电站锅炉是火力发电的关键设备,其能否长周期运行将直接影响整个机组的发电效率。锅炉运行时,通过过热器将饱和蒸汽加热成过热蒸汽,过热器管是过热器的主要受热面,也是电站锅炉承受温度最高的承压部件之一。锅炉过热器管断裂失效是导致锅炉停运的常见原因[1]。12Cr1MoVG低合金耐热钢是锅炉过热器管常用材料,其主控元素为铬、钼、钒。其中,铬元素可以提高材料的抗氧化性,钼元素起固溶强化作用,钒元素可以降低铬、钼元素从铁素体向碳化物转移的速率,提高材料的热稳定性[2]。12Cr1MoVG钢具有较高的抗蠕变性能和持久塑性、良好的焊接性能、成熟的热处理工艺、高性价比等优点,其最高使用温度为550 ℃,主要用于锅炉受热面管道[3]。
某单位一台蒸发量220 t/h的电站锅炉运行半年后,过热器管即发生开裂失效。锅炉的设计压力为9.8 MPa,最高工作温度为540 ℃。过热器管采用12Cr1MoVG钢,规格为ϕ51 mm×65 mm。为查明其开裂原因,对过热器管进行形貌观察、电镜微观分析、化学成分分析、力学性能测试、金相分析等,并查阅了安装及运行技术资料,找出了过热器管的开裂原因,以防止同类事故再次发生。
1. 理化检验与结果
1.1 形貌观察
对失效过热器管进行宏观检查,其形貌如图1所示。结果表明,过热器管有两处呈弯曲状,内弯部位为向火面,外弯部位为背火面,开裂发生在其中一个弯管内弧侧,且并排多根过热器管在同一位置均出现相似开裂现象。裂纹开口较宽且穿透整个管壁,断口两侧管段无明显胀粗、变形现象,断口最大宽度为2 mm,裂纹沿周向扩展至弯管两侧面,断口实测周长79 mm,接近管子全周长的二分之一。最小壁厚出现在弯管外弧侧,内弯侧最小壁厚为4.6 mm,外弯侧最小壁厚为4.3 mm。断口处外壁被黑褐色高温氧化物覆盖,这表明断口是在高温运行时开裂的。
为了进一步观察断口形貌,将管子从开裂处横向切开,再纵向切割为两部分,结果如图2所示。结果表明:断口呈黑色,表面已明显氧化,壁厚无明显减薄现象;断口处内壁有厚0.5 mm左右的氧化层,且局部氧化层已出现剥落现象。
采用X-MAX 20型能谱仪(EDS)对断口处弯管内壁氧化层的化学成分进行分析,结果如图3所示。结果表明,内壁氧化层主要含有铁和氧元素,同时伴有大量的磷、钠元素,推测氧化层的主要成分为氧化铁。
将断口试样放入弱酸水溶液中清洗,去除表面高温氧化物,然后采用ZEISS Sigma 300型扫描电镜观察断口微观形貌。在断口上可见开裂源处的缺口,如图4(a)所示;缺口放大后,可见裂纹扩展痕迹,裂纹从内壁以“倒川字”形态向外壁扩展,如图4(b)所示;断口表面和内壁近表面都存在二次裂纹,如图4(c)、(d)所示;在断口脆断区可见微观撕裂痕迹,如图4(e)所示;断口上还出现了呈脆性开裂特征的解理形貌,如图4(f)所示。
1.2 化学成分检测
从过热器管断口处取样,依据GB/T 4336-2016《碳素钢和中低合金钢多元素含量的测定火花放电原子发射光谱法》标准,采用X-MET8000型直读光谱仪对试样进行化学成分检测,结果如表1所示。从表1中可见,过热器管断口处的化学成分符合GB/T5310-2017《高压锅炉用无缝钢管》标准对12Cr1MoVG钢的要求。
项目 | 质量分数/% | |||||||
---|---|---|---|---|---|---|---|---|
C | Si | Mn | S | P | Cr | Mo | V | |
检测值 | 0.118 | 0.195 | 0.635 | 0.007 | 0.012 | 1.06 | 0.270 | 0.196 |
标准值 | 0.08~0.15 | 0.17~0.37 | 0.40~0.70 | ≤0.010 | ≤0.025 | 0.9~1.2 | 0.25~0.35 | 0.15~0.30 |
1.3 力学性能测试
由于开裂位置处于弯管处,无法截取拉伸试样,故从开裂位置两侧直管段向火面和背火面分别取样,进行室温拉伸试验,结果如表2所示。由表2可知,开裂过热器管的抗拉强度、屈服强度、断后伸长率均满足GB/T 5310-2017标准要求,但向火面的各项力学性能数据低于背火面,可见向火面力学性能有劣化趋势。
项目 | 抗拉强度/MPa | 屈服强度/MPa | 断后伸长率% | |
---|---|---|---|---|
检测值 | 向火面 | 529 | 383 | 25.3 |
背火面 | 586 | 426 | 29.1 | |
标准值 | 470~640 | ≥255 | ≥21 |
1.4 硬度测试
在过热器管开裂部位弯曲段及相邻直段截取全壁厚环状试样,采用H V-1000型维氏硬度仪在试样横截面进行硬度测试,考虑到试件表面有脱碳层,从距离内外表面0.5 mm处开始测量[4],每个位置测4个点,结果如表3所示。由表3可知,直管段向火面的硬度略低于背火面,这与力学性能试验结果一致;弯曲段向火面硬度为170.7 HV,上述测试结果均满足GB/T5310-2017标准要求,但是背火面硬度为206.8 H V,高于标准值,这是由弯曲变形强化所致。弯管冷弯成型后没有经过消除应力的热处理,但高温烟气与向火面接触,对向火面起到了热处理作用,故向火面硬度低于背火面硬度[5]。
测试位置 | 测试值 | 均值 | 标准值 | |
---|---|---|---|---|
直段 | 向火面 | 177.6~183.5 | 179.6 | 135~195 |
背火面 | 181.5~188.7 | 185.9 | ||
弯曲段 | 向火面 | 165.8~175.8 | 170.7 | |
背火面 | 201.6~209.8 | 206.8 |
1.5 非金属夹杂物分析
在断口内壁、断口延伸部位分别截取全壁厚纵向试样,按照GB/T 10561-2005《钢中非金属夹杂物含量的测定》标准要求进行非金属夹杂物分析[6],结果如图5所示。结果表明,两个取样部位均无夹杂物聚集现象,基体中只有少量夹杂物。其中,氧化铝(B类)细系级别为1.0级,球状氧化物(D类)细系级别为0.5级、粗系级别为0.5级,其余夹杂物A类、C类、DS类均未检出。非金属夹杂物级别符合GB/T 5310-2017标准中不大于2.5级的规定。
1.6 金相检查
在开裂过热器管断口部位、断口延伸部位(弯管侧面)分别沿纵向取样,断口相邻管段沿横向取样,按照GB/T 13298-2015《金属显微组织检验方法》标准要求,采用ZEISS Scope.A1型显微镜进行金相检查。
1.6.1 断口部位
由图6(a)可见,断口部位内壁的组织为铁素体、珠光体、贝氏体和颗粒状晶界碳化物,晶粒度为7.0级,脱碳层厚度为370 μm,内壁存在多处凹坑,凹坑中有氧化铁等腐蚀产物。由图6(b)可见,断口部位外壁组织、晶粒度与内壁相同,只是脱碳层比内壁薄,厚度为270 μm,组织已发生3级球化,说明管壁有过超温现象[7]。由图6(c)可见,断口边缘组织中有部分晶粒出现沿晶脱落现象,此为低合金钢碱应力腐蚀的特征[8]。
1.6.2 断口延伸部位
由图7(a)可见,断口延伸部位(弯管侧面)组织为铁素体、珠光体、贝氏体和颗粒状晶界碳化物,晶粒度为7.5级;由图7(b)可见,试样内壁有多处凹坑,脱碳层厚280 μm;由图7(c)可见,试样外壁脱碳层厚250 μm;由图7(d)可见,断口延伸部位内壁有多条二次裂纹,裂纹长度为1.0~1.6 mm,方向与试样表面近似垂直。
1.6.3 断口相邻管段
由图8(a)可见,断口相邻管段内壁(未用硝酸腐蚀)与开裂源区域有多处位置出现微裂纹和凹坑,凹坑深度为0.04~0.10 mm,裂纹与表面接近垂直,其他区域未见裂纹缺陷,内壁氧化层厚度为0.10 mm。由图8(b)可见,试样外壁(未用硝酸腐蚀)未见明显裂纹,但存在凹坑缺陷,氧化层厚度为0.09~0.20 mm;试样内外壁均有脱碳层,厚250 μm左右。由图8(c,d)可见,试样横截面组织多为铁素体、珠光体、贝氏体和颗粒状晶界碳化物,晶粒度为7.5级,只有一个区域组织为板条状马氏体,这是断口处蒸汽泄漏引起的急速冷却所致。
2. 失效原因分析
通过化学成分检测、力学性能试验、硬度测试可知,12Cr1MoVG钢过热器管各项测试数据均符合GB 5310-2017标准要求,不存在错用材料问题。宏观测厚发现弯管内弧侧、外弧侧均有减薄现象,外弧侧减薄为弯管拉伸所致,内弧侧减薄为氧化腐蚀所致,但壁厚均能满足强度要求,不会导致弯管开裂。非金属夹杂物分析可知,断口内表面无夹杂物聚集现象,夹杂物粗细级别最高为1.0级,满足GB/T 5310-2017标准要求。
金相分析可知,除相邻管段一个区域由于蒸汽泄漏导致的马氏体组织外,其余部位组织均为铁素体、贝氏体、珠光体;其中断口向火面组织有3级球化现象,断口内外壁均有脱碳层,内壁脱碳层厚度为370 μm,不满足GB/T 5310-2017标准中“内表面全脱碳层厚度小于300 μm”的要求[9],但是组织未出现老化现象,不会引起弯管开裂[10]。在断口相邻管段未采用硝酸腐蚀的内壁上,发现有微裂纹和腐蚀凹坑存在;断口延伸部位内壁有厚280 μm的脱碳层及多条二次裂纹。
宏观分析可知,过热器管于弯管内弯处开裂,裂纹两端扩展至弯管两个侧面,断口处弯管内壁有氧化层,氧化层热传导性能较差是导致过热器管超温的主要原因[11]。由扫描电镜分析可知,仅断口边缘有轻微撕裂痕迹,整个断口呈阶梯状解理形貌,与宏观脆性断裂特征相符。弯管内表面微裂纹和腐蚀凹坑是开裂起点,清除氧化物后可见二次裂纹及沿晶开裂痕迹,裂纹呈“倒川字”由内壁向外壁扩展。
查阅安装资料可知,12Cr1MoVG钢过热器管冷弯之后,没有进行热处理,导致弯管部位硬度、强度升高,韧性降低[12]。冷弯加工使外侧管壁减薄,弯管横截面变为椭圆形,产生较大的残余应力,内弯部位的管子内壁环向应力为拉应力,为管子的轴向开裂提供了条件[13]。
查阅运行资料可知,爆管前一个月水汽化验记录中,炉水中磷酸根离子含量和p H偏高质量浓度为9~13 mg/L,p H为10.0~11.5。依据GB/T 12145-2016《火力发电机组及蒸汽动力设备水汽质量》标准规定,当汽包压力为5.9~10.0 MPa时,炉水中
质量浓度应为2~10 mg/L,p H应为9.0~10.5。为防止锅炉运行时结垢,在炉水中加入Na3PO4,并用NaOH调整炉水碱度。从运行记录可以看出,Na3PO4含量和碱度均高于标准值,溶解在水中的盐类和游离态的碱会随蒸汽流入过热器[14]。在过热器管弯头部位蒸汽流速和方向变化,加之弯管处有氧化层,碱液在此沉积并浓缩,因此在内壁氧化层中检测出了钠、磷元素,见图3。
通过上述分析可知,过热器管存在碱应力腐蚀必备的三个条件,即较高的拉应力、较高碱含量、较高壁温[15]。碱应力腐蚀从内壁抗蚀能力较弱的脱碳层开始,在弯曲残余应力和蒸汽压力作用下,过热器管以微裂纹和腐蚀凹坑为起点发生应力腐蚀开裂,裂纹以沿晶开裂形式扩展至管道外壁,导致过热器管断裂。
3. 结论与建议
(1)过热器管冷弯成型时未进行消除应力热处理,且在弯管向火面内壁有微裂纹;运行期间炉水中含量和p H偏高,水蒸气携带盐离子和游离态碱离子沉积在弯管处的氧化层中,浓缩的碱液在高温下对过热器管内壁产生碱应力腐蚀,在弯曲应力和蒸汽压力作用下,过热器管产生微裂纹和腐蚀凹坑,并以此为起点发生沿晶开裂。
(2)断口部位弯管内壁有较厚的氧化层,且运行中氧化层有脱落现象,大幅降低了传热效率,导致弯管部位超温运行,造成金属组织3级轻度球化、晶界有脱碳层析出,从而降低了断口部位金属的抗腐蚀能力,也加快了碱应力腐蚀的发生。
(3)建议锅炉受热面弯管制作时进行热处理以消除应力,并加强工艺控制,防止产生加工缺陷;锅炉运行期间严格控制各种药剂含量,防止碱含量超标;加强汽水循环指标的监控,防止局部超温引起金属组织劣化,从而导致受热面金属耐高温腐蚀性能下降。
免责声明:本网站所转载的文字、图片与视频资料版权归原创作者所有,如果涉及侵权,请第一时间联系本网删除。
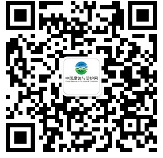
官方微信
《腐蚀与防护网电子期刊》征订启事
- 投稿联系:编辑部
- 电话:010-62316606
- 邮箱:fsfhzy666@163.com
- 腐蚀与防护网官方QQ群:140808414