涂料工业: 随着环保要求的提高和“双碳”目标的提出,制造业在实现绿色转型中扮演着重要角色,也面临着前所未有的节能减排压力。农机涂装是整车制造过程中高能耗、重污染的环节,在整车制造过程中贡献了较多的碳排放量。为了实现企业的“双碳”目标,农机涂装线新建或改造需要采用绿色前处理、环保涂料、自动化喷涂、余热回收利用、智慧能源管理等绿色低碳技术减少能耗、降低“三废”等污染物的产生和排放。 1.1. 环保型涂料 传统溶剂型涂料在生产和使用过程中会产生大量的污染物,对环境造成严重影响;近些年,依环保要求国家鼓励使用水性、高固分、粉末涂料等低VOCs含量的环保型涂料替代传统溶剂型涂料,降低涂料自身所产生的污染。不同涂料的各项性能对比如表1所示: 表1 不同涂料的各项性能对比 近些年较多农机涂装线改造将溶剂油性漆切换成水性漆。在生产运行中,发现产生的VOC废气浓度虽然降低了,但是对于环保标准比较严苛的城市来说,仍需要加废气处理设施,且水性漆对施工的温湿度较为敏感,喷漆室在生产阶段需要启动空调控制温湿度,这些无疑增加了动能能耗、设备维护及运行成本;对于增加的动能能耗会带来较多的碳排放量,不利于实现低碳环保的要求。随着粉末涂料在制造业的广泛应用,粉末涂料价格逐步降低,且具有粉末回收利用率高、无“三废”产生及处理设施、综合能耗低的优点,因此在农机结构件涂装线正在逐步推广应用。 1.2. 环保型低温脱脂剂 涂装前处理使用的传统脱脂剂的槽液温度一般为50~55 ℃,在生产过程中随着对工件的清洗将会带走部分槽液热量,因此脱脂剂槽液需要一直加热保持工作温度,能耗较高。低温脱脂剂多数为环保型,其工作温度通常为25~45 °C,针对油污较重的场合的工作温度稍微高些为40~45 ℃,在该温度下也能达到与传统脱脂剂相当的效果,减少能耗约20%,具有明显的节能降碳作用。 2.1. 前处理绿色技术 (1) 短流程工艺 传统的脱脂和磷化工艺需要在50~60 ℃的温度下进行,消耗大量能源。随着绿色低碳发展要求,更环保、低能耗的硅烷或新型防安途工艺正在逐步取代传统磷化工艺。硅烷或新型防安途不仅无毒无磷无重金属离子无沉渣,而且工作温度较低或常温,无需加热达到节能降碳的目的,还可以简化工艺流程、缩短处理时间、获取更优异的防腐蚀性能。其磷化、硅烷、防安途等工艺流程如图1所示,各项性能对比如表2所示。 图1 多种形式前处理工艺流程图 表2 不同前处理工艺的各项性能对比 (2) 电泳废水回收EDRO技术 电泳工艺段主要包括电泳、后冲洗工序,电泳采用全浸及出槽UF水喷淋相结合的方式。传统的电泳系统采用UF过滤回收技术,如图2所示,实现电泳及UF液水系统的封闭循环,但最后一级纯水洗有新鲜纯水喷淋补加,纯水槽会产生溢流排放,造成电泳系统有大量废水排放,若直接排放不仅污染环境,且造成涂料流失。电泳系统采用EDRO技术,是以超滤液作为处理原液,进行电泳反渗透(EDRO)处理,产生的“水”代替新鲜纯水作为工件喷淋用,喷淋液逆序返回至电泳槽,产生的浓缩液返回到UF2槽,电泳漆利用率达99%以上,实现高效节约的闭路循环利用和废水零排放,如图3所示。 图2 电泳后冲洗UF过滤回收技术方案 图3 电泳后冲洗EDRO反渗透技术方案 2.2. 喷漆室绿色技术 喷漆室是涂装车间最大的耗能设备,其能量消耗占涂装线耗能的50%以上。近几年,循环风、干式喷漆室、机器人自动喷涂等绿色低碳技术逐步推广应用。 (1) 循环风技术 传统水性漆喷漆室往往采用全新风的空调送风方式,喷漆室全新风一般风量较大、且需要调温、调湿,以致于空调耗能较大。为了降低喷漆室能耗,可将采用漆雾捕集装置的擦净室、气封室和人工补漆室的排风作为循环风,用于机器人喷漆室循环一次后进行排放;或者机器人喷漆室采用自循环风,自循环过程中需要抽取一定量风进行排风进入废气处理装置,并往机器人喷漆室补充一定量新风,在机器人喷漆室安装有机溶剂浓度检测报警装置,实现喷漆室新风量动态精确控制和确保自循环风中的有机溶剂浓度始终低于其爆炸下限的25%。 (2) 干式喷漆室 前些年,国内涂装线大都采用水帘、文丘里、水旋等湿式喷漆室,仅有少数汽车线使用干式喷漆室,采用石灰粉、静电等干式处理漆雾技术,石灰粉吸附漆雾后虽然理论上可以作为建材使用,但现实中处理困难;静电吸附漆雾技术尚未国产化。近几年,随着纸盒干式漆雾捕集装置技术的快速发展,在投资运行成本及能耗等方面占明显优势,使纸盒式干式喷漆室正在涂装线上逐步推广应用,纸盒干式喷漆室与传统湿式喷漆室相比,具有不用消耗水、也无废水产生,因此也不需要水循环系统及除渣系统,降低设备投资、减少设备占地面积、操作维护简单无需专业人员维护等优点。不同形式的干式喷漆室对比如表3所示。 表3 不同形式的干式喷漆室对比分析 (3) 拖动示教喷涂机器人 在农机行业上,每条涂装线上均要满足多品种、复杂工件喷涂,就意味着编程人员需要进行大量的编程工作才能满足实际生产的需要,为了降低编程的复杂性和多样性,在底盘涂装线上采用新型的拖动示教机器人。在复杂的底盘工件喷涂时,操作人员通过操作机器人末端的拖动手柄,根据工人的操作习惯和喷涂工艺要求,完成复杂底盘表面喷涂作业,机器人自动记录人工拖动喷涂过程生成的喷涂轨迹程序,即完成程序编制。拖动示教编程方式的优点是无需掌握编程语言和仿真软件,喷漆工人通过简单培训即可完成程序编制,生产过程中2~3人配合,5 min可实现新产品的程序编制,该编程方式比较适用于多品种、生产线切换比较频繁的工件喷涂。 2.3. 前处理绿色技术 (1) RTO尾气余热利用 涂装喷漆室、烘干炉的尾气处理装置RTO需常年运行,一直有高温烟气排出,这不仅造成环境局部变暖,而且浪费了大量宝贵能源,造成企业运行成本居高不下。在RTO烟气排放口安装“气-水”余热回收系统,使净化后的尾气经余热回收装置与前处理工艺回水交换热量,进水温度由75 ℃加热到90 ℃,尾气排放温度由约200 ℃降至120 ℃,工艺回水被加热后回到燃气热水机组,从而减少热水机组天然气耗量,达到节能降碳的目的。 (2) 热泵技术 随着双碳政策的出台以及高效热泵技术的发展,越来越多的涂装线前处理与烘干炉上应用高效热泵。针对前处理的预脱脂槽液、脱脂槽液及低温水性漆烘干炉的温度较低,可以采用热泵加热式代替燃气或电加热方式,热泵吸收空气中的低品位热量产生较高品位的热量可以用来烘干工件、加热脱脂槽液,在夏季时,热泵排出的低温风送至上下件、遮蔽等人工操作岗位,改善员工工作环境,这种冷热联供形式提高了热泵的综合能效,与传统的电、燃气加热相比降低40%~60%的能耗。若在谷电、平电阶段使用热泵,其运行成本与传统的电、燃气加热相比有明显降低;若在峰电阶段使用热泵,其运行成本与传统的电、燃气加热相比降低不明显。 涂装线首先是能耗大户,再者生产中需要电、天然气、蒸汽、压空、水等能源、资源种类较多,人工抄表工作量大、难免遗漏,不利于生产过程的能源管理。新的能源管理方式应完善能源三级计量智能仪器仪表,通过搭建能源管理数字化平台系统,可实时统计与分析日耗量、月耗量、年度耗量及单车能耗,并及时给出能耗超标预警提示;便于实现能耗指标的统计、追溯、分析;使能源成本细化。 通过对能源数据进行长期跟踪,及时发现涂装线节能潜在机会。 涂装线喷漆室控温控湿、烘干炉加热、机运系统等电耗量较大,越来越多的企业自建分布式光伏发电系统,所产生的绿电可以“自己自足”,也可以通过与电网并网,以“多交少补”的形式灵活用电,降低了煤电用电量,进而逐步达到节能降碳、零碳涂装线的目的。 绿色涂装技术在农机涂装线中正逐步推广应用,通过源头减碳、清洁生产、过程减碳、绿色技术应用以及能源管理和能源结构优化等措施,农机生产企业可以显著降低生产过程中的能耗和碳排放,提高产品质量和生产效率。
免责声明:本网站所转载的文字、图片与视频资料版权归原创作者所有,如果涉及侵权,请第一时间联系本网删除。
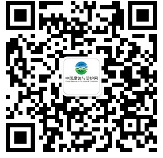
官方微信
《腐蚀与防护网电子期刊》征订启事
- 投稿联系:编辑部
- 电话:010-62316606
- 邮箱:fsfhzy666@163.com
- 腐蚀与防护网官方QQ群:140808414