元素 | Cr | Mo | Al | Re | Co | W | Ta | Ni |
---|---|---|---|---|---|---|---|---|
质量分数/% | 7 | 1.5 | 6.2 | 3 | 7.5 | 5 | 6.5 | 余量 |
航空发动机是飞机动力关键部件,是衡量飞机发展水平的重要标志之一[1]。随着航空发动机推重比增加,发动机燃烧室、涡轮机和压气机等热端部件的工作温度大幅提升,其核心部件如叶片、火焰筒、过渡段等需在恶劣的服役环境中长时间运行,即使采用先进定向凝固技术制备的单晶高温合金作为涡轮叶片,并辅以最新冷却技术,也难以满足抗氧化、隔热、耐腐蚀等实际要求[2-3]。热障涂层(TBC)为解决上述问题提供了有效的途径[4-5]。热障涂层的性能及寿命成为影响航空发动机性能的关键。一直以来,各国航空发动机推进计划均把热障涂层技术列为高压涡轮叶片的关键技术[6]。
目前应用最为广泛的TBC系统主要包括陶瓷隔热层、金属黏结层、高温合金基体以及在陶瓷层与黏结层之间形成的以氧化铝为主要成分的热生长氧化层[7-9]。其中,金属黏结层作为过渡层可降低陶瓷隔热层与金属基体之间的热物性差异[10],同时可为高温合金基体提供抗氧化及腐蚀防护[11]。因此,金属黏结层的热稳定性及高温性能直接决定了热障涂层的服役性能及寿命[12-13]。
目前,广泛应用的黏结层主要有铝化物涂层(如NiAl涂层)及MCrAlY(M为Ni、Co或Ni和Co)包覆涂层[14]。与MCrAlY涂层相比,NiAl涂层中Al含量更高,其抗高温氧化性能更好。随着铝化物涂层中各种改性元素的加入,其抗氧化性能可进一步提升,因此该类涂层被广泛应用于航空航天领域[15-17]。在众多改性铝化物涂层中,(Ni,Pt)Al涂层由于具有优异的抗氧化性能、良好的氧化膜黏附性能及与基体合金相匹配的力学性能而受到广泛关注。其中,Pt元素对涂层的有益作用表现在以下几个方面:第一,降低热生长氧化层/金属黏结层界面上有害元素如S的影响,减少界面孔洞的产生,提高氧化膜的黏附性能[18];第二,降低氧化膜的生长速率,从而减小氧化膜内的生长应力[19];第三,涂层表面高含量的Pt原子可牵引Al原子发生上坡扩散,从而在较长时间内保证涂层中有足够的Al原子可向外扩散形成氧化膜,并对有缺陷的氧化膜进行及时修复[20]。
(Ni,Pt)Al涂层虽然具有良好的抗高温氧化性能,但在长期的服役过程中,涂层表面会发生较为严重的起伏[21-23]。当产生表面起伏时,氧化膜内部应力急剧增加,从而加速裂纹产生及涂层剥落。研究表明,氧化膜出现裂纹或剥落是导致TBC系统失效的主要原因之一[24]。研究者们发现,在(Ni,Pt)Al涂层中添加一些活性元素如Hf、Y、Zr,Dy等可有效降低该涂层服役过程中的表面起伏,显著增强氧化膜的黏附性[25-29]。Hf元素的添加不仅可以有效抑制氧化膜/涂层界面孔洞的形成,降低服役过程中氧化膜的表面起伏现象[30],而且可以使涂层互扩散区(IDZ)上方形成富Hf带,从而降低涂层与基体之间的互扩散倾向。
当对涂层或合金进行多元素或双元素改性时,若一类活性元素在提高氧化膜黏结性方面有效,而另一类元素在降低氧化膜生长速率方面有效,则涂层的抗高温氧化性能可进一步显著提升[31-32]。Hf元素在氧化膜中以Hf4+的形式存在,可有效改变Al2O3缺陷浓度,从而提高氧化膜的黏附性能;而Cr是公认的可以促进Al2O3选择性氧化的元素[33],在涂层中添加Cr元素可以促进θ-Al2O3向α-Al2O3的转变,从而降低氧化速率[34]。因此,理论上Hf与Cr元素可产生协同效应,进一步提高(Ni,Pt)Al涂层的抗氧化性能。目前,关于Hf+Cr共改性(Ni,Pt)Al涂层的研究较为罕见。为了阐明Hf、Cr共改性对(Ni,Pt)Al涂层高温氧化行为的影响,作者先后在N5单晶合金上沉积了Ni-Cr复合镀层和Pt-Hf复合镀层及后续的气相渗铝,制备了Hf+Cr共改性(Ni,Pt)Al涂层,通过观察共改性涂层在高温氧化过程中的微观结构演变,讨论了Hf及Cr在(Ni,Pt)Al涂层抗氧化行为中的协同作用机制。
1. 试验
1.1 涂层制备
试验所用基体合金为第二代镍基单晶高温合金René N5,其名义成分如表1所示。用电火花线切割机将ϕ15 mm的圆柱形试件加工成ϕ15 mm×2 mm的圆片试样,并用砂纸(至800号)逐级打磨试样表面,然后在0.3 MPa压力下对试样进行喷砂处理;将喷砂后试样置于沸腾的50 g/L氢氧化钠水溶液中脱油10 min,然后分别在丙酮和酒精中超声清洗10 min。
将清洗后的试样分成三组。对其中两组试样分别进行电镀Pt和复合电镀Pt-Hf(Hf为纳米尺寸的金属颗粒),对另一组试样先进行复合电镀Ni-Cr(Cr为金属颗粒,粒径3~5 μm)再进行复合电镀Pt-Hf。Pt-Hf复合镀液组分为:8~15 g/L NaNO2、8~15 g/L Pt(NH3)2(NO2)2、0.01~0.02 g/L十二烷基硫酸钠、7~12 g/L Hf;Ni-Cr复合镀液组分为:150~200 g/L NiSO4·6H2O、10~20 g/L NaCl、100~150 g/L Na2SO4、30~40 g/L H3BO3、0.01~0.02 g/L十二烷基硫酸钠、15~20 g/L Cr。复合电镀工艺参数如表2所示。
工艺 | 温度/℃ | pH | 电流密度/(mA·cm-2) |
---|---|---|---|
Pt-Hf复合电镀 | 70~80 | 10~12 | 4~6 |
Ni-Cr复合电镀 | 30~40 | 3~5 | 10~20 |
将电镀后的试样置于真空管式炉中进行退火处理(1 050 ℃下保温1 h,真空度为10-3 Pa),以降低应力及调整基体表面的Pt含量。随后在化学气相沉积真空炉中进行气相渗铝(1 060 ℃下保温6 h)得到最终涂层。渗铝过程中通入Ar气作为保护气体,渗剂为由铁铝合金粉(Fe质量分数为49 %)及活化剂(NH4Cl质量分数1%~4 %)组成的混合粉末。
1.2 高温氧化试验
高温氧化试验在马弗炉中进行,试验温度为1 100 ℃,时间为500 h。试验前先将刚玉坩埚在1 150 ℃下烧至质量不变。试验过程中,将试样放入坩埚中保温,确保剥落的氧化膜掉落在坩埚内。每隔一段时间将装有试样的坩埚取出并冷却至室温,将坩埚和试样一同称量,天平精度为10-5 g。
1.3 结构表征
采用UItima IV型X射线衍射仪(XRD)对氧化后涂层表面的物相进行分析:以Cu的Kα衍射为入射线,加速电压为40 kV,步长为5(°)/min,范围为10°~90 °。采用LabRAM HR Evolution型激光显微共聚焦拉曼光谱仪对氧化物的组成进行了分析(激发光源波长为532 nm)。采用RTEC MFT-5000多功能摩擦磨损试验机测试氧化后涂层的表面粗糙度。通过Zeiss Sigma 300型扫描电镜(SEM)观察涂层的表面及截面形貌。其中,表面形貌采用二次电子模式观测,截面形貌采用背散射模式观测。为了防止氧化膜脱落,在制备截面形貌观测试样前对涂层进行化学镀镍。
2. 结果与讨论
2.1 电镀层的形貌
图1为三组试样经过不同工艺电镀后的表面及截面形貌。从表面形貌可以看出,三种镀层表面致密,无明显的针孔、裂纹等缺陷。Pt-Hf复合镀层中的Hf颗粒均匀分布在镀层表面,被包裹在Pt晶粒内。对比图1(b)及图1(c)可知,Hf颗粒具有相同的表面形貌,这说明Ni-Cr镀层的引入对后续Pt-Hf镀层的形态及结构没有影响。从截面形貌可知,三种镀层与基体界面以及镀层之间的界面结合紧密。镀层与基体界面存在少量黑色颗粒,该颗粒为喷砂过程中引入的Al2O3颗粒。Pt镀层及Pt-Hf镀层厚度均约为6 μm,Ni-Cr镀层厚度约为20 μm,其中Hf及Cr以复合颗粒的形式存在,且分布均匀。
2.2 涂层的物相组成
图2为三种涂层的XRD谱。由图2可知,三种涂层表面均为单一的NiAl相。Hf及Cr元素加入后,XRD谱中未出现新的物相,这表明Hf及Cr元素在涂层中以固溶体的形式存在。对比三种涂层的衍射峰位可知,(Ni,Pt)Al涂层及Hf改性(Ni,Pt)Al涂层中(Ni,Pt)Al相的峰位相对于标准NiAl峰位(虚线位置)向左发生偏移,见放大图。由布拉格方程(2dsin θ=nλ)可知[35],加入的Pt元素与Hf元素的原子尺寸较大,使得NiAl晶格增大,因此其峰位发生了向左偏移。Cr原子在NiAl晶格中的位置随NiAl相的成分及温度变化而变化,当Ni原子分数大于50%或温度低于1 000 K时,Cr原子在NiAl晶格中取代Al原子的位置[36]。本试验中三种涂层的Ni原子分数均为55 %左右,结合其XRD谱可以确定涂层中的Cr原子取代了部分NiAl晶格中的Al原子。由于Cr原子尺寸较Al原子小,当其掺杂进入NiAl晶格后,晶格收缩,因此Hf+Cr共改性(Ni,Pt)Al涂层中(Ni,Pt)Al相的峰位相对其他两种涂层发生向右偏移。
2.3 涂层的形貌
图3为三种涂层的形貌。可以看出,三种涂层表面均由等轴晶粒组成。由于晶界是元素扩散的快速通道,渗铝过程中,晶界位置快速生长,使得晶界位置略高于晶粒内部从而形成“山脊”,晶粒内部高度均匀,形成“山沟”。从截面形貌可知,三种涂层具有相似的结构,均由(Ni,Pt)Al层和互扩散区(IDZ)组成。值得注意的是,与(Ni,Pt)Al涂层和Hf改性(Ni,Pt)Al涂层相比,Hf+Cr共改性(Ni,Pt)Al涂层的(Ni,Pt)Al层最厚,且IDZ最薄。IDZ的形成与渗铝过程中涂层与基体间的元素互扩散有关。在渗铝过程中,Ni原子向外扩散形成NiAl涂层,促使基体表面γ/γ'相转变为单一的γ'-Ni3Al相甚至β-NiAl相。由于难溶元素在γ'-Ni3Al及β-NiAl相中的溶解度较小,相变发生后难溶元素原位析出形成IDZ。当Pt-Hf层与基体之间有一层Ni-Cr层时,Ni-Cr层可在渗铝过程中为涂层的生长提供Ni原子,从而最大限度地保留基体中的Ni元素,阻止基体表面相变的发生,抑制IDZ的形成。因此Hf+Cr共改性(Ni,Pt)Al涂层的IDZ层最薄。另一方面,Ni-Cr层中不含Al原子,其容纳Al元素的能力较高温合金基体强,在渗铝过程中Ni-Cr层可以吸附更多的Al原子。因此,经过相同的渗铝工艺后,Hf+Cr共改性(Ni,Pt)Al涂层的(Ni,Pt)Al层更厚。
2.4 涂层的高温氧化行为
2.4.1 氧化动力学分析
图4为三种涂层的氧化质量增加曲线及氧化速率常数。由图4(a)可知,在氧化过程中三种涂层的质量增加曲线均遵循抛物线规律,即在初期氧化阶段(前50 h)氧化膜快速生长,随后进入稳定阶段。氧化500 h后,Hf+Cr共改性(Ni,Pt)Al涂层的质量增量Δm最小,约为0.58 mg/cm2。三种涂层在初期氧化阶段(0~50 h)及稳定氧化阶段(50~500 h)的氧化速率常数Kp由公式(Δm)2=Kpt计算得到,如图4(b)所示。对比发现,在初期氧化阶段,Hf改性(Ni,Pt)Al涂层具有最低的氧化速率,而普通(Ni,Pt)Al涂层的氧化速率最大,Hf+Cr共改性(Ni,Pt)Al涂层的氧化速率位于二者之间。进入稳定氧化阶段后,普通(Ni,Pt)Al涂层、Hf改性(Ni,Pt)Al涂层和Hf+Cr共改性(Ni,Pt)Al涂层的氧化速率常数分别为2.36×10-4、3.13×10-4、5.79×10-5 mg2/(cm4·h)。由此可知,Cr元素的加入可有效降低涂层稳定氧化阶段的氧化速率。
2.4.2 氧化膜的生长及演变
氧化膜的生长及演变过程对涂层的抗氧化性能具有重要的影响。为了研究Hf及Cr元素的添加对(Ni,Pt)Al涂层氧化膜形成机制的影响,对三种涂层的初期氧化行为进行了研究。图5为在1 100 ℃下氧化不同时间后三种涂层表面氧化膜的拉曼光谱。由图5可知,三种涂层氧化10 min后,涂层中均存在α-Al2O3和θ-Al2O3两种物相。当氧化时间延长至30 min时,Hf+Cr共改性(Ni,Pt)Al涂层表面的θ-Al2O3消失,普通(Ni,Pt)Al涂层和Hf改性(Ni,Pt)Al涂层表面依然存在α-Al2O3和θ-Al2O3两种物相。氧化铝具有多种晶体结构,其中α-Al2O3最稳定。在α-Al2O3形成之前,涂层中会先形成一系列不稳定的暂态氧化铝。θ-Al2O3是其中最常见的一种,其生长速率快、不致密且呈针状。随着氧化时间的延长,暂态氧化铝会向稳态氧化铝转变,而转变时间的长短对涂层的抗氧化性能至关重要。Hf作为常用的活性元素之一,与O具有较大的亲合力,在氧化过程中能优先形成氧化物[37]。在氧化初期,尺寸较大的Hf4+掺杂在θ-Al2O3中会稳定θ-Al2O3的结构,延长其向α-Al2O3转变的孕育期,从而推迟了θ-Al2O3向α-Al2O3的转变[38]。添加了Cr元素的Hf+Cr共改性(Ni,Pt)Al涂层,在1 100 ℃下氧化30 min后,θ-Al2O3即可完成向α-Al2O3的转变。该结果表明,Cr元素的加入促进了θ-Al2O3向α-Al2O3的转变,从而在涂层表面快速生成致密的保护性氧化膜。Cr元素加速氧化膜的转变机理可以归纳为两个方面:一方面,在氧化开始时,由于涂层表面吸附了大量的O,涂层中的Cr、Al、Ni等元素一起发生氧化,形成混合氧化物,尺寸较小的Cr3+掺杂进入θ-Al2O3产生了与Hf4+完全相反的效果,即缩短θ-Al2O3向α-Al2O3转变的孕育期[39];另一方面,在转变过程中Cr2O3可作为α-Al2O3的形核位点,促进α-Al2O3在短时间内大量形核[40],从而降低涂层的氧化速率。
2.4.3 高温氧化后的物相组成
图6为三种涂层在1 100 ℃下氧化500 h后的XRD谱。由图6可知,在经过长达500 h的高温氧化后,三种涂层表面都能形成Al2O3保护膜。在Hf改性(Ni,Pt)Al涂层和Hf+Cr共改性(Ni,Pt)Al涂层中检测到了明显的NiAl峰,而在普通(Ni,Pt)Al涂层中仅检测到了γ/γ'相的峰,这表明普通(Ni,Pt)Al涂层中Al元素的消耗速率更快。
2.4.4 高温氧化后的形貌
图7为三种涂层在1 100 ℃下氧化500 h后的表面及截面形貌。氧化500 h后,普通(Ni,Pt)Al涂层氧化膜中出现了大量的剥落,见图7(a),氧化膜内部及氧化膜/涂层界面均出现了孔洞,并且氧化膜厚度不均匀,表面起伏严重,见图7(d)。在Hf改性(Ni,Pt)Al涂层表面及截面上均能观察到少量的剥落和裂纹。相比之下,Hf+Cr共改性(Ni,Pt)Al涂层表面氧化膜没有明显的剥落,仅出现了少量的裂纹,见图7(c),氧化膜致密连续,涂层内部γ'相较少,见图7(f)。
图8为三种涂层在1 100 ℃下氧化过程中的表面轮廓演变。图中的曲线的波峰和波谷分别代表涂层表面凸起和凹陷的位置。可以看出,在氧化开始前,三种涂层表面较为平整,表面粗糙度相差不大。随着氧化的进行,普通(Ni,Pt)Al涂层表面迅速发生起伏,氧化100 h后,其表面粗糙度明显变大。当氧化至500 h时,Hf改性(Ni,Pt)Al涂层的表面也产生了明显的起伏。相比之下,Hf+Cr共改性的(Ni,Pt)Al涂层表面起伏最小。
众所周知,在长期氧化过程中,(Ni,Pt)Al涂层中的Al元素消耗在两个方面:一方面,Al元素向外扩散与O反应生成Al2O3膜,当氧化膜发生剥落后,若涂层中仍有足够的Al元素,它会继续与O反应,修复氧化膜;另一方面,由于涂层和基体之间元素成分相差较大,在氧化过程中,Al元素会向基体发生扩散而流失。随着Al元素的消耗,涂层中Al含量下降,并发生如下相变:
|
(1) |
研究表明,相变的发生伴随着8%~32%的体积变化[41],并且该相变并不是在整个涂层内部均匀发生,而是优先发生在涂层的缺陷部位如晶界、孔洞处等,因此在这些局部位置产生内应力。随着Al元素的持续消耗,体积变化增大,产生的应力也会随之增大。当涂层局部内应力积累到一定值后,会通过蠕变变形的方式释放。在初始阶段涂层表面氧化膜随涂层一起发生变形,但陶瓷相的氧化膜与金属涂层具有不同的塑、韧性,二者协同变形过程中在氧化膜/涂层界面产生应力。当涂层/氧化膜界面处的应力大于涂层与氧化膜的结合力时,氧化膜便会出现裂纹,并最终导致剥落。
结合三种涂层的氧化动力学及氧化过程中的组织结构演变可知,普通(Ni,Pt)Al涂层氧化膜生长速率快,涂层内部Al元素消耗快,导致涂层内发生大量的相变,并伴随着产生较大的残余应力,促使表面出现了较为严重的起伏,最终导致表面氧化膜发生剥落。Hf元素的加入一方面可以降低稳定氧化阶段的氧化速率,减缓涂层内部Al元素的消耗速率。另一方面,在初期氧化阶段,Hf元素稳定了θ-Al2O3,使得这种疏松态的氧化膜能存在更长时间,提高了氧化膜的应力容量。随着Cr元素的加入,涂层的氧化速率进一步降低,涂层内Al元素因氧化膜生长而消耗的速率进一步变慢。同时,由于电镀过程中在基体和Pt-Hf层之间增加了一层相对较厚的Ni-Cr层,该复合镀层经过渗铝后吸收了少量Al原子,部分转变为Ni3Al相,从而形成了一个由Ni及Ni3Al组成的区域,该区域与基体相邻并与基体具有相近的Al原子及Ni原子浓度。因此,涂层与基体的互扩散驱动力降低,二者的互扩散更少,涂层通过互扩散而消耗的Al元素更少,涂层内的相变更为缓慢。
3. 结论
(1)通过复合电镀的方法在N5单晶合金上沉积了Ni-Cr层和Pt-Hf层,随后通过气相渗铝的方法,制备了一种Hf+Cr共改性(Ni,Pt)Al涂层。
(2)对普通(Ni,Pt)Al涂层、Hf改性(Ni,Pt)Al涂层和Hf+Cr共改性(Ni,Pt)Al涂层试样在1 100 ℃下空气气氛中进行了500 h的氧化试验,结果表明Hf+Cr共改性(Ni,Pt)Al涂层具有最好的抗高温氧化性能,涂层表面的氧化膜更加完整,表面起伏更小。
(3)Hf与Cr元素产生协同作用,提高涂层的抗氧化性能,Ni-Cr层可以作为(Ni,Pt)Al涂层与基体之间的缓冲层,抑制涂层制备及服役过程中涂层与基体之间的互扩散行为。
免责声明:本网站所转载的文字、图片与视频资料版权归原创作者所有,如果涉及侵权,请第一时间联系本网删除。
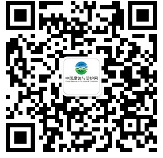
官方微信
《腐蚀与防护网电子期刊》征订启事
- 投稿联系:编辑部
- 电话:010-62316606
- 邮箱:fsfhzy666@163.com
- 腐蚀与防护网官方QQ群:140808414