护作用的生物膜,使其较未含SRB 体系的腐蚀速率有所降低;后者认为SRB 的代谢产物HS?与阳极溶解的Al3+形成了Al2S3,然后水解形成了Al(OH)3,这一过程加速了铝的阳极溶解。阴极产生的氢气易被SRB 捕获和利用,使其代谢活性增加,因此SRB 通过影响阴、阳极反应加速了铝合金的腐蚀。后来,Guan 等[76]再次对5052 和Al-Zn-In-Cd 铝合金的SRB 腐蚀行为进行了对比分析,结果与先前保持一致,只是Al-Zn-In-Cd 铝合金的耐蚀性能较好,原因是Zn 元素的加入起到了杀菌效果。从以上文献看出,海洋环境中微生物对铝合金腐蚀的作用机理观点尚未一致,且研究并不系统。目前,铝合金在海水淡化、海洋油气开发装备等海洋工程领域用量不断增多,为了避免其遭受更严重的破坏,对微生物腐蚀的研究已迫在眉睫。
4 铝合金的腐蚀防护
由于铝合金表面形成的钝化膜厚度仅为纳米级,在Cl?和低溶解氧作用下很容易被破坏,从而引发腐蚀,严重时会造成海洋工程装备的失效[77]。为了延长海洋工程装备的使用寿命,扩大铝合金的应用范围,对其进行腐蚀防护是非常必要的。在海洋环境下,常用的腐蚀防护方法有阴极保护、缓蚀剂、阳极氧化、保护涂层等[78-79]。
4.1 阴极保护
电化学阴极保护一般指2 种方法,一种是对被保护金属施加外部电流,使其电位始终处于阴极范围内,从而不会被氧化;另一种是牺牲阳极,即在被保护金属上连接电位更负的另一种金属,形成腐蚀原电池,添加的金属作为阳极,被保护金属作为阴极[80]。Simoes 等[81]在铝合金表面制备了一层富镁涂层,利用扫描振动电极和扫描电化学显微镜测试了富镁涂层对基体的阴极保护效果,研究发现,富镁涂层能够抑制铝合金表面点蚀成核,降低已形成的点蚀坑中阳极的活性。阴阳面积比在腐蚀速率上起着积极作用。Dinh 等[82]利用表面沉淀对AA7075 和AA6061 铝合金进行了阴极保护,将铝合金切割为厚度1 mm 的小块后,通过不同热处理(HT)方式在其表面生成MgZn2、Al2MgCu 和Mg2Si 沉淀产物,作为牺牲阳极,形成小型阴极保护装置(见图4)。开路电位、零电阻电流和CuSO4 浸泡测试均证明,表面沉淀物对于铝基体来说为阳极,首先发生溶解,为Al 基体提供阴极保护,这种表面沉淀的阴极保护方法与其他方法相比具有操作简单、经济有效等优点。由于铝合金的电位较低,常被用作牺牲阳极,因此单独采取阴极保护方法对铝合金进行腐蚀防护的应用实例较少,在实际工程中一般将其与其他防腐方法搭配使用[83]。
4.2 缓蚀剂
缓蚀剂是一类向腐蚀介质中添加后能有效抑制金属腐蚀的物质,其种类众多,常见的类型包括有机、无机、稀土和天然缓蚀剂[84]。为了减少对环境的污染,目前对于铝合金缓蚀剂的研究主要集中在环境友好的天然和稀土缓蚀剂。Byrne 团队[85-86]研究了将天然化合物单宁酸作为缓蚀剂对在中性NaCl 溶液中铝合金防腐性能的影响,发现在单宁分子吸附和掺入腐蚀产物的生成过程中,形成了保护性的三维钝化层结构,延缓了阴阳两极反应,显著降低了铝合金的腐蚀速率。Tang 等[87]利用理论计算和实验方法研究了香豆素对铝合金的缓蚀行为,发现香豆素自发以平行方式吸附在铝合金表面,香豆素中的C=O 键是最易发生吸附的位置。香豆素的最佳缓蚀浓度(质量分数)为0.5%,过量缓蚀剂会导致竞争性和不稳定吸附。香豆素作为绿色缓蚀剂可以在工业和工程领域应用。Deyab 等[88]研究了海水环境中稀土化合物CeCl3 和Ce2(SO4)3 对AA6061 铝合金的缓蚀作用,结果表明,2 种铈盐的添加扩大了钝化电位的区间,能有效抑制AA6061 的腐蚀,Ce2(SO4)3 的防腐效果优于CeCl3。稀土化合物的存在促进了铝合金表面Ce2O3/Ce(OH)3薄膜的形成,阻断了腐蚀活性位点,提高了腐蚀活化能,降低了铝合金的腐蚀速率。
图4 AA7050 铝合金表面经470 ℃热处理1 h 后以150 ℃/min 速度冷却到不同温度及保持不同时间的扫描电镜图[82]
总的来说,添加缓蚀剂是一种可操作性强、成本低、防腐效果显著的方法,只是缓蚀剂的使用范围受限,绝大部分缓蚀剂需要在溶液中才能发挥作用。因为海洋是一个相对开放的环境,无法将缓蚀剂直接投入其中使用,所以缓蚀剂解决的主要是海洋工程设施内部的腐蚀问题,比如海底管线内部、海洋油气田的采油系统。通过向腐蚀介质中添加缓蚀剂,使缓蚀剂伴随着溶液的流动到达金属表面,并形成一层保护膜,从而起到缓释作用[89]。
4.3 阳极氧化
阳极氧化是利用电化学方法在金属表面原位生成一层氧化物薄膜[90]。阳极氧化膜在酸性环境下的稳定性较差,在外部环境刺激下易发生膜损伤,威胁着内部基体的安全。为了改进和优化阳极氧化工艺,微弧氧化(Microarc Oxidation, MAO)技术应运而生。与传统阳极氧化涂层相比,MAO 陶瓷膜能够在复杂形状的工件上制备,与基体结合紧密,具有耐高温、耐腐蚀和耐磨损等优异性能[91-92]。在涂层制备过程中,电解液成分、电参数、温度和基体成分等对氧化物陶瓷膜的性能起着举足轻重的作用[93-96]。铝合金作为微弧氧化常用的阀金属,其表面MAO 涂层的制备和腐蚀性能的研究一直受到专家学者们的关注[97-98]。Wang 等[97]利用微弧氧化在7075 铝合金表面制备了腐蚀防护涂层,在模拟海水溶液中对涂层进行了划伤测试。结果表明,MAO 涂层与基体结合良好,主要成分为α–Al2O3 和γ–Al2O3,涂层形成了良好的屏障作用,从而使基体免受腐蚀,在涂层被划伤后其腐蚀速率仍比7075 铝合金低一半,对铝合金基体依然具有保护作用。Gong 等[98]在铝合金表面创新性地制备了负载CeO2 的MAO 薄膜,研究了薄膜的自修复和腐蚀性能,发现CeO2 与电解质中的H+和H2O2 反应生成O2 和Ce3+后,铝与O2 和H2O 反应生成Al(OH)3,能够愈合表面受损的MAO 薄膜,使得负载CeO2 的MAO 薄膜的防腐性能得到大幅提升。Liang 等[99]为了提高铝合金钻杆的腐蚀和磨损性能,利用超声波冷锻技术(UCFT)和微弧氧化方法在其表面制备了涂层,发现UCFT+MAO 涂层拥有较高的显微硬度和耐磨性。EIS 测试结果显示,与铝合金相比MAO 涂层的阻抗值提高了2.4 倍,UCFT+MAO 涂层提高了7.7倍,说明强化涂层有利于提高2618 铝合金的防腐能力。Wang 等[100]在7050 铝合金表面制备了不同厚度的MAO 涂层,用硅烷偶联剂改性后涂刷聚氨酯(PU),通过对MAO+PU 涂层进行电化学腐蚀评价发现,涂层的厚度和孔隙率与硅酸钠浓度呈线性关系,当硅酸钠的质量浓度为12 g/L 时,MAO+PU 涂层的黏结力最好,经MAO 修饰的聚氨酯涂层的耐蚀性比未经修饰的更优异。
4.4 保护涂层
根据表面防护涂层成分的不同,将其分为金属涂层、有机涂层和无机涂层。铝合金的表面防腐常采用金属涂层和有机涂层。金属防腐涂层一般通过喷涂、激光熔覆等方法制备[101-103],有机涂层则是在铝合金表面涂敷涂料,常用的防腐涂料有氟碳、聚氨酯、环氧树脂等[104-105]。邱实等[106]利用超音速火焰喷涂技术在2024 铝合金表面制备铝基非晶涂层,并与基体的腐蚀行为进行对比,发现涂层表面发生了均匀腐蚀,而2024 铝合金局部出现了点蚀坑,涂层的低频阻抗模值为2024 铝合金基体的4 倍,表现出优异的耐腐蚀性。Li 等[107]利用高能激光束在铝合金表面熔覆了AlxCrFeCoNiCu 高熵合金涂层,观察涂层的显微组织变化情况,对涂层在模拟海水中的腐蚀性能进行了研究。结果表明,随着Al 添加量的增加,涂层的晶体结构由面心立方(FCC)向体心立方(BCC)转变,晶体形态先由胞状向树枝状枝晶发展,后枝晶消失,当Al 的质量分数达到2%时出现了晶间裂纹。从极化曲线可知,所有涂层均出现钝化区,说明涂层表面都形成了钝化膜,涂层的腐蚀电流密度明显低于基底,证实钝化膜对涂层起到了良好的保护作用。随着Al含量的增加,涂层的腐蚀电流密度先降低后增加,Al0.8CrFeCoNiCu 涂层的腐蚀电流密度相对最小,说明其耐腐蚀性相对最好。从图5 和图6 可以明显看出,基体表面腐蚀程度比涂层严重,AlxCrFeCoNiCu(x为0%~0.8%)涂层出现了晶间腐蚀,高铝含量涂层则发生了严重的点蚀现象。Zeng 等[108]在铝合金表面涂敷双硅烷预聚物改性的环氧树脂防腐涂料,并对其腐蚀行为进行了研究,发现长期浸泡后,防腐涂层仍能保持较低的电容、较高的电荷转移电阻,说明改性环氧涂料具有防水渗透性和基底防腐能力,另外还发现其具有自愈合能力。
图5 基体表面腐蚀形貌[107]
图6 AlxCrFeCoNiCu 涂层表面腐蚀形貌[107]
5 结语
铝合金的力学性能和腐蚀性能优良,是一种广泛应用于海洋工程领域的新型金属材料。研究铝合金,特别是研究常用的5 系和6 系铝合金在海洋环境下的腐蚀行为具有避免海洋工程装备失效和减少经济损失等重要意义。与陆地腐蚀相比,海洋腐蚀还包含Cl?、溶解氧含量、pH 值和湿度等影响因素,所受的腐蚀损伤更加严重。不仅如此,海洋大气区、浪花飞溅区和海水全浸区作为金属表面发生腐蚀速率最高的3 个区域,其腐蚀类型各有差异。针对铝合金在海洋环境中的腐蚀损伤,一般采用电化学保护、缓蚀剂、阳极氧化和保护涂层等方法。文中总结了海洋工程用铝合金的类型和应用场所,以及铝合金在不同海洋区域的腐蚀行为和防护方法,根据铝合金在使用过程中存在的问题,指出未来重点研究的方向。
1)加强高性能铝合金国产化研究与开发。近些年,虽然铝合金的国产化水平一直在提升,但是在显微组织均匀度、晶间沉淀物尺寸等方面仍是短板,导致国产铝合金难以在长期服役于恶劣环境的大型受力结构件的零部件中使用,如船舶制造用的5083 和7A33 铝合金均依赖进口。由此可见,需进一步优化铝合金铸造工艺和轧制过程,研发高性能的国产铝合金。
2)深入分析海洋环境中铝合金的腐蚀与应力、微生物等多因素的耦合关系,探讨其腐蚀机理。随着海洋工程装备中铝合金用量的不断提升,对铝合金的寿命和工作强度提出了新的要求。研究单一因素影响下铝合金的腐蚀已不能满足当下需求,探究多因素耦合作用下铝合金的腐蚀行为是未来的发展趋势。例如微生物对铝合金电偶腐蚀的影响,在含有微生物溶液中铝合金的应力腐蚀开裂倾向等,这些都是值得探究的问题,毕竟多因素耦合作用下的腐蚀才真正符合铝合金的实际服役环境。
3)继续加强防腐技术的创新。为了使防腐效果更稳定、更持久、更有效,避免进行铝合金表面的二次防腐,应加大对新型缓蚀剂、防腐涂层材料的开发。设计开发出针对不同海域、不同海深的自修复防腐涂层,使涂层具有自愈合能力,防止表面损伤。应用多重手段协同进行腐蚀防护,如阴极保护与有机防腐涂料、MAO 涂层相结合的防腐方式。
参考文献:略
免责声明:本网站所转载的文字、图片与视频资料版权归原创作者所有,如果涉及侵权,请第一时间联系本网删除。
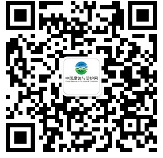
官方微信
《腐蚀与防护网电子期刊》征订启事
- 投稿联系:编辑部
- 电话:010-62316606-806
- 邮箱:fsfhzy666@163.com
- 腐蚀与防护网官方QQ群:140808414