在汽车工业中,锌镀层通常用于保护碳钢,避免其因环境中介质而腐蚀生锈。部分镀锌板出锌锅后会经过热处理,在热处理过程中,锌镀层与基体铁通过扩散发生合金化,使漆膜附着力、可涂装性和可焊接性得到提高[1]。合金化镀锌(GA)镀层由多层铁-锌系金属间化合物薄层组成,包括Γ相(Fe3Zn10)、Γ1相(Fe11Zn40)、δ相(FeZn7)和ζ相(FeZn13)[2-6]。GA镀层的结构、各相厚度都与镀层的成型性能相关。最内层的Γ相为脆性相,对镀层的附着性影响最大,Γ相越厚越容易粉化剥落;次内层的Γ1相能够抑制裂纹横向扩展;中部的栅状δ相具有良好的塑性;外层少量粒状δ相有利于成型性能;而少量ζ相和η相能够起到润滑作用。GA镀层表面微观形貌一般只能反映镀层最外层组成相的形貌和成分,要了解镀层整体结构还需从截面观察,考察各相的形貌以及分布比例。
一旦GA镀层受损,镀层在腐蚀环境中的溶解就会加速,多相镀层的腐蚀速率会不断变化[7-12]。镀层的腐蚀速率由镀层中各金属间化合物层的电化学性能决定。因此,为理解镀层的腐蚀过程,有必要对多相镀层的电化学行为进行表征。GA镀层中不同的金属间化合物层会显示出不同的电化学电位[13-15]。通常采用化学剥离试验(在没有任何外加电流的情况下)或电化学剥离试验(在外加电流的情况下)测量GA镀层在溶解过程中的腐蚀电位变化来表征各层的电化学行为[16-19]。然而,由于剥离试验无法提供镀层溶解速率,对于GA镀层的定量分析存在一定的局限性。作者通过扫描电镜(SEM)、透射电镜(TEM)观察了GA镀层的形貌,通过辉光放电光谱(GDS)、X射线光电子能谱(XPS)和X射线衍射(XRD)分析镀层的厚度、元素分布和物相结构,并采用恒电流极化对镀层进行了电化学剥离,研究了镀层中不同相的电化学性能。
1. 试验
试验材料为DX54D+ZF(单面镀层质量90 g·m-2)GA板。将GA板过碱洗除油、酒精超声清洗、吹干后,切割成10 mm×10 mm的试样。
采用化学法测量GA镀层中铁含量:将上述试样置于六次甲基四胺盐酸溶液中(镀层中的铁随之溶解出来,六次甲基四胺的缓蚀作用使基板中的铁不会溶解出来);将溶解了铁的溶液定容,采用Arcos型电感耦合等离子体光谱仪(ICP)测量溶液中的总铁量;根据测得的总铁量和试样上镀层的质量(镀层溶解前后试样的质量差),计算得到镀层中的铁含量。
采用美国力可公司的GDS-850A型GDS分析GA板镀层的厚度及元素分布,电压700 V,电流20 m A。利用JSM-7001F型SEM对GA镀层表面和截面形貌进行观察与成分分析。其中脆性断口是利用液氮冷却合金化锌层,使其呈脆性,再将其冲断,镀锌层沿晶断裂,能够清晰显示镀层的晶粒,从而能反映合金化热镀锌层的相结构。利用XRD对镀层的物相结构进行分析。采用Contour CT-K 3D型光学显微镜对GA镀层表面进行三维轮廓观察。采用赛默飞ESCALAB 250Xi型XPS分析GA镀层浅表层元素种类及价态。采用铜管和胶固定样品,再逐步减薄GA镀层截面样品,采用TEM观察其截面形貌。
采用PARSTAT4000+型电化学工作台进行电化学测试分析。铂电极为对电极,几种镀锌板为工作电极,Ag/AgCl电极为参比电极。极化曲线扫描速率为1 mV·s-1,电解液为3.5%(质量分数)NaCl溶液。用环氧树脂将10 mm×10 mm试样进行封装制成电极。采用恒电流极化法对镀层进行电化学剥离,试验溶液为250 g·L-1 NaCl+50 g·L-1 ZnSO4,极化电流为0.3 m A·m-2。随着电化学剥离时间的延长,不同的相会出现在表面,分别选择不同相进行极化曲线测试。
2. 结果与讨论
2.1 GA镀层的化学成分
GA镀层中的铁含量是镀层合金化程度的重要指标之一。镀层中铁含量必须控制在一定的范围之内(其质量分数通常为8%~12%),过高过低都不利于GA板的成型性能。镀层如果过合金化,铁含量就会过高,Г相生成较多,其抗粉化性能就会变差。镀层如果欠合金化,则铁含量会偏低,表面残存有较多ζ相,其硬度远低于Г相和δ相,冲压成型时镀层表面的移动阻力增大,从而使其与模具咬合,抗剥落性能变差。采用化学法测得试验镀层中铁质量分数为11.05%。
主要元素沿GA镀层深度的分布如图1所示。将Zn和Fe曲线相交处定义为镀层与基材的相界面,试验用GA镀层的厚度约为5 μm,且在界面处未见明显的铝元素富集,这说明其表面未形成良好的抑制层(Fe2Al5)。由于生产GA板时锌锅里面铝含量较生产纯锌镀层(GI)板时低,同时GA板出锌锅后还需经过高温合金化过程,此时基材中的铁向镀层中扩散,故GA镀层与基材界面处未见明显的抑制层。在0~5 μm深度范围内,铁含量随镀层深度的增加逐渐增加,不同铁含量对应不同的合金相(见表1),所以GA镀层为多相分布,从上往下依次为ζ相、δ相、Γ1相、Γ相。
相 | 化学式 | ρ(Fe)/% | 相 | 化学式 | ρ(Fe)/% |
---|---|---|---|---|---|
Γ | Fe3Zn10 | 24.0~27.7 | δ1k | FeZn10 | 7.0~11.5 |
Γ1 | Fe5Zn21 | 16.6~21.2 | ζ | FeZn15 | 5.1~7.1 |
δ | FeZn6.67 | 8.1~13.2 | η | Zn | 0.003 |
2.2 GA镀层形貌
图2为GA板表面SEM图。从图2中可见,其表面形态不均匀,可见明亮相和黑暗相的混合物,这是由镀锌后平整轧制工艺造成的,平整作为精加工步骤可以提供钢板所需的表面粗糙度。在表面局部还可以看到微裂纹,这些裂纹由退火处理时的热应力引起。GA镀层表面晶粒一般呈粒状或者长柱状,主要是δ相和ζ相,其中绝大部分为δ相,柱状晶长度可达到7.8 μm,平行分布的柱状晶束周围分布有颗粒状δ相。
从GA镀层脆性断口可以观察到各相的晶粒形状以及各相的厚度,与浸蚀截面相比,脆性断口晶界更清晰,对比效果如图3所示。在浸蚀截面可以看到许多贯穿镀层的微裂纹,这可能是剪切磨样过程中镀层粉化引起的;在脆性断口截面上未见明显贯穿镀层的微裂纹,但可以看见明显的光整坑、δ相、ζ相和Γ相。
图4为GA板表面的三维轮廓图。其与表面SEM图有较好的对应关系。ζ相部分结构高低起伏较明显,这种独特的表面结构使得GA板与镀层具有良好的结合力,涂装后耐蚀性较为优异。
由图5可见,GA镀层主要由δ相(FeZn6.67)组成,并含有少量的Г相(Fe3Zn10)以及ζ相(FeZn15)。利用X射线衍射进行镀层合金相定量分析时,会受到各合金相厚度以及合金相与分析表面距离的影响,因此该分析结果是半定量的。
2.3 XPS谱
从图6(a)可以看出,在GA板表面0 nm处检测到Zn 2p、O 1s、C 1s以及Al 2p信号。其中C 1s信号主要来自于表面污染碳,此处不作分析。O 1s信号证明了GA板表面氧化物的存在。从图6(b)可见,GA板外侧未见明显Fe的信号,随着溅射深度的增加,Fe的信号逐渐增强,这是由于GA板最外侧为η相(纯锌相)。尽管镀锌槽中的铝含量较低(质量分数0.12%),但镀层的外表面铝质量分数高达12.8%,这主要是由于Al2O3具有较高的表面形成能,铝元素倾向于向表面扩散。根据w(Fe)/w(Zn)计算结果可以看出,随着溅射深度的增加,w(Fe)/w(Zn)值逐渐增大,在10 nm处达到0.22,说明检测到了ζ相。
图7为各元素高分辨XPS谱。由图7(a)可见,在GA板表面(溅射深度为0 nm)不存在Fe 2p特征峰,对应GA板η相,当溅射深度为5 nm时,出现明显Fe 2p特征峰;由分峰结果可以看出,Fe元素以合金态离子形式(Fe2+、Fe3+)存在,随着溅射深度增加,合金态Fe离子含量降低,单质态Fe含量逐渐增加。由图7(b)可以看出,随着溅射深度增加,O 1s峰值逐渐降低,O含量减少,其在531.8 eV、530.0 eV以及533.5 eV结合能处的三个特征峰分别代表Al2O3、ZnO以及表面的吸附H2O/C—O;从分峰结果可以看出,表面吸附H2O/C—O含量逐渐降低,在溅射深度20 nm内,氧化物主要以Al2O3形式存在,同时在溅射深度15 nm范围内存在ZnO特征峰。结合图7(c)可以看出,在溅射深度10 nm范围内,Zn元素出现氧化态Zn2+(1 022.4 eV)以及金属态Zn(1 021.8 eV)两个特征峰,当溅射深度为15 nm时,氧化态Zn2+特征峰消失,仅存在金属态Zn特征峰。
2.4 TEM形貌
减薄后的GA镀层TEM形貌如图8所示。在较低的放大倍数下可以大致区分出钢板基体、Γ层和δ层。在GA镀层上从外到内用能谱法依次分析各处元素含量,测量位置如图9所示,结果见表2。结果表明,尽管能谱分析得到铁含量的测量值远远超过理论值,但是其变化趋势符合逻辑,通过铁含量相对变化可以大致判断出各部分的物相。例如,在最外层1、2处铁含量最低,并且含有少量的铝,该处应该是ζ相;8处紧邻基材,其铁含量是合金中最高的,此处应该是Γ相;9和10处为钢板基材。
位置 | 质量分数/% | 位置 | 质量分数/% | ||||
---|---|---|---|---|---|---|---|
Zn | Fe | Al | Zn | Fe | Al | ||
1 | 72.33 | 27.37 | 0.29 | 6 | 68.93 | 31.07 | 0.00 |
2 | 64.98 | 33.85 | 1.78 | 7 | 50.67 | 49.33 | 0.00 |
3 | 56.15 | 43.85 | 0.00 | 8 | 35.07 | 64.93 | 0.00 |
4 | 75.10 | 24.90 | 0.00 | 9 | 0.00 | 100.00 | 0.00 |
5 | 70.87 | 29.13 | 0.00 | 10 | 0.00 | 100.00 | 0.00 |
2.5 电化学性能
在一定的外加电流下,金属能够在介质中发生阳极溶解,相应的电位-时间曲线可以反映这一溶解过程。GA镀层中由于各相组成和结构不同,其溶解过程也各不相同,电位-时间曲线的变化能够反映镀层的组成。因此,在特定条件下控制GA镀层的溶解,通过测量溶解过程的电位-时间曲线,便能够对镀层各相进行定性甚至定量分析。图10(a)为GA镀层在250 g·L-1 NaCl+50 g·L-1 ZnSO4溶液中阳极溶解时的电位-时间曲线。图10(b)为各电位点的极化响应即各相的极化曲线,极化曲线拟合参数见表3。其中,电位点1~4分别与GA镀层中ζ相、δ相、Γ1相、Γ相对应,电位点5与基体对应。结果表明,电位点5即基体的自腐蚀电位为-619 mV,远高于其他相的自腐蚀电位,这种局部电位差加速了GA渡层的电偶腐蚀[13,20-21]。ζ相、δ相均具有较好的耐蚀性,且ζ相和δ相之间的电位差异较小,其电偶腐蚀作用较小,当中间层的δ相腐蚀完全消耗后,Γ1相、Γ相和基体暴露在溶液中并形成电偶,腐蚀加快。因此,δ相应保持均匀和厚实,以保护基体免受腐蚀。Γ相与基体间腐蚀电位差较大,其电偶腐蚀作用较强,Γ相的自腐蚀电位较负,先发生腐蚀;因为Γ1相和基体之间的腐蚀电位差大于Γ1相和Γ相之间的腐蚀电位差,所以Γ相在Γ1相之前溶解[22]。
试样 | Jcorr/( μA·cm-2) | Ecorr(vs. SCE)/mV |
---|---|---|
ζ | 7.4 | -991 |
δ | 6.9 | -957 |
Γ1 | 11.7 | -876 |
Γ | 17.8 | -798 |
基体 | 23.6 | -619 |
3. 结论
(1)GA镀层为多相分布,从上往下依次为ζ相、δ相、Γ1相、Γ相,铁含量随镀层深度的增加逐渐增加。
(2)ζ相、δ相均具有较好的耐蚀性,且ζ相和δ相之间的电位差异较小,其电偶腐蚀作用较小,当δ相腐蚀消耗完全后,内层Γ1相、Γ相和基体才会发生腐蚀。其中,Γ相的自腐蚀电位较负,先发生腐蚀。因此,δ相应保持均匀和厚实,以保护基体免受腐蚀。
免责声明:本网站所转载的文字、图片与视频资料版权归原创作者所有,如果涉及侵权,请第一时间联系本网删除。
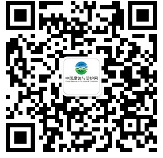
官方微信
《腐蚀与防护网电子期刊》征订启事
- 投稿联系:编辑部
- 电话:010-62316606
- 邮箱:fsfhzy666@163.com
- 腐蚀与防护网官方QQ群:140808414