
在石油化工、航空航天领域,奥氏体不锈钢由于具有优良的力学性能和抗腐蚀性能得到广泛应用。奥氏体不锈钢表面绝大部分处于钝性状态,腐蚀速率可以忽略不计,但在表面很小的区域,腐蚀速率相差几十万倍。奥氏体不锈钢在一定条件下会发生腐蚀,尤其以局部腐蚀最为常见。局部腐蚀主要有电偶腐蚀、点蚀、缝隙腐蚀、应力腐蚀、晶间腐蚀、氢脆等,并且它们存在协同作用。局部腐蚀广泛发生且危害性较大,腐蚀破坏通常没有明显预兆,不仅影响正常使用还可能引发安全事故[1]。
晶间腐蚀是金属材料在特定的腐蚀介质中沿着材料的晶界产生的腐蚀,由微电池作用引起。这种腐蚀从表面开始,沿着晶界向内部发展,直至成为溃疡性腐蚀[2-5]。
点蚀指金属表面个别区域或微小区域出现腐蚀孔或者麻点,随着时间推移,腐蚀孔不断向纵深方向发展,形成腐蚀坑[6-7]。
某不锈钢氮气管路系统,在服役18个月后发生了管路弯头穿孔泄漏现象,弯头材料0Cr18Ni9(新牌号06Cr19Ni10),型号为DN50。为了保证管路系统安全可靠运行,笔者从失效弯头的宏观形貌、理化检测以及微观扫描电镜等方面进行了分析,找到弯头失效的原因,提出相应的改进措施,以期避免类似事故的再次发生[8-9]。
1. 概述
某氮气供气系统设计压力为9 MPa,管路为DN50,管路材料为0Cr18Ni9奥氏体不锈钢(符合GB/T 14976-2002《流体输送用不锈钢无缝钢管》标准)。不锈钢弯头采用GB/T 12459-2005《钢制对焊无缝管件》标准中的1.5倍弯曲变径(长半径)弯头,牌号0Cr18Ni9,供货状态为固溶热处理。
弯头与不锈钢管采用手工氩弧焊接连接,焊缝进行了射线检测(I级合格)。弯头焊缝外表面进行了酸洗钝化处理。系统安装完成后,对整条管路进行了9 MPa气密性检查,未发现任何异常现象。
管道系统使用18个月后进行检修维护,出现持续压力降低现象,在某管路弯头处听到漏气声音,初步判断弯头出现了泄漏小孔。采用渗透无损检测方法对问题管路弯头进行着色检测,在弯头焊缝热影响区存在缺陷显影以及小孔缺陷,图1(a)标示位置为小孔泄漏区域。对整根管线弯头部分进行了表面渗透检测,有的弯头热影响区仅存在孔蚀现象,并未腐蚀穿透,见图1(b);有的弯头表面完好,未发生腐蚀,见图1(c)。
2. 理化检验与结果
2.1 宏观形貌
将管路系统进行放气处理后,采用机械工具将弯头从钢管上切割下来,便于进一步进行弯头泄漏原因分析,弯头外表面形貌见图2。
对失效弯头的外表面进行宏观观察,可以看出,弯头外表面焊缝附近的腐蚀情况比较严重,腐蚀部位均发生在焊缝两侧距离焊缝大约10 mm的位置,腐蚀严重区域的宽度约10 mm,该区域为弯头焊缝热影响区,颜色明显较深。弯头其他区域与焊缝区域表面光亮,未见锈蚀现象。泄漏区域外表面焊缝热影响区存在多处腐蚀斑点。
将弯头剖开,观察内表面。弯头内表面余高较大,并且凹凸不平,因未经过酸洗钝化而呈现灰黑色,热影响区发生了高温氧化,因温度不同呈现亮黄色或亮蓝色。焊缝内表面部分区域存在明显的黄褐色锈蚀形貌,主要分布在焊缝及其两侧熔合线位置,熔合线缝隙处锈蚀较为严重。泄漏点对应内表面也存在腐蚀区域,见图3。
2.2 化学成分
弯头采用不锈钢管推制加工制作而成,若元素成分不达标,可能会在使用过程中引起失效问题。首先对弯头母材的化学成分进行分析,见表1。可以看出母材成分满足GB/T 14976-2002《流体输送用不锈钢无缝钢管》的规定。
元素质量分数 | GB/T 14976-2002标准 | 弯头母材实测值 |
---|---|---|
w(C) | ≤0.07 | 0.05 |
w(Cr) | 17.00~19.00 | 18.23 |
w(Ni) | 8.00~11.00 | 9.20 |
w(P) | ≤0.035 | 0.028 |
w(S) | ≤0.030 | 0.023 |
w(Mn) | ≤2.00 | 0.76 |
w(Si) | ≤1.00 | 0.64 |
选取未见腐蚀的弯头母材,沿厚度方向制备样品,由图4可见:母材组织正常,为固溶态奥氏体组织,未见腐蚀孔隙、晶间腐蚀、沟状组织等缺陷。
母材试样的能谱分析结果表明其主要元素成分(质量分数)为:Fe69.19%、Cr19.5%、Ni9.04%、Mn1.43%、Si0.84%,其主合金元素及含量与0Cr18Ni9不锈钢基本相符。
2.3 微观形貌
采用扫描电镜观察弯头泄漏区域外表面形貌,由图5可见,泄漏区域外表面形态存在“泥纹”状腐蚀形貌,腐蚀产物脱落区域的基体可见多个腐蚀孔洞和沿晶微裂纹。能谱分析结果表明腐蚀产物主要含有O、Fe和少量的Cl、S元素,为基体腐蚀产物。
采用扫描电镜观察弯头泄漏区域内表面形貌,由图6可见,漏区域内表面存在腐蚀现象,腐蚀产物脱落区域的基体可见腐蚀孔洞和沿晶微裂纹,还可见分叉、断续沿晶微裂纹。能谱分析结果表明腐蚀产物主要含有O、Fe、Cr和少量的S、Cl元素,为基体的腐蚀产物。
2.4 显微组织
在弯头泄漏区域附近沿横截面制备金相试样进行观察,采样位置见图7,分别是母材(位置1),热影响区外表面(位置2),热影响区内部(位置3),泄漏通道(位置4),焊缝熔合线(位置5)和焊缝内表面(位置6)。由图8可见:母材组织为孪晶奥氏体组织,晶界未见异常。热影响区外表面存在明显的沿晶腐蚀及沿晶微裂纹,腐蚀深度约0.2 mm,表明外表面热影响区的腐蚀为晶间腐蚀。热影响区域组织与母材组织及熔合线区域的组织存在明显差异,热影响区奥氏体晶界上存在网状分布的颗粒状碳化物,表明该区域组织在焊接后存在敏化现象。泄漏区域存在一定深度的沿晶腐蚀现象,沿晶腐蚀呈断续状,逐层磨抛后观察到最长一处沿晶腐蚀深度约1.5 mm,表明泄漏区域的腐蚀均为晶间腐蚀,并存在明显的泄漏通道。焊缝熔合线区域组织正常,未见明显的气孔、焊接热裂纹、夹杂等焊缺陷。内表面焊缝及熔合线的剖面上观察不到明显的腐蚀现象(黑色氧化物),表明内表面腐蚀深度较浅,但是存在腐蚀凹坑。
3. 分析与讨论
3.1 结果分析
弯头母材正常,弯头部分焊缝热影响区发生了晶间腐蚀,在盐雾环境中,S2-、Cl-引起局部腐蚀(点蚀),导致介质穿孔泄漏。
弯头焊接过程中焊接参数控制不当,焊缝热影响区发生敏化,引起晶间腐蚀。后续焊缝进行酸洗钝化处理会加剧晶间腐蚀。焊接因素以及酸洗钝化工艺对焊缝热影响区的金相组织影响将进行进一步讨论。
3.2 焊接因素影响
敏化现象指经过固溶处理的奥氏体不锈钢,在500~850 ℃时,Cr从奥氏体中以碳化物的形式析出,而C在不锈钢晶粒内部的扩散速度大于Cr的扩散速度,C不断向奥氏体晶粒边界扩散,并在晶间形成C和Cr的化合物。热影响区奥氏体晶界上存在网状分布的颗粒状碳化物,而其他位置碳化物析出较少,表明热影响区组织发生了敏化,从而造成晶间腐蚀。
敏化现象的发生与焊接时热输入量相关,而焊接时的热输入量与焊接电流和焊接速率相关。依据《焊工手册》中对氩弧焊工艺参数的推荐数值,当焊接速率为5 cm/min时,随着焊接电流的增大,焊缝热影响区的显微组织更容易发生晶间腐蚀。
3.3 酸洗钝化因素影响
弯头焊接后,为了保证焊缝外表面的美观,通常对外表面进行酸洗钝化。酸洗钝化工艺所用酸洗钝化膏的主要组分为:硝酸、氢氟酸、缓蚀剂以及钝化剂等。根据产品使用说明书,酸洗钝化方法为涂抹法,酸洗钝化后采用洁净水冲洗。
对于存在晶间腐蚀趋势的热影响区,对比经过酸洗钝化前后试样表面的扫描电镜(SEM)观察结果,酸洗钝化后的表面晶界更加明显,晶间腐蚀加剧,见图9。
4. 结论及建议
为了保证管路系统在后续使用过程中的安全运行,对氮气管路系统所有弯头进行渗透检测。根据弯头的腐蚀情况进行相应的处理,主要采取了以下措施。
(1)对于已经发生腐蚀穿孔的弯头,进行切除更换。弯头焊接过程严格控制焊接热输入量,降低焊接电流,控制焊接速率,缩小焊缝热影响区的宽度,避免引起晶间腐蚀。
(2)对于焊缝附近发生轻微腐蚀的弯头,采用测厚仪测量减薄量,根据弯头的承压能力评判是否可以继续使用或者更换。对于腐蚀后弯头厚度仍可以满足强度设计要求的,对腐蚀区域进行打磨处理,去除腐蚀层。
(3)对于表面渗透检测未发现有任何腐蚀迹象的弯头,可以继续使用。
(4)对所有弯头进行防腐蚀处理,采用双组份氟碳防腐涂料。氟碳涂料以特种树脂、固化剂为主要成分,是常温固化型有色金属防腐蚀涂料,抗紫外线能力强,具有极高的化学稳定性,优异的耐温性能,可以抵抗盐雾环境下Cl-引起的点蚀。
免责声明:本网站所转载的文字、图片与视频资料版权归原创作者所有,如果涉及侵权,请第一时间联系本网删除。
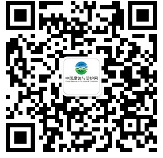
官方微信
《腐蚀与防护网电子期刊》征订启事
- 投稿联系:编辑部
- 电话:010-62316606
- 邮箱:fsfhzy666@163.com
- 腐蚀与防护网官方QQ群:140808414