《涂层与防护》基于聚脲弹性体技术的铁路货车长效防腐解决方案
2024-07-18 14:46:10
作者:涂料工业 来源:涂料工业
分享至:
铁路货车主要用于运输矿石、煤炭等大宗货物,运输工况较为恶劣,受货物装卸磨损、磕碰及化学腐蚀等因素影响,车体内部的腐蚀一直是困扰行业的难点问题。2019 年因我公司某出口铁路矿石敞车项目车体内部 20 a 防腐需要,基于聚脲弹性体材料在耐磨、耐冲击及耐腐蚀方面卓越的性能,经论证分析和试验研究,选择使用聚脲弹性体防腐方案并取得良好的效果。该铁路矿石敞车车体采用全碳钢结构,主要用于运输粒径为 8~32 mm 的铁矿石颗粒。早在 2007 年我公司就为该用户生产 1 000 多辆同款车型,因运输工况恶劣,该批车辆在使用约 10 a 后,大部分车辆因车体内壁磨损和锈蚀而出现墙板局部严重减薄甚至穿透的情况。考虑到使用的经济性,用户不愿在车辆运营期间投入相关资源进行涂层维护和车体维修工作,因此选择直接报废腐蚀超标车体而重新制造,并要求后续新造车体要在免维护、维修的条件下达到20 a的使用寿命。按用户原技术规范要求,为达到防腐和耐磨的双重目的,车体内部采用单层无机硅酸锌底漆,干膜厚度 75~125 μm。从车辆使用现场考察的情况看,墙板减薄现象主要发生在侧墙板内壁上半部,穿孔现象也是表现为由内到外经现场考察分析,引起墙板减薄及穿孔的主要原因为车体内表面的无机硅酸锌涂层在运用过程中因铁矿石中微酸性水分的腐蚀和矿石装卸过程中的磨损,逐渐被腐蚀和磨损殆尽,致使钢板基体失去防护屏障而裸露在外;后期,在雨水及铁矿石中微酸性水分和矿石磨蚀的双重作用下,车体墙板被逐渐腐蚀减薄直至穿孔。根据以上分析,墙板减薄和穿孔的根源在于防护涂层提早失效,如能通过引入性能优越的长寿命耐磨防腐涂层材料,解决好涂层的腐蚀和磨损失效问题,墙板减薄及穿孔问题则会迎刃而解。
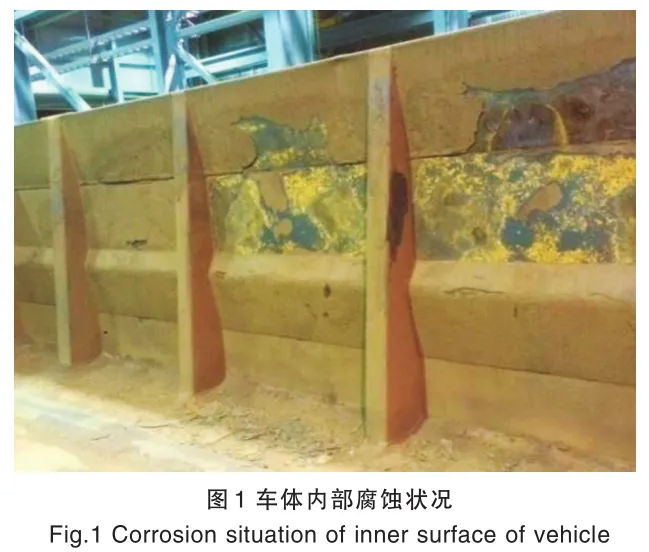
聚脲弹性体是一种由异氰酸酯组分(简称 A 组分)与氨基化合物组分(简称R组分)反应生成的多功能防护材料,其涂覆于金属表面形成的涂层具有优异的耐磨、耐老化、抗腐蚀及柔韧性等性能,尤其适用于使用寿命15 a以上的超重防腐领域。该项技术于20世纪 80 年代中期由美国 Texaco 公司开发并获得商业应用,90年代末期开始在国内应用,历经20多年的发展,目前该技术已趋于成熟并向多功能化、高性能化、高品质化方向发展。在金属防腐领域,该技术已在石化设备、矿山机械、汽车及军工领域得到大量应用。(1)涂层材料本身具有优异的耐磨性、拉伸强度、伸长率和低温韧性等物理机械性能,且与底材的附着力强,能够抵抗本项目中矿石的摩擦和冲击。实验室测试表明,聚脲涂层的耐磨性能是普通聚氨酯弹性体的 10 倍以上,是碳钢的 20 倍左右;在碳钢表面的附着力可达14 MPa。(2)可通过专用喷涂设备,一次性喷涂膜厚可达数毫米,大大延长涂层的耐磨及防腐蚀寿命。(3)由于分子结构稳定,涂层具有优异的耐水、耐化学腐蚀及耐老化等性能,防护功能较为持久。(4)聚脲材料固含量接近100%,不含挥发性有机溶剂,施工过程安全、环保。基于聚脲弹性体材料自身优异的耐磨、耐冲击性能,再加上高膜厚、强附着力及优良的耐老化性等因素,是解决本项目中车体内部提早腐蚀问题的最佳方案。表 1 所列为聚脲涂层和原无机硅酸锌涂层主要技术性能在实验室的测试结果。从表 1 对比数据看,聚脲涂层与原无机硅酸锌涂层相比,不仅在断裂伸长率、拉伸强度和撕裂强度等力学性能方面有独特的优势,而且在耐磨性、耐冲击性、附着力、耐酸性、耐盐雾性等关键技术指标方面远高于原无机硅酸锌涂层。

为评价涂层的抗矿石冲蚀性能,采用类似表面喷砂的方法,向涂层表面喷射磨料。试验喷射进气压力0.7 MPa(与一般喷砂工艺压力相同),喷砂口距试件距离约为50 mm,对试件表面进行定位喷射。试验结果:聚脲涂层连续喷射固定点达 10 min,试件涂层没有击穿(涂层厚度为 3 mm),而原无机硅酸锌底漆涂层在瞬间即被打掉露出金属底材。

参照 GB/T 20624.2—2006 落锤冲击试验方法评价涂层的抗冲击能力。试验时,落锤从管道上部释放,在管道内垂直落下击打到涂有涂层的试板中心。试验采用1.3 kg和4.15 kg两种规格的落锤,落锤管道高度为3.6 m。试验结果:涂层厚度为3 mm和5 mm的试板涂层击伤区域周围涂层保持完好,无开裂、起皮及脱落等现象。
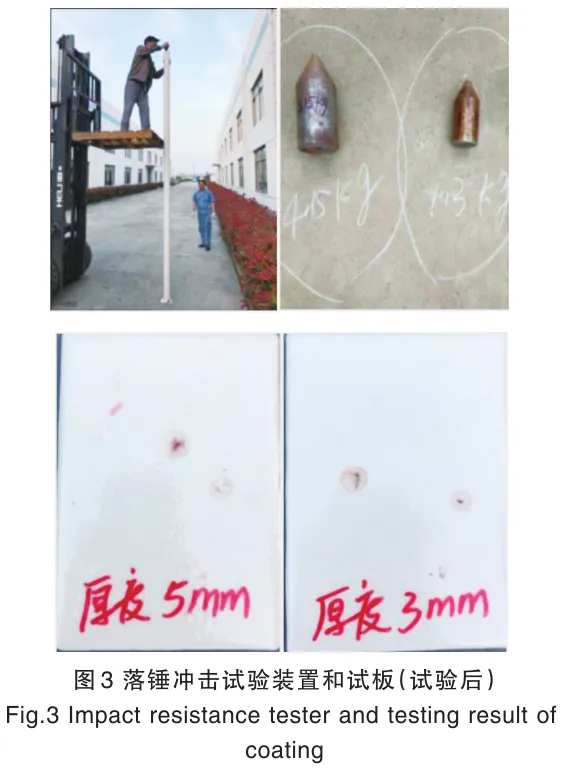
涂层附着力试验按照 GB/T 5210—2006 拉开法进行。试板表面取3点测试,测试数据分别为13.2 MPa、15.1 MPa和 13.7 MPa,均 100%从粘胶层断裂,附着力明显优于常规防腐涂层。根据考察及试验研究情况,最终确定矿石敞车内部采用由打底层和聚脲层组成的复合型聚脲涂层体系,具体构成见表2。
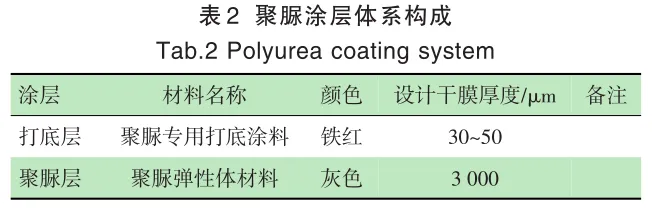
聚脲专用打底涂料以聚脲/聚氨酯树脂为主要原料,适用于金属表面。涂层致密坚固,具有优良的屏蔽性能和抗阴极剥离性能,与后道聚脲涂层配套使用,能增强聚脲涂层的附着力。聚脲弹性体材料以特种胺基聚醚树脂和特种异氰酸酯为主要原料,具有优良的耐冲击性、高耐磨性和出色的防腐性能。聚脲涂层的性能不仅跟材料的品质有关,而且与其涂装工艺有密不可分的关系, “三分材料,七分涂装”的说法同样适用于聚脲涂层。适合的涂装工艺能使材料充分发挥其防护性能。根据制定的涂装技术方案,车体内部涂聚脲涂层(包括打底涂层),外部涂防锈底漆和面漆。根据车辆内、外部涂层的工艺特点并结合涂装生产线布局情况,制定的聚脲涂层涂装工艺流程为:钢结构缺陷处理→表面喷砂处理→灰尘清洁→打底涂层喷涂→打底涂层干燥→外部喷涂底、面漆→外部涂层遮盖防护→聚脲涂层喷涂→检查修补。表面处理是聚脲材料涂装工艺中的重要环节,表面处理质量的好坏直接关系着聚脲涂层的防护性能。在聚脲材料的涂装工艺中,表面处理工艺应得到充分重视并切实做到。在本项目中,表面处理工艺主要包括以下3部分:与普通油漆材料相比,聚脲材料喷涂黏度很大,对底材的渗透性不好,钢材表面的锐边、孔隙及飞溅等缺陷会影响成膜及涂层附着力,容易造成后期聚脲涂层起泡和脱落。因此,涂装前,需对车体内部表面进行仔细处理:所有的锐边打磨处理成≥R2 的圆角;焊缝的气孔、咬边等缺陷须全部修复;焊接飞溅须打磨清理干净。喷砂处理是目前普遍使用且处理效果最为彻底的一种技术,对于厚3 mm左右的聚脲涂层来说,喷砂处理工艺产生的表面粗糙度将显著提高聚脲涂层的附着力,是聚脲涂层的最佳表面处理方法。在本项目中,喷砂处理的工艺标准为:车体内部表面喷砂处理达到 ISO 8501-1 中规定的 Sa 2 1 / 2 级,粗糙度达到 75~100 μm。喷砂前应注意将表面可见的油污清洗干净。喷砂质量验收完工后,应对车体内部表面用真空吸尘器进行一次彻底的清洁。重点针对角落及焊缝处的灰尘,确保清洁后的底材表面干净、干燥,无灰尘、油污及其他污染物。喷砂后的钢铁表面应于 4 h 内喷涂打底涂层,间隔时间越短越好。打底涂层采用空气喷枪喷涂,喷涂干膜厚度控制在30~50 μm。聚脲材料采用聚脲专用喷涂机喷涂,该设备主要由供料系统、加压加热计量控制系统(主机)、输送系统和雾化系统组成,其特点是功能先进,实现自动混合,可控制温度和压力。为了使涂层厚度尽量均匀,喷涂聚脲时,下一道要覆盖上一道的 50%,并按从上到下、从里到外的顺序施工。喷涂过程中应及时进行检查,表面若有针孔等缺陷,应及时修补。
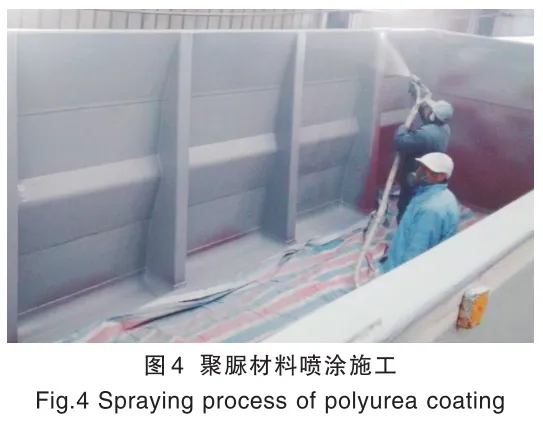
聚脲涂层喷涂后应尽快进行厚度检测,发现厚度不够的地方应在 6 h 内及时补喷。为避免存在漏涂点,应进行电火花检测,若出现漏点,应在 6 h 内及时补喷。超过 6 h 后再补喷时,需要在补喷界面处涂刷聚脲专用搭接剂。涂层附着力采用制作随车试板的方法测试。聚脲涂层附着力要求达到 10 MPa 以上,测试方式符合GB/T 5210—2006。以上所述聚脲弹性材料及应用涂装工艺已在该矿石敞车上成功应用,并经过近5 a的运用考验,涂层未出现开裂、起皮、剥离等质量问题,防护效果良好。因用户满意度较高,一直在追加订单,截止目前,累计生产达800多辆。
本研究阐述的聚脲弹性体涂层防护技术,经试验及初步运用检验,应用于铁路矿石敞车内部后具有优异的耐磨、耐冲击及防腐性能,能够大幅提升铁路矿石敞车车体的使用寿命。该项技术尤其适用于防护寿命15 a 以上的超重防腐领域,且因涂装过程中安全、环保,符合当今绿色环保及安全的发展方向,是交通车辆及类似钢结构工程项目值得借鉴的一项解决方案。
免责声明:本网站所转载的文字、图片与视频资料版权归原创作者所有,如果涉及侵权,请第一时间联系本网删除。