元素 | Cr | Ni | Mo | Si | Mn | Cu | C | S | P | Fe |
---|---|---|---|---|---|---|---|---|---|---|
质量分数/% | 16.68 | 12.63 | 2.09 | 0.59 | 1.57 | 0.13 | 0.023 | 0.003 | 0.024 | 余量 |
316L不锈钢因其优异的力学性能及耐腐蚀性能而被广泛地用作压水堆核电结构材料。长期服役于一回路高温高压水环境中,316L不锈钢的力学性能、耐腐蚀性能及抗应力腐蚀开裂性能都会发生显著的劣化,这将严重制约反应堆的运行寿命并影响反应堆的安全运行[1-2]。因此,探究316L不锈钢在高温高压水中的应力腐蚀开裂机理及如何降低其腐蚀开裂敏感性是目前备受关注的问题之一[3]。
研究表明,奥氏体不锈钢表面氧化膜的形成受表面状态的影响,而氧化膜的厚度及化学组成将显著影响其在高温高压水中的应力腐蚀开裂行为[4-8]。WANG等[5]研究了表面粗糙度对不锈钢在压水堆一回路水环境中腐蚀行为的影响,结果表明,随着316L不锈钢表面粗糙度的降低,氧化膜内层厚度逐渐减小,氧化膜中铬含量逐渐增加,因此不锈钢的耐腐蚀性能提高。此外,在相同的腐蚀条件下,在304L不锈钢表面也观察到类似的结果[6]。HAN等[7]对比了不同的表面处理方法对316L不锈钢在模拟压水堆一回路水环境中腐蚀行为的影响,发现电解抛光后的试样表面形成了致密的富铬氧化膜,其显著提高了316L不锈钢的耐腐蚀性能。除此之外,MING等[8]研究了不同表面状态对焊接308L不锈钢在压水堆一回路水环境中的腐蚀影响,发现样品腐蚀后均生成了外层富铁、内层富铬的氧化膜,并且富铁氧化物的数量和氧化膜的厚度均随冷加工表面层中位错和亚晶界密度的增加而减小。综上所述,通过表面改性可改变不锈钢氧化膜的结构及化学成分,从而提高不锈钢的耐腐蚀性能,增强其抗应力腐蚀开裂敏感性。
已有氧化膜的存在将显著影响奥氏体不锈钢在高温高压水中的应力腐蚀开裂行为,如在应力腐蚀开裂过程中裂纹的起点往往位于氧化膜附近[9-11]。此外,在压水堆运行过程中管道表面已有的氧化膜会随腐蚀环境(温度、流速和水化学参数)的变化而发生显著变化,进而威胁到反应堆安全,如:在反应堆多次启动和停堆过程中,已有氧化膜的脱落会造成氧化物在管道中的堆积和放射性核素的富集,进而威胁到核电站及维修人员的安全[12-13]。在反应堆一回路中加入适量的锌可以调控氧化膜的组分,起到稳定氧化膜的作用,因此需要了解已有氧化膜的结构及化学成分[14-16]。在研究核电站注锌对结构材料腐蚀行为的影响时,绝大部分材料都经过了表面处理[17-19]。但是,在实际停堆注锌过程中,一回路结构材料表面已经形成了氧化膜。锌对有氧化膜和无氧化膜不锈钢腐蚀行为的影响有很大不同[20-21]。由此看出,表面氧化膜对材料后续腐蚀过程有重要的影响。
在上述研究中,研究者往往只关注于氧化物对裂纹扩展的影响及氧化物的脱落、转移和沉积行为,却忽略了已有氧化膜自身的化学成分及厚度对反应堆管道后续腐蚀行为及机理的影响。为此,作者在316L不锈钢试样表面预制了不同厚度的氧化膜,研究了预制氧化膜厚度对316L不锈钢在模拟压水堆一回路水中腐蚀行为的影响。
1. 试验
试验材料为商用316L不锈钢,化学成分如表1所示。将不锈钢板材切割成20 mm×10 mm×3 mm的片状试样,并在试样中心打孔(直径3 mm),用于悬挂试样。依次用240号至2000号碳化硅砂纸打磨试样,然后在丙酮和超纯水中超声清洗,最后烘干。将烘干后试样置于马弗炉内进行恒温预氧化处理,预氧化温度分别为600 ℃和800 ℃,预氧化时间分别为100、500、1 000 h,炉内冷却速率为40 ℃/min。预氧化完成后,通过扫描电镜(SEM)测量氧化膜厚度,如表2所示。在600 ℃下预氧化100 h后,氧化膜总厚度为0.02 μm,而氧化时间更长试样的氧化膜具有双层结构。
试样编号 | 预氧化时间/h | 预氧化温度/℃ | 氧化膜厚度/μm | ||
---|---|---|---|---|---|
总厚度 | 内层厚度 | 外层厚度 | |||
P1 | 100 | 600 | 0.02 | - | - |
P2 | 500 | 600 | 4.46 | 2.52 | 1.94 |
P3 | 1 000 | 600 | 8.61 | 2.72 | 5.89 |
P4 | 500 | 800 | 18.45 | 9.82 | 8.63 |
P5 | 100 | 800 | 22.71 | 8.57 | 14.14 |
P6 | 1 000 | 800 | 41.69 | 24.22 | 17.47 |
在0.5 L静态高压釜中进行模拟腐蚀试验。试验介质为模拟压水堆一回路水,即1 200 mg/L H3BO3和2.2 mg/L LiOH水溶液。试验前,往溶液中连续通入N2,将溶液中溶氧量控制在25 μg/L以下。腐蚀温度维持在(320±2) ℃,压力控制在(14±1) MPa,腐蚀时间为500 h。
采用精度0.01 mg的METTLER分析天平对腐蚀前后试样进行称量,采用扫描电子显微镜(SEM)和X射线能谱仪(EDS)分析试样表面的形貌及化学成分,采用X射线衍射仪(XRD)分析试样表面氧化物的物相。
2. 结果与讨论
2.1 预制氧化膜形貌
从图1中可以看出,随预氧化参数的变化,试样表面形貌也发生显著变化。当预氧化温度为600 ℃、氧化时间为100 h时(P1),由于铁含量高、铬氧化物的吉布斯自由能较低,试样表面首先形成致密且较薄的(Fe,Cr)2O3氧化膜,厚度为0.02 μm。当预氧化时间延长到500 h或1 000 h时(P2、P3),致密氧化膜向疏松多孔结构转变,氧化物之间的相互反应还会导致膜上附着有大量的FeCr2O4尖晶石条状颗粒;多孔结构氧化膜将加速氧气向内扩散,形成内层氧化物NiFe2O4和NiCr2O4,同时铁元素向外扩散会形成外层氧化物Fe2O3和FeCr2O4。当预氧化温度为800 ℃时(P4、P5、P6),试样表面均生成双层氧化膜,氧化膜成分与600 ℃时相似,但氧化膜厚度显著增加。这主要是因为温度升高将加速元素的扩散及氧化物形成。此外,试样表面氧化膜均出现了剥落的现象,剥落区表面为富铬氧化物,未剥落区为富铁氧化物,剥落原因主要是氧化物与基体材料的热膨胀系数不同[22]。
2.2 腐蚀后质量变化
在高温高压模拟压水堆一回路水中腐蚀500 h后,316L不锈钢试样质量变化与预制氧化膜厚度的关系如图2所示。由图2可知,当预制氧化膜厚度小于8.61 μm时,质量变化即单位面积试样腐蚀后质量与腐蚀前质量的差值(Δw)为正数,说明腐蚀后试样质量增加,且在此范围内随着预制氧化膜厚度的增加,Δw先减小后增大,当预制氧化膜厚度为4.46 μm时,Δw达到最小。当预制氧化膜厚度从8.61 μm减薄至4.46 μm时,试样表面氧化膜由疏松多孔的结构转变为致密结构,后者对试样起到保护作用,因此Δw减小。当预制氧化膜厚度大于8.61 μm后,Δw为负数,说明腐蚀后试样质量减小,且在此范围内随着预制氧化膜厚度的增加,Δw负向增大,最负达到-1.7 mg/cm2。随预制氧化膜厚度的增加,表面致密氧化膜逐渐转变为多孔状且生成了大量的(Fe,Cr)3O4白色条状颗粒,氧化膜孔隙率的不断增大促进了溶解氧向基体扩散并生成内层氧化膜FeCr2O4,而基体金属离子的选择性溶解和再沉淀则生成外层氧化膜Fe3O4,因此腐蚀后试样的质量损失量不断增大。该结果表明预制氧化膜厚度的增加将降低试样的耐腐蚀性能;当预制氧化膜厚度大于8.61 μm时,溶解氧和金属离子的移动速率减缓,预制氧化膜(Fe,Cr)2O3的溶解速率大于内层氧化膜FeCr2O4的生长速率,且外层氧化膜容易剥落,因此出现腐蚀质量损失且程度加剧。
2.3 腐蚀前后氧化膜结构
以试样P6腐蚀前后的XRD谱为例研究氧化膜结构,结果如图3所示。由图3可知,腐蚀前氧化膜的物相为铁铬尖晶石(Fe,Cr)3O4和赤铁矿(Fe,Cr)2O3,腐蚀后氧化膜中的(Fe,Cr)3O4相增加,(Fe,Cr)2O3相减少。产生该现象的原因是预制氧化膜中(Fe,Cr)2O3发生了溶解,溶出的部分金属离子再以(Fe,Cr)3O4的形式沉淀在试样表面,导致两种氧化物的含量发生变化。此外,在腐蚀后试样的XRD谱上还观察到316L不锈钢基体的衍射峰,这表明试样P6表面氧化膜在腐蚀后急剧减薄。
2.4 腐蚀形貌
从图4可知,随着预制氧化膜厚度的增加,试样表面的腐蚀形貌逐渐发生变化。腐蚀后氧化膜的亚表层由多面体晶粒组成,在多面体晶粒层上分布有尺寸较大的等轴晶粒,等轴晶粒和多面体晶粒的尺寸随预制氧化膜厚度的增加而增加。当预制氧化膜厚度从0.02 μm增加至41.69 μm(P1~P6),等轴晶粒的平均尺寸从0.60 μm增加至1.69 μm,而多面体晶粒的平均尺寸则从0.25 μm增加至1.03 μm。晶粒的化学成分如表3所示,结合SEM-EDS和XRD谱可知,等轴晶粒为Fe2O3,多面体晶粒则为Fe3O4。此外,从图4还可看出,氧化膜的孔隙率随预制氧化膜厚度的增加而增大。孔洞的出现将加速离子的扩散,从而加速材料的腐蚀,这表明预制氧化膜厚度的增加将降低316L不锈钢的耐腐蚀性能。
试样 | 原子分数/% | |||
---|---|---|---|---|
Cr | Ni | Fe | O | |
P1 | 4.12 | 1.37 | 39.06 | 55.46 |
P3 | 1.03 | 4.30 | 35.81 | 58.86 |
P4 | 5.25 | 1.63 | 39.54 | 53.58 |
P6 | 5.63 | 3.78 | 38.54 | 52.05 |
由图5可知,腐蚀后试样表面氧化膜仍为双层结构,结合图6可知,外层氧化膜为Fe3O4,内层氧化膜为FeCr2O4。当预制氧化膜厚度小于18.45 μm时(P1~P3),试样腐蚀后生成的氧化膜薄且均匀。而当预制氧化膜厚度进一步增加时(P4~P6),腐蚀后试样基体与氧化膜之间出现裂缝。由于氧化膜与基体具有不同的热膨胀系数,因此在升温和降温过程中氧化膜与基体出现裂缝。
图7为试样腐蚀后氧化膜厚度随预制氧化膜厚度的变化趋势,其中氧化膜厚度变化是指腐蚀前后氧化膜厚度的差值。由图7可知,随着预制氧化膜厚度的增加,试样腐蚀后氧化膜厚度先增加后减小。当预制氧化膜厚度小于18.45 μm时,试样腐蚀后氧化膜厚度增加,这是因为在高温高压水中,氧向金属基体内扩散使内层氧化膜厚度增加。当预制氧化膜厚度大于18.45 μm时,腐蚀后氧化膜厚度显著降低,这是因为腐蚀后外层氧化膜急剧减薄。
2.5 讨论
大量研究表明,奥氏体不锈钢在高温高压水中通过固态生长机理形成内层氧化膜,通过金属基体的溶解以及氧化物的沉淀形成外层氧化膜,即高温高压水中的溶解氧通过外层氧化膜的孔隙或缺陷向内扩散与金属基体形成内层氧化膜,而金属基体则通过选择性溶解向溶液中释放金属离子,部分金属离子再以氧化物的形式沉淀,从而形成外层氧化膜[23-24]。但是,当奥氏体不锈钢表面存在预制氧化膜时,阴阳离子的扩散行为将受到阻碍,并且预制氧化膜在高温高压水中也会发生溶解,这使得试样的腐蚀机理发生改变。
KUMAI等[25-27]在不同溶氧量的高温高压水中研究了Fe-Ni-Cr三元合金氧化膜的结构与成分并指出,在低溶氧条件下合金倾向于生成M3O4型氧化物,在高溶氧条件下则生成M2O3型氧化物。KIM等[28]研究了高温高压水中不同金属的电化学腐蚀电位与溶氧量的关系,发现溶氧量越高,合金的腐蚀电位越高,而Fe-Ni-Cr三元合金在高温水中的布拜图显示,合金在低电位下稳定的氧化物是M3O4,在高电位下稳定的氧化物则是M2O3[29]。综上所述,奥氏体不锈钢在低溶氧高温高压水中因较低的腐蚀电位更易形成M3O4型氧化物。在本试验的模拟压水堆一回路水环境中,溶液中溶氧量控制在25 μg/L以下(属极低溶氧量),预制的(Fe,Cr)2O3氧化膜将发生溶解,试样表面更易生成尖晶石氧化物(Fe,Cr)3O4,这与试样表面形貌随腐蚀时间的变化相吻合,如图8所示。从图8可知,腐蚀100 h后试样表面仍残留了多孔状Fe2O3氧化膜(标记为α),并伴有多面体尖晶石颗粒Fe3O4(标记为β)镶嵌在多孔氧化膜中形核长大;当腐蚀时间延长至500 h时,Fe3O4氧化层完全取代了多孔状Fe2O3氧化膜。
从上述研究结果可以推断,将试样P1置于低溶氧(<25 μg/L)高温高压水环境中时,M2O3氧化物不能稳定存在,试样表面预生成的(Fe,Cr)2O3将通过固相反应生成更为稳定的FeCr2O4尖晶石,反应如式(1)所示[29],而未参与固相反应的(Fe,Cr)2O3则发生溶解。基于Fe-Cr-Ni三元合金在高温水中的布拜图可知,溶解到高温高压水中的铁离子将以M3O4氧化物的形式沉淀,并促进FeCr2O4尖晶石的进一步长大,反应如式(2)所示。
|
(1) |
|
(2) |
上述腐蚀过程将导致试样表面(Fe,Cr)2O3含量降低,Fe3O4和FeCr2O4含量增加,这与图3所示试样腐蚀前后XRD图谱的变化相吻合。
当预制氧化膜厚度增加(试样P2~P4)时,预制氧化膜转变为多孔状结构,如图1所示。多孔状氧化膜将加剧溶解氧向基体内扩散和金属离子向外扩散。溶解氧与基体发生反应形成富铬的内层氧化膜,如式(3)~(6)所示,从而导致内层氧化膜厚度增加及腐蚀后试样质量增加。此外,阳离子从基体向外扩散与溶解氧结合形成Fe3O4颗粒,进一步导致腐蚀后试样质量增加和外层氧化膜厚度增加。
|
(3) |
|
(4) |
|
(5) |
|
(6) |
由于预制氧化膜(Fe,Cr)2O3在低溶氧环境中不稳定,部分氧化膜将溶解到高温高压水中,导致外层氧化膜厚度减薄,但内层氧化膜的增厚速率快于外层氧化膜减薄速率。从腐蚀后试样的质量变化(见图2)可以推测,预制氧化膜(Fe,Cr)2O3层溶解造成的质量损失与内层氧化膜增厚导致的质量增加将达到动态平衡。由此推断,存在一个临界的预制氧化膜厚度使试样腐蚀前后质量保持不变。
当预制氧化膜厚度进一步增加时(试样P5与P6),虽然多孔氧化膜能够加速阴阳离子的扩散,但氧化膜厚度较厚,离子扩散所需时间增加,无法为外层氧化膜生长提供足够的金属离子。因此,预制氧化膜(Fe,Cr)2O3层的溶解与尖晶石在内层氧化膜的沉淀之间的动态平衡被破坏,此时外层氧化膜(Fe,Cr)2O3的溶解主导了腐蚀过程。当预制氧化膜厚度大于18.45 μm时,腐蚀后试样的质量损失及氧化膜厚度损失更为显著。
3. 结论
(1)当预制氧化膜厚度小于4.46 μm时,氧化膜为致密的(Fe,Cr)2O3,对后续腐蚀过程起抑制作用;当预制氧化膜厚度进一步增大时,(Fe,Cr)2O3晶粒逐渐被(Fe,Cr)3O4晶粒取代,氧化膜呈多孔状且孔隙率不断增大,使其耐腐蚀性能逐渐降低。
(2)腐蚀后预制氧化膜外层为Fe3O4颗粒,内层为FeCr2O4尖晶石,而(Fe,Cr)2O3逐渐消失;当预制氧化膜厚度大于18.45 μm时,腐蚀后氧化膜与基体之间出现明显裂缝,氧化膜容易脱落,因此试样质量减小且腐蚀程度加剧。
(3)预制氧化膜厚度存在一个临界值,使得溶解氧与基体新生成的FeCr2O4氧化膜的增量和预制氧化膜(Fe,Cr)2O3的溶解量达到动态平衡,腐蚀前后质量保持不变。
免责声明:本网站所转载的文字、图片与视频资料版权归原创作者所有,如果涉及侵权,请第一时间联系本网删除。
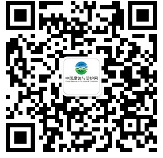
官方微信
《腐蚀与防护网电子期刊》征订启事
- 投稿联系:编辑部
- 电话:010-62316606
- 邮箱:fsfhzy666@163.com
- 腐蚀与防护网官方QQ群:140808414