使用农作副产物如秸秆等生物质能部分替代煤炭发电,不仅可以减少CO2排放,还有利于减少其他常规污染物的排放,如CO、NO x 、SO x 和PM2.5等[1, 2],而且可以通过结合碳捕集技术实现CO2的负排放[3]。但是,目前大多数发电设备都是为燃煤而设计的,必须研究添加生物质燃料对现有锅炉的影响。据报道,在150MW级煤粉锅炉中,煤+20%木料共燃比纯煤燃烧更容易引起炉壁内锅炉传热管的腐蚀,因为共燃产生的K2SO4和Na2SO4是煤燃烧的2~3倍,氯的含量也大大增加[1]。此外,为了使燃料燃烧更充分和方便碳捕获,氧-燃料燃烧是其中最为可行的技术路线[3~5]。使用氧燃料燃烧对燃灰的影响较小,主要影响烟气成分。特别是对腐蚀影响较大的水蒸气和硫氧化物,它们的浓度将不同程度地提升3~6倍,这同样可能加速腐蚀[6]。
HR3C不锈钢因其高的耐蚀性在中国的620℃超超临界电站中得到了广泛的应用,因为其能够在高温下形成连续稳定的Cr2O3保护膜[7]。尽管有诸多有关其在传统电站中的应用研究,但其在新燃烧环境中的腐蚀研究却很少,特别是含水蒸气和氯的环境。水蒸气对腐蚀的影响复杂但轻微[8~10],而氯的影响则更引人关注。众所周知,Al2O3比Cr2O3在面对氯盐侵蚀过程具有更高的稳定性[11~13]。渗铝是最常用的在合金表面获得Al2O3的方式,能够显著提高合金的抗氯腐蚀能力[14,15]。同时,许多报道认为气氛中的水蒸气也能促进保护性Al2O3在低温下形成[16, 17]。总之,煤灰腐蚀是一个复杂的过程,铝化物涂层可能是有效的防护手段之一。众所周知,煤灰通过形成低熔点共晶盐物的方式腐蚀合金,碱金属盐Na2SO4(884℃)、K2SO4(1067℃)和KCl(770℃)是煤灰中熔点最低的物质。它们含量的增加能够明显的降低煤灰的熔点,增强煤灰的腐蚀性[18]。而且高温下Cl-对金属的腐蚀有着致命的催化作用[19,20],几乎没有合金能在这种条件下稳定服役。因此,本实验研究了HR3C合金和它的铝化物涂层在煤灰沉积下的腐蚀行为,探索了煤灰中碱金属和氯化物含量对材料腐蚀的影响。从而扩展合金的适用范围并且探索铝化物涂层的可行性。
1 实验方法
本论文中选用HR3C奥氏体不锈钢作为实验用基体合金,其名义的化学成分(质量分数,%)为:C 0.04~0.10、Cr 24~26、Ni 17~23、Si ≤ 0.75、Mn ≤ 2.00、N 0.15~0.35、Nb 0.2~0.6、Fe余量。将基体合金经电火花线切割设备加工成10 mm × 15 mm × 2 mm的长方体试样,其中一部分试样经400#、800#、2000#碳化硅砂纸依次打磨后在丙酮中超声波清洗15 min后烘干。对其中一半的样品采用固体粉末包埋法进行渗铝,渗铝剂为2%NH4Cl + 98%FeAl粉,温度为900℃,时间为3 h。表面粗糙度对腐蚀有重要的影响,同时为了除去样品表面烧结的铁铝粉以便确认后续腐蚀产物的组成,使用2000#砂纸将渗铝后的样品磨平,直至没有残余铁铝粉。最后,将所有样品称重备用并命名为A-HR3C。
随后,将准备好的样品浸入模拟煤灰悬浮液中使其表面被煤灰包裹,通过多次浸涂控制煤灰的沉积量约为(20 ± 2) mg/cm2。然后,将样品置于预热温度为150℃的管式炉(SK2-6-12TP,炉膛尺寸为ϕ100 mm × 1350 mm)中。随后,使用Ar排出管式炉内的空气,并以20 mL/min的总流量通入混合气体,气体的名义成分(体积分数,%)为SO2 0.5、O2 4、H2O 20和CO2 75.5。待20 h后,炉管中的绝大多数Ar被混合气体所替代。此时,管式炉将以15℃/min的速率升温至700℃,保温一定时间后,样品将随炉冷却到室温。最后,将样品在去离子水中超声波清洗3 min以去除残余的煤灰,并在80℃烘箱中烘干1 h后称重。
使用Sartorius BP211D电子天平(精度为0.01 mg)记录样品的重量变化。利用扫描电子显微镜(SEM, FEI INSPECT F50)并结合能谱仪(EDS, OXFORD X-Max)分析腐蚀产物的形貌及成分,利用X射线衍射仪(XRD, Rigaku, SmartLab (9 kW), Cu Kα, 40 kV)分析相组成。
2 结果与讨论
2.1 样品的初始状态
图1
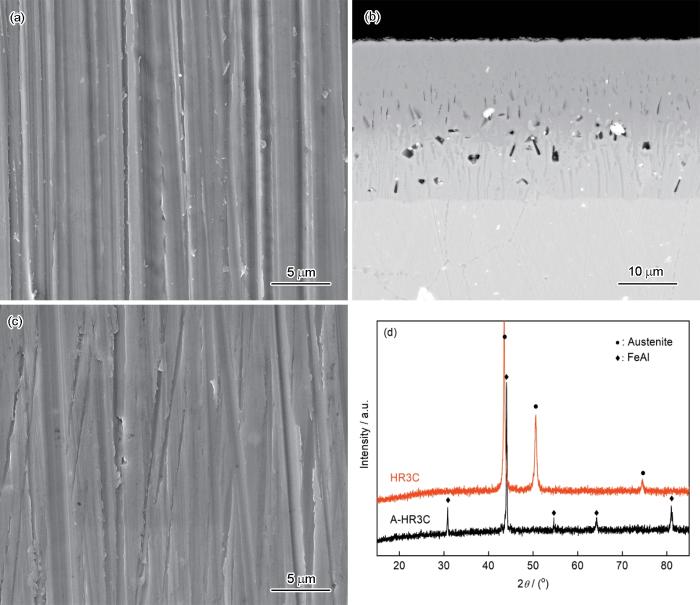
图1 A-HR3C的表面、截面形貌和HR3C的表面形貌及对应的XRD谱
Fig.1 Surface (a) and cross-sectional (b) morphologies of A-HR3C, surface morphology of HR3C (c), and corresponding XRD patterns of A-HR3C and HR3C surface (d)
2.2 宏观照片和腐蚀动力学
图2是HR3C和A-HR3C在不同煤灰中腐蚀1000 h后的宏观照片。对于HR3C基体,从图2a~c中可以看出,随着煤灰中Na2SO4和K2SO4含量的增加样品表面的颜色越来越红,这说明煤灰中的Fe2O3开始大量烧结在样品表面上。在经过超声清洗之后,HR3C-3#样品表面出现了大面积的剥落。从图2a、d~f中可以看出,当煤灰中总的碱金属含量不变时,随着KCl含量的增加合金的腐蚀逐渐加剧;当KCl含量增加至2%时,合金的腐蚀程度发生了突变,大量的煤灰烧结在样品表面并且在冷却和清洗过程中剥落,和其他样品不同的是剥落后的区域也不再是金属的颜色。对于A-HR3C样品,所有合金表面非常光滑,几乎没有大面积的煤灰残留。但是从图2g~i来看,随着煤灰中Na2SO4和K2SO4含量由4%增加至8%和12%,样品的颜色由金属色转变为红色。和HR3C样品不同的是,这种颜色更明亮,十分接近于α-Fe2O3的颜色。从图2g、j~l可以看出,若碱金属总量不变,合金总是展现出类金属的颜色,样品表面的划痕依然隐约可见,这说明氧化膜非常薄,也没有煤灰的吸附。如图2g、j、k所示,当煤灰中氯的含量是0,0.5%和1%时,这3种样品的宏观形貌几乎是一致的,观察不到任何明显的区别。当KCl含量开始增加到2%时,HR3C样品开始发生可见的腐蚀,腐蚀区域呈深红色,这说明腐蚀伴随着煤灰的吸附。
图2
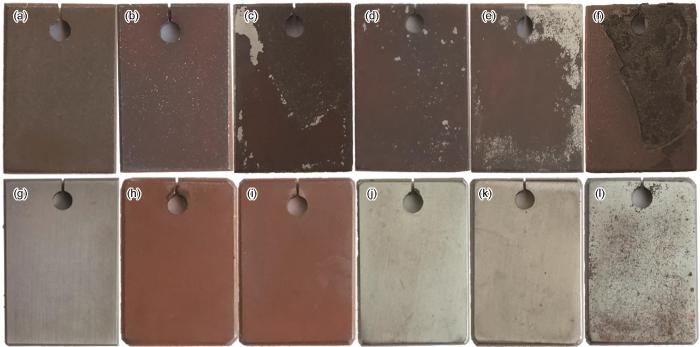
图2 HR3C和A-HR3C在不同煤灰中腐蚀1000 h后的宏观照片
Fig.2 Macro photos of HR3C (a-f) and A-HR3C (g-l) corroded in 1# (a, g), 2# (b, h), 3# (c, i), 4# (d, j), 5# (e, k) and 6# (f, l) coal ash for 1000 h
图3是HR3C和A-HR3C在700℃模拟煤灰中腐蚀1000 h的质量变化曲线。对于HR3C基体来说,合金在1#煤灰中的腐蚀表现为持续失重,其余2~6#样品均表现为有波动的增重。波动的原因是样品同时发生着增重和失重过程。导致样品增重的原因可能是样品氧化腐蚀或是煤灰烧结到样品上,失重来自于冷却和清洗过程中合金腐蚀产物和煤灰的剥落。因为1#煤灰中碱金属含量较少且不含Cl-,合金表现出了较好的抗腐蚀性能且烧结煤灰的量最少。因此在经过超声波清洗后,合金表现为缓慢的失重。对于2~5#样品,合金的质量变化均在-0.2~0.2 mg/cm2之间波动。结合图2来看,3#和5#样品出现了大面积的剥落,所以质量增加处在一个较低的水平。因此质量变化曲线很难区分1~5#样品的腐蚀情况。当KCl的含量增加至2%后,合金的增重发生了较大的跳跃,平均增重从小于(0.05 ± 0.12) mg/cm2(2#)跳跃至约(1.58 ± 4.86) mg/cm2,这说明合金发生了更为严重的腐蚀且更多的煤灰烧结到了合金表面。需要注意的是,增重和失重主要发生在腐蚀的后半段,这是因为热腐蚀的启动需要一定时间的孕育期,后半段的取样间隔更长,前期频繁的取样和洗样过程可能阻碍热腐蚀的孕育。对于A-HR3C样品,所有的样品都表现为缓慢的增重,其中碱金属含量较高的2#和3#样品的质量变化波动更大,增重更多,这说明在腐蚀过程中不断发生着煤灰的吸附和脱落,这与宏观照片中看到的现象相符。1、4、5#样品的增重均非常小,且增重曲线几乎重合。煤灰中氯含量的增加似乎没有影响腐蚀速率。但对于6#样品,即当KCl的含量增加至2%时,合金的腐蚀行为发生了改变,曲线从400 h开始与1、4、5#样品的曲线分离,并保持更高的增长速率,这说明腐蚀形式发生了改变。但A-HR3C-6#样品的增重仅有(0.13 ± 0.04) mg/cm2,远小于HR3C-6#的(1.58 ± 4.86) mg/cm2。总之,仅从增重来看,碱金属含量对合金基体的腐蚀影响较小,而对渗铝合金的影响更大。氯离子的作用则相反,它对合金基体的腐蚀影响较大而对渗铝合金的影响较小。这说明铝化物涂层对于抵抗含氯环境的热腐蚀是有效的。
图3
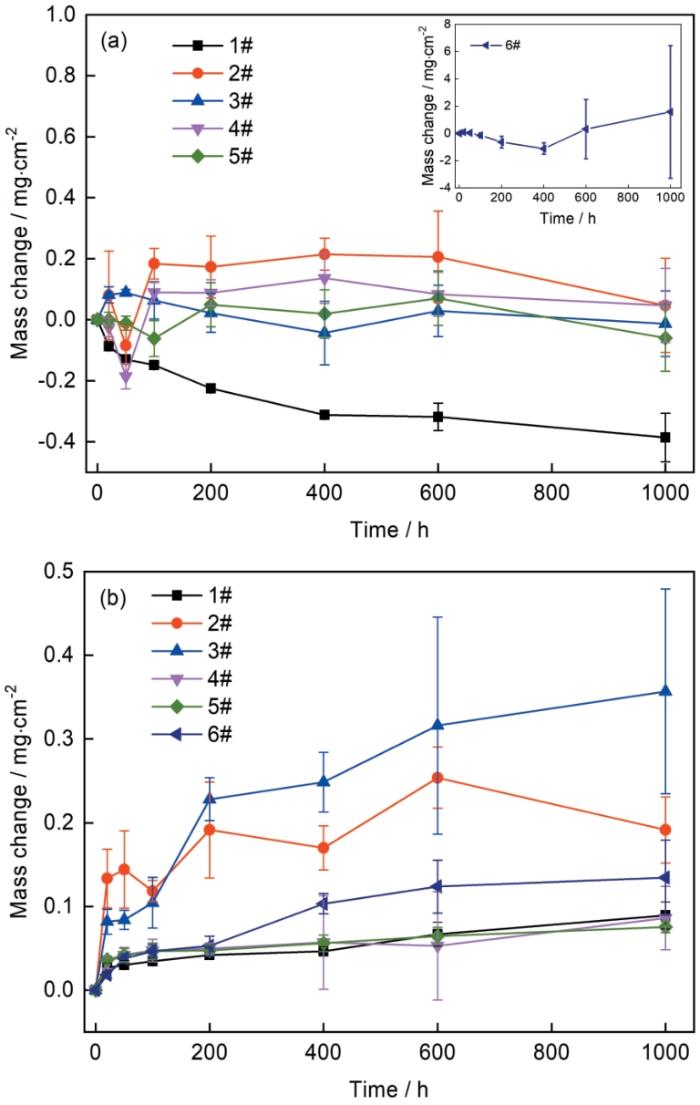
图3 HR3C和A-HR3C在700℃模拟煤灰中腐蚀1000 h的质量变化曲线
Fig.3 Mass change curves of HR3C (a) and A-HR3C (b) after corrosion in simulated coal ash at 700oC for 1000 h
2.3 HR3C的腐蚀产物和形貌
图4是HR3C在700℃ 1~6#煤灰中腐蚀1000 h的XRD谱。结果显示,Fe2O3和Cr2O3是所有样品的主要腐蚀产物。在2、3、5、6#样品上检测到了SiO2,其对应峰的强度随着碱金属硫酸盐或是氯盐含量的增加而增加。在含KCl的样品上检测到了Al2O3的衍射峰,它在4、5#样品上非常微弱,在6#样品上十分明显。在腐蚀最严重的6#样品上没有检测到奥氏体相的存在,这说明样品表面的煤灰和腐蚀产物非常厚,X射线无法穿透。尽管如此,在5#和6#样品上还是检测到了尖晶石的衍射峰,而尖晶石的形成依赖于基体氧化形成的FeO或NiO,这说明腐蚀非常严重。
图4

图4 HR3C在700℃不同的模拟煤灰中腐蚀1000 h的XRD谱
Fig.4 XRD patterns of HR3C after corrosion in simulated coal ash at 700oC for 1000 h
图5是 HR3C合金在1~6#煤灰中腐蚀1000 h后的表面形貌,图6是对应的截面形貌。图5中1~7区域的元素成分分析结果汇总于表2。除了1#样品之外,在其余样品上均观察到了不同程度的剥落。裸露的金属区是多孔的,说明氧化膜和基体的结合并不致密。从形貌来看,1~5#样品均没有发生非常严重的腐蚀(图5a~e),尽管经过超声波清洗,所有样品上均有明显的Fe2O3和SiO2颗粒烧结在样品表面,Al2O3较少。样品表面的SiO2颗粒并非棱角分明而是较为圆滑,这是因为SiO2的熔点较低,它易于与Na2SO4、K2SO4等反应形成低熔点的玻璃相从而黏附在样品上。在截面照片中也可以明显的观察到SiO2的存在(如图6a所示),它在背散射照片中明显比以Fe2O3和Cr2O3为主的氧化物更暗。从元素成分来看,铁氧化物是所有样品氧化膜的主要成分,这是因为合金具有较高的Cr含量,Cr2O3是合金基体的主要氧化产物,它们具有和煤灰中的α-Fe2O3相同的晶体结构和参数[22,23],因此煤灰中的Fe2O3能够比较容易的烧结在样品表面[24],并且通过固态扩散发生下列反应。
图5
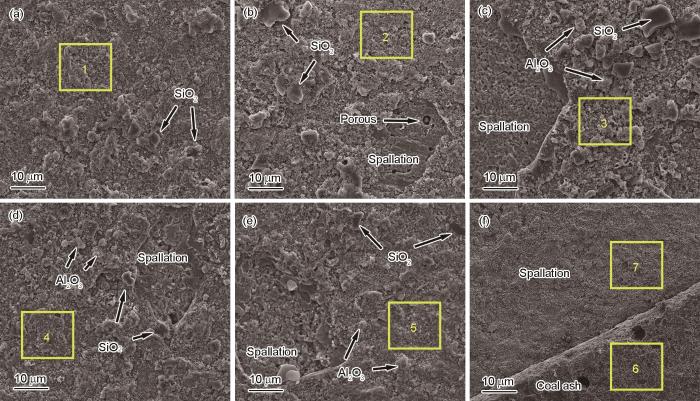
图5 HR3C合金在1~6#煤灰中腐蚀1000 h后的表面形貌
Fig.5 Surface morphologies of HR3C alloy after corrosion in different coal ash for 1000 h: (a) 1#, (b) 2#, (c) 3#, (d) 4#, (e) 5#, (f) 6#
图6
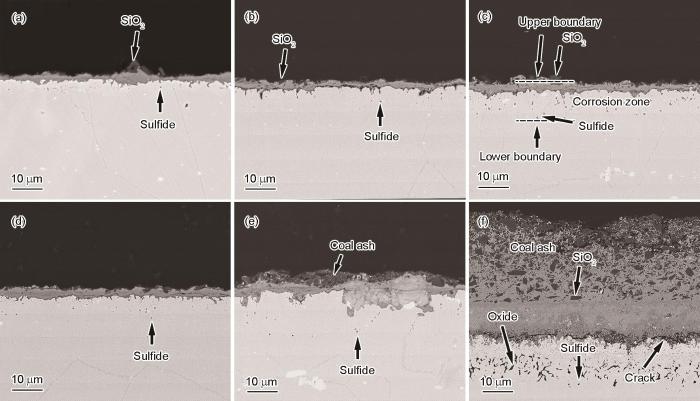
图6 HR3C合金在1~6#煤灰中腐蚀1000 h后的截面形貌
Fig.6 Cross-sectional morphologies of HR3C alloy after corrosion in different coal ash for 1000 h: (a) 1#, (b) 2#, (c) 3#, (d) 4#, (e) 5#, (f) 6#
对于1~3#样品,表面检测到的Cr含量不断降低而Al、Si含量不断升高(p1~p3)。这说明煤灰的烧结随着煤灰中碱金属的含量增加而越发严重了,以至于X射线更难检测到下层的Cr2O3。从1、4、5、6#样品来看,随着煤灰中KCl含量的增加,表面上检测到Cr的含量随之减少,而Ni的含量在不断增加(p1,p4~p6)。6#样品发生了非常严重的腐蚀,以至于需要在更大的尺度观察腐蚀产物的剥落区(图5f)。从截面(图6f)可以看出,以最下方的SiO2为界,有超过100 μm的煤灰层烧结在样品表面。尽管如此,依然在表面检测到了3.67%的Ni和15.22%的Fe(p6),这说明Ni和Fe扩散通过了超过100 μm厚的煤灰层,合金发生了严重的腐蚀。在剥落区,能谱显示Cr、O、Fe、S在这里富集,S的含量达到了6.57%(p7),并且不溶于水,说明合金发生了严重的硫化。
图7
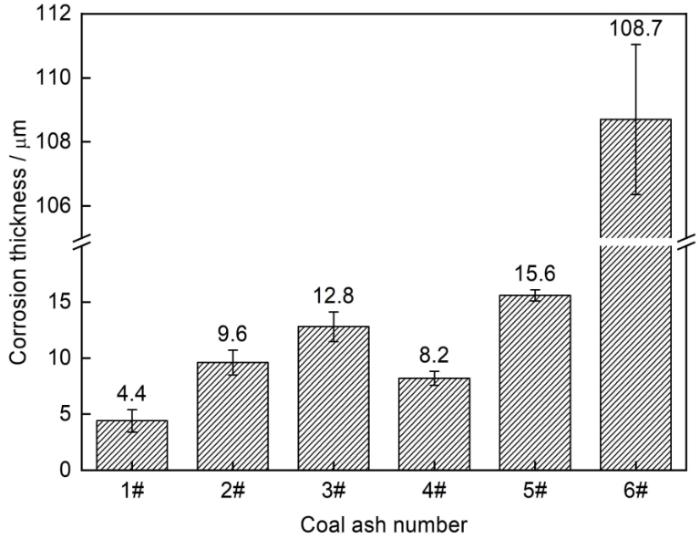
图7 HR3C合金在1~6#煤灰中腐蚀1000 h后腐蚀区的厚度
Fig.7 Thickness of the corrosion zone of HR3C after corrosion in 1-6# coal ash for 1000 h
从图中我们可明显的看到,合金的腐蚀深度随着煤灰中碱金属和铝化物的增加而增加。在本实验中Na2SO4 + K2SO4含量的增加对腐蚀的影响是接近线性的(1、2、3#煤灰中的Na2SO4 + K2SO4含量为4%、8%、12%,对应的腐蚀深度为4.4、9.6、12.8 μm)。氯对腐蚀的影响是巨大的。保持碱金属含量不变,当KCl含量<1%时,合金的腐蚀与纯硫酸盐腐蚀相同。对比2、3#和4、5#煤灰,它们的碱金属硫酸盐含量差为4.5%和9%;氯盐差距为0.5%和1%。结合腐蚀深度来看,0.5%的KCl对腐蚀的影响接近4.5%的Na2SO4 + K2SO4;1%的KCl对腐蚀产生的影响超过9%的Na2SO4 + K2SO4。当煤灰中的KCl增加至2%时,合金发生了剧烈的腐蚀,最大腐蚀深度超过108.7 μm。这是因为随着氯化物的增加,煤灰中的低熔点组分的含量和体积分数也在增加,直到超过某一阈值。此时熔融物能够隔绝氧气和合金表面氧化物的直接接触,构建氧分压从气氛到保护性氧化物(Cr2O3)的负浓度梯度,从而导致Cr2O3溶解和破坏[25,26]。熔融的Cl-具有更强的活性。因为半径较小,Cl-比SO
在这个过程中硫酸盐和氯盐均没有被消耗,它们作为一种催化性的介质阻碍保护性腐蚀产物的产生,使得合金持续的被环境中的SO3和O2氧化,在合金内部和外侧留下硫化物或氧化物作为腐蚀产物。
2.4 渗铝HR3C的腐蚀产物和形貌
图8是A-HR3C在700℃ 1~6#煤灰中腐蚀1000 h的XRD谱。渗铝样品的腐蚀是非常轻微的以至于所有样品上FeAl相的衍射峰都非常强。和宏观结果相符,在1、4、5#样品上,除了FeAl之外没有明显的其他相的衍射峰出现。在腐蚀现象较为明显的2、3、6#样品上检测到了Fe2O3、SiO2和Al2O3的衍射峰,其中6#样品上Al2O3的衍射相对最强。
图8
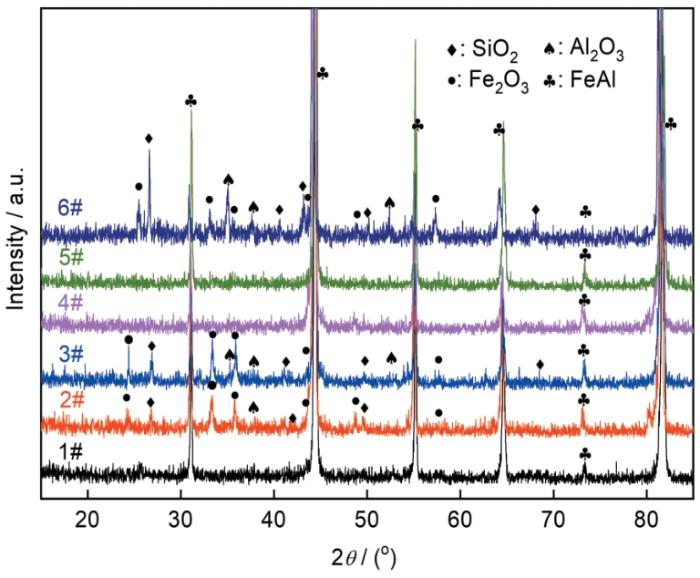
图8 A-HR3C在700℃不同的模拟煤灰中腐蚀1000 h的XRD谱
Fig.8 XRD patterns of A-HR3C after corrosion in simulated coal ash at 700oC for 1000 h
图9是A-HR3C合金在1~6#煤灰中腐蚀1000 h后的表面形貌,图10是对应的截面形貌。表3是图9中1~6区域的元素成分分析结果。所有的样品均未观察到内氧化或内硫化。如图9a、d、e,1、4、5#样品的腐蚀是非常轻微的,表面因研磨留下的划痕依然清晰可见。能谱结果中O含量远低于氧化物中的含量(p1、p4、p5),这说明氧化膜太薄,以至于X射线穿透氧化膜检测到了基体。除此之外,它们腐蚀产物主要是Al2O3,仅有极少量的Fe2O3吸附在表面。截面形貌显示,它们表面氧化物的总厚度均小于1 μm。随着碱金属含量的增加,煤灰中的成分开始大量吸附在表面(图9b和c),能谱显示其中最多的是Fe2O3(p2、p3),当煤灰中的碱金属硫酸含量增加后,下述反应开始发生并且显著影响腐蚀行为。
图9
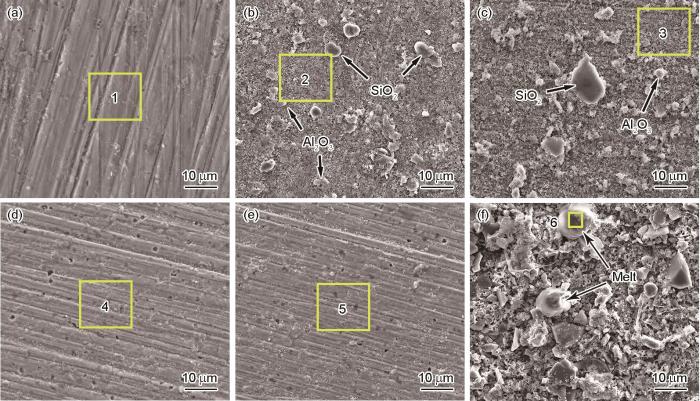
图9 A-HR3C合金在1~6#煤灰中腐蚀1000 h后的表面形貌
Fig.9 Surface morphologies of A-HR3C alloy after corrosion in different coal ash for 1000 h: (a) 1#, (b) 2#, (c) 3#, (d) 4#, (e) 5#, (f) 6#
图10
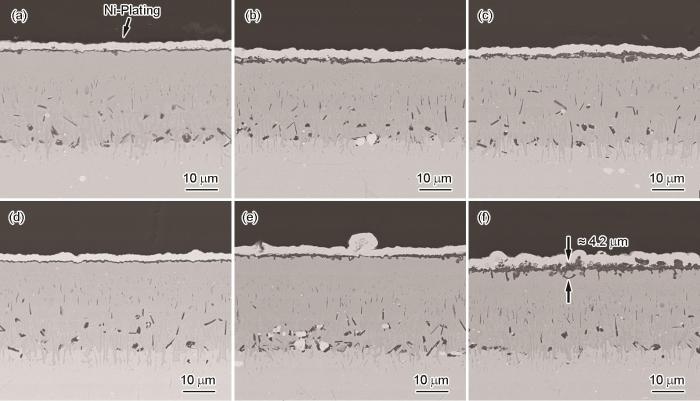
图10 A-HR3C合金在1~6#煤灰中腐蚀1000 h后的截面形貌
Fig.10 Cross-sectional morphologies of A-HR3C alloy after corrosion in different coal ash for 1000 h: (a) 1#, (b) 2#, (c) 3#, (d) 4#, (e) 5#, (f) 6#
这是一种熔点较低的物质,它能够充当助熔剂的角色,使得煤灰更容易烧结在样品表面[28]。因此2#和3#样品表面的氧化物层相比于1#更厚(图10a~c)。此外,和HR3C基体不同的是,渗铝涂层含有很高的铝含量,在氧化和腐蚀过程中倾向于在表面生成Al2O3。因此,在低熔点共晶物的辅助作用下,同样成分的Al2O3更容易烧结在样品表面上,所以在样品表面上检测到了比HR3C样品上更多的Al2O3(图10b、c、f)。至于氯的影响,和HR3C基体的腐蚀类似,6#煤灰的腐蚀形式也发生了跳跃式的转变。样品的表面上烧结了大量的煤灰。而且观察到了明显熔融的痕迹(p6),能谱显示Si、Al、Fe在这里富集。腐蚀开始向涂层内发展,在1000 h后达到了约4.2 μm,约是无涂层HR3C的二十五分之一。尽管如此,在所有的样品中均没有观察到内氧化和硫化,这说明Al2O3氧化膜比Cr2O3在面对煤灰腐蚀时更加稳定且致密,能够阻止硫和氯的侵蚀。
3 结论
在700℃时,煤灰和烟气以氧化+内硫化/氧化的形式腐蚀HR3C合金,增加煤灰中的碱金属硫酸盐含量,不会导致合金腐蚀速率的明显增加,但是会增加合金内硫化的深度。氯盐的参与会明显加速合金的腐蚀,仅2%的KCl便会导致极其严重的腐蚀。由于形成Al2O3保护膜,渗铝合金表现出了优异的抗腐蚀性能。煤灰中的碱金属硫酸盐含量从4%增加至12%或者是KCl含量增加至1%时,对渗铝合金的腐蚀几乎没有影响;KCl的含量增加至2%时,才能观察到明显的腐蚀现象,此时渗铝合金的腐蚀深度仅为HR3C基体的约二十五分之一。
免责声明:本网站所转载的文字、图片与视频资料版权归原创作者所有,如果涉及侵权,请第一时间联系本网删除。
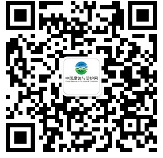
官方微信
《腐蚀与防护网电子期刊》征订启事
- 投稿联系:编辑部
- 电话:010-62316606
- 邮箱:fsfhzy666@163.com
- 腐蚀与防护网官方QQ群:140808414