1. 理化检验与结果
1.1 化学成分与硬度
347不锈钢是在普通8-18系列不锈钢中添加Nb,经稳定化处理后形成NbC,该材料耐晶间腐蚀能力比普通不锈钢更强。采用火花放电原子发射光谱法对管节进行化学成分测定,测定结果如表1所示。该管节的化学成分基本满足GB/T 14976-2012标准[2]的要求。利用维氏硬度计测量管节1/2壁厚位置的硬度(载荷9.8 N)。结果表明,其硬度为180 HV,满足正常标准要求。由于管节的材料较少,无法加工出标准的拉伸试样,因此未进行其他力学性能试验。
试样及标准 | 质量分数/% | |||||||
---|---|---|---|---|---|---|---|---|
C | Si | Mn | P | S | Cr | Ni | Nb | |
试样 | 0.046 | 0.371 | 1.323 | 0.017 0 | 0.003 7 | 17.45 | 9.77 | 0.445 |
GB/T 14976-2012标准 | ≤0.08 | ≤0.75 | ≤2.00 | ≤0.035 | ≤0.015 | 17.00~19.00 | 9.00~12.00 | 10w(C)~1.00 |
1.2 宏观观察
在现场沿焊缝将管节取下,送到实验室进行宏观观察。泄漏点位于管节长度的1/2处。管节外壁呈金属光泽,无腐蚀凹坑,也无其他腐蚀痕迹,外壁上存在一条周向裂纹,裂纹长度约为5 mm,裂纹曲折不平直,如图2(a)所示。由此可以推断裂纹起始于内壁,沿壁厚方向扩展至外壁形成泄漏点。
管节内壁表面被黑色油泥覆盖,如图2(b)所示,因此难以观察到金属形貌。将管节沿轴线方向分割成4瓣,选取包括泄漏点的部分,弯曲成U形(使裂纹更明显),弯曲后管节内壁形貌见图3。由图3可见:该管节内壁有多条裂纹,裂纹深浅不一,均由内壁起裂,其中一条裂纹扩展至外壁,引起内部介质泄漏;裂纹方向呈多样性,有平行于轴线方向的纵向裂纹、垂直于轴线方向的横向裂纹以及与轴线方向呈一定角度的斜向裂纹。
1.3 金相检查
从靠近管节焊缝位置取样进行金相检查,结果见图4。由图4可见,该裂纹由内壁多点起裂,分叉明显,整体呈树根形,该形貌符合不锈钢应力腐蚀开裂(SCC)特征[3],由此推断该管节发生了SCC。在管节下端,裂纹不但出现在母材处,而且出现在焊缝内,这说明焊缝内也发生了SCC;在管节上端的焊缝内未发现裂纹,在母材内也仅发现1条具有分叉特征的裂纹,且该裂纹的长度以及发展程度都不及管节下端母材中的裂纹。将母材内裂纹放大观察。由图5可见,该裂纹分叉特征明显,而且裂纹为穿晶裂纹。
1.4 扫描电镜和能谱分析
采用扫描电镜观察裂纹尖端位置断口形貌,结果见图6。由图6可见,裂纹尖端为金属破坏原始表面,断口表面无腐蚀产物覆盖,且凹凸不平,在断口上可见多条穿晶型二次裂纹。断口上裂纹形貌与图5中穿晶裂纹的特征相符。
在靠近内壁断口上,裂纹表面被腐蚀产物覆盖,利用能谱仪(EDS)对腐蚀产物进行成分分析,结果见图7。能谱分析结果表明,除铁、铬元素外,腐蚀产物中还含有较多的氯元素。氯元素由介质带入,是导致管节发生应力腐蚀开裂的主要元素。
1.5 晶间腐蚀试验
经稳定化处理的347不锈钢比一般的304不锈钢具有更优秀的抗晶间腐蚀能力,但添加的Nb元素对提高材料抗应力腐蚀开裂的作用不大。若347不锈钢处理不当,其中的碳元素与铬元素结合会形成沿晶界析出的铬碳化物,造成材料敏化。敏化后材料的抗腐蚀能力下降,更容易发生应力腐蚀开裂。因此为排除管节材料敏化造成的应力腐蚀开裂,依据标准对管节母材进行晶间腐蚀试验,确定材料是否敏化。
晶间腐蚀试验过程如下:将试样焊接导线并用环氧树脂进行封装,封装后试样用砂纸逐级打磨、抛光,清洗干燥;将处理好的试样置于10%(质量分数)草酸溶液中电解浸蚀(阴极材料为铂片)[4]。在显微镜下观察试样腐蚀情况,结果如图8所示。结果表明,晶间腐蚀后347不锈钢为一类阶梯组织,这说明材料未发生敏化。
2. 失效原因分析
管节泄漏的原因为应力腐蚀开裂。由裂纹形貌可见,该裂纹由管节内壁多点起裂,裂纹整体呈树根形,分叉明显,这是奥氏体不锈钢典型的应力腐蚀开裂特征。对裂纹尖端放大后可见裂纹为穿晶裂纹,裂纹尖端形貌也符合穿晶裂纹特征。裂纹分叉和穿晶是由氯离子引起的奥氏体不锈钢应力腐蚀开裂的典型特征。能谱分析结果也表明,断口表面腐蚀产物中残存着较多氯元素。综合裂纹特征和腐蚀产物成分可以推断该管节发生了由氯离子引起的应力腐蚀开裂,裂纹由管节内壁多点开始,沿壁厚向外侧扩展,最终扩展至外壁形成贯穿裂纹,引起内部介质泄漏。
一般认为,导致材料发生应力腐蚀开裂需要同时满足三个条件,即材料、应力和腐蚀环境[5]。以下从这三方面逐一讨论。
首先,管节材料为奥氏体不锈钢347。化学成分分析结果表明,其化学成分满足标准要求,而且材料未敏化。由此排除材料因素导致应力腐蚀开裂的可能性。此外,在管节下端的焊缝内发现了应力腐蚀裂纹。焊缝的化学成分以及经历的热处理与管节母材不同,这也从侧面表明应力腐蚀开裂的主要原因与管节材料关系不大。
其次,由于管节与主管道相通,管节与主管道承担相同的介质压力。管节内介质压力为20 MPa,在介质压力的作用下,管节产生环向应力,从而引起内壁纵向裂纹的产生。管节下方与阀门连接,工作时阀门处于关闭状态,作用于阀门的介质使管节沿纵向产生轴向应力;此外,管节下方阀门组件、排污管线受到的重力也会使管节产生轴向应力。轴向应力会引起内壁环向裂纹的产生。环向应力与轴向应力共同作用会使内壁产生斜向裂纹。管节的工作环境具备导致应力腐蚀开裂的应力条件。
最后,管道输送介质为渣油,其中含有氯离子等腐蚀性元素。炼油过程中,原油中的氯离子残存在渣油中,与其他反应介质一并通过管道输送,在一定条件下,氯离子在管节处汇聚,为应力腐蚀开裂提供了腐蚀环境。主管线内介质始终处于流动状态,介质内的腐蚀性元素难以汇聚。主管线内介质温度较高,介质内的水以气相形式存在,尽管介质内存在微量的氯离子,但其仍难以使主管线发生应力腐蚀开裂。排污管与主管线相连,正常生产时,排污阀关闭,管节内介质不流动,因此无法从流动的介质中获得热量,其热量仅来自于金属热传导。管节后方的排污阀热量流失较大,而热量又得不到补充,造成管节两端温差较大。低温造成管节内局部水相析出,而主管道内介质中的腐蚀性元素在水相中聚集,形成应力腐蚀开裂的环境。
3. 结论与建议
管节失效的原因为氯离子引起的应力腐蚀开裂。腐蚀性元素来源于管道内输送介质,管节内介质温度低于主道内介质温度,使介质中水蒸气凝结成水相,渣油中的氯元素,溶解进入管节内水相中,同时该位置温度高于室温,加速应力腐蚀开裂;管节与主管道连通,应力腐蚀开裂的应力来源于管节内介质的压力和管节下方组件所受重力;管节材料为奥氏体不锈钢,对介质中氯离子敏感。
建议适当提高管节的温度,避免介质水蒸汽在管节析出。依据能量来源,提高管节温度可以通过被动提高以及主动提高两种方式[6]。被动提高管节温度方式包括:通过增加管节以及管节相连的阀门外保温层厚度,减少与管节相连的阀门、管道等位置的热量流失,从而提高管节局部的温度;通过增加管节壁厚、缩短管节长度,降低主管道至阀门之间的热阻,使更多热量从主管道流向管节。主动提高管节温度的方式有增加蒸汽。此外,对管节位置的温度进行监控,可确保管节温度始终处于水冷凝点之上,避免水凝结析出;检修时及时打开排污阀门,可避免管节内腐蚀介质聚集。
免责声明:本网站所转载的文字、图片与视频资料版权归原创作者所有,如果涉及侵权,请第一时间联系本网删除。
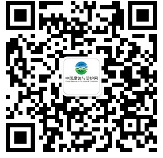
官方微信
《腐蚀与防护网电子期刊》征订启事
- 投稿联系:编辑部
- 电话:010-62316606
- 邮箱:fsfhzy666@163.com
- 腐蚀与防护网官方QQ群:140808414