-
0 前言
-
电磁轨道发射是利用电磁能替代机械能和化学能进行发射的新型发射技术,它突破了传统意义上火炮的局限性,能实现超过 2 km/s 的极高速度,具有发射速度快、射程远、安全性能高、可控性强等优点,应用前景广阔[1]。
-
电磁轨道发射装置由储能系统、脉冲功率调节系统、电磁轨道发射器和远程遥控系统组成[2],如图1 所示。储能系统在发射过程中,通过脉冲功率调节系统将积蓄的能量调节为瞬时超大功率电能输出给电磁轨道发射器,从而激发磁场,电枢在洛伦兹力的作用下,推动负载加速发射以达到预定速度,远程遥控系统通过信息指令实现对能量的控制。其中,电磁轨道发射器由电枢、轨道以及绝缘支撑体组成,如图2 电磁轨道发射枢轨载流摩擦副及装配弹丸示意图所示。电枢和轨道是主要运动接触部件,常称为枢轨载流摩擦副。
-
图1 电磁轨道发射装置组成示意图
-
Fig.1 Schematic diagram of the composition an electro-magnetic rail launcher
-
图2 电磁轨道发射枢轨载流摩擦副及装配弹丸示意图
-
Fig.2 Schematic diagram of electromagnetic rail launching armature rail carrier friction pair and assembled projectile
-
由于电-磁-热-力多场耦合条件下的极端服役工作环境,即有大电流(~MA 级)、强磁场(~T 级)、高热量(~103 K 级)、强作用力(~106 N 级)通过枢轨接触表面,枢轨载流摩擦副不可避免地会产生一定的损伤。其中,电枢将弹丸推动至超高速,以较小的电流通流面积导通回路中的所有电流,承担着发射系统产生的大部分能量,是系统中将电能转化为弹丸动能的关键部件,表面状态会直接影响枢轨载流摩擦副的服役性能,并与发射装置的效率和精度密不可分,其损伤不仅导致电枢自身性能的下降,同时会降低轨道的使用寿命,制约其发展前景[2]。
-
为解决发射过程中电枢损伤问题,研究者将研究重点放在电枢损伤机理和损伤防护技术上。目前,对于电枢损伤的试验验证研究主要是通过对发射后电枢进行回收,观察其经过一个服役过程后的表面形貌,从而判断是否出现损伤以及损伤的严重程度; 对于电枢损伤的模拟与仿真主要是通过调节不同的参量,包括过盈量、电流密度以及电流波形等,分析其在服役过程中各项性能的变化,进而推导出服役过程后的损伤情况。
-
本文综述了近年来国内外研究者对电磁轨道发射电枢损伤的研究进展。从典型损伤特征及其影响因素,损伤机制和改进手段等方面进行阐述,归纳了电枢损伤的分类和特征,总结了对应的理论分析,梳理了不同的防护优化技术。可以发现,电枢损伤研究发展至今,针对其损伤机理的探究仍不够深入,尚不具备一套完整的理论体系,损伤防护处理技术尚不成熟。
-
1 典型损伤
-
1.1 载流摩擦磨损
-
载流摩擦磨损是指在导入电流后,两金属表面相互接触并由于发生相对运动出现一系列摩擦学行为而产生的磨损[3]。由于电枢自身的机械属性和预紧力条件下的电接触特征,在大电流、高运动速度的极端服役过程中会不可避免地产生载流摩擦磨损。这种损伤主要是由于枢轨间接触斑点在预紧力、温度升高和电磁压力增大下产生黏着,而后在摩擦力的作用下相互磨损导致的,即损伤发生于旧接触斑点损坏而消失,新接触斑点不断形成的循环往复过程中。区别于一般的机械磨损,载流摩擦磨损不仅要受到电枢自身机械结构的影响,其还处于大电流场中,受到电流热效应的制约,同时间在发射过程中会出现短暂分离的接触特性导致电枢存在严重的电弧磨损,因此,电枢的载流摩擦磨损主要包括机械磨损、电流磨损及电弧磨损等形式。
-
1.1.1 机械磨损
-
GAO 等[4]在考虑了预紧力和电磁压力的共同效应下,采用 Archard 磨损模型对枢轨接触进行有限元仿真,研究预紧力和电磁压力(洛伦兹力在法向上的分力)对电枢磨损的影响,结果表明,在发射过程中,电磁压力提供了大部分的枢轨接触力,并发现最大接触压力分布于电枢尾翼两侧,这也是电枢磨损集中的区域。MERRILL[5]建立了枢轨接触界面的熔化润滑模型,严格控制焦耳热的影响,重点对发射过程中电枢产生的机械磨损进行研究,其结果显示,法向载荷的增加会加剧电枢的磨损。主要是因为法向载荷的增大会导致枢轨间机械混合层厚度逐渐增加,并在发射过程中产生裂纹。当裂纹扩展至一定程度后,一部分电枢基体材料就会和枢轨间机械混合层一起剥落,从而导致严重的损伤。因此,电枢的机械磨损主要是由其复杂的受力条件导致,主要发生在枢轨接触的低速阶段。
-
1.1.2 电流磨损
-
电流磨损通常指电接触材料在导入电流后,由于滑动摩擦以及电阻而引起的热量和磨损现象,热量的产生会导致温度升高,进而引起材料发生热膨胀、热应力、氧化等现象[6-7]。一方面,升温会导致表面氧化物的生成,造成电接触材料间接触电阻的增大和润滑性的降低;另一方面,电流产生的焦耳热会造成材料表面层软化,降低摩擦层与基体的结合程度,从而影响材料的摩擦学性能[8]。电枢在 MA 级大电流作用下在轨道间高速滑动,枢轨间摩擦界面温度迅速升高。电流磨损成为电枢载流摩擦磨损的重要特征之一。SENOUCI 等[9]在进行滑动电接触摩擦磨损试验中对比了是否通入电流的磨损情况,结果表明,电流的加入会加剧材料的磨损。这是由于通入电流会在枢轨摩擦副中产生电流热效应,释放热量破坏表面润滑膜,导致枢轨界面粗糙度增加,磨料性能提升,力学性能下降,发生电流磨损,磨损率增大。WATT[10]对不同电流条件下发射后电枢进行回收处理,通过电枢质量损失测定和表面磨损机械轮廓测定两种方法确定电枢损伤量,如图3 所示。可以发现,电枢损伤量与电流值的大小近似成一阶线性正比。
-
图3 不同电流条件下电枢质量损失和表面磨损量[10]
-
Fig.3 Armature mass loss and surface wear under different current conditions[10]
-
1.1.3 电弧磨损
-
电枢在轨道间非全约束条件下进行的高速飞升,常导致电枢与轨道发生短暂分离而形成电弧。 NAGASAWA 等[11]重点关注电弧磨损导致的载流摩擦磨损,研究表明电弧产热是导致材料热熔化的主要来源之一。CHEN 等[12]利用高速摄像机记录了电弧磨损的全过程,结果表明磨损率与累计电弧放电能量近似成正比,但在合理范围内加大法向力以增加摩擦副接触面积,可以有效降低电弧磨损带来的影响。可以发现,以弧光形式散发的热量会导致枢轨接触界面温度急剧升高,导致材料发生严重熔化剥落。
-
目前研究者认为载流摩擦磨损是在载流条件下,机械能和电能相互耦合,二者互相影响共同作用下的结果。图4 展现了 Al-Zn-Mg-Cu 系电枢在高速载流试验过程中所表现出的“三阶段”典型载流摩擦磨损形貌。可以看到,在电流较小的上升阶段,表面形貌主要以犁沟为主;在电流最大的峰值阶段,表面形貌主要为犁沟、熔融状组织等;在电流下降阶段,枢轨间出现电弧,热量急剧增加,表面形貌主要为熔融状组织等。
-
图4 “三阶段”载流摩擦磨损形貌
-
Fig.4 “Three-stage” current-carrying friction and wear morphology
-
1.2 热熔化
-
在电磁轨道发射过程中,由于枢轨接触面间的接触电阻和电枢自身体电阻,当电流经轨道流向电枢时会产生焦耳热。另一方面,为保证枢轨间良好的电接触性能,枢轨间需紧密配合,存在预紧力。电枢在磁场中还要承受极大的电磁扩张力,发射过程中,随着枢轨间相对运动速度呈指数增长,二者相互摩擦而产生大量的机械摩擦热。在两种不同形式的热量叠加作用下,电枢表面温度陡然增加。当表面温度高于自身熔点时,电枢表层会向熔融态转变,发生热熔化,并在枢轨接触面间形成一层液态金属膜(Liquid Metal Film,LMF)。
-
李鹤等[13]开展了电磁轨道发射电枢接触界面温度场仿真研究,结合试验数据,初步揭示了焦耳热和摩擦热对电枢温度场分布的影响规律,为电枢表面熔化过程提供了基础理论。CHEN 等[14]设计电枢的相关结构,使得枢轨接触表面全部转化为熔体磨损,建立了熔体磨损与发射参数、材料参数之间的构效关系。在电枢高速运动的同时,液态金属膜厚度也在不断增加,其本身也会产生粘滞热,加剧电枢表面的热熔化。STSFANI 等[15]在考虑液态金属膜的影响下研究了固体电枢表面的熔化波侵蚀,发现电枢表面经历了一个快速加热和熔化过程。同时,不同发射阶段下枢轨接触状态不同,引发电枢热熔化的热源占比会发生改变,电枢表面不同位置的熔化深度也不同。CHEN 等[16]基于电磁轨道炮的三维多物理场耦合模型,通过建立仿真模型和进行缩比试验,对电枢熔化区域的热源占比、最大熔化深度位置演变以及电枢损伤形貌进行了分析,如图5 所示。可以发现,接触电阻和电枢的体电阻产生的焦耳热是电枢熔化的主要因素,熔化深度最大位置基本保持不变,为最先开始熔化区域。该仿真模型能为后续研究电枢热熔化过程和预测电磁轨道发射过程中的全尺寸温度特性提供帮助。
-
目前,关于电枢热熔化产热来源的研究理论已相对成熟,主要是摩擦热和焦耳热。但对于电枢运动过程中不同热源产热量的变化及其对电枢表面热熔化影响程度大小的时空演化特性研究尚浅,缺乏系统的理论指导。
-
图5 电枢熔化区域热源占比、最大熔化深度位置演变及电枢典型损伤形貌示意图[16]
-
Fig.5 Schematic diagrams of the heat source percentage in the melting region of the armature, the evolution of the location of the maximum melting depth and the typical damage morphology of the armature[16]
-
1.3 转捩烧蚀
-
由于枢轨载流摩擦副自身结构的局限性,在极端服役工况下,电枢在发射过程中产生轻微垂直振动,与轨道发生失接触或者接触压力不足,使枢轨间的接触方式由“固-固”或“固-液-固”转变为 “固-等离子体-固”,这种转变称之为转捩[17],如图6 所示。转捩的产生会导致枢轨接触面上产生电弧击穿现象,在电枢表面引起严重烧蚀,从而加剧电枢的热熔化损伤,破坏电枢的效能。典型的转捩烧蚀损伤形貌如图7 所示[18]。
-
图6 转捩烧蚀产生示意图
-
Fig.6 Schematic diagram of transition erosion generation
-
图7 典型的转捩烧蚀损伤形貌[18]
-
Fig.7 Typical transition erosion damage topography[18]
-
为达到电磁轨道发射过程中枢轨摩擦副间无电弧接触的状态要求,以确保其精确性和安全性,开展对于枢轨间发生转捩的内在机理性研究是十分有必要的。研究者从枢轨接触界面材料热应力、熔化波烧蚀模型以及过盈压力和电磁压力等方面展开了分析,当电枢因各种外界因素发生轻微形变或者材料损失时,转捩产生的几率将大大增加。关晓存等[19] 在假设电枢磨损主要为熔化磨损的前提下,通过仿真分析和试验验证研究了电枢表面磨损区域分布和磨损量大小,为建立材料损失与转捩的关系奠定了理论基础。朱仁贵等[20]研究了枢轨接触间过盈压力和电磁压力大小在电枢运动过程中的变化,发现由于电枢的载流摩擦磨损,过盈压力不断减小,当二者合力降低到一定阙值时,转捩发生概率增加。在现有理论基础上,转捩烧蚀在发射参数表现为膛口电压的突然升高,炮口电阻增大,脉冲电流处于下降阶段。陈允等[21]在研究发射过程中滑动电接触特性的试验中,对炮口电压和电枢电流进行了测量,研究表明:转捩经常发生于电流下降至峰值电流 80%~90%的时刻。在此基础上,王志恒等[22]利用有限元软件 ANSYS Workbench 对电枢转捩过程进行了模拟仿真,分析了电流下降段电枢内部通流情况,电流下降段电枢内部和表面的电流分布如图8 所示,可以看出在电流下降段电枢内部会产生涡流,内表面电磁力发生反转,导致枢轨间接触压力不足,电弧放电,发生转捩;进而分析了电流下降率的影响,结果表明:电流下降率越大,电枢发生转捩的可能性越大,但是此试验未能考虑电枢运动对电流分布的影响。
-
图8 电流下降段电枢内部和表面的电流分布
-
Fig.8 Current distribution inside and on the surface of the armature in the current drop section
-
国内外研究者对转捩烧蚀的产生机理提出了许多看法,包括电枢材料载流摩擦磨损过大且损伤区域不均一导致枢轨间无法共面接触,脉冲电流在下降阶段产生的涡流使内部磁力反转导致的电枢尾部离开轨道表面等。从其定义本身来看,发生转捩烧蚀时必然伴随着枢轨间的失接触,产生由等离子体填充的空间间隙,而这种空间间隙极大程度上是载流摩擦磨损带来的,其带给电枢材料的物质损失直接导致枢轨间空间间隙的存在,从而引起失接触位置产生电弧击穿现象,导致转捩的发生,其产生机理目前尚不能用单一一种理论体系成功加以说明。
-
2 典型损伤影响因素
-
为了研究电枢载流摩擦磨损,热熔化以及转捩烧蚀等典型损伤形式的影响因素,近年来,大量研究者采用试验现象分析和数值模拟两种方法相结合,分别从服役变量和电枢自身参数进行对比试验论证。
-
2.1 服役变量
-
针对服役变量,研究者们以电流波形、界面液层厚度、轨道通流长度、极性、滑行距离以及摩擦因数等因素为切入点,通过调节不同的外界影响量进行电枢损伤试验和仿真,探究其损伤程度的大小。
-
LI 等[23]根据接触面金属液态膜(LMF)和 Reynolds 方程,在温度、应力和电磁场耦合作用下,建立了热弹性磁流体力学模型,分析了电流波形对表面热熔化速率和 LMF 厚度的影响,结果表明:电流波形越平滑,电枢表面热熔化速度越慢,最小 LMF 厚度越薄;张宝[24]舍弃常规研究,认为枢轨接触界面温度相同的非真实条件,在考虑真实具体的界面温度分布下,建立了界面液层磁场、热场以及润滑流场等多物理场耦合模型,分析了不同厚度液层的基本流体属性及其降温作用,在一定程度上还原了电枢与轨道间在高速相对滑动时产生的载流摩擦磨损,但未考虑引入液层后电接触性能的变化; 李天亮等[25]在基于面电流假设,建立了电枢电磁感应强度场计算模型和电枢所受电磁力模型,以轨道通流长度这一参数为变量进行研究,观察电枢所受到的电磁力和磨损情况,综合各项性能要求提出了 “4 倍口径法则”。但该模型假设条件苛刻,不能完全运用于实际电枢运行过程;宋联美等[26]在自制的载流电弧试验机上进行了极性对载流电弧的演化过程和烧蚀影响试验,结果表明:不同极性条件下的载流电弧能量不同,阳极材料蒸发气化是电弧燃蚀的主要因素,抑制阳极材料的蒸发气化,缩短枢轨间电弧存在时间能有效减轻电枢电弧磨损,这为保护电枢和减少电枢耗材提供了理论思路。但是该试验未考虑客观磁场的存在以及电枢高速运动下的机械摩擦热对试验结果的干扰。张玉燕等[27]在传热学理论的基础上建立了电接触摩擦副的二维有限元模型,并进行电接触构件表面温度测量试验,以电枢为研究对象,观察了电枢最高温度出现的时间点以及随电流、滑行距离以及接触面摩擦因数等等参量的变化趋势,探究了电枢高温升的因素,为高速载流滑动电接触中电枢材料的选取及如何降低温升、提高电接触性能提供了参考依据。但是该试验和模拟模型都以单一变量进行研究,未考虑诸如接触面摩擦因数在滑动过程的动态变化对试验结果的影响。综合以上研究可以发现,全面考虑服役多因素耦合的研究仍然存在不足。
-
2.2 电枢自身参数
-
对于电枢自身参数,研究者们通过调整不同的电枢尺寸,包括口径高度、尾部长度、尾翼倾角等,设计枢轨间过盈尺寸、接触方式等,观察电枢在不同自身参数和差异化枢轨间状态下的损伤。
-
LI 等[28]通过试验研究了电枢口径高度对电枢尾部冲蚀的影响,总结了不同线电流密度下电枢电流熔体侵蚀的研究结果,并利用有限元软件 COMSOL 分析了枢轨间的初始接触位置及其接触界面的电流密度分布;LI 等[23]根据接触面金属液态膜(LMF)和 Reynolds 方程,在温度、应力和电磁场耦合作用下,建立了热弹性磁流体力学模型,分析了电枢尾部长度和角度对表面熔化速率和 LMF 厚度的影响,结果表明:一定范围内电枢尾翼长度越大,电枢表面熔化速度越慢,最小 LMF 厚度越薄; 杜翔宇等[29]通过枢轨间一般的电接触特性设计了枢轨间理想的接触压力,基于反向加载法改进了电枢的过盈尺寸和形态,并对装配过盈电枢和非过盈电枢的发射器进行仿真研究,观察发射过程中某些典型时刻电枢内部电流和焦耳热集中情况。该研究为电枢的结构尺寸设计提供了新的思路,但其研究适应性不强,试验观察结果没有连续性,只适用于某些特殊时刻。CHENG 等[30]采用 ANSYS 与试压纸相结合的方法对电枢材料接触特性进行了研究,结果表明:枢轨接触特性在一定范围内与电枢材料强度成正比。LIU 等[31]为研究枢轨间接触方式对电磁轨道发射性能的影响,采用有限元法分别计算了 C 型电枢在不同接触面积和接触位置下的电磁推力、电磁压力和电流密度,并对不同接触方式下的计算结果进行了比较,结果表明:电枢尾部与轨道的分离会导致电磁压力急剧下降,电枢尾部与轨道需要保持紧密接触,以保证稳定的电流传递,实现电枢与轨道完全接触的电气性能,这对改善枢轨接触特性以及有效减轻甚至是防止电枢发生电弧磨损具有参考价值。
-
3 典型损伤机制模拟与仿真趋势分析
-
电枢发生损伤是电-磁-热-力多场耦合服役环境下的结果。在电磁轨道发射过程中,各种内外界因素的交互作用导致电枢的服役效能下降,其中接触应力集中、电流密度集中以及热量集中是电枢发生损伤的三种主要原因。国内外研究者们基于此,通过不同的机制模拟与仿真展开了深入研究。
-
3.1 接触应力集中
-
枢轨载流摩擦副接触界面兼具摩擦接触和电接触的特性,其共面性和粗糙性导致了损伤机制的多场耦合性,是一种特殊的电接触形式。宏观上光滑的接触表面在微观上是粗糙不平的,其粗糙度一般使用平均斜度 masp 和平均高度 σasp 进行表证,其中 σasp,u与 σasp,d分别为接触面上、下两侧凸起的平均高度,masp,u 与 masp,d 分别为接触面上、下两侧表面的平均斜度。微观接触表面示意图如图9 所示[32],可以看出微观有效接触面是由一个个离散的接触点构成,以此形成的接触面为有效接触面。研究指出有效接触面积仅为名义接触面积的 1%左右[3]。这些接触点承担着电流传导和应力承载的作用。
-
图9 枢轨微观有效接触界面示意图[32]
-
Fig.9 Schematic diagram of the microscopic effective contact interface of the pivot rail[32]
-
一方面,枢轨在加载装配后会导致接触应力集中于电枢局部区域。另一方面,预紧力和电磁压力在发射过程中集中加载于枢轨界面的接触点,从而带来接触应力集中。电枢表面接触应力集中分布区域如图10 所示,可以看出有部分区域接触应力为 0,即失接触,接触应力集中于某一块区域[33]。田振国等[34]在考虑了枢轨间摩擦和电磁热效应的基础上,利用 Ansys 软件分析了枢轨间接触应力分布随电枢运动的变化特性。侯俊超[35]基于“Marshall 法则”,利用 ANSYS LS-DYNA 有限元软件模拟出枢轨间的机械预紧力和电磁压力,建立了电枢所受接触应力的理论计算模型。范薇等[36]提出“安克法则”的瞬态应用方法,指出电枢在运动过程中所受接触力大小应超过“1 g/1 A”,以此规避电枢接触失效问题。
-
图10 电枢装配后表面接触应力分布[33]
-
Fig.10 Surface contact stress distribution after armature assembly[33]
-
电枢和轨道自身的结构尺寸参数对枢轨间的接触状态影响巨大,间接地决定着接触应力集中的位置。研究者们从电枢和轨道的形状,大小以及枢轨间匹配性等方向进行思考,研究了避免接触应力集中的最优结构尺寸参数。白春艳等[37]利用数值分析的方法,研究了 V 形、U 形以及 Saddle 形 3 种不同形状电枢在发射过程中的接触应力分布情况,研究表明,在相同的电磁轨道发射系统条件下,V 形电枢的服役接触应力值最大,Saddle 形电枢的服役接触应力值最小,故 Saddle 形电枢为最优选择。冯登等[33]利用 ABAQUS 有限元分析软件,对固体 C 形电枢各结构参数对接触应力分布的影响,研究表明减小电枢尾翼长度和增大电枢肩部厚度能促进接触应力分布的均匀性。李鹤等[38]设计并比较了凸形和凹形两种不同截面形状轨道对枢轨接触特性的影响,其结果显示凸形轨道具有更好的机械和电流特性。在此基础上,刘峰等[39]对电枢力学模型进行有限元分析,设计了一种新型 H 形电枢,并通过简化的悬臂梁模型确定过盈尺寸,以此分析改进前后枢轨界面接触应力的分布情况,如图11 所示,可以看到,改进后电枢模型所承受的等效应力由 538 MPa 减小到 446 MPa,接触应力集中的情况得到改善。冯建源等[40]通过正交试验分析研究了枢轨间过盈装配中电枢各结构尺寸参数的匹配性,并对其影响程度进行了排序,其结果显示,影响程度依次为:翼根宽度>过盈量>尾翼长度>翼尖宽度>肩部高度。
-
同时,接触应力集中会导致电枢在装配后各区域载荷不一,出现某块区域载荷过大或者过小的现象。载荷过小,枢轨载流摩擦副接触应力不足,发生失接触或者接触不良,引起电火花导致电弧磨损和转捩烧蚀的产生。载荷过大,枢轨载流摩擦副表面接触点所需承受的压力增大,在高运动速度下剪切力增大,磨损率提高,摩擦热和焦耳热也随之增加,导致材料热熔化程度加深,造成电枢损伤情况严重。因此,在保证枢轨间基本接触应力的前提下,找到枢轨损伤率最低的最优载荷值意义重大。 YASAR 等[41]的摩擦磨损试验结果表明,随着载荷的增加,载流摩擦因数和磨损率呈现先降低后升高的相同变化趋势,30~50 MPa 的接触应力区间内为轻度磨损;50~120 MPa 的接触应力区间内为中度磨损;小于 30 MPa 和大于 120 MPa 的接触应力区间为重度磨损。赵晓非等[42]的研究证明了载流摩擦副存在一个最优接触应力值,但其研究未能形成适用于不同载流条件下最优接触应力值的系统理论和变化规律。
-
图11 枢轨间接触应力分布[39]
-
Fig.11 Contact stress distribution between armature rails[39]
-
3.2 电流密度集中
-
区别于传统电接触,电磁轨道发射装置表现出工作时间短,电流振幅高,电流密度大等特点,具有特殊的电流密度分布特性。这对电枢上电磁力分布和热场的分布状态都有一定的影响,是电枢设计不可忽视的一环。
-
分布均匀的电流密度会使电枢在服役工作中表现出更好的力学性能和电接触性能。然而在实际发射过程中,电枢上瞬态电流密度的分布往往是不均匀的,呈现出在局部区域上电流密度高度集中的态势,这会加剧电枢局部热熔化和增加转捩烧蚀发生的可能性。由于电枢发射时间较短(ms 级),目前对于电枢瞬态电流密度分布特性的研究主要采用数值分析和仿真模拟等手段,利用 COMSOL 建立非理想枢轨接触界面磁扩散模型和利用 ANSYS 建立枢轨接触界面电流密度分布计算模型进行计算分析。由此建立了一系列导致电枢上电流集中的物理效应,包括电流趋肤效应(Current skin effect,CSE)、速度趋肤效应(Velocity skin effect,VSE)以及临近效应(Proximity effect,PE)等[32,43-44],如图12 所示。
-
图12 稳态电流分布与三种电流集中的物理效应
-
Fig.12 Physical effects of steady state current distribution with three current concentrations
-
XIA 等[45]研究表明电流趋肤效应在电流熔体侵蚀(CME)中的影响不可忽略。巩飞等[46]在考虑 VSE 的影响下,通过建立电流熔化波烧蚀的计算模型分析了电流熔化波的形成及传播过程,在电枢表面得到了一个 U 型烧蚀面。ZHOU 等[47]通过观察发射过程中的磁热耦合现象,分析了不同速度下 VSE 对电流密度分布的影响,研究结果显示,随着速度的增大,VSE 带来的电流集中现象愈加明显,但同时存在一定的速度阙值。LOU 等[48]指出临近效应加剧了轨道相邻侧电流密度的集中,提出适当增加轨道间距等减小临近效应的方法,这对降低发射过程中的电枢损伤具有一定的帮助。曹昭君等[49]在结合趋肤效应和临近效应等相关理论,模拟出静态电枢电流密度分布特性,其结果表明电流密度主要集中在枢轨接触界面头部和电枢边沿的中部,如图13 所示[49]。
-
图13 电枢电流密度集中区域[49]
-
Fig.13 Concentration area of armature current density[49]
-
3.3 热量集中
-
目前对枢轨载流摩擦副产热大和温升高带来损伤失效问题的研究主要集中在电枢。这是由于在发射过程中,运动电枢与发射出口方向未通过的轨道部分没有电流通过,相比于电枢温度较低,在一定程度上能够传导部分热量,起到散热降温作用。而电枢一直有大电流通过,且始终与轨道紧密接触,几乎不存在散热功能,是系统的主要热源之一。因此,电枢温度能客观直接地反映电磁轨道发射器内温度。由于枢轨间自身机械结构和装配的特殊性,在电磁轨道连续快速发射下电枢温度随时间和空间分布不均匀,使得热量在一定时空内聚集,进而导致电枢损伤。
-
针对电磁轨道发射系统膛内热效应和发射过程中电枢温度分布情况,研究者在结合枢轨载流摩擦副中非完全式接触(Imperfect electric contacts, ImPEC)这一实际接触模型的基础上,以电流产热和摩擦生热作为枢轨系统中热量的主要来源进行探索。KIM 等[50]采用电磁有限元软件 EWAP3D 对枢轨接触面处电流产热导致的温度分布情况进行了仿真模拟,进而推导出热量集中区域,其结果显示,电枢最大温度分布出现在 1 ms 时刻,而非 4 ms 出口时刻。同时,接触界面以下电枢内部 0.5 mm 处温升要大于电枢表面。原因在于轨道在发射过程中会起到冷却降温的作用。娄建勇等[51]基于 COMSOL 有限元仿真软件建立了电磁发射装置动态计算模型,并以此模拟了电枢在发射过程中温度分布的时空演变过程,如图14 所示,可以看出,高温区主要集中在电枢尾端,热量集中导致电枢尾端率先熔化。王昊 [52] 针对枢轨间温度场利用有限元软件 COMSOL 建立了三维模型,研究了温度分布时空特性,并探讨了发射次数、峰值电流和材料电导率对热量集中的影响。同时,由于枢轨接触特性,轨道温度及其热量会通过传导间接影响电枢,导致电枢处热量集中,温度升高,其表面热熔化程度也随之加深。徐伟东等[53]研究发现轨道温度升高会增加枢轨间接触电阻,降低电枢初速,使得电枢在低速阶段持续时间过长,加剧了电枢的载流摩擦磨损。
-
图14 发射过程中电枢温度云图[51]
-
Fig.14 Temperature cloud diagram of armature during launching process[51]
-
4 电枢损伤防护优化
-
现如今,对于枢轨载流摩擦副时空演化过程的研究采用的是追溯性模式,即对发射后的电枢进行静态分析,结合发射动力学模拟,推测实际发射过程中摩擦副的时空演化行为。
-
针对接触应力集中、电流密度集中以及热量集中等机制模拟与仿真模型,国内外研究者分别从结构防护、材料防护以及表面防护等方面进行研究,通过优化电枢自身结构和改善材料以达到减轻甚至是避免发射过程中的电枢损伤,以提高枢轨系统的效率和使用寿命。
-
4.1 结构防护
-
在结构防护方面,通过设计电枢自身结构参数及其装配结构刚度,获得更加紧密的枢轨结构和更加平整的接触界面,以此减少枢轨接触面的粗糙度和电枢尾翼部分的接触应力集中、电流集中以及热量集中,从而降低摩擦和烧蚀等损伤的出现。
-
研究者们大多以改善枢轨间的接触特性和降低电枢发生转捩烧蚀的可能性为出发点,在缩比试验和有限元三维模拟仿真中,通过调整电枢形状、长度、尾翼倾角、颈部角度等参数以及设计电枢内部结构,观察电枢在极端条件下的服役效能,以此比较出各个参数在不同匹配机制下的最佳值。GUO 等[54]在电枢脉冲电流产生的冲力特性基础上,对常见的 C 形电枢和新设计的凹形电枢分别进行仿真和试验验证,对比了两种电枢在相同电流服役环境下的力学性能,试验结果显示新设计的凹形电枢具有更好的力学性能,损伤率低。随后,以此结果探索电枢结构设计时应考虑的方面,包括机械设计、电流和热量分布、推动有效负载的机械结构优化以及质量最小化等。这对于后续研究电枢的稳定性以及防止电枢在发射过程中发生转捩和烧蚀具有一定的参考价值。
-
LIU 等[55]在分析电枢内电流和电动势的分布后,通过电磁-结构耦合的方法进行一系列的仿真分析,得到了不同长度电枢接触参数与接触效率之间的关系,并且提出了一种“反向加载”的方法设计电枢结构,如图15 所示,将传统的直线型电枢替换为弯曲型电枢,结果表明弯曲型电枢的接触效率大大提高。CHEN 等[56]研究了矩形口径轨道炮单片 C 型电枢的几个关键参数,在分析电枢质量、电枢与轨道的电磁接触力、电枢尾部机械强度和电感梯度的基础上,提出了矩形口径轨道炮单片 C 型电枢关键参数的关系,结果表明:尾翼倾角的增大可以减小电枢质量,提高电枢尾部的机械强度,但会降低电枢与导轨之间的电磁接触压力。减小电枢高度与电枢宽度之比可以显著提高电感梯度,进而提高发射系统效率。
-
图15 “反向加载”电枢结构示意图[55]
-
Fig.15 Schematic diagram of the "reverse loaded" armature structure[55]
-
LIU 等[57]在枢轨过盈配合的计算结果上建立了多物理场耦合模型,以温度和热应力等方面为出发点,提出了一种两端干涉的新型电枢结构设计,并通过试验比较,新型电枢能够在发射过程中保持较好的稳定性,大大降低了热应力对电枢发射性能的影响。TANG 等[58]通过仿真模拟,对凹弧表面 C 形电枢(ASCA)的表面弧的半径(r)和中心角(θ) 进行研究,得到了在不同电流密度下的最优值。同时,还有研究者以电枢内部结构为研究对象,设计出在电枢内部放置一个润滑物储蓄池,通过惯性作用,在发射过程中不断将润滑物质释放到枢轨接触位置,以确保在每一次发射以及在发射全过程位置上均存在此润滑物质,其发射前与发射中状态如图16 所示[59]。
-
图16 润滑物储蓄池电枢[59]
-
Fig.16 Lubricant savings pool armature[59]
-
4.2 材料防护
-
在材料防护方面,研究者以电枢所需优异性能为出发点,包括高导电性、高硬度、高导热性、高耐磨性、耐高温、抗电弧烧蚀性和质量低等,聚焦于金属材料,通过对比研究各种电枢材料在电磁交互复杂环境下的性能优劣,同时考虑与轨道材料间的匹配性,以此减少在发射过程中枢轨摩擦副的损伤。
-
ALTENHOF 等[60]对结构设计相同的铝、镁电枢进行了冲击试验和耐撞性评价,结果表明:在峰值冲击载荷近似相等的情况下,铝电枢比镁电枢具有更高的能量吸收率。HINAJE 等[61]通过比较铝、铜、钨、银、镍等 5 种材料的电枢,得出了电枢材料必须具有极高电导率和低密度的结论。付磊等[62]利用同步感应电磁推进系统,使用 MagNet 有限元软件建立了单级同步感应电磁推进装置的仿真模型,并对比分析了铝、铜、钨、银、镍等 5 种材料电枢的基本物理属性,如表1 所示[62]。可以看出,铝的电阻率为 2.655×10−8 Ω·m,密度为 2 700 kg·m−3,综合考虑高导电率和低密度两种因素下,铝质材料为最适宜的选择。因此,对铝进行合金化以加强其强度、硬度、抗烧蚀以及导电率等各方面的性能,这对于改善电枢效能具有重要意义。
-
表1 电枢制造材料[62]
-
Table1 Armature manufacturing materials[62]
-
铝合金长期以来在各大领域应用广泛,特别是飞机和航空航天,铝合金都占据着重要的地位。然而,电磁轨道发射过程中的极端服役环境对铝合金的高强度、高导电性、高硬度以及高熔点提出了更高的要求。目前,大多数方法是通过在一定程度上牺牲电导率来提高力学性能,如合金化法和复合材料法。合金化方法是通过固溶强化、析出强化、细晶强化、变形强化等手段对基体进行强化。在高强高导合金的实际生产和应用中,采用单一的强化方法往往是非常有限的,多种强化方式相结合是主流趋势。复合方法是通过添加第二相颗粒、晶须以及纤维来增强铝基体。高强度铝合金是以 Al-Zn-Mg-Cu 系为主的合金。自 20 世纪 30 年代以来,全球许多国家对 Al-Zn-Mg-Cu 系合金进行了大量的研究。发展至 20 世纪 80 年代,随着快速凝固/ 粉末冶金(RS/PM)工艺的愈发成熟,成功制备出抗拉强度达 700 MPa 以上的 7 系超高强合金,这将 Al-Zn-Mg-Cu 系合金推向了一个更高的水平[63-64]。至今,各国开发出的 Al-Zn-Mg-Cu 系高强合金牌号达几十种,部分合金成分如表2 所示[63]。其主要的颗粒相为 η-MgZn2、T-Al2Zn3Mg2。LIN 等[65]通过 Johnson-cook 材料模型,在多物理场耦合模型中比较了 7075 铝合金和 6061 铝合金在不同电流下的失效时间,如图17 所示,可以看出,7075 铝合金具有更高的载流能力,表明其具有更高的屈服强度。同时相关试验指出,6 系铝合金具有更高的韧性,在发射出口处得到的电枢不破碎,结构完整性的保持效果更佳。在后续电枢材料的研究中,针对 6 系和 7 系铝合金的选择上还有待进一步研究。
-
表2 Al-Zn-Mg-Cu 系高强合金成分表(质量分数/%)[63]
-
Table2 Composition table of Al-Zn-Mg-Cu high-strength alloys (wt.%) [63]
-
通过对 Al-Zn-Mg-Cu 系铝合金进行合金化以达到增强其各方面物理性能的目的,这对于保障电磁轨道发射过程的完整性和可靠性起到了极大的积极作用。值得注意的是,由于铝自身低熔点和高化学反应活性的属性,在发射过程中电枢不可避免地会发生熔化摩擦磨损,进而使得枢轨间产生材料转移,在轨道表面形成铝熔凝沉积层[66-67],即轨道黏铝问题,如图18 所示。一方面,电枢在发射过程中,其表层材料发生熔化,于铜轨道表面形成液态润滑层。这会使得枢轨接触由完全的“固-固”接触在短时间内转换为“固-液-固”接触。该接触方式在一定程度上能降低电枢与轨道间的粗糙度,有利于减少枢轨系统运动过程中的摩擦损伤;另一方面,在轨道冷却的作用下,电枢熔化物会与轨道发生机械结合和化学结合,在轨道表面出现机械黏着物和化合物,例如铝合金、Al2O3 等,使得轨道表面产生大量的微凸起硬质颗粒,恶化枢轨接触效果导致磨粒磨损增加,降低了枢轨发射系统的精确性和使用寿命。同时,这也会影响脉冲输出电流的持续性和稳定性,导致电枢的出口速度不能达到预期效果,此影响会随着发射次数增加而导致的沉积层累积厚度增加而越来越显著。因此,轨道表面铝熔凝沉积层对枢轨摩擦副的影响具有双面性,二者存在竞争关系。在后续电枢材料的选择中,如何平衡二者的影响效果,减小枢轨接触面间隙,优化接触状态以提高电磁轨道发射系统的效率也是研究重点之一。
-
图17 电枢在不同电流下的失效时间[65]
-
Fig.17 Failure time of armature at different currents[65]
-
图18 轨道表面铝熔凝沉积层
-
Fig.18 Aluminum fusion deposits on the surface of the rail
-
4.3 表面防护
-
在表面防护方面,不同研究者在明晰电枢表面性质的基础上,根据所需改善电枢的不同物理性能,采取不同的表面强化技术制备了贴合度较高的不同材质表面涂层。DROBYSHEVSKI 等[68]在枢轨接触界面注入一层液体,在考虑了速度趋肤效应、能量耗散以及热传导等因素,研究了液态涂层对枢轨间滑动电接触性能的影响,结果表明:液态涂层可以显著抑制速度趋肤效应,减少接触界面的焦耳热和摩擦热,但对于如何保持液态涂层的完整性和防止流失方面的研究不够深入。
-
同时,在表面涂层的设计过程中,还应避免涂层材料在发射过程中因摩擦和熔化而丢失过快造成枢轨间的接触不良。GHASSENMI 等[69]采用了一种新型的电枢设计,将具有良好导电性的铟液膜添加到电枢表面,研究了该涂层对枢轨界面间热感应及磁感应分布的影响,结果表明:使用液态铟涂层不仅提高了枢轨界面间的导电性,还减少了摩擦并迟缓了电枢的熔化。LI 等[70]从材料熔点和硬度的角度出发,提出钨可以作为电枢表面的涂层材料,设计了涂层的形状和厚度,通过计算涂层与基体之间的剪切力,确定最佳涂层成形工艺,并分析了涂层对电接触性能、系统效率和弹丸刨削阈值速度的影响,结果表明:涂层与基体之间的最大剪切力在 171 MPa 以上,激光熔覆技术可以满足工艺要求,涂层处理后,枢轨间的接触电阻增加了 6%。
-
陈建伟等[71]利用锡合金的高导热性、低膨胀系数和高导电性等优点,制备了锡合金导电镀层,并计算了镀层电枢/轨道的接触电阻,分析了锡合金在电流作用下的特性以及对电枢运动特性的影响,结果表明:锡合金镀层电枢较普通 U 型电枢的炮口速度提高大约 15%。杜传通等[72]制备了一层石墨烯涂层在电枢表面,并进行了相关理论分析和仿真研究,结果表明:石墨烯涂层不仅能改善枢轨界面间的电接触状态,在提高电枢速度、减少界面间热量产生等方面具有一定的积极影响。如图19 所示是普通电枢与添加石墨烯涂层后电枢的发射试验对比,可以看出石墨烯涂层具有抗电弧烧蚀和润滑的作用。 LIU 等[73]从复合涂层材料的角度出发,以 Cu 作为硬底材、Sn-GE 作为软导电润滑膜,在电枢用铝合金表面制备了一层复合涂层,并通过载流试验检测其各项性能,结果表明:该复合涂层在降低摩擦因数和减少电弧烧蚀等方面均有一定帮助。
-
图19 电枢发射试验前后对比[71]
-
Fig.19 Before and after armature emission experiment[71]
-
综合以上研究者的研究成果,可以看出,满足枢轨载流摩擦副材料应用化需求的电枢表面涂层应具有以下性能:
-
(1)具有良好的导电性和较高的熔点,以减少接触界面产生的焦耳热导致的电枢熔化。
-
(2)具有较高的硬度,以减少电枢表面的机械磨损。
-
(3)在设计表面涂层的形状和制备方法等因素时,应综合考虑磨损情况以及枢轨间的抗剪切强度,防止在发射过程中涂层因摩擦等不利因素而导致脱落。
-
(4)涂层材料与电枢表面之间应具有较大的亲和力。
-
(5)对于复合涂层材料,应从“硬底材-软导电润滑膜”结合模式综合考虑,以此保证涂层兼具硬度高、润滑性、高导电等性能。
-
对于表面涂层的制备,现阶段常用的方法为:电镀、化学镀、真空镀、粉末喷涂、磁控溅射、激光熔覆等。其中,激光熔覆技术冷却速度快、涂层稀释率低、热输入和畸变较小、熔覆层的厚度范围大,是一种应用前景广阔的表面处理技术。目前,相关铝合金电枢涂层的制备工艺、应用条件及微观机理的研究不够成熟,特别是在发射过程的极端工况服役环境下,存在各种物理量耦合场,表面涂层的各项抗冲击性能和其他物理性能能否达标的相关检测试验仍然缺乏系统性的指导。
-
5 结论与展望
-
从国内外研究者对电磁轨道发射用电枢损伤的研究进展可以发现,针对电枢载流摩擦磨损、热熔化以及转捩烧蚀等典型损伤,已构建相应的规律体系和理论分析体系,并结合分析模型做出了对应的防护优化,取得了较好的试验和仿真效果。但对于电枢损伤的形貌演变规律、仿真复现手段以及与轨道损伤特征的对应关系等的研究还不够深入。主要原因如下:
-
(1)受限于当前的技术手段,对电枢和轨道的损伤探究都是基于发射后的结果进行。而电枢损伤是单次发射后产生的结果,轨道损伤是多次发射后累积产生的结果,这导致电枢与轨道的分析对象不匹配,所得到的表面损伤机制不具有统一性和相关性。
-
(2)电磁轨道发射过程中,枢轨接触界面各项性能参数是否变化以及变化趋势的数据实时显现手段尚不完备,这导致枢轨载流摩擦副的损伤对发射性能的影响难以量化。
-
(3)电磁轨道发射装置处于电-磁-热-力极端工况下,电枢与轨道间的材料转移不可避免,转移过程受到枢轨载流摩擦副损伤的严重影响。而针对损伤与枢轨间结构变化目前没有准确高效的三维重构模型以说明两者间本征关系。
-
对于上述难点和问题,依据电磁轨道发射相关技术要求,未来电枢损伤的研究应着力于以下几个方面:
-
(1)理清电磁发射极端工况下各物理量场的深度耦合关系,追溯发射过程中电枢形貌演变规律。
-
(2)明晰电磁轨道发射行为的关键物理量及其影响机制,包括接触电阻、摩擦因数等,探索发射过程中枢轨间接触状态的变化。
-
(3)构建电磁轨道发射苛刻工况三维分析模型,研究仿真复现技术,探明处于电-磁-热-力多场耦合下枢轨材料的物性演化。
-
(4)现有防护优化手段尚不能满足极端服役环境下的结构和性能保持需求。开展新型枢轨材料及其结构的研发是未来的研究重点之一。
免责声明:本网站所转载的文字、图片与视频资料版权归原创作者所有,如果涉及侵权,请第一时间联系本网删除。
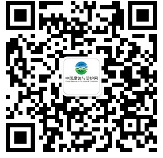
官方微信
《腐蚀与防护网电子期刊》征订启事
- 投稿联系:编辑部
- 电话:010-62316606
- 邮箱:fsfhzy666@163.com
- 腐蚀与防护网官方QQ群:140808414