随着汽车制造业发展以及钢铁冶金技术的不断提升, 超轻型高强度汽车用钢的开发与研究已历经了3个阶段的发展. 从上世纪80年代末开始无间隙原子(IF)钢的广泛研究, 随后发展了低合金高强度(HSLA)钢、双相(DP)钢[
当前在Q&P钢的生产中, 为保证获得超高强度以及较多的残余奥氏体, 采取的是提高钢中C的添加量的方法, 一般C含量都要在0.3%~0.5% (质量分数)[
因此, 本工作以C-Si-Mn系高强钢为研究对象, 围绕提高残余奥氏体含量及其机械稳定性等关键问题, 开展合金元素配分工艺及微观组织控制的研究. 采用在双相区保温+奥氏体化淬火+低温退火的热处理工艺, 就Mn元素双相区配分行为对组织演变及力学性能的影响进行了表征. 对探索合金元素配分的理论和机制有重要意义, 为当前开发适用于汽车轻量化发展需求的先进高强钢提供实践基础.
1 实验方法
实验用钢采用50 kg真空熔炼炉冶炼, 其化学成分(质量分数, %)为: C 0.20, Si 0.37, Mn 1.28, P 0.0032, S 0.0014, B 0.0018, 余量为Fe. 实验钢的Ac3=844 ℃, Ac1=718 ℃, Ms=345 ℃(Ac3为加热时先共析铁素体全部转变成奥氏体的终了温度, Ac1为加热时珠光体向奥氏体转变的开始温度, Ms为冷却时马氏体初始转变温度). 将冶炼后钢锭锻造并剪切成50 mm×50 mm×100 mm方坯, 在二辊热轧实验机上轧制得到厚度为3.5 mm的热轧板坯, 经5道次冷轧得到厚度为1.5 mm钢板.
图1a为双相区保温后直接淬火(I&Q)的工艺流程图, 采用双相区760 ℃进行保温加热, 保温时间为600, 1000, 1300和1500 s, 使之生成一定比例的铁素体和奥氏体, 通过保温使Mn元素由铁素体向奥氏体中进行扩散, 之后水淬到室温, 通过观测室温下Mn元素在铁素体和马氏体两相中的元素分布, 验证双相区的元素配分行为. 图1b为传统淬火+低温退火(Q&P)处理工艺流程图, 将实验用钢加热到奥氏体化温度(AT=930 ℃)并保温120 s, 使之完全奥氏体化, 然后采用盐浴淬火使其快速冷却到Ms~Mf (Mf为冷却时马氏体转变的终了温度)之间的某一温度(奥氏体化后冷却时淬火温度QT=220 ℃, 由马氏体含量计算公式Krauss-Koistinen-Marburger公式[
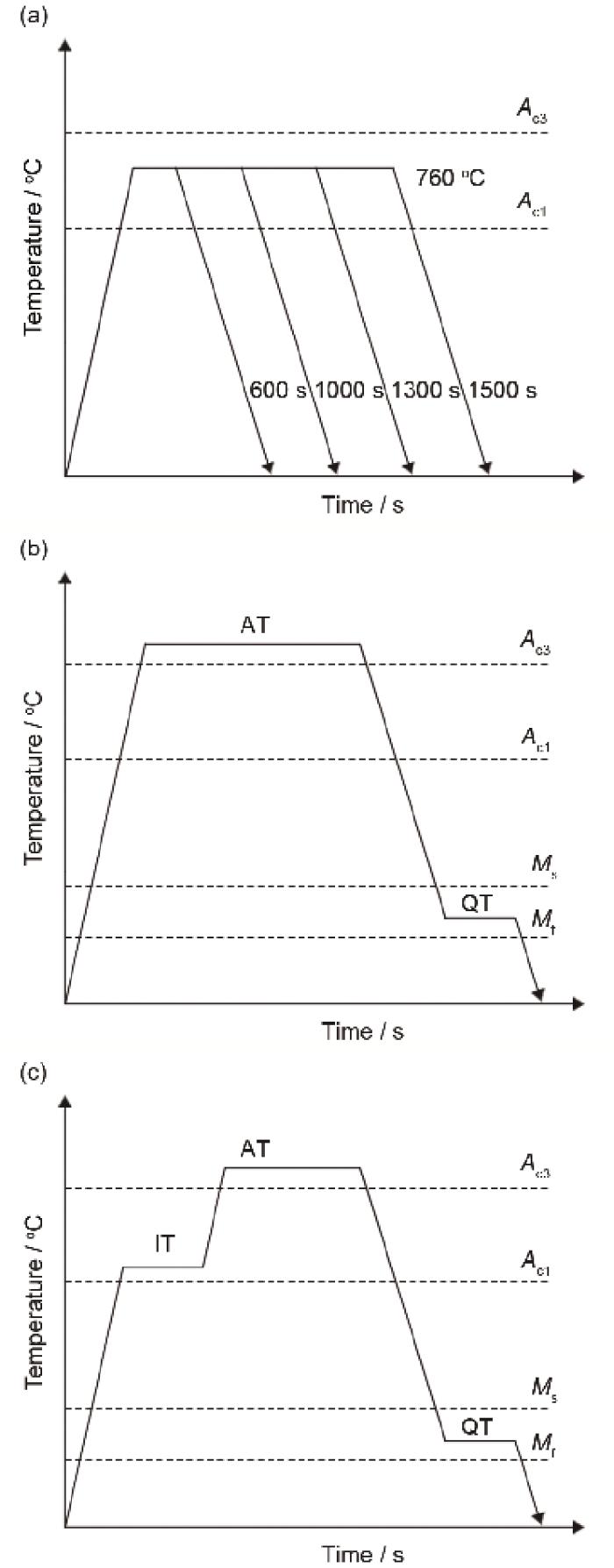
图1
Fig.1 不同热处理工艺流程图
将试样经不同工艺处理, 经过研磨、抛光和4%硝酸酒精(体积分数)浸湿后, 采用Axiovert200MAT光学显微镜(OM)和S-4800场发射扫描电镜(SEM)进行显微组织观察及分析; 采用线切割按照GB/T228-2002标准制取拉伸实验样品, 在WBW-600B液压万能试验机上进行拉伸实验; 利用D/MAX2500PC X射线衍射仪(XRD)分析实验用钢中的残余奥氏体, 实验参数为: Cu靶, 步宽0.02°, 功率40 V, 电流150 mA, 实验角度范围60°~100°, 速度10 °/min, 测定精确的衍射角2θ和积分强度I, 按国标GB8362-87对残余奥氏体的体积分数进行分析, 利用奥氏体(220)γ, (200)γ, (311)γ和马氏体(211)α′, (220)α′晶面的积分强度通过直接比较法[
2 实验结果及分析
2.1 I&Q工艺Mn元素配分行为
图2为双相区760 ℃保温并淬火后钢的SEM像. 由图可知, 试样的原始组织为铁素体(F)和珠光体(P)组织, 经双相区保温并淬火后, 试样的室温组织主要由铁素体(F)和板条马氏体(M)组成, 随着双相区保温时间的延长, 室温马氏体体积分数逐渐增多, 当保温时间达到1000 s时, 室温马氏体体积分数达到最大值55%, 如图2d所示. 当保温时间进一步延长时, 马氏体和铁素体两相趋于平衡, 室温马氏体体积分数随不同保温时间的变化曲线如图3所示, 说明在双相区进行保温时, 双相区中奥氏体体积分数会随着保温时间的延长逐渐增多直至达到饱和, 之后随着保温时间进一步延长, 奥氏体和铁素体两相趋于平衡.
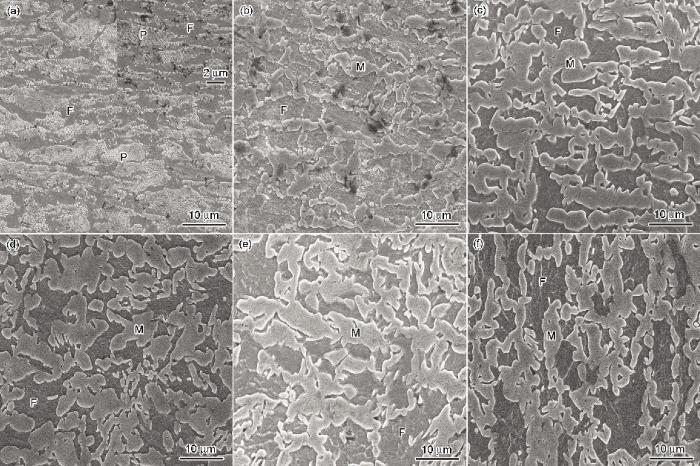
图2
Fig.2 760 ℃保温不同时间并淬火后钢的SEM像
图4和5为双相区760 ℃保温并直接淬火后钢的EBSD像及Mn元素分布的EMPA像. 由图可知, 在原始组织中(图4a), Mn分布均匀, 铁素体与珠光体中Mn含量基本相等, 当加热到760 ℃保温300 s并淬火后, 室温组织中出现少量马氏体组织, Mn开始出现不均匀分布现象, 马氏体中Mn含量稍高于铁素体, 说明此时双相区中Mn已经发生了从铁素体向奥氏体中的扩散. 当保温时间达到600 s时, 试样的室温组织已呈现出典型的马氏体和铁素体两相组织, 由EMPA像中能明显看到马氏体中的Mn含量高于铁素体中的Mn含量. 随着保温时间的延长, 向奥氏体中扩散的Mn含量逐渐增多, 当保温时间增至1300 s时, Mn在铁素体与奥氏体两相中化学势达到平衡, 不再进行两相间的扩散, 并且当保温时间为1300 s时双相区奥氏体中Mn含量达到最大值2.51%, 而随着时间的进一步延长, 奥氏体和铁素体两相虽趋于平衡, 但双相区组织仍呈现长大趋势, 使得Mn在奥氏体中含量相对减少, 钢中马氏体的Mn含量变化趋势如图6所示.

图3
Fig.3 不同保温时间对马氏体体积分数的影响
2.2 Q&P和I&Q&P工艺处理后钢的微观组织
图7为经不同工艺处理后钢的SEM像. 由图7a可知, 经Q&P工艺处理后, 室温组织主要由少量板条状马氏体、少量板条间弥散分布的碳化物颗粒和极少量的残余奥氏体组成, 还存在较多的块状组织, 这是经最终淬火时未转变奥氏体发生马氏体转变, 形成的二次淬火马氏体(M2)或残余奥氏体(RA), 呈规则几何形状, 无明显析出物. 在传统Q&P工艺奥氏体化盐浴淬火过程中, 将得到一定量的板条状一次淬火马氏体(M1), 此时C元素由一次淬火马氏体向未转变的奥氏体扩散使之趋于稳定, 由于盐浴淬火冷却速度较低, 配分过程中一次淬火马氏体会发生自回火分解, 马氏体板条边界较模糊, 产生颗粒状白色碳化物析出, 而较低的Si含量对碳化物抑制作用较小, 致使最终室温下钢的延展性能变差; 之后经水淬至室温时, 由于冷速较快且C配分对奥氏体的稳定性影响较小, 一部分未转变的奥氏体发生马氏体转变, 室温组织中出现部分二次淬火马氏体或残余奥氏体. 由图7b可知, 经I&Q&P工艺处理后, 室温组织主要由大量板条状马氏体、少量板条间弥散分布的碳化物颗粒和残余奥氏体组成, 存在少量的块状组织. 经双相区加热保温时, 铁素体中Mn元素随着保温时间的延长向奥氏体中逐渐扩散直至达到化学势平衡, 之后加热至奥氏体化温度, 此时由铁素体转变成的奥氏体组织中Mn元素的含量大大降低, 再经盐浴淬火时, 此部分奥氏体全部转变为一次淬火马氏体, 而未转变的奥氏体由于其Mn元素含量较高, 能稳定到室温, 而之后经水淬至室温时, 只有少量Mn元素含量较少的未转变奥氏体发生马氏体转变, 其余则保留至室温, 而双相区保温时, 铁素体中的C元素由于较高的自由能, 使得其在较短的时间已经完成了向奥氏体的扩散, 而QT阶段得到的一次淬火马氏体由于其C元素含量较低, 致使自回火产生的白色碳化物颗粒较少, 从而室温组织中板条马氏体量较多.
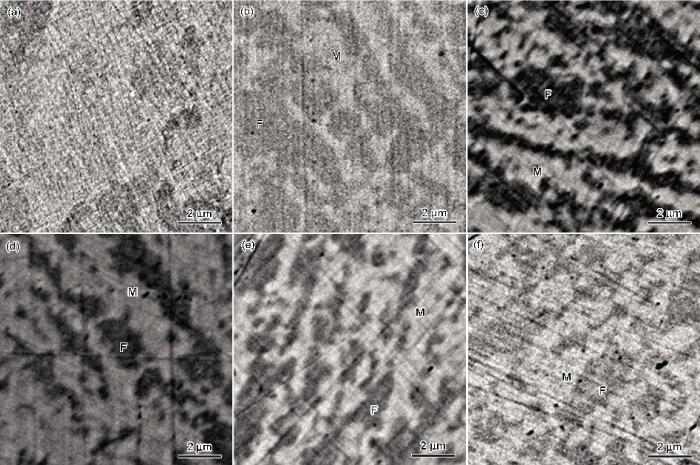
图4
Fig.4 760 ℃保温不同时间并淬火后钢的EBSD像
图8为经I&Q&P处理后钢的室温组织中马氏体和残余奥氏体的Mn元素分布情况. 由图可见, 实验用钢经I&Q&P处理后通过EMPA能观察到Mn元素在室温组织的马氏体和残余奥氏体中较为明显的不均匀分布情况, 薄膜状残余奥氏体在室温中存在于马氏体板条间. 从图8中A和B位置可以看出, 位于马氏体板条间的残余奥氏体中Mn元素含量明显高于马氏体基体, 这是由于当Mn元素在双相区达到化学势平衡时, 双相区奥氏体中Mn元素含量达到最大值, 又经淬火+低温退火处理后, 这部分富Mn的奥氏体经盐浴淬火时可以稳定下来, 该部分未转变的奥氏体由于较高的Mn元素含量使得大部分能够保留到室温形成残余奥氏体, 只有少量会发生马氏体转变. 可见, I&Q&P工艺对稳定钢中残余奥氏体以及提高室温残余奥氏体含量起到了良好的作用, 而这种软硬搭配的多相组织结构也可为实验钢提供更高的强度和塑性.
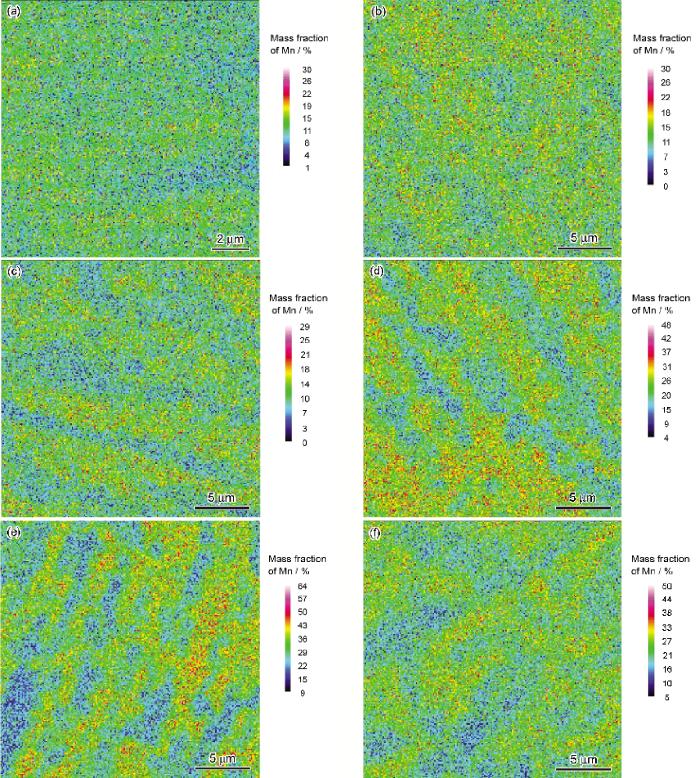
图5
Fig.5 760 ℃保温不同时间并淬火后钢中Mn元素分布的EMPA像
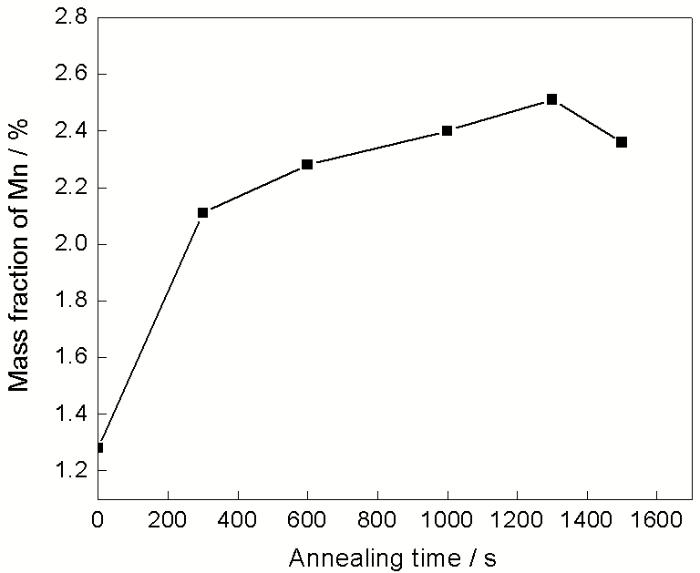
图6
Fig.6 760 ℃保温不同时间并淬火后钢中马氏体的Mn含量变化趋势
2.3 Q&P和I&Q&P工艺处理后钢中残余奥氏体含量和力学性能
图9为实验钢经Q&P工艺和I&Q&P工艺处理后残余奥氏体的XRD谱. 由图可知, 直接经Q&P处理的试样中有2个奥氏体峰, 且峰值强度偏低, 而经I&Q&P处理后的试样的XRD谱中明显观测到在60°~100°间又出现了2个晶面的奥氏体衍射峰, 分别是(311)γ和(220)γ, 说明双相区Mn元素的扩散对奥氏体起到良好的稳定作用, 从而使室温下保留了更多的残余奥氏体, 提高了钢的塑性.
经Q&P和I&Q&P工艺处理后钢的力学性能见表1. 由表可知, 实验钢的原始力学性能中, 抗拉强度为640 MPa, 延伸率为26.0%, 其原始组织为铁素体和珠光体组织. Q&P工艺处理后, 其抗拉强度为1560 MPa, 延伸率为8.3%, 强塑积为12948 MPa·%, 而经I&Q&P处理后, 与Q&P工艺相比, 钢的抗拉强度略有降低为1310 MPa, 延伸率有显著提高为12.0%, 强塑积为15720 MPa·%, 强塑积比Q&P工艺下提高了约20%.
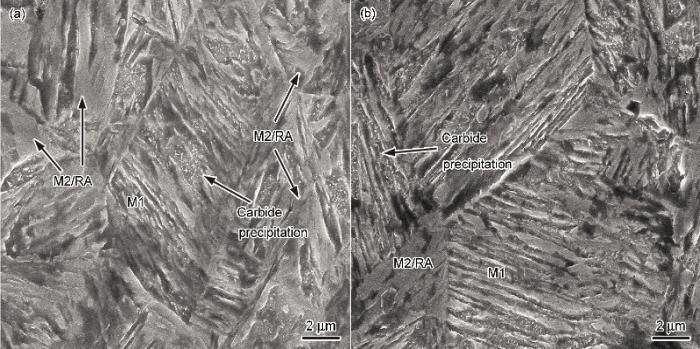
图7
Fig.7 不同工艺处理后钢的SEM像
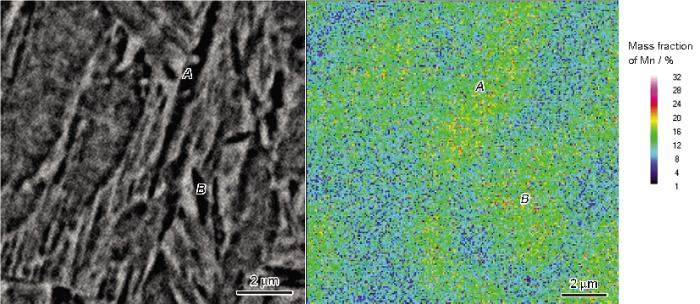
图8
Fig.8 I&Q&P处理后钢中马氏体和残余奥氏体的Mn元素分布
3 I&Q&P工艺各阶段组织演变分析讨论
图10为I&Q&P工艺各阶段钢的组织演变模型. γI为双相区奥氏体,γA表示双相区铁素体在AT阶段转变而成的奥氏体, γ′表示为双相区奥氏体在AT阶段转变而成的奥氏体, γ″表示为稳定到室温的残余奥氏体, M1表示为盐浴淬火阶段先形成的一次淬火马氏体, M2表示为最终水淬阶段形成的二次淬火马氏体. 由图可知, 实验用钢经冷轧后室温组织主要为铁素体和珠光体, 其中各相Mn元素含量相同. 加热到双相区进行保温时, 珠光体首先转变为奥氏体γI, 随着保温时间的延长, 双相区奥氏体逐渐增多直至达到两相平衡, 而铁素体中Mn元素也会伴随时间的延长向奥氏体中发生扩散, 直至达到化学势平衡, 此时钢的组织为铁素体和奥氏体, 且奥氏体中Mn元素含量明显高于铁素体. 随后升温至奥氏体化(AT)进行保温时, 双相区的铁素体转变为Mn元素含量较少的奥氏体γA, 而双相区的奥氏体γI转变为富Mn的奥氏体γ′, 之后盐浴淬火至QT阶段时, 奥氏体γA由于其稳定性元素Mn含量较少使得其在淬火时全部转变为一次淬火马氏体M1, 而富Mn的奥氏体γ′在此阶段则大部分可以保留下来, 只有少量发生马氏体转变, 且未转变的奥氏体γ′中Mn元素含量高于一次淬火马氏体. 最后经水淬至室温的过程中, 奥氏体γ′由于较高Mn元素含量最终能够稳定到室温, 得到残余奥氏体γ″, 只有少量发生二次马氏体转变, 而残余奥氏体γ″中Mn元素含量也明显高于钢中马氏体的Mn元素含量.
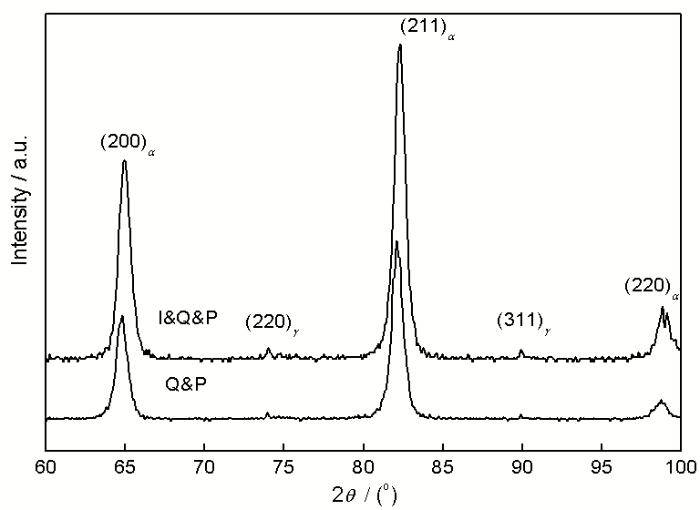
图9
Fig.9 不同工艺下钢的XRD谱
表1 不同工艺处理后钢的力学性能
Process | Rm / MPa | Rp0.2 / MPa | A / % | Rm·A / (MPa·%) |
---|---|---|---|---|
Original | 640 | 505 | 26.0 | 16640 |
Q&P | 1560 | 1150 | 8.3 | 12948 |
I&Q&P | 1310 | 975 | 12.0 | 15720 |
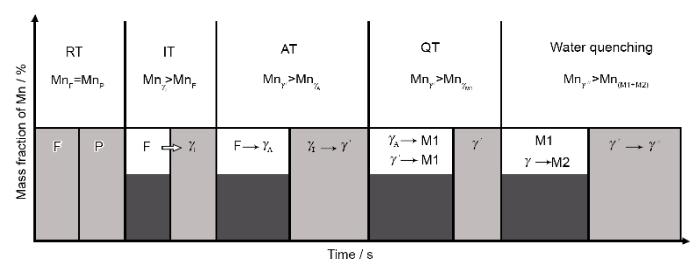
图10
I&Q&P工艺各阶段组织演变过程模型
值得指出的是, 经Q&P工艺处理的试样只含有少量由C配分作用稳定的残余奥氏体, 而I&Q&P工艺处理后的试样其室温残余奥氏体由富Mn的残余奥氏体和经C配分作用稳定的残余奥氏体共同组成, 富Mn的残余奥氏体其尺寸往往很小, 且Mn元素含量较高, 从而使高强钢具备了更优异的塑性.
4 结论
(1) 实验用钢经双相区保温时, 随着保温时间延长, 奥氏体体积分数逐渐增多, 保温时间为1000 s时, 室温马氏体体积分数达到最大值55%; 而铁素体中向奥氏体扩散的Mn元素含量也逐渐增多直至其在两相间达到化学势平衡, 并且当保温时间为1300 s时, 奥氏体中Mn元素含量达到最大值2.51%.
(2) 经Q&P工艺处理后, 室温组织为大量块状马氏体、少量板条状马氏体、少量板条间弥散分布的碳化物颗粒和极少量的残余奥氏体, 而经I&Q&P工艺处理后, 室温组织中块状马氏体含量大幅减少, 主要为板条状马氏体形貌, 而残余奥氏体含量显著增多, 达到4.3%, 抗拉强度为1310 MPa, 延伸率为12.0%, 强塑积达到15720 MPa·%以上.
(3) Q&P工艺处理后钢中只含有少量由C配分作用稳定的残余奥氏体, 而I&Q&P工艺处理后钢中残余奥氏体由富Mn的残余奥氏体和经C配分作用稳定的残余奥氏体组成, 显著提高室温下钢中残余奥氏体的含量和机械稳定性, 从而提高高强钢的室温成形能力.
免责声明:本网站所转载的文字、图片与视频资料版权归原创作者所有,如果涉及侵权,请第一时间联系本网删除。
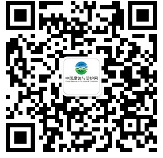
官方微信
《腐蚀与防护网电子期刊》征订启事
- 投稿联系:编辑部
- 电话:010-62316606
- 邮箱:fsfhzy666@163.com
- 腐蚀与防护网官方QQ群:140808414