内径/mm | 壁厚/mm | 材质 | 入口温度/℃ | 出口压力/MPa | 输量/(kg·s-1) | 上下坡段倾角/(°) | CO2摩尔分数/% | 气油比/(m3·t-1) | 含水率/% |
---|---|---|---|---|---|---|---|---|---|
300 | 16 | L360N | 52 | 14 | 30 | 45 | 3 | 8 523 | 3.5 |
内腐蚀是导致油气田集输管道失效的重要原因,具有隐蔽性、突发性等特点。随着国内非常规油气田开发的不断深入,采出介质的组成和运行工况更为复杂苛刻,集输管道面临的内腐蚀问题也更为突出。其中高压气田集气管道运行压力高,一旦发生腐蚀失效,就会造成极为严重的后果。
CO2是集输管道内腐蚀的主要影响因素,其腐蚀作用机理复杂,国内外研究人员对此进行了大量研究[1-3]。钟功祥等[4]采用失重法研究了温度和CO2分压对X52管线钢腐蚀速率的影响,结果表明管道沿线的温度、压力、持液率、流型及pH对CO2腐蚀的影响都很大。张喜庆等[5]对CO2和Cl-共同作用下的腐蚀规律进行了研究,结果表明流速、CO2分压等的升高会增加L245M管线钢的腐蚀速率。谢飞等[6]总结了现行CO2腐蚀研究的缺陷和不足,认为目前的腐蚀速率预测模型只考虑了电化学腐蚀因素,没有考虑管道内介质流动的影响,应建立更符合管道实际工况的预测模型。SADEGHI等[7]研究了温度和NaCl浓度对X65管线钢在CO2腐蚀介质中应力腐蚀开裂(SCC)的影响,发现腐蚀敏感性随温度升高和NaCl浓度降低而增加。ELGADDAFI等[8]研究了介质流动对高强度API碳钢CO2腐蚀的影响,发现无论温度高低,介质流速都会影响API钢的CO2腐蚀速率。目前,现有CO2腐蚀规律的研究主要侧重于常规运行工况或单一变量的影响,对于处在介质温度最高达90 ℃、运行压力超过15 MPa、输量最高达50 kg/s的高温、高压、大输量苛刻服役工况的管道沿线CO2腐蚀速率变化规律研究较少。此外,腐蚀试验无法体现长距离输送条件下的多相流变化特点及其对腐蚀速率的影响,而多相流仿真软件结合CO2腐蚀计算模型可以弥补上述问题。因此,笔者采用模拟计算的方式,以某高压气田集气管道为例,研究了温度70~90 ℃、压力15~18 MPa、输量35~50 kg/s的苛刻工况及15°~60°倾角变化对管道CO2腐蚀速率分布的影响规律,以期明确主要影响因素,为该高压气田集气管道腐蚀控制提供指导。
1. 试验
1.1 仿真模拟方法
已有文献研究表明[9-10]碳钢的CO2腐蚀受到多种因素影响,包括物理因素、环境因素和管道材料参数以及腐蚀产物膜等。
为提高腐蚀预测的准确度,将多相流瞬态模拟和De Waard95 CO2腐蚀模型相结合,进行苛刻服役工况下CO2腐蚀规律模拟研究,这克服了传统CO2腐蚀模拟对管内流型流态考虑不足的问题。De Waard95 CO2腐蚀模型是应用广泛的典型半经验模型[11],其包含了与流速相关的物质过程及与流速无关的腐蚀反应动力学过程,考虑了影响腐蚀的多个因素。多相流瞬态模拟采用OLGA多相流瞬态仿真模型,它能模拟管道中流体与时间相关的瞬态流动过程,精确预测生产系统中的诸多关键参数[12-13]。
1.2 模拟试验条件
以国内某条集气管道的正常运行工况数据建立对照模型,其正常运行工况如表1所示。此外,受地层波动影响,该集气管道面临异常高温、高压和大输量,采出介质最高运行温度为90 ℃,最高运行压力为18 MPa,最高输量为50 kg/s。此外,管道沿山脉铺设,高程变化较大,爬坡角度最高达60 ℃。为避免与CO2腐蚀有关的多因素混杂对本研究产生影响,将集气管道模型进行简化,如图1所示。管道模型水平段长3 200 m,上下坡段均长1 000 m,相对高差70 m。
2. 结果与讨论
2.1 温度的影响
以对照模型为基础,仅改变管道入口温度为70、80、85、90 ℃,研究温度对集气管道CO2腐蚀速率的影响。不同入口温度条件下管道沿线腐蚀速率分布如图2所示,最大腐蚀速率如表2所示。
入口温度/℃ | 52 | 70 | 80 | 85 | 90 |
最大腐蚀速率/(mm·a-1) | 4.88 | 5.77 | 6.23 | 6.45 | 6.67 |
由模拟结果可以发现,管道沿线腐蚀速率分布与高程变化直接相关,腐蚀速率的变化拐点与高程变化拐点重合。下坡管段腐蚀速率最高,水平管段次之,上坡管段腐蚀速率最小。各温度下,最大腐蚀速率均出现在下坡段的坡脚位置,最小腐蚀速率均位于上坡段。下坡管段和水平管段的腐蚀速率随入口温度变化均较为明显,即随温度的升高而增大。上坡管段腐蚀速率则随入口温度的升高有所降低。
上述规律表明,管道沿线腐蚀速率分布主要受高程引起的腐蚀介质传质速率变化控制。上坡段流速降低、传质速率降低,腐蚀速率降低;下坡段流速增加,传质速率增加,腐蚀速率升高。而温度的升高会影响多相流介质的气液比、黏度等,上坡段主要受气液比升高、液相减少的影响,流速降低,导致腐蚀速率降低;下坡段和水平段主要受液相黏度随温度升高而降低的影响,流速增加,腐蚀性离子传质速率增加,且壁面剪切力上升,影响腐蚀产物膜的稳定性,腐蚀速率升高[14-15]。
2.2 运行压力的影响
以对照模型为基础,仅改变出口压力,分别研究15、16、17、18 MPa高压输送工况下集气管道CO2腐蚀速率变化规律。不同出口压力下的腐蚀速率分布和最大腐蚀速率分别如图3和表3所示。
出口压力/MPa | 14 | 15 | 16 | 17 | 18 |
最大腐蚀速率/(mm·a-1) | 4.88 | 5.04 | 5.18 | 5.28 | 5.37 |
由图3可见,单一工况下,管道沿线的腐蚀速率仍与高程变化直接相关,最大腐蚀速率均位于管线下坡段的坡脚位置。对比不同出口压力下的模拟结果可知,管道腐蚀速率随着出口压力的升高而上升,且最大腐蚀速率随出口压力的变化尤为明显。
随着压力的增加,CO2气体分压增加,CO2在液相中的溶解量增大,阴极去极化过程加快,因此压力增加腐蚀速率增大[16]。下坡段腐蚀速率显著增大主要还是因为管内液相介质流速在重力作用下迅速增大,腐蚀离子传质速率快速提高,且使壁面剪切力锐增,腐蚀产物保护膜的稳定性显著降低。
2.3 输量的影响
以对照模型为基础,仅改变入口流量为35、40、45、50 kg/s,研究输量对集气管道CO2腐蚀速率的影响。不同输量下管道的腐蚀速率分布和最大腐蚀速率分别如图4和表4所示。
进口流量/(kg·s-1) | 30 | 35 | 40 | 45 | 50 |
腐蚀速率/(mm·a-1) | 4.88 | 4.96 | 5.02 | 5.06 | 5.08 |
由图4可见,管道沿线腐蚀速率的分布规律不受管道输量变化影响,仅随管线高程变化,最大腐蚀速率仍位于下坡段的坡脚位置,且相对其他位置,该处的腐蚀速率增幅较小。横向对比各工况发现,随着输量的增大,管道腐蚀速率明显增大。这是因为随着输量增大,介质流速增大,腐蚀性离子传质速率增加,壁面剪切力提高,H+等去极化剂能更快地扩散到电极表面,增强阴极去极化作用,腐蚀产生的Fe2+能够迅速离开金属表面,阻止金属表面保护膜的形成,并对已形成的保护膜起到破坏作用,形成活化钝化微电池,使腐蚀速率升高[17]。此外,在出口压力不变的情况下,随着输量增大,管线压力会升高,CO2气体分压也会相应增加,导致CO2在液相中的溶解量增大。下坡段坡脚处的腐蚀速率增幅相对较小是因为该位置液相流速和压力的增幅均较小。
2.4 管道倾角的影响
以对照模型为基础,仅改变上下坡管道倾角为15°、30°、45°和60°,研究上下坡管道倾角对集气管道CO2腐蚀速率的影响。不同倾角下的腐蚀速率分布和最大腐蚀速率分别如图5和表5所示。
上下坡倾角/(°) | 15 | 30 | 45 | 60 |
腐蚀速率/(mm·a-1) | 3.88 | 4.56 | 4.88 | 5.09 |
由图5可见,水平段的腐蚀速率基本不受管道倾角的影响。当倾角为15°、30°、45°时,上坡段腐蚀速率较水平段低,但当倾角为60°时,上坡段腐蚀速率较水平段高。上坡段腐蚀速率随着倾角的增大而增大;下坡段腐蚀速率显著高于水平段,亦随着管道倾角的增大而增大,最大腐蚀速率仍位于下坡段坡脚处。
管道倾斜会导致上坡段管道内液相爬升困难,流速降低,因此腐蚀速率较水平段低,但当倾角增大到一定程度后(60°),管内液体持续集聚,持液率上升,出现段塞流现象,增大流速和壁面剪切力,腐蚀速率会高于水平段。对于下坡段,倾角增大使管内介质流速增大,腐蚀性离子扩散速率增大,且压力逐渐上升导致CO2分压增大,促使其更多溶解于液相水中,增大了管道的腐蚀速率。
2.5 讨论
为了分析苛刻服役工况下管线最大腐蚀速率对介质温度、运行压力、输量和管道倾角变化的敏感性,以表1所示工况为基础模拟条件,将各影响因素的变化程度和对应最大腐蚀速率的变化程度按照百分数进行计算,曲线斜率可以直观显示最大腐蚀速率对各因素变化的敏感性。
由图6可见:在给定的苛刻服役工况下,管道的最大腐蚀速率对介质温度变化最为敏感,其次为运行压力,对输量的变化则相对最不敏感。这主要是因为介质温度的变化对管道腐蚀具有综合性作用,虽然温度升高会降低CO2在水中的溶解度,但同时会使CO2的扩散过程和电极反应速率加快,且温度升高还会降低液相黏度和流动阻力,提高液相流速,促进阳极和阴极反应的去极化作用;温度升高还会增加溶液的电导率,使腐蚀电流增大。运行压力则直接决定了介质中CO2分压的大小,显著影响CO2在液相中的溶解度和溶液pH,这些是影响CO2腐蚀的重要因素。此外,由于所选取的基础工况输量较大,输量继续增大则主要使运行压力升高、介质被压缩,而对流速提高有限,即传质速率变化不大,因此,最大腐蚀速率对输量变化相对不敏感。而管道倾角是影响腐蚀的外部因素,其对最大腐蚀速率的影响亦有限。
3. 结论
(1)随着介质温度从52 ℃提高到90 ℃,管道的腐蚀速率在上坡段降低,在水平段和下坡段明显提高,特别是下坡段增幅最大,约为37%;随着运行压力从14 MPa提高到18 MPa,管道的腐蚀速率稍有增加,但下坡段的增幅较明显,约为10%;随着输量从30 kg/s提高到50 kg/s,管道的腐蚀速率在水平段和上坡段大幅提高,最大增幅约为93%,而在下坡段的最大增幅仅4%;随着管道倾角从15°增加到60°,管道的腐蚀速率在水平段未见明显变化,而上下坡段明显增大,尤其下坡段增幅最大,约为31%。
(2)在苛刻服役工况下,管道沿线腐蚀速率分布主要受高程引起的腐蚀介质传质速率变化控制,其变化拐点与高程变化拐点重合,下坡段腐蚀速率最高,最大腐蚀速率位于下坡段的坡脚处,温度、压力、输量及管道倾角变化不影响腐蚀速率分布走向。
(3)在给定的苛刻服役工况下,管线最大腐蚀速率对介质温度变化最为敏感,其次为运行压力,对输量和管道倾角的变化最不敏感,腐蚀控制应重点关注介质温度、运行压力和下坡段等。
免责声明:本网站所转载的文字、图片与视频资料版权归原创作者所有,如果涉及侵权,请第一时间联系本网删除。
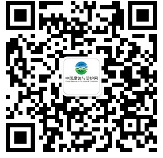
官方微信
《腐蚀与防护网电子期刊》征订启事
- 投稿联系:编辑部
- 电话:010-62316606
- 邮箱:fsfhzy666@163.com
- 腐蚀与防护网官方QQ群:140808414