铝合金中铬的质量分数一般不超过0.35%。如超过该成分范围,则会发生包晶反应,形成极粗大的初生相 Al7Cr。商用合金中的合金元素和杂质元素可能会降低铬在铝中的固溶度,使Al7Cr初生相在包晶反应中形成。铝合金中铬的上限值取决于其他合金和杂质元素的数量和性质。如铸造铝合金含有过量的铬,则会因其在包晶反应过程中停留而产生残存的相。 在AI-Mg、AI-Mg-Si和Al-Mg-Zn合金体系的许多合金中,铬是常用的合金元素。铬形成细小颗粒相,在不可热处理强化铝合金中,有利于细化晶粒,提高合金的强度;在可热处理强化铝合金中,可控制晶粒尺寸和再结晶程度。由于铬的扩散速度慢,在变形铝合金中形成了细小弥散相。对5xxx系列合金,在(铸)锻锭预热过程中形成面心立方的 AlsMg;Cr弥散相;在7xxx合金中,弥散相的成分则更接近于Al1MgzCr。这些细小弥散相抑制了 A1-Mg合金中的形核和晶粒长大,并阻碍了Al-Mg-Si合金和Al-Zn合金在热加工或热处理过程中发生再结晶。在可热处理强化铝合金中,铬的主要缺点是增加了强化相在已存在的铬颗粒处的析出倾向,由此增加了合金的淬火敏感性。 铜在铝中具有相当大的固溶度,具有明显的析出强化作用,因此,铜是铝合金中最重要的合金元素之一。二元铝-铜合金体系是典型的析出强化例子,是最受关注的研究系统之一。尽管如此,实际上很少看到商用二元铝-铜合金。大多数商用铝-铜合金都含有其他合金元素。通常,铝-铜合金体系含有铜(质量分数为2%~10%)和其他合金元素,包括2xxx变形铝合金系列和2xx.x铸造铝合金系列。此外,许多其他可热处理强化铝合金中也含有铜。根据合金中其他成分的不同,铜的质量分数为4%~6%时对铝合金的强化效果达到最大。不同热处理条件下铝-铜合金薄板的性能如图 1所示。 图1 高纯度变形铝-铜合金的拉伸性能 注:薄板试样宽13mm(0.5in)宽,厚1.59mm(0.06in)。0-退火;W一固溶水淬后立即测试;T4-固溶水淬后在室温下时效;T6-在 T4后高温时效。 与其他合金体系相比,对二元铝-铜合金的时效特性已进行了较为详细的研究,但很少有商用的二元铝-铜合金。大多数铝-铜合金都含有镁等其他合金元素。在铝-铜合金中加入镁的主要优点是,通过固溶淬火能进一步提高合金的强度。如对某些变形铝合金进行室温时效,在提高合金强度的同时还能提高其塑性。如对合金进行人工时效,则可获得更高的强度,但塑性会有所降低。在铸造和变形铝合金中,添加质量分数约为0.05%的镁,能有效提高合金的时效强化性能。 在精炼铁钒土和熔炼生成氧化铝后,铁作为杂质元素残存于铝合金中,因此,实际上所有铝合金中都会残存一定的铁元素。铝-铁二元合金体系的共晶成分为w(Fe)=1.8%,在共晶温度655℃(1211℉)下,铁在铝中最大的固溶度为0.05%。尽管可能存在其他相,在固溶度极限温度出现的平衡相是Al3Fe(θ)。根据凝固速率和存在锰等其他合金元素,合金中可能出现亚稳相。如采用适中的速率淬火冷却,则出现FeAl6相;快速火冷却时出现 Fe2Al9相。铝中铁的固溶度非常有限,因此常用作导电材料。固溶的铁使铝的强度略有提高,在温度略有升高的条件下,将具有更好的抗蠕变性能。虽然铝合金中存在少量的铁可减少压铸过程中出现的焊合危害,但通常在铝-硅铸造合金中,铁会形成粗大的富铁相,因此通常不希望铝-硅合金中含有铁。 由于铝合金中总是会残存少量的铁,铁在铝中的影响应根据三元或四元相图来分析。随着添加其他合金元素,铁在铝合金中的固溶度会进一步降低在大多数铝合金中,铁的最大固溶度可降低到w(Fe)=0.01%或以下。由于铁和硅是工业纯铝中常见的杂质元素,因此,人们非常注重对A1-Fe-Si三元相图的富铝角的研究。在硅含量低的情况下几乎所有的铁元素都形成 Al3Fe 相。 铝-镁合金是变形5xxx系列和铸造5xxx系列中,不可热处理强化铝合金。合金中的镁能提高固溶强化效果,而不会过度降低合金的塑性。铝-镁合金具有优异的固溶强化和耐蚀综合性能,通过形变强化,变形铝合金的强度得到了进一步提高。目前,5xxx变形铝合金系列中镁的质量分数不超过5.5%,而铸造铝合金中镁的质量分数为4%~10%。当铸造铝合金中镁的质量分数达到10%时,在室温下会形成第二相。当铸造铝合金中镁的质量分数小于7%时,在室温下合金是稳定的,在高于室温时则是不稳定的。 为控制晶粒或亚晶结构,以及残存铁和硅杂质元素形成的金属间化合物颗粒,通常在铝-镁合金中添加少量铬、锰、锆等过渡族元素。虽然镁在铝中的最大固溶度约为17%,但之前的冷加工工序会加速 Mg2Al;相的析出,因此,目前变形铝合金中镁的质量分数一般不超过5.5%。相对于铝-镁合金基体而言,这种析出相呈高度阳极电位,并沿晶界呈连续网状分布,由此在长期室温环境或短时间高温环境下,合金具有很高的应力腐蚀开裂(SCC)敏感性。在正常情况下,由于5182、5083、5086、5154、5356和5456合金中镁的质量分数约为3%,因此易受到应力腐蚀开裂的影响。一般来说,对于经严重冷变形的合金,大多数有害析出相是在室温下长年累月形成的,或者持续暴露在65~180℃(150~350℉)的温度下而形成。在较高的温度下析出相会发生粗化,在晶界呈不连续析出,此时会降低或去除应力腐蚀开裂。 在铝-镁合金中添加锰,可提高合金强度。添加锰主要有两个优点:第一,促进镁析出相在组织中更加均匀地析出;第二,在达到合金所要求强度的条件下,添加锰可降低合金中镁的含量,从而确保合金的稳定性更高,使变形铝合金具有更高的强度和耐蚀性。在铸造铝-镁合金中添加质量分数为0.75%的锰,对合金耐蚀性的影响很小,但提高了合金的硬度且降低了塑性。 硅和铁一样,是工业铝合金中常见的杂质元素。电解铝中杂质硅的质量分数为0.01%~0.15%,当铝中存在铁时,硅在铝中的固溶度将极大地下降。随着硅含量的增加,工业铝中先形成六角晶系的α相(Al8Fe2Si),然后形成单斜晶系的β相(以化学计量的 Al5FeSi或 Al9Fe2Si2)。 作为合金元素,硅加入铝或铝合金中,能显著改善合金的铸造性能。不含铜的铝-硅合金具有良好的铸造性能和耐蚀性。二元铝-硅合金体系是一个简单的共晶体系,其共晶点硅的质量分数为12.6%。在共晶温度577℃(1071℉),硅在铝中的最大固溶度为w(Si)=1.65%。在很大程度上,硅提高了铝合金的铸造性能和流动性能。因此,合金元素硅在4xxx铝合金钎焊薄板和3xx.x4xx.x铸造铝合金中应用广泛。现已有硅的质量分数低至2%的铸造铝合金,但通常铸造铝合金中硅的质量分数在5%~13%范围内,有时硅的质量分数高达 20%,为过共晶合金。 含铜量高的铝-铜合金[w(Cu)=7%~8%],是最早的常用铸造铝合金,现已完全被Al-Si-Cu/Mg(3xx.x)合金所取代。Al-Cu-Si合金系列是使用最广泛的铸造铝合金之一,不同合金牌号中铜和硅两种元素的含量在很大范围内变化,其中一部分合金中铜占主导地位,而另一部分合金中硅为主要合金成分。在这类合金中,铜有助于提高合金的强度,硅则可提高合金的铸造性能和降低其热脆性。在Al-Cu-Si合金系列中,铜的质量分数达到3%~4%时为可热处理强化铝合金,通常这部分合金中还含有一定量的镁,以进一步提高合金的热处理强化效果。 多年来铝-锌合金早已为人所知,但是铝-锌铸造铝合金的热裂问题,以及变形铝合金的应力腐蚀开裂敏感性问题限制了它们的使用。锌的固溶强化和形变强化作用很小,因此,单独在铝中添加锌没有明显的作用。然而,在添加铜和/或镁的同时添加锌以及少量的铬,则铝合金可以进行热处理强化或自然时效。 在铝-锌合金,特别是在w(Zn)=3%~7.5%的铝合金中添加镁,可以有效提高该系列合金的强度。合金中的镁和锌形成MgZn2,其热处理强化效果明显大于铝-锌二元合金体系。Al-Zn-Mg合金体系中的析出相是7xxx变形铝合金系列和7xx.x铸造铝合金系列的强化基础。在商用Al-Zn-Mg合金的共晶分解过程中,可以形成六方晶系的MgZn2相和体心立方的Al2Mg3Zn3相。根据合金中的锌镁比,不含铜的铝合金通过析出MgZn2或Al2Mg3Zn3亚稳态过渡相来实现强化。在Al-Zn-Mg-Cu合金体系中,铜和铝置换了MgZn2相中的锌,形成了Mg(Zn,Cu,AI)相。在这类合金中也可以通过共晶分解和固相析出形成Al2CuMg颗粒。 在A1-Zn-Mg合金体系中添加铜和少量且重要的铬和锰,可得到商用高强度铝合金。在该合金体系中,铜的作用是提高固溶体的过饱和度,在时效时提高CuMgAl2相的形核速率,从而提高时效速率锌和镁的作用是控制时效进程。在热处理过程中铜也会提高淬火敏感度。一般来说,铜降低了Al-Zn-Mg合金的耐蚀性,但能提高合金抗应力腐蚀的能力。铬、锆等附加合金元素对提高合金的力学性能和耐蚀性有显著的影响。 锂可以降低铝合金的密度,提高其模量。在铝-锂二元合金中,锂以亚稳态Al3Li相析出。在Al-Cu-Li合金中,形成了大量的 Al-Cu-Li 相。与其他合金元素相比,锂的成本较高,因此迄今为止,铝-锂合金主要在航天航空和军工等领域得到了应用。 钪是铝合金中新的合金元素。铝-钪合金在凝固或过饱和固溶体分解过程中,形成立方结构的Al3Sc相,由此使铝-钪合金具有独特的性能组合。Al3Sc立方相属Ll2晶体结构,晶格参数与铝的参数略有不同,比任何其他平衡相与基体的匹配都要好,与铝基体保持共格。此外,Al3Sc相能有效地阻碍晶界迁移和再结晶过程。 由于钪的价格非常昂贵,现在的生产原料基本来源于苏联的Sc203储备,而且该资源还在不断减少,因此仅限应用于特定的场合。目前,绝大多数钪的生产都来自于稀土生产过程中的副产品,钪的主要生产国是中国、俄罗斯、乌克兰和哈萨克斯坦。由于缺乏可靠性、安全性和稳定的长期生产,因此限制了钪在工业中的广泛应用。 同时添加钪和锆,可以将合金中钪的质量分数减少到0.15%~0.20%,由此可在提高力学性能、服役性能和热稳定性的情况下,降低合金的成本。在这种情况下,形成了致密晶体结构立方相(Al3Sc平衡相和亚稳态立方Al3Zr相),在300~400℃(570~750℉)范围内,这两种析出相都为共格析出。 铝合金材料的研发主要是围绕提高材料的强度、塑性、韧性、耐蚀性以及疲劳性能等综合性能来开展的,而合金的性能又是由其组织决定的,热处理是铝合金性能优化的关键手段,通过控制温度、时间和冷却速度等工艺参数,可以显著改变合金的内部微观结构,从而增强其强度、硬度和耐腐蚀性等性能。热处理不仅影响合金的晶粒大小和析出相的分布,还能促使强化相的形成和转变,为不同使用环境和力学要求提供精准的性能调控。基于此,针对铝合金的强化方法,如固溶强化、时效强化和细晶强化等,成为提升合金性能的核心手段。 铝合金在常温和中等应力作用下产生塑性变形,主要由位错滑移所致,而高温和低应力作用下产生塑性变形则由位错蠕动和扩散流变产生。总的来说,不管工作温度高低,合金抵抗变形能力主要由位错运动难易所决定。因而,把增加铝合金对位错运动的抗力称为铝合金强化。 铝合金的强化及其分类方法很多,一般将其分为加工硬化和合金化强化两大类。铝合金强化方法可细分为加工硬化、固溶强化、异相强化、弥散强化、沉淀强化、晶界强化和复合强化七类。在实际应用过程中往往是几种强化方法同时起作用。 通过塑性变形(轧制、挤压、锻造、拉伸等)使合金获得高强度的方法,称为加工硬化。塑性变形时增加位错密度是合金加工硬化的本质。据统计,金属强烈变形后,位错密度可由106根/cm2增至1012根/cm2以上。因为合金中位错密度越大,继续变形时位错在滑移过程中相互交割的机会越多,相互间的阻力也越大,因而变形抗力也越大,合金即被强化。 金属材料加工强化的原因是:金属变形时产生了位错不均匀分布,先是较纷乱地成群纠缠,形成位错缠结,随变形量增大和变形温度升高,由散乱分布位错缠结转变为胞状亚结构组织,这时变形晶粒由许多称为“胞”的小单元组成;高密度位错缠结集中在胞周围形成包壁,胞内则位错密度甚低。这些胞状结构阻碍位错运动,使不能运动的位错数量剧增,以至需要更大的力才能使位错克服障碍而运动。变形越大,亚结构组织越细小,抵抗继续变形的能力越大,加工硬化效果越明显,强度越高。由于产生亚结构,故也称亚结构强化。 加工强化的程度因变形率、变形温度及合金本身的性质不同而异。同一种合金材料在同一温度下冷变形时,变形率越大则强度越高,但塑性随变形率的增加而降低。合金变形条件不同,位错分布亦有所不同。当变形温度较低(如冷轧)时,位错活动性较差,变形后位错大多呈紊乱无规则分布,形成位错缠结,这时合金强化效果好,但塑性也强烈降低。当变形温度较高时,位错活动性较大,并进行交滑移,位错可局部集聚、纠结、形成位错团,出现亚结构及其强化,届时强化效果不及冷变形,但塑性损失较少。 加工硬化或亚结构强化在常温时是十分有效的强化方法,适用于工业纯铝、固溶体型合金和热处理不可强化的多相铝合金,但在高温时通常因回复和再结晶而对强度的贡献显著变小。 某些铝合金冷变形时能形成较好的织构而在一定方向上强化,称为织构强化。 合金元素固溶到基体金属(溶剂)中形成固溶体时,合金的强度、硬度一般都会得到提高,称为固溶强化。所有可溶性合金化组元甚至杂质都能产生固溶强化。特别可贵的是,对合金进行固溶强化时,在强度、硬度得到提高的同时,塑性还能保持在良好的水平上,但仅用这一种方法不能获得特别高的强度。 合金元素溶入基体金属后,使基体金属的位错密度增大,同时晶格发生畸变。畸变所产生的应力场与位错周围的弹性应力场交互作用,使合金元素的原子聚集到位错线附近,形成所谓“气团”,位错要运动就必须克服气团的钉扎作用,带着气团一起移动,或者从气团中挣脱出来,因而需要更大的切应力。另外,合金元素的原子还会改变固溶体的弹性系数、扩散系数、内聚力和原子的排列缺陷,使位错线变弯,位错运动阻力增大,包括位错与溶质原子间的长程交互作用和短程交互作用,从而使材料得到强化。 固溶强化作用大小取决于溶质原子浓度、原子相对尺寸、固溶体类型、电子因素和弹性模量。一般来说,溶质原子浓度越高,强化效果越大;原子尺寸差别越大,对置换固溶体的强化效果亦可能越大;溶质原子与铝原子的价电子数相差越大,固溶强化作用亦越大;弹性模量大小的差异度越大,往往强化效果越好。 在采用固溶强化的合金化时,要挑选那些强化效果高的元素作为合金元素。但更重要的是要选那些在基体金属中固溶度大的元素作为合金元素,因为固溶体的强化效果随固溶元素含量的增大而增加。只有那些在基体金属中固溶度大的元素才能大量加入。例如,铜、镁是铝合金的主要合金元素;铝、锌是镁合金的主要合金元素,都是因为这些元素在基体金属中的固溶度较大的缘故。 进行固溶强化时,往往采用多元少量的复杂合金化原则(即多种合金元素同时加入,但每种元素加入量少),使固溶体的成分复杂化,这样可以使固溶体的强化效果更高,并能保持到较高的温度。 图3 原子尺寸对强化的影响 图4 固溶体中镁对退火铝-镁合金拉伸性能的影响 过量的合金元素加入到基体金属中去,一部分溶入固溶体,超过极限溶解度的部分不能溶入,形成过剩的第二相,简称过剩相。过剩相对合金一般都有强化作用,其强化效果与过剩相本身的性能有关,过剩相的强度、硬度越高,强化效果越大。但硬脆的过剩相含量超过一定限度后,合金变脆,力学性能反而降低。此外,强化效果还与过剩相的形态、大小、数量和分布有关。第二相呈等轴状、细小和均匀分布时,强化效果最好。第二相很大、沿晶界分布或呈针状,特别是呈粗大针状时,合金变脆,合金塑性损失大,而且强度也不高,常温下不宜大量采用过剩强化,但高温下的使用效果可以很好。另外,强化效果还与基体相与过剩相之间的界面有关。 过剩相强化与沉淀强化有相似之处,只不过沉淀强化时,强化相极为细小,弥散度大,在光学显微镜下观察不到;而在利用过剩相强化合金时,强化相粗大,用光学显微镜的低倍即能清楚看到。过剩和强化在铝合金中应用广泛,几乎所有在退火状态使用的两相合金都应用了过剩相强化。或者更准确地说,是固溶强化与过剩相强化的联合应用。过剩相强化有时亦称复相强化或异相强化。 非共格硬颗粒弥散物对铝合金的强化称弥散强化。为取得好的强化效果,要求弥散物在铝基体中有低的溶解度和扩散速率、高硬度(不可变形)和小的颗粒(0.1μm左右)。这种弥散物可用粉末冶金法制取或由高温析出获得,产生粉末冶金强化和高温析出强化。 由弥散质点引起的强化包括两个方面:弥散质点阻碍位错运动的直接作用,弥散质点为不可变形质点,位错运动受阻后,必须绕越通过质点,产生强化,弥散物越密集,强化效果就越好;弥散质点影响最终热处理时半成品的再结晶过程,部分或完全抑制再结晶(对弥散粒子的大小和其间距有一定要求),使强度提高。弥散强化对常温或高温下均适用,特别是粉末冶金法生产的烧结铝合金,工作温度可达350℃。弥散强化型合金的应变不太均匀,在强度提高的同时,塑性损失要比固溶强化或沉淀强化的大。熔铸冶金铝合金中采用高温处理,获得弥散质点使合金强化,越来越得到人们关注。在铝合金中添加非常低的溶解度和扩散速率的过渡族金属和稀土金属元素,如含Mn、Cr、Zr、Sc、Ti、V等,铸造时快速冷却,使这些元素保留在α(Al)固溶体中,随后高温加热析出非常稳定的0.5μm以下非共格第二相弥散粒子,即第二类质点。其显微硬度可大于5000MPa,使合金获得弥散强化效果。 这些质点一旦析出,很难继续溶解或聚集,故有较大的弥散强化效果。以Al-Mg-Si系合金为例,加入不同量的过渡元素可使抗拉强度增加6%~29%,屈服强度提高最多,达52%。此外,弥散质点阻止再结晶即提高再结晶温度,使冷作硬化效果最大限度保留,尤以Zr和Sc提高Al的再结晶温度最显著。 从过饱和固溶体中析出稳定的第二相,形成溶质原子富集亚稳区的过渡相的过程,称为沉淀。凡有固溶度变化的合金从单相区进入两相区时都会发生沉淀。铝合金固溶处理时获得过饱和固溶体,再在一定温度下加热,发生沉淀生成共格的亚稳相质点,这一过程称为时效。由沉淀或时效引起的强化称沉淀强化或时效强化。第二相的沉淀过程也称析出,其强化称析出强化。铝合金时效析出的质点一般为G.P区,共格或半共格过渡相,尺寸为0.001~0.1μm,属第三类质点。这些软质点有三种强化作用即应变强化、弥散强化和化学强化。时效强化的质点在基体中均匀分布,使变形趋于均匀,因而时效强化引起塑性损失都比加工硬化、弥散强化和异相强化的要小。通过沉淀强化,合金的强度可以提高百分之几十至几百倍。因此,沉淀强化是Ag、Mg、Al、Cu等有色金属材料常用的有效强化手段。 沉淀强化的效果取决于合金的成分、淬火后固溶体的过饱和度、强化相的特性、分布及弥散度以及热处理制度等因素。强化效果最好的合金位于极限溶解度成分,在此成分下可获得最大的沉淀相体积分数。 铝合金晶粒细化,晶界增多,由于晶界运动的阻力大于晶内且相邻晶粒不同取向使晶粒内滑移相互干涉而受阻,变形抗力增加,即合金强化。晶粒细化可以提高材料在室温下的强度、塑性和韧性,是金属材料最常用的强韧化方法之一。晶界上原子排列错误,杂志腹肌 晶界上原子排列错乱,杂质富集,并有大量的位错、孔洞等缺陷,而且晶界两侧的晶粒位向不同,所有这些都阻碍位错从一个晶粒向另一个晶粒的运动。晶粒越细,单位体积内的晶界面积就越大,对位错运动的阻力也越大,因而合金的强度越高。晶界自身强度取决于合金元素在晶界处的存在形式和分布形态,化合物的优于单质原子吸附的,化合物为不连续、细小弥散点状时,晶界强化效果最好。晶界强化对合金的塑性损失较少,常温下强化效果好,但高温下不宜采用晶界强化,因高温下晶界滑移为重要形变方式,使合金趋向沿晶界断裂。 铝合金的晶粒细化的方法主要有三种。 (1)细化铸造组织晶粒 熔铸时采用变质处理,在熔体中加入适当的难溶质点(或与基体金属能形成难熔化合物质点的元素)作为非自发晶核,由于晶核数目大量增加,熔体即结晶为细晶粒。例如,添加Ti、Ti-B、Zr、Sc、V等都有很好的细化晶粒的作用;另外,在熔体中加入微量的,对初生晶体有化学作用从而改变其结晶性能的物质,可以使初生晶体的形状改变,如Al-Si合金的Na变质处理就是一个很好的例子。用变质处理方法,不仅能细化初生晶粒,而且能细化共晶体和粗大的过剩相,或改变它们的形状。此外,在熔铸时,采取增加一级优质废料比例、避免熔体过热、搅动、降低铸造温度、增大冷却速度、改进铸造工具等措施,也可以(或有利于)获得细晶粒铸锭。 (2)控制弥散相细化再结晶晶粒 抑制再结晶的弥散相MnAl₆、CrAl₇、TiAl₃、ScAl₃、VAl₃和ZrAl₃质点,在显微组织中它们有许多都是钉扎在晶界上,使晶界迁移困难,这不仅阻碍了再结晶,而且增加了晶界的界面强度,它们可以明显细化再结晶晶粒。这些弥散相的大小和分布,是影响细化效果的主要因素,越细小越弥散,细化效果越好。弥散相的大小和分布主要受高温热处理和热加工的影响。获得细小弥散相的方法主要有:在均匀化时先进行低温预处理形核,然后在进行正常热处理;对含Sc的合金采用低温均匀化处理;对含Mn、Cr的合金采用较高温度均匀化处理;还可以采用热机械加工热处理的方法获得细小弥散相,即对热加工后的铝合金进行高温预处理,然后再进行正常的热加工,如7175-T74合金锻件就采用过这种工艺;此外,也可以通过热加工的加热过程和固溶处理过程来调控弥散相。 (3)采用变形及再结晶方法细化再结晶晶粒 采用强冷变形后进行再结晶,可以获得较细的晶粒组织;采用中温加工可以获得含有大量亚结构的组织;采用适当的热挤压并与合理的再结晶热处理相结合,可以获得含有大量亚结构的组织,得到良好的挤压效应;在再结晶处理时,采用高温短时,或多次高温短时固溶处理均可以获得细小的晶粒组织。 采用高强度的粉、丝和片状材料和压、焊、喷涂、溶浸等方法与铝基体复合,使基体获得高的强度,称为复合强化。按复合材料形状,复合强化可分为纤维强化型、粒子强化型和包覆材料三种。晶须和连续纤维常作纤维强化原料,粒子强化型有粉末冶金和混合铸造两类。对烧结铝合金属粒子复合强化合金,多数学者认为是弥散强化的典型合金。复合强化的机理与异相强化相近。这种强化在高温下强化效果最佳,在常温下也可显著强化,但塑性损失大。可以用作增强纤维的材料有碳纤维、硼纤维、难熔化合物(Al3O2、SiC、BN、TiB2等)纤维和难熔金属(W、Mo、Be等)细丝等。这些纤维或细丝的强度一般为2500~3500MPa。此外,还可用金属单晶须或Al3O2、B4C等陶瓷单晶须作为增强纤维,它们的强度就更高。但晶须的生产很困难,成本很高。 铝合金是一种典型的基体材料。以硼纤维增强和可热处理强化的合金(如Al-Cu-Mg、Al-Mg-Si)或弥散硬化的Al-Al3O2系为基的金属复合材料,其比强度和比刚度为标准铝合金的2~3.5倍,已被用于航空及航天工业。 金属基体复合材料的强化机理与上述固溶强化及弥散强化等机理不同,这种强化主要不是靠阻碍位错运动,而是靠纤维与基体间良好的浸润性紧密粘结,使纤维与基体之间获得良好的结合强度。这样,由于基体材料有良好的塑性和韧性,增强纤维又有很高的强度,能承受很大的轴向负荷,所以整个材料具有很高的抗拉强度及优异的韧性。此外,这种材料还能获得很高的比强度、很高的耐热性及抗腐蚀性,是目前材料发展的一个新方向。 不可热处理强化铝合金的强化 纯铝、Al-Mg、Al-Mg-Sc、Al-Mn合金属于不可热处理强化铝合金,主要靠加工硬化和晶界强化获得高强度,辅助强化机制还有固溶强化、过剩相强化、弥散相强化等。加工硬化可通过热变形、冷变形、冷变形后部分退火而不同程度地获得。热变形产生亚结构强化,变形温度越高,亚晶尺寸越粗大,强化效果越差,但塑性相当高。经完全退火的材料进行不同程度的冷变形,冷变形率越大,制品强度越高,但塑性也越低。冷变形的加工硬化效果最大。充分冷变形的制品在不同温度下退火,控制回复和再结晶阶段,可保留不同程度的加工硬化量即不同的强化效果。 可热处理强化铝合金的强化 工业生产的可热处理强化铝合金有Al-Cu-Mg、Al-Cu-Mn、Al-Mg-Si、Al-Zn-Mg和Al-Zn-Mg-Cu合金,以及开发中的Al-Cu-Li和Al-Mg-Li合金等。这些合金普遍采用淬火时效,并主要通过沉淀强化方法来获得很高的强度,辅助强化机制也有固溶强化、过剩相强化、弥散相强化、晶界强化等。自然时效时G.P区为主要强化相,人工时效主要是G.P区加过渡相起强化作用,过时效时才出现稳定相,出现稳定相后强度降低。 形变时效与挤压效应强化 在Al-Cu系和Al-Mg-Si系合金中,较多采用形变时效方法获得高强度,该方法包括T3、T8和T9三种状态,都是利用时效强化和冷作硬化的交互作用及强化在一定程度上的叠加作用。2124-T8厚板因冷变形产生的大量滑移线,滑移线上成排分布着时效析出相,二者的联合作用使塑性变形更为困难,即强度进一步提高。 可热处理强化铝合金挤压制品淬火时效后的强度比其他方法生产的同一合金相同热处理状态下的强度高,这一现象称为挤压效应。其组织观察发现全部或部分保留了冷作硬化效应,基体中保留了大量亚结构,故强化是时效强化和亚结构强化的叠加。 Al-Si合金的强化 Al-Si系变形铝合金,特别适合于生产活塞等模锻件,合金中硅含量ω(Si)=12%~13%,还含有一定量的Cu、Mg、Ni等。组织中有较多的结晶时生成的共晶硅,均布在软的α(Al)基体上,尺寸大都在5μm左右,硬且脆。这种共晶硅是铝合金中异相强化的典型例子。由于异相强化具有耐高温、耐磨和中强等特点,故特别适合于制作活塞。 来源:《铝合金的热处理》、《简明铝合金加工手册》、网络
免责声明:本网站所转载的文字、图片与视频资料版权归原创作者所有,如果涉及侵权,请第一时间联系本网删除。
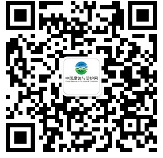
官方微信
《腐蚀与防护网电子期刊》征订启事
- 投稿联系:编辑部
- 电话:010-62316606
- 邮箱:fsfhzy666@163.com
- 腐蚀与防护网官方QQ群:140808414