摘要:针对超级双相不锈钢的传统铸造方法易出现漏钢、漏渣、表面成型差等问题,采用抽锭电渣重熔处理,通过改变重熔过程中的供电制度、冷速条件、液固界面位置等因素,对船用脱硫塔大直径板坯进行技术设计,分析了坯锭的内部凝固质量和表面状态。结果表明:重熔过程增大了钢—渣界面积,起到渣洗的作用,使得重熔的钢纯度高、非金属夹杂物少,满足了生产要求。在重熔铸坯的成型过程中,最合适的工艺参数是抽锭速度由1.5 mm/min缓慢增加到12mm/min,炉顶电压为62V,二级电流维持在19 KA,电极熔化速度在1100~1200 kg/h。得到的坯锭分布均匀,并且表面质量良好,无夹渣、重皮等缺陷,表面修磨量小于3mm,可进行后续轧机轧制等工序。
1 引言
现代化工业快速发展,重型机器制作、压力容器、炉具制作等各式钢板的需求每年不断提高。为保证大型设备的安全性和可靠性,其使用的钢材质量要求变得越来越严格,其中,双相不锈钢是一种固溶组织中铁素体与奥氏体组织分别占比至少40%,同时具备较高的强度和耐腐蚀性的钢种材料。自1930年,第三代双相不锈钢的研发和应用已经开始,以2507钢为代表的超级双相不锈钢是最显著的例子,如表1所示,其化学成分中碳的质量占比为0.01%~0.02%,钼和氮的含量则较为丰富,质量占比分别为4%和0.3%。同时,铁素体的体积占比为40%~45%,该结构展现出优秀的抗孔蚀性能。
在超级双相不锈钢成型工艺中,传统铸造方法易出现漏钢、漏渣、表面成型差等问题。电压重熔技术需要将一种自消耗电极放入水冷结晶器的渣池,使渣池的温度逐渐升高至熔化,形成的液态金属通过渣池后进入金属熔炉。这个金属熔炉会在水冷的环境下逐步硬化,最终形成钢锭。该流程具备高生产效率、大产量以及低成本的优势。图1描绘了抽锭电渣重熔的基本原理,通过利用浮力和洛伦兹力在渣池中引起旋流。该旋流的形成会影响金属液滴的下落和渣池内的温度分布,从而直接影响金属的凝固质量。此外,抽锭电渣重熔与传统电渣重熔流程存在差异,体现在金属锭是由下至上逐步凝固,并在整个电渣重熔流程中,钢锭始终从结晶器底部连续抽取。再者,由于渣-晶界面位置保持不变,导致钢锭不同位置的热传递系数保持基本稳定。因此,电渣重熔工艺可用于生产大吨位和直径的钢锭。在结晶器的出口部位需要加设额外的冷却手段,以便加强钢锭内部的冷却效果,保障钢锭内部凝固质量的稳定性,适配于脱硫塔钢锭的生产过程。
电力供应方式在抽锭电渣重熔过程有两种形式,一种是电极-钢锭-底部水箱组合,另一种是电极/结晶器-钢锭-底部水箱组合。电极-钢锭-底部水箱形式中,电力传输的路线是从变压器通过短网和电极连接至钢锭,然后到达底部水箱。此形式下,高温的渣池部分位于金属电极下方并且接近金属熔液水面。短网的电压降随着钢锭长度的增加而提高,因此存在钢锭长度的限制。因此,这种电力供应方式被广泛用于直径小于?1000mm 的钢锭的生产。电极/结晶器-钢锭-底部水箱供电方式在电极-钢锭-底部水箱形式的基础上增加了一条路径,即从变压器通过结晶器到钢锭,然后到底部水箱。此模式使用2个独立的电源供电,通过调整2个变压器的输入功率改变渣池的温度分布,以得到浅平的金属熔液。特别是在大直径钢锭的重熔过程中,通过结晶器的供电方式对钢锭冷却质量的影响起到了关键的作用。此外,在更换电极时,可以将热量从结晶器的电源电路传导到渣池中,以保持温度不降低,从而延长电极更换的操作时间。对小直径的钢锭进行重熔时,钢锭的表面也非常光滑。因此针对于船用脱硫塔钢锭电渣重熔技术中使用电极/结晶器-钢锭-底水箱供电方式,具体原理如图2所示。
在考虑超级双相不锈钢的特性基础上,进行了抽锭电渣重熔的处理,并在重熔过程中调整了供电制度、冷却速度和抽锭时的液固界面位置等参数以控制液固界面的形状。特别为船用脱硫塔大直径板坯进行了技术设计,选择了电极/结晶器-钢锭-底水箱作为供电方式,并探究了电渣板坯温度场控制、渣系配比以及熔速-抽速的匹配对凝固质量和表面状态的影响趋势。
2 方案设计
2.1 研究路线
铁水脱硫—电炉冶炼—精炼—电渣重熔—控制轧制—下线缓冷—热处理—精整—检验。
2.2 电炉冶炼及电渣重熔工艺电弧炉为电渣重熔冶炼提供所需的消耗电极,其工作流程包括:初炼炉—精炼炉—连铸—铸坯检验(表2):
图3描绘了板块电渣重熔冶炼的步骤,工艺流程涵括了铸坯打磨、假电极焊接、渣料准备、渣炉化渣还有电渣重熔,具体的工艺参数设置如表2所示。适用的渣料包含CaF2、Al2O3、CaO、MgO 及SiO2,成分比例为CaF2 ∶Al2O3∶CaO∶MgO∶SiO2=50∶19∶19∶6∶6,总质量是290 kg。渣料在800 ℃下加热8~10h后,让其在渣化炉内熔化。在液态熔渣温度增加到1600~1700℃时,将其导入结晶器。接着插入电极到渣池,深度约15~20 mm,然后开启重熔过程。首先高功率化钢,形成金属熔池,然后让钢在引锭板上成型凝固,进而抽出锭子。锭的抽取速度初始为1.5mm/min,慢慢提升至目标速度12mm/min。这个时候,炉口电压设置为62V,二次电流为19kA,并控制电极熔化速度在1100~1200kg/h。
2.3 轧制及冷却工艺为了防止奥氏体晶粒因温度过高或加热时间过久而过度增长,将板坯的加热温度控制在1200~1260 ℃。根据“高温、低速、大压”的操作规律,在四辊可逆轧机上设定了奥氏体的再结晶区和未再结晶区两个阶段的温度。第一阶段的轧制温度范围是1070~1180℃,第二阶段的起始轧制温度设定在860~900℃,轧制结束时的温度控制在830~860℃。选用加速冷却方式进行冷处理,最后冷却的温度维持在580~620℃。为提高钢板性能的一致性,最后进行正火处理。
3 结果讨论
3.1 电渣重熔板坯内部质量控制 对S2507超级双相不锈钢板的电渣坯锭的结晶组织进行了详尽的剖析,发现该结晶组织是由边界地带的细小等轴晶区、中心地带的柱状晶区以及核心部位的粗等轴晶区所构成。在电渣锭的角部和中心部位进行取样,并将样品加热到1250℃,维持3.5 h后,通过水冷使其迅速冷却下来,这样做能够使高温组织状态得以保持。查看样品坯锭长度方向上的奥氏体形状和分布。图4(a)展示了电渣锭核心部分的奥氏体形态,图4(b)展示了电渣锭边角部分的奥氏体形态。从图4中可以看出,钢锭核心部分的奥氏体大部分是粒状的,而钢锭边角部分的奥氏体则主要是板条状的,平行度较高。
不锈钢凝固模式为:L→δ +L→δ +L+γ →δ +γ 。δ铁素体将首先从液态分离出来,伴随着复杂的共晶或包晶反应,在后续会发生由固态相向γ相的转换,若δ铁素体的转变没有及时完成,其会作为残余铁素体留在枝晶主干的核心,以此形态存在于室温结构中。在电渣重熔扁锭凝固过程中,奥氏体的析出长大是扩散型相变,主要受冷却速率和晶体缺陷的数量影响,冷却速率直接决定了元素能够迁移的时间,而晶体缺陷则决定了原子迁移的能垒。
由于在电渣坯锭的核心,熔融的金属离发热区是最近的,固液两相区在凝固时会放出潜藏的热量,这使得液态区的热度逐渐平缓,热值的分布将呈现无定向的状态,最终在中央区域出现较粗大的均匀晶体区,这个区的生长速度很慢,产出的冷却铁素体瑕疵少,形成奥氏体需要克服巨大的阻力,需要非常大的冷却才能形成,而这个部分的冷却环境是最差的,不利于奥氏体的生长,所以,奥氏体的含量一般较低,一般以球形和岛形状为主。 在电渣坯锭的边角,此处位于加热区的最远端,同时得到了结晶器宽边和窄边的冷却,拥有最优的冷却环境,这导致了金属凝固速度的加快,过早出现了富含铁素体晶界等缺陷,同时元素的扩散途径也增加了,因此在奥氏体分解后,其可以沿着柱状晶的生长方向迅速生长,其形态与柱状晶的区域相当类似,展现出粗糙的片状结构,拥有较好的平行度。 大直径钢板的主要特质在于其较低的压缩性,这使得通过轧制修补连铸坯内的空洞等缺陷变得相当困难。因此,对钢板内部的缺陷检测势在必行。至于那些经过实验制作的成品钢板,进行了一一的探伤检查,测试结果显示,除了钢板的两端,其他部分在全厚度上均满足探伤一级的合格准则。 在冶炼过程中,铁液在穿越有一定深度的熔渣过程中,将以液滴形态逐个通过。于是,相对于平滑质地的液态金属,铁液滴的单位面积会扩大几百倍,从而进一步提升钢与熔渣之间的接触面积,并提高熔渣对钢中非金属杂质的吸附效率。在这个环节中,钢中的杂质会按照特定的规律在穿过熔渣后重新分散,因此降低了钢液中的杂质含量,实现了熔渣的净化作用。根据对电渣重熔处理后的钢在实验中的检测结果显示,钢的纯度高,并且非金属悬浮物的含量少,完全达到了生产制造要求。
3.2 电渣重熔板坯表面质量控制 针对大型的电渣重熔工艺,板坯表面质量的主要缺陷包括波纹、重皮、漏渣、凹陷或铸锭不饱满。(1)渣系对铸坯表面质量的影响。渣皮厚度对电渣重熔锭的表面品质有着显著的影响,这是核心要素。只有保证炉渣厚度的稳定性或微小的改变,才能使铸锭的表面生成均匀、光滑。但是,只要有某些炉渣层的厚度发生剧烈的改变,铸锭表面就可能出现像渣槽、重皮、漏渣等问题。在大板坯电渣重熔的过程中,铸锭和结晶器的相对移动可能会引起渣池温度的波动。频繁的温度波动并不利于形成均匀的渣皮厚度。因此,在大板坯电渣重熔过程中,应采用黏度适当低、粘度稳定性好的炉渣体系。对于取得均匀厚度的渣皮以及提升钢锭的表面质量有益的,是那些粘度较小且稳定性较高的渣。相反,炉渣的粘度会随着温度的升高而突然变化。在滤渣池的温度环境发生急剧改变的情况下,可能会引起渣皮厚度的快速变化,如突然增厚或减薄,这容易在铸锭表面引发渣槽、波纹、双皮、漏渣等一系列表面缺陷。
在大规模的电渣重熔板坯生产过程中,由于结晶器和钢锭的相互移动,固态的渣皮承受着来自结晶器壁与钢锭外表的摩擦阻力。在遭受这2种阻力的影响下,渣皮极易产生脆性的分裂,导致熔池内的钢液或渣液流散,触发重皮、漏渣等一系列的表面缺陷,对钢锭的表面质量产生影响。因此,固态的渣皮在高温的环境下,必须拥有适当的摩擦系数、力量和塑性能力。在本研究的重熔渣系中,加入了适量的Al2O3 和MgO 使得渣内包含了一部分具有高硬度、高熔点的尖晶石和黄长石等矿物质,这些矿物质在高温(1200 ℃)下难以发生变形,既增强了渣的强度,又有助于其强化。SiO2 矿物在高温作用下,容易产生变形或软化,生成具有塑性变形能力的矿物、非晶质矿物和低熔物相等,进而提高渣系的塑性变形能力,使电渣表面厚度均匀,成型性较好。(2)熔池输入功率对铸坯表面质量的影响。在电渣重熔的过程中,输入功率对铸造零件表面质量的效应是相当复杂的。通常而言,如果电流和电压偏低,那么将会使得炉渣温度下降,渣皮会变得过于厚实,从而使得钢锭表面不再光滑。电流和电压的不稳定会导致铸坯表面质量的起伏,通常来说,电压对铸坯表面质量的影响更为突出。在研究报告中,当电压设置为62 V,二次电流为19 kA,板坯的表面质量等级达到最高,重熔之后能够达到一级。(3)抬结晶器速度控制方式的影响。在大板坯电渣重熔的生产过程中,坯料与结晶器之间始终存在相对运动,结晶器提升速度的稳定性对坯料的表面质量也有显著影响。升降结晶器的速度突然变化,会增加坯料与渣壳之间的摩擦力。在情况较轻的情况下,可能会出现一些表层缺点,比如重皮或炉渣泄漏,在严重的情况下,可能导致结晶容器发生形变。所以,在提高结晶容器的过程中,需要让速度改变得更加温和。
因此,在电渣重熔过程中,对填充比、渣系、渣量、供电制度以及抬结晶器速度控制方式等多方面进行了优化和调整。这样可以有效地提高电渣坯锭的表面质量。如图5所示,在电渣坯锭样本中,扁锭的表面质量优异,没有因漏钢、漏渣而产生的表面夹渣或重皮缺陷,而且表面修磨厚度小于3mm。
4 结论
本文采用抽锭电渣重熔处理,通过改变重熔过程中的供电制度、冷速条件、抽锭时的液固界面位置等因素控制液固界面形态,对船用脱硫塔大直径板坯进行技术设计,分析板坯温度场控制、渣系配比及熔速-抽速的匹配对内部凝固质量和表面状态的影响趋势。
(1)降碳保铬、增进金属得率、减少生产花费是重熔电渣技术的核心要点,通过安装连续测温仪器可以对熔池温度进行检测,利用炉口的钢渣混冲出钢,可以提升合金的收得率,进一步配上氧枪系统可有助于缩短冶炼的时长,显著改良与前后工艺的配套关系。(2)电渣板坯成型工艺是通过电极/结晶器-钢锭-底部水箱的电源方式进行设计的,使用2个独立的电源供电,通过改变2个变压器的输入能量以控制渣池的温度分布,从而创建一个平坦的金属熔池。在进行大直径钢锭的重熔操作时,结晶器的供电方法对钢锭凝固效果有决定性影响。(3)在重熔电渣铸坯的成型过程中,最佳的工艺参数是抽锭速度由1.5 mm/min缓慢增加到目标抽锭速度12mm/min,炉口电压保持在62 V,二级电流维持在19kA,电极的熔化速度在1100~1200 kg/h。得到的坯锭具有分布均匀,厚度一致的渣皮厚度,并且表面质量良好,无夹渣、重皮等缺陷,表面修磨量小于3mm,可进行后续轧机轧制等工序。
免责声明:本网站所转载的文字、图片与视频资料版权归原创作者所有,如果涉及侵权,请第一时间联系本网删除。
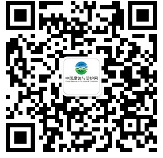
官方微信
《腐蚀与防护网电子期刊》征订启事
- 投稿联系:编辑部
- 电话:010-62316606
- 邮箱:fsfhzy666@163.com
- 腐蚀与防护网官方QQ群:140808414