管道信息 | 天然气管道 | 管道4(油气混输海底管道) | ||
---|---|---|---|---|
管道1 | 管道2 | 管道3 | ||
水深/m | 190~338 | 190~201.5 | 190~201.5 | 262.2~305.0 |
管长/km | 6.2 | 3.9 | 15.3 | 10.75 |
管道材质 | API 5L X70 | X65+316L | X65+316L | API 5L X65 |
外径×壁厚/mm | 273.1×15.9 | 168.3×12.7 | 168.3×12.7 | 外管559×15.9 mm;内管457×15.9 mm |
结构形式 | 单层不保温管 | 单层不保温管 | 单层不保温管 | 双层保温管 |
埋设方式 | 不埋设 | 不埋设 | 不埋设 | 不埋设 |
投产年份 | 2014年 | 2014年 | 2014年 | 2012年 |
设计年限/a | 20 | 20 | 20 | 20 |
涂层类型 | 3LPP | 3LPP | 3LPE | 3LPE |
涂层厚度/mm | 2.8 | 2.8 | 2.8 | 2.8 |
设计温度/℃ | 103 | 103 | 68 | 65 |
最大入口温度/℃ | 66.9 | 72.3 | 49.9 | - |
绝缘情况 | 管道与管汇中的基础结构绝缘,但与管汇中的管线存在电连接 | 管道与管汇中的基础结构绝缘,但与管汇中的管线存在电连接 | 通过金属焊接的方式与水下结构物PLET连接,且管道与管汇中的基础结构及管线均存在电连接 | |
ROV监测数据 | 2017年阳极均为B级;2018年出现6处阳极为C级,损耗严重;2019年发现7处阳极为C级,4处电位值不在正常范围内。位置均在靠近水下井口一侧 | 2017年出现1处阳极为C级;2018年发现3处阳极为C级,2处阳极电位不在正常范围;2019年发现5处阳极为C级,2处阳极脱落,1处电位值不在正常范围。位置均靠近水下井口侧 | 2019年有39处阳极消耗严重(C级)。对其中65个阳极进行电位测量,有12处阳极的测量值不在正常电位范围。位置位于PLET一侧区域管段范围内 |
深海资源开发已成为全球产业进步的重要标志[1],深海油气开发涉及大量钢铁结构物,如海洋平台、海底管道及水下设施等,海水具有极强的腐蚀性,为了减缓钢铁结构物在海水中的腐蚀,阴极保护已经在国内外海洋环境中得到了广泛的应用[2-4]。海底管道及水下设施普遍采用牺牲阳极阴极保护方式[5],牺牲阳极保护系统需要根据水下金属结构物的服役寿命进行设计,南海浅水区域四十多年的管道阴极保护应用案例表明,管道阴极保护设计的阳极使用寿命达到预期设计寿命。但近年来,南海东部海域出现了深水区域管段阳极加速消耗的情况,使深水中的阴极保护系统面临失效风险,这给我国南海东部海域海管的安全服役防腐蚀设计带来了新的挑战。
海洋环境所用阴极保护设计参数多依据浅水参数制定[6-10],而深海环境是一个与浅海环境截然不同的复杂腐蚀环境,深海环境中的溶解氧、温度及其中海底管道承受的压力都会发生较大变化,这些因素对阴、阳极的电化学性能均会产生较大影响,进而影响阴极保护参数的选择[11-12],此外,这些因素也可能导致阳极消耗异常。FISCHER等[13]进行了原位深海试验,发现在牺牲阳极保护过程中,金属材料表面很难形成保护性沉淀,这可能会造成牺牲阳极消耗增加。TRAVERSO等[14]对深海环境中金属及合金进行了腐蚀原位试验,发现受深海环境参数影响,铝合金及其他金属结构物的腐蚀速率会增加,其在深海环境中的点蚀和缝隙腐蚀比浅海环境中更严重。SUN等[15]模拟了350 m深水环境,研究了Al-Zn-In-Mg-Ti牺牲阳极在模拟深水环境中的腐蚀行为和性能,发现阳极在深水中的效率显著下降,与浅水环境相比,在此环境中对钢结构物进行阴极保护时,所需阳极数量增加了22%。LI等[16]研究了不同溶解氧条件下铝合金阳极的电化学行为,发现Al-Zn-In-Cd及Al-Zn-In阳极在低溶解氧条件下,表面溶解不均匀。也有研究表明,管道绝缘失效以及深海环境参数,如压力、溶解氧和温度等都可能加速海底管道上阳极的消耗[17-18],但目前国内外缺乏中国南海海域的阴极保护数据,其他海域的参数是否适用于南海海域也尚不明确,并且水下结构物之间情况复杂,海管绝缘情况不能确定,这导致海底管道牺牲阳极消耗异常的原因有待进一步分析研究。
针对南海东部出现的阳极消耗异常问题,笔者对目标海底管道进行了设计资料调研和阴极保护系统电场分析,并在此基础上开展了深水环境中海底管道阳极消耗异常的实验室评价,以期明确特定深水环境中阳极性能和管道表面钙质沉积层保护性能的变化情况,澄清可能存在的阴极保护系统影响因素,为南海东部海域海底管道的安全服役提供技术保障。
1. 阳极的基础参数调研与消耗异常原因分析
对南海东部海域相关海底管道阴极保护系统设计资料进行调研可知,其阴极保护系统参数按照国际标准ISO 15589-2 Petroleum, petrochemical and natural gas industries - Cathodic protection of pipeline transportation systems - Part 2: Offshore pipelines和DNV-RP-B401 Cathodic Protection Design制定,但在投产初期便发现区域管道阳极消耗量最高达到50%,且阳极电位不在正常范围,该阳极设计寿命为20 a,这些阳极不能达到阴极保护设计要求。
目标海底管道的基本参数与阳极消耗监测数据如表1所示,阴极保护设计参数如表2所示,结合由水下机器人(ROV)监测所得阳极消耗情况及评级结果(评级依据见表3),可知阳极消耗异常的海底管道具有以下共性:牺牲阳极消耗异常管道主要集中在某些局部区域,如靠近水下结构物区域,并且海管与水下结构物可能存在电连接,或在海底管道出入口靠近井口位置;阳极消耗异常海域水深为190~338 m。调研设计资料发现,与管道存在电连接的水下结构物(PLET平台)服役已超设计年限,推断其阴极保护状态较差。
保护电位/V | 阳极 | 设计电容量/(A·h·kg-1) | 阳极利用系数 | 阳极闭路电位/V | 涂层破损率(平均)/% | 裸钢电流密度/(mA·m-2) | |
---|---|---|---|---|---|---|---|
管道1 | ≥-0.8 | Al-Zn-In | 2 000 | 0.8 | ≥-1.05 | 2.34 | 125 |
管道2 | ≥-0.8 | Al-Zn-In | 2 000 | 0.8 | ≥-1.05 | 2.34 | 116 |
管道3 | ≥-0.8 | Al-Zn-In | 2 000 | 0.8 | ≥-1.05 | 2.34 | 93 |
管道4 | ≥-0.9 | Al-Zn-In | 1 600 | 0.8 | ≥-1.05 | 2.34 | - |
评价等级 | 状态 | 形貌 |
---|---|---|
A | 状态极好,完整边角,无麻坑(原始尺寸的95%~100%) | ![]() |
B | 状态较好,有原始边角和麻坑(原始尺寸的80%~94%) | ![]() |
C | 状态交叉,有大量麻坑,无规则形状(原始尺寸的50%~79%) | ![]() |
D | 状态很差,有较大麻坑,无规则形状(低于原始尺寸的50%) | ![]() |
由图1可见:被保护结构物极化电位与阳极极化电位存在电位差,从而构成电路回路。根据欧姆定律,回路中阳极输出电流ICP的计算见式(1),而根据阳极输出电流可计算阳极寿命L,见式(2)。
|
(1) |
|
(2) |
式中:Ep,s为被保护结构物极化电位,V;Ep,a为阳极极化电位,V;Ra,re为阳极对远地电阻,Ω;Rs,re为被保护结构物对远地电阻,Ω;Rc为阳极和结构物之间的焊接电阻,Ω;Wt为阳极质量,g;Cr为阳极消耗率,%;U为阳极的利用系数;E为阳极的电流效率。阳极消耗异常在式(2)中表现为阳极寿命L降低,其中Wt为定值,则阳极寿命下降原因可能为阳极输出电流ICP增加,或利用系数(U)和电流效率E的乘积与阳极消耗率Cr比值的下降。而阳极消耗率、利用系数与电流效率都为阳极材料电化学参数。因此,导致阳极消耗异常的原因可能为阳极输出电流ICP增加或阳极材料性能较差。其中阳极输出电流ICP可通过式(1)计算,在实际工况中保护结构物极化电位、阳极极化电位、阳极和结构物之间的焊接电阻变化不大[19]。而随着阳极正常服役,阳极表面腐蚀产物会使阳极对远地电阻增加,故如果阳极输出电流ICP升高,被保护结构物对远地电阻可能会降低。被保护结构物对远地电阻降低的原因可能为:管道防腐蚀层老化破损、管线钢表面钙质沉积层的变化以及海底管道与其他水下系统结构电连接使得被保护结构物对远地电阻降低。而3PP、3PE防腐蚀层性能较好,管段的平均防腐蚀层电阻率随服役年限的变化较小[20],且使用年限较短,管道阴极保护设计也已考虑管道破损率2.3%,故笔者暂不考虑防腐蚀层整体的老化、破损问题。
基于以上调研及分析结果,在实验室开展了管线钢裸金属的保护电流密度需求量试验、阳极电化学性能评价试验以及海底管道与水下结构物电连接的室内缩比试验,着重研究温度、海底管道与水下结构物电连接等因素对牺牲阳极消耗的影响,以期为明确阳极消耗异常的原因提供试验数据和理论基础。
2. 试验
2.1 管线钢的保护电流密度需求量试验
2.1.1 试样和溶液
试验采用X65管线钢,主要化学成分(质量分数,%)为:C 0.03, Si 0.17, Mn 1.51, P 0.024, S 0.005, Cr 0.03, Ni 0.17, Cu 0.04, Mo 0.16, N 0.006, Nb 0.06, Al 0.02, Ti 0.01, Fe余量。试样取自某服役海底管道,尺寸为10 mm×10 mm×5 mm(用于电化学测试)。用SiC砂纸(200~800号)逐级打磨试样表面后,用去离子水冲洗并用丙酮超声波清洗,冷风快速吹干,然后在试样背面焊接铜导线,用环氧树脂密封试样非工作面,留出一个10 mm×10 mm面作为工作面。根据ASTM D1141 Standard Practice for Preparation of Substitute Ocean Water,采用分析纯级试剂配制人造海水溶液,成分详见表4。
成分 | NaCl | MgCl2 | NaSO4 | CaCl2 | KCl | NaHCO3 |
---|---|---|---|---|---|---|
质量浓度/(g·L-1) | 24.53 | 5.20 | 4.09 | 1.16 | 0.695 | 0.201 |
2.1.2 恒电位极化测试
利用恒电位仪进行恒电位极化,并测量电流密度的变化情况。采用三电极体系,X65管线钢为工作电极,饱和甘汞电极(SCE)为参比电极,Pt电极为辅助电极。根据阴保设计参数,管道保护电位≥-0.8 V(相对于Ag/AgCl电极,SSC),故试验选取的阴极保护电位为-0.8 V(vs. SSC),恒电位极化时间为7 d。每组试验有3个平行试样,试验温度为(7±1)℃。
2.1.3 电化学阻抗谱测试
恒电位极化7 d后,进行X65管线钢的电化学阻抗谱(EIS)测试。EIS测试与恒电位极化测试一致,也采用三电极体系,即X65钢为工作电极,饱和甘汞电极为参比电极,Pt电极为辅助电极。在EIS测试之前,先进行开路电位测量,待其稳定后(偏移量不超过1 mV/min)再进行EIS测试。EIS测试频率为10 mHz~100 kHz,正弦交流激励信号为10 mV。
2.2 牺牲阳极电化学性能评价试验
2.2.1 试样及溶液
采用实际服役牺牲阳极,其化学成分(质量分数/%)为Zn 5.47,In 0.025,Si 0.085,Fe 0.086,Cu≤0.01,余量为Al。将阳极加工成ϕ16 mm×28 mm,表面积为14.07 cm2的圆柱形电极试样,并在试样中心加工ϕ3 mm的圆孔以便引出导线。辅助阳极采用碳素钢,尺寸为ϕ150 mm×280 mm,工作面积为840 cm2。采用数据记录仪UDL-2记录电路回路中通过阳极的电流以及阳极表面电位,试验电路如图2所示。试验采用人造海水溶液,成分见表4,采用恒温水浴锅控制温度为7 ℃与60 ℃,参比电极为Ag/AgCl电极。
2.2.2 试验方法
采用国标GB/T 17848-1999《牺牲阳极电化学性能试验方法》对牺牲阳极进行电化学性能测试,对阳极施加恒电流,第一天15 000 mA/m2,第二天4 000 mA/m2,第三天40 000 mA/m2,第四天15 000 mA/m2。内容有试验起始时的开路电位、闭路电位、电化学容量测量及牺牲阳极形貌观察。
2.3 海管与水下系统结构电连接的室内缩比试验
室内缩比试验采用工程中实际使用的管道,尺寸为ϕ57 mm×3.5 mm,材质为X65管线钢,长1 000 mm,管道两头采用绝缘密封处理,然后将处理好的管道与测试线焊接,并绝缘密封。模拟水下结构物的材质为普通碳素钢板。阳极材料为实际服役的Al合金牺牲阳极材料,尺寸为10 mm×10 mm×5 mm,绝缘密封并留下1 cm2工作面积,将其与管道测试线连接,与模拟管道和模拟水下结构物一起放置在海水试验池中,通过模拟管道和模拟水下结构物之间连接线的开合,获得有无电连接工况下,管道上不同位置的阳极输出电流,室内缩比试验测试示意如图3所示。试验采用人造海水溶液,成分见表4。
3. 结果与讨论
3.1 管线钢的保护电流密度
由图4(a)可见:随着试验时间的延长,电流密度逐渐减小,随后趋于稳定。当温度为7 ℃和60 ℃时,试样的初始电流密度分别为139 mA/m2与1 500 mA/m2,其稳定电流密度分别为112.78 mA/m2与30 mA/m2。与7 ℃时的相比,60 ℃时试样电流密度达到稳定所需的时间更短,且稳定电流密度更低,因此,低温条件下所需阴极保护电流更大。由图4(b)可见:随着试验温度升高,Nyquist图中的阻抗弧半径更大,即极化电阻Rp更大。因此,在-0.8 V的极化电位下,7 ℃条件下形成的钙质层比60 ℃条件下的差。
由图5可见,在7 ℃条件下,试样表面钙质沉积层稀疏且不致密,表面出现少量蚀坑;而当温度为60 ℃时,试样表面明显生成了一层白色物质,且表面结构比较致密。结合试样电流密度变化情况与EIS测试结果可知,低温条件下X65钢表面致密性较差,其稳定电流密度比60 ℃条件下的更大。7 ℃下试样的电流密度需求与设计电流密度相符,而60 ℃下试样的电流密度小于设计电流密度,故温度几乎不会导致牺牲阳极输出电流增大,牺牲阳极消耗异常。
3.2 牺牲阳极的电化学性能
由图6可见:两种温度条件下,阳极试样表面都以白色腐蚀产物为主,但在60 ℃条件下,阳极试样腐蚀坑更深,阳极表面溶解不均匀;而在7 ℃条件下,阳极表面溶解较均匀。清除表面腐蚀产物后可见:在60 ℃条件下,阳极表面发生严重的局部腐蚀,表面溶解不均匀;7 ℃条件下,阳极表面溶解均匀,腐蚀产物脱落,见图7。电化学性能测试结果表明,高温影响了该阳极材料的溶解性能。
由图8可见:60 ℃条件下,牺牲阳极的开路电位(OCP)为-1.09 V;7 ℃条件下,牺牲阳极的开路电位为-1.17 V。且60 ℃条件下,牺牲阳极的工作电位发生较大幅度的波动(-1.1~-0.7 V);7 ℃条件下,其工作电位约为-1.15 V。本试验结果表明,7 ℃条件下,阳极试样的开路电位更负,极化率更小,性能更好。
由表5可见:60 ℃下,牺牲阳极的实际电容量为2 627.5 A·h/kg,实际消耗速率为3.33 kg/(A·a),电流效率为91.86%;7 ℃条件下,牺牲阳极的实际电容量为2 778.7 A·h/kg,实际消耗速率为3.15 kg/(A·a),电流效率为97.15%。相较于60 ℃,7 ℃下阳极的电化学性能更好,但在这两种温度下,阳极的电化学性能都符合设计标准要求,结合阳极宏观形貌可知,高温是影响阳极加速消耗的潜在因素。
项目 | 60 ℃ | 7 ℃ |
---|---|---|
平均消耗质量/g | 0.901 7 | 0.895 6 |
实际电容量/(A·h·kg-1) | 2 627.5 | 2 778.7 |
实际消耗速率/(kg·A-1·a-1) | 3.33 | 3.15 |
电流效率/% | 91.86 | 97.15 |
3.3 室内缩比试验
由图9可见:当海底管道与水下结构物无电连接时,管道上1#位置阳极电流密度为1 250 mA/m2,2#与3#位置阳极电流密度分别为450 mA/m2和280 mA/m2,此时管道电位约为-1.10 V,故在此工况下管道阴极保护系统运行良好;当海底管道与阴极保护效果较好的水下结构物电连接时,水下结构物的阴极保护电位约为-1.1 V,管道1#、2#和3#位置的电流密度分别为1 100,800,900 mA/m2,与无电连接下的相比变化不大,阳极没有加速消耗的现象。
当海底管道与阴极保护效果较差的水下结构物电连接时,水下结构物的阴极保护电位约为-0.79 V,与之前的两种工况相比,阳极的电流密度大幅度升高,管道1#、2#和3#位置的阳极电流密度分别增加到44 000,21 900,16 500 mA/m2,管道上阳极消耗加速,并且越靠近水下结构物端,阳极的输出电流越大。
4. 结论
对南海东部海域出现阳极消耗异常的相关海底管道阴极保护设计参数调研显示,阳极消耗异常位置大多位于海管出入口处,该位置特点为温度高,并且靠近水下生产系统,管道与水下结构物存在电连接风险。基于资料调研,从海底管道阴极保护系统电场分布出发,探究了高温和电连接对阳极消耗异常可能存在的影响,具体结果如下:
(1)60 ℃条件下,铝合金牺牲阳极出现局部腐蚀,这对铝合金牺牲阳极的性能有一定的影响,但其电化学性能仍符合标准要求,即高温是阳极加速消耗的潜在影响因素。
(2)60 ℃条件下,X65钢试样表面生成的钙质沉积层的致密性相比7 ℃下的更好,且X65钢试样的保护电流密度需求量明显小于7 ℃下的。60 ℃和7 ℃条件下的电流密度需求都符合设计值,故温度不是导致牺牲阳极输出电流增大,牺牲阳极消耗异常的因素。
(3)当管道与水下结构物发生电连接时,若水下结构物的阴极保护条件较差,靠近水下结构物的局部管道区域的牺牲阳极输出电流将明显增大,会导致阳极使用寿命降低。管道与水下结构物的电连接是导致管道局部区域阳极加速消耗的重要因素。
(4)当水下结构物与管道电连接时,管道临近水下结构物区域内的保护电流需求量增大,建议在设计阶段考虑电流密度增加量,加密阳极排布;而对于目前已经出现加速消耗的阳极,可根据牺牲阳极实际的消耗率,计算电流密度需求,并依据相关的设计规范,在海管上加装阳极。
免责声明:本网站所转载的文字、图片与视频资料版权归原创作者所有,如果涉及侵权,请第一时间联系本网删除。
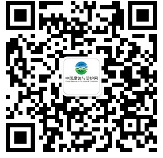
官方微信
《腐蚀与防护网电子期刊》征订启事
- 投稿联系:编辑部
- 电话:010-62316606
- 邮箱:fsfhzy666@163.com
- 腐蚀与防护网官方QQ群:140808414