界面过程,特别是钝化金属腐蚀过程,常伴随着局部微区pH的变化,这种变化会诱导或改变电化学反应[1~5],因此,实现电极/溶液界面局部pH瞬态变化的原位检测对理解界面过程的反应机理具有重要的意义。目前,对于界面电化学反应中瞬时pH的原位测量仍具有较大的挑战性,因为需要将pH传感器放置在样品表面附近并快速达到稳定状态以跟踪pH变化,这对pH传感器的尺寸、响应时间和稳定性提出了较高的要求[6]。玻璃pH传感器电极虽具有高的灵敏度和稳定性,但玻璃的脆性导致其难以微型化,不能实现界面微区pH的高分辨检测。后期虽然发展出了水凝胶pH传感器[7]、敏感场效应晶体管pH传感器[8, 9]和固态传感器[10]等,但这些传感器电极部分存在机械强度差、制造工艺困难、性能不稳定、难以微型化等缺点,限制了其应用。
金属/金属氧化物pH传感器电极因其易微型化、机械强度高、不易污染、耐腐蚀等优点,而受到广泛关注。目前,该类电极的研究较多的是TiO2[11],RuO2[12, 13],WO2[14, 15],Sn2O3[16, 17]等。但该类电极对电位响应的稳定性欠佳,实验中通常容易出现电位漂移、迟滞效应等现象。相比于其它金属氧化物电极,IrO x -pH传感器电极因具有响应时间快、灵敏度高、稳定性好、pH响应范围宽、使用寿命长等系列优点,而被广泛应用于各个领域。但IrO x -pH传感器电极在检测金属局部腐蚀过程中,可能会受到金属阳极溶解的阳离子,如Fe2+、Cu2+、Ti3+和阴离子如Cl-等的干扰,目前对于IrO x -pH传感器电极在这些离子溶液中的稳定性、响应速度和抗离子干扰能力 (即交叉敏感度) 研究明显不足,因此,无法保证测得的金属电极界面微区空间离子信息的准确性。
本文首先通过电化学沉积的方式在直径10 μm Pt超微电极 (Pt UME) 表面沉积一层氧化铱薄膜,制备出具有pH响应的全固态铂/氧化铱 (Pt/IrO x ) 电化学微传感器,对其线性响应、瞬时响应、稳定性和抗离子干扰能力进行测试,并结合扫描电化学显微镜 (SECM) 电位模式原位高分辨监测海工装备中常见电偶对铜/不锈钢在模拟海水中电偶腐蚀时表面微区pH的变化及其演变,为海工装备电偶腐蚀控制提供理论和数据支撑。
1 实验方法
实验中所使用的Cu和304不锈钢样品直径均为1.5 mm,通过环氧树脂封装制备成电极。测量Cu和304不锈钢电偶腐蚀行为时,两样品在树脂中的距离为0.5 mm,电极背面用焊锡和镍导线引出,用热熔胶固定。铜型号为T2,不锈钢型号为304不锈钢,两种材料均购自于大鑫金属材料 (东莞) 有限公司。样品电极在测试前均需经过400#~1600#砂纸打磨,并使用粒度1 μm的金刚石抛光喷雾剂抛光,直至金属电极端面呈镜面,用无水乙醇清洗烘干备用。
本文所有电化学测试,包括响应曲线、稳定性曲线,以及SECM的面扫描图和线扫描曲线,均是在CHI 920D电化学工作站上采用三电极体系进行,参比电极为Ag/AgCl电极,对电极为Pt丝电极。SECM测试采用电位模式,探针电极为自制的半径5 μm Pt/IrO x -pH超微传感器电极,探针和基底之间的距离通过将探针缓慢逼近样品至接触,然后再抬高至5 μm确定。为避免Cu和304不锈钢耦接后电场对pH电极检测的影响,在测试时将两电极断开,测试完成后再连接。本文电位若非特别说明,均是相对于Ag/AgCl参比电极 (内含3 mol/L KCl溶液,相对于标准氢电极+0.197 V)。
实验中测量Pt/IrO x -pH超微传感器电极的线性响应、瞬时响应和稳定性测试时采用的支持电解质为0.01 mol/L NaCl,在抗离子干扰测量时,支持电解质为0.6 mol/L NaCl (模拟海水,即3.5% (质量分数) NaCl),干扰离子Fe2+、Cu2+和Ti3+浓度为5 mmol/L。
2 结果与讨论
2.1 Pt/IrO x -pH传感器的制备
Pt UME的制备过程见前期发表的文章[18~21]。图1a为自制的Pt UME在1 mmol/L FcMeOH+0.1 mol/L KNO3溶液中的循环伏安 (CV) 曲线。图中显示Pt UME的循环伏安曲线表现出较好的S形,且曲线的极限电流iT,∞与半径a之间的关系满足iT,∞=4nFDca[22].表明制备的Pt UME密封性好、电化学性能稳定。随后,通过电化学工作站的循环伏安模式 (电压扫描范围0.2~0.75 V,扫速50 mV/s,100个循环) 在Pt UME表面电化学沉积一层氧化铱 (IrO x ) 膜 (电沉积液配制和沉积实验,具体步骤见前期发表论文[23, 24])。沉积后光学照片如图1b所示,与沉积前相比,中心光亮的Pt表面覆盖了一层蓝紫色薄膜,表明在Pt UME上成功沉积了一层IrO x 薄膜。通过测量,该超微电极尖端外径约45 μm,RG (即尖端玻璃半径与金属丝半径比值) 约为4.5。
图1

图1 直径10 μm Pt UME在1 mmol/L FcMeOH+0.1 mol/L KNO3溶液中CV曲线及沉积IrO x 后电极端面光学形貌
Fig.1 CV curve of diameter 10 μm Pt UME in 1 mmol/L FcMeOH+0.1 mol/L KNO3 solution (a), and optical photo of electrode surface after deposition of IrO x (b)
2.2 Pt/IrO x 电极对pH响应和稳定性测试
图2a为Pt/IrO x 电极在不同pH溶液中稳定后的电位值及其线性拟合曲线。结果表明制备的Pt/IrO x 电极对pH具有优异的线性响应性能 (R2=99.97%),斜率达到79.8 mV/pH,呈现超能斯特响应。图2b结果显示Pt/IrO x -pH电极在pH=1.70~10.44的范围内,随着溶液pH的改变电位瞬间产生响应,且能快速达到电位稳定,说明制得的Pt/IrO x 电极对pH响应快。图2c是分析制备的Pt/IrO x 电极在0.01 mol/L HCl溶液中的稳定性,结果显示在20000 s的测试时间内Pt/IrO x 电极电位基本保持稳定,电位波动在10 mV以内。图2d为Pt/IrO x 电极在空气中放置不同时间后稳定性测试结果,结果显示电极在pH=1.00~13.00的范围内对pH的响应仍表现为Nyquist线性响应 (斜率保持在-59±5 mV/pH),线性相关系数也在0.999±0.010。由此可见,实验所制得的Pt/IrO x -pH超微传感器电极在短期和长期均保持着较高的稳定性能和较好的线性响应,使用寿命长。
图2

图2 Pt/IrO x -pH超微传感器在不同pH下的响应电位及其拟合曲线,对pH变化的瞬时响应时间曲线,在0.01 mol/L HCl溶液中短期稳定性曲及在空气中放置时长期稳定性
Fig.2 Response potential and fitting curve of Pt/IrO x -pH micro-sensor electrode at different pH (a), instantaneous response curve of the Pt/IrO x -pH electrode to pH change (b), short-term stability of the Pt/IrO x -pH electrode in 0.01 mol/L HCl solution (c) and long-term stability of the Pt/IrO x -pH electrode when placed in air (d)
2.3 Pt/IrO x -pH电极抗离子干扰性能测试
IrO x 对pH的响应机理是氧化铱膜在沉积过程中表面会吸附较多的羟基基团,这些基团在膜/水界面常发生氧化还原反应 (一般是与H+或OH-反应),达到消耗或释放质子的效果,从而呈现出Nyquist响应[23]。但是IrO x 电极在对pH响应过程中可能受到溶液中其它离子的干扰,如溶液中的Cl-,以及金属腐蚀产生的阳离子等,这些物质与氧化物薄膜反应,有时甚至生成络合物附着在薄膜表面,这将严重影响pH电化学传感器的线性响应和稳定性。一个性能良好的pH电化学传感器应该表现出对除质子外其它离子低甚至零灵敏度,即抗其它离子干扰能力。本文系统研究了海工装备中常见的金属离子,如Ti3+、Cu2+、Fe2+,以及阴离子Cl-对Pt/IrO x -pH超微电化学传感器性能的影响。对于抗Cl-干扰测试,图2中测试时采用的是低浓度的Cl-溶液 (浓度为0.01 mol/L),表现出了较好的稳定性,但实际应用在模拟海水体系中,Cl-浓度高达0.6 mol/L (3.5%),因此本文进一步测试了Pt/IrO x -pH传感器在高Cl-浓度中的抗干扰能力。图3a显示Pt/IrO x -pH传感器在酸性、中性和碱性的高Cl-浓度溶液中均表现出较高稳定性。将pH与电位的关系作图 (图3b),并进行线性拟合,可以看出电位与溶液pH之间仍存在较高的线性关系 (R2=0.998),以上结果表明Pt/IrO x -pH传感器具有较好的抗Cl-干扰能力。
图3

图3 Pt/IrO x -pH传感器在不同pH的3.5% NaCl溶液中OCP和响应电位与pH的线性关系及其拟合曲线,Pt/IrO x -pH传感器在含有5 mmol/L Fe2+,Cu2+和Ti3+的3.5 % NaCl溶液 (pH=2.00) 中的OCP以及Pt/IrO x -pH传感器在含5 mmol/L Fe2+或Cu2+溶液中的电极电位及其拟合曲线
Fig.3 OCP (a) and linear relationship between response potential and pH and its fitting curve of Pt/IrO x -pH sensor in 3.5% NaCl solution with different pH value (b), OCP of Pt/IrO x -pH sensor in 3.5% NaCl solution (pH=2.00) containing 5 mmol/L Ti3+, Fe2+ and Cu2+, respectively (c), electrode potential of Pt/IrO x -pH sensor in 5 mmol/L Fe2+ or Cu2+ solution and its fitting curve (d)
图3c是Pt/IrO x -pH传感器在Cu2+、Fe2+和Ti3+典型金属离子溶液中的OCP。为防止这些离子可能在弱酸性、中性或碱性溶液中不稳定存在,统一将溶液pH调整为2,浓度固定为5 mmol/L,支持电解质为3.5% NaCl。图3c显示,在含Fe2+和Cu2+溶液中,Pt/IrO x -pH传感器的电位可以保持长时间的稳定,而在含有Ti3+的溶液中,Pt/IrO x -pH传感器在200 s内电位发生突降,随后稳定在-0.31 V附近,在测试完成后,测量溶液pH仍为2,表明电位的变化并非溶液pH改变所引起,表明Ti3+会显著干扰Pt/IrO x -pH传感器的稳定性,其原因可能是溶液中的Ti3+具有较强的还原性,易与Pt/IrO x -pH传感器电极中间价态的IrO x 薄膜发生反应,使得电极失去了对pH检测的能力。因此,对于发生钛腐蚀的体系,不能用Pt/IrO x -pH传感器进行溶液pH的检测。
为进一步证明Fe2+和Cu2+不会影响Pt/IrO x -pH传感器的电位与pH的线性关系,实验中调节溶液pH为1和3,然后测量其电位,并分析其线性关系,结果如图3d所示。图中黑色标记是没有添加Fe2+或Cu2+时溶液的电位,结果显示在溶液中添加Fe2+或Cu2+并不会改变Pt/IrO x -pH传感器的线性关系,表明制备的Pt/IrO x -pH传感器具有优异的抗Fe2+和Cu2+干扰能力。需要指出的是,实验中采用两根pH电极进行测试 (标记为No.1和No.2),但两根pH电极的斜率并不相同,这是因为在相同的电沉积溶液和参数下,得到的IrO x 氧化膜状态不完全相同 (即使采用同一根Pt电极),因此,在每次测试之前都需要在标准溶液中线性测试以确定pH和电位的线性关系。综合以上稳定性测试的结果可以确定本文制备的Pt/IrO x -pH超微传感器对于Fe2+、Cu2+和Cl-不存在敏感性,可以在上述离子的溶液环境中进行局部腐蚀pH的检测。
2.4 Cu/304不锈钢电偶腐蚀表面pH分布原位监测
2.4.1 偶接前Cu和304 不锈钢表面pH分布原位监测
对于超微电极,探针与样品之间距离的精确控制是实现高分辨成像的关键,实验中Pt/IrO x -pH超微传感器电极与样品之间距离通过逼近曲线确定为5 μm,具体步骤见前期发表论文[23]。随后,在3.5% NaCl溶液 (pH=2.00) 中,利用SECM电位模式在Cu表面进行面扫描测试,结果如图4所示。图中显示Cu开始腐蚀时,表面pH在2.18至3.02之间 (图4a),略高于本体溶液pH,随着浸泡时间增加至6 h,表面pH值升至5.28~5.92之间 (图4b),明显高于本体溶液pH值,但当浸泡12 h后,表面又降至3.54~4.00之间 (图4c)。图4d是不同浸泡时间下表面pH变化的对比,从中更加明显的看出pH先增加后减小。出现上述这种变化的原因可能是:在浸泡初期,Cu表面氧化膜发生溶解,导致表面pH逐渐升高,当反应一段时间后,表面可能出现腐蚀产物的堆积,降低了Cu的腐蚀速率,从而引起pH的降低。此外,从面扫描图中没有看到明显的pH增大或减小的点,表明Cu在pH=2.00的3.5% NaCl溶液中发生的是均匀腐蚀过程。
图4
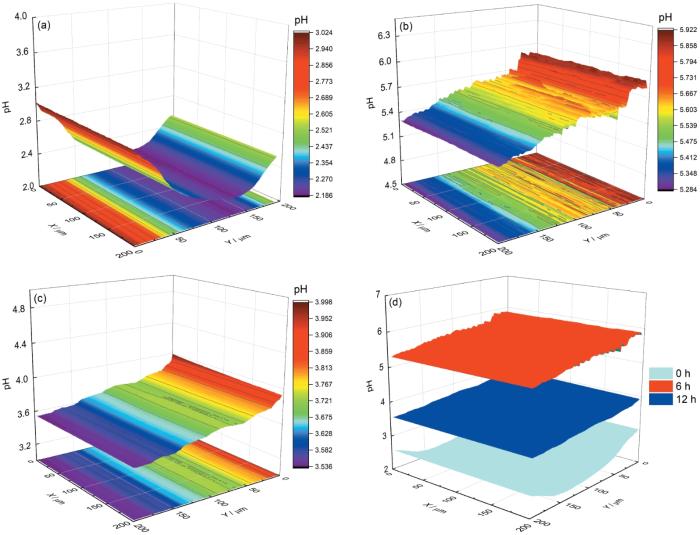
图4 Cu在pH=2.00的3.5% NaCl溶液中不同浸泡时间面扫描结果及3个时间面扫描对比图
Fig.4 Surface scanning diagram of Cu electrode in 3.5% NaCl solution with pH=2.00 after immersion for 0 h (a), 6 h (b), 12 h (c), and comparison of surface scanning of Pt/IrO x -pH microsensor electrode on Cu surface with distance of 5 μm in the three immersion times (d)
图5为Pt/IrO x -pH超微传感器电极在pH=2.00的3.5% NaCl溶液中304不锈钢表面的面扫描结果。图5a显示在浸泡初期,304不锈钢面pH在2.45至2.75之间,略高于本体溶液pH,大部分区域pH呈现均匀的变化,但在局部区域出现pH减小或增大的峰,这认为是304不锈钢局部腐蚀时阴极或阳极活性位点。在浸泡6 h (图5b) 和12 h (图5c) 后,与浸泡初期相比,表面pH变化较小,这可从图5d中更能明显的看出。需要注意的是,虽然在图5b和c中没有检测到明显的腐蚀活性位点,但从面扫描的投影中仍可以看到表面存在一定的pH波动。以上结果表明304不锈钢在pH=2.00的3.5% NaCl溶液中腐蚀较为缓慢。
图5

图5 304不锈钢在pH=2.00的3.5% NaCl溶液中不同浸泡时间面扫描结果及3个时间的面扫描对比图
Fig.5 Surface scanning of 304 stainless steel in 3.5% NaCl solution with pH=2.00 after immersion for 0 h (a), 6 h (b), 12 h (c), and comparison of surface scanning of Pt/IrO x -pH microsensor electrode on 304 stainless steel with distance of 5 μm in the three immersion times (d)
2.4.2 偶接后Cu/304不锈钢表面pH分布原位监测
图6为Cu和304不锈钢在pH=2.00的3.5% NaCl溶液中发生电偶腐蚀时样品表面pH随浸泡时间的变化,其中图6a-c和图6e-g分别为Cu和304不锈钢在浸泡0、6和12 h时表面pH的演变。图6a显示在浸泡初期Cu表面pH在4.6至5.7之间,远高于本体溶液的pH,而304不锈钢表面pH也出现增加,但幅度较小 (pH在3.2至4.7之间),当浸泡6和12 h时,Cu表面pH逐渐减小,而304不锈钢表面pH则逐渐增加,从图6d和图6h中更能明显的看出这种变化。在开始测试时,Cu和304不锈钢表面pH均显著大于2的原因是Pt/IrO x -pH探针电极在逼近样品表面过程中,Cu和304不锈钢表面均发生了自腐蚀过程阴极质子还原和氧还原过程导致表面pH显著增加;随着浸泡时间的增加 (图6b和图6f),Cu和304不锈钢发生电偶腐蚀时两电极极化程度降低,导致两样品的pH比较接近;在浸泡12 h时Cu表面pH继续降低,而304不锈钢表面pH升高,可能与电偶腐蚀时阴阳极极性的转变有关,此时Cu由开始浸泡时的阴极转变为阳极,导致质子还原和氧还原速率降低,从而引起pH的降低。为进一步验证Cu和304不锈钢表面pH的变化,在两样品表面进行了线扫描测试 (图7)。结果显示开始浸泡时Cu表面pH高于304不锈钢,在6 h时,两表面pH接近,在12 h时,Cu表面pH低于304不锈钢,这与图6的结论相一致。
图6

图6 Cu和304 不锈钢在3.5% NaCl溶液中 (pH=2.00) 发生电偶腐蚀时,不同浸泡时间下面扫图对比图
Fig.6 Surface scanning of Cu (a-d) and 304 stainless steel (e-h) galvanic corrosion under different immersion times in 3.5% NaCl solution with pH=2.00, in which results of surface scans at 0 h (a, e), 6 h (b, f), 12 h (c, g), and comparison of surface scanning of Pt/IrO x -pH microsensor electrode on sample surface with distance of 5 μm in the three immersion times (d, f)
图7
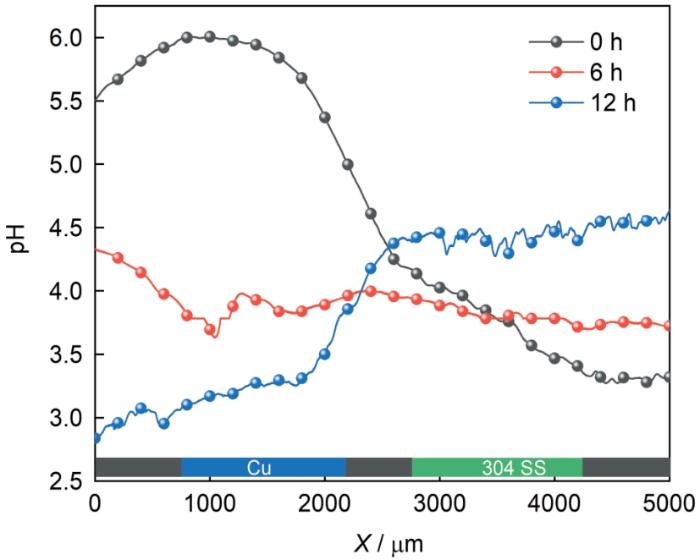
图7 Pt/IrO x -pH电极在3.5% NaCl溶液中Cu/304不锈钢表面线扫描曲线
Fig.7 Line scanning curves of Pt/IrO x -pH electrode on Cu/304 stainless steel surface with distance of 5 μm in 3.5% NaCl solution with pH=2.00
为了证明上述Cu和304不锈钢在电偶腐蚀过程中会发生阴阳极极性变化的假设,对Cu和304不锈钢在电偶腐蚀过程中0、6和12 h时各自的OCP进行测量 (测试时断开,测完后再连接),结果如图8所示。图8a显示在开始浸泡时,Cu电极电位比较稳定,在-0.130 V左右,而304不锈钢电位逐渐正移,但一直低于Cu,表明开始浸泡时Cu为阴极,304不锈钢为阳极;当电偶腐蚀6 h时 (图8b),Cu与304不锈钢表面OCP比较接近,在-0.185左右,表明此时阴阳极金属偶接后极化程度降低,腐蚀较为缓慢,这也能解释图6c和g,以及图7中Cu和304不锈钢表面pH接近的结果;当电偶腐蚀12 h时 (图8c),Cu电极的OCP低于304不锈钢,表明偶接时Cu为阳极,发生阳极溶解,304不锈钢为阴极,在表面发生质子还原和氧还原过程,这种Cu和304不锈钢电偶腐蚀过程中极性反转可以充分的解释面扫描 (图6) 和线扫描 (图7) 的结果。
图8

图8 Cu/304不锈钢在pH=2.00的3.5%NaCl溶液中浸泡不同时间发生电偶腐蚀的各自OCP
Fig.8 OCP of Cu and 304 stainless steel under different immersion times with galvanic corrosion in 3.5%NaCl solution with pH=2.00: (a) 0 h, (b) 6 h, (c) 12 h
3 结论
(1) 通过简单电化学沉积方法在直径10 μm Pt UME上制备得到线性响应好、瞬时响应快、稳定性高的全固态Pt/IrO x -pH电化学传感器电极,其对Fe2+、Cu2+和Cl-具有较强的抗离子干扰能力,而Ti3+的存在会影响检测的准确性。
(2) 基于SECM的电位模式,结合ISET,实现了Cu和304不锈钢偶接前后表面pH的原位高分辨监测。在偶接后,Cu表面pH逐渐降低,而304不锈钢表面pH逐渐增加,结合OCP的变化发现在Cu/304不锈钢电偶腐蚀过程中发生了阴阳极极性变化,Cu由开始腐蚀时的阴极转变为阳极,相反,304不锈钢由阳极转变为阴极。
免责声明:本网站所转载的文字、图片与视频资料版权归原创作者所有,如果涉及侵权,请第一时间联系本网删除。
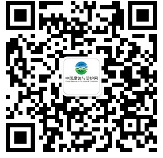
官方微信
《腐蚀与防护网电子期刊》征订启事
- 投稿联系:编辑部
- 电话:010-62316606
- 邮箱:fsfhzy666@163.com
- 腐蚀与防护网官方QQ群:140808414