1 单晶高温合金研发概况
单晶高温合金(如无特殊说明,文中单晶合金均指镍基单晶高温合金)主要用于制造航空发动机、燃气轮机热端涡轮叶片,其承温能力是提升发动机性能、效率、可靠性的关键技术指标。在美国、俄罗斯、德国、英国、法国、日本等发达国家,单晶高温合金的研发工作开展早、技术成熟度高,但对单晶高温合金研发及单晶叶片的研制一直非常重视。
单晶高温合金的研发起始于20世纪70年代的美国普惠公司(Pratt & Whitney),M. E. Shank、F. VerSnyder和A. F. Giamei等人在普惠的先进材料实验室中组建和领导了由材料性能、氧化和腐蚀、工艺、难熔金属、陶瓷、化学、X-射线衍射、微观结构等领域相关人员构成的研发队伍。到20世纪70年代中期,实验室已经在相图、微量元素、γ/γ'共格关系、位错、反相筹界、层错、位错动力学、析出相成分及动力学、γ'粗化、成分分配、微观偏析、晶界、碳化物、枝晶竞争生长、弹性各向异性等方面开展了大量工作,同时也针对定向凝固、型壳、雀斑等工艺问题进行了深入研究[1,2]。实验室开发了定向和单晶合金,与供应商密切合作,很快将定向铸件的合格率提升到90%。随着单晶叶片在直升机发动机PT6上的成功测试,到1981年,单晶叶片开始在军用和民用发动机上大量测试。
经过几十年的发展,目前在高强单晶高温合金的成分设计方面已经掌握了一些基本规律[3],例如:(1) 要有较高的Al、Ti、Ta含量以保证足够高的γ'相体积分数;(2) γ/γ'两相的错配度必须调整到很小以降低界面能;(3) 要有足够多的固溶强化元素W、Mo、Ta、Re、Ru,以保证高温蠕变性能,但这些元素的含量又需要精确控制以防止有害相的析出;(4) 必须保证足够的抗氧化性能。在长寿命抗热腐蚀单晶合金的成分设计中也发现了一些初步的规律[3,4,5],例如:(1) 需要保证足够高的Cr含量、较高的Ti含量以形成稳定的Cr2O3,抵抗熔盐热腐蚀;(2) Mo、W对热腐蚀性能不利,而适量的Ta、Re可能改善热腐蚀性能;(3) γ/γ'两相的错配度要调整到更小以保证合金长期的组织和性能稳定性。
单晶高温合金从第一代发展到第四代,贵金属元素Re、Ru含量不断增加,成本越来越高(典型第二代单晶合金含3%Re (质量分数,下同),第三代单晶合金Re含量达到6%,而第四代单晶合金中除了6%Re,同时添加了3%Ru)。合金承温能力以20~30 ℃/代的速率缓慢提升,但与此同时,单晶叶片的工作温度已经提高到1827 ℃,甚至更高,远远高于单晶高温合金的初熔温度(1280~1330 ℃)。因此单晶叶片工作温度的提升除了依赖单晶合金及防护涂层,更重要的是单晶叶片冷却技术的发展。从早期的实心无冷却叶片,到细直孔、大孔、蛇形/矩阵冷却通道,加上气膜冷却,甚至是复杂的双层壁冷却结构,叶片的冷却效率不断提升。复杂的冷却结构对单晶高温合金的工艺性能提出了很高的要求,如何控制复杂结构和高合金化带来的各种铸造和后处理缺陷也因此成为单晶高温合金研发的重要方向之一。
近年来,我国单晶高温合金研制与应用取得了显著进展,已经具备了单晶高温合金新材料、新工艺自主研发能力,并形成了生产装备比较先进、具有一定规模的生产基地,特别是近几年在军民融合相关政策的引导和推动下,出现了一批高温合金相关的民营企业,其中绝大多数聚焦于单晶高温合金母合金和单晶叶片的生产。
但是,目前国内航空发动机、燃气轮机用单晶高温合金及叶片大部分仍处于研发、试制、考核阶段,以需求牵引为主,仅仅初步解决了有无问题,单晶高温合金的研发水平与发达国家仍有很大差距,技术成熟度低,在工程应用中还面临很多问题。
本文概述了近年来单晶高温合金的研发进展。总结了单晶合金近几年的发展及其成分设计方法[6,7,8,9,10,11,12,13,14,15,16,17,18,19,20,21,22,23,24,25,26,27,28,29,30,31,32];介绍了单晶合金蠕变[33,34,35,36,37,38,39,40,41,42,43,44,45,46,47,48,49,50,51,52,53,54,55,56,57]、疲劳[58,59,60,61,62,63,64,65,66,67,68,69]、氧化和热腐蚀[70,71,72,73]机理,以及单晶合金中常见缺陷对力学性能的影响[74,75,76,77,78,79,80,81,82,83,84,85,86,87,88,89,90,91,92,93,94,95,96,97,98,99,100,101,102,103,104,105,106,107,108]。在单晶叶片制造工艺方面,总结了高速凝固、气冷、液态金属冷却、以及流态床冷却等几种常见定向凝固工艺的研发和应用现状[109,110,111,112,113,114,115,116,117,118,119],并介绍了单晶叶片中几种常见缺陷的形成机制和相关控制技术[120,121,122,123,124,125,126,127,128,129,130,131,132,133,134,135,136,137,138,139]。
2 先进单晶合金的研制
近十年,由于先进单晶高温合金成分设计空间越来越小,提高单晶合金综合性能的难度越来越大,在考虑单晶合金工艺性能、材料成本等因素的前提下,国外根据合金的具体用途,在大量前期积累的基础上,研发了多种“定制”合金。例如,与航空发动机比较,针对燃气轮机涡轮叶片服役温度较低、载荷稳定,但需要在热腐蚀环境下长期稳定工作的要求,研制了Cr含量较高而γ′体积分数稍低的SC16单晶合金[10]。此外,由于Re元素资源稀缺、价格高,国内外都发展了多种无Re或低Re的第二代和第三代单晶合金,以及热腐蚀环境下兼顾高温氧化和热腐蚀性能的无Re或低Re单晶合金。例如,GE公司为了降低第二代单晶合金中的Re含量,发展了性能接近René N5的René N515合金(1.5%Re),并逐渐替代René N5应用于航空发动机涡轮叶片[11]。同样地,Cannon-Muskegon公司也发展了1.5%Re含量的CMSX-8单晶合金,该合金在1038 ℃以下的蠕变寿命与CMSX-4合金相当,合金组织稳定性好,具有优异的抗疲劳、抗氧化和铸造性能,但CMSX-8合金超高温蠕变寿命(1094 ℃以上)明显低于CMSX-4合金[12]。
钴基单晶高温合金由于熔点高,具有与镍基合金类似的γ/γ'双相结构,因此可能发展成为工作温度更高的新一代单晶高温合金[13]。目前公开报道的性能数据中,钴基合金的蠕变性能已经与第一代镍基单晶高温合金水平相当(图1)[14,15,16,17,18]。然而,Co-Al-W系合金仍存在许多挑战,例如γ'相溶解温度较低且γ/γ'两相组织区很窄[8];合金经高温热暴露后主要形成CoO、Co3O4以及混合氧化物,因此高温抗氧化性能较差[19];考虑钴基合金的密度,其比强度仍低于第一代镍基单晶合金。进一步优化合金成分(如添加Ni、Cr、Al、Ta等)为新型钴基高温合金的发展提供了新思路。例如,随着Ni含量的增加,γ'相溶解温度逐渐提高[8];B和Cr的加入可以显著提高合金的抗氧化性能[20]。
图1
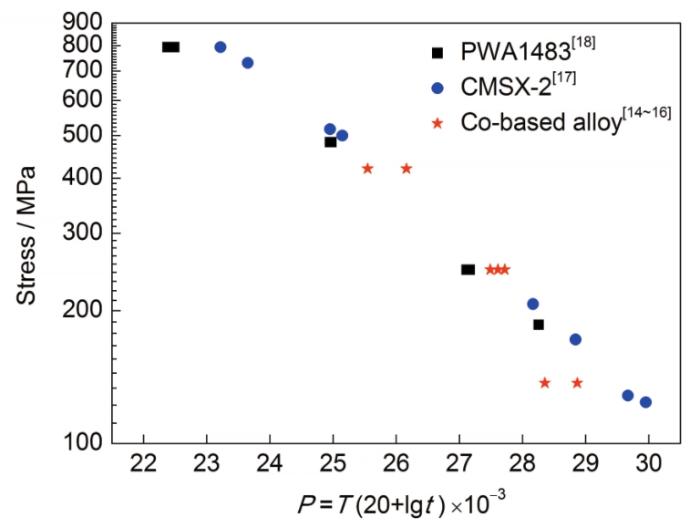
图1 钴基合金与典型第一代镍基单晶合金持久性能对比
Fig.1 Creep rupture properties of Co-based alloys and the 1st generation Ni-based single crystal (SX) superalloys (T—temperature, K; t—time, h; P—Larson-Miller parameter)
合金设计首先需要考虑材料的组织稳定性,相计算也因此被最早引入到了材料计算中,基于电子空位理论、结合次数和合金元素的d轨道能,发展和完善了多种相计算方法,模拟和预测了合金中TCP相的析出规律[23,24]。目前基于成分预测合金相组成的方法已经相对完善,如何建立合金成分与高温性能之间的量化关系,是单晶合金设计的关键。德国拜罗伊特大学的Fleischmann等[25],通过深入研究含不同难熔元素的单相γ固溶体合金的蠕变性能,确定了不同难熔元素的强化效果及其之间的量化关系;埃朗根-纽伦堡大学的Singer研究组[26]提出了合金强度可由固溶强化指数表示,并建立了固溶强化指数与关键难熔元素的量化关系;英国牛津大学Crudden等[27]则针对γ'相强化机制,确定了反相畴界与合金元素的关系,提出了合金屈服强度与反相畴界的量化关系模型。
从公开的文献报道看,目前单晶合金成分设计方法方面的研究主要集中在英国、德国和日本等几个研究所和大学(表1)。日本国立金属材料研究所(NIMS)等机构在20世纪80年代就提出了ADP (alloy design program)单晶合金设计理论[28,29],基于大量实验通过计算机回归处理确定了合金性能与元素的最佳匹配关系,指导了高强抗热腐蚀合金、低Re高强合金及含Ir单晶合金等多种合金的研制,但在ADP合金设计方法中并未引入合金强度与元素关系的量化模型。英国牛津大学Reed等[30]和剑桥大学Rae等[31]提出了ABD (alloys-by-design)单晶合金设计方法,引入一些限制参量(如抗氧化水平、蠕变强度和密度等),通过大数据计算筛选,发展了低Re单晶合金、兼顾氧化性能的低成本抗热腐蚀合金等,但合金蠕变强度与元素的关系主要基于扩散系数等因素建立,元素分配和界面强化等因素考虑不充分。德国埃朗根-纽伦堡大学的Singer研究组[32]则提出了MultOPT (numerical multi-criteria global optimization)单晶合金设计理念,基于多标准最优和半经验模型成功研制了无Re第二代单晶合金,但其合金强度与元素的关系只考虑了固溶强化机制,并未深入分析γ'相沉淀强化和界面强化机制的影响。
总体看来,计算材料学、大数据处理、机器学习等方法在单晶高温合金成分设计领域将占据越来越重要的地位,国内外在相关领域的研发投入也逐年增加,近年来国内启动的多项重点研发计划也均安排了单晶高温合金高通量设计、制备与表征的相关工作。但是,无论采用上述何种手段开展先进单晶合金的成分设计,全面可靠的数据积累与数据库构建都是基础。与国外相比,国内在这方面仍需开展大量工作。
3 单晶高温合金的性能
3.1 单晶高温合金的蠕变
离心应力导致的蠕变损伤是单晶涡轮叶片的主要失效机制之一,根据单晶叶片服役条件下的温度和应力分布情况,材料所受的蠕变大致可以分为2类:中温高应力和高温低应力蠕变。
单晶高温合金叶片部分冷却通道、叶根部位的工作温度为650~850 ℃,这些部位的蠕变主要是中温蠕变[33]。通常认为[33,34],中温蠕变过程中,a/2<110>位错在外加应力作用下,会在γ/γ'界面发生反应,形成的不全位错切入γ'相,产生超点阵内禀堆垛层错(SISF)、超点阵外禀堆垛层错(SESF)、反相畴界(APB)等复杂位错结构。位错反应形成的a<112>位错带切过γ和γ',会使蠕变速率迅速增加[33,34,35]。前期也有文献报道了其它可能的变形机制,例如a/2<110>位错直接切入γ'并产生APB[36]或a/2<110>位错在界面发生分解反应等[37]。表2[33,34,36,37,38]对比了文献中报道的几种中温蠕变机制。本课题组在对第一代单晶合金760 ℃、600~850 MPa蠕变中断样品的观察中发现,表2中几种不同的蠕变机制可能与蠕变应力相关,随应力提高,a/2<110>位错分解机制逐渐占主导地位[38]。
图2
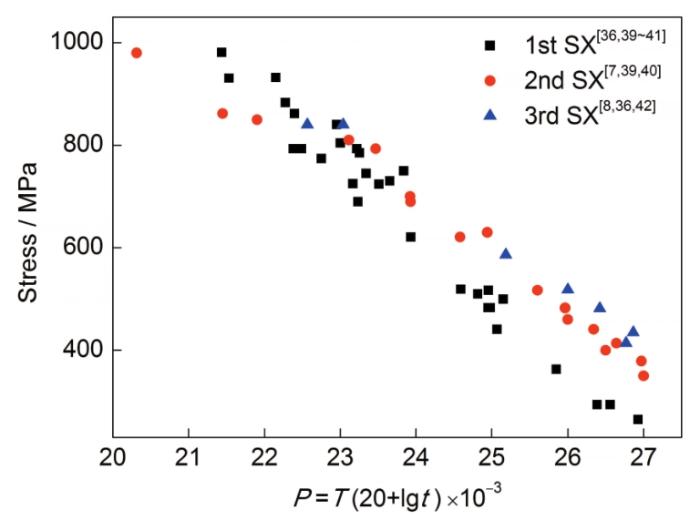
图2 不同代别单晶高温合金的持久性能对比
Fig.2 Creep rupture life of different single crystal superalloys
在高温低应力蠕变初期,大量位错在基体内快速萌生和增殖。随蠕变进行,位错在γ'界面塞积。基体中不同滑移系的界面位错在温度、外加应力、错配应力以及位错之间应力场的相互作用下发生反应,形成界面位错网[43,44,45,46,47] (图3[47])。高代别单晶合金中由于添加了Re、Ru,增大了γ/γ'两相界面的晶格错配度,使位错网间距减小[44,45,48],位错网阻碍了γ基体通道中的位错滑移,位错切入γ'相也更加困难,因此降低了蠕变第二阶段的最小蠕变速率,延长了合金蠕变断裂寿命[44,48,49]。在外加应力和界面错配应力的共同作用下,γ基体水平和竖直通道中合金元素发生定向扩散,在稳态蠕变初期形成γ'筏化结构[43,47]。此后,γ'相不断被位错切割而导致筏形扭曲。切入γ'相的超位错,在γ'相中运动困难,其攀移控制着位错运动速率,一般认为这一切割机制与稳态蠕变中较低的蠕变速率有关[47,50,51]。
图3
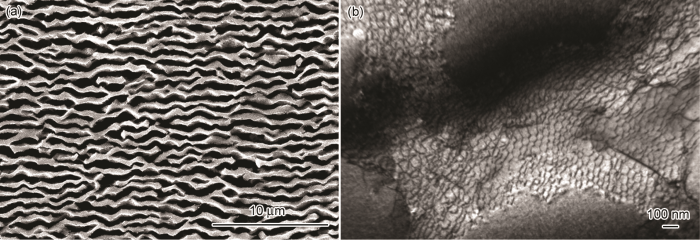
近几年,越来越多的先进测试和表征手段被应用到单晶合金蠕变机制的研究中。例如:Ram等[54]采用高角分辨电子背散射衍射(HR-EBSD)技术测定了蠕变过程中的晶体转动,发现蠕变位错主要起源于单个位错的增殖,而非小角晶界(<1°)附近的位错。Makineni等[55]采用原子探针测试了SISF和APB处元素三维分布情况,发现APB处富集Cr元素,APB前端富集W元素,溶质扩散使APB面积增大,促进γ'相的分解,导致蠕变抗力降低。Coakley等[56]采用同步辐射观察了750~900 ℃蠕变过程中合金错配度的实时变化情况。Ding等[57]采用80-200 Titan G2 TE球差校正场发射电子显微镜原位观察了拉应力作用下Re在单晶合金中的分布,发现Re富集在界面位错核心处,形成柯氏气团(Cottrell atmosphere),有效阻止位错运动和裂纹扩展。显然,高分辨电镜、三维原子探针、同步辐射等先进表征手段提供了更直观、更确切的实验证据,为进一步深入揭示单晶高温合金的蠕变机理提供了新的方法和思路。
3.2 单晶高温合金的疲劳
单晶高温合金服役中,会经历温度、应力或应变的循环反复变化,造成疲劳损伤。据不完全统计,近几年公开报道的关于单晶高温合金疲劳研究的文献中,60%以上关注低周疲劳,其次是高周疲劳,而热机械疲劳和热疲劳相对较少。
在单晶高温合金的低周疲劳研究中,主要涉及低周疲劳变形机理、损伤行为以及疲劳影响因素和疲劳寿命预测。室温低周疲劳变形,位错以分解切割、直接切割等方式切割γ'相,位错运动以平面滑移为主,形成滑移带是显著特征。中温和高温低周疲劳变形过程中,位错的运动方式主要为滑移、攀移、γ/γ'界面位错网络形成以及层错切割γ'析出相等。最近Wang等[58]还在高代次单晶合金的γ基体中观察到了高密度的堆垛层错和Lomer-Cottrell位错。
单晶高温合金低周疲劳寿命预测始终是人们关注的重要问题。基于晶体塑性理论的疲劳本构模型考虑了裂纹形核和扩展的关键参数,但对于局部应力集中情况不适用;临界距离理论考虑了裂纹萌生到扩展一定距离的应力集中,结合其它方法,如多轴疲劳准则、线弹性有限元方法等,可以预测疲劳强度和寿命。最近,结合晶体塑性和临界距离理论,Wen等[60]还提出了含致密气膜孔单晶的低周疲劳寿命预测模型,预测结果与实验结果符合较好。
相对蠕变,目前尚未建立疲劳寿命与单晶代次之间的明确关系,可能原因包括:首先,单晶代次的划分主要基于承温能力即蠕变性能,而非疲劳寿命;其次,与蠕变主要受温度和应力的影响不同,疲劳寿命的外界影响因素较多,包括温度、应力、应力比、应变幅、加载频率、加载波形等,综合考虑上述因素评价不同代次单晶高温合金的疲劳寿命仍有较大困难;第三,不同代次单晶高温合金疲劳寿命的数据积累仍显不足。
3.3 单晶高温合金的氧化和热腐蚀
单晶高温合金在服役过程中除了承受蠕变、疲劳等机械载荷,还存在明显的氧化和热腐蚀损伤。单晶合金的氧化是指合金在高温环境下与氧化介质反应生成氧化物的过程,而热腐蚀则是指在高温含硫气氛下合金与沉积在其表面的盐发生反应而引起的高温腐蚀。高温合金一般通过Cr和Al的选择性氧化形成致密的保护性氧化膜以提高抗氧化和耐热腐蚀性能。
3.4 单晶高温合金中常见缺陷对性能的影响
由于受叶片几何尺寸、合金成分、凝固工艺等因素影响,单晶叶片在定向凝固及随后的热处理过程中容易出现小角度晶界、条纹晶、杂晶、疏松、雀斑及再结晶等缺陷。图4是几种常见缺陷的典型宏观形貌。工程应用中,单晶叶片的非正常失效往往与上述缺陷密切相关。
图4

图4 单晶叶片中几种典型的缺陷
Fig.4 Typical defects observed in single crystal blade including low angle grain boundary (LAGB) (a), sliver (b), spurious grains (c), freckle (d), shrinkage (e) and recrystallization (RX) (f)
3.4.1 小角度晶界
为了平衡单晶叶片性能与成本,实际应用中往往允许单晶叶片在规定区域内存在6°~10°的小角度晶界。然而,单晶叶片在高温服役过程中,小角度晶界作为薄弱环节易产生蠕变或疲劳裂纹,导致叶片失效或断裂。
3.4.2 再结晶
图5
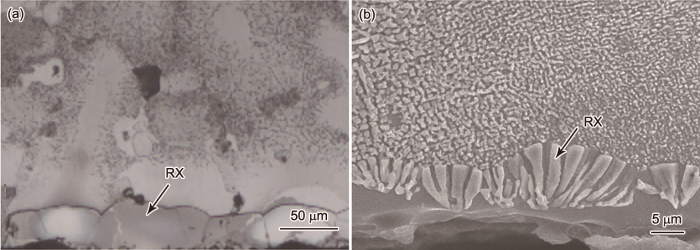
图5 在固溶温度以上形成的再结晶层和在较低温度下形成的胞状再结晶
Fig.5 RX layer formed at high temperature (a) and cellular RX formed at temperature below the solution temperature (b)
图6
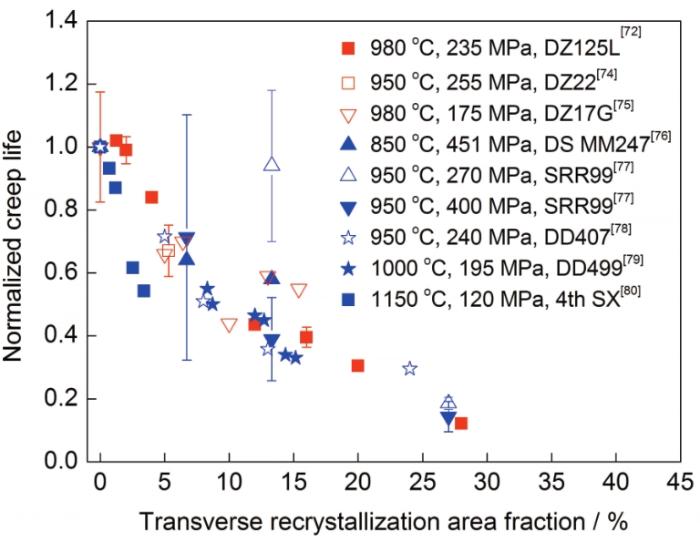
图6 再结晶对定向和单晶高温合金高温持久性能的影响
Fig.6 Effect of recrystallization on high temperature creep properties of DS and SX alloys
3.4.3 显微孔洞
微孔也会影响单晶合金的蠕变性能[95,96,97,98]。由于缺乏高温原位检测手段,针对显微孔洞在单晶合金蠕变中的演化规律及其对合金变形和损伤机制的影响目前仅有少数探索性工作。例如Link等[99]利用同步辐射研究了CMSX-4合金在1100 ℃蠕变变形前后的微孔形状。Komenda和Henderson[100]发现,与750 ℃中温蠕变相比,CMSX-4合金在950 ℃蠕变条件下,微孔体积分数增长明显较快。最近,在研究MC2单晶高温合金在高温蠕变中的微孔演化规律时发现[101],至少在蠕变的第一、二阶段,微孔的体积分数线性升高,随应变增加,在蠕变第三阶段微孔的体积分数可能显著升高,但体积分数的增加主要取决于塑性变形量而不是时间。这一观点在其它工作中也得到了验证[102,103,104]。
图7
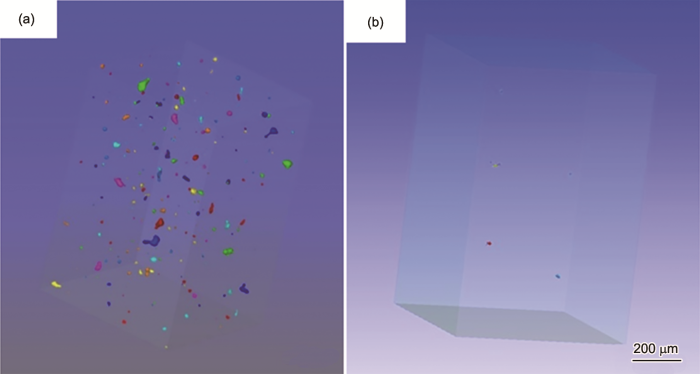
图7 利用X射线断层扫描(XCT)观察到的铸态和热等静压DD33单晶合金中的显微孔洞
Fig.7 Micro-porosities in as cast (a) and as hot isostatically pressed (HIPed) (b) DD33 superalloy
Color online
近年来,为了揭示单晶叶片服役损伤机制,除了深入研究单晶合金的变形和损伤机理、常见缺陷的影响,对单晶合金力学行为的相关研究越来越重视实际服役环境的影响。例如,非等温/多轴应力蠕变-疲劳行为研究,超温/氧化/薄壁/涂层/冷却孔结构/第二取向等对单晶合金蠕变-疲劳、热机械疲劳及冷热疲劳性能的影响等等。为实现近服役环境下的观测与表征,同步辐射、中子衍射、XCT、原位TEM和SEM,高通量表征结合多尺度-多场耦合模拟等手段在单晶高温合金组织与性能研究中逐渐普及。
4 单晶叶片的制备工艺
4.1 定向凝固工艺
单晶叶片的制造工艺复杂,涉及母合金纯净化冶炼、模具设计制造、陶瓷型芯和型壳及蜡型制造、定向凝固、无损检测、机械加工、涂层、热处理等等,其中定向凝固是关键工序之一,也是最容易出现缺陷、影响叶片合格率的工序。
LMC工艺采用低熔点液态金属Al或Sn作为冷却介质,尤其适合大尺寸定向和单晶叶片的制造[115]。俄罗斯采用液态Al为冷却介质,从20世纪80年代就开始单晶叶片的批产。国内借鉴欧美经验采用液态Sn为冷却介质,近年来解决了低熔点冷却介质污染、动态隔热层设计、高强抗热冲击型壳等问题,工艺日趋成熟,利用LMC工艺研制的多型定向和单晶涡轮叶片已经开始小批量生产。研究[116]表明,LMC工艺中使用的动态隔热层对提高定向凝固中的温度梯度起到了重要作用,动态隔热层可以随铸件的形状变化,有效隔离高温(保温炉)和低温(冷却介质)区,保证温度梯度。但在LMC-Al工艺中,冷却介质Al的密度低,很难找到合适的动态隔热材料。最近的研究工作[117]还发现,采用液态Sn为冷却介质时,冷却介质Sn与高温铸件接触,可能发生反应,影响铸件表面质量。结合工艺实验,利用ProCast软件可以比较准确地预测发生反应的临界铸件尺寸[118]。
FBC以悬浮在惰性气体(通常为Ar)中的稳定非金属粉末或颗粒为冷却介质,冷却介质温度可以保持在100~120 ℃,浇注后的铸件在悬浮的冷却介质中冷却,实现定向凝固。传统的FBC冷却介质通常为陶瓷材料(如刚玉砂、ZrO2陶瓷粉末等),这些材料的细小颗粒容易对合金和设备造成污染。最近德国埃朗根-纽伦堡大学进一步优化了FBC工艺[119],使用硬壳包覆的球状玻璃碳颗粒(尺寸约500 μm)作为冷却介质,解决了因颗粒破碎带来的污染问题;采用底吹Ar气,并在保温炉底的冷却介质上覆盖了一层密度较大的动态隔热材料,使大部分气体从保温炉侧面的出气通道流出。初步实验结果表明,采用该工艺使铸件的一次枝晶间距减小了40% (与HRS工艺比较),并且可以有效地避免冷却介质对铸件和设备的污染。
4.2 缺陷控制
4.2.1 晶体取向控制
单晶取向的控制方法通常有2种:螺旋选晶法和籽晶法。
图8
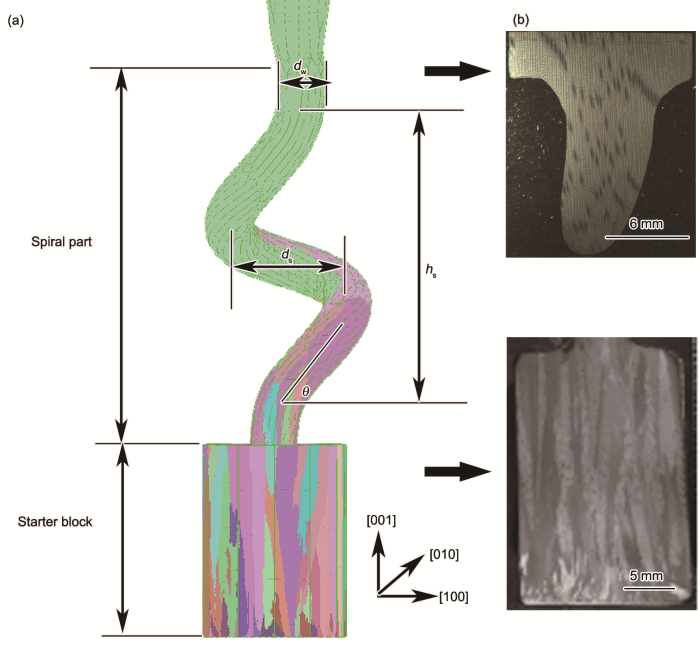
图8 螺旋选晶器的结构与典型组织
Fig.8 Typical configuration (a) and microstructures (b) of a spiral grain selector (hs—length of screw pitch, ds—diameter of spiral, θ—initial angle of spiral, dw—diameter of helicoid)
籽晶法是指在模壳底部安装特定取向的籽晶,浇注后籽晶发生部分熔化,晶体沿着与籽晶相同的取向生长获得单晶的方法。采用籽晶法可以获得三维取向可控的单晶,但在籽晶回熔区与模壳相接触的位置容易形成杂晶,而且隔热挡板参数、浇注温度、保温炉温度、冷却底盘的冷却效率等定向凝固工艺参数都会影响籽晶的回熔,因此与螺旋选晶法相比,籽晶法单晶生长的工艺难度稍大。
4.2.2 条纹晶
近期本课题组[128]利用XCT和EBSD技术,结合详细的金相观察,探讨了条纹晶的形成机制以及演化过程,发现条纹晶主要发生在型壳与枝晶形成的发散界面侧,大部分条纹晶相对基体既倾侧又扭转。条纹晶由靠近铸件表面的1~2根变形的三次枝晶发展而来。枝晶变形(应变)发生在固相体积分数较高的糊状区下部。相对于枝晶间熔体对流,热收缩应力对条纹晶的形成影响更大。条纹晶产生以后继承变形枝晶的取向继续生长,但条纹晶的上部没有应变。由于铸件复杂几何形状的限制,可能会导致个别条纹晶与基体的二次枝晶臂取向发生同步转动。大部分条纹晶在铸件表面不发生扩展,但总会缓慢向铸件内部扩展。条纹晶的扩展行为可能受枝晶尖端溶质场的影响。
4.2.3 再结晶
4.3 增材制造
由于增材制造类似焊接,在制备复杂几何形状零件时,难以获得稳定的温度场、热应力大,因此制备γ'相含量较高的高温合金很容易出现裂纹,制备单晶高温合金难度就更大。此外,目前商用的增材高温合金粉末主要有IN718、IN625和哈氏合金,单晶高温合金的粉末尚没有商业化。Liang等[141]通过优化激光增材制造(laser additive manufacturing,LAM)工艺,在SRR99基体上制备了约5.5 mm长的Rene N5单晶高温合金,样品无裂纹、表面无明显等轴晶层。与LAM工艺比较,由于整个过程在真空环境下进行,电子束选区熔化(selective electron beam melting,SEBM)在单晶高温合金制备中具有独特的优势。德国埃朗根-纽伦堡大学利用SEBM技术在单晶高温合金制备方面取得了较大进展,制备了直径约8.5 mm (棒状样品总直径约为12 mm,其中外围是有大量裂纹的等轴晶组织)、长度约60 mm的CMSX-4单晶样品,与铸造单晶样品相比,SEBM获得的单晶枝晶间距大幅减小,热处理后消除了微观偏析,高温和中温蠕变性能与常规铸造样品相当,但SEBM样品具有更好的低周疲劳性能和更好的组织稳定性[142,143,144]。
5 总结
单晶高温合金及叶片的研发和应用水平是国家工业基础的重要体现,近年来以需求牵引为主、技术推动为辅,我国单晶高温合金的研制与应用取得了显著进展。
单晶高温合金涉及的学科多,单晶叶片的制造要求高、容错空间小。单晶高温合金的成熟应用建立在对研发和制造体系全面深入的理解和长期积累的基础之上,因此相关的基础研究、应用基础研究、数据积累、工程化研究、部件测试和考核缺一不可,在单晶高温合金的发展中,既要加大投入,保证重要科研平台和队伍的可持续发展;又要统筹规划,避免低水平重复。
与发达国家相比,我们未来仍有大量工作需要深入:(1) 开展共性基础问题研究和数据积累,特别是推动单晶合金-涂层、单晶合金-型芯型壳、单晶合金-结构等交叉领域的研究;(2) 发展更精确和快速的计算模拟手段,对合金成分设计——包括多组元平衡和非平衡组织和性能预测、工艺设计和优化、寿命评估和预测等起指导作用;(3) 发展新工艺,不断提升单晶叶片制造技术;(4) 发展更高效快速的检测和修复技术;(5) 返回料的管理和高效利用。
免责声明:本网站所转载的文字、图片与视频资料版权归原创作者所有,如果涉及侵权,请第一时间联系本网删除。
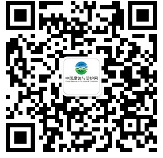
官方微信
《腐蚀与防护网电子期刊》征订启事
- 投稿联系:编辑部
- 电话:010-62316606
- 邮箱:fsfhzy666@163.com
- 腐蚀与防护网官方QQ群:140808414