Sm-Co永磁材料和Nd-Fe-B永磁材料是现有常用的稀土永磁材料,其中前者由于具有高居里温度和优异的高温性能,常应用于对温度要求比较高的领域;而后者在室温下的磁能积高,主要应用于对温度无较高要求的场合。由于Sm-Co永磁材料多在温度较高的场合中应用,其主要问题在于高温氧化;Nd-Fe-B永磁材料面临的问题则包括氧化和腐蚀。
目前Sm-Co永磁材料应用的主力军是2:17型Sm-Co永磁材料,其合金成分为Sm(Co,Fe,Cu,Zr)z(z=7~8.5)。2:17型Sm-Co永磁材料具有典型的纳米胞状结构,该结构由纳米尺度Sm2Co17胞体相(2:17 R)和SmCo5胞壁相(1:5 H)组成。
2:17型Sm-Co永磁材料兼具优良的磁性能、高温稳定性及耐腐蚀性,现已广泛应用于电子通讯、航空航天等领域,成为可在500 ℃或更高温度下应用的永磁材料。但是,Sm-Co永磁材料在高温环境下长期使用时,高温氧化会造成不可逆的磁损失,这是在高温环境中服役时所面临的主要问题。
当Sm-Co磁体长期暴露在高温环境中时,磁体会发生老化,氧化层结构分为外部氧化区(EOS)、中间层(ML)和内部氧化区(IOZ)。
磁体的氧化层结构如图1所示。将Sm(CobalFe0.22Cu0.08Zr0.02)7.5磁体在600 ℃下氧化1小时,磁体最外层的部分是外部氧化区(EOS),厚度约为1.4 μm,富含Co和Fe,为Co-Fe混合氧化物(Co3O4,CoFe2O4和Fe3O4等);紧挨着外部氧化区的部分为中间层(ML),厚度约为200 nm,富Co,含富Cu沉淀颗粒,且不含Sm;中间层下面为内部氧化区(IOZ),约10.4 μm厚,含有约22%的氧,含Sm2O3,fcc Co-Fe和bcc Co-Fe。Sm氧化后,磁体中的1:5 H相和2:17 R相分解为Co-Fe相。内部氧化区除O含量高外,Sm、Co、Fe、Cu等含量与中心磁体基本一致。内部氧化区发生的O扩散,会引起Sm的氧化导致体积膨胀,其厚度随氧化时间呈抛物线状增长。
图1 Sm-Co磁体氧化过程示意图
Sm-Co永磁材料在高温环境下应用时,随着氧化程度的增加,其磁性能急剧下降。因此,必须对磁体进行氧化防护处理,目前主要的防护技术包括合金化和涂层防护。
对于形状复杂的磁体,很难得到均匀的涂层,可采用合金化来提高其抗氧化性。研究表明在Sm-Co磁体中加入少量的Si,可以在磁体表面生成SiO2,从而有效地提高磁体的高温抗氧化能力。对Sm(Co0.76Fe0.1Cu0.1Zr0.04)7磁体,随着Si含量的不断增加,磁体经氧化后的质量增量显著减少,同时内部氧化区显著减小。进一步研究得知Si的添加在内部氧化区形成了SiO2,阻碍了氧的扩散进而减缓了磁体的氧化。
值得注意的是,该方法虽然显著提高了磁体的内禀矫顽力和抗氧化性,但同时也降低了磁体的剩磁和最大磁能积,所以必须选择合适的Si添加量,来平衡抗氧化性的提高与磁性能降低之间的矛盾,以满足实际应用的需求。
Sm-Co永磁材料的涂层主要用于提高磁体的抗高温氧化能力,基本原理是阻断或者减少氧在磁体中的扩散。例如,在磁体表面镀上一层金属(Al,Cu,Ni,Cr,Mo和W等),实验发现均匀且具有足够厚度(不小于10 μm)的涂层能够对磁体提供有效的保护。Sm-Co永磁材料常见涂层类型包括电镀Ni、电弧离子镀Cr2O3和磁控溅射镀Al2O3、包覆Si涂层和硼硅玻璃涂层等,其各自防护效果及特点如表1所示。
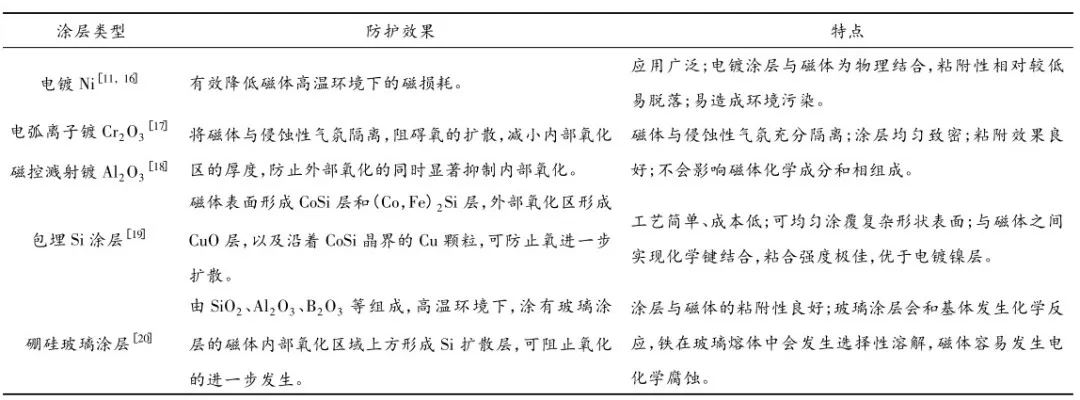
与Sm-Co永磁材料相比,Nd-Fe-B永磁材料的室温磁能积更高、价格更低,主要应用于对使用温度无过高要求的领域。按照制备工艺,Nd-Fe-B磁体主要可分为烧结、粘结和热变形磁体,其中烧结Nd-Fe-B磁体的应用最为广泛。Nd-Fe-B永磁体由主相、富Nd相和富B相三种主要的合金相组成。(1) 主相(Nd2Fe14B):硬磁相,具有高的饱和磁化强度和很强的单轴磁晶各向异性,约占磁体体积分数的84%。(2) 富Nd相(Nd5Fe2B6):非磁性相,以薄层状和块状形式存在,沿主相晶界或晶界交隅处呈网状分布,能促进磁体致密化,抑制晶粒的长大,并提高矫顽力,约占磁体体积分数的14%。(3) 富B相(Nd1+εFe4B4):介稳相,主要以颗粒状分布于主相晶界处,含量较小,对磁体磁性能的影响不大,约占磁体体积的2%。Nd-Fe-B永磁体除以上三种合金相组成外,还包括Nd2B5、NdB4、FeB、Nd2Fe7等诸多合金相。其中,Nd-Fe-B永磁体中富Nd相和富B相两相的化学活泼性较主相更大,极易发生氧化,且磁体中主相与其他相的电化学电位相差较大,容易在高温、湿热、电化学三种环境中发生氧化或腐蚀。其腐蚀过程示意图如图2所示。
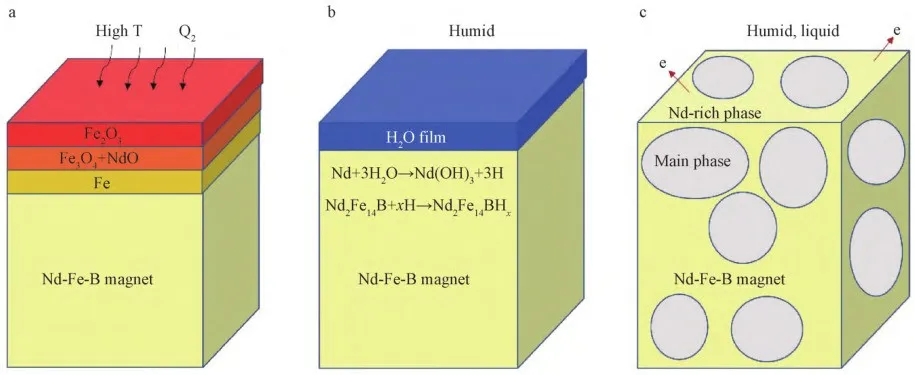
(a) 高温氧化;(b) 吸氢腐蚀;(c) 电化学腐蚀
在高温干燥(相对湿度低于15%)环境中Nd-Fe-B永磁体主要发生氧化,氧化层的深度与磁体暴露在空气中时间的平方根成正比(扩散控制过程),氧化包括以下两个过程 :(1) 晶间富Nd相(Nd5Fe2B6)的氧化化学性活泼的富Nd相优先发生氧化,产生疏松的氧化钕。反应式为:4Nd+3O2→2Nd2O3。(2) 主相(Nd2Fe14B)随后氧化分解为Fe和Nd2O3,Fe又进一步被氧化成Fe2O3和Fe3O4等产物。TEM表征显示发生氧化的磁体氧化层实际由三个连续层组成,最外层为Fe2O3层,次外层为Fe3O4和NdO层,最内层为Fe层 。Nd-Fe-B磁体的主相和富Nd相都有很强的吸氢能力,甚至在室温下也容易发生吸氢腐蚀。湿热的条件下,富Nd相与磁体表面空气中的水发生反应,生成氢氧化钕,释放出的氢原子又被主相所吸收。
氢的侵入会引起晶格变大,导致磁体发生局部的膨胀,从而造成材料局部的磁性能下降,严重的吸氢反应会使晶界发生断裂,甚至造成磁体粉化,导致不可逆的磁性能损失。
环境湿度对Nd-Fe-B磁体腐蚀速率的影响比温度影响更为显著,在高达155 ℃的干燥环境中未观察到明显的腐蚀现象,而在潮湿条件下,室温时磁体就会出现明显腐蚀。原因是在潮湿的环境下生成的含氢化合物等腐蚀产物与干燥环境下的腐蚀产物相比缺乏致密性,无法阻碍氧的进一步侵入。湿度过大时,磁体将发生电化学反应,加速腐蚀。
此外,在磁体清洗或电镀等工艺过程中,若操作不当,对防护镀层造成损坏,电镀液等会渗入磁体,加速其吸氢腐蚀,造成镀层结合力下降,沿磁体取向方向容易发生裂纹,最终导致磁体粉化失效。
常温湿润环境下,由于磁体中各相间的电化学电位不同且相差较大,容易形成原电池,Nd-Fe-B磁体便以电化学腐蚀为主。Nd-Fe-B磁体在不同溶液中各相腐蚀电位的顺序如下:
酸性溶液中:Nd2Fe14B主相>富B相>富Nd相
中性溶液中:富B相>Nd2Fe14B主相>富Nd相
碱性溶液中:Nd2Fe14B主相>富Nd相>富B相
Nd-Fe-B磁体的腐蚀速率很大程度上取决于富Nd相的抗腐蚀能力。在酸性、中性以及碱性溶液中,阳极为富B相和富Nd相,阴极为Nd2Fe14B主相,其中阳极的富B相和富Nd相分布在主相晶界处,含量较少,腐蚀电流密度更大,极易发生晶间腐蚀。
此外,对磁体进行镀层处理时,若酸洗液或镀液渗入磁体或磁体表面镀层中出现裂纹和孔洞等缺陷,镀层与磁体之间将发生电化学反应,形成腐蚀电流。多数情况下磁体作为阳极将优先发生腐蚀,作为阴极的镀层发生暴皮现象,最终导致磁体失效。
为了拓展Nd-Fe-B永磁体的使用范围,提高其服役性能,必须进行抗氧化和防腐蚀处理。目前主要有提高磁体的自身耐蚀性和对磁体进行表面涂层处理这两种防护方法。
一是合金化处理。相对于Nd2Fe14B主相,富Nd相更容易发生腐蚀,这是进行腐蚀防护时需要关注的重点。在Nd-Fe-B材料中添加Si、P、Cr、Zr、W、Al等中的1~2种来取代磁体中的Fe,或加入Nb、Ta、V、Ti、Al中的1种或2种,使其在晶界上发生偏析,降低富Nd相的化学活性,使其电化学电位与主相接近,从而改善晶界的耐蚀性,进而提高磁体的耐腐蚀性能。
此外,在晶界中引入MgO/Mg或 MgO和ZnO中间相,能够提高晶界的腐蚀电位,降低腐蚀电流密度,减少磁性能损失,在显著提高磁体矫顽力的同时能够提高磁体的耐蚀性 。需要注意的是,合金化处理在一定程度上能够有效地提高磁体的耐蚀性,但会牺牲部分磁性能,且耐蚀性提升有限,不能从根本上解决Nd-Fe-B材料耐蚀性差的问题,同时增加了生产成本,这些都限制了该方法的应用。
二是优化磁体微观结构。Nd-Fe-B磁体中腐蚀行为的程度取决于其微观结构,尤其取决于硬磁相的晶粒尺寸。在Nd-Fe-B磁体的制备过程中采用热压/热变形工艺可使晶粒尺寸细化,磁体高致密化,在提高磁体矫顽力的同时能够获得高抗腐蚀性和热稳定性的优质磁体。但该工艺受成型技术和成本的限制,目前热压/热变形Nd-Fe-B磁体主要做成磁环来用于汽车EPS电机等领域。
与前述合金化处理不同,表面涂层处理不但可以对磁体的氧化和腐蚀进行防护,而且对磁体磁性能的影响很小。根据使用要求,Nd-Fe-B磁体的表面涂层应满足以下条件:
(3) 致密性:无微孔或裂缝等缺陷,对气体或液体有良好的抗渗透能力;(6) 其他条件:某些特定情况下需具备热稳定性、电绝缘性、可焊接、可粘贴等。
目前最常用的表面涂层防护技术是电镀和化学镀,如表2和表3所示;此外还有化学转化成膜、有机物涂层、物理气相沉积等防护技术,具体如表4所示。
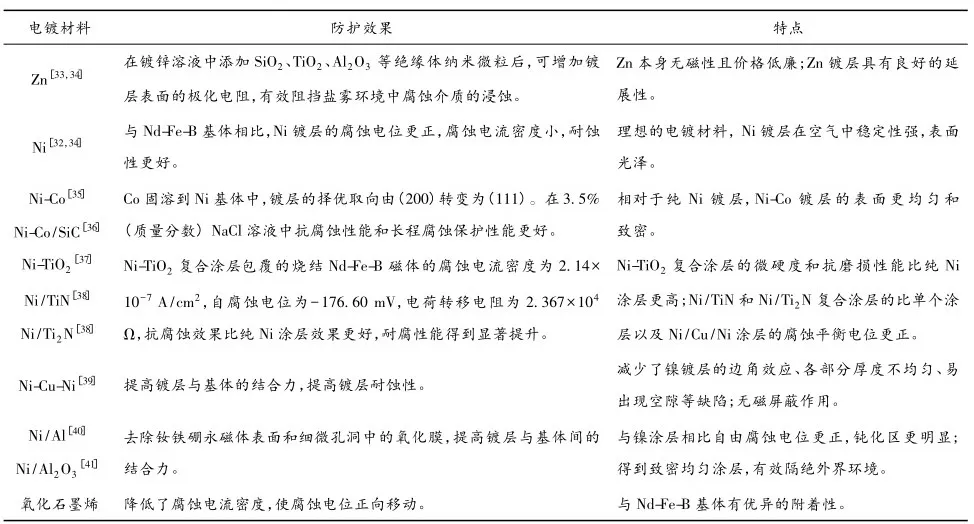
表3 Nd-Fe-B磁体的化学镀防护材料、特点及效果
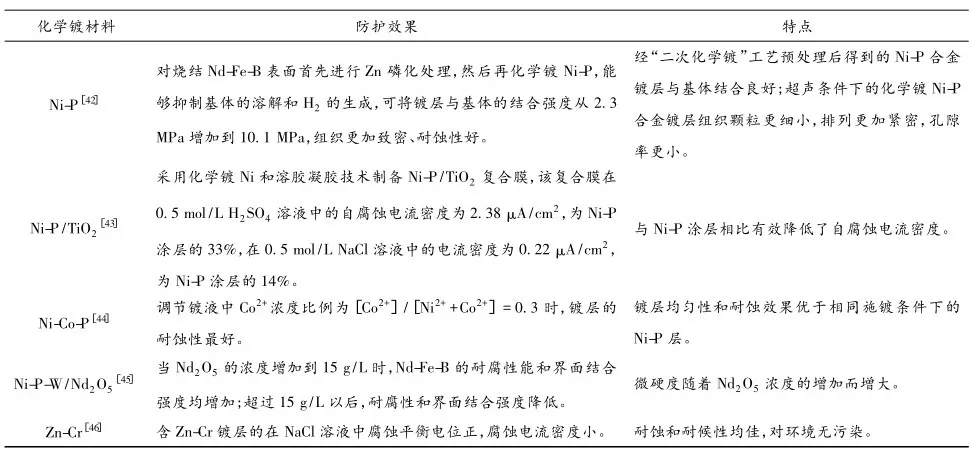
表4 Nd-Fe-B磁体的其他防护涂层材料、特点及效果
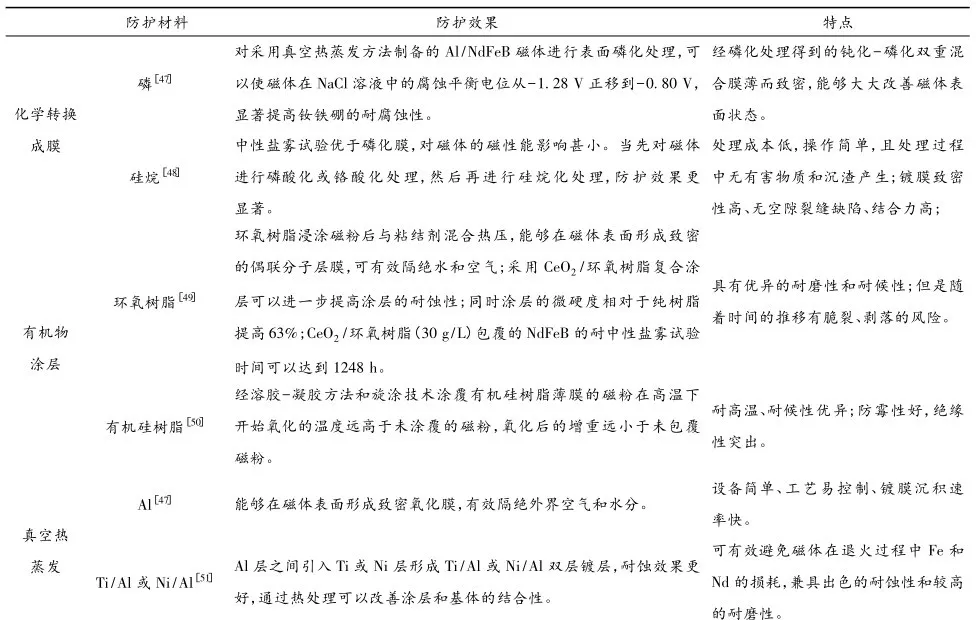
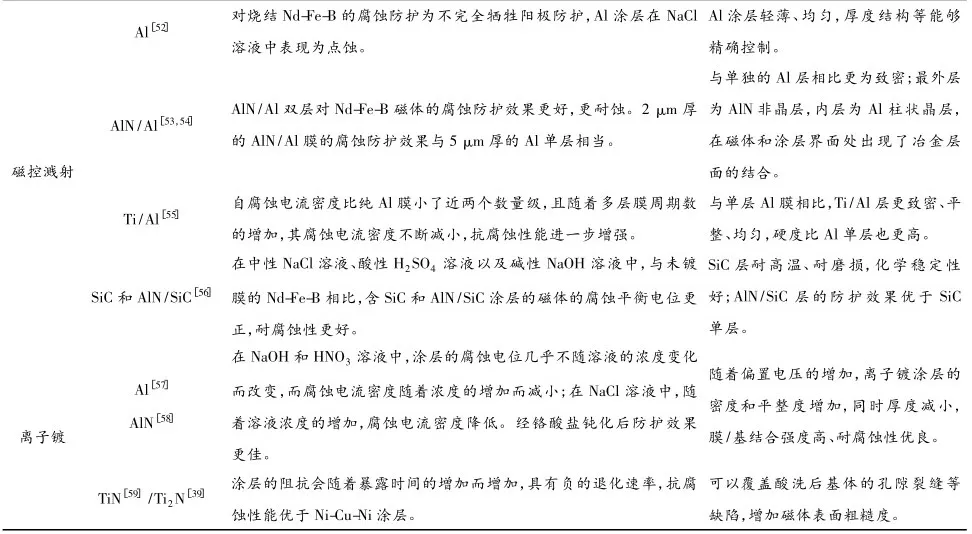
此外,将多种技术联用制备复合涂层,可以满足更苛刻的服役条件的需要。复合镀层不仅有双重保护的叠加作用,而且后一道涂层对前一道涂层的缺陷还有修补作用,如化学镀与电泳环氧树脂相结合、化学镀和电镀双层镀工艺、先真空热蒸发后磷化处理等。通常复合涂层防护效果更好,但是,生产成本也随涂层复杂度的提高而增加。实际生产过程中,应综合考虑防护需求和成本,选择合适的涂层及其制备技术。除上述传统防腐工艺外,近年来也陆续发展了一些新兴技术,例如,冷喷涂技术和微弧氧化技术等。在Nd-Fe-B磁体上采用冷喷涂技术(CS)沉积Ti涂层,能够有效保护基体,与使用氮气相比,使用氦气作为加速气体会产生更好的夯实效果,并且顶层孔状区域更薄。采用冷喷涂技术沉积Al层,能获得厚度均匀、孔隙率低的Al2O3保护层 。与热喷涂工艺相比,冷喷涂仅需要较少的热量输入,沉积过程中不会发生高温氧化、气化、熔化等反应,对喷涂材料的成分和微观结构影响小,因此更适合对氧化或热敏感的材料或基材。需要指出的是,冷喷涂技术目前还存在成本高、生产效率低、难以实现复杂磁体表面的均匀涂覆等不足。复杂几何形状的基体可采用微弧氧化(MAO)技术进行均匀涂覆。在硅酸盐溶液中通过微弧氧化可在Nd-Fe-B基体上制备具有“珊瑚礁”状表面形貌的非晶态SiO2涂层,该涂层具有优异的热冲击性,且涂层的耐蚀性随电压的升高而增加,与未涂层的Nd-Fe-B样品相比,涂层样品的耐腐蚀性提高了一个数量级。在铝酸盐中通过微弧氧化可制备Al2O3陶瓷涂层,也能有效改善磁体的耐腐蚀性,随着电压的升高,涂层的表面粗糙度随之增加,在420 V时,耐蚀效果达到最优 。但该方法同样存在一定的缺点:涂覆时会在磁体中形成少量的Nd2O3和Fe2O3等氧化物相从而降低磁体的磁能积(10%~20%)。
稀土永磁材料的氧化和腐蚀防护十分重要,随着其应用领域的拓宽、服役环境的愈发苛刻和用户要求的提升,对氧化和腐蚀防护技术提出了更高的要求。Sm-Co永磁材料的应用偏重于高温氧化防护,而Nd-Fe-B永磁材料的应用则偏重于腐蚀防护。对两类永磁材料,所采用的防护方法均包括提高自身耐蚀性和涂层防护两个方面。其中,涂层防护对磁体本身的磁性能影响小,应用更为广泛。针对具体的应用需求,需开发效果好、绿色环保、成本低廉的新型防护涂层及其制备技术。未来的研究和发展方向主要包括:
(1) 采用多元复合防护技术,实现不同防护技术优势互补,进一步提高抗氧化和耐腐蚀性,同时考虑成本;
(2) 将磁体的制备和防护过程“全链条”综合考虑,提高涂层的致密性和与基体的结合强度;
(3) 磁体的氧化和腐蚀防护机理方面,尤其是针对新的服役环境时,还需进一步深入研究;
(4) 开发新的涂层材料和涂覆技术,降低涂层制备过程对环境的影响等。