我国西部某油田处理站的凝析油处理工艺主要采用“闪蒸+蒸馏”,凝析油稳定塔塔底重沸器是凝析油处理工艺中的重要环节,但是由于腐蚀问题换热管束频繁失效,造成严重损失[1-3]。重沸器换热管束失效案例屡见不鲜[4-10],失效原因包含多个因素,如材料质量、制造过程、服役介质、管束震动、气蚀等。
该失效重沸器于2014年服役,2019年管束开裂失效,运行期间重沸器一备一用,因此其总共服役时间为2.5 a。该重沸器为U形管式釜氏重沸器,管程设计压力为1.18 MPa,设计温度为300 ℃,管程介质为导热油,导热油进出口设计温度分别为280 ℃和220 ℃。运行期间,壳程凝析油进口温度约50 ℃,凝析油出口温度约75 ℃,壳程运行压力约0.18 MPa;管程导热油进出口温度分别约为240 ℃和210 ℃,管程运行压力约0.4 MPa。换热管束材料为2205双相不锈钢。为了明确换热管束失效原因,对换热管束进行了宏观检查、化学成分和组织检查、残余应力测试、断口分析以及浸泡试验,探讨了管束腐蚀开裂的特征及成因。
1. 理化检验与结果
1.1 宏观检查
为了确定重沸器管束的失效原因和失效位置,将所有管束进行拆解、打磨,采用渗透检测对换热管束表面的裂纹进行测试。结果表明,管束的失效形式主要为开裂,共计42根U形换热管出现裂纹,裂纹数量达到203条,裂纹分布及典型形貌如图1所示。另外,出现开裂的换热管位于整个管束的最外层。该重沸器管程介质为导热油,并且导热油的流向比较复杂。导热油从进口(B区)进入,经U形管束后从D区流出,再经重沸器封头流入C区,最后从A区流出。其中B区和D区的U形管束内导热油温度相对较高,A区和C区导热油温度相对较低。由图1(a)可见,高温区(B区和D区)失效U形管数量相对较多,达到27根,裂纹数量达到144条;温度相对较低的A区和C区同样出现裂纹,失效管数量为15根,裂纹数量为59条。相比较而言,高温区管束的失效问题更为严重。由图1(b)可以看出,管束表面裂纹数量最多达到29条。
1.2 化学成分和组织检测
采用ARL 4460型直读光谱仪分析直管段和U形弯的化学成分,结果如表1所示。结果表明,开裂管束直管段和U形弯的化学成分均符合GB/T 20878-2007《不锈钢和耐热钢 牌号及化学成分》标准对2205钢的要求。
试样或标准 | 质量分数/% | ||||||||
---|---|---|---|---|---|---|---|---|---|
C | Si | Mn | P | S | Ni | Cr | Mo | N | |
直管段 | 0.016 | 0.36 | 1.29 | 0.023 | 0.001 1 | 4.91 | 22.57 | 2.98 | 0.19 |
U形弯 | 0.018 | 0.39 | 1.28 | 0.022 | 0.001 6 | 4.86 | 22.22 | 2.94 | 0.19 |
GB/T 20878-2007标准 | ≤0.035 | ≤1.05 | ≤2.04 | ≤0.035 | ≤0.025 | 4.40~6.60 | 21.75~23.25 | 2.90~3.60 | 0.13~0.22 |
采用MEF3A型金相显微镜及图像分析系统对直管段和U形弯进行金相分析,结果如图2所示。结果表明,失效管束直管段和U形弯的非金属夹杂物均为薄系A0.5、B0.5和D0.5,组织为γ+α,两相分布均匀,α相体积分数分别为45.03%和57.99%,无析出相。
1.3 残余应力测试
依照GB/T 31310-2014《金属材料残余应力测定-钻孔应变法》标准对失效管束进行残余应力试验,共测试了3个平行试样。测试位置如图3所示,包含直管段和U形弯区域共计5个点。首先,在应变花上对应的圆孔内采用慢速钻孔仪打孔,孔深为孔径的1.2倍。然后,通过静态电阻应变仪测量释放的应变值,按式(1)~(2)计算得到相应的残余应力。
|
(1) |
|
(2) |
式中:εx和εy分别为环向和轴向释放应变,应变数量级为10-6;σx和σy分别为环向和轴向残余应力;A、B为应变释放系数,单位为MPa-1。
由表2可以看出,尽管开裂后管束局部的残余应力得到了释放,但是在开裂区周围仍存在较大的残余拉应力,最大值达到262 MPa,并且不同曲率半径和不同位置对应的残余应力分布不均匀。
试样 | σx/MPa | σy/MPa | ||||||||
---|---|---|---|---|---|---|---|---|---|---|
1 | 2 | 3 | 4 | 5 | 1 | 2 | 3 | 4 | 5 | |
1号 | 151 | 144 | 131 | 73 | -122 | 100 | 133 | 141 | 71 | -87 |
2号 | -253 | 108 | 54 | -90 | 29 | -265 | 68 | 49 | 100 | -53 |
3号 | 135 | 131 | -246 | 29 | 262 | -165 | -146 | -270 | -229 | 200 |
1.4 断口分析
在开裂位置即U形弯处取断口试样,采用Philips XL-20型扫描电镜(SEM)及其附带的能谱仪(EDS)分析断口试样。由图4可以看出,裂纹从外壁起裂向内壁扩展,在裂纹尖端出现明显的二次裂纹,且裂纹尖端存在明显的穿晶和沿晶特征。由图5可以看出,在开裂试样表面存在明显的点蚀行为,并且在裂纹起始位置可见明显的点蚀坑,这说明管束裂纹起源于表面生成的点蚀坑。由图6可以看出,断口表面无明显颈缩和局部减薄特征,高倍下可以观察到明显的解理台阶、河流状花样以及大量二次裂纹,呈现明显的脆性断裂特征。能谱测试结果表明,断口表面存在Fe、Cr、Ni、Mo、C、O、Cl等元素。
2. 应力腐蚀试验
采用高温高压反应釜模拟现场服役工况研究U形管束的失效行为。从失效管束上切割获得尺寸为65 mm×5 mm×1.5 mm的试样,依次采用240号、400号、800号、1200号的SiC水砂纸打磨试样表面。再依次采用离子水、丙酮超声清洗,冷风吹干后置于干燥器中备用。采用四点弯曲夹具对试样进行加载,依据残余应力测试结果,加载应力分别为70, 150, 250 MPa。腐蚀介质为模拟气田水溶液,其离子含量如下:236 mg/L 、1 140 mg/L
、79 000 mg/L Cl-、2 941 mg/L Ca2+、317 mg/L Mg2+、47 930 mg/L(K++Na+)。将试样置于高温高压反应釜、浸泡在腐蚀介质中进行腐蚀试验,试验时间为720 h,温度为240 ℃。试验结束后,取出试样,用蒸馏水冲洗干净并用冷风吹干;用除膜液(配方详见GB/T 16545-1996)在60 ℃下去除试样表面的腐蚀产物(时间20 min);在室温下用无水乙醇脱水、吹干、干燥。在光学显微镜下观察试样表面是否存在裂纹(放大10倍)。
由图7可以看出,当加载应力为70, 150, 250 MPa时,试样表面均出现明显的裂纹,并且随着应力增大,对应试样上裂纹的数量增加。由图8可见,当加载应力为70 MPa和250 MPa时,在裂纹尖端能够观察到明显的二次裂纹和穿晶特征。应力腐蚀试验结果表明,2205不锈钢存在明显的应力腐蚀敏感性。
3. 失效原因分析
由失效管束断口的形貌及能谱分析结果可以看出,该2205双相不锈钢的断口呈现脆性断裂的特征,并且断口表面存在明显的点蚀坑以及Cl-,据此推测该管束的失效原因为氯化物应力腐蚀开裂。通常认为,应力腐蚀开裂发生需具备三个条件:敏感材料、腐蚀环境和应力。从材料角度分析,该失效管束的化学成分满足GB/T 20878-2007标准要求,组织也无异常,奥氏体和铁素体体积比接近1∶1。从应力角度分析,换热管束表面存在明显的残余拉应力,其中最大的残余拉应力达到262 MPa。从腐蚀环境角度分析,在2014年至2018年管束表面存在明显结盐情况,在2018年底引入洗盐工艺,管束服役半年后出现大面积开裂,因此失效管束服役环境为高温-结盐-含氧苛刻环境。应力腐蚀试验结果表明,在高温模拟气田水环境中,2205双相不锈钢在较低应力条件下同样会出现应力腐蚀开裂。结合残余应力测试结果可知,2205不锈钢管束的开裂与制造或运行过程产生的残余应力以及服役环境相关。
在2018年之前,管束失效形式为表面结盐,但是在引入未除氧的洗盐水后,管束在短时间内开裂。溶解氧可以作为强去极化剂加速腐蚀,也有研究表明溶解氧有助于加速钝化膜的生长,提高钝化膜的稳定性[11-14]。但是,一旦钝化膜破裂,氧含量增加会促进点蚀的生长。该失效重沸器管束表面处于高温-结盐复杂环境,随着温度的升高,钝化膜的稳定性逐渐降低[15-16],点蚀敏感性逐渐增加。结盐的影响主要体现在两个方面:一方面,凝析油中水与沉积盐接触,使盐溶解,加速钝化膜破坏过程;另一方面,沉积盐作为“沉积层”,导致管束表面发生垢下腐蚀,进一步加速钝化膜的破坏。
综上分析,可推断管束开裂的原因为应力腐蚀开裂,其机理为阳极溶解。失效过程如图9所示[17-18]。在服役初期管束表面光滑,随着换热过程的进行,凝析油中的盐逐渐形核并且在管束表面沉积,出现结盐现象;洗盐水中的氧与管束表面接触,表面钝化膜逐渐破裂,裸露出新鲜金属;在盐沉积、高温、氧的共同作用下,点蚀生长加速;在残余拉应力的作用下,管束表面的点蚀向裂纹转变;当点蚀转变为裂纹后,在盐沉积、高温、氧的共同作用下,裂纹尖端钝化和溶解交替出现,最终在拉应力和腐蚀介质的共同作用下,裂纹不断扩大,直至管束断裂。
4. 结论
(1)重沸器2205不锈钢换热管束失效多集中在U形弯区域,裂纹多呈现环向开裂特征。
(2)残余应力测试结果表明,管束U形弯表面存在残余拉应力,最大值达262 MPa。
(3)断口形貌及应力腐蚀试验结果表明,管束开裂为氯化物应力腐蚀开裂,主要与管束服役过程中的高温、结盐、氧相关。
免责声明:本网站所转载的文字、图片与视频资料版权归原创作者所有,如果涉及侵权,请第一时间联系本网删除。
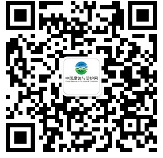
官方微信
《腐蚀与防护网电子期刊》征订启事
- 投稿联系:编辑部
- 电话:010-62316606
- 邮箱:fsfhzy666@163.com
- 腐蚀与防护网官方QQ群:140808414