-
0 前言
-
热障涂层(Thermal barrier coatings,TBCs)是一种将陶瓷材料涂覆在合金基体表面,保障动力装备的热端部件可靠运行的功能隔热涂层,具有耐高温、低热导率和耐腐蚀等优点[1]。以航空发动机为例,推重比 10 级的航空发动机涡轮前端的温度已经超过 1 800 K,而涡轮叶片的镍基高温合金只能承受 1 373 K 的高温。为了保障发动机能够长期可靠的工作,过去通过在涡轮叶片内部开设导气通道的方法来降低叶片的基体温度[2-3]。但是随着航空发动机朝着高推重比方向发展,涡轮前进气口的温度不断增加,即使采用先进的冷却技术也无法解决镍基高温合金熔点远低于环境温度的问题[4]。为了降低叶片基体温度,延长发动机的使用寿命,美国国家航空航天局于 20 世纪 50 年代提出了热障涂层的概念。
-
传统的热障涂层体系如图1 所示,其结构主要包括 4 个部分:直接与高温环境接触的顶部涂层 (TC)、因氧化反应生成的 TGO 层、金属粘结层(BC) 和高温合金基体。目前,应用最成熟的 TC 材料是 YSZ,粘结层采用 MCrAlY 合金。在 1 200℃以上的高温或超高温环境,这类涂层在服役过程中长期受到热循环作用,会导致涂层分层和剥落,降低涂层的使用寿命。因此,充分了解热障涂层的失效机制,对延长 TBCs 寿命的研究至关重要。选择低热导率、良好高温相稳定和断裂韧性的新型材料,可以显著提高 TBCs 的隔热性能和使用寿命。先进的 TBCs 结构设计,可以有效缓解各层之间的热膨胀系数差、减小涂层内部应力、增加涂层在热循环下的使用寿命。本文主要综述了热障涂层几种典型的失效机制、近年来新型顶部涂层材料和先进涂层结构设计的研究进展。对热障涂层超高温环境应用进行了展望。
-
图1 TBCs 的多层功能示意图[5]
-
Fig.1 Multilayer Functional Schematic of TBCs[5]
-
1 影响热障涂层失效的原因
-
热障涂层常用于极端工况下,涂层的热物理性能和力学性能在高温或超高温环境中会显著下降。此外,动力装置在实际工作过程中会摄入各种环境污染物,这些污染物随着温度的升高而熔融沉淀在热障涂层表面,从而造成侵蚀。残余应力、高温烧结、CMAS 腐蚀、氧化层(TGO)生长是造成热障涂层剥落与开裂失效的重要因素[6],如图2 所示。本章总结了残余应力、高温烧结、CMAS 腐蚀、氧化层(TGO)生长这四种影响热障涂层寿命的主要因素。对涂层的层间界面失效、TGO 形成和生长、涂层氧化、裂纹萌生和扩展等失效机制进行了分析。
-
图2 热障涂层的主要失效模式及其影响因素[6]
-
Fig.2 Main failure modes and influencing factors of thermal barrier coatings[6]
-
1.1 残余应力
-
残余应力为多种原因引起的未能释放的应力的统称,是导致涂层失效的主要因素。残余应力主要包括淬火应力、热失配应力和相变应力,其中涂层制备过程中产生的相变应力较小,可忽略不计。本节主要总结了残余应力的产生原因、计算方法以及对涂层开裂分层失效的作用过程。
-
1.1.1 淬火应力
-
热障涂层的制备过程中,涂层材料被加热到熔融或半熔融状态。在沉积到粘结层与基体上时,由于基体温度远低于涂层材料的制备温度,涂层材料沉积到基底会快速冷却,导致熔融物心部和基体的底部体积胀缩不均匀,从而产生淬火应力。淬火应力的计算公式为[7]:
-
式中,Tm 是热障涂层材料的熔点;Ts 是基体温度; Ec 是涂层的弹性模量; ac 是涂层的热膨胀系数。由于涂层中存在裂纹和孔隙,实际的淬火应力往往会小于计算值。
-
KURODA 等[8]研究了等离子喷涂过程中涂层的材料属性对残余应力的影响,最早发现了熔融或半熔融态的涂层粉末遇到低温基体会产生淬火应力。在涂层沉积过程中,淬火应力对整个制备过程的残余应力影响较小;但在整体冷却阶段,对产生的残余应力占比影响较大[9]。PINA 等[10]通过 X 射线衍射(XRD)的方法来测试涂层的淬火应力,发现淬火应力的大小只与涂层和基体的温度差有关,与涂层厚度、基体和粘结层材料无关。为了对 TBCs 的淬火应力和损伤状况进行有效预测和评估,一些学者采用基于图像处理的有限元方法[11-12]。但是,该方法未分析沉积应力的影响[13-14]。此外,对多个微结构图像进行噪声清除和网格重建十分繁琐,使得该方案难以应用[15-16]。近年来,针对上述问题,学者们提出了混合计算的方法,采用光滑粒子流体动力学(SPH)建立了喷雾模型,替代了先前难以处理的微结构图像。并且,通过钻孔试验证明了该方法能够更有效预测涂层的微观结构缺陷(如孔隙,界面和裂纹)和淬火应力[17]。
-
1.1.2 热失配应力
-
除淬火应力外,热失配应力对热障涂层的影响也不容忽视。热障涂层中顶部涂层材料的热膨胀系数最小,其次是粘结层材料,基体材料的热膨胀系数最大。由于热障涂层各层的热膨胀系数存在差异,在热循环过程中热障涂层会产生热失配应力,该应力会导致涂层内部裂纹扩展,从而造成涂层分层。在涂层的制备过程中,淬火应力是在从顶部涂层材料的熔点到沉积温度(基体顶面温度)的温度范围内产生的,而热失配应力是在从沉积温度到室温的温度范围中产生的。热失配应力的数学式为[7]:
-
式中, Δα 是热障涂层材料和基体材料的热膨胀系数差;v 是涂层的泊松比。
-
KARABAS 等[18]研究了由非晶态 La2Zr2O7 (LZA)和晶态 La2Zr2O7(LZC)原料制备的 La2Zr2O7 (LZ)单层热障涂层和 YSZ / LZ 双层热障涂层。三种涂层横截面的显微照片如图3 所示。LZC 的孔隙率高于 LZA,由于较高的孔隙率可以缓解涂层的热失配应力,LZA,LZC 和 YSZ / LZC 双层 TBC 分别在 67、86 和 400 次热循环后发生剥落,剥落后的涂层样品如图4 所示。此外,YSZ / LZC 双层 TBC 的耐烧结性较高,且陶瓷层和金属层之间的热膨胀系数差较小,因此 YSZ / LZC 双层 TBC 的热循环寿命高于 LZA,LZC 单层涂层。LIU 等[19]对高温环境下 LaZrCeO / YSZ 涂层在熔融 NaCl 中的腐蚀反应进行了研究,发现顶部涂层与粘结层由于较大的热膨胀系数差而产生热失配应力,这是造成涂层损伤的主要原因。考虑热失配应力对裂纹萌生和扩展的影响, RANJBAR-FAR 等[20]和 KRISHNASAMY 等[21]分别建立了堆叠扁平颗粒模型和宏观-微观积分模型来研究涂层界面裂纹和裂纹扩展行为。结果表明,基体的热失配应力是导致冷却过程中涂层边缘裂纹萌生和扩展的关键因素。
-
图3 涂层的横截面显微照片[18]
-
Fig.3 Cross-sectional photomicrographs of coatings[18]
-
图4 热循环试验后的 TBCs 样品照片[18]
-
Fig.4 Photos of TBCs samples after thermal cycling test [18]
-
基于上述研究可知,层间热膨胀系数差会导致涂层内部产生热失配应力,从而严重影响涂层的使用寿命。主要有两种方法来提高涂层的抗剥落性和抗裂性,一种方法是通过释放应力的方法来缓解涂层内部应力,例如增大涂层内部的孔隙率、用以裂止裂的方法在涂层内部制备的垂直裂纹来释放热失配应力;另一种方法是选取热膨胀系数接近基底的新型陶瓷材料,从而缓解涂层与基体的热膨胀系数差。这两个方面在未来还需要更多研究。
-
1.2 烧结效应
-
热障涂层内部往往具有孔隙,在高温工况下陶瓷顶部涂层不可避免的会产生烧结现象。随着烧结的进行,多孔的顶部涂层会逐渐致密化。一方面会引起涂层的热膨胀系数降低,进一步增加热失配应力;另一方面会降低涂层的应变容限,引起界面应力的增加。较差的应变容限会导致烧结应力的产生,从而造成顶部涂层的开裂和剥落。此外,烧结效应会导致涂层弹性模量增加,引起涂层内部应力增加。
-
LIU 等[22]研究了 La2Ce2O7 / 8YSZ 双陶瓷层热障涂层在极端温度梯度下的抗热震性和失效机理。结果表明,高温热应力对涂层有很大影响,La2Ce2O7 陶瓷层的烧结会产生很大的烧结应力,这是 La2Ce2O7 / 8YSZ 热障涂层失效的主要原因,并且温度越高,La2Ce2O7 层的烧结过程越快。李太江等[23] 采用等离子喷涂法制备氧化钇稳定氧化锆(YSZ)涂层,并对其进行 1 000、1 100、1 200 和 1 300℃高温烧结试验,研究其高温烧结过程中的微观结构及热导率演变规律。结果如图5 所示,同一温度的条件下,孔隙率随热接触时间的增加而减小;同一时间的条件下,孔隙率随温度的增加而减小。 LAVASANI等[24]采用大气等离子喷涂法制备了喷涂参数不同的 8YSZ 涂层,研究了烧结对涂层微观结构、孔隙率和抗热震性的影响。结果表明,喷涂参数会改变涂层的基本特性、孔隙率和裂纹的数量和大小,并且较大的孔隙率和裂纹百分比、较小的孔隙尺寸和裂纹尺寸会导致更高的烧结率。在陶瓷基体内掺杂金属氧化物可以有效解决涂层的烧结问题。例如,采用固相反应烧结法在 YSZ 涂层内掺杂质量分数为 7.5%的 TiO2 可以调整内部孔隙结构,但存在严重的气孔愈合现象,减小了应变容限[25]。而按一定比例掺杂 CeO2和 Sc2O3 在烧结过程中,涂层内部其他位置处的晶界消失之后,孔隙仍然保留并且存在于晶粒内部,有效降低了涂层的烧结致密化程度[26]。
-
图5 YSZ涂层在不同温度热处理不同时间的表观孔隙率[23]
-
Fig.5 Apparent porosity of YSZ coating at different temperatures and heat treatment times[23]
-
烧结应力是导致热障涂层失效的驱动力之一,环境温度越高,烧结过程越快。高温环境中,涂层材料的烧结会导致涂层内部的孔隙和裂纹愈合,涂层表层发生明显硬化[27]。涂层内部的孔隙决定了其应变容限,孔隙和裂纹的愈合将减小涂层的应变容限,导致涂层产生较大的烧结应力。为了延长涂层的寿命,一方面可通过在涂层基体中掺杂金属氧化物来调整内部孔隙结构,改善涂层的抗烧结性;另一方面,可以设计具有孔隙率梯度的先进涂层来提高涂层的应变容限,如具有纳米分区结构的涂层。
-
1.3 钙-镁-铝-硅酸盐(CMAS)渗透腐蚀
-
除了应力导致的热障涂层失效,熔融沉淀物腐蚀也是使热障涂层失效的一个重要原因。在实际工况下,航空发动机会摄入大量沙尘、火山灰、跑道碎屑以及各种环境污染物,这些污染物在高温下附着于发动机热端部件(如涡轮叶片、燃烧室壁等) 形成沉积物。沉积物的成分主要为 CaO、MgO、 Al2O3 和 SiO2,简称 CMAS[28]。CMAS 对热障涂层的渗透过程如图6 所示,其中图6a 为没有沉积 CMAS 的热障涂层;随着飞机发动机在高温环境中运行,热障涂层开始发生变化,CMAS 逐渐沉积在热障涂层表面上如图6b 所示;当环境温度升高到 CMAS 的熔点温度(高于 1 200℃)时,固体 CMAS 沉积物转变为液态,从而渗透到顶部涂层的孔隙与裂缝中,如图6c 所示[29]。在航空发动机的热-冷循环过程中,CMAS 的熔融和固化会导致涂层的应变容限降低,从而产生较大的应力而导致涂层的开裂与剥落,降低涂层寿命。
-
图6 CMAS 对热障涂层的渗透过程[29]
-
Fig.6 Penetration process of CMAS on thermal barrier coatings[29]
-
LI 等[30]采用放电等离子烧结法(SPS)制备了钇稳定氧化锆涂层,对涂层在 CMAS 攻击下的演变过程进行了研究。发现 CMAS 腐蚀对应力场(如峰值应力)具有显著影响。应力峰值随着保温时间的增加而增加,最后导致热障涂层的脆性断裂。此外,体积应变是导致CMAS腐蚀在过程中应力增加和集中的主要原因。SHAN 等[31]研究了 YSZ 涂层在 CMAS 渗透腐蚀下的屈曲现象,指出液态的 CMAS 由于毛细力的作用渗透到顶部涂层,导致顶部涂层体积膨胀。在高温环境中,涂层发生大规模屈曲变形,使涂层由于较大应力剥落。GUO 等[32]对未抛光和抛光状态下的块状 YSZ、GdPO4 和 LaPO4 涂层试样进行了研究。与未抛光的样品相比,抛光样品上的熔融 CMAS 具有较低的润湿性和较小的铺展面积,由此认为降低表面粗糙度有利于提高 TBCs 的 CMAS 耐腐蚀性。KUMAR 等[33]研究了 CMAS 黏度和涂层微观结构对 CMAS 渗透深度的影响。结果表明,低黏度的 CMAS 容易渗透 TBCs,并且具有垂直裂纹和水平带状孔隙的涂层结构的样品,与其他样品相比,渗透深度更低。MORELLI 等[34]研究了四种不同热喷涂工艺制备出的等离子喷涂涂层在 CMAS 侵蚀下的腐蚀降解过程,测试的 YSZ 涂层样品包括:标准化学纯度的 YSZ 原料粉末大气等离子喷涂(APS)涂层;高化学纯度的 YSZ 原料粉末 APS 涂层;致密垂直裂纹结构(DVC)的大气等离子喷涂涂层;悬浮等离子喷涂(SPS)涂层。结果表明,当比较两个具有相似微观结构的传统 APS 涂层样品时,化学纯度较低的样品发生了更严重的腐蚀降解;DVC 涂层的主要问题是大量的 CMAS 渗透到裂缝中,在冷却过程中对涂层造成了冷冲击。此外,SPS 涂层发生了最严重的腐蚀降解。当 TC\BC 界面被 CMAS 侵蚀时会出现界面高温分层现象。目前,通过制备致密覆盖层或采用原位自生的制备方法,可以抵抗 CMAS 渗透。使用稀土锆酸盐材料制备涂层,可在陶瓷层顶部形成致密层,该致密层由结晶磷灰石结晶组成[35]。采用原位自生方法制备 LCO(La2Ce2O7)的双层 TBC,由于 CMAS 和 LCO 在高温状态下发生反应,可以形成由钙长石、尖晶石和 La2Si2O7 组成的致密保护层,能够有效抑制 CMAS 的渗透[36]。
-
上述研究表明,CMAS 腐蚀会使涂层发生体积应变,从而导致涂层内部应力集中,这是涂层失效的主要原因。此外,CMAS 侵蚀会导致涂层屈曲变形,从而引起界面应力增加,导致涂层剥落。并且涂层的表面粗糙度、环境中的 CMAS 黏度、涂层原料的化学纯度和热喷涂工艺会影响热障涂层的寿命。通过制备致密覆盖层或采用原位自生的制备方法可以提高涂层的抗侵蚀性,但该方法还须要进一步研究。
-
1.4 TGO 失效
-
1.4.1 TGO 形成与生长
-
TBCs 中的 BC 层通常由 MCrAlY 合金(M 主要有 Fe、Ni、Co 以及 Ni 和 Co 共掺等几种选择) 制成。在高温环境下,氧气从 TC 层扩散到 BC 层时会形成 TGO 层,并沿着 TC 和 BC 的界面生长[37]。初始的氧化物可以保护基体不被进一步氧化,但当 TGO 生长到临界厚度(通常为 5~10 μm),TGO 中逐渐积累的最大应变能会使 TGO 或 TGO 层附近产生裂纹导致 TBCs 失效,因此延缓高温环境中 TGO 的生长速率对延长 TBCs 的寿命非常重要。根据传统的 Wagner 氧化理论(抛物线定律),TGO 的增长率可以表示为:
-
式中,δ 是 TGO 厚度, k 是速率常数,t 是氧化时间。TGO 厚度的增长率在较短的氧化时间满足抛物线定律,但是随着氧化时间的增加,增长率会逐渐偏离抛物线定律。因此,ZHANG 等[38]研究了低压等离子喷涂 MCrAlY 粘结涂层的非抛物线等温氧化动力学,并修正了传统的抛物线定律,如式(4)。
-
修正后的模型与试验结果相一致,如图7 所示。 TGO 层主要是由 a-Al2O3 和其他混合氧化物所组成,其中氧化初期会形成的 Al2O3层。但随着环境温度升高和涂层氧化时间增加,其他混合氧化物会快速生长,使 TGO 层体积膨胀从而产生较大的应力。有学者提出,由于 Al2O3层具有优异的高温稳定性,并且氧和金属离子的扩散系数较低,在沉积顶部涂层之前,在低氧分压下对粘结涂层进行适当的预处理是降低 TGO 生长速率和抑制混合氧化物生长的有效方法[39]。根据上述观点,MENG 等[40]利用空气等离子喷涂法和可控气氛热处理制备了有 a-Al2O3 的 TGO 的涂层,分析了粘结涂层界面微观结构的变化对 TGO 生长的影响。指出非热处理粘结涂层的氧化速率常数为 0.26μm/h1/2,而热处理粘结层的氧化速率常量为 0.14μm/h1/2。由于晶界扩散会影响 TGO 的生长,因此可以通过增大晶粒尺寸来降低其生长速率[40-42]。在制备涂层时使用可控气氛处理,预先在粘结层表面制备一层具有大尺寸晶粒的 TGO 层[43]。通过调节热处理过程的氧压,控制 MCrAlY 粘结层表面保持氧化膜形态,可以制备平均晶粒尺寸高达 1 μm 的 TGO 层。如图8 所示,在热循环过程中,TGO 层的较大晶粒尺寸显著抑制了 TGO 的生长率[44]。
-
图7 改进模型理论值与试验值的比较[38]
-
Fig.7 Comparison between theoretical and experimental values of the improved model[38]
-
高温环境中 TGO 的生长会导致 TGO 层的厚度增加,TGO 层附近会产生较大的应力,从而导致涂层产生裂纹和剥落,缩短 TBCs 的使用寿命。为了延长 TBCs 的使用寿命,可以对粘结层进行特殊的预处理,预先制备具有大尺寸晶粒的 TGO 层来减缓 TGO 的生长速率。目前对高温环境下 TGO 生长速率模型还须不断改进,对粘结层预处理的方法还缺少深入研究。
-
图8 热处理后粘结层和普通粘结涂层的增长率比较[40]
-
Fig.8 Comparison between the growth rate of the heattreated bond coat and the as-sprayed bond coat[40]
-
1.4.2 TGO 生长诱发的应力
-
热氧化物的生长会导致 TGO 层的厚度增加。在高温环境中,超过临界值的 TGO 厚度是衡量导致 TBC 剥落的失效机制之一。除此之外,BC 系统中的 TGO 生长会导致 TGO / BC 或 TC / TGO 界面之间的热膨胀失配,进而导致热障涂层的失效。
-
ABDELGAWAD 等[45]建立了一个有限元模型研究 TGO 厚度对 TBCs 损伤的影响,结果如图9 所示,TBC 的裂纹长度随着 TGO 整体厚度的增加而增加。DONG 等[46]通过控制冷喷涂 MCrAlY 粘结涂层的等温氧化时间,制备了不同 TGO 的 TBCs,并对具有不同 TGO 厚度的 TBCs 进行了梯度热循环试验。结果表明,存在临界 TGO 厚度 6.01 μm,在小于该临界厚度的范围内,热循环寿命随着 TGO 厚度的增加而显著降低,结果图10 所示。WEI 等[47]建立了含有非均匀 TGO 的 TBCs 有限元模型,探讨了 TGO 的非均匀特征对局部应力状态和开裂分层行为的影响。结果表明,氧化物的不均匀生长会导致 TGO 层局部厚度增加,与均匀的 TGO 相比,8 μm 非均匀 TGO 模型的裂纹驱动力增加了 30%,并且随着不均匀度的增加,裂纹长度也会逐渐增加。
-
上述研究表明,TGO 厚度的增加会导致涂层的开裂分层,并且均匀度低的 TGO 层会导致局部氧化层厚度增加,因此减缓 TGO 层厚度的增长速率及通过工艺优化来提高 TGO 层的均匀度,是延长 TBCs 使用寿命的关键措施。
-
图9 不同冷却时间下 TBC 的裂纹长度[45]
-
Fig.9 Crack length of TBC under different cooling times[45]
-
图10 具有不同厚度 TGO 的 TBC 在失效后的宏观形貌[46]
-
Fig.10 Macromorphology of TBC with different thicknesses of TGO after failure[46]
-
2 热障涂层陶瓷层材料
-
2.1 传统钇稳定氧化锆(YSZ)
-
氧化锆通常处于三种不同的状态,分别为单斜晶、四方晶和立方晶。在加热过程中,纯氧化锆会在 1 170℃左右发生从单斜晶相到四方晶相的转变,陶瓷晶体内部结构变化会导致陶瓷的体积变化,这种变化会引起陶瓷内应力的升高,从而生成裂纹。为了防止上述情况的发生,可以添加具有稳定性的氧化物(如 MgO、CaO、Y2O3)。其中 Y2O3 为常用的稳定剂,质量分数为 6%~8%的氧化钇稳定氧化锆的柱状微观结构提供了优异的应变容限和对涂层的附着力,并且它还具有良好的耐 Na2SO4 和 V2O5 的腐蚀性,因此成为目前应用广泛的热障涂层材料。然而 YSZ 在高温下也易发生相变,当温度高于 1 200℃时,非稳态四方相(t')会转变为四方相(t) 和立方相(c)的混合物,冷却过程中四方相又转变为单斜相(m),此过程会发生体积膨胀,产生裂纹,导致热障涂层系统的失效[48]。除了相变,严重的烧结收缩也对 TBCs 的性能造成不利影响,会使 TBCs 产生较大的应力,热循环载荷下的寿命降低。
-
由于 YSZ 在高温下的力学性能较差,寻找替代 YSZ 的新型 TBC 材料就显得格外重要。新型 TBC 材料与 YSZ 相比应该具有更低的热导率,更高的热膨胀系数,以及具有良好的高温相稳定性。针对超高温和极端工况,稀土掺杂氧化锆、A2B2O7 型化合物、稀土钽酸盐和自愈合材料受到了广泛关注。
-
2.2 几种新型涂层材料
-
2.2.1 多元稀土氧化物稳定氧化锆
-
尽管 YSZ 具有优异的物理性能,但在高温环境中依然会有不稳定性。以 Ta2O5、Yb2O3、Gd2O3和 Sc2O3 等多元稀土氧化物共掺杂的 YSZ 涂层可以提高相稳定性,成为 YSZ 材料的替补材料。CHEN 等[49]的研究表明,试验测得的掺杂 Ta2O5-Y2O3的 ZrO2 (TYSZ)涂层的导热系数为 1.8~2.0 W·m−1 ·K−1,比 YSZ 涂层的导热系数(2.0~2.3 W·m−1 ·K−1) 低约 20%,试验结果如图11 所示,其原因是 Ta2O5 的掺杂会诱导晶格畸变,晶格畸变的存在增加了声子散射,从而导致低热导率。 SONG 等 [50]对 Yb2O3-Gd2O3-Y2O3 共掺杂 ZrO2(YGYZ)涂层在 Na2SO4和V2O5熔盐环境的热腐蚀行为进行了研究,结果表明 YGYZ 涂层具有很好的耐腐蚀性与相稳定性,在腐蚀 20 h 后涂层仍保留较高的四方相,并且降解的涂层比 YSZ 涂层少 40%。LIU 等[51]研究了 8 mol.%Sc2O3,0.6 mol.%Y2O3稳定的 ZrO2 (ScYSZ)涂层的相稳定性和烧结行为。在 1 500℃ 下热处理 10 h 后,ScYSZ 涂层仍为单一的不可转变四方相,但 YSZ 涂层中单斜相的含量达到 49.4 mol.%,ScYSZ 涂层表现出更加优异的高温稳定性。温度从 1 000℃升高到 1 500℃,ScYSZ 涂层比 YSZ 涂层具有更优异的抗烧结性,因此涂层表面更光滑,如图12 所示,且提高抗烧结性能降低材料的热导率,从室温到 700℃,ScYSZ 涂层的热导率为 2.22~2.1 W·m−1 ·K−1,YSZ 涂层的热导率为 1.21~1.04 W·m−1 ·K−1。
-
图11 TYSZ 和 YSZ 的热导率与温度变化曲线[49]
-
Fig.11 Thermal conductivities versus temperature curves of TYSZ and YSZ bulks[49]
-
图12 试样在 1 500℃烧结 10 h 后的 SEM 显微照片[51]
-
Fig.12 SEM micrographs of the specimen after sintering at 1 500℃ for 10 h[51]
-
近年来学者们研制了不同的氧化物稳定氧化锆涂层来解决 YSZ 涂层遇到的问题。从抗烧结性、低热导率、高温稳定性这三个角度来分析,该涂层材料具有卓越的物理性能,但从氧化物掺杂含量、涂层的制备、氧化物掺杂机理对涂层性能影响的方面来考虑,还需要更加深入的研究。
-
2.2.2 A2B2O7 型化合物
-
在新型 TBC 材料研究中,除了一些对氧化物稳定氧化锆涂层的研究,还探索了一些新的涂层材料。 A2B2O7(A 为稀土元素,B 为四价元素,如 Zr,Ce 等)化合物根据氧空位的顺序分为烧绿石结构(被视为有序缺陷萤石结构)和萤石结构[52]。A2B2O7 型氧化物具有高熔点,并且熔点以下无相变,因此具有良好的高温稳定性。A2B2O7 型氧化物具有复杂的晶体结构,晶体内部具有高浓度的氧空位和质量更大的稀土原子,会降低平均声子的自由程,从而降低热导率。目前对 A2B2O7 化合物的研究主要集中在 A2Zr2O7和 A2Ce2O7类型的材料上。BOBZIN 等[53] 分析了La2Zr2O7和YSZ在1 000~1 300℃的高温环境下的热导率,结果表明,随着温度的升高,两种材料的热导率均升高,但在某一温度下 La2Zr2O7 的热导率(0.87~1.24 W·m−1 ·K−1)显著低于 YSZ 的热导率(1.83~1.59 W·m−1 ·K−1)。王衍飞等[54] 研究了 La2Zr2O7 涂层在高温长时间条件下的物相组成与微观结构,结果表明,随着热处理时间的增加,La2Zr2O7 涂层始终为单一绿烧石结构,表明高温暴露对 La2Zr2O7 的晶体结构影响不大,因此不会导致膨胀失效,具有良好的高温相稳定性。虽然 La2Zr2O7 涂层具有优异的高温性能,但相对较低的热膨胀系数以及较差的断裂韧性,使其无法作为顶部陶瓷层直接制备在粘结层上[55]。因此,如何通过采用材料掺杂、结构设计的方法来改善涂层和粘结层之间膨胀系数的匹配、提高断裂韧性、延长涂层的使用寿命还需要进一步研究。
-
除了 A2Zr2O7 化合物,很多学者发现 A2Ce2O7 化合物也具有的较低的热导率、较高的热膨胀系数以及优异的高温相稳定性,由此成为制备热障涂层的候选材料之一。与 A2Zr2O7 化合物不同,A2Ce2O7 化合物一般以萤石结构为主。俞显芳等[56]研究了 Dy2Ce2O7 和 Y2Ce2O7陶瓷材料的相组成、微观组织和热导率。试验结果表明,在 800℃的工作环境下, Dy2Ce2O7 的热导率为 1.78 W·m−1 ·K−1,Y2Ce2O7 的热导率为 1.82 W·m−1 ·K−1,均低于 YSZ 的热导率(2.15 W·m−1 ·K−1)。XU 等[57]通过固态反应的方法合成了一类高熵萤石型氧化物,并研究了它们的热膨胀系数、热导率、抗烧结性和相稳定性。如表1 所示,室温下氧化物具有很低的热导率,远远低于 La2Ce2O7 的热导率和 YSZ 的热导率,并且这类氧化物同样具有优异的抗烧结性和高温相稳定性,由于这些优异的物理性质,可以作为热障涂层材料的候选。尽管 A2Ce2O7 化合物有很多优异的性能,但如何制备具有额定化学计量比的 A2Ce2O7 化合物仍是一大难题。
-
表1 室温下高熵氧化物的热导率[57]
-
Table1 Thermal conductivity of high entropy oxides at room temperature [57]
-
2.2.3 稀土钽酸盐
-
由于钽酸盐具备高熔点、铁弹增韧等特性,近年来,高熵稀土钽酸盐作为热障涂层候选材料备受关注[58]。根据氧化钇和氧化钽比例的变化,稀土钽酸盐主要包括 3 种化学结构:ReTaO4、Re3TaO7 和 ReTa3O9 [59]。CHEN 等[60]研究了 ReTaO4 的热力学性能,并探讨了其作为高温环境下 TBC 的应用,研究结果如图13 所示,在 900℃的高温条件下 ReTaO4 的热导率为 1.40~2.1 W·m−1 ·K−1,远远低于 YSZ 的热导率。 WANG 等 [61] 成功制备了(Y0.2Ce0.2Sm0.2Gd0.2Dy0.2)TaO4,并对其相的结构、铁弹增韧机理、热力学性能进行了研究,结果表明 ReTaO4 的断裂韧性(3.05 MPa⋅m 1/2)高于 YSZ 的断裂韧性(2.5 MPa·m 1/2),ReTaO4 的脆性指数 (1.34 μm−1/2)低于 YSZ(7 μm−1/2),因此 ReTaO4 具有更好的力学性能,与此同时,与其他高熵陶瓷相比,它的热导率也较低(1.2~2.6 W·m−1 ·K−1),在 1 200℃的高温条件下,它的热膨胀系数高达 10.03×10−6 / K,但弹性模量低至 66~189 MPa,这导致了材料具有更高的应变容限。WU 等[62]通过固相反应合成了(AlxGd1-x)3TaO7(x=0,0.01,0.03,0.05) 固溶体陶瓷,研究了它们的热导率和热膨胀系数,结果表明,在 900℃以内的环境中,(AlxGd1-x)3TaO7 的热导率为 1.37~1.47 W·m−1 ·K−1,低于 YSZ 的热导率,与此同时,在 100~1 200℃的环境下,(AlxGd1-x)3TaO7 的热膨胀系数为 6×10−6 / K~10× 10−6 / K,与 YSZ 接近。CHEN 等[63]通过固态反应制备了 RETa3O9 块状陶瓷,研究了该材料的热物理性能,结果表明,RETa3O9 的热导率低至 1.33~3.37 W·m−1 ·K−1,远低于 YSZ 和 La2Zr2O7;热膨胀系数范围为 4.0×10−6~10.2×10−6 / K,接近 La2Zr2O7和 YSZ。
-
图13 RETaO4(RE=Nd,Sm,Eu,Gd,Dy, Ho,Y,Er)的热导率[60]
-
Fig.13 Thermal conductivity of RETaO4 (RE=Nd, Sm, Eu, Gd, Dy, Ho, Y, Er) [60]
-
三种化学结构的稀土钽酸盐(ReTaO4、Re3TaO7 和 ReTa3O9)都具有很好的热物理性质和热力学性能,可以作为热障涂层材料的候选。但是,由于高熵稀土钽酸盐的研究正在起步,各项综合性能有待提高,所以高熵稀土钽酸盐成为更好的 TBC 材料还缺少更多的理论和试验来论证。
-
2.2.4 自愈合材料
-
热障涂层一般应用于恶劣的工况下,所以可靠性和耐久性往往是涂层材料选择的重要考虑因素。热障涂层在工作条件下的寿命与裂纹的产生和扩展密切相关,有效抑制裂纹的产生和扩展是热障涂层提高寿命的关键。自愈合热障涂层通常具有抑制裂纹扩展的功能,因此自愈合材料成为 TBC 材料的候选。自愈合材料(又称自修复材料)是一类从结构上具有自修复能力的智能材料。具有这种能力的材料在受到长期的热载荷和机械载荷或其他外部载荷时,能够自行修复内部损伤。然而,这些材料实际上不能实现完全自愈合,所以,凡是能够一定程度实现自愈合的材料称为自愈合材料[64]。SONAYA 等[65]通过低压等离子喷涂法制备了顶部为 YSZ、中间引入 MoSi2、底部为 NiCrAlY 合金的涂层,结果表明,MoSi2氧化产生的 SiO2 可以密封裂缝和孔隙,防止了粘结涂层的氧化,从而改善涂层的热循环性能,将热循环寿命提高为传统 YSZ 涂层的 3 倍,与此同时,通过引入中间层来消除顶部涂层和粘结涂层之间的热膨胀和收缩差异的梯度来改善热循环性能。HUANG 等[66]通过火花等离子烧结制备了具有增韧和裂纹愈合性能的 NiAl 颗粒改性 Al2O3复合材料,研究了不同颗粒尺寸和含量的 NiAl 的增韧效应,结果表明,与纯 Al2O3 相比,加入质量分数为 15 wt.%的 1 μm NiAl 颗粒后,涂层的断裂韧性提高了 80%,且裂纹自愈合过程后,复合材料的断裂韧性进一步提高 40%。
-
尽管自愈合材料可以抑制涂层裂纹的产生与扩展,但自愈合材料的制备过程比较复杂,对制备环境依赖极强。此外,自愈合材料在高温环境中生成的氧化物可能和涂层材料的热膨胀系数较大,可能导致涂层产生较大的应力而剥落。自愈合材料在热障涂层方面的应用还较少,并且此类涂层的制备方法还需要进一步探究。
-
3 长寿命热障涂层的结构设计
-
新型顶部材料的热力学能更优异,抗腐蚀性更好,可以有效延长 TBC 的使用寿命。此外,从结构设计的角度考虑,单层涂层具有较低的制备成本和较小的层间热膨胀系数差,但单层涂层在极端高温下容易相变和烧结。因此,在极端高温环境中,TBC 结构优化对降低内部热应力、提高涂层可靠性和延长寿命起着至关重要的作用。
-
3.1 层状结构
-
层状结构的热障涂层主要有两种结构,单层热障涂层和双层热障涂层。层状结构的涂层一般由等离子喷涂法来制备,制备原理如图14 所示。在喷涂过程中,位于等离子射流内部的涂层材料被加热到熔融或半熔融状态,并高速喷向工件表面。由于液滴与工件表面之间具有较大温差,使得液滴迅速凝固,最终形成层状结构。传统的单层热障涂层具有制备方法简单,制备成本较低的优点,因此被广泛使用。新型涂层材料可以解决单层 YSZ 涂层在超高温环境中发生相变和烧结的问题,但新型材料的热膨胀系数与粘结层材料往往具有较大差异,容易导致热障涂层层间产生较大的热失配应力。因此,单层的新型材料涂层效果远不及 YSZ 涂层[67-68]。为了克服上述缺点,学者们综合结构和材料两方面因素,开发了双层热障涂层结构。
-
图14 等离子喷涂示意图[67]
-
Fig.14 Schematic diagram of plasma spraying [67]
-
双层热障涂层结构由新的顶层材料、YSZ 涂层和粘结层组成。新的顶层材料直接暴露在工作条件中,往往具有高温稳定性,YSZ 涂层用来降低顶部涂层材料和粘结层材料的热膨胀系数差,减小内部热应力。WANG 等[69]通过等离子喷涂在镍基高温合金基底上以 NiCrAlY 为粘结层,制备了单层 YSZ 涂层(常规和纳米结构)和双层 La2Zr2O7 / 8YSZ 热障涂层,并且研究了三种涂层在高温下的热冲击行为。结果表明,La2Zr2O7 / 8YSZ 涂层在 1 000、 1 200℃的高温环境下与纳米结构和传统结构的 YSZ 涂层相比具有更好的抗热震能力和更长的热循环寿命。WEI 等[70]设计了三组具有不同弹性模量组合的 La2Zr2O7/ YSZ 双层热障涂层,进行了梯度热循环试验。结果表明,三组不同弹性模量组合的 La2Zr2O7/ YSZ 双层热障涂层均具有较长的热循环寿命,其中两组低弹性模量的 La2Zr2O7/ YSZ 双层涂层的热循环寿命比纯 YSZ 涂层高 50%。CHEN 等[71] 采用等离子喷涂法制备了基于Mg2SiO4 / 8YSZ双层热障涂层,并且在高温环境下进行了热循环试验。结果表明,与单层 Mg2SiO4 涂层相比,Mg2SiO4 / 8YSZ 双层热障涂层具有更长的热循环寿命。双层热障涂层结构可以满足热障涂层的隔热和寿命要求,也可以减小高温工作环境下单层热障涂层内部的热应力。但是,热障涂层只有在固定的厚度范围才可以具有优异的性能,而不是涂层越厚越好,因此在制备双层热障涂层时要考虑厚度比例对性能的影响。此外,双层热障涂层较单层热障涂层增加了一个层间界面,如果该界面粗造度较低,那么涂层的粘合度下降易导致剥落;如果界面粗造度较高,那么涂层会产生较大的应力而产生裂纹,所以双层涂层的制备要充分考虑层间界面的设计。
-
3.2 柱状结构
-
柱状结构的热障涂层一般由电子束物理气相沉积法 EB-PVD 和等离子物理气相沉积法 PS-PVD 制备。EB-PVD 的设备组成如图15 所示,其工作原理是利用电子束的能量加热并汽化蒸发涂层材料,在真空的低气压环境中,蒸发的涂层材料在熔池上方汽化形成云状物,气相原子通常是以直线从熔池表面运动到工件表面并沉积在工件表面形成涂层。袁柯等[72]通过 EB-PVD 技术在 DZ406 合金和 DZ125 合金表面制备了 1.0Gd2O3-2.0Yb2O3 稀土掺杂改性 YSZ 陶瓷层(GYb-YSZ),由图16a 和 16c 所示,该涂层均呈典型的柱状晶结构,图16b 和 16d 可以发现陶瓷层和粘结层结合良好,研究了该涂层在 1 250℃下的高温燃气热冲击性能。结果表明, DZ406 / GYb-YSZ 热障涂层的热冲击寿命为 10 000 次,DZ125 / GYb-YSZ 热障涂层的热冲击寿命为 7 800 次。SHEN 等[73]通过 EB-PVD 技术制备了一系列稀土氧化物稳定 La2Zr2O7涂层,研究结果表明,所获得的涂层具有相对较高的热循环寿命 (395 次循环)和热冲击寿命(2 201 次循环),并且涂层具有极低的热导率和氧化物生长速率。
-
图15 EB-PVD 设备示意图[74]
-
Fig.15 Schematic diagram of EB-PVD equipment[74]
-
图16 热障涂层试样的截面微观形貌[72]
-
Fig.16 Cross section micromorphology of thermal barrier coating specimen[72]
-
PS-PVD 的设备组成如图17 所示,由真空泵、喷枪、除尘系统、冷却系统、电力系统和中控系统构成。与 EB-PVD 技术相比,PS-PVD 技术可实现大面积、均匀化物理气相沉积,并且可以实现多相复合涂层的沉积。付朗等[75]以纳米团聚的 8YSZ、Gd2Zr2O7(GZO)及(Gd0.9Yb0.1)2Zr2O7(GYbZ)粉末为原料,采用 PS-PVD 工艺制备出柱状结构完整、力学性能优异的锆酸钆热障涂层。结果表明,只喷涂 GZO 的涂层出现了剥落,喷涂 GZO 和 8YSZ 的涂层未剥落但内部存在大量微裂纹,而 Yb 掺杂的 GZO 涂层((Gd0.9Yb0.1)2Zr2O7,GYbZ)内无裂纹存在,并且和 GZO 涂层相比,GYbZ 涂层具有更高的硬度(5.4 GPa)、弹性模量(111.6 GPa)和结合强度(41.3 MPa)。REZANKA 等[76]使用 PS-PVD 制备出了具有柱状结构的 YSZ 热障涂层,结果表明, PS-PVD 技术制备的柱状热障涂层比APS制备的层状热障涂层具有更好的的抗 CMAS 腐蚀能力。
-
图17 PS-PVD 设备示意图
-
Fig.17 Schematic diagram of PS-PVD equipment
-
上述两种方法制备的柱状结构热障涂层的优势在于,从结构设计方面有效提高了涂层的热力学性能,增加了热障涂层的使用寿命。但由于柱状结构间存在很多间隙,会使得涂层的热导率普遍较高。因此,如何缩小柱间间隙、降低涂层热导率是设计柱状结构时需要考虑的问题。此外,柱间间隙较大容易导致 CMAS 侵蚀涂层,该结构的耐腐蚀性也会降低。因此如何提高该结构的硬度和抗颗粒侵蚀性是未来发展的关键。
-
3.3 新型结构设计
-
3.3.1 纳米结构
-
纳米结构涂层一般由悬浮液和固体粉末等离子共喷涂技术制备,该方法的设备组成和喷涂过程如图18 所示。ZHANG 等[77]通过悬浮液和固体粉末等离子共喷涂技术将具有大长径比的均匀纳米颗粒堆引入到传统的层状涂层中,制备了具有纳米结构的 YSZ 涂层,并且发现复合纳米结构涂层的热导率比传统等离子喷涂法制备的层状涂层低 1 / 5。JOSHI 等[78]通过悬浮液和固体粉末等离子共喷涂技术制备了 YSZ 纳米结构涂层,并与传统的大气等离子喷涂法和液相等离子喷涂法制备的涂层进行对比,结果表明,纳米结构涂层在热导率、热循环耐久性和热腐蚀性方面优于传统方法制备的涂层。
-
图18 悬浮液和固体粉末等离子共喷涂示意图[79]
-
Fig.18 Schematic diagram of plasma co spraying of suspension and solid powder [79]
-
尽管纳米结构涂层有优异的热力学性能,可以应用于各种恶劣的工况。但是,学者们在悬浮液和固体粉末等离子共喷涂技术方面的研究还不够丰富,并且纳米结构的涂层在实际应用中出现的问题还没有相关报道,所以这些原因制约了纳米结构涂层的发展。
-
3.3.2 功能梯度涂层结构
-
与传统层状结构涂层和柱状结构涂层相比,功能梯度涂层的特征是涂层材料的成分或材料的微观结构(晶粒尺寸、密度、孔隙率等)至少沿一个方向逐渐发生变化,从而导致该涂层物理性质发生转变[80]。功能梯度涂层可分为连续和不连续两种,如图19 所示,左图为连续功能梯度涂层,右图为不连续功能梯度涂层。连续功能梯度涂层一般没有明显的界面分层,如图20a~20c 所示,可分为尺寸/ 结构梯度涂层、取向梯度涂层和体积分数连续变化梯度涂层;不连续功能梯度涂层一般有明显的界面分层,如图20d~20f 所示,可分为成分梯度涂层、晶粒排列梯度涂层和体积分数不连续变化梯度涂层。 FAN 等[81]通过改变喷涂参数制备了一种新型的 Sc2O3-Y2O3共稳定 ZrO2功能梯度结构涂层,该梯度涂层根据纳米颗粒含量的不同分为三层。结果表明,该梯度涂层平均隔热温度为 132.6℃热循环寿命达到 641 次,这两个指标较传统纳米涂层分别高约10 %和 70.5%。SOLTANI 等[82]通过等离子喷涂法制备了三种热障涂层,分别为 NiCrAlY / YSZ 双层结构涂层、NiCrAlY / YSZ / 莫来石三层结构涂层和 NiCrAlY / YSZ / 莫来石梯度结构涂层,然后在 1 050℃下,在 45 wt.%Na2SO4 和 55wt.%V2O5 熔盐中对上述三种热障涂层进行了热腐蚀研究,结果发现,NiCrAlY / YSZ / 莫来石的抗热腐蚀性能优于常规层状 YSZ 试样,并且梯度热障涂层上致密莫来石层的存在减少了熔盐渗透到这些涂层中,并增加了涂层的抗热腐蚀性。
-
图19 功能梯度涂层的分类[80]
-
Fig.19 Classification of functional gradient coatings[80]
-
图20 功能梯度涂层的种类[80]
-
Fig.20 Types of functionally gradient coatings[80]
-
层状结构陶瓷直接将顶部涂层制备到粘结层上,由于材料较大的热膨胀系数差,在高温条件下会出现裂纹或陶瓷层的剥落。但是功能梯度涂层的材料成分或微观结构是沿一个方向逐渐变化,可以有效的控制热膨胀系数差,此外与层状结构厚热障涂层相比,带有垂直裂纹的梯度结构涂层具有更好的耐久性,其内部裂纹提供了大量的应变容限,释放了厚热障涂层内部积累的热膨胀应力。尽管功能梯度涂层有很多优点,但是在涂层的制备工艺和技术方面还存在很多问题。如何将不同材料应用于功能梯度热障涂层制备,怎样实现涂层材料成分和微观结构呈现线性变化是目前学者应该聚焦的问题。
-
4 结论与展望
-
TBCs 能够在先进航空发动机、燃汽轮机和其他动力装置的高温段部件中提供必要的热保护,是降低基体温度的关键技术之一。目前,TBCs 在高温环境下长时间服役的失效机制已较为明晰,主要分为残余应力失效、高温烧结、CMAS 腐蚀、TGO 生长导致失效这四个部分。针对此,以高隔热、长寿命为目标,从顶部涂层材料选择和先进结构设计的角度,总结了近年来 TBCs 的研究进展:
-
(1)残余应力、高温烧结、CMAS 腐蚀、TGO 生长是造成 TBCs 失效的主要原因。为了减小残余应力,一方面须要逐步完善不同制备工艺、不同材料 TBCs 的失效预测模型,提高预测模型结果的可靠性和准确性;另一方面,可以增大涂层应变容限来释放残余应力,从而缓解涂层应力集中现象,例如增加涂层内部孔隙率、在涂层内部预制裂纹。针对高温烧结问题,如何通过在基体掺杂金属氧化物来调整涂层内部孔隙结构的方法还有待进一步研究。为了延缓 CMAS 侵蚀,可以考虑热-力-化学耦合效应,采用原位自生的方法制备致密层,但这一方面的研究偏少。此外,在粘结层表面预先制备一层具有大尺寸晶粒的 TGO 层,能够通过增大晶粒尺寸减缓晶界扩散,限制 TGO 的生长。
-
(2)氧化锆基陶瓷韧性高,热导率低,且与基体热匹配较好,因此被广泛使用。关于多元稀土元素掺杂氧化锆材料的研究,大多数集中在掺杂后如何提高涂层的热力学性能和隔热性能,而关于稀土元素的掺杂含量和掺杂方式对材料性能的影响以及相关机理研究较少。目前常用的新型 TBC 材料有 A2B2O7 型氧化物、稀土钽酸盐、自愈合材料等,这些材料都具有低热导率、高温稳定性、优异的抗烧结性和耐腐蚀性,能够满足 TBC 材料的需求。
-
(3)为进一步提高 TBCs 的高温稳定性并延长其寿命,先进的结构设计也至关重要。针对传统单层涂层结构由于热失配应力剥落的问题,提出了双层结构、柱状结构、纳米结构和功能梯度结构这四种先进结构设计,详细的介绍了 APS、EB-PVD、 PS-PVD 等涂层制备方法。
-
基于以上总结,为进一步提高 TBCs 的隔热性能、延长 TBCs 的使用寿命,针对现有涂层材料和结构的研究做出如下展望:
-
(1)通过传统的制备工艺(APS、EB-PVD 等) 沉积新材料,易导致涂层成分偏析和内部相结构差异较大等问题,目前涉及新型陶瓷材料可沉积特性的研究报道较少,因此 TBC 材料的可沉积性是未来重点关注的方向。
-
(2)在实际生产中,先进结构涂层的制备难度较大、成本较高,因此将计算机数值模拟技术与传统的 TBCs 制备相结合,能够直观反应不同结构涂层的可靠性,协助选择最合适的制备工艺参数,从而降低研发成本。
免责声明:本网站所转载的文字、图片与视频资料版权归原创作者所有,如果涉及侵权,请第一时间联系本网删除。
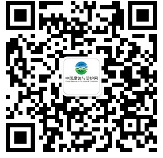
官方微信
《腐蚀与防护网电子期刊》征订启事
- 投稿联系:编辑部
- 电话:010-62316606
- 邮箱:fsfhzy666@163.com
- 腐蚀与防护网官方QQ群:140808414