文章详情 Article details 面向氢能本质安全利用——氢致损伤研究进展与挑战 孙彬涵,张显程,涂善东 承压系统与安全教育部重点实验室,华东理工大学机械与动力工程学院,上海 200237 引用本文 孙彬涵, 张显程, 涂善东. 面向氢能本质安全利用——氢致损伤研究进展与挑战[J]. 化工进展, 2025, 44(5): 2898-2906. DOI:10.16085/j.issn.1000-6613.2025-0211
摘要 summary 氢致损伤或氢脆(hydrogen-induced damage or hydrogen embrittlement)是氢能装备安全服役过程中面临的主要挑战之一。本文综述了氢致损伤的特性与机理、测试与评价技术以及抗氢损伤材料本质安全设计的最新研究进展与挑战。近年来在氢致损伤机理和测试技术方面取得了显著进展,但其高度复杂性的本质仍使可靠性评价和工程实践面临诸多难题。未来,需进一步完善氢致损伤理论体系,按实际应用场景评价临氢部件在全寿命周期的氢致损伤敏感性,并结合抗氢损伤设计的工程实践,为氢能产业的安全健康发展提供技术支撑。
氢能作为一种清洁、高效的能源,具有能量密度高、来源丰富、零碳排放等优势,被视为未来可持续能源体系的重要组成部分。近年来,全球多个国家和地区相继出台了氢能发展规划,以推动氢能技术的规模化应用。预计到2030年,全球氢能市场投资额度将达到6800亿美元,相关产业链将迅速扩展。然而,氢气的使用涉及高压、低温及高温等复杂工况,尤其是在储存、运输和使用过程中,对材料和装备的安全性提出了极高的要求。大量的研究表明,金属材料在氢环境下会发生氢致损伤,显著降低材料的塑性、断裂韧性以及抗疲劳性能。这种现象增加了氢能装备在服役过程中的安全隐患,制约了氢能技术的推广和工程应用,因此对氢致损伤的研究至关重要。本文综述了氢致损伤的特性与机理、测试与评价技术以及抗氢损伤材料本质安全设计的最新研究进展与挑战。
01 材料氢致损伤研究进展与挑战 1.1 氢致损伤特性与机理
氢致损伤的本质在于氢分子在材料表面解离,以原子的形式扩散进材料内部,在载荷/温度的驱动下与材料内部的微观缺陷发生交互作用,改变材料的局部力学特性,进而诱发局部的损伤萌生和加速扩展。相比于其他环境损伤模式(如氧化、腐蚀等),氢致损伤具有以下特殊性:①氢原子高扩散性,氢原子极小,能快速扩散进入金属材料内部,且能够在较低的温度下在材料内部移动和聚集;②机制复杂性,氢可通过多种机制(如氢增强局部塑性、氢诱导界面脱黏等)影响材料力学性能;③载荷的核心作用,在很多情况下,氢原子进入到材料中,往往需要载荷的驱动才会诱发氢致损伤断裂。自英国学者Johnson在1875年发现和提出氢致损伤概念以来,其发生机制一直是研究的热点,迄今为止,已有如下几个主流的理论,如图1。
图1 氢致损伤主流理论及其发展 (1)氢压理论(high-pressure molecular H-induced failure or internal pressure theory):这一理论主要适用于氢浓度很高的情况,例如对于车轮钢,当制造时钢液中氢浓度高于2×10-6(质量分数)时,冷却时氢将以分子形式析出,产生高压,从而金属表面会出现氢鼓泡白点。该理论认为,大量的氢原子在材料内部的缺陷(如微孔、夹杂物等)处聚集,并以分子形式(H2)析出,形成高压气泡,诱发微裂纹的萌生和扩展。 (2)高温氢腐蚀理论(high-temperature H attack,HTHA):高温氢腐蚀的研究主要集中在钢铁材料,广泛出现在炼油、化工及高温氢气环境中的材料应用中。该理论认为钢在高温高压氢环境中服役一定时间后,氢与钢中的碳原子或碳化物反应形成甲烷气,高压甲烷气泡在晶界或其他高能界面处形核长大,互相连接形成裂纹。同时,该反应使得材料脱碳,从而降低金属的强度和硬度。 (3)氢化物致裂理论(hydride-induced failure, HIF):该理论适用于易形成氢化物的材料(如Ti、Zr、V等),其核心观点是,在应力的促进下,氢原子与材料发生反应,形成氢化物。这些氢化物通常具有较低的韧性,导致材料局部脆化,进而在应力作用下诱发裂纹的萌生与扩展。 (4)氢促进脱黏理论(H-enhanced decohesion,HEDE):该理论提出,固溶的氢原子能够降低金属材料内部的原子结合力,尤其是在晶界、相界等核心区域,导致界面强度下降,最终在应力作用下诱发界面解离和裂纹萌生。该理论是常温和低温氢致损伤领域中最广泛讨论的机制之一,对比前面三种理论,具备更广泛的适用性。 (5)氢促进局部塑性理论(H-enhanced localized plasticity,HELP):同HEDE理论一样,该理论同样适用于较宽的温域以及较广的材料范围(钢铁、镍基合金等非氢化物形成材料)。其认为,氢的存在能够降低位错的运动障碍,使位错更容易在材料内部滑移,导致局部塑性变形能力增强,即材料发生局部“软化”。这个效应在裂纹尖端区域尤为明显,促进了裂纹尖端塑性变形高度局部化,因而导致这些局部区域快速断裂,促进裂纹加速扩展。 (6)氢吸附诱导位错发射理论(H-adsorption induced dislocation emission,AIDE):同HELP理论类似,该理论同样强调了位错在氢致损伤过程中的核心作用。该理论认为,当氢原子吸附到材料表面或裂纹尖端时,会促使位错从表面或裂纹尖端发射出来。这种位错发射会改变材料的变形机制,并降低材料的断裂韧性,使其更易发生断裂。 (7)氢增强应变诱导空位理论(H-enhanced strain-induced vacancy,HESIV):该理论认为,在氢环境下,材料的塑性变形过程中会产生大量的空位,而氢原子的存在能够稳定这些空位并抑制其湮灭。这些空位可能在材料内部聚集,形成微孔洞,从而导致微裂纹的萌生和扩展,最终诱发断裂。 目前,对于多数材料的氢致损伤机理仍存在较大争议,尤其是在HEDE、HELP、AIDE和HESIV等机制的适用性上。这些机制往往能够解释多种氢致损伤现象,但由于缺乏直接明确的决定性实验证据,其具体作用边界尚未完全厘清。这四类机制主要关注固溶氢原子与材料缺陷之间的物理交互作用,而这类作用难以直观表征,对于氢致损伤的本质理解仍然任重道远。近年来,越来越多的研究表明,氢致损伤可能涉及多种机制的协同作用。例如,在某些材料的塑性变形过程中,HELP机制可能促使位错大量移动并在界面处塞积,从而加速氢致界面脱黏(HEDE)的发生。同时,HELP机制增强的位错活动可能会加剧应变诱导空位的形成,从而进一步激活氢致应变诱导空位(HESIV)机制,促进材料局部塑性变形和损伤演化。而在裂纹扩展过程中,HELP机制会导致裂纹尖端材料局部软化,通常会促进孔洞的扩展和融合,随着氢在孔洞中析出,使其表面吸附氢的浓度达到临界水平,从而进一步通过AIDE机制诱导开裂。而在AIDE机制主导的裂纹扩展过程中,HELP作用可能增强裂纹尖端位错的运动能力,使位错更容易远离裂纹尖端,从而降低后续位错发射所受的背应力。同时,AIDE和HEDE也可能依次发生,即裂纹扩展初期,AIDE机制占主导,直到已发射位错产生的背应力增加到一定程度,使HEDE机制开始主导裂纹扩展,随后裂纹尖端远离先前发射的位错应力场时,AIDE机制再次发挥作用。此外,研究结果还表明,氢致损伤或许并不存在单一普适的理论,其主导机制可能因材料类型、载荷模式、氢浓度等边界条件的不同而发生变化。例如,Dong等在研究双相钢时发现,随着氢浓度的增加,铁素体晶粒内部的穿晶裂纹主导机制可能从HELP向HEDE转变。因此,如何利用更先进的实验技术和计算模拟方法,精准判定不同损伤机制的作用边界,或将成为氢致损伤研究的核心问题之一。 除了上述挑战,温度对氢致损伤机理的影响也是一个亟待深入研究的方向。目前,除了高温氢腐蚀理论外,大多数氢致损伤研究仍集中在近常温条件下,对超低温及超高温条件下的氢致损伤机制认识尚不充分。尤其是在极端温度条件下,氢原子与材料内部微观缺陷(如空位、位错、碳化物等)的相互作用,以及氢致损伤与高温/低温环境损伤的耦合作用,仍是尚未解决的科学难题。氢致损伤动力学模型的缺少,导致无法合理评价特定应用场景下结构的寿命。因此,深入研究这些问题不仅有助于完善氢致损伤理论体系,也将为拓展氢的应用范围提供重要的理论支撑。 1.2 测试与评价技术
测试与评价技术是科学发展的重要基础,也是理论模型缺失时,实现工程应用的科学途径。材料的氢致损伤涉及温度、载荷和环境的复杂交互作用,其科学评估相比普通环境下的材料损伤更加困难,而关键瓶颈在于如何准确模拟临氢环境。当前,临氢环境的实现主要依赖两种方法:电化学充氢和高压氢气环境。电化学充氢通过施加外加电势,使电解液中的水或酸溶液分解产生氢原子,这些氢原子在材料表面吸附后扩散至内部,从而实现持续充氢;而高压氢气方法则通过在高压环境下使氢气分子在材料表面解离形成氢原子,并逐步扩散进入材料内部。在高压氢储运和氢能利用领域,高压氢气环境更接近实际服役条件,因此具有更高的工程应用价值。在材料的宏观力学性能测试中,为了简化实验流程,降低实验难度,研究人员通常采用预充氢后在大气环境中进行测试的方法评价材料的氢致损伤敏感性。然而,一方面由于真实服役条件下材料中的含氢量和分布具有不确定性;另一方面,由于氢原子体积极小且扩散速率极高,充氢后的材料在空气中很容易发生氢逸散,导致测试结果无法真实反映材料在实际服役条件下的力学行为。因此,为了提高实验的可靠性,通常需要在氢环境下开展原位力学性能实验。然而,氢气的易燃易爆性、高扩散性及易逸散性,使得这类实验的实施面临很大的挑战,尤其是在高温高压条件下,实验设备的安全性和可靠性成为关键技术难点,测试的代价相当高昂。在高压氢环境下材料力学性能测试方面,美国Sandia国家实验室、日本九州大学和中国浙江大学等研究机构开展了大量研究工作。针对CrMo钢、管线钢和不锈钢等典型氢储运材料建立了力学性能数据库,相关的临氢环境材料力学测试标准也已相继颁布,如图2。然而,液氢环境下材料力学性能测试数据还鲜见报道。近年来,Feng等对低温力学测试平台进行了优化改进,将最低测试温度扩展至液氢温度范围(20K),并利用该平台对S30408奥氏体不锈钢在20K和77K下进行了拉伸实验,以评估其低温力学性能。同时,对于氢能动力装备、氢冶金等其他氢能领域工程材料,当前仍缺乏系统的氢致损伤敏感性评估规程,未来仍需进一步加强研究,以完善氢相关材料的评价体系以及数据库,为临氢部件科学选材提供依据。
在微观层面,氢原子的表征是氢致损伤研究中最具挑战性但也最为关键的一步。由于氢原子体积小、质量轻、易逃逸,许多传统的元素表征技术难以有效捕捉氢原子分布。常用的氢探测技术包括热脱附光谱(TDS)、氢微印技术(HMT)、二次离子质谱(SIMS)、扫描开尔文探针力显微镜(SKPFM)以及原子探针等(APT),如图3(a)。其中,APT和SKPFM具有最高的空间分辨率,能够揭示氢在微观结构特征(如纳米级析出物、位错和界面)中的捕获行为。然而,对于局部氢浓度的精准定量仍面临巨大挑战,同时仍缺乏有效手段直观表征氢原子在材料内部的动态扩散与偏聚行为,这在根本上限制了对氢致损伤物理机制的深入理解。此外,氢与微观缺陷(如空位、位错和界面)的交互作用同样是理解氢致损伤的关键。早期的研究通过原位透射电子显微镜实验直接观察了氢对位错滑移的影响,发现氢促进了位错滑移,减少了位错堆积距离,并增强了位错平面滑移的趋势。近年来发展的原位纳米压痕和环境透射电子显微镜(ETEM)等先进技术可实现更定量的氢-位错相互作用的研究,如图3(b)。例如,Xie等通过在ETEM中设置氢环境循环加载模块,实时观察了氢环境循环加载过程中的位错运动,并定量了氢对位错滑移临界应力的影响作用。然而,氢致损伤涉及跨尺度问题,从原子级别的氢扩散到纳米尺度的位错运动,再到微观乃至宏观尺度的裂纹萌生与扩展,均需系统厘清其演变规律。以上的微观表征手段在高分辨率与统计性之间仍存在较大技术空白,这也成为研究氢致损伤机理的关键瓶颈之一。
尽管近年来材料氢致损伤测试技术取得了显著进展,但在科学评价真实服役条件下临氢部件可靠性及服役寿命方面仍面临很大挑战。首先,实际服役环境往往比实验室条件复杂得多,涉及温度、压力、应力状态等多种因素的耦合作用。部件的表面状态以及渗氢速率也与实验室不同。现有的评价标准(如ASTM G129等)一般是通过对比材料在氢气和空气(或氩气)下的力学性能,评估材料的氢致损伤敏感性。这类方法仅适用于不同材料的横向对比,无法用来评估其在真实服役工况下的可靠性及寿命。同时,临氢部件在服役过程中,还会涉及多种环境和腐蚀介质的影响,其他环境对氢致损伤的作用也是一个必须要研究的问题。因此,如何针对各类临氢服役场景,建立能够准确模拟实际服役条件的实验方法,是一个亟待解决的问题。其次,如何将实验室尺度的测试结果外推到实际工程部件的性能评估,也是一个复杂的问题。这需要考虑尺寸效应、多轴复杂载荷、应力集中、焊接冶金等实际工程因素的影响。多尺度化学-力学建模和仿真技术的应用为解决这一问题提供了新的思路,如图4,然而由于氢致损伤物理机制和动力学规律的复杂性,这方面仍需进一步发展和验证。此外,在很多情况下,氢致损伤是一个长期累积的过程,如何在较短时间内评估材料的长期服役性能,是另一个重要挑战,需要考虑氢致损伤与疲劳等其他损伤模式的交互作用,这方面的研究还存在较大的不足。特别在高温部件(如氢燃机和航机高温合金部件)长时服役过程中,氢损伤和蠕变损伤耦合作用下的寿命预测方面仍需进一步系统研究。最后,如何在以上研究的基础上,针对不同涉氢行业,建立科学合理的评价标准和规范,以指导临氢部件的长寿命设计和安全评估,是推动氢能产业发展的关键。这需要材料科学家、力学家、工程师和标准制定机构等多方的协同努力。
图4 氢-疲劳寿命预测模型的演绎历史 1.3 抗氢损伤材料的本质安全设计
针对不同材料和临氢部件进行抗氢损伤本质安全设计,使其更好地满足服役需求,是研究氢致损伤的重要目的。氢致损伤的发生通常需要经历如下几个阶段:①氢从环境中进入结构部件;②氢在材料内部扩散并在局部区域偏聚;③氢与缺陷相互作用,导致裂纹萌生和扩展。抑制或延缓上述任一过程都有助于提高材料的抗氢损伤能力。基于此,学者们近年来已提出了多种抗氢损伤的策略,如图5,典型的策略包括以下几点。
图5 典型抗氢损伤方法 (1)覆盖阻氢涂层。该方法旨在通过覆盖低氢渗透性或低氢扩散率的涂层来阻止氢从含氢环境中进入材料或部件。目前开发的阻氢涂层主要包括陶瓷涂层(氧化物、碳化物和氮化物)、金属涂层、二维材料涂层和复合涂层。这些涂层可使氢的扩散速率降低至基体的1/104。然而,涂层的耐久性是一个重要问题,特别在恶劣环境(如磨损或腐蚀环境)中长时服役过程后。一旦涂层受损,暴露的金属基体与涂层材料之间的电化学反应可能导致氢的生成和重新渗入,从而诱发氢致损伤。 (2)引入氢陷阱。该方法利用某些第二相(如钢中的V、Ti和Nb基碳化物)捕获氢,降低氢原子在材料内部的扩散速率,从而延缓氢原子在局部区域的聚集。然而,如果这些析出相及相关界面本身容易发生氢致开裂,则可能产生负面影响。此外,氢捕获相可能导致材料吸收更多的氢,在高温环境下,这些捕获的氢可能重新扩散,从而增加氢致损伤风险。特别需要注意的是,该方法一般适用于氢含量较少的情况,对于在临氢环境下服役的部件,氢陷阱最终均会充满,因此失去了防护效果。 (3)微观界面调控。研究表明,细化晶粒可降低晶界处的氢覆盖率,同时可减小应力在晶界上的集中,降低氢致晶界开裂的倾向。然而,当晶粒尺寸减小到微米级以下时,材料的应变硬化能力和均匀延伸率一般会显著降低。另外一种微观界面的调控方式是通过增加低能界面(如退火孪晶界)的比例,降低晶界处的氢聚集,并阻断沿晶断裂扩展路径。可以看出,以上方法仅适用于氢致沿晶断裂为主的情况。 (4)化学成分调控。在合金中,一些成分的含量往往对材料的氢致敏感性有重要作用。如Ni元素可显著地增加奥氏体不锈钢的机械稳定性,降低因形变诱发马氏体而导致氢致损伤的概率。又如,B和C等合金元素可提高晶界的结合强度,抑制氢致沿晶开裂。某些情况下,合金内部的化学成分异质性也可有效提升其抗氢损伤能力。例如,Sun等提出了一种通过微纳尺度Mn元素偏聚的方法,局部稳定奥氏体组织,显著抑制了氢致裂纹的扩展,在保障材料优异强塑性的同时,提升了其抗氢损伤能力。 近年来,机器学习在材料抗氢设计领域开始获得了一定的关注。传统的抗氢材料设计通常依赖于实验测试和物理模型,而机器学习方法能够基于大规模数据进行高效预测和优化,在特定服役场景下对材料的性能进行预测与筛选,并为材料开发提供新的思路。例如,Gong等通过广泛搜集高强度钢的氢脆性能数据,并通过迭代贝叶斯多目标优化方法设计了抗氢脆高强度钢,极大地提高了材料的抗氢性能。 总体而言,不同抗氢损伤方法的适用性、优缺点各异。未来,随着氢能经济的快速发展,对临氢装备高可靠性的需求将不断推动抗氢损伤材料本质安全设计方法的进步。在不能完全消除氢致损伤的现实下,更合理的目标是通过先进的损伤容限设计方法,使得材料和部件在全寿命周期内实现安全服役。在设计的过程中,必须充分考虑材料的服役条件(如载荷和环境因素)、相关工艺在工程化应用方面的可行性和经济性,这样才能做到设计优化与工程实践的有机结合,确保临氢装备在高效、安全、经济的前提下实现长周期稳定运行。
02 结语 (1)氢致损伤虽然是一个较为古老的科学问题,但其机理复杂且尚未完全厘清。目前提出的理论虽然能够解释部分氢致损伤现象,但其适用边界和协同作用机制仍需进一步研究。特别是在极端温度条件下,氢原子与材料微观缺陷的相互作用及其与环境损伤的耦合效应,仍是亟待解决的科学难题。目前仍然缺乏氢致损伤下工程寿命的科学评估方法,未来,需借助先进的实验技术和计算模拟方法,精准判定不同损伤机制的作用边界。深入研究氢原子在不同环境(低温液氢、高温燃烧、辐照、腐蚀环境等)与材料微观缺陷(如位错、空位、晶界等)的相互作用机制,明确其对材料力学性能的影响。完善氢致损伤理论体系,并开发精准的氢致损伤预测方法,为工程寿命评估提供可靠的理论依据。 (2)尽管氢致损伤测试技术取得了显著进展,但在科学评价真实服役条件下临氢部件的可靠性及服役寿命方面仍面临很大挑战。现有的测试方法多基于理想实验室条件,难以准确模拟实际服役环境中的复杂环境和载荷工况。未来,需建立更接近实际服役条件(如高压、动态载荷、温度变化等)的实验方法,发展多尺度化学-力学建模方法,开发基于数据驱动和物理建模相结合的多尺度损伤演化模型,实现氢致损伤的精准预测,并为迫在眉睫的实际工程应用提供验证。 (3)抗氢损伤的材料本质安全设计是保障临氢装备长周期稳定运行的关键。目前,阻氢涂层和材料微观组织调控等策略在提升材料抗氢损伤能力方面取得了一定进展,但其适用性和工程化实践仍面临诸多挑战。未来,抗氢损伤设计需充分考虑材料的服役条件、工艺可行性和经济性,推动设计优化与工程实践的有机结合。同时,需建立科学合理的评价标准和规范,为临氢部件的长寿命设计和安全评估提供指导。 综上,氢致损伤研究从科学理论到工程实践仍有许多挑战,目前亟需在机理研究、测试技术、抗氢损伤设计等方面取得突破,为氢能产业的安全、高效、可持续发展提供坚实的技术支撑。但可以预期,在大量科学研究和工程实践的基础上,一个更加安全的氢能社会是完全可以实现的。
致谢:曹湘洪院士积极倡导和支持我国氢能利用技术的研发,本文作者多次请教曹院士,得到他的悉心指导,特致以崇高敬意与衷心谢忱! 特别感谢参与首届临氢环境材料服役行为青年研讨会(上海,2024)的同行,为本文观点的形成提供了有益的帮助。 感谢赵昱博、周晶晶、纪宇、张傲晨、孔帅、田冉、董紫轩在评价标准和模拟方法调研方面的帮助。 第一作者:孙彬涵,教授,研究方向为氢能装备安全与金属材料。 通信作者:涂善东,教授,中国工程院院士,研究方向为化工装备安全、高温强度学、先进能源材料与装备。
免责声明:本网站所转载的文字、图片与视频资料版权归原创作者所有,如果涉及侵权,请第一时间联系本网删除。
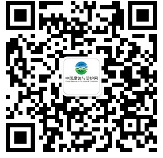
官方微信
《腐蚀与防护网电子期刊》征订启事
- 投稿联系:编辑部
- 电话:010-62316606
- 邮箱:fsfhzy666@163.com
- 腐蚀与防护网官方QQ群:140808414