合金涂层 | 喷涂丝材 | 喷涂电压/V | 喷涂电流/A | 喷涂距离/mm | 喷涂角度/(°) |
---|---|---|---|---|---|
NiAl | Ni95Al5 | 35 | 180 | 200 | 90 |
ZnAl | Zn85Al15 | 28 | 120 | 200 | 90 |
ZnNiAl | Ni95Al5(喷枪1),Zn85Al15(喷枪2) | 35(喷枪1),28(喷枪2) | 180(喷枪1),120(喷枪2) | 200 | 45(喷枪1),45(喷枪2) |
工业领域各种设备和金属管道表面经常因高温,与酸、碱等刺激性液体接触,而受到强烈的腐蚀作用[1]。国内外相关的研究数据显示,每年由于环境侵蚀报废的金属制品和材料占到了其全球年产量的20%~40%,在发达国家每年因金属腐蚀事故造成的经济损失约为GDP的1%~4%,而在我国这一数字达到近4%[2]。电弧喷涂涂层是通过电弧喷涂技术在钢结构表面形成的金属防护层,可以隔离强腐蚀介质,对基体起到很好的防护作用[3-4]。电弧喷涂涂层不仅要具备优异可靠的耐腐蚀性能,还应具备较好的耐磨性能[5]。电弧喷涂锌铝涂层是钢结构表面常用涂层,在恶劣的工作环境中,涂层中的锌元素会被优先氧化生成各种难溶产物如ZnO,难溶产物会黏附在涂层表面[6-7],沉积在涂层的孔洞内,防止腐蚀介质通过涂层,有效避免了基体的腐蚀。同时,在氧气供应充分条件下,涂层内的铝元素会与氧反应在涂层表面形成一层致密、性能稳定的Al2O3氧化膜,氧化膜凭借着良好的遮蔽和反射作用,取得较好的防腐蚀效果[8]。在强电解液环境中,ZnAl等阳极性喷涂涂层可以作为牺牲阳极,对整个钢结构起到阴极性保护作用[9-10]。镍基涂层是另一种具有优良耐腐蚀性能和良好耐磨性能的金属涂层,铝、铬、钛等元素固溶于镍基体中,可以增强镍基合金的耐蚀性、抗氧化性,延长基材的使用寿命[11]。王建新等[12]研究发现,在100 mm的喷涂范围内,以Ni-Cr-Ti合金丝为主要喷涂材料的电弧喷涂涂层的组织结构最致密,硬度等级最高,耐盐雾侵蚀能力最好。霍树斌等[13]采用双丝电弧喷涂工艺在6061-T6铝合金表面成功获得了NiAl-95/05、NiAl-80/20两种组分配比的NiAl涂层。试验结果显示,这两种涂层与基体材料的黏结强度都很高,没有出现明显的裂纹。另外,电弧喷涂NiAl涂层在高温、摩擦环境中有着广泛的应用前景[14]。ZnNi涂层同时兼具锌基涂层与镍基涂层的优势,适用于海洋环境中不锈钢零部件的表面防护[15],且ZnNi涂层的耐腐蚀性能随涂层中镍含量升高而增强[16]。由于金属镍的熔点远远高于金属锌的熔点,因此传统的熔炼法和电镀法都难以制备出镍质量分数为5%~15%的ZnNi涂层。闵捷等[17]通过机械合金化制备ZnNi合金粉末,再利用高能火焰热喷涂方式获得了ZnNi合金涂层,该涂层的耐腐蚀性能明显优于不锈钢。
在ZnNi涂层中引入Al形成ZnNiAl三元合金涂层,则有望进一步提升合金涂层的耐磨和耐腐蚀性能。然而,有关热喷涂工艺制备ZnNiAl三元合金涂层,以及涂层耐磨和耐腐蚀性能评价的研究鲜见报道。因此,作者采用双枪电弧喷涂方式,在Q235钢基体表面以一定倾斜角度同时电弧喷涂Zn85A115与Ni95Al5丝材,获得异种丝材电弧喷涂ZnNiAl三元合金涂层,同时分别电弧喷涂Zn85Al15丝材与Ni95Al5丝材获得ZnAl和NiAl合金涂层作为对比试样,并采用X射线衍射仪(XRD)、能谱仪(EDS)和扫描电子显微镜(SEM)对三种电弧喷涂合金涂层的物相、化学成分以及微观组织进行了表征,最后通过摩擦磨损试验和电化学测试研究了合金涂层的耐磨与耐蚀性能。
1. 试验
1.1 试验材料与喷涂工艺
基体材料为Q235钢,基体试样尺寸为100 mm×70 mm×2 mm。基体试样经丙酮清洗后进行表面除油、除锈等清洁处理,再用棕刚玉颗粒对试样进行喷砂处理,使基体试样具有一定的表面粗糙度,从而增强涂层与基体的结合强度。喷砂处理后,立即采用CMD-400电弧喷涂系统对基体试样进行电弧喷涂制备三种电弧喷涂涂层。喷涂丝材为国产Ni95Al5合金和Zn85Al15合金,丝材直径均为2.0 mm。各涂层工艺参数如表1所示,喷涂压力为0.6 MPa。涂层的厚度约为250 μm。喷涂完成后,线切割加工成10 mm×10 mm的小块,制成组织分析试样。
1.2 涂层表征方法
采用Bruker AXS D8-Advance型X射线衍射仪(XRD)对涂层的物相和晶粒尺寸进行测定。测定时,选用封闭式X射线衍射管,阳极靶为Cu靶,管电压为40 kV,管电流为30 mA,并使用连续扫描模式,扫描范围为20°~90°,步长为0.02°,扫描速率为5 (°)/min。利用JSM6360扫描电镜(SEM)观察各涂层的显微形貌,同时利用X-Max Extreme型能谱仪(EDS)分析涂层的化学成分。
涂层硬度试验在HXJ-HV800Z半自动维氏硬度计上进行,载荷为9.808 N,加载总时间为15 s。一个试样测试3次,结果取平均值。
采用Rtec-MFT5000多功能摩擦磨损试验机测试涂层的耐磨性。选用往复式摩擦磨损模式,摩擦副为直径5 mm的40Cr钢球,摩擦副与涂层试样表面进行点面接触的相对运动。其中,载荷为5 N,摩擦速率为10 mm/s,摩擦时间为600 s。
采用PARSTAT 2273电化学工作站对涂层进行电化学测试,评价其耐蚀性。工作电极为涂层,参比电极为饱和甘汞电极(SCE),辅助电极为铂丝。腐蚀介质为3.5%(质量分数)NaCl溶液。测试前,将涂层试样进行超声波清洗、酒精脱脂并在空气中干燥,为了确保测量的准确性,用环氧树脂垫片覆盖涂层表面,仅留下约1 cm2的工作面。测试结束后,根据Tafel外推法计算腐蚀电流密度(Jcorr)和自腐蚀电位(Ecorr)。
2. 结果与讨论
2.1 涂层物相
图1为三种电弧喷涂涂层的XRD谱。NiAl涂层的物相以面心立方(fcc)结构的Ni(Al)固溶体相为主,同时存在少量镍氧化物相(NiO)和铝氧化物相(Al2O3);此外,其衍射峰的半高峰宽相对较低,没有明显的背底衍射,这表明热喷涂所得NiAl涂层具有良好结晶能力,且晶粒尺寸相对较为粗大。ZnAl涂层具有以密排六方(hcp)结构Zn相为主、少量fcc结构Al相为辅的双相结构,在其XRD谱中未发现明显的锌氧化物相和铝氧化物相的衍射峰,这表明在电弧喷涂过程中,Zn85Al15丝材的喷涂粒子未发生明显的氧化现象;其半高峰宽相对较低,没有明显的背底衍射,这表明ZnAl涂层同样具有良好结晶能力,且晶粒尺寸相对粗大。ZnNiAl涂层的物相主要以hcp-Zn相、fcc-Ni(Al)固溶体相以及fcc-Al相为主;在各个物相衍射峰强度方面,hcp-Zn相特征峰较强,fcc-Ni(Al)固溶体相次之,fcc-Al相则最低,这表明在同时喷涂两种丝材的过程中,Zn85Al15丝材的喷涂效率比Ni95Al5丝材高,故ZnNiAl涂层中hcp-Zn相含量最高;在其XRD谱中未能观察到明显的氧化物衍射峰,这表明采用异种丝材喷涂过程中,喷涂粒子同样未发生显著的氧化现象。
2.2 涂层微观组织形貌
图2为采用单枪电弧喷涂所得NiAl与ZnAl涂层以及双枪电弧喷涂所得ZnNiAl涂层的表面宏观形貌。电弧喷涂Ni95Al5丝材所得NiAl涂层在基体表面覆盖均匀,颜色较深,涂层表面较为粗糙,存在一定的团聚状的喷涂颗粒。电弧喷涂Zn85Al15丝材所得ZnAl涂层均匀、致密,且较为平整,颜色较浅,表面粗糙度则相对较低,未出现显著的喷涂颗粒。双枪电弧喷涂异种丝材所得ZnNiAl涂层表面同样较为平整、致密,喷涂颗粒在基体上分布均匀,其表面粗糙程度介于NiAl涂层与ZnAl涂层之间。
从图3(a)中可以看出,NiAl涂层表面较为粗糙,上下起伏明显,且存在部分颗粒和孔隙,涂层致密度相对较低。从图3(b)中可以看出,ZnAl涂层表面则相对平整,表面上下起伏较低,表面粗糙度则相对较低,同时仍存在部分小颗粒团聚现象,表面致密度较高。从图3(c)中可以看出,ZnNiAl涂层的组织形貌较为均匀、致密,熔融的金属粒子在基体上分布均匀,仅存在极少量未熔融的金属粒子,几乎没有较大的未熔粒子,进一步确定ZnNiAl涂层表面粗糙度介于NiAl涂层与ZnAl涂层之间。
对三种涂层进行EDS分析,分析位置为图3中方形区域,结果如表2所示。结果表明,NiAl涂层中主要化学成分为镍元素与铝元素,还存在一定量的氧元素,且铝含量高于喷涂丝材Ni95Al5中,这是因为在喷涂过程中铝元素更易熔融并雾化喷涂至基体表面,且喷涂粒子易产生氧化现象。结合XRD分析结果可知,NiAl涂层中白色颗粒主要为NiO相以及少量Al2O3相。由此可以推测,在电弧喷涂过程中镍元素更加倾向于与氧元素相结合,一定量氧元素的存在会导致涂层中出现大量气孔等缺陷,使涂层致密度有所下降。相比之下,ZnAl涂层表面白色颗粒相则相对较少,结合能谱分析结果与XRD物相分析结果可知,ZnAl涂层中氧元素含量极低,且涂层中的锌含量与铝含量与对应喷涂丝材中锌、铝元素含量基本一致。因此,ZnAl涂层存在极少的孔隙与第二相,组织分布相对均匀。ZnNiAl涂层中则存在极少量的白色颗粒,能谱分析结果表明该涂层中锌元素含量最高,镍元素含量次之,铝元素含量较低,且含有少量氧元素。由此可知,在双枪喷涂过程中ZnAl丝材在电弧作用下较易发生熔融并被雾化喷涂至基材表面,其喷涂效率较高,故所得涂层中锌元素含量最高。结合XRD结果可知,相比于NiAl涂层,ZnNiAl涂层中氧化物颗粒数量显著下降,未出现显著氧化现象,且孔隙数量也有所下降,这在一定程度上提高了涂层的表面质量。
涂层 | 原子分数/% | |||
---|---|---|---|---|
Zn | Ni | Al | O | |
NiAl | 0 | 78.2 | 12.3 | 9.5 |
ZnAl | 83.5 | 0 | 14.6 | 1.9 |
ZnNiAl | 67.8 | 16.9 | 11.8 | 3.5 |
2.3 涂层耐磨性
对三种涂层表面进行硬度测量,其维氏硬度如表3所示。其中,NiAl涂层的硬度最高,ZnNiAl涂层的硬度次之,而ZnAl涂层的硬度则相对较低。由于NiAl镍基涂层中Ni(Al)固溶体相和NiO、Al2O3氧化物相均具有较高的硬度,因此NiAl涂层的硬度显著高于其他两种涂层。ZnNiAl涂层中也引入了部分硬度较高的Ni(Al)固溶体相和NiO氧化物相,因此相比于ZnAl涂层,其硬度也得到了显著的提升,这有助于提高涂层的耐磨性。
涂层材料 | 平均维氏硬度/HV |
---|---|
NiAl | 359.7 |
ZnAl | 131.5 |
ZnNiAl | 207.2 |
图4是在载荷5 N、摩擦速率10 mm/s条件下,三种涂层分别与40Cr钢球对磨过程中摩擦因数随时间变化的曲线图。由图4可知,在摩擦磨损试验的稳定磨损阶段,NiAl涂层的平均摩擦因数最大,ZnAl涂层的平均摩擦因数次之,ZnNiAl涂层的平均摩擦因数则最低。从图4(a)可见,在摩擦磨损试验的起始阶段,NiAl涂层的平均摩擦因数为0.57。这是由于在初始阶段,涂层表面的突出部分首先与摩擦副接触,此时接触面积相对较小,突出部分很容易被磨损,因此平均摩擦因数较小。随着摩擦磨损试验的进行,摩擦过程中产生的磨屑等产物逐渐填充至磨损表面孔洞处,并在磨球反复运动作用下,接触面积增大,进而导致摩擦因数陡然升高至0.86左右,然而随着摩擦磨损试验不断进行,磨损部位被压实,摩擦因数则逐渐趋于稳定。从图4(b)可见,ZnNiAl涂层的摩擦因数则随着摩擦磨损过程的进行缓慢增加,最后逐渐趋于稳定。在摩擦磨损过程中ZnNiAl涂层表面与磨球不断接触,涂层磨损表面微小孔洞以及凸起部位被不断压实,因此摩擦因数不断上升,并逐渐趋于稳定。从图4(c)可见,由于ZnAl涂层表面相对较为平整,在起始阶段其摩擦因数迅速上升,随着摩擦磨损过程的进行,不断产生的磨屑造成磨损表面粗糙度变化,从而引起ZnAl涂层表面摩擦因数波动。
图5为摩擦磨损试验后电弧喷涂涂层的磨损形貌。由图5(a)可见,NiAl涂层磨损后,磨痕深度较浅,表面存在一定磨屑碎片,呈现出一定黏着磨损特征。由于该涂层硬度相对较高,故电弧喷涂NiAl涂层的耐磨性较高。从图5(b)可见,在ZnNiAl涂层磨损后表面,除可观察到碎屑外,还可以观察到犁沟的存在,ZnNiAl涂层的磨损形貌呈现出黏着磨损和磨粒磨损复合特征,相比于NiAl涂层,该涂层磨痕宽度有所增加,且由于该涂层硬度较低,因此耐磨性有所下降。从图5(c)中可以看出,磨损后ZnAl涂层表面出现显著的犁状沟槽,且磨痕较深。ZnAl涂层由于硬度较低,发生了磨粒磨损,在摩擦磨损过程中,ZnAl涂层剥落,然后被碾碎成磨屑,使涂层的表面粗糙度增大,而在摩擦副往复运动过程中磨屑被压实,摩擦因数随之波动,这证实了此前根据摩擦因数变化所得结论。
2.4 涂层耐蚀性
图6为电弧喷涂涂层以及Q235钢在3.5%NaCl溶液中的极化曲线,依此计算所得自腐蚀电位与腐蚀电流密度如表4所示。由图6和表4可知,NiAl涂层的自腐蚀电位最高,ZnNiAl涂层、ZnAl涂层以及Q235钢基材的自腐蚀电位依次下降,且较为接近。比较发现,相比于Q235钢基材,ZnNiAl涂层的自腐蚀电位略微上升,但腐蚀电流密度显著降低。也就是说在Q235钢表面喷涂ZnNiAl涂层有助于全面提升基材的耐腐蚀能力。与Q235钢比,NiAl涂层的自腐蚀电位显著上升,但腐蚀电流密度也有所升高。这表明在Q235钢表面喷涂NiAl涂层后,材料的腐蚀倾向降低,然而NiAl涂层中的微孔洞为腐蚀介质进入涂层内部提供了通道,使得NiAl涂层在腐蚀过程中无法产生钝化效应,不利于基体耐蚀性的全面提升。在Q235钢表面喷涂ZnAl涂层后,自腐蚀电位和腐蚀电流密度均下降,这表明ZnAl涂层的腐蚀倾向大于Q235钢,ZnAl涂层可作为牺牲阳极对基材发挥保护作用。
材料 | Ecorr (vs SCE)/V | Jcorr/(A·cm-2) |
---|---|---|
NiAl涂层 | -0.59 | 2.71×10-5 |
ZnNiAl涂层 | -1.01 | 5.81×10-6 |
ZnAl涂层 | -1.02 | 6.79×10-6 |
Q235钢基材 | -1.05 | 2.13×10-5 |
值得注意的是,ZnAl和ZnNiAl涂层表面发生了钝化现象,形成高密度的ZnO和Al2O3等氧化物,从而抑制溶液中离子的扩散。这可能是由于涂层中的锌具有较强的化学活性,很容易与H2O反应生成Zn (OH)2,从而在涂层表面形成保护膜。随着与溶液接触时间的延长,腐蚀产物逐渐变成了具有非致密性的絮状物,而这些絮状物会反复产生并脱落,直到其厚度足以阻挡腐蚀介质时,才会发生钝化。在钝化区外,金属氧化膜被破坏,Cl-从涂层内部缺陷透过涂层,引起基体腐蚀。所以,在ZnAl涂层中添加镍元素,有助于涂层自腐蚀电位的提高,且在保证涂层较为致密的前提下,与腐蚀介质反应生成较为致密的NiO等氧化物,从而有效减缓腐蚀速率。铝元素由于活泼性低于锌元素而更易发生钝化,其腐蚀产物Al2O3比ZnO更致密、更耐腐蚀,最终形成的腐蚀产物Al (OH)3也更为致密,能够有效保护基体材料,使腐蚀电流密度下降。因此,电弧喷涂ZnNiAl涂层能够显著改善Q235钢的耐蚀性以及耐磨性能。
3. 结论
(1)NiAl涂层以Ni(Al)固溶体相为主,具有一定量的氧化物相,表明喷涂过程中其喷涂粒子发生一定的氧化现象,导致该涂层表面较为粗糙,且存在氧化相颗粒与微孔洞。ZnAl涂层为Zn相和Al相的双相组织,涂层表面较为致密,无氧化物颗粒存在。ZnNiAl涂层为Zn相、Ni(Al)固溶体相以及Al相的多相组织,且存在少量的氧化物颗粒与微孔洞,涂层微孔洞数量与表面粗糙度介于ZnAl涂层与NiAl涂层之间。
(2)ZnNiAl涂层的硬度为207.2 HV,且磨损形貌呈现出显著的黏着磨损与磨粒磨损复合特征,耐磨性介于ZnAl涂层与NiAl涂层之间。
(3)相比于Q235钢基材,电弧喷涂NiAl涂层的自腐蚀电位有所提高,耐腐蚀性能得到提升,然而由于涂层中存在微孔洞,腐蚀电流密度有所升高,对基材的保护效果产生一定的负面影响。电弧喷涂ZnAl和ZnNiAl涂层表面发生了钝化现象。与Q235钢比,ZnAl涂层的自腐蚀电位和腐蚀电流密度都较低,这表明该涂层在腐蚀过程中以牺牲阳极的方式对基材起到保护作用。在Q235钢表面电弧喷涂ZnNiAl涂层后,自腐蚀电位提升,腐蚀电流密度降低,该涂层较低的孔隙度以及镍元素的加入使腐蚀速率减缓,耐腐蚀性能得到全面提升。
免责声明:本网站所转载的文字、图片与视频资料版权归原创作者所有,如果涉及侵权,请第一时间联系本网删除。
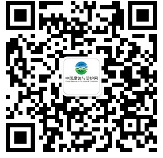
官方微信
《腐蚀与防护网电子期刊》征订启事
- 投稿联系:编辑部
- 电话:010-62316606
- 邮箱:fsfhzy666@163.com
- 腐蚀与防护网官方QQ群:140808414