作者结合新疆油田X井区的现场情况,先介绍了一种多元热流体地面管线监测系统,该监测系统可对全管线的腐蚀情况进行动态监测。然后,根据监测结果,挑选了具有代表性的失效样品进行分析,对多元热流体地面管道的损伤程度和腐蚀行为进行了评估。根据评估结果讨论了20钢地面管道的腐蚀机理,并通过室内试验进行了验证,以期为后续防腐蚀工艺的实施提供理论指导。
1. 地面管道监测系统
1.1 腐蚀监测方案
为降低输送成本,新疆油田X井区多元热流体的注采工艺采用了集输管线的运输方式,即一个多元热流体发生器同时用于多口稠油井[14]。为简化系统,以5口井为例介绍腐蚀监测方案设计思路,图1为腐蚀监测方案示意。选择配气量较大的3口井进行监测。由于多元热流体出口管线、多通阀计量配气管汇(深蓝色线)、单井注汽管线(黑色线)均为注入阶段流经管线,因此仅对靠近井口处的管线设置监测点,腐蚀监测点位于出口下游10 m范围内;采出阶段与注入阶段管道内流体不同,且流体组分更加复杂,需要对单井采油管线(蓝色线)、集油管线(黄色线)进行腐蚀监测,监测点位于出口下游10 m范围内;同时,集油管线末端需设置腐蚀监测点,监测点位于末端上游10 m范围内。对每个监测点采用腐蚀挂片方法进行动态监测。
1.2 腐蚀监测方法
采用带压开孔器对管线上的腐蚀监测挂片进行安装和拆卸(油气管道腐蚀挂片悬挂装置主要由装置主体、悬挂探杆、闸板阀、放空接头等零部件构成),该方法已在新疆油田进行应用[15]。常规腐蚀挂片只能在地面管道停运状态下安装,操作复杂,且不能实现对管线的实时监测。而本方案中所用开孔器可在带压状态下完成作业,因此可实现对管线的实时动态监测。同时,可通过腐蚀速率计算、化学成分分析等多种方法对挂片进行综合评估。
腐蚀监测周期可根据需要进行调整,定期取出腐蚀挂片进行腐蚀损伤程度评估。腐蚀监测挂片材料与监测管线材料相同,以便于监测管线的真实腐蚀情况,评估腐蚀行为。
2. 腐蚀行为综合评估
图2是根据腐蚀监测数据挑选的具有代表性的失效管段。对该失效管段进行宏观检查、壁厚测量、组织观察、腐蚀速率计算、化学成分分析、腐蚀产物分析,以综合评估地面管道在多元热流体中的腐蚀行为。由于失效管段与该处腐蚀监测挂片所处环境和所用材料均相同,因此腐蚀速率计算、化学成分分析、腐蚀产物分析都是针对腐蚀监测挂片进行的。
2.1 宏观检查
对失效管段进行宏观检查。结果表明,失效管段的管径为114 mm、长107 mm,一侧发生胀裂,胀裂侧呈现黑色,胀裂侧对立面仍可见绿色保护漆色;胀裂处最大张开口长217 mm、宽107 mm,距裂口660 mm处的管体位置处有环焊缝;管段上共有3处发生鼓包变形。该管段包含了目前地面管道失效的几种行为(开裂、鼓包等),分析结果对其他失效管件也有一定的参考价值。
2.2 壁厚测量
在第二个鼓包位置将失效管段沿径向切开,检查发现:管件横截面呈椭圆状,且壁厚不均匀,最小壁厚为6.30 mm,如图3(a)所示,最大壁厚为11.14 mm,如图3(b)所示。最小壁厚值与最大壁厚值相差1倍,管体变形严重,不符合API中最小壁厚的要求[16]。从现场管道腐蚀的严重程度猜测管道失效的原因为氢腐蚀,但多元热流体中腐蚀性气体为CO2、O2,不会引起该类腐蚀。同时,氢腐蚀按腐蚀程度分为氢腐蚀、氢脆和氢蚀三个阶段[17],管体具体处于何种阶段,还需结合后续化学成分分析进行判断。
2.3 组织观察
从失效管段的管体和裂口处取样,进行组织观察和分析,结果如图4和表1所示。由图4可见,失效样品的管体组织为铁素体(F)和珠光体(P);裂口处组织中除了铁素体和珠光体,还出现了贝氏体(B);裂口附近组织还出现了魏氏组织(WF),这说明腐蚀区域管道的化学成分发生了变化,这也是管体发生崩裂失效的原因之一。由表1可知:失效管段组织中共有3类(A、B、D)夹杂物,夹杂物等级介于0.5~1.0,这些夹杂物会严重影响管道的力学性能。
取样位置 | 非金属夹杂物 | 组织 |
---|---|---|
管体 | A0.5,B1.0,D1.0 | F+P |
裂口 | A0.5,B0.5,D1.0 | P+F+B(裂口);P+F+B+WF(裂口附近) |
2.4 腐蚀速率计算
利用超景深光学显微镜观察失效管段处腐蚀挂片的三维形貌,结果如图5所示。考虑到曲率的影响[18],测量得到图中最大蚀坑深度为148 μm,按照式(1)计算腐蚀速率。腐蚀挂片的腐蚀速率即为失效管段的腐蚀速率。结果表明,失效管段的腐蚀速率为8.206 mm/a。根据GB/T 18590-2001《金属和合金的腐蚀点蚀评定方法》标准,该处管道腐蚀情况极为严重。
|
(1) |
式中:Rpit为腐蚀速率,mm/a;dm为蚀坑最大深度,mm;t为腐蚀时间,d。
2.5 化学成分分析
使用ARL4460型直读光谱仪测量失效管段处腐蚀挂片的各元素含量,结果见表2。由表2可见,挂片中各元素含量均符合GB/T 699-2015《优质碳素结构钢》标准中对20钢的要求,这说明该管段并未进入氢蚀阶段。但其碳含量已经到达了标准的临界值,这说明如果腐蚀反应继续进行,管段就会进入氢蚀阶段。综合判断失效管道处于氢脆向氢蚀转化的阶段。
试样和标准 | 质量分数/% | |||||||
---|---|---|---|---|---|---|---|---|
C | Si | Mn | P | S | Cr | Ni | Cu | |
挂片 | 0.17 | 0.27 | 0.52 | 0.022 0 | 0.008 5 | 0.023 | 0.007 9 | 0.007 1 |
GB/T 699-2015 | 0.17~0.23 | 0.17~0.37 | 0.35~0.65 | <0.035 | <0.035 | <0.25 | <0.30 | <0.25 |
2.6 腐蚀产物分析
图6为失效管段处腐蚀挂片的表面形貌。从图6(a)中可以观察到腐蚀产物有明显的坑洞,且坑洞附近区域较为完好,相对比较光滑和致密。将该腐蚀坑区域放大后,可以观察到腐蚀产物排列不均,颗粒大小也不一致,如图6(b)所示。这说明管道局部腐蚀比较严重,且腐蚀后形成了不同的腐蚀产物膜,腐蚀产物膜出现了明显的分层。
将样品沿横截面切开后,观察其截面形貌,结果如图7所示。在图7(a)中可以更清楚地观察到腐蚀产物的分层现象。对图中腐蚀产物放大后可以发现:腐蚀产物膜下部区域中存在孔洞,这些孔洞导致了腐蚀坑的形成;腐蚀产物膜有两种颜色,代表两种不同的物质,这两种物质由不同的腐蚀反应产生。
2.7 腐蚀原因分析
多元热流体是天然气、柴油或原油、空气和水在燃烧室中密闭燃烧后产生的高压混合气体,主要成分是CO2、N2、H2O。其中,CO2和H2O会参与到地面管道的腐蚀反应[19]。在燃烧不完全情况下,剩余的氧气会严重腐蚀地面管道[20]。在多元热流体中20钢管道先发生了二氧化碳腐蚀,然后发生氧腐蚀。
(1)二氧化碳腐蚀
阳极反应:
|
(2) |
阴极反应:
|
(3) |
|
(4) |
|
(5) |
总反应:
|
(6) |
正常情况下铁与二氧化碳的反应会到此结束,但由于井筒中存在氧气,加之高温环境的影响,碳酸亚铁会与氧气反应生成疏松多孔的三氧化二铁,反应方程式见式(7)。这与化学成分分析中碳元素含量的测量结果是一致的。
|
(7) |
(2)氧腐蚀
阳极反应见式(2)。
阴极反应:
|
(8) |
|
(9) |
|
(10) |
总反应:
|
(11) |
在氧气腐蚀管道的过程中,随着腐蚀时间的延长,H2含量会逐渐增加。H2会对管道造成氢腐蚀,长期的氢腐蚀会使管道的力学性能急剧下降。
3. 室内试验验证
3.1 试验过程
为了探究氢腐蚀成因,选取20钢为试样,进行了动态腐蚀模拟试验[21]。采用控制变量法在不同试验条件下对试样进行腐蚀速率评价,以评估不同类型气体(CO2和O2)对腐蚀速率的影响程度。试验介质为模拟油田水,总压为6 MPa,温度分别为40、60、80、100、120、140 ℃,流速为0.4m/s、时间为24 h。
共设置5组试验,包括1组对照组和4组试验组,各组试验参数的设置如下:
(1)对照组:仅采用N2作为试验气体,CO2分压为0 MPa、O2分压为0 MPa;
(2)试验组1:采用单一CO2气体,CO2分压为1 MPa、O2分压为0 MPa;
(3)试验组2:采用单一O2气体,CO2分压为0 MPa、O2分压为1 MPa;
(4)试验组3:采用混合气体,CO2分压为0.2 MPa、O2分压为0.8 MPa;
(5)试验组4:采用混合气体,CO2分压为0.8 MPa、O2分压为0.2 MPa。
3.2 试验结果
图8为不同试验条件下20钢的腐蚀速率。在试验组1中当参与反应气体仅为CO2时,腐蚀速率随温度呈先增加后降低的趋势。这是由于温度的升高,分子运动速度加快,所以腐蚀速率增大;但当温度到达临界点(80 ℃左右)时,CO2在水中的溶解度随温度升高明显降低,因此腐蚀速率开始减小。试验组2~4与试验组1中,腐蚀速率随温度的变化趋势不同。试验组2~4中,随温度升高,腐蚀速率均呈现不同幅度的增大,这是由于这3组试验中O2对腐蚀速率的影响占主导作用,而温度对其溶解度的影响较小。对比试验组1与试验组2~4可得,O2对腐蚀速率的影响比CO2大,随着O2含量的增加,腐蚀速率明显增大,这与腐蚀过程的推测结果一致。
4. 结论与建议
(1)结合新疆油田X井区地面集输管道特点,设计了地面管道监测方案;采用的腐蚀挂片监测方法可实现对管线的实时动态监测。
(2)综合评估结果表明,20钢地面管道在多元热流体中腐蚀严重;表面显微组织中观察到贝氏体和魏氏组织,管道中碳含量减少;腐蚀产物主要成分为Fe2O3和Fe3O4。
(3)结合地面管道腐蚀行为的评估结果,对腐蚀机理进行了研究;在多元热流体中20钢管道先发生了二氧化碳腐蚀,然后发生氧腐蚀;反应物中O2对腐蚀速率的影响最大,并通过室内试验验证了这一结论。
免责声明:本网站所转载的文字、图片与视频资料版权归原创作者所有,如果涉及侵权,请第一时间联系本网删除。
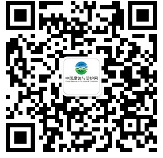
官方微信
《腐蚀与防护网电子期刊》征订启事
- 投稿联系:编辑部
- 电话:010-62316606
- 邮箱:fsfhzy666@163.com
- 腐蚀与防护网官方QQ群:140808414