氢能作为清洁、高效、零碳的能源载体,被视为21世纪最具发展潜力的清洁能源。2022年,国家发改委发布的《氢能产业发展中长期规划(2021-2035年)》明确指出,氢能将成为未来国家能源体系的重要组成部分,以及实现终端绿色低碳转型的重要载体[1]。结合中国丰富的可再生能源资源和完善的天然气基础设施,利用天然气掺氢技术,将可再生能源制取的绿氢掺入天然气管网,可有效提升我国可再生能源利用比例,推进传统能源的转型。2023年9月,国家能源局综合司发布《天然气利用政策(征求意见稿)》,提出明确和优化天然气利用顺序,并在优先类中提到了在保障安全前提下的终端天然气掺氢示范项目等天然气利用新业态[2]。然而,氢气与天然气的结合对现役天然气长输管道带来了新的安全技术挑战。通常情况下,影响天然气长输管道寿命的主要因素是湿H2S、CO2等杂质气体引起的管道内腐蚀[3],氢气的掺入可能诱发氢脆,并影响天然气长输管道的腐蚀机理和破坏类型。为了解决掺氢天然气管道的氢脆与腐蚀问题,国内外学者开展了一系列研究,提出了如无机涂层[4]、有机涂层[5]及其复合涂层等多种防护技术,为掺氢天然气管道的安全运行做出了重要贡献。
在气体阻隔防护涂层领域,包括金属及金属氧化物涂层、聚合物涂层或以上涂层的复合涂层[6,7],其中最常见的为Al2O3[8]、ZrO2[9,10]涂层及其复合涂层,这些涂层具有良好的阻氢性和防腐蚀性,但大多数应用于热核反应中,与掺氢天然气管线钢的实际工况不完全匹配,缺乏实用性。因此,本文通过文献研究,对掺氢环境下天然气管线钢的氢脆及腐蚀防护技术的相关研究成果进行归纳与总结,当前,应用于管线钢的防护涂层主要以含Ni类涂层为主的无机防护涂层和以含Mo类、氧化石墨烯类、金属锌、氧化铈物质为填料的聚合物复合涂层为主。
1 含Ni类无机涂层
由于H在Ni等金属中的扩散系数较低,Ni常被电镀在管线钢上以阻隔气体与钢材表面的接触。Ni-P涂层具备优良的阻氢和防腐蚀特性,其阻隔能力与涂层结构密切相关。非晶态Ni-P涂层的氢渗透系数(~10-14 m2/s)小于晶态Ni涂层的氢渗透系数。Samanta等[11]采用含有NiSO4、Na2H2PO2和琥珀酸作为络合剂的化学镀液,在X70钢基底上制备了非晶态Ni-P涂层,并利用Devanathan-Stachursky电化学渗透池对涂层的氢渗透性进行了详细评价。图1a显示,非晶态Ni-P涂层有效减缓了氢的渗透,相比晶态Ni涂层显示出更低的氢渗透电流,证实其作为氢阻隔层的潜力。图1b显示,动电位极化曲线揭示了非晶态Ni-P涂层相比晶态Ni涂层和基体钢在3.5%NaCl溶液中展现出更低的腐蚀电流密度,表明了其更优异的防腐蚀性能。
图1
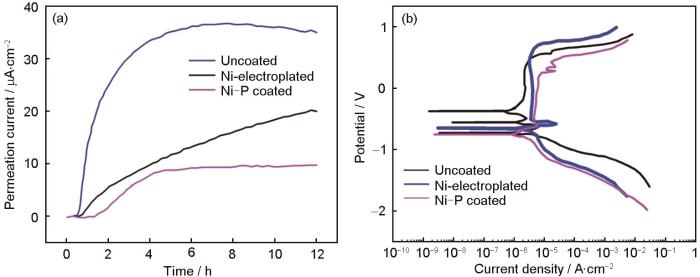
研究表明[12,13],在Ni-P-SiO2复合涂层中,SiO2的存在能够细化镀层晶粒,从而提高涂层的各项性能。Zhao等[14]通过预镀制备了具有核壳结构的SiO2@Ni纳米粒子,然后将这些纳米粒子引入到Ni-P镀层中,得到了Ni-P-SiO2@Ni复合镀层。结果表明,SiO2@Ni纳米粒子的存在可以显著减少纳米粒子在涂层中的团聚,提高纳米粒子的分散程度,更好地填充镀层孔隙,从而增强涂层性能。与Ni-P和Ni-P-SiO2纳米复合涂层相比,Ni-P-SiO2@Ni复合涂层具有更好的阻氢和防腐蚀性能。其中,未镀层基底具有较大的稳态氢渗透电流,而电镀有Ni-P基涂层的基底则显示出较低的氢渗透电流,特别是Ni-P-SiO2@Ni涂层,当SiO2@Ni纳米粒子的含量为3.6 g/L时,Ni-P-SiO2@Ni涂层展现出最佳的氢气阻隔性能,其有效氢扩散系数(Deff)达到最小值,SiO2@Ni纳米粒子的引入可以显著提高涂层的抗氢渗透能力。随着Ni-P比例的变化,Ni-P由次共晶向近共晶转化。图2显示了涂层在96 h盐雾测试后的腐蚀形貌,Ni-P-SiO2@Ni涂层仅有轻微腐蚀,主要发生在晶界处,而Ni-P-SiO2涂层则遭受了更严重的腐蚀,不仅晶界受损,晶粒本身也受到了严重腐蚀,表明Ni-P-SiO2@Ni涂层在实际应用环境中具有优异的防腐蚀性能。
图2
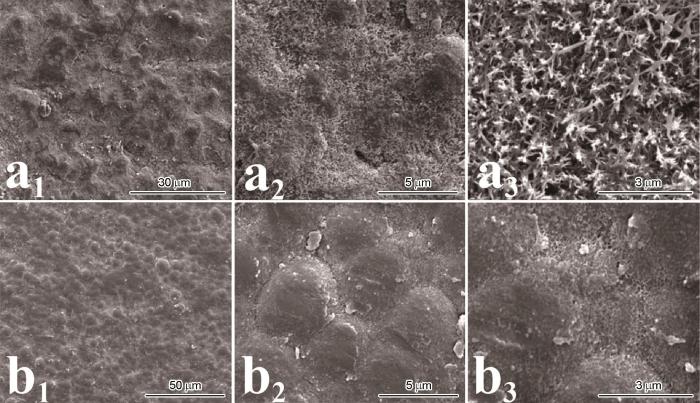
图3
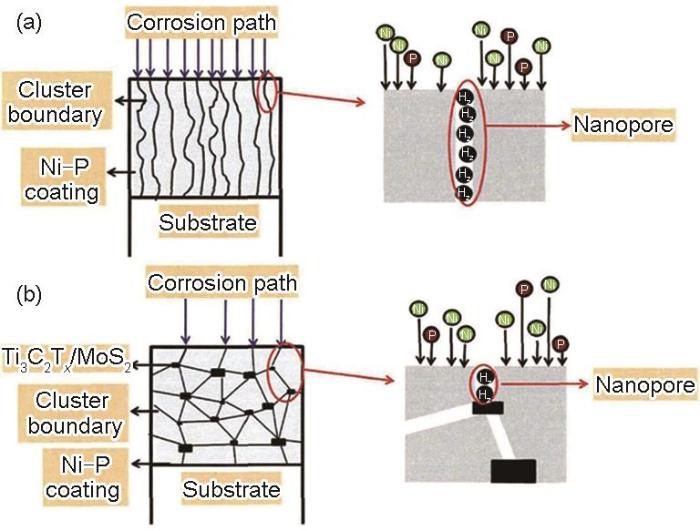
综上所述,含Ni类无机涂层的研究已经取得显著成果。与单层涂层相比,纳米复合涂层具有更好的阻氢和防腐蚀性能,且其性能与纳米容器在涂层中的均匀程度和分散性有关,并且与纳米容器和涂层的热膨胀系数的一致性有很大关系。然而,由于无机物涂层的制备工艺复杂且容易脱落,相关涂层在掺氢天然气管道中的实用性较低。相比之下,有机涂层种类更多且适用性强,但其自由体积过大,很难阻隔小分子的进入[17]。将纳米填料掺入有机涂层中可以降低涂层自由体积,是一种可靠策略。常见的纳米填料包括含Mo类、氧化石墨烯类、石墨烯类、Zn等,这些纳米填料具有出色的阻隔性[4,18,19]。聚合物基体与纳米填料的适当组合对于提升涂层的性能具有重要影响。
2 含Mo类有机复合涂层
在管线钢阻氢和防腐蚀研究过程中,有研究表明Mo类物质能够改善涂层的阻氢和防腐蚀性能。Mo的掺入会提高C在奥氏体中的扩散激活能降低弥散系数,抑制先共析铁素体的形成,Mo的掺入还会生成硫化钼,降低H2S的活性,促进氧化膜的形成,从而提升管线钢的性能[20]。Wallaert等[21]深入探究了在富含H2S的环境中,钢材基体中Mo含量的变动对腐蚀产物的构成及其对氢吸收作用的影响,低Mo材料在670和700 ℃下回火1 h得到低Mo(A)和低Mo(B),高Mo材料在700 ℃情况下回火1 h得到高Mo材料。特别关注3种材料在H2S饱和溶液中形成的腐蚀产物的特性,研究结果如图4所示,加入适量的Mo能够改善腐蚀产物膜的致密程度,从而提高材料的阻氢和防腐蚀性能。
图4
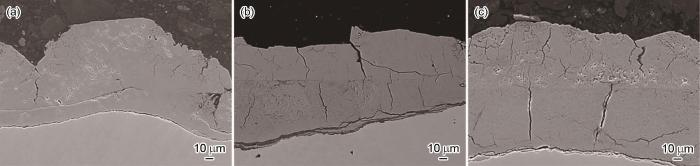
图5
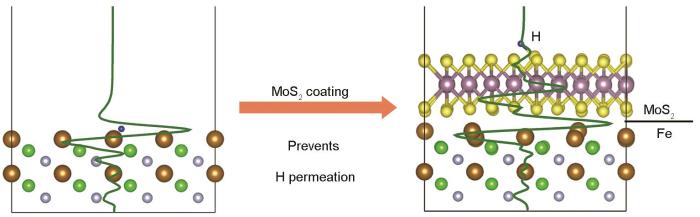
由于环氧树脂(EP)具有高粘度、附着强度和优异的物理阻隔性,常被用作复合涂层的基体。在Mo类填料中,金属有机框架材料(MoFs)能够显著改善高分子树脂类涂层的性能。MoFs能够进入涂层微陷处形成迷宫效应,延迟和切断腐蚀离子与金属表面的接触。参与MoFs的有机配体中的官能团和金属阳离子中心能够作为路易斯(Lewis)酸/碱参与环氧基团的开环反应,预聚物和固化剂分子能够进入多孔结构的MoFs中,为涂层分子固化提供条件。此外,MoFs作为异相核心能够促进高分子树脂聚合和凝固,提升涂层的固化反应,增加涂层的交联密度,从而增强管线钢的阻氢和防腐蚀能力[24,25]。Wang等[26]将多巴胺(DA)与MoF-5表面相结合,其中多巴胺中的氨基参与环氧树脂中的开环反应,提升MOF-5与环氧树脂的相容性,增加涂层的交联密度。此外,MoF-5可作为氧化石墨烯(GO)、氮化硼(HBN)等的填料进一步改善涂层的孔隙率,提高涂层的性能。随着MoFs材料的发展,其在有机涂层方面的应用逐渐走向成熟。MoFs在涂层阻氢和防腐蚀领域可与其他材料产生协同作用,提高涂层的被动阻隔性和主动防腐蚀性能。
图6
从图7中可以明显看出容抗弧半径大小排序为:1% > 0.8% > 0.3% > 0% > 1.5%。在1%的钼酸盐水性环氧树脂涂层中表现出最好的耐腐蚀性,适当的钼酸盐对抑制腐蚀的发生具有积极作用。钼酸盐能够使金属腐蚀电位正移,减缓腐蚀,形成钝化膜增加涂层性能,但钼酸盐的特性在较高离子浓度下才能发挥,然而水性环氧树脂涂层中钼酸盐的溶解能力有限,过高的浓度会破坏涂层连续性,降低涂层性能。因此,存在一个最佳浓度值,使得钼酸盐在水性环氧树脂中表现出最佳性能。导致含Mo类涂层防护机理的研究仍然比较模糊,且难以实现长效防护,由此,以氧化石墨烯类复合涂层研究应运而生。
图7
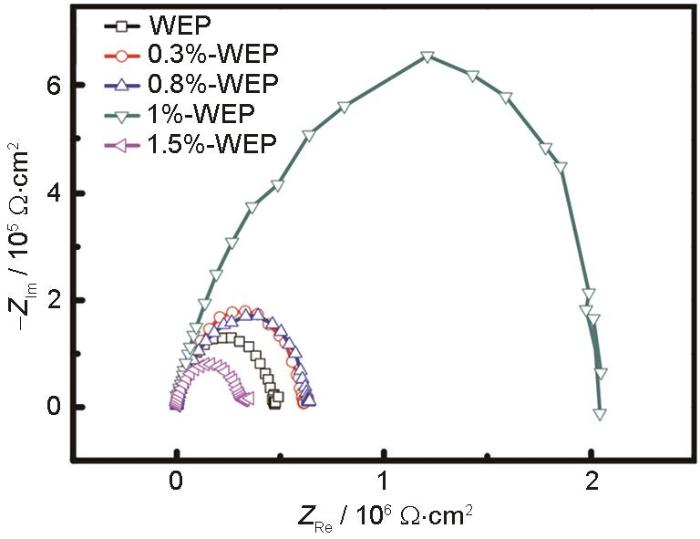
3 氧化石墨烯类聚合物复合涂层
在已知的纳米填料中,氧化石墨烯的发展十分迅速。其紧密堆积结构、高表面能和局域电场能够增强分子间作用力,从而提供较强的阻隔作用。大量研究表明环氧树脂/氧化石墨烯(EP/GO)复合涂层具有耐腐蚀性、阻隔性和实用性[30,31]。Tran等[32]通过使用EP/GO复合涂层,发现基体的氢渗透系数下降了17.5%。Rajabi等[33]向水性环氧树脂涂层中掺入0.25% (质量分数)的氧化石墨烯,提高了涂层的耐腐蚀性,腐蚀速率为2.3666 × 10-3 mm/a。尽管氧化石墨烯在阻氢和防腐蚀方面表现出良好的性能,但由于其在树脂中的均匀度和分散度受到限制,阻隔性和耐腐蚀性未能完全展现,因此,改性GO的研究成为热点。Yuan等[34]采用两步高速自旋镀膜法制备了热塑性聚氨酯(TPU)和P-苯二胺非共价功能化取向石墨烯(Gr-PPD)双层EP复合涂层,以协同提高其隔气性能和耐腐蚀性。由于Gr-PPD良好的分散性和定向,提供了强大的纳米屏障壁,减少了氢气分子或腐蚀性介质与管道表面接触的可能性,降低了管道失效可能性。
Li等[35]将十八烷胺(ODA)改性的氧化石墨烯(mGO-ODA)与接枝马来酸酐的聚丙烯(MAPP)复合,制备成复合材料涂层。该涂层通过喷涂方法涂覆在尼龙片和钢基底上,用于提高气体阻隔性能和防腐性能。结果显示,纯尼龙薄膜具有较高的H2GTR和O2GTR值,分别为180和40 cm3/(m2·d·Pa)。相比之下,mGO-ODA/MAPP复合涂层显著降低了这两种气体的传输率,60%mGO-ODA/MAPP涂层的H2GTR和O2GTR值分别降至10.6和2 cm3/(m2·d·Pa),表明该复合涂层对氢气和氧气具有极高的阻隔性能。此外,通过Henis和Tripodi电阻模型计算得到的渗透系数(P1)值进一步证实了60%mGO-ODA/MAPP涂层在阻隔氢气和氧气方面的效果,其P1(H2)和P1(O2)值分别为0.259和0.049 cm3/(m2·d·Pa)。这些结果表明,mGO-ODA/MAPP复合材料通过在聚合物基质中形成高纵横比的二维层状结构,有效地增加了气体分子的扩散路径和曲折度,从而实现了优异的气体阻隔性能,有效减少了氢气分子和腐蚀介质与管道表面接触的机率。Wan等[36]将羧甲基壳聚糖(CMCS)修饰在GO上,显著改善了GO在水性环氧树脂中的分散性和均匀性。研究表明,当羧甲基壳聚糖改性氧化石墨烯(CGO)浓度为0~0.25% (质量分数)时,随着CGO浓度的增加,涂层的阻氢能力随之上升,当CGO为0.25%时,两种组分相容性最高,环氧树脂/CGO涂层在氢渗透测试中展现出最低的氢渗透电流密度、最小的有效氢渗透系数,以及最低的固溶氢和扩散氢含量。随着CGO浓度继续增加,涂层的附着强度降低,导致涂层的阻氢能力下降。不同涂层的SEM形貌如图8所示,CGO的掺入使涂层产生了迷宫效应,提高纳米填料的分散度可以有效的增加迷宫效应的效果,从而达到阻氢和防腐蚀的目的,产生的迷宫效应路径如图9所示。
图8
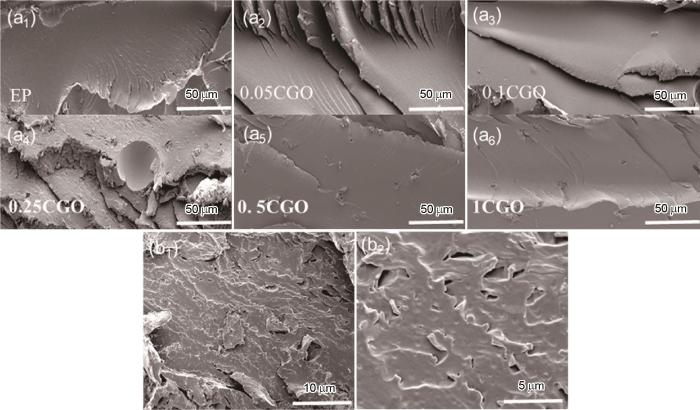
图9
黄科智[5]制备了一种APTES-GO改性环氧树脂/PVDF有机涂层,研究表明当APTES-GO在PVDF中的含量在0.1%~1% (质量分数)时,随着含量的增加,涂层性能不断提高。然而,当APTES-GO含量超过1%时,由于超出涂料溶解度发生团聚,导致涂层性能开始下降。APTES-GO能够改善PVDF有机涂层的结晶度和链段完整度,从而提高涂层的阻氢和防腐蚀性能。
不透气的疏水APTES-GO分散在PVDF有机涂层降低了PVDF有机涂层的自由体积,并且改变了腐蚀物质的传播路径,延迟和切断了氢气分子和腐蚀物质与金属表面的结合,如图10所示。
图10
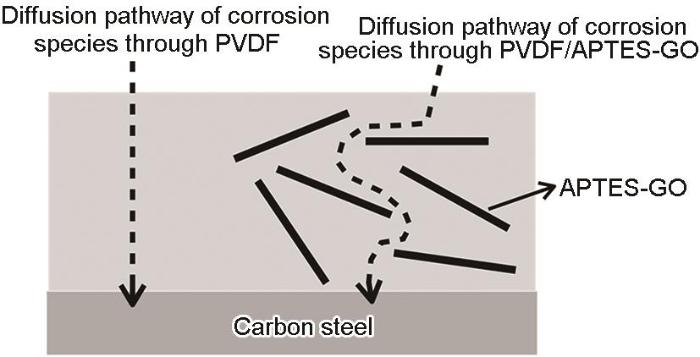
此外,二维材料被证明具有良好的阻氢和防腐蚀性能,氧化物、碳化硅等传统的材料显示出更高的氢渗透减少因子[37]。近些年,类石墨烯MXenes材料在各个领域得到广泛关注[38]。MXenes分子筛和储氢特性增加了其对H的有效阻隔[39,40]。Shi等[41]采用旋涂法将MXene (Ti3C2T x 纳米片)涂层沉积在X70管线钢上,并对其阻隔性能进行了电化学氢渗透实验评估,研究表明,MXene (4 mg/mL-1L)涂层的阻氢性能最优,氢渗透电流为9.1 × 10-6 A/cm2,低于X70钢的27.5 × 10-6 A/cm2。适合浓度的MXene涂层具有优异的阻氢和防腐蚀性能。氧化石墨烯类复合涂层凭借其优异的防腐蚀性和气体阻隔性,以及良好的机械性能和化学稳定性,已经成为各个领域广泛关注的对象。随着科技的不断进步和应用领域的不断拓展,氧化石墨烯类复合涂层的发展潜力将会得到进一步挖掘和利用,同时,由于金属及金属氧化物作为纳米填料,能够极大的改善涂层在高温、高压环境下阻氢和防腐蚀性能,此类涂层也成为学者的研究热点。
4 其他金属及金属氧化物有机复合涂层
氧化铈和锌等金属及金属氧化物也可作为纳米填料。由于这些无机物需要改性以增加与涂层的相容性,其填料的加入能改善有机涂层的耐腐蚀性和阻氢性能。
纳米氧化铈毒性小,作为金属化缓蚀剂已被广泛使用[42]。CeO2掺入有机涂层中,不仅发挥物理屏障作用,且Ce3+向Ce4+(CeO2)转化过程中会形成许多氧空位,对H产生吸附阻隔作用[43]。CeO2在阴极的沉淀反应会形成腐蚀产物膜,增加涂层的耐腐性能[44]。但由于氧化铈容易团聚,难以协助涂层形成致密保护膜,因此需要改性以制备成与有机涂层基体高相容性和分散性的物质。Yuan等[45]在玻璃薄片(GFs)上采用水热原位法生成疏水性CeO2,制备一种独特的复合填料,并将其加入到环氧树脂(EP)中。EP和填料之间通过共价键Ce-O-Si和最佳样品中的氢键形成的强界面力减少了EP中的自由体积,有效地提高了CeO2分散性,增强了阻氢和防腐性能,CeO2薄膜的抑制作用和复合填料的疏水性可以防止进一步的腐蚀。从图11中不同填料含量涂层的微观形貌可以看出,30%FAS-CeO2@GFs/EP中出现空腔,50%FAS-CeO2@GFs/EP和60%FAS-CeO2@GFs/EP由于纳米填料发生团聚,涂层内部出现裂纹;而40%FAS-CeO2@GFs/EP的结构比较完整,阻隔性能最佳。在3.5% (质量分数) NaCl溶液中浸泡60 d后,|Z|0.01 Hz保持最高值2 × 1010 Ω·cm2,其H2GTR值比纯PET薄膜降低约42%,其氢气渗透系数比纯EP涂层降低约65.64%,如图12所示这是由于高填充量下的GFs的择优取向和高纵横比,以及CeO2纳米粒子的锚定,这些因素共同产生了“迷宫效应”,为氢气分子提供了更长、更曲折的扩散路径,材料表现出优异的阻氢和防腐蚀性特性。
图11
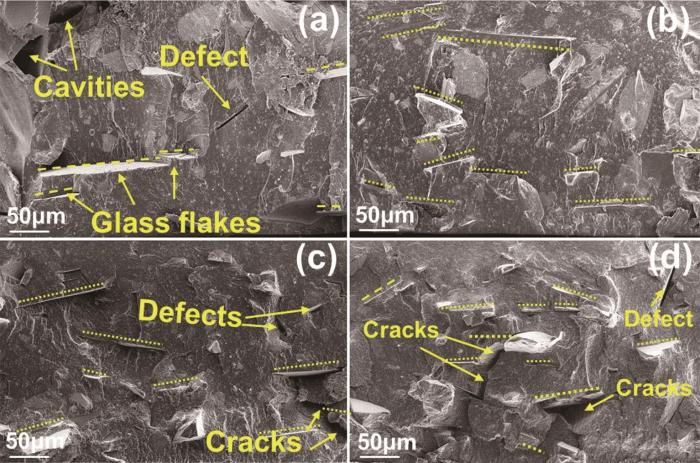
图12
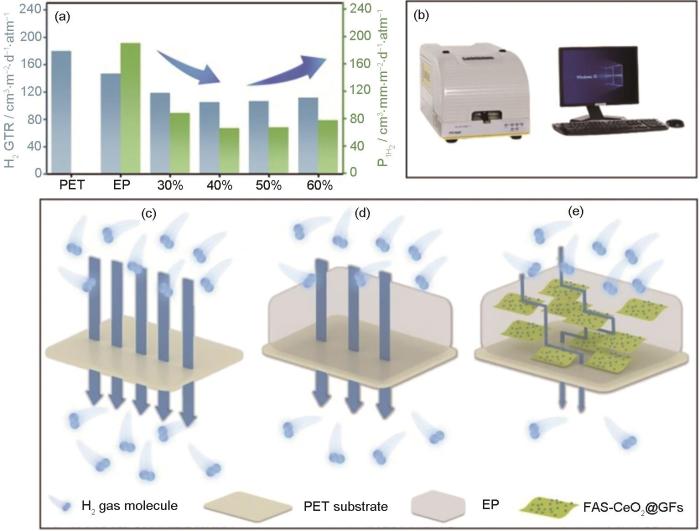
图12 PET基材、EP涂层PET和复合涂层涂层涂层PET的H2气体透过率(GTR),不同填料含量的EP和复合涂层的H2渗透系数值,气体渗透机示意图PET、EP涂层PET和复合涂层覆盖PET的H2气体分子渗透过程和还原机理示意图[45]
Fig.12 H2 gas transmission rate (GTR) of PET substrate, EP coated PET and composite coatings coated PET, H2 permeability coefficient values of EP and composite coatings with different filler content (a), schematic diagram of gas permeability machine (b), schematic illustrations of H2 gas molecule permeation process and reduction mechanism of PET, EP coated PET and composite coatings covered PET (c-e)[45]
此外,金属有机复合涂层的研究也在进行。Yang等[46]采用碱性锌酸盐电沉积技术成功制备了锌-环氧粉末(Zn-EP)复合涂层,结果表明,环氧粉末的添加使得涂层结构更加致密。通过电化学氢渗透实验,探讨了涂层对钢基底氢扩散行为的影响,环氧粉末的添加有效阻碍了氢气向钢基底的渗透,这可能有助于减轻镀锌钢的氢脆化问题。随后,通过电化学方法来评估EP对复合涂层耐腐蚀性能的影响,结果表明,EP的加入显著提升了涂层的耐腐蚀性,且Zn-6 g/L EP涂层的耐腐蚀性最佳。
总之,无机涂层与有机涂层都能够显著提高管线钢的阻氢和防腐蚀性能,上述研究中,涂层阻氢性能实验多以电化学氢渗透方法为主,难以模拟在高压气相氢对防护涂层的实际影响规律,掺氢天然气管道中产生氢脆的氢原子来源主要有两种,一是来源于湿H2S等腐蚀介质在发生腐蚀时析出的氢,二是管道输送介质中的高压气态氢。两种来源的氢对管线钢的破坏机制相同,但氢原子进入钢材内部的机理不同,电化学液相氢渗透的扩散动力来源于自由电子,掺氢天然气管道中的高压气相氢渗透的扩散动力来源于氢原子浓度梯度。有关掺氢天然气氢脆行为研究中,学者们将充氢方法划分为液相充氢法和气相充氢法两种方式,并且在研究过程中学者们观察到,气相充氢法更接近掺氢天然气运行的实际工况[47~49]。对于管线钢涂层防腐蚀性能研究中采用的实验方法多以室内环境下的电化学腐蚀实验为主,并未模拟出掺氢天然气管道内由H2S和CO2等杂质为主组成的腐蚀环境,涂层在掺氢天然气管道环境中的防护效果仍然模糊,需要改进实验装置,开展原位测试进行涂层性能测试。因此,在进行掺氢天然气管道防护涂层阻氢和防腐蚀性能研究时,应综合考虑管道的高压气相氢环境,采用气相充氢法进行实验,也要考虑湿H2S和CO2等杂质气体引起的液相氢渗透,同时还需要考虑杂质引发的析氢腐蚀问题,是气相液相充氢的协同,同时也是氢脆和腐蚀的耦合,因此,开展气液相充氢共存并耦合腐蚀的涂层防护性能评价研究将更符合工程实际。
5 总结
目前,随着全球清洁能源的需求的增加以及“双碳”目标的提出,掺氢天然气项目的发展进入关键时期,掺氢天然气管道阻氢和防腐蚀复合技术成为管道安全运行的必要保障,但气液相充氢共存并耦合腐蚀的研究处于起步阶段,未来将成为研究热点。通过上述研究可知:
(1) 腐蚀介质通过接触管道表面扩散入管道内部破坏管道结构。涂层作为一种有效的防护技术机制主要分为两种,首先是作为物理屏障,通过迷宫效应延迟和切断腐蚀分子与金属表面的接触;其次,通过与氢原子竞争或捕获氢原子,减少氢原子在金属表面的吸附和解离,从而达到阻氢和防腐蚀效果。
(2) 无机涂层、有机涂层及其复合涂层都具有更优异的阻氢和防腐蚀性能,相比之下有机复合涂层的种类更加丰富,性能更加优异。它们由纳米填料和涂层基体组成,纳米填料通过减小有机涂层的自由体积提高涂层的阻氢和防腐蚀能力。选择纳米填料时需考虑其与有机涂层的相容性,通常通过改性增加其在有机涂层中的分散性和均匀性,从而增强涂层性能。随着纳米填料含量增加,涂层性能也随之提升至最佳值,继续增加则因填料团聚而使涂层性能降低。
(3) 目前的涂层防护技术研究未考虑掺氢天然气管道实际运行过程中高压气相氢对涂层的作用效果,与工程偏差较大,需要进一步开展针对掺氢天然气管道涂层防护性能的气液相充氢共存并耦合腐蚀的研究,为掺氢天然气管道的安全运输提供参考。
免责声明:本网站所转载的文字、图片与视频资料版权归原创作者所有,如果涉及侵权,请第一时间联系本网删除。
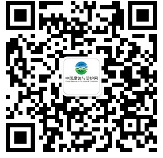
官方微信
《腐蚀与防护网电子期刊》征订启事
- 投稿联系:编辑部
- 电话:010-62316606
- 邮箱:fsfhzy666@163.com
- 腐蚀与防护网官方QQ群:140808414