试验材料 | 质量分数/% | |||||||||
---|---|---|---|---|---|---|---|---|---|---|
C | Mn | Mo | Cr | Ni | Cu | P | S | Si | Fe | |
L-1 | 0.119 | 0.54 | 1.04 | 9.0 | 0.19 | 0.17 | 0.013 | 0.002 | 0.62 | 余 |
L-2 | 0.118 | 0.38 | 0.98 | 9.02 | 0.13 | 0.06 | 0.01 | 0.002 | 0.43 | 余 |
随着石油、天然气等能源的开采环境日益苛刻,油井管材腐蚀已成为制约油气资源高效、安全开采的关键问题,而解决该问题的重要途径之一是选用经济合理的管材[1-3]。L80-9Cr马氏体耐热钢(以下简称L80-9Cr钢)作为API 5CT-2018《套管和油管规范》钢级,因兼具较好的耐蚀性、优良的力学性能及经济性,已被广泛应用于含CO2、H2S等腐蚀介质的高温高压井下环境中[4-5]。
L80-9Cr钢以L80钢为基础,在成分设计上,增加了Cr、Mo有益合金元素含量,提高了材料的回火抗力,进而获得稳定的回火马氏体组织,实现强度与韧性的完美匹配[6]。钢中主要强化相为分布在原奥氏体晶界及马氏体板条束间的M23C6(M主要是Cr)型碳化物[7-8]。有研究表明,M23C6型析出相对含Cr马氏体不锈钢的腐蚀行为存在重要影响,其形成往往伴随着周围Cr含量的降低,在碳化物与基体界面形成贫Cr区,从而降低该处钝化膜的保护性[9-10]。ZHAO等[11]利用扫描开尔文探针发现M23C6型析出相电位高于周围钢基体,贫Cr区电位低于钢基体,因此贫Cr区在腐蚀过程中将优先发生溶解,该区也往往被认为是点蚀的初始形核点。而非钝化体系含Cr钢中因Cr含量相对较低,其M23C6型碳化物的析出及分布特征对耐蚀性能的影响尚未明确。
此外,受冶炼、脱氧等生产环节的影响,夹杂物也是钢中常见组分,同样对材料的耐蚀性有一定影响[12-13]。LIU等[14]研究发现,Al2O3夹杂的杨氏模量与钢基体相差较大,两者变形能力不同,加工或热处理过程中夹杂物与钢基体会产生微裂纹或缝隙。TYURIN等[15]比较了不同非金属夹杂物的电化学活性,判断了相同条件下夹杂物与钢基体的腐蚀倾向。然而,析出相与夹杂物的共同作用对材料耐蚀性的影响研究鲜有报道。
笔者采用电化学测试和FeCl3点蚀测试,对两种析出相及夹杂物存在明显差异的商用L80-9Cr钢的耐蚀性进行了对比研究,利用电子背散射衍射(EBSD)对钢中局部塑性变形进行了表征,探讨了析出相、夹杂物与材料耐蚀性之间的联系,以期为指导油气管材的研发提供理论基础。
1. 试验
1.1 试验材料
试验材料为两种商用L80-9Cr钢,分别编号为L-1和L-2,其化学成分如表1所示,供货状态均为调质处理态。
利用Jmatpro软件对两种钢中的相组成进行热力学计算。用于显微组织观察的试样尺寸为15 mm×15 mm×10 mm,将试样打磨抛光后用Zeiss Scope. A1型金相显微镜(OM)和JSM 7200F型扫描电子显微镜(SEM)观察钢中夹杂物形貌,用配套能谱仪(EDS)分析析出相及夹杂物组成,再用由10 mL HNO3+20 mL HCl+30 mL H2O配制成的溶液对试样进行侵蚀,采用扫描电镜观察显微组织形貌。将试样振动抛光后进行电子背散射衍射(EBSD)测试,加速电压23 kV,扫描步长0.125 μm,所得试验数据由Channel 5软件进行分析处理。
1.2 电化学测试
电化学测试在Gamry 1010E电化学工作站中进行,采用三电极体系,工作电极为两种商用L80-9Cr钢,其工作面积为1 cm2,辅助电极为铂片,参比电极选用饱和甘汞电极(SCE)。试验前,用砂纸逐级(至800号)打磨两种钢工作面,然后依次用去离子水和酒精冲洗,高压N2吹干备用。测试溶液采用由去离子水和分析纯化学试剂配制成的3.5%(质量分数)NaCl溶液,试验温度为(25±1)℃。在开路电位(OCP)下稳定1 h后依次进行电化学阻抗谱(EIS)和动电位极化曲线测试。阻抗谱测试频率范围为10-2~105 Hz;极化曲线扫描初始电位-250 mV(相对于OCP),扫描速率为0.5 mV/s。
1.3 FeCl3点蚀试验
按照GB/T 17897-2016《金属和合金的腐蚀不锈钢三氯化铁点腐蚀试验方法》标准中A方法,采用FeCl3点蚀试验测试两种钢的耐点蚀性能。试验溶液为6%(质量分数)FeCl3溶液,试样尺寸为50 mm×25 mm×3 mm,表面用SiC水砂纸逐级(至800号)打磨,然后用去离子水冲洗、酒精擦拭、丙酮除油,冷风吹干后放入干燥器中备用。每组试验采用3个平行样,浸泡周期为72 h,试验温度为25 ℃。采用LSM900-ZEISS型共聚焦显微镜和SEM观察腐蚀后试样的表面形貌,并根据式(1)计算局部腐蚀速率[17]。
|
(1) |
式中:RL为钢的局部腐蚀速率,mm/a;h为平均点蚀深度,μm;t为试验周期,d。
2. 结果与讨论
2.1 显微组织
经过热力学计算,得到了两种L80-9Cr钢中平衡相组成与温度的关系,如图1所示。可见,两种材料在500~800 ℃范围内回火后的平衡相都主要由基体铁素体相和M23C6型碳化物析出相组成。
由图2可见,两种材料的显微组织均为保持马氏体位向的回火索氏体(铁素体基体加球状碳化物)[17],白亮色M23C6型碳化物多沿马氏体板条束间分布,但L-2钢中碳化物析出量高于L-1钢。此外,对比图2(b)和(d)可以看出,L-2钢中夹杂物的数量明显高于L-1钢。
如图3所示,碳化物析出相中主要合金元素为C、Fe和Cr,且Cr和C原子比接近4∶1,可确定析出相为Cr23C6。而夹杂物主要由O和Al两种元素组成,其原子比接近3∶2,可确定为Al2O3,为初炼钢经过脱氧后形成[18-19]。
进一步研究了Cr23C6析出相分布对组织的影响。如图4所示,图中蓝线表示小角度晶界(<10°),黑线为大角度晶界(>15°)[20],而绿色区域为高密度晶格畸变的存在位置。可见,两种材料显微组织中高密度晶格畸变主要分布于小角度晶界处,且L-2钢的晶格畸变程度远高于L-1钢。
2.2 极化曲线
由图5可以看出:两种材料的极化曲线相似,阴极极化部分线段均呈现近乎垂直的形态,受氧扩散过程控制,发生氧去极化反应;阳极极化部分线段则较为平缓,没有出现明显的活化-钝化转变,主要发生Fe的阳极溶解[21-22]。
进一步对极化曲线Tafel区进行拟合,结果如表2所示。可见,L-1钢的自腐蚀电位(Ecorr)和自腐蚀电流密度(Jcorr)分别为-412.8 mV和5.84 μA/cm2,而L-2钢的分别为-495.5 mV和8.79 μA/cm2。对比结果表明,L-2钢的自腐蚀电位较低,且自腐蚀电流密度较高,相较于L-1钢具有更高的电化学腐蚀倾向。
试样 | Ecorr/mV | Jcorr/(A·cm-2) | ba/(mV·dec-1) |
---|---|---|---|
L-1 | -411.77 | 6.01×10-6 | 82.22 |
L-2 | -495.47 | 8.89×10-6 | 108.81 |
2.3 电化学阻抗谱
由图6可见,两种材料的电化学阻抗谱均呈现两个时间常数,出现两个容抗弧,即高频容抗弧和低频容抗弧。其中,高频容抗弧与腐蚀产物膜的电容(Qf)和电阻(Rf)有关,低频容抗弧与双电层电容(Qdl)和电荷传递电阻(Rct)有关。
图7和表3分别为阻抗谱等效电路和电化学参数拟合结果。其中,Rct为电荷转移电阻,Rf为腐蚀产物膜电阻,Qf为腐蚀产物膜电容,Qdl为界面电容,Rs为溶液电阻,W为与扩散过程相关的Warburg阻抗。可见,L-2钢的Rf与Rct均低于L-1钢,说明电荷越过基体与腐蚀介质界面的阻力较小。对比结果表明,L-1钢表面形成腐蚀产物膜的覆盖率和致密性均优于L-2钢。
试样 | Rs/(Ω·cm2) | Qf/(μF·cm-2) | n | Rf/(Ω·cm2) | Qdl/(μF·cm-2) | n | Rct/(Ω·cm2) | W/(Ω-1·s-n·cm-2) |
---|---|---|---|---|---|---|---|---|
L-1 | 5.977 | 0.4735 | 0.781 9 | 54.4 | 0.117 8 | 0.909 | 2 240 | 0.015 94 |
L-2 | 7.422 | 0.229 4 | 0.811 6 | 7.518 | 0.120 5 | 0.782 8 | 1 609 | 0.019 98 |
2.4 耐FeCl3点蚀性能
由图8可见:两种材料表面均被一层灰黑色腐蚀产物覆盖,且L-2钢表面腐蚀产物膜存在较多孔洞;去除腐蚀产物后发现,两种材料表面金属光泽均消失且变得粗糙,表明点蚀过程中伴随严重的全面腐蚀。但与L-1钢相比,L-2钢表面还存在较多明显的点蚀坑,即L-2钢发生了严重的点蚀。
为进一步研究两种材料的点蚀行为差异,对去除腐蚀产物后试样的表面三维形貌进行观测,结果如图9所示。可以看出,L-1钢表面仅存在部分较小突起,未发现点蚀坑,而L-2钢表面有较多开放型点蚀坑,通过测量可知,点蚀坑的深度为62.9~942.9 μm,局部腐蚀速率为56.59 mm/a。此外,在去除腐蚀产物膜后观察L-2钢表面SEM形貌(见图10)发现,在点蚀形核与发展过程中,蚀坑内均存在Al2O3夹杂。
2.5 讨论
两种L80-9Cr钢经调质处理后,其显微组织均为回火索氏体,不同点主要在于Cr23C6析出相与夹杂物的含量。由此可推断,Cr23C6析出相与夹杂物是导致L-2钢耐蚀性较差的关键因素。在回火组织中,原始奥氏体晶界、板条束界都属于大角度晶界,相邻的马氏体板条界属于小角度晶界[23],而两种材料显微组织中Cr23C6析出相沿原马氏体板条束呈片层状连续分布。顾洋等[24]研究发现,回火过程中小角度晶界会逐渐转变为高能大角度晶界,位错分布减少,晶格畸变程度降低。而EBSD结果(见图4)表明,高密度晶格畸变主要分布于小角度晶界。因此,结合两种L80-9Cr钢显微组织中析出相的分布特征可以判断,Cr23C6在小角度晶界处的析出聚集是引发高密度晶格畸变的主要原因。
根据机械电化学理论,高密度晶格畸变的存在意味着该区域内储能较高,在畸变区域内的金属原子比远离畸变区域的原子更加活跃,具有更高的自由能。因此,高密度晶格畸变处具有较高的电化学活性,在腐蚀环境中更容易吸附侵蚀性离子(如Cl-),降低表面腐蚀产物膜的致密性,导致材料自腐蚀电流密度升高,耐均匀腐蚀性能下降。同时,Cr23C6的析出会减少周围Cr元素的含量,形成贫Cr区,增大材料点蚀的发生倾向。
此外,图10表明,Al2O3夹杂物对点蚀萌生和发展存在促进作用。Al2O3作为非金属夹杂物,其表面电位较正,在电化学环境中容易充当阴极,导致周围基体的溶解,从而在钢基体与夹杂物之间形成缝隙。随之在FeCl3的水解作用下,溶液pH降低[25],Al2O3夹杂物的边缘溶解进一步加速,缝隙尺寸增大,点蚀坑在该处萌生并不断发展,直至蚀坑内难以溶解的夹杂物最终脱落,在试样表面形成点蚀。
3. 结论
(1)Cr23C6在原马氏体板条束内的析出聚集增大了小角度晶界处的晶格畸变程度。
(2)高密度晶格畸变处具有较高的电化学活性,导致自腐蚀电流密度增加,L80-9Cr钢的耐均匀腐蚀性能下降。
(3)Cr23C6的大量析出导致贫Cr区的形成,增大材料点蚀发生倾向,同时Al2O3夹杂物为点蚀萌生与发展提供有利位置。
免责声明:本网站所转载的文字、图片与视频资料版权归原创作者所有,如果涉及侵权,请第一时间联系本网删除。
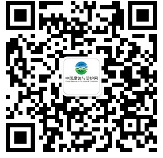
官方微信
《腐蚀与防护网电子期刊》征订启事
- 投稿联系:编辑部
- 电话:010-62316606
- 邮箱:fsfhzy666@163.com
- 腐蚀与防护网官方QQ群:140808414