氢致键合力降低 (HEDE) 和氢促进局部塑性变形 (HELP) 是目前广为接受的两种氢脆 (HE) 机制[1,2],前者认为氢能够降低原子键合力,使晶面、晶界或各种界面在较低的应力下开裂,后者则认为氢能够促进位错滑移造成应变局部化,从而降低宏观塑性。早期,HEDE被广泛用于解释脆性沿晶 (IG) 断裂。但近年来研究表明HELP与HEDE可协同作用致HE,且两机制孰起主导作用与氢浓度水平有关。在低氢浓度下HE受控于HELP机制,而高氢浓度下HE主要由HEDE控制 (HELP参与)。如Djukic等[3,4]在分析氢致某蒸发器失效时观察到,从贫氢区域切取的试样的断口呈现大量韧窝,伴有少量准解理 (QC) 断裂形貌,此时试样HE程度较低,但逐渐向富氢区域切取试样并测试可见QC断裂逐渐盛行并最终出现IG断裂,表明随着氢浓度的升高HEDE机制逐渐占主导,相应地HE程度增加。Verma等[5]在研究电流密度对某沉淀强化Fe-Cr-Ni钢HE影响时发现不充氢试样和充氢电流密度为1 A·m-2的试样断口均呈现韧窝+QC混合断裂形貌,区别是充氢试样的QC形貌更多,导致了轻微的塑性减损。此时,氢的作用应主要是通过加速滑移和诱导滑移局部化去帮助平面滑移,符合HELP机制。然而充氢电流密度为10 A·m-2的试样呈现明显的IG断口形貌,表明试样的氢浓度水平超过了诱发HEDE机制的氢浓度临界值。但在IG面上可观察到滑移痕迹,表明HELP发挥协同作用。
与碳钢、低合金钢相比,奥氏体不锈钢 (ASSs) 虽HE抗性高,但强度低限制了其在临氢环境下使用,如用于高压储氢容器。基于剧烈塑性变形 (SPD)的晶粒细化可有效提高ASSs强度,如高压扭转、挤压、重度冷轧 (Heavy cold-rolling,HCR)等。然而对亚稳定ASSs,如304/304L等,SPD会导致γ奥氏体向αʹ马氏体相变[6],降低钢的HE抗性 (H在αʹ中的扩散速度比在γ中高5~6个数量级)。但若将SPD和退火处理 (AT) 组合起来,在适当的参数下,利用高温引起的再结晶和αʹ向γ逆变,则可制备近等轴的细晶乃至纳晶全奥氏体ASSs[7,8]。更有意义的是,研究表明基于SPD+AT的晶粒细化不仅可以提高ASSs强度,还可以进一步抑制钢的HE。Macadre等[9],Fan等[10]基于实验观察解释认为细晶钢的塑性变形较均匀,从而缓减HELP,抑制HE。但是,晶界作为典型氢陷阱,其对氢浓度和氢扩散的影响机制,仍需澄清。Bai等[11]研究表明晶粒细化明显增加了Fe-31Mn-3Al-3Si孪晶诱导塑性钢预充氢时吸收的氢含量,但其他研究表明其对Fe-22Mn-0.6C钢[12]、Fe-18Mn-0.6C钢[13]和CoCrFeMnNi高熵合金[14]的氢含量无影响。Koyama等[14]研究表明预充氢条件下晶粒细化降低了CoCrFeMnNi高熵合金的HE,但Fu等[15]对同样的合金采用动态充氢却揭示细晶试样的HE敏感性更高。后者基于显微结构观察认为制备细晶试样的低温短时AT导致了大量位错残留于试样中,因此HE敏感性高。显然,考虑到不同加氢条件下氢扩散、陷阱与位错运动相互影响存在差异 (动态充氢条件下,氢伴随位错运动进入试样),有必要直接对比研究预充氢和动态充氢两种加氢条件下晶粒尺寸对ASSs HE的影响,以进一步揭示晶粒细化抑制HE的原因。
本文以304L奥氏体不锈钢为研究对象,通过HCR+AT获得不同晶粒尺寸的钢样,进行单轴拉伸试验,评定预充氢和动态充氢两种加氢条件下试样的HE敏感性,分析断裂行为异同,并基于氢扩散、陷阱、位错相互作用等相关理论,讨论断裂行为异同的原因,从氢浓度角度揭示晶粒细化能否抑制HE的本质条件。
1 实验方法
所用304L不锈钢板化学成分(质量分数,%)为:C 0.02,Cr 18.30,Ni 8.10,Mn 1.1,Si 0.37,P 0.031,S 0.004,Mo 0.014,其余Fe,初始厚度为10 mm。沿原热轧方向以每道1 mm下压量进行冷轧,道间水冷,最终得到1 mm厚钢板,总冷轧变形量为90%。通过线切割制备拉伸试样,标距段尺寸为25 mm×10 mm×2 mm。试样经清洗去油污、干燥后采用箱式电阻炉进行AT并水淬。在电阻炉达到设定温度后快速放入试样,AT参数分别选取在700 °C保温5 min,800 °C保温20 min,900 °C保温20 min和1050 °C保温20 min (即固溶处理) 以获得不同晶粒尺寸。其中,由于304L钢在700 °C下较长时间保温易发生敏化 (碳化物析出),干扰晶粒尺寸对氢脆的影响分析,故取AT时间为5 min,同时较少的保温时间能够获得较小的晶粒尺寸。试样表面用砂纸从100目逐级打磨到2000目,并经0.5 μm Al2O3悬浮液抛光,去除表面污染、氧化层和机械损伤。根据AT温度和时间为各试样命名,如AT800-20表示该试样在800 °C保温20 min。
采用D8 Advance 型X射线衍射 (XRD) 技术测量试样位错密度和αʹ马氏体含量,以评价再结晶和αʹ向γ逆变程度。在XRD测量之前,先将试样电解抛光5 min,去除表面变形层。测量参数为电压40 kV、电流40 mA,Cu靶,检测角度2θ为40°~100°,步长0.02°。测量完成后,利用Jade软件分析衍射图谱,提取特征参数计算试样的α′含量和位错密度。其中α′含量计算基于下式:
式中,Vα′ 为α′体积分数,n为峰个数,Ii 和Ri (i为αʹ或γ) 分别为各峰积分强度和散射因子。该公式指出任一相的体积分数与该相所有衍射峰的积分强度呈正比。位错密度计算采用Williamson-Hall法[16] (峰宽化正比于微应变,由于晶粒尺寸不低于100 nm,忽略细晶对峰宽化的影响),即:
式中,β为半峰宽,θ为Bragg's角,d为晶粒尺寸,λ为X射线波长,0.154 nm,εc为微应变。基于
式中,ρd为位错密度,b为Burgers矢量,0.254 nm。
将抛光后各试样放入65%硝酸溶液中进行电解腐蚀,腐蚀电流密度为200 mA·cm-2,时间为25 s,以浸蚀晶界使晶粒尺寸显现。采用Quanta TM 250扫描电子显微镜 (SEM) 观察腐蚀后金相并采用截距法测量平均晶粒尺寸d。
将各试样在预充氢后进行常温拉伸试验或动态充氢拉伸实验,拉伸速率为0.5 mm·min-1 (对应应变速率为3.3×10-4 s-1)。动态充氢使用0.5 mol·L-1 H2SO4溶液加入1 g·L-1硫氰酸铵 (毒化剂,阻碍氢原子复合为氢分子) 作为电解液,充氢电流密度为50 mA·cm-2。预充氢使用与动态充氢相同的电解液和电流密度,充氢时间为96 h。将充氢试样的拉伸力学性能与未充氢试样进行比较,采用
式中,δ0和δH是试样未充氢及充氢拉伸后的延伸率,δL表示试样的HE指数,越大则该试样HE敏感性越高。使用SEM观察试样的断口形貌,分析其断裂机制。部分实验条件拉伸测试两个试样,以检查重复性,取平均值。采用ONH836型ONH分析仪基于惰性气体熔融法热导法 (GB/T 223.82-2018) 测量充氢试样的氢含量。对预充氢试样,充氢后迅速截取充氢段,对动态充氢试样,试样断裂后截取充氢段,后低温封存直至测试。
2 实验结果
2.1 晶粒尺寸、 αʹ 含量和位错密度
图1a给出了各试样的XRD图谱,并依据
图1
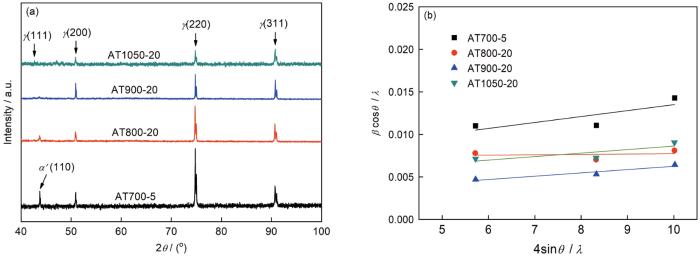
图1 不同退火处理试样的XRD图谱和Williamson-Hall图
Fig.1 XRD spectrums (a) and Williamson-Hall plots (b) of specimens annealed by different parameters
图2

图2 各试样显示晶粒尺寸的金相图
Fig.2 Metallographic images of AT700-5 specimen (a), AT800-20 specimen (b), AT900-20 specimen (c) and AT1050-20 specimen (d) showing the grain sizes
表1 不同退火处理试样的平均晶粒尺寸、αʹ马氏体含量和位错密度
Table 1
2.2 力学性能和HE指数
各试样的应力应变曲线如图3a~d所示。随着晶粒尺寸降低,屈服强度增加,证实细晶强化效应。其中AT800-20,AT900-20和AT1050-20等3个试样数据符合经典Hall-Petch关系,如图3e所示,可拟合得Hall-Petch系数为441 MPa·m1/2,和文献报道的304L钢Hall-Petch系数接近[19]。然而AT700-5试样的屈服强度偏离了拟合直线,这应是因为该试样含有较多的αʹ马氏体和位错。动态充氢和预充氢对钢屈服强度的影响均不大,略降低抗拉强度,但降低了延伸率。测量断后试样的延伸率代入
图3

图3 各退火试样的拉伸应力应变曲线、屈服强度和预充氢试样与动态充氢试样HE敏感性指数比较
Fig.3 Tensile stress-strain curves of specimens (a-d), yield strength (e) and comparison in HE susceptibility index between hydrogen pre-charged specimens and in situ hydrogen-charged specimens (f)
2.3 断口形貌和氢含量
图4
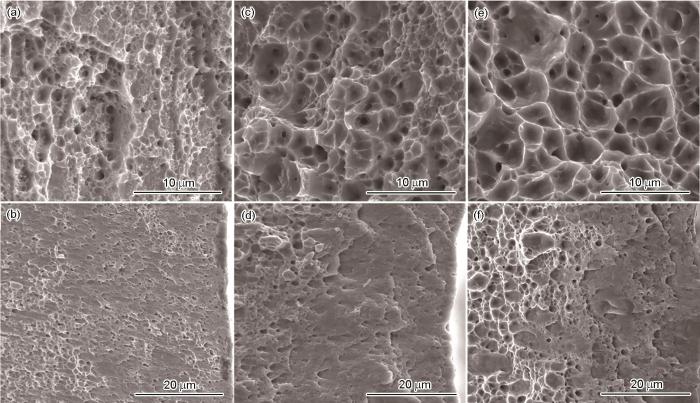
图4 未充氢试样的断口心部和边缘区域形貌
Fig.4 Fracture morphologies of uncharged specimens including both their center regions (a, c, e) and edge regions (b, d, f): (a, b) AT700-5 specimen, (c, d) AT800-20 specimen, (e, f) AT1050-20 specimen
图5给出了充氢试样断口的心部区域形貌。与未充氢试样断口心部形貌类似,呈现大量韧窝,因为无论是预充氢还是动态充氢,由于氢在γ奥氏体中扩散系数较低,氢无法扩散到达试样心部。
图5
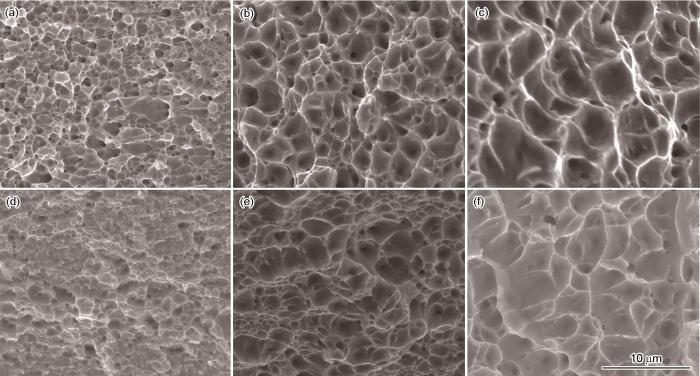
图5 充氢试样断口心部形貌
Fig.5 Fracture morphologies of center regions of hydrogen-charged specimens: (a) in situ hydrogen-charged and (b) hydrogen pre-charged AT700-5 specimen, (c) in situ hydrogen-charged, (d) hydrogen pre-charged AT800-20 specimen, (e) in situ hydrogen-charged, (f) hydrogen pre-charged AT1050-20 specimen
图6

图6 动态充氢试样断口边缘区域断裂形貌
Fig.6 Fracture morphologies of edge regions in situ hydrogen-charged specimens: (a, b) AT700-5 specimen, (c) AT800-20 specimen, (d-f) AT900-20 specimen, (g-i) AT150-20 specimen
图7
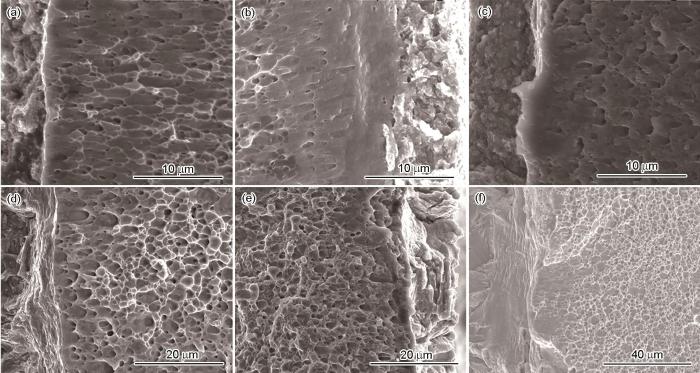
图7 预充氢试样断口边缘区域断裂形貌
Fig.7 Fracture morphologies of edge regions of hydrogen-precharged specimens: (a, b) AT700-5 specimen, (c) AT800-20 specimen, (d, e) AT900-20 specimen, (f) AT150-20 specimen
表2 充氢试样的氢含量、脆性断裂区深度和有效氢扩散系数
Table 2
动态充氢条件下,细晶AT700-5和AT800-20试样的断口较平坦,存在二次裂纹和许多小、浅、发育不良的韧窝,有一些区域呈QC状形貌,如图6a~c所示。这些形貌特征表明HELP机制控制这两个试样的HE,与Djukic等[4]和Verma等[5]的结果一致。随着晶粒尺寸的增加,脆性特征变得更加明显,AT900-20试样呈现更多QC形貌,如图6d~f,而粗晶AT1050-20试样则呈现混合的QC和部分IG (包含沿孪晶界开裂) 断裂形貌,如图6g~i,表明HEDE作用逐渐增强。而且,脆性断裂区域的深度增加,如表2所示,晶粒尺寸从3.7 μm (AT800-20试样) 增加到35.0 μm (AT1050-20试样),脆性区深度zb从15.3 μm增加到了178.0 μm,增加了超过10倍。以上观察和图3fHE敏感性指数数据一致,细晶试样的抗氢性能更高。表2显示细晶试样的含氢量也更低。
预充氢条件下,细晶AT700-5和AT800-20试样呈现较明显QC断裂特征,如图7a~c所示,粗晶AT900-20和AT1050-20试样呈现QC+部分IG断裂特征,如图7d~i所示。与动态充氢不同,预充氢试样从细晶到粗晶,断口形貌变化并不突然。表2显示,预充氢条件下,细晶、粗晶试样的氢含量变化也没有动态充氢显著,这与Bai等[12],Park等[13]和Koyama等[14]的结果类似。此外,晶粒尺寸从1.3 μm增加到35.0 μm,预充氢脆性区深度从7.6 μm仅增加到55.6 μm,增加幅度也显著小于动态充氢。脆性区深度代表了氢进入试样的有效扩散系数,考虑到两条件下的氢暴露时间显著不同 (预充氢时间为96 h,动态充氢时间不超过1.5 h),可推断预充氢条件下氢的有效扩散系数显著低于动态充氢。从这些结果可见,晶粒细化既没有显著改变预充氢试样脆性断裂特征,也没有明显降低氢扩散系数和进入试样的氢含量,因此没有降低HE敏感性,反而细晶试样的HE敏感性指数更高。
两种加氢条件下,试样HE敏感性呈现相反变化趋势,与之伴随的是进入试样的氢含量和扩散系数不同,考虑到晶界作为典型氢陷阱,影响的正是溶解度和有效扩散系数,因此,有必要从扩散和氢陷阱角度分析、理解晶界的作用,阐明其影响HE的内在本质原因。
3 分析讨论
根据氢陷阱理论,氢不仅分布于晶格间隙位置,还被位错、晶界等陷阱捕获。晶格间隙氢浓度CL=βNLθL,其中NL=5.2×1029 m-3为单位体积金属原子数,β=1为每个原子对应的晶格间隙位置数,θL为间隙被氢占据率。陷阱氢浓度CT,k =αkNT,kθT,k,NT,k 为单位体积氢陷阱数 (密度),αk 为每个陷阱供给氢占据的位置数,θT,k 为陷阱被氢占据率 (下标k表示陷阱的类型:k=d为位错,NT,k =
式中,Deff即有效氢扩散系数,为
总氢浓度Ctotal为
对fcc奥氏体,θT并不显著小于1,但为简化计算,通常仍采用
将Deff值代入
图8
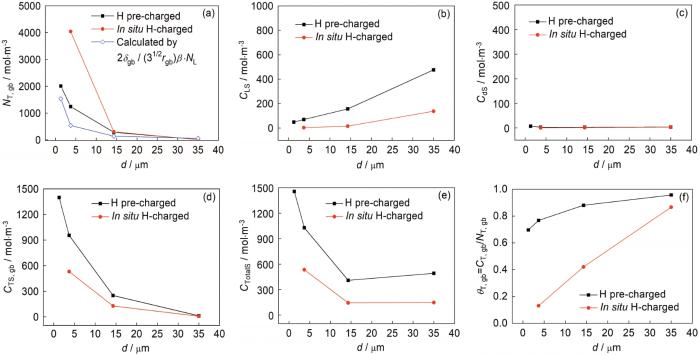
图8 试样内晶界陷阱密度及其充氢时表面处的晶格间隙氢浓度CLS、位错陷阱氢浓度CTS,d、晶界陷阱氢浓度CTS,gb、表面处的总氢浓度即有效氢溶解度CtotalS和单位晶界陷阱氢浓度CT,gb/NT,gb
Fig.8 Density of grain boundary traps (a), lattice hydrogen concentration at surface CLS (b), hydrogen concentration in dislocations CTS,d (c), hydrogen concentration in grain boundary traps at surface CTS,gb (d), total hydrogen concentration at surface CtotalS (e) and hydrogen concentration per unit grain boundary CT,gb/NT,gb (f) of specimens
进入试样的总氢含量可通过
式中,MH为氢摩尔质量,L为试样含氢段长度,P为含氢段周长。对
下面针对动态充氢和预充氢两条件从氢扩散和氢浓度两个方面进行进一步比较和讨论。
(1) 动态充氢条件
表2表明,动态充氢条件下Deff均比预充氢条件下Deff大约3个数量级。这表明动态充氢条件下氢向试样内部的传输被加速。导致氢传输加速的因素应有:表面裂纹扩展、裂尖应力集中和位错运动。事实上,在充氢试样表面可见大量表面裂纹,是椭圆形表面裂纹的形成、向两侧 (沿椭圆长轴) 和向试样内部 (沿短轴) 的扩展、多个表面裂纹的相互连接最终导致了试样的断裂。动态充氢拉伸时,氢在试样表面溶解使表面处氢浓度最大并逐渐向试样内部传输形成表面富氢层,拉伸应力也在逐渐增加,当应力和氢的组合达到一定水平时,在表面一些薄弱点形成椭圆形表面裂纹,出现裂尖,使氢 (充氢溶液) 与金属的接触面向试样内部推进,从而加速氢的传输,然而由于试样内部乏氢,裂纹并不会连续、高速向内扩展,裂尖表面溶解的氢在浓度梯度驱动、应力诱导和运动位错的携带下向裂尖前方高应力处传输并聚集,同时伴随着拉伸应力的继续增加,当应力和聚集的氢又达到一定水平时,引发新的裂纹形核并与原裂尖连接,造成裂纹向试样内再一次扩展。可见表面裂纹扩展使氢-金属接触面向试样内推进,使裂尖处保持高的浓度梯度,是动态充氢试样表现出较高的有效扩散系数的原因之一。Gerberich等[27]研究表明,裂尖应力集中引起的氢传输平均速度可表示为vH=VHD/(RT)·dσ/dz(VH=2×10-6 m3·mol-1为氢偏摩尔体积,dσ/dz≈3σys/(2d)为应力梯度,σys=σ0.2为屈服强度),代入相关数据可得vd<2×10-10 m·s-1。而位错移动携带氢的速度可表示为:
式中,为应变速率,ρdm为携带氢的位错的密度。由于ρdm<ρd,将表1中ρd代入
(2) 预充氢
预充氢试样,随着晶粒尺寸降低,HE不降反升,与动态充氢情况相反。图8f显示随着晶粒尺寸降低其CT,gb/NT,gb并不迅速降低,可见在拉伸之前预充氢的细晶和粗晶试样晶界局部氢浓度相差并不大。究其原因,可从氢传输速度角度分析,动态充氢试样氢传输和拉伸变形同时作用,由于表面裂尖向试样内部推进和位错运动导致氢扩散系数较高,氢会被快速带入试样内部纵深,对细晶试样,氢面对大量未填充空陷阱,被瓜分,从而CT,gb/NT,gb低,即使考虑拉伸应力和变形导致的新生位错,由
Kumnick和Johnson[29]测量了随塑性变形增加铁中陷阱 (不局限于位错) 密度变化,给出拟合式log10NT=A-2.33exp(-5.5εp),其中εp为塑性应变,常数A=23.26,该式被广泛使用[30,31]。Huang等[32]基于钢的实验分析、Sofronis等[33]基于理论模型 (只考虑塑性变形导致位错增加,εp≤0.5时ρd=ρ0+2ξεp,ξ为比例系数,εp>0.5后不变) 也分别给出了一组数据,这些数据和Kumnick和Johnson的数据变化趋势基本一致,若拟合,Wang等[34]认为所得拟合式只是代表初始陷阱密度的A值不同。如果认为塑性变形主要引起位错陷阱变化,本文试样的初始位错陷阱密度为NT,d≈3 mol·m3 (αd=10),代入上述拟合式可得A=26.64,高于Kumnick和Johnson的值,但接近于Huang等[32]的值。如果使用拟合式log10NT=26.64-2.33exp(-5.5εp) 来表示陷阱密度随塑性应变增加的变化,通过式 (
图9
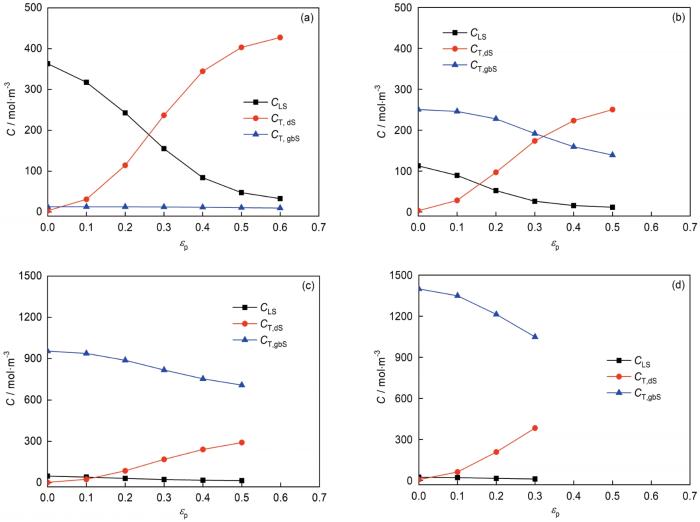
图9 随着拉伸应变增加预充氢试样表面处氢浓度的再分布
Fig.9 Hydrogen concentration re-distribution at the surface of hydrogen pre-charged specimens with the increase of plastic strain: (a) AT1050-20 specimen, (b) AT900-20 specimen, (c) AT800-20 specimen, (d) AT700-5 specimen
对粗晶试样AT1050-20,由于晶界陷阱数量较少,H主要位于晶格间隙中,如图8b所示,其在后续拉伸过程中向新生的位错陷阱供氢,因此随着塑性应变增加,晶格间隙中氢浓度降低,位错氢浓度增加,如图9a所示。但对细晶试样AT700-5,拉伸前氢主要分布于晶界陷阱中,如图8d所示,其在后续拉伸过程中向新生的位错供氢,随着塑性应变增加,晶界陷阱氢浓度降低,位错氢浓度增加,如图9d所示。更重要的是,可以看出,在同样的塑性应变下,细晶试样位错氢浓度更高。这便是因为细晶试样在拉伸之前在晶界存储 (陷阱) 了大量氢,如图8d所示,在拉伸过程中向新生位错供氢能力比粗晶试样中晶格间隙向新生位错供氢能力强,而且,细晶试样拉伸应力更高,事实上若考虑应力 (应力影响的晶格间隙氢浓度为CLσ=CL·exp(σh/RT),σh为表面处静水应力,可由应力应变曲线得到) 的影响,细晶和粗晶的差距将更高,结果细晶试样高的位错氢浓度和高的应力促进了HE的发生,这解释了预充氢条件下,细晶试样HE敏感性反而高的原因。当然,对AT700-5试样,高的αʹ马氏体含量对其显著高的HE敏感性应也有贡献,Wang等[35]研究表明,当304L钢中αʹ含量超过10%后,其对HE的加剧影响才会表现出来。
因此,动态充氢和预充氢这两种加氢条件下晶粒尺寸对HE呈现相反影响,本质上可归因于氢扩散和氢浓度差异,动态充氢是氢进入大量未填充空晶界陷阱,虽然有位错运动加速氢进入,但进入的氢面对大量晶界陷阱反而被大量陷阱瓜分,均匀化了氢浓度、降低了氢浓度。预充氢试样,在拉伸变形前,氢陷阱已被氢填充至高氢浓度,反而在后续变形过程中成为氢源,加剧了HE。
一直以来,向金属内引入氢陷阱是否可降低HE敏感性存在争议。早期,HELP机制的主要贡献者之一Sofronis及其合作者[36]基于
4 结论
通过重度冷轧和退火处理制备了不同晶粒尺寸的304L钢试样,采用单轴拉伸实验对比研究了预充氢和动态充氢两种加氢条件下晶粒尺寸对304L不锈钢HE敏感性的影响,表明两种条件下晶粒尺寸对HE的影响呈现相反规律,并根据氢含量测量、断口分析从氢陷阱、氢浓度的角度给出了解释。动态充氢条件下,表面裂纹扩展和位错运动能够加速氢进入试样内部,但随着晶粒尺寸降低,由于晶界的陷阱作用增加,氢有效扩散系数降低,同时由于进入试样的氢被大量晶界陷阱瓜分使每个晶界处的微观局部氢浓度降低,导致动态充氢条件下晶粒细化抑制钢的HE。预充氢条件下晶粒细化增加HE,是因为细晶试样在预充氢时进入并存储于晶界陷阱内高的氢浓度在后续拉伸过程中作为氢源向拉伸变形导致的新生位错供氢。晶界作为氢陷阱,能否降低ASSs的HE,本质上取决于其数量 (晶粒尺寸) 和加氢条件是否能够满足使氢分布均匀化,使局部氢浓度降低。
免责声明:本网站所转载的文字、图片与视频资料版权归原创作者所有,如果涉及侵权,请第一时间联系本网删除。
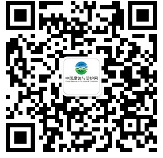
官方微信
《腐蚀与防护网电子期刊》征订启事
- 投稿联系:编辑部
- 电话:010-62316606
- 邮箱:fsfhzy666@163.com
- 腐蚀与防护网官方QQ群:140808414